ABB Drives Technical Guide Book 2 ABB Drives I Technical Guide Book ABB Drives - Technical Guide Book
Total Page:16
File Type:pdf, Size:1020Kb
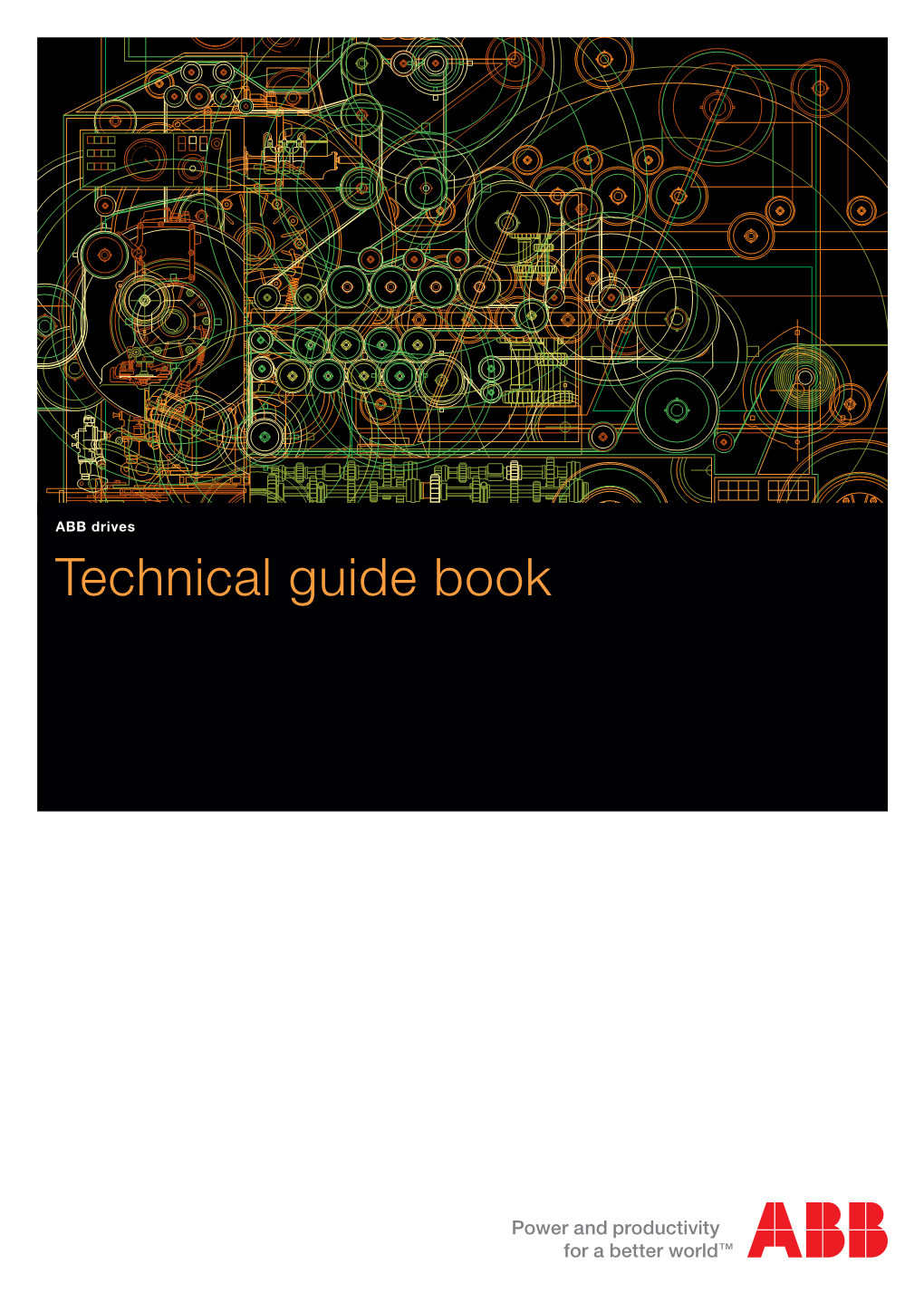
Load more
Recommended publications
-
ACSM1 System Engineering Manual
ACSM1 System Engineering Manual 2 3 ACSM1-04 Drive Modules System Engineering Manual 3AFE 68978297 REV A EN EFFECTIVE: 08.10.2007 PDM Vault ID: 00579251 2007 ABB Oy. All rights reserved. 4 5 Safety instructions Never work on the drive, the braking chopper circuit, the motor cable or the motor when input power is applied to the drive. After disconnecting input power, always wait for 5 minutes to let the intermediate circuit capacitors discharge before you start working on the drive, control cabling, motor or motor cable. Even when input power is not applied to the drive, externally supplied control circuits may carry dangerous voltages. Always ensure by measuring that no voltage is actually present. A rotating permanent magnet motor can generate a dangerous voltage. Lock the motor shaft mechanically before connecting a permanent magnet motor to the drive, and before doing any work on a drive system connected to a permanent magnet motor. For complete safety instructions see the ACSM1-04 Drive Modules (0.75 to 45 kW) Hardware Manual (code: 3AFE68797543 [English]). 6 Table of contents Safety instructions ................................................................................................................... 5 Table of contents...................................................................................................................... 6 About this manual .................................................................................................................... 8 Compatibility .............................................................................................................................. -
Siemens On-Stage Powerpoint-Template
Electromobility Solutions for Modern Haul Trucks 2017 Haulage & Loading Exhibition / Conference Phoenix, Arizona USA Unrestricted © Siemens Industry, Inc. 2017 usa.siemens.com/mining Introduction What is Electromobility? Electromobility is a general term for the development of electric- powered drivetrains designed to shift vehicle design away from the use of fossil fuels and carbon gas emissions. • Hybrid Electric Vehicles (Internal Combustion Engine (ICE) and batteries w/ Electric motor) • Plug-in Electric Vehicles (HEV that can be externally charged) • Battery Electric Vehicles (all electric vehicle that can be externally charged) Electric Drive Technology and Charging Solutions for Mobility. Unrestricted © Siemens Industry, Inc. 2017 2017 Haulage & Loading Exhibition and Conference Page 2 May 8, 2017 Electromobility Solutions for Modern Haul Trucks Mechanical Vehicle (MV) w/ On-board Diesel Engine Traditional Powertrain Main Components: - Diesel Engine - Torque Converter - Drive Shaft (Cardan) - Transmission - Differential - Gearbox Disadvantages: - Low efficiency - High maintenance costs Unrestricted © Siemens Industry, Inc. 2017 2017 Haulage & Loading Exhibition and Conference Page 3 May 8, 2017 Electromobility Solutions for Modern Haul Trucks Electric Vehicle (EV) w/ On-board Diesel Engine Electrical Drivetrain replaces Mechanical Drivetrain, keeps the diesel engine Main Components: - Diesel engine - Alternator w/ Rectifier - Inverters - Traction motors - Braking chopper/Grid resistor Benefits - Higher efficiency - Electrical braking -
Brushless DC Electric Motor
Please read: A personal appeal from Wikipedia author Dr. Sengai Podhuvan We now accept ₹ (INR) Brushless DC electric motor From Wikipedia, the free encyclopedia Jump to: navigation, search A microprocessor-controlled BLDC motor powering a micro remote-controlled airplane. This external rotor motor weighs 5 grams, consumes approximately 11 watts (15 millihorsepower) and produces thrust of more than twice the weight of the plane. Contents [hide] 1 Brushless versus Brushed motor 2 Controller implementations 3 Variations in construction 4 AC and DC power supplies 5 KM rating 6 Kv rating 7 Applications o 7.1 Transport o 7.2 Heating and ventilation o 7.3 Industrial Engineering . 7.3.1 Motion Control Systems . 7.3.2 Positioning and Actuation Systems o 7.4 Stepper motor o 7.5 Model engineering 8 See also 9 References 10 External links Brushless DC motors (BLDC motors, BL motors) also known as electronically commutated motors (ECMs, EC motors) are electric motors powered by direct-current (DC) electricity and having electronic commutation systems, rather than mechanical commutators and brushes. The current-to-torque and frequency-to-speed relationships of BLDC motors are linear. BLDC motors may be described as stepper motors, with fixed permanent magnets and possibly more poles on the rotor than the stator, or reluctance motors. The latter may be without permanent magnets, just poles that are induced on the rotor then pulled into alignment by timed stator windings. However, the term stepper motor tends to be used for motors that are designed specifically to be operated in a mode where they are frequently stopped with the rotor in a defined angular position; this page describes more general BLDC motor principles, though there is overlap. -
Electrical Braking 2 Technical Guide No.8 - Electrical Braking Contents
Technical Guide No. 8 Electrical Braking 2 Technical Guide No.8 - Electrical Braking Contents 1. Introduction ........................................................... 5 1.1 General .................................................................... 5 1.2 Drive applications map according to speed and torque ..................................................................... 5 2. Evaluating braking power................................... 7 2.1 General dimension principles for electrical braking ..................................................................... 7 2.2 Basics of load descriptions ................................... 8 2.2.1 Constant torque and quadratic torque...... 8 2.2.2 Evaluating brake torque and power .......... 8 2.2.3 Summary and Conclusions ........................ 12 3. Electrical braking solutions in drives .............. 13 3.1 Motor Flux braking ................................................. 13 3.2 Braking chopper and braking resistor .................. 14 3.2.1 The energy storage nature of the frequency converter ................................... 14 3.2.2 Principle of the braking chopper ............... 15 3.3 Anti-parallel thyristor bridge configuration ........... 17 3.4 IGBT bridge configuration...................................... 19 3.4.1 General principles of IGBT based regeneration units ....................................... 19 3.4.2 IGBT based regeneration-control targets . 19 3.4.3 Direct torque control in the form of direct power control ............................................. -
W.E.F. : 2016-2017
R.V.R. & J.C. College of Engineering (Autonomous) R-16 R V R & J C COLLEGE OF ENGINEERING, CHOWDAVARAM, GUNTUR-19 (Autonomous) R-16 REGULATIONS & SCHEME CHOICE BASED CREDIT SYSTEM Regulations, Scheme of Instruction, Examination and Detailed Syllabi for 4-Year B.Tech Degree Course in Electrical & Electronics Engineering (Semester System) w.e.f. : 2016-2017 B.Tech.(EEE)/R-16/2016-2017 Page 1 of 187 R.V.R. & J.C. College of Engineering (Autonomous) R-16 EEE Department Vision: “To impart education leading to highly competent professionals in the field of Electrical & Electronics Engineering who are globally competent and to make the Department a Centre for Excellence”. EEE Department Mission: “Integrated development of professionals with knowledge and skills in the field of specialization, ethics and values needed to be employable in the field of Electrical Engineering and contribute to the economic growth of the employing organization and pursue lifelong learning” Program Educational Objectives of B. Tech Program in Electrical & Electronics Engineering: PEO I. To facilitate the students to become Electrical & Electronics Engineers who are competent, innovative and productive in addressing the broader interests of the organizations & society. PEO II. To prepare the students to grow professionally with necessary soft skills. PEO III. To make our graduates to engage and excel in activities to enhance knowledge in their professional works with ethical codes of life & profession. Program Specific Outcomes of B. Tech Program in Electrical & Electronics Engineering: PSO1 Graduates of the program will be able to demonstrate knowledge and hands on competence in developing, Testing, Operation and Maintenance of Electrical & Electronics systems. -
OPERATING INSTRUCTIONS NORDAC Frequency Inverters
OPERATING INSTRUCTIONS NORDAC Frequency Inverters Type series SK 1.300/1 to SK 2.400/1 And Type series SK 1.300/3 to SK 38.000/3 BU 3000/93E GETRIEBEBAU NORD Schlicht + Küchenmeister GmbH & Co. Rudolf-Diesel-Str. 1 * D - 22941 Bargteheide Postfach 1262 * D - 22934 Bargteheide Tel.: 04532/401-0 * Telex 261505 * Fax 04532/401-555 Table of contents Page 1.0 General 1 1.1 Delivery 1 1.2 Scope of delivery 1 1.3 Installation and operation 1 2.0 Installation 2 3.0 Frequency inverter dimensions 3 3.1 Braking chopper dimensions 3 4.0 Connection 4 4.1 Power section 4 4.1.1 Type SK 1.300/1 - SK 2.400/1 4 4.1.2 Type SK 1.300/3 - SK 38.000/3 4 4.1.3 Additional measures 4 4.2 Control section 5 4.2.1 Control terminal strip 5 4.2.2 Control inputs 6 5.0 Operation and displays 12 5.1 Setting and display facilities 13 5.2 Description of settings and displays 14 6.0 Commssioning 22 6.1 Parameter record 23 7.0 Braking chopper 24 7.1 Technical data 24 7.2 Installation instructions 24 7.3 Settings 24 7.4 Selection criteria 24 8.0 Failure and faults 26 9.0 Speed controller 27 10.0 Mains filter 29 10.1 Radio interference suppression 29 10.2 Effect on other consumers 30 10.3 Line capacitances (motor cable) 30 10.4 Output filters 30 10.5 Regulations 30 11.0 Technical data 31 T.-Nr.: 06063082 Stand: 42/93 1.0 General NORDAC frequency Inverters are sine-related pulse-width modulated inverters with a constant DC link voltage. -
Design Considerations of Traction Converter for Three Phase AC Locomotive
© 2018 JETIR June 2018, Volume 5, Issue 6 www.jetir.org (ISSN-2349-5162) Design considerations of Traction converter for three phase AC locomotive Dr. Premananda Pany [email protected] Synergy Institute of Engineering & Technology Dhenkanal, Odisha Abstract- This paper presents some of the important design issues of traction converter for three phase AC locomotive. The analytical approach is required to select appropriate components which will make the system more reliable, stable with minimum power loss. The mathematical approach required in the design of each component is presented. The main components of TC such as IGBTs, Driver circuit, heat sink, precharging resistor, DC link capacitor, resonant filter, bleeder resistors, earth fault resistors, braking chopper are discussed in this paper. The behavior of each component under variation in power supply and supply frequency are discussed. The analysis presented in this paper is very much useful for a designer while designing a converter inverter system for a vehicular system. The control strategy adopted for front end converter is discussed and simulated results using PSIM is also presented. Keywords: Traction converter, Inverter, DC link, Resonant, PSIM. I. Introduction The traction drives consists of power electronic have become more complex over the past decades due to the advancement of high power and high speed semiconductors such as IGBT, IGCT, microprocessor control and three phase inverter drives . Now a day it is common to operate 3 phase induction motor drives with traction electric multiple unit and locomotive. The three phase induction motor drive provides an improved in the overall performance of electric traction equipment. With the ability to increase the level of the available power, the train operator has been able to improve train operating times, the speed of the traction unit and the demand on the power supply system. -
Analysis and Simulation of Mechanical Trains Driven By
ANALYSIS AND SIMULATION OF MECHANICAL TRAINS DRIVEN BY VARIABLE FREQUENCY DRIVE SYSTEMS A Thesis by XU HAN Submitted to the Office of Graduate Studies of Texas A&M University in partial fulfillment of the requirements for the degree of MASTER OF SCIENCE December 2010 Major Subject: Mechanical Engineering ANALYSIS AND SIMULATION OF MECHANICAL TRAINS DRIVEN BY VARIABLE FREQUENCY DRIVE SYSTEMS A Thesis by XU HAN Submitted to the Office of Graduate Studies of Texas A&M University in partial fulfillment of the requirements for the degree of MASTER OF SCIENCE Approved by: Chair of Committee, Alan B. Palazzolo Committee Members, Won-jong Kim Hamid A. Toliyat Head of Department, Dennis O'Neal December 2010 Major Subject: Mechanical Engineering iii ABSTRACT Analysis and Simulation of Mechanical Trains Driven by Variable Frequency Drive Systems. (December 2010) Xu Han, B.S., Zhejiang University, P.R.China Chair of Advisory Committee: Dr. Alan B. Palazzolo Induction motors and Variable Frequency Drives (VFDs) are widely used in in- dustry to drive machinery trains. However, some mechanical trains driven by VFD- motor systems have encountered torsional vibration problems. This vibration can induce large stresses on shafts and couplings, and reduce the lifetime of these me- chanical parts. Long before the designed lifetime, the mechanical train may encounter failure. This thesis focuses on VFDs with voltage source rectifiers for squirrel-cage induction motors of open-loop Volts/Hertz and closed-loop Field Oriented Control (FOC). First, the torsional vibration problems induced by VFDs are introduced. Then, the mathematical model for a squirrel-cage induction motor is given. -
University of Engineering & Management, Jaipur
UNIVERSITY OF ENGINEERING & MANAGEMENT,JAIPUR Lecture-wise Plan Subject Name: Electric Drives Subject Code-EE701 Year: 4th Year Semester: Eight Module Topics Number of Lectures Number Electric Drive: 5L 1. Concept, classification, parts and 1 advantages of electrical drives. 1 2. Types of Loads, Components of load 2 toques, Fundamental torque equations, Equivalent value of drive parameters for loads with rotational and translational motion.. 3. Determination of moment of inertia, 1 Steady state stability, Transient stability 4. Multi quadrant operation of drives. Load 1 equalization Motor power rating: 6L 1. Thermal model of motor for heating and 2 2 cooling, classes of motor duty 2. Determination of motor rating for continuous, short time and intermittent 2 duty. 3. Equivalent current, torque and power 1 methods of determination of rating for fluctuating and intermittent loads 4. Effect of load inertia & environmental 1 factors Stating of Electric Drives: 6L 1. Effect of starting on Power supply, motor \2 3. and load 2. Methods of stating of electric motors. 2 Acceleration time Energy relation during stating, 3. Methods to reduce the Energy loss during starting 2 Braking of Electric Drives: 2L 4 1. Types of braking, braking of DC motor, 2 Induction motor and Synchronous motor, Energy loss during braking Dc Motor Drives: 6L 5 1. Modelling of DC motors, State space modelling, block diagram &Transfer 2 function 2. Single phase, three phases fully controlled and half controlled DC drives. Dual 2 converter control of DC drives 3. Power factor, supply harmonics and ripple in motor current chopper controlled DC 2 motor drives Induction motor drives: 4L 6 1. -
An Efficient Braking Algorithm for Interior Permanent Magnet Synchronous Motors
13th INTERNATIONAL SYMPOSIUM on POWER ELECTRONICS - Ee 2005 XIII Međunarodni simpozijum Energetska elektronika – Ee 2005 NOVI SAD, SERBIA & MONTENEGRO, November 2nd - 4th, 2005 AN EFFICIENT BRAKING ALGORITHM FOR INTERIOR PERMANENT MAGNET SYNCHRONOUS MOTORS Vladan R. Jevremović, Borislav Jeftenić* SR Drives Ltd – Emerson Motor Technologies, Harrogate, United Kingdom Faculty of Electrical Engineering, University of Belgrade, Serbia & Montenegro* Abstract: This paper presents an efficient braking permanent magnet and reluctance torque has been algorithm for a permanent magnet synchronous motor proposed. drives with a diode front end rectifier. Regenerative braking energy is dissipated in stator windings which act 2. EFFICIENT BRAKING CRITERIA as a braking resistor, without adding any additional Braking methods within electrical motor drives can braking choppers and electronic control circuits. be classified into three main groups – inertial, soft and Application of this braking algorithm results in maximum active braking. power losses in stator windings and relatively high a) Inertial, passive braking (coast down) is achieved braking torque, all within inverter current and voltage simply by turning off the inverter. The whole braking capabilities. Also, this algorithm determines braking process relies on rotor inertia, mechanical load, viscous dynamics by regulating voltage on a DC link capacitor and ventilating friction. This braking method has no well bellow critical limit. practical value when being used at high motor speeds, Key Words: Braking/Permanent Magnet Synchronous Motor due to very long stopping time. Also, this way of braking is recommended for low speeds only. In case of high 1. INTRODUCTION speeds, where field weakening algorithm is used (with Permanent magnet synchronous motor drives can notoriously high direct axis currents), electromotive operate in all four quadrants of torque-speed force can be relatively high (several kV). -
— Technical Guide No. 8 Electrical Braking
— ABB DRIVES Technical guide No. 8 Electrical braking 2 TECHNICAL GUIDE NO. 8 ELECTRICAL BRAKING — Electrical braking Cranes, elevators, centrifuges, downhill conveyors and test benches are typical examples of braking applications. Several factors affect the selection of the most optimal braking solution, such as system efficiency, installation footprint, complexity of the installation and investment and energy cost. 3 — Table of contents 04 Introduction 04 General 05 Drive applications map according to speed and torque 06 Evaluating braking power 06 General dimension principles for electrical braking 07 Basics of load descriptions 09 Constant torque and quadratic torque 09 Evaluating brake torque and power 11 Summary and conclusions 12 Electrical braking solution in drives 12 Motor flux braking 13 Brake chopper and resistor 13 The energy storage nature of the variable speed drive 14 Principle of the brake chopper 16 A thyristor bridge configuration 17 Regenerative rectifier unit 18 Matrix technology 19 Regenerative braking unit 20 IGBT bridge configuration 20 General principles of IGBT based regeneration units 20 IGBT based regeneration – control targets 21 Active control of the IGBTs for low harmonic content 22 Dimensioning an IGBT regeneration unit 23 Common DC 25 Evaluating the life cycle cost of different forms of electrical braking 25 Calculating the direct cost of energy 25 Evaluating the investment cost 26 Calculating the life cycle cost 26 Case 1 – Occasional braking 27 Case 2 – Crane application 28 Case 3 – Centrifuge application 29 Comparison of different braking technologies 30 Symbols and definitions 4 TECHNICAL GUIDE NO. 8 ELECTRICAL BRAKING — Introduction — General This guide continues ABB’s technical guide series, describing the practical solutions available in reducing stored energy and transferring stored energy back into electrical energy. -
Design and Analysis of Drive System with Slip Ring Induction Motor for Electric Traction in India
View metadata, citation and similar papers at core.ac.uk brought to you by CORE provided by Crossref International Journal of Power Electronics and Drive System (IJPEDS) Vol. 5, No. 3, February 2015, pp. 374~382 ISSN: 2088-8694 374 Design and Analysis of Drive System with Slip Ring Induction Motor for Electric Traction in India C. Nagamani*, R. Somanatham**, U. Chaitanya Kumar*** * Research Scholar, University College of Engineering, Osmania University, Hyderabad, India ** HOD, Dept. Of Electrical & Electronics Engineering, Anurag College of Engineering, Hyderabad, India *** M.Tech Student, Dept. Of EEE, Anurag College of Engineering, Hyderabad, India Article Info ABSTRACT The use of Squirrel Cage Motor for Traction has revolutionised the motive Article history: power of a Locomotive. The Asynchronous Motor is rugged, has high Received Oct 31, 2014 starting Torque, very smooth Voltage and Speed control as compared to a Revised Jan 12, 2015 DC Series Motor. When looking at the Traction perspective, a Wound Rotor Induction Motor can be an alternative to the Squirrel Cage Motor as it has Accepted Jan 24, 2015 higher starting Torque at lower starting current and better efficiency than a Squirrel Cage Motor. The Slip Power Recovery scheme also plays a Keyword: proactive role as there can be substantial savings of energy in case of a Wound Rotor Induction Motor as the Slip Power recovered can be used to Electric Traction drive the Auxiliary Loads of the Locomotive and also for powering the Slip Power Recovery trailing Passenger Cars. A detailed design and analysis of a Drive System Squirrel Cage Induction Motor with Wound Rotor Induction Motor for Electric Traction is presented in this Wound Rotor Induction Motor Research Paper.