Nº De Arquivo
Total Page:16
File Type:pdf, Size:1020Kb
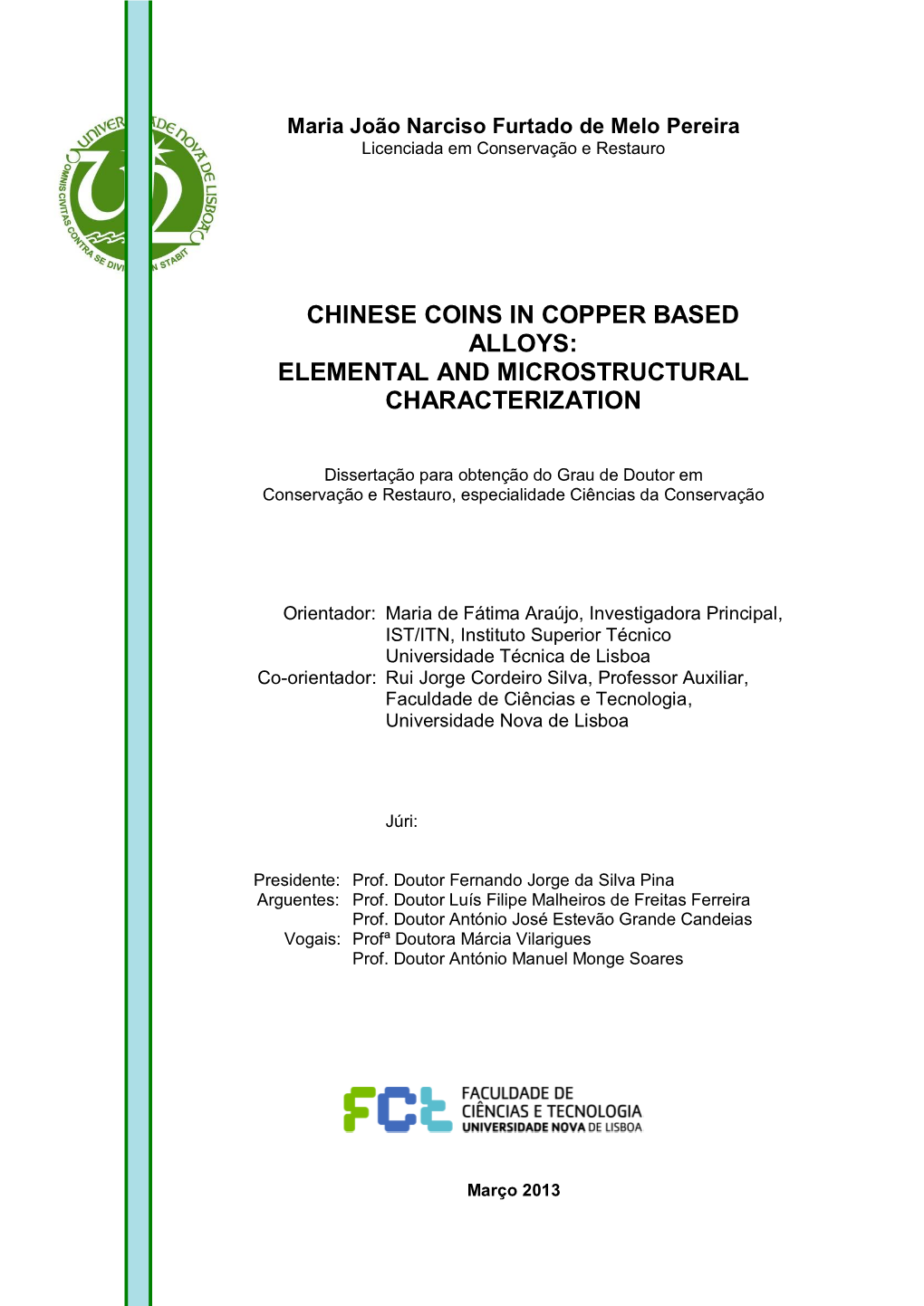
Load more
Recommended publications
-
European and Chinese Coinage Before the Age of Steam*
《中國文化研究所學報》 Journal of Chinese Studies No. 55 - July 2012 The Great Money Divergence: European and Chinese Coinage before the Age of Steam* Niv Horesh University of Western Sydney 1. Introduction Economic historians have of late been preoccupied with mapping out and dating the “Great Divergence” between north-western Europe and China. However, relatively few studies have examined the path dependencies of either region insofar as the dynamics monetiza- tion, the spread of fiduciary currency or their implications for financial factor prices and domestic-market integration before the discovery of the New World. This article is de- signed to highlight the need for such a comprehensive scholarly undertaking by tracing the varying modes of coin production and circulation across Eurasia before steam-engines came on stream, and by examining what the implications of this currency divergence might be for our understanding of the early modern English and Chinese economies. “California School” historians often challenge the entrenched notion that European technological or economic superiority over China had become evident long before the * Emeritus Professor Mark Elvin in Oxfordshire, Professor Hans Ulrich Vogel at the University of Tübingen, Professor Michael Schiltz and Professor Akinobu Kuroda 黑田明伸 at Tokyo University have all graciously facilitated the research agenda in comparative monetary his- tory, which informs this study. The author also wishes to thank the five anonymous referees. Ms Dipin Ouyang 歐陽迪頻 and Ms Mayumi Shinozaki 篠崎まゆみ of the National Library of Australia, Ms Bick-har Yeung 楊 碧 霞 of the University of Melbourne, and Mr Darrell Dorrington of the Australian National University have all extended invaluable assistance in obtaining the materials which made my foray into this field of enquiry smoother. -
Hwang, Yin (2014) Victory Pictures in a Time of Defeat: Depicting War in the Print and Visual Culture of Late Qing China 1884 ‐ 1901
Hwang, Yin (2014) Victory pictures in a time of defeat: depicting war in the print and visual culture of late Qing China 1884 ‐ 1901. PhD Thesis. SOAS, University of London http://eprints.soas.ac.uk/18449 Copyright © and Moral Rights for this thesis are retained by the author and/or other copyright owners. A copy can be downloaded for personal non‐commercial research or study, without prior permission or charge. This thesis cannot be reproduced or quoted extensively from without first obtaining permission in writing from the copyright holder/s. The content must not be changed in any way or sold commercially in any format or medium without the formal permission of the copyright holders. When referring to this thesis, full bibliographic details including the author, title, awarding institution and date of the thesis must be given e.g. AUTHOR (year of submission) "Full thesis title", name of the School or Department, PhD Thesis, pagination. VICTORY PICTURES IN A TIME OF DEFEAT Depicting War in the Print and Visual Culture of Late Qing China 1884-1901 Yin Hwang Thesis submitted for the degree of Doctor of Philosophy in the History of Art 2014 Department of the History of Art and Archaeology School of Oriental and African Studies, University of London 2 Declaration for PhD thesis I have read and understood regulation 17.9 of the Regulations for students of the School of Oriental and African Studies concerning plagiarism. I undertake that all the material presented for examination is my own work and has not been written for me, in whole or in part, by any other person. -
Conceptualizing the Blue Frontier: the Great Qing and the Maritime World
Conceptualizing the Blue Frontier: The Great Qing and the Maritime World in the Long Eighteenth Century Inauguraldissertation zur Erlangung der Doktorwürde der Philosophischen Fakultüt der Ruprecht-Karls-Universität Heidelberg Vorgelegt von Chung-yam PO Erstgutachter: Prof. Dr. Harald Fuess Zweitgutachter: Prof. Dr. Joachim Kurtz Datum: 28 June 2013 Table of Contents Abstract 2 Acknowledgments 3 Emperors of the Qing Dynasty 5 Map of China Coast 6 Introduction 7 Chapter 1 Setting the Scene 43 Chapter 2 Modeling the Sea Space 62 Chapter 3 The Dragon Navy 109 Chapter 4 Maritime Customs Office 160 Chapter 5 Writing the Waves 210 Conclusion 247 Glossary 255 Bibliography 257 1 Abstract Most previous scholarship has asserted that the Qing Empire neglected the sea and underestimated the worldwide rise of Western powers in the long eighteenth century. By the time the British crushed the Chinese navy in the so-called Opium Wars, the country and its government were in a state of shock and incapable of quickly catching-up with Western Europe. In contrast with such a narrative, this dissertation shows that the Great Qing was in fact far more aware of global trends than has been commonly assumed. Against the backdrop of the long eighteenth century, the author explores the fundamental historical notions of the Chinese maritime world as a conceptual divide between an inner and an outer sea, whereby administrators, merchants, and intellectuals paid close and intense attention to coastal seawaters. Drawing on archival sources from China, Japan, Korea, Vietnam, and the West, the author argues that the connection between the Great Qing and the maritime world was complex and sophisticated. -
View / Download 7.3 Mb
Between Shanghai and Mecca: Diaspora and Diplomacy of Chinese Muslims in the Twentieth Century by Janice Hyeju Jeong Department of History Duke University Date:_______________________ Approved: ___________________________ Engseng Ho, Advisor ___________________________ Prasenjit Duara, Advisor ___________________________ Nicole Barnes ___________________________ Adam Mestyan ___________________________ Cemil Aydin Dissertation submitted in partial fulfillment of the requirements for the degree of Doctor of Philosophy in the Department of History in the Graduate School of Duke University 2019 ABSTRACT Between Shanghai and Mecca: Diaspora and Diplomacy of Chinese Muslims in the Twentieth Century by Janice Hyeju Jeong Department of History Duke University Date:_______________________ Approved: ___________________________ Engseng Ho, Advisor ___________________________ Prasenjit Duara, Advisor ___________________________ Nicole Barnes ___________________________ Adam Mestyan ___________________________ Cemil Aydin An abstract of a dissertation submitted in partial fulfillment of the requirements for the degree of Doctor of Philosophy, in the Department of History in the Graduate School of Duke University 2019 Copyright by Janice Hyeju Jeong 2019 Abstract While China’s recent Belt and the Road Initiative and its expansion across Eurasia is garnering public and scholarly attention, this dissertation recasts the space of Eurasia as one connected through historic Islamic networks between Mecca and China. Specifically, I show that eruptions of -
The Jesuit Role As “Experts” in High Qing Cartography and Technology∗
臺大歷史學報第31期 BIBLID1012-8514(2003)31p.223-250 2003年6月,頁223~250 2003.1.7收稿,2003.5.29通過刊登 The Jesuit Role as “Experts” in High Qing Cartography and Technology∗ Benjamin A. Elman∗∗ Abstract Earlier accounts have generally overvalued or undervalued the role of the Jesu- its in Ming-Qing intellectual life. In many cases the Jesuits were less relevant in the ongoing changes occurring in literati learning. In the medical field, for example, before the nineteenth century few Qing physicians (ruyi 儒醫) took early modern European “Galenic” medicine seriously as a threat to native remedies. On the other hand, the Kangxi revival of interest in mathematics was closely tied to the introduc- tion of Jesuit algebra (jiegen fang 借根方), trigonometry (sanjiao xue 三角學), and logarithyms (duishu 對數). In the midst of the relatively “closed door” policies of the Yongzheng emperor and his successors, a large-scale effort to recover and col- late the treasures of ancient Chinese mathematics were prioritized in the late eight- eenth and early nineteenth century. Despite setbacks during the early eighteenth century Rites Controversy, the Jesuits in China remained important “experts” (專家) in the Astro-Calendric Bureau (欽天監) and supervisors in the Qing dynasty’s imperial workshops. Earlier Adam Schall (1592-1666) and Ferdinand Verbiest (1623-1688) had not only championed the role of mathematics in Christianizing literati elites, but they also produced in- struments and weapons at the behest of both the Ming and Qing dynasties. The tech- nical expertise of the Jesuits in the China mission during the eighteenth century also ranged from translating Western texts and maps, introducing surveying methods to producing cannon, pulley systems, sundials, telescopes, water-pumps, musical in- struments, clocks, and other mechanical devices. -
Dressing for the Times: Fashion in Tang Dynasty China (618-907)
Dressing for the Times: Fashion in Tang Dynasty China (618-907) BuYun Chen Submitted in partial fulfillment of the requirements for the degree of Doctor of Philosophy in the Graduate School of Arts and Sciences COLUMBIA UNIVERSITY 2013 © 2013 BuYun Chen All rights reserved ABSTRACT Dressing for the Times: Fashion in Tang Dynasty China (618-907) BuYun Chen During the Tang dynasty, an increased capacity for change created a new value system predicated on the accumulation of wealth and the obsolescence of things that is best understood as fashion. Increased wealth among Tang elites was paralleled by a greater investment in clothes, which imbued clothes with new meaning. Intellectuals, who viewed heightened commercial activity and social mobility as symptomatic of an unstable society, found such profound changes in the vestimentary landscape unsettling. For them, a range of troubling developments, including crisis in the central government, deep suspicion of the newly empowered military and professional class, and anxiety about waste and obsolescence were all subsumed under the trope of fashionable dressing. The clamor of these intellectuals about the widespread desire to be “current” reveals the significant space fashion inhabited in the empire – a space that was repeatedly gendered female. This dissertation considers fashion as a system of social practices that is governed by material relations – a system that is also embroiled in the politics of the gendered self and the body. I demonstrate that this notion of fashion is the best way to understand the process through which competition for status and self-identification among elites gradually broke away from the imperial court and its system of official ranks. -
Introduction
Notes Introduction 1. Hobsbawm 1990, 66. 2. Diamond 1998, 322–33. 3. Fairbank 1992, 44–45. 4. Fei Xiaotong 1989, 1–2. 5. Diamond 1998, 323, original emphasis. 6. Crossley 1999; Di Cosmo 1998; Purdue 2005a; Lavely and Wong 1998, 717. 7. Richards 2003, 112–47; Lattimore 1937; Pan Chia-lin and Taeuber 1952. 8. My usage of the term “geo-body” follows Thongchai 1994. 9. B. Anderson 1991, 86. 10. Purdue 2001, 304. 11. Dreyer 2006, 279–80; Fei Xiaotong 1981, 23–25. 12. Jiang Ping 1994, 16. 13. Morris-Suzuki 1998, 4; Duara 2003; Handler 1988, 6–9. 14. Duara 1995; Duara 2003. 15. Turner 1962, 3. 16. Adelman and Aron 1999, 816. 17. M. Anderson 1996, 4, Anderson’s italics. 18. Fitzgerald 1996a: 136. 19. Ibid., 107. 20. Tsu Jing 2005. 21. R. Wong 2006, 95. 22. Chatterjee (1986) was the first to theorize colonial nationalism as a “derivative discourse” of Western Orientalism. 23. Gladney 1994, 92–95; Harrell 1995a; Schein 2000. 24. Fei Xiaotong 1989, 1. 25. Cohen 1991, 114–25; Schwarcz 1986; Tu Wei-ming 1994. 26. Harrison 2000, 240–43, 83–85; Harrison 2001. 27. Harrison 2000, 83–85; Cohen 1991, 126. 186 • Notes 28. Duara 2003, 9–40. 29. See, for example, Lattimore 1940 and 1962; Forbes 1986; Goldstein 1989; Benson 1990; Lipman 1998; Millward 1998; Purdue 2005a; Mitter 2000; Atwood 2002; Tighe 2005; Reardon-Anderson 2005; Giersch 2006; Crossley, Siu, and Sutton 2006; Gladney 1991, 1994, and 1996; Harrell 1995a and 2001; Brown 1996 and 2004; Cheung Siu-woo 1995 and 2003; Schein 2000; Kulp 2000; Bulag 2002 and 2006; Rossabi 2004. -
Revisiting the Relationship Between Indigenous Agency and Museum Inventories
Revisiting the Relationship between Indigenous Agency and Museum Inventories: An Object-Centered Study of the Formation of Lübeck's Jacobsen Collection (1884/1885) from the Northwest Coast of America By Angela Hess Cover: Objects from Lübeck’s Jacobsen collection. Photo: Angela Hess, July 2019 Revisiting the Relationship between Indigenous Agency and Museum Inventories: An Object-Centered Study of the Formation of Lübeck's Jacobsen Collection (1884/1885) from the Northwest Coast of America Author: Angela Hess Student number: s2080087 MA Thesis Archaeology (4ARX-0910ARCH) Supervisor: Dr. M. De Campos Françozo Specialization: Heritage and Museum Studies University of Leiden, Faculty of Archaeology Leiden, June 5, 2020, final version 1 2 Table of Contents Acknowledgements ............................................................................................................. 5 Chapter One: Introduction .................................................................................................. 6 Defining the Research Scope: Aims and Objectives, Hypotheses, Limitations ............. 10 Methodology and Theoretical Frameworks .................................................................. 12 Working Definitions ...................................................................................................... 14 Outline of Chapters ....................................................................................................... 17 Chapter Two: Contexts and Concepts for the Study of the 1884/85 Jacobsen Collection19 2.1 -
Ming China As a Gunpowder Empire: Military Technology, Politics, and Fiscal Administration, 1350-1620 Weicong Duan Washington University in St
Washington University in St. Louis Washington University Open Scholarship Arts & Sciences Electronic Theses and Dissertations Arts & Sciences Winter 12-15-2018 Ming China As A Gunpowder Empire: Military Technology, Politics, And Fiscal Administration, 1350-1620 Weicong Duan Washington University in St. Louis Follow this and additional works at: https://openscholarship.wustl.edu/art_sci_etds Part of the Asian History Commons, and the Asian Studies Commons Recommended Citation Duan, Weicong, "Ming China As A Gunpowder Empire: Military Technology, Politics, And Fiscal Administration, 1350-1620" (2018). Arts & Sciences Electronic Theses and Dissertations. 1719. https://openscholarship.wustl.edu/art_sci_etds/1719 This Dissertation is brought to you for free and open access by the Arts & Sciences at Washington University Open Scholarship. It has been accepted for inclusion in Arts & Sciences Electronic Theses and Dissertations by an authorized administrator of Washington University Open Scholarship. For more information, please contact [email protected]. WASHINGTON UNIVERSITY IN ST. LOUIS DEPARTMENT OF HISTORY Dissertation Examination Committee: Steven B. Miles, Chair Christine Johnson Peter Kastor Zhao Ma Hayrettin Yücesoy Ming China as a Gunpowder Empire: Military Technology, Politics, and Fiscal Administration, 1350-1620 by Weicong Duan A dissertation presented to The Graduate School of of Washington University in partial fulfillment of the requirements for the degree of Doctor of Philosophy December 2018 St. Louis, Missouri © 2018, -
Münzen Aus Dem Reich Der Mitte – Von Der Kaurischnecke Zum Käsch
Münzen aus dem Reich der Mitte – von der Kaurischnecke zum Käsch Um 1500 v. Chr. benutzte man in China Schneckengehäuse als Münzen; später wurden die Schnecken aus Knochen oder Kupfer nachgeahmt. Daneben zirkulierte Gerätegeld, zum Beispiel in Form von Messer- oder Spatenmünzen, aber auch runde Münzen waren in Gebrauch. 211 v. Chr. begann der erste chinesische Kaiser mit der Ausgabe von einheitlichen Reichsmünzen, aus denen sich schliesslich die Käschmünze entwickelte: eine runde Kupfermünze mit viereckigem Loch, die bis zum Ende der chinesischen Kaiserzeit im Jahr 1911 ausgegeben wurde. 1 von 21 www.sunflower.ch China, Shang-Dynastie, durchbohrte Cypraea moneta (Kauri) Denomination: Cypraea Moneta (Kauri) Prägeautorität: Prägeort: Prägejahr: -1500 Gewicht in Gramm: 0.9 Durchmesser in mm: 21.0 Material: Andere Eigentümer: Sunflower Foundation Kaurischnecken waren die langlebigste Währung aller Zeiten. In China wurden sie schon vor über 3000 Jahren als Geld benutzt und liefen, zusammen mit anderen Zahlungsmitteln, bis 1578 um. Die chinesische Schrift, die im 2. Jahrtausend v. Chr. entwickelt wurde, verwendet das Zeichen für Kauri noch heute in Wörtern wie Münze, Geld, Kaufen, Wert und ähnlichen. Das Zeichen ist auch Bestandteil der Inschrift auf vielen chinesischen Käschmünzen. Der venezianische Händler Marco Polo, der im späten 13. Jahrhundert während mehrerer Jahre in China lebte, überlieferte in seinen Reisebeschreibungen (Il Milione) einige Preise. Demnach bezahlte man damals in China für ein Huhn 5 Kauri, für vier Kilogramm Getreide 8 Kauri und für eine Kuh 320 Kauri. 2 von 21 www.sunflower.ch China, Zhou-Dynastie, Kauriimitation aus Knochen, ca. 700 v. Chr. Denomination: Kauriimitation Prägeautorität: Zhou-Dynastie Prägeort: Unbestimmt Prägejahr: -700 Gewicht in Gramm: 2.84 Durchmesser in mm: 28.0 Material: Andere Eigentümer: Sunflower Foundation Um dem Handel und dem täglichen Gebrauch zu genügen, brauchte man eine grosse Menge Kauris. -
Copyrighted Material
INDEX Aodayixike Qingzhensi Baisha, 683–684 Abacus Museum (Linhai), (Ordaisnki Mosque; Baishui Tai (White Water 507 Kashgar), 334 Terraces), 692–693 Abakh Hoja Mosque (Xiang- Aolinpike Gongyuan (Olym- Baita (Chowan), 775 fei Mu; Kashgar), 333 pic Park; Beijing), 133–134 Bai Ta (White Dagoba) Abercrombie & Kent, 70 Apricot Altar (Xing Tan; Beijing, 134 Academic Travel Abroad, 67 Qufu), 380 Yangzhou, 414 Access America, 51 Aqua Spirit (Hong Kong), 601 Baiyang Gou (White Poplar Accommodations, 75–77 Arch Angel Antiques (Hong Gully), 325 best, 10–11 Kong), 596 Baiyun Guan (White Cloud Acrobatics Architecture, 27–29 Temple; Beijing), 132 Beijing, 144–145 Area and country codes, 806 Bama, 10, 632–638 Guilin, 622 The arts, 25–27 Bama Chang Shou Bo Wu Shanghai, 478 ATMs (automated teller Guan (Longevity Museum), Adventure and Wellness machines), 60, 74 634 Trips, 68 Bamboo Museum and Adventure Center, 70 Gardens (Anji), 491 AIDS, 63 ack Lakes, The (Shicha Hai; Bamboo Temple (Qiongzhu Air pollution, 31 B Beijing), 91 Si; Kunming), 658 Air travel, 51–54 accommodations, 106–108 Bangchui Dao (Dalian), 190 Aitiga’er Qingzhen Si (Idkah bars, 147 Banpo Bowuguan (Banpo Mosque; Kashgar), 333 restaurants, 117–120 Neolithic Village; Xi’an), Ali (Shiquan He), 331 walking tour, 137–140 279 Alien Travel Permit (ATP), 780 Ba Da Guan (Eight Passes; Baoding Shan (Dazu), 727, Altitude sickness, 63, 761 Qingdao), 389 728 Amchog (A’muquhu), 297 Bagua Ting (Pavilion of the Baofeng Hu (Baofeng Lake), American Express, emergency Eight Trigrams; Chengdu), 754 check -
Violence and Predation, Mainly in the Form of Piracy, Were Two Of
violence and predation robert j. antony Violence and Predation on the Sino-Vietnamese Maritime Frontier, 1450–1850 iolence and predation, mainly in the form of piracy, were two of V the most persistent and pervasive features of the Sino-Vietnamese maritime frontier between the mid-fifteenth and mid-nineteenth cen- turies.1 In the Gulf of Tonkin, which is the focus of this article, piracy was, in fact, an intrinsic feature of this sea frontier and a dynamic and significant force in the region’s economic, social, and cultural devel- opment. My approach, what scholars call history from the bottom up, places pirates, not the state, at center stage, recognizing their impor- tance and agency as historical actors. My research is based on various types of written history, including Qing archives, the Veritable Records of Vietnam and China, local Chinese gazetteers, and travel accounts; I also bring in my own fieldwork in the gulf region conducted over the past six years. The article is divided into three sections: first, I discuss the geopolitical characteristics of this maritime frontier as a background to our understanding of piracy in the region; second, I consider the socio-cultural aspects of the gulf region, especially the underclass who engaged in clandestine activities as a part of their daily lives; and third, I analyze five specific episodes of piracy in the Gulf of Tonkin. The Gulf of Tonkin (often referred to here simply as the gulf), which is tucked away in the northwestern corner of the South China Sea, borders on Vietnam in the west and China in the north and east.