Civil Engineering Journal
Total Page:16
File Type:pdf, Size:1020Kb
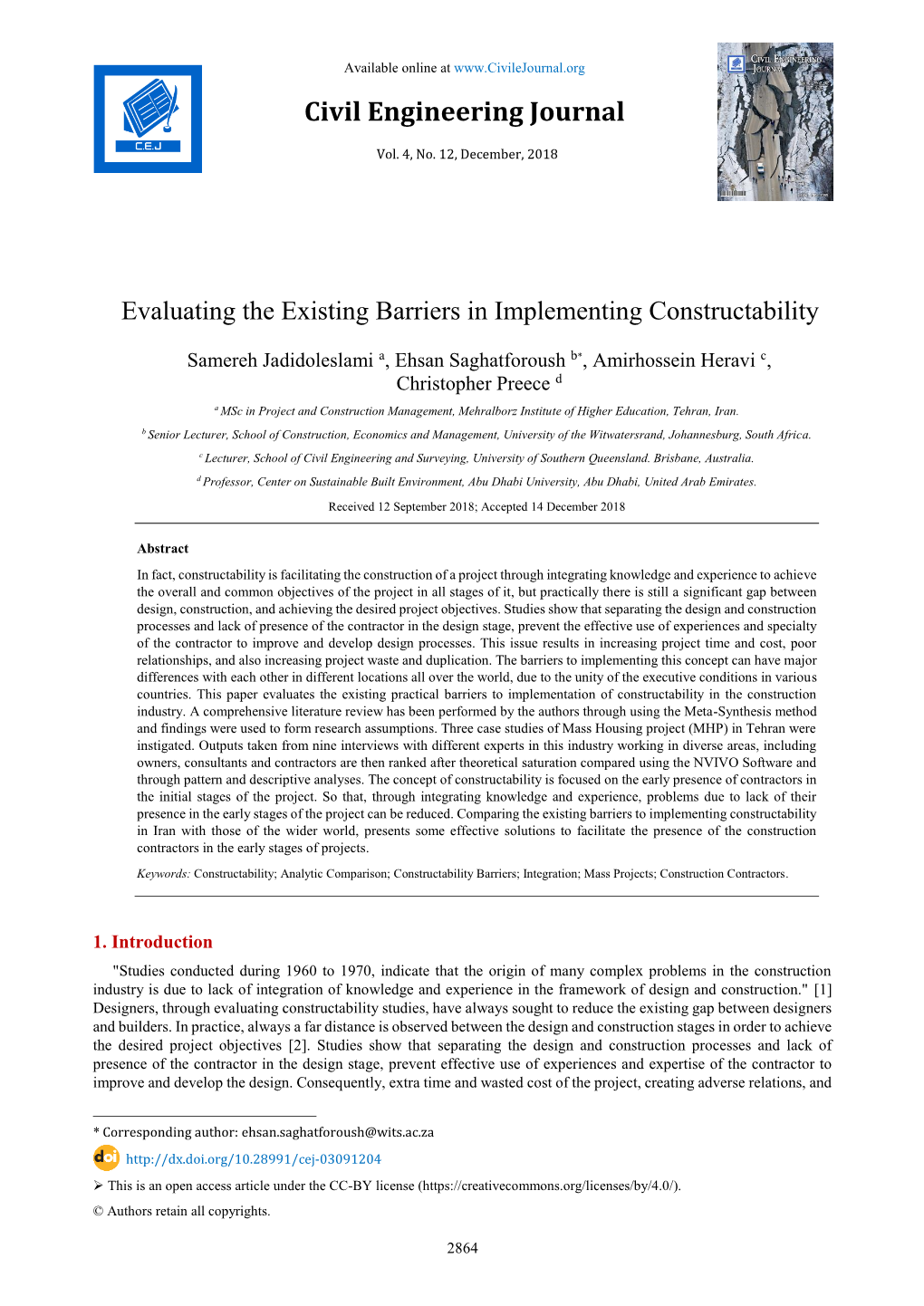
Load more
Recommended publications
-
The 15Th Int,L. Exhibition of Electricity Industry - 8 to 11 November 2015
The 15th Int,l. Exhibition of Electricity Industry - 8 to 11 November 2015 Row Company name Telephone Address WebSite Hall No Booth No 1 Zolfaghari shop 33992310 NO 200 . South Lalehzar St www.legrandco.ir 31A 101 33113636- No:10.first floor lalehzar trading bilding torabi 2 NOORASA TRADING CO noorasa.com 31A 102 33117575 godarzi alley. south lalezar st.Tehran iran No. 15 , Shemshad St. , Shahrivar 17th Ave. , 3 ZAFAR INDUSTRIES 66791575-8 www.zafarco.com 31A 103 Shadabad , Tehran-IRAN Unit 7, No67, street12, Yousef Abad, Tehran, 4 Mehregan Tejarat 88029365 www.telergon.co 31A 104 Iran Apt.61 , No.3047 , Vali e asr Ave., Tehran - 5 PARS KAVIR ARVAND 2122727609 www.parskavirarvand.ir 31A 105 IRAN no 379 , 7th st , sanat blvd , tous industrial estate 6 novin harris puya 051-35413465 www.novinharris.com 31A 106 , mashad No-1,Intersection Afsharian with Dehghan St, 7 Elkopars 021-66044150 www.Elkopars.com 31A 107 Mirghasemi St, Azadi Ave, Tehran, IRAN RM.801,BLOCK C ,BUILDING 2 , WAN TJPFTZ L.X. INTERNATIONAL ZHAO KE MAO INDUSTRIAL BUILDING, 8 0086 22 27314832 www.encgroupltd.com 31A 110 TRADING CO.,LTD. FU’AN ST., HE PING DISTRIST,TIANJIN, CHINA. Tianjin Tianfa Power Equipment No.1 Jingxiang Road, Beichen Technical Area, 9 86-22-86813187 www.chinatianfa.com 31A 111 Manufactory Co., Ltd. Tianjin, China Anhui EvoTec Power Generation 0086-0551- No.9 Suhe Road ,Lujiang Economic 10 www.evotecpower.com 31A 112 Co.,Ltd 87717188 Development Zone,Hefei, Anhui Province.China 38, XINGUANG ROAD, XINGUANG China. Shangyuan Electric Power 0086-577- 11 INDUSTRIAL PARK, YUEQING, ZHEJIANG www.chsys.cc 31A 113 Science & Technology CO., LTD 62797999 PROVINCE, CHINA China. -
Iran Chamber of Commerce,Industries and Mines Date : 2008/01/26 Page: 1
Iran Chamber Of Commerce,Industries And Mines Date : 2008/01/26 Page: 1 Activity type: Exports , State : Tehran Membership Id. No.: 11020060 Surname: LAHOUTI Name: MEHDI Head Office Address: .No. 4, Badamchi Alley, Before Galoubandak, W. 15th Khordad Ave, Tehran, Tehran PostCode: PoBox: 1191755161 Email Address: [email protected] Phone: 55623672 Mobile: Fax: Telex: Membership Id. No.: 11020741 Surname: DASHTI DARIAN Name: MORTEZA Head Office Address: .No. 114, After Sepid Morgh, Vavan Rd., Qom Old Rd, Tehran, Tehran PostCode: PoBox: Email Address: Phone: 0229-2545671 Mobile: Fax: 0229-2546246 Telex: Membership Id. No.: 11021019 Surname: JOURABCHI Name: MAHMOUD Head Office Address: No. 64-65, Saray-e-Park, Kababiha Alley, Bazar, Tehran, Tehran PostCode: PoBox: Email Address: Phone: 5639291 Mobile: Fax: 5611821 Telex: Membership Id. No.: 11021259 Surname: MEHRDADI GARGARI Name: EBRAHIM Head Office Address: 2nd Fl., No. 62 & 63, Rohani Now Sarai, Bazar, Tehran, Tehran PostCode: PoBox: 14611/15768 Email Address: [email protected] Phone: 55633085 Mobile: Fax: Telex: Membership Id. No.: 11022224 Surname: ZARAY Name: JAVAD Head Office Address: .2nd Fl., No. 20 , 21, Park Sarai., Kababiha Alley., Abbas Abad Bazar, Tehran, Tehran PostCode: PoBox: Email Address: Phone: 5602486 Mobile: Fax: Telex: Iran Chamber Of Commerce,Industries And Mines Center (Computer Unit) Iran Chamber Of Commerce,Industries And Mines Date : 2008/01/26 Page: 2 Activity type: Exports , State : Tehran Membership Id. No.: 11023291 Surname: SABBER Name: AHMAD Head Office Address: No. 56 , Beside Saray-e-Khorram, Abbasabad Bazaar, Tehran, Tehran PostCode: PoBox: Email Address: Phone: 5631373 Mobile: Fax: Telex: Membership Id. No.: 11023731 Surname: HOSSEINJANI Name: EBRAHIM Head Office Address: .No. -
Row Company Name Activity Telephone Address Website Hall No Booth No
The 10th Auto Parts Int,l. Exhibition - 16 to 19 November 2015 Row Company Name Activity Telephone Address WebSite Hall No Booth No 1 Abarashi Group (021)36466786 31B 38 D46 Golgasht St., Golzar Ave, Parand Industrial 2 Abzar Andisheh (021)56419014 www.abzarandisheh.com 40B 7 City, Tehran- Iran No.120, Kalhor Blvd, Shahre Ghods, 20th km of 3 Ace Engineering Co Electrical Auto Part Manufacturer (021)46884888-9 www.ACE.IR 40B 16 Karaj Old Road, Tehran, Iran Unit 2, No. 4, Koopayeh Alley, Before the 4 ADIB IMENi Garment industry and advertising (021)55380846 Open Area South 31 Qazvin Sq, South Kargar St, Tehran, Iran No. 17, Dastgheib Ave, West Shahed Blvd., 5 Agradad Industrial Automatic Door (021)44588684 www.agradad.com Open Area South 31 Tehransar, Tehran, Iran 6 AL.TECH. (021)26760992 www.dinapart.com 6 38 Manufactur of Types of Steel Parts by hot Sarir Bldg., Peykanshahr Exit,15th km Tehran- 7 Alborz Forging IND forging method, Auto Gearbox, Suspension (021)44784191-5 www.forgealborz.com 40B 29 Karaj Highway, Tehran- Iran Chassis No. 18 & 19, Next to the Gas Station, West 15 8 Aluminium Faz Car Aluminium Parts (Die Casting) (021)55690137 www.aluminiumfaz.ir 40A 3 Khordad St., Tehran, Iran First Floor, No.7, Zahiroleslam Alley, Iranshahr 9 Alvand Electronic Dana Vehicle Tracking, kinds of electronic boards (021)88313640 www.alvandelectronic.com 20-22 16 St., Taleghani Ave., Tehran- Iran Production of different kind of oil filters, Fuel Aman Filter Industrial 10 filters & Air filters for light & heavy (021)77167003-5 Unit 6, 3rd Floor, Piroozi Ave, Tehran, Iran www.amanfilter.com 31B 28 Production Group automobile No.207, 208- F, Sarv 24 St, Nasirabad 11 Aman Ghate Kar Automobile spare parts (021)56390795 20-22 20 Industrial Town, Saveh Road, Tehran, Iran Manufacturing Auto suspension & steering 1st Eastern 20 Meter St., Tabriz Exhibition old 12 Amirnia Co. -
Annual Report 2010/11 Annual Report 2010/11
ANNUAL REPORT 2010/11 2010/11 REPORT ANNUAL The intelligent Bank [email protected] www.sb24.com 1 ANNUAL REPORT 2010/11 CONTENTS OVERVIEW 5 FIVE-YEAR SUMMARY 6 FINANCIAL HIGHLIGHTS 7 CEO MESSAGE 8 CORPORATE PROFILE 10 HISTORY 11 BUSINESS MODEL 12 VISION, MISSION AND OBJECTIVES 13 OUR STRATEGY 14 SAMAN FINANCIAL GROUP 16 SHAREHOLDER STRUCTURE AND CAPITAL 18 BUSINESS REVIEW 19 OVERVIEW 20 RETAIL AND ELECTRONIC BANKING 22 INVESTMENT PRODUCTS AND SERVICES 25 INTERNATIONAL BANKING 26 LENDING 28 GOVERNANCE 37 CORPORATE GOVERNANCE 38 BOARD OF DIRECTORS 42 BOARD COMMITTEES 44 INTERNAL AUDIT AND CONTROL 46 INDEPENDENT AUDIT 47 EXECUTIVE MANAGEMENT 48 RISK MANAGEMENT 51 COMPLIANCE 54 HUMAN RESOURCES 56 CORPORATE SOCIAL RESPONSIBILITY 61 FINANCIAL STATEMENTS 67 SAMAN BANK BRANCH NETWORK 99 3 ANNUAL REPORT 2010/11 OVERVIEW 5 ANNUAL REPORT 2010/11 OVERVIEW FIVE-YEAR SUMMARY for the years ended March 21 US$ m Change in % in IRR billion, except where indicated 2011 2011 2010 11/10 2009 2008 2007 Profit and loss data Total income 894 9,262 7,043 31.5 5,700 4,462 2,880 Total expenses 747 7,747 6,164 25.7 5,237 3,950 2,621 Profit before tax 146 1,515 879 72.4 463 512 259 Tax 15 160 92 73.9 24 0 0 Net profit 131 1,355 787 72.2 439 512 258 Balance sheet data Total loans 5,813 60,246 34,184 76.2 27,341 23,989 15,269 Total assets 8,193 84,912 49,315 72.2 41,733 34,846 26,209 Total deposits 5,325 55,189 40,072 37.7 34,167 29,583 22,370 Total liabilities 7,727 80,081 46,393 72.6 39,341 33,320 24,954 Share capital 289 3,000 1,800 66.7 900 900 900 Total shareholders' -
Le 3 1 MARS 2016 5- Somayyeh Mousavi, Board Member [Signature] ,____
1:111111.1111:1 1 111 : 111:/I , JII~II:IInlll/11 1 [Emblem of Chogan Association of Isfahan Province] 0128200020 Date: Number: Given the existence of the world's oldest Meydan-e-Chogan (Chogan Field) in the city of Isfahan (which has been inscribed in the World Heritage List), we the board of the non-government lsfahan Choglin Association, on behalf of ourselves and our members, hereby proclaim our participation in the nomination process of "Chogan: A Horse-riding Game Accompanied by Music and Storytelling" in the Intangible Cultural Heritage List of UNESCO as well as our free, prior and informed consent for the inscription of this heritage. We hope that the inscription of this element results in a heightened awareness with regards to the values of the intangible heritage of humanity. 1- Hossein Jafari, Head ofthe Chogan Association oflsfahan Province [Signature] 2- Zahra Yavari, Women's Deputy[Signature] 3- Alireza Shams, Treasurer [Signature] Requ CLT I CIH I ITH 4- Hassan Aali, Secretary [Signature] Le 3 1 MARS 2016 5- Somayyeh Mousavi, Board Member [Signature] ,____ ... - No ......... Of3S'. ..... .. ....... .. 6- Karam Shiasi, Board Member [Signature] 7- Nourmohammad Karimi, Board Member [Signature] Address: Isfahan, End of Kaveh Street, Khrzough Bridge, Chogan Association oflsfahan Province Telephone: 0313-4457815 Fax: 0313-44487792-3 • • (LIP I ji/J cl.' (fl/1 ;1 fif ~ J ,; •-:·";~ ;1 (j~l (j~ (f'/ /1 •-:..;:.,~ (fl/1 ,, ccl.f£,J.I JJ:',. t, y. ~ u )r 1.f;t :c~Y)) dye ._.:J/ 1:/J; J _; ,, & .. • • • ' 't .. .. ;r,tjr/~ -o ;;,if~(/, ;r t(./../;;; -V Ao [Emblem ofChogan Association of Alborz Province] Date: 29/03/2016 Number: N49 We, the board of the Alborz Province Chogan Association, on behalf of ourselves and our members, hereby proclaim our participation in the nomination process of Chogan in the Intangible Cultural Heritage List of UNESCO as well as our free, prior and informed consent for this inscription. -
Programs of Studies Agriculture
AdmissionPrograms of Studies Agriculture Programs 6 of Studies 40 41 AdmissionPrograms of Studies Agriculture +QQ 42 43 AdmissionPrograms of Studies Agriculture Agriculture Course Associate * Master +8|8 $|VCQ]IVJ Agricultural Economy $8HQJQI78$$R$+7 Extension $8HQJQI78$$R$+QR%H @V$ $8HQJQI78$$R$ $VIVJ+8HQJQI7 Agricultural Economy Engineering-Environment and Natural Resources Economy Agricultural Economy-Natural Resources Economy $8R%H:86VJ1QJ Agricultural Engineering- Water $8$$R#VH$$ $8$$R$*$7 Agricultural Engineering-Agricultural Economy $8$$R$8R%H:QJ:JR Extension Agricultural Engineering-Agricultural Entomology Agricultural Engineering-Agricultural Extension and 8R%H:R8R%H:QJ Agricultural Engineering-Agricultural Extension and 8R%H:R86VJ1QJ Agricultural Engineering-Agricultural Machineries Mechanics Agricultural Engineering-Agricultural Management Agricultural Engineering-Agricultural Management- Agricultural Management Agricultural Engineering-Agricultural Management-Farm Management Agricultural Engineering-Agroecology Agricultural Engineering-Agronomy $8$$R$QJQI7+*$ $8$$R$QJQI7+*$R +*$ $8$$R$QJQI7+*$R Agronomy $8$$RR+7 44 Course Associate * Master +8|8 $8$$RR{V @ +7$7 Agricultural Engineering-Animal Sciences-Animal Husbandry Management $8$$RR{V @*$ $8$$RR{V @} $8$$RR+7} $8$$R*R7 V8$$ Agricultural Engineering-Farm Animal Sciences $8$$RR{V @ Agricultural Engineering-Food Industries and Sciences-Food Materials Chemistry Agricultural Engineering-Food Industries and Sciences-Food Materials Microbiology Agricultural Engineering-Food -
List of Twenty-Five Activated 16-Hours Health Centers in Tehran
List of twenty-five activated 16-hours health centers in Tehran: Centre Tel Medical Zone Centre Name Centre Address No University Municipality/District (021) Emam No 101, between ValiAsr 3 and 5, Pirouzi 55193322 Zone 19 Mohammad St, Morteza Gord Town, before Kazemi, 55193050 Bagher East Azadegan Highway 668652534 Zone 10 Centre No 10 No 584, Hashemi St, Khoshnabsh St. 66838772 Shahid Ahmadi Bagh Alley, Salehnia corssroad, Zamzam 55856818 Zone 17 Centre St, Ghalemorghi 55824030 Janbazan Blv, Hosseinanad Mofarah Zone Chahrdangeh Chahrdangeh 55268556 Road, Chahardangeh, Saveh Road No 298, Shahid Motahari St, Emam Tehran 56713748 Zone AhmadAbad AhmadAbad Hossein Sq, ValiAsr St, AhmadAbad 56718380 Mostophi Next to Second Rounabout, Ghaemiyeh Zone Ghaemiyeh Ghaemiyeh 56463541 Town Next to new Polic station, Azadi Blv, Zone 15 Emam Reza 33583882 Ghiyamdasht Emam Reza Blv, Hasan Abad, 56222121 Fashafouyeh Hasan Abad Fashafouyeh, Tehran-Qom Old road 56221072 Next to Forensic medicine, end of Shahid Zone 20 Kahrizak 56523686 Beheshti Blv, Kahrizak Next to Zendan Taavoni, Evin St, 24meter Zone 2 SaadatAbad 22115750 SaadatAbad Shahid Athami St, Opposite to 1st Zone 5 Kan Shahran St, Kohsar St, Shahran St, 44300894 Shahran Shohadaye Sazman Ab St, Hejab St, Zone 6 Fazel 88995073 Keshavarz Blv Iran West Shahid Dastgheyb St, End of Ostad Zone 9 Valfajr 66064613 Moeen St, Azadi St Zone 18 YaftAbad Zandiyeh St, Alghadir Sq, YaftAbad Blv 66801616 Dastgheyb St, Niloufar Blv, Golha Blv, Zone 21 Tehransar 44507797 Tehransar End of Dehkadeh Olampic Blv, Before -
49714 7 54 2 Abangan Industrial Group
The 15th Tehran Int,l. Industry Exhibition T.I.I.E 2015- 5 to 8 October 2015 Hall Booth Row Company Name Activity Phone Address Website No No 1 1st E-Commerce CRM (021)49714 7 54 Manufacturing steel billet - West Unit 2, No.75, Sattari Blvd, Open 2 Abangan industrial group Industrial and constructional -Steel (021)88200099 www.abangangroup.com Alman Africa(Jordan) St, Tehran, Iran Area bars Sq. Number 10, Mokhberi St., Ashrafi 3 Abnoos Palayesh Water treatment Systems (021)44477967-8 www.abnoos-p.com 27 29 Esfahani Highway, Tehran - Iran No.2, Golbon Sevom Gharbi, Fath Abzar Hava Pishe Gan Asia Vacuum Pump, Air Blower, www.asiavacuumpumps.c 4 (021)66791775 11, Fath Highway, Saeedi St., 40B 11 (Asia Vacuum) Compressor, Centrifuges om Azadi Sq., Tehran- Iran 5 Abzar Melli Services (051)37295708 7 12 Fiber Optic Lasers Marking & Unit 8, 4th Floor, No. 5, 3rd Acsid Maad Engineering Group Cutting, Laser welding Systems, 3D 6 (021)66593505 Kosar St, Sattarkhan Ave., Tohid www.acsid.ir 40A 30 Co. printers & Advanced industrial Sq., Tehran, Iran machines No.2, 5th Khoramdasht St., Sheet Metal, Laser cut, Punch press Siahsang Ave., Khoramdsht 7 Afra (021)76212468 31A 47 tooling Industrial Zone, Abali Rd., Tehran- Iran No. 287, Between Third and Fourth Avenue, Siyah Sang St 8 Afraz Sanat Tehran Seller of CNC Punch (021)76215104 31A 7 Khoramdasht Industrial Town, Tehran, Iran No. 17, Dastgheib Ave, West 9 Agradad Industrial Automatic Door (021)44588684 Shahed Blvd., Tehransar, Tehran, www.agradad.com 27 7 Iran Open North 10 Ahmad Asia (021)55488993-4 Area 38 No. -
A Modeling Study of Boundary Layer Wind Flow Over Tehran Region During a High Pollution Episode
Journal of Applied Fluid Mechanics, Vol. 7, No. 2, pp. 299-313, 2014. Available online at www.jafmonline.net, ISSN 1735-3572, EISSN 1735-3645. DOI: 10.36884/jafm.7.02.19569 A Modeling Study of Boundary Layer Wind Flow over Tehran Region during a High Pollution Episode H. Malakooti1† and A. A. Bidokhti2 1 Atmospheric and Oceanic Environmental Modeling Laboratory [AOEML], Faculty of Atmospheric and Oceanic Science and Technology, University of Hormozgan, P.O. Box: 3995, Bandar Abbas, Iran 2 Institute of Geophysics, University of Tehran, P.O. Box: 14155-6466, Tehran, Iran †Corresponding Author Email: [email protected] (Received February 24, 2012; accepted June 27, 2013) ABSTRACT The influence of a mega-city on the atmospheric boundary layer wind field was examined in the complex-terrain, semi-arid Tehran region using the Pennsylvania State University/National Center for Atmospheric Research fifth-generation Mesoscale Model (MM5) during a high pollution period. In addition, model sensitivity studies were conducted to evaluate the performance of the urban canopy and urban soil model "SM2-U (3D)" parameterization on the wind field. The topographic flows and urban effects were found to play important roles in modulating the wind field, and the urbanized areas exerted important local effects on the boundary layer meteorology. An emission inventory of heat generation was developed and updated for 2005 in this work. By using a detailed methodology, we calculated spatial and temporal distributions of the anthropogenic heat flux (Qf) for Tehran during 2005. Wintertime Qf is found larger than summertime Qf, which reflects the importance of heating emissions from buildings and traffic during cold and warm periods respectively. -
Tehran Provincial Directorate Department of the Environment
No. Japan International Cooperation Agency Tehran Provincial Directorate Department of the Environment The Study on Strengthening and Improving Air Quality Management in the Greater Tehran Area in the Islamic Republic of Iran FINAL REPORT January 2005 PADECO Co., Ltd. PACIFIC CONSULTANTS INTERNATIONAL GE JR 04-049 Japan International Cooperation Agency Tehran Provincial Directorate Department of the Environment The Study on Strengthening and Improving Air Quality Management in the Greater Tehran Area in the Islamic Republic of Iran FINAL REPORT January 2005 PADECO Co., Ltd. PACIFIC CONSULTANTS INTERNATIONAL for the currency conversion, exchange rate in January 2005 is applied: USD 1.00=IRR 7,900 USD 1.00 = JPY 102 PREFACE In response to a request from the Government of Islamic Republic of Iran, the Government of Japan decided to conduct “The Study on Strengthening and Improving Air Quality Management in the Greater Tehran Area in the Islamic Republic of Iran” and entrusted the Study to the Japan International Cooperation Agency. JICA dispatched to Iran a study team headed by Mr. Yuichiro Motomura, PADECO Co., Ltd. and composed of members of PADECO Co., Ltd. and Pacific Consultants International, four times during the period between September 2002 and December 2004. The team held discussions with the officials concerned of the Government of Iran, and conducted field surveys at the study area. After the team returned to Japan, further studies were made and the present report was prepared. I hope that this report will contribute to the promotion of the air quality management in Iran and to the enhancement of friendly relations between our two countries. -
Iauislamic Azad University
2015 2016 ISLAMIC AZAD UNIVERSITY ISLAMIC General General Catalog General Catalog IAU Catalog 2015-2016 AZAD 2015-2016 UNIVERSITY Islamic Azad University Learn & Live ... Higher Education for All Milad Tower; Tehran / Iran ISLAMICIS AZADA UNIVERSITY IAU General Catalog 2015-2016 www.intl.iau.ir 1 In the name of God I do hope that you DOO WKHRI¿FLDOVDQG HYHU\RQHHOVH KHOSWR SURPRWHWKHDFWLYLWLHV ,$8LVDQDVSLUDWLRQ RIWKLV8QLYHUVLW\ IRUKLJKHUHGXFDWLRQ ,VODPLF,UDQDQG ,$8 HVWDEOLVKHG VHHNHUVDFURVVWKH WKH5HYROXWLRQDUH XSRQ0U+DVKHPL¶V FRXQWU\ SURXGRI,VODPLF$]DG SURSRVDOZKLFKZDVDQ ,UDQ¶V6XSUHPH/HDGHU 8QLYHUVLW\ H[FHOOHQWSURSRVDODQG $\DWROODK$OL.KDPHQHL ,$8+HDGRI%RDUG WRH[SDQGLWVUHDFK RI7UXVWHHV$\DWROODK )RXQGHURI,VODPLF +DVKHPL5DIVDQMDQL 5HSXEOLFRI,UDQ ,PDP.KRPHLQL Learn & Live ... Contents Welcome from the President 07 1. About the University a) Our history 10 b) Mission Statement 11 c) Governance and Structure 12 d) Facts and Figures 14 e) ĐŚŝĞǀĞŵĞŶƚƐ;ĐĂĚĞŵŝĐ͕ƵůƚƵƌĂů͕ƚŚůĞƟĐ͕DĞĚŝĐĂůͿ ϭϳ 2. ĐĂĚĞŵŝĐīĂŝƌƐ a) &ĂĐƵůƟĞƐ ϮϮ b) DƵůƟƚƵĚĞŽĨ^ƉĞĐŝĂůŝnjĂƟŽŶ ϮϮ c) Research Centers 23 d) Academic Excellence 23 3. Student Life a) ĂŵƉƵƐĞƐ Ϯϲ b) ^ƉŽƌƚƐ&ĂĐŝůŝƟĞƐ Ϯϲ c) ^ƚƵĚĞŶƚZĞƐŝĚĞŶĐĞƐ Ϯϲ d) ^ƚƵĚĞŶƚ'ƌŽƵƉƐĂŶĚƐƐŽĐŝĂƟŽŶƐ Ϯϲ e) ĂƌĞĞƌ^ĞƌǀŝĐĞƐΘůƵŵŶŝ Ϯϳ ĨͿ Counseling Services Ϯϳ 4 4. Admission a) Academic Calendar 30 b) Admission Requirements 30 c) /ŶƚĞƌŶĂƟŽŶĂů^ƚƵĚĞŶƚƐĚŵŝƐƐŝŽŶ ϯϮ d) dƵŝƟŽŶ&ĞĞƐĂŶĚƵƌƐĂƌŝĞƐ ϯϯ 5. /ŶƚĞƌŶĂƟŽŶĂůīĂŝƌƐ a) /ŶƚĞƌŶĂƟŽŶĂůWƌŽĮůĞ ϯϲ b) DĞŵďĞƌƐŚŝƉŽĨ/ŶƚĞƌŶĂƟŽŶĂůƐƐŽĐŝĂƟŽŶƐ ϯϳ c) /ŶƚĞƌŶĂƟŽŶĂůǁĂƌĚƐ ϯϴ d) /ŶƚĞƌŶĂƟŽŶĂůZĞĐŽŐŶŝƟŽŶŽĨYƵĂůŝĮĐĂƟŽŶƐ ϯϴ e) /ŶƚĞƌŶĂƟŽŶĂůdžĐŚĂŶŐĞWƌŽŐƌĂŵƐ ΘZĞƐĞĂƌĐŚŽͲŽƉĞƌĂƟŽŶƐ ϯϴ ĨͿ /ŶƚĞƌŶĂƟŽŶĂůŽŶĨĞƌĞŶĐĞƐ ϯϵ g) /ŶƚĞƌŶĂƟŽŶĂůWƵďůŝĐĂƟŽŶƐ ϯϵ 6. Programs of Studies a) Agriculture 42 b) ƉƉůŝĞĚͲ^ĐŝĞŶĐĞ ϱϬ c) ƌƚ ϱϮ d) ĂƐŝĐ^ĐŝĞŶĐĞƐ ϱϲ e) ŶŐŝŶĞĞƌŝŶŐ ϲϮ ĨͿ ,ƵŵĂŶ^ĐŝĞŶĐĞƐ ϳϰ g) DĞĚŝĐĂů^ĐŝĞŶĐĞƐ ϴϲ h) sĞƚĞƌŝŶĂƌLJDĞĚŝĐŝŶĞ ϴϴ 7. Structure of Programs a) ŐƌŝĐƵůƚƵƌĞ ϵϮ b) ƌƚ ϵϲ c) Engineering 100 d) ,ƵŵĂŶ^ĐŝĞŶĐĞƐ ϭϬϴ e) ĂƐŝĐ^ĐŝĞŶĐĞƐ ϭϮϬ 8. -
Meteorology and Air-Quality in a Mega-City: Application to Tehran, Iran
PhD thesis of École des Ponts ParisTech Presented and publicly defended on January 21, 2010 by Hossein MALAKOOTI for obtaining the PhD degree of École des Ponts ParisTech / Universite Paris Est Specialty: Science and technology environment Meteorology and air-quality in a mega-city: application to Tehran, Iran The defense committee was consisted of Matthias BEEKMANN LISA laboratory, CNRS & President University Paris XII and VII Alain CLAPPIER LIVE laboratory, University of Reviewer Strasbourg Abbas-Ali ALI-AKBARI Institute of Geophysics, Reviewer BIDOKHTI University of Tehran Bruno SPORTISSE INRIA Thesis Supervisor Sylvain DUPONT EPHYSE research unit, INRA Referee Maya MILLIEZ EDF Research & Development Referee Abstract The influence of a mega-city on the atmospheric boundary layer and surface conditions was examined in the complex-terrain, semi-arid Tehran region using the Pennsylvania State University/National Center for Atmospheric Research fifth-generation Mesoscale Model (MM5) during a high pollution period. In addition, model sensitivity studies were conducted to evaluate the performance of the urban canopy and urban soil model "SM2-U (3D)" parameterization on the meteorological fields and ground level air pollutant concentrations in this area. The topographic flows and urban effects were found to play important roles in modulating the wind and temperature fields, and the urbanized areas exerted important local effects on the boundary layer meteorology. An emission inventory of air pollutants and an inventory of heat generation were developed and updated for 2005 in this work. Emissions from on-road motor vehicles constitute a major portion of the emission inventory and play the most important role in terms of contributions of air pollutants to the atmosphere in Tehran.