A Heterogeneous PLC with BLE Mesh Network for Reliable and Real-Time Smart Cargo Monitoring
Total Page:16
File Type:pdf, Size:1020Kb
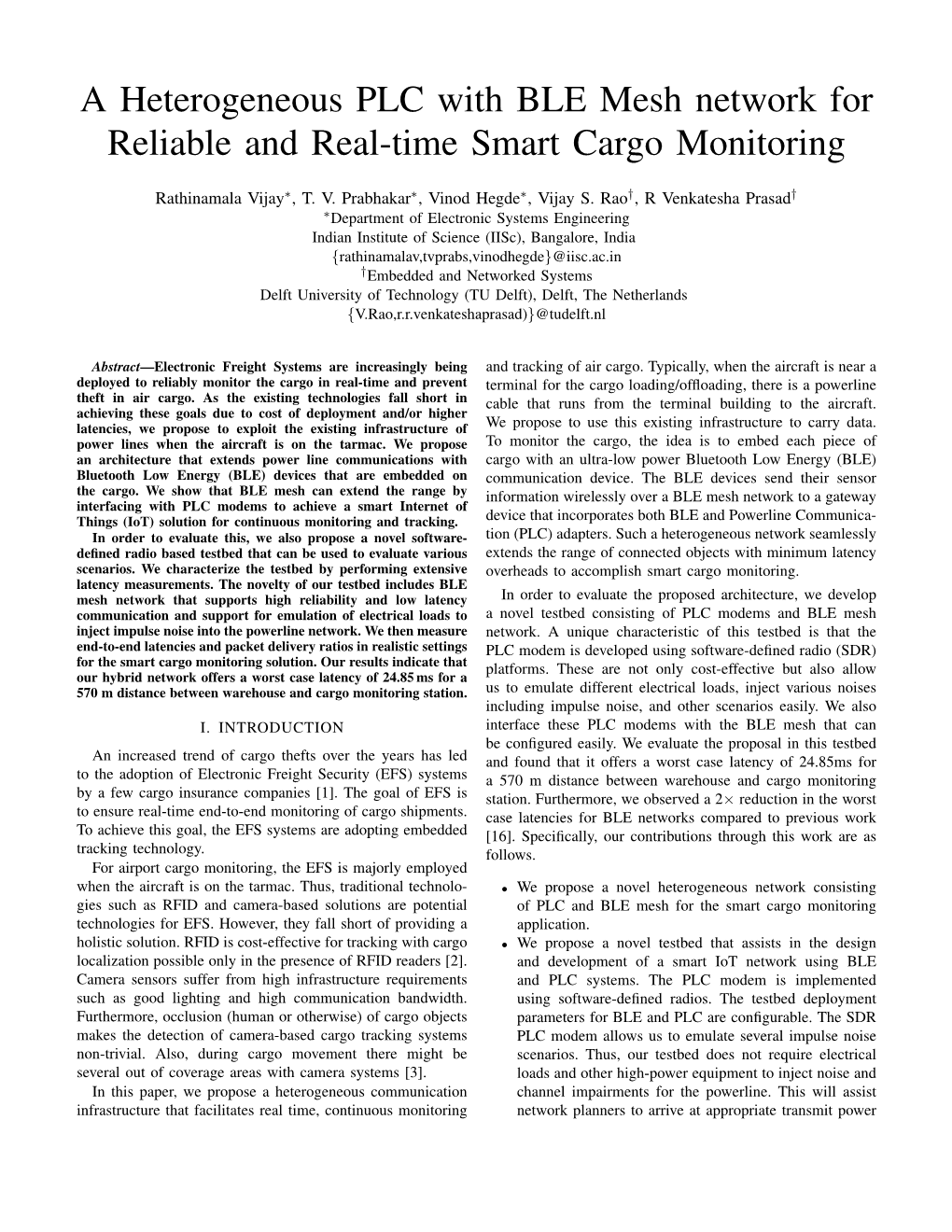
Load more
Recommended publications
-
Powerline and Coax Adapters
Powerline and Coax Adapters Powerline Ethernet Adapters Powerline Wireless Extenders HomePNA Ethernet Bridges Powerline and Coax Adapters Powerline and Coax Adapters Introduction Introduction ZyXEL Powerline and Coax Adapters Powerline Home Network NSA325 2-Bay Power Plus Turn Your Power Lines or Coaxial Cables into a Smart Home Network Media Server NWD2205 Wireless N ZyXEL’s broad line of Powerline adapters allow you to use your existing power outlets to create a fast and secure home network. You won’t need USB Adapter Study Room to install new cables, which saves you time, money and effort. Your Powerline network will enable you to share your Internet connection as well PLA4231 as all your digital media content, so you can enjoy Broadband content anywhere in your home. In fact, Powerline extends your network to areas 500 Mbps Powerline PLA4211 500 Mbps Mini Powerline even wireless signals may not reach. Wireless N Extender STB2101-HD Pass-Thru Ethernet Adapter HD IP Set-Top Box Game Wired LAN Adapter Product Portfolio Console Internet Blu-ray HDTV xDSL/Cable Player Modem PLA4201 PLA4225 500 Mbps 500 Mbps Mini Powerline Powerline 4-Port Power Line NBG5615 Ethernet Adapter Gigabit Switch Living Room Wireless N Ethernet Simultaneous AV/HDMI Cable Dual-Band Wireless HD Powerline PLA4231 N750 Media Router Extender 500 Mbps Powerline Wireless N Extender Power Line Benefits of Wired LAN Adapter 500 Mbps Mini Powerline Plug-and-Play Design Oce Room Ethernet Adapter 500 Mbps Mini Powerline Pass-Thru Simply plug a ZyXEL Powerline Adapter into an outlet near your Ethernet Adapter IEEE 1901 router and plug your router into it. -
MLKHN1500 Fully Compliant IEEE 1901 HD-PLC Power Line Communications (PLC) IC
MLKHN1500 Fully compliant IEEE 1901 HD-PLC Power line Communications (PLC) IC Datasheet KDS-HANFF02EAA Rev. 1.00 MegaChips’ Proprietary and Confidential This information shall not be shared or distributed outside the company and will be exchanged based on the signed proprietary information exchange agreement. MegaChips reserves the right to make any change herein at any time without prior notice. MegaChips does not assume any responsibility or liability arising out of application or use of any product or service described herein except as explicitly agreed upon. MegaChips’ Proprietary Information – Strictly Confidential Page 1 of 68 MLKHN1500 Datasheet Rev.1.0.0 Contents 1. Product Overview ....................................................................................................................................... 6 1.1. Functional Overview ............................................................................................................................ 6 1.1.1. Key Features ................................................................................................................................ 6 1.1.2. Applications .................................................................................................................................. 7 1.2. Block Diagram ..................................................................................................................................... 7 2. Pins ............................................................................................................................................................ -
Smart Grid Last-Mile Communications Model and Its Application to The
IEEE TRANSACTIONS ON SMART GRID, VOL. 4, NO. 1, MARCH 2013 5 Smart Grid Last-Mile Communications Model and Its Application to the Study of Leased Broadband Wired-Access Felipe Gómez-Cuba, Student Member, IEEE, Rafael Asorey-Cacheda, and Francisco J. González-Castaño Abstract—This paper addresses the modeling of specificSmart Grid (SG) communication requirements from a data networking research perspective, as a general approach to the study of dif- ferent access technologies suitable for the last mile (LM). SGLM networks serve customers’ Energy Services Interfaces. From functional descriptions of SG, a traffic model is developed. It is then applied to the study of an access architecture based on leased lines from local broadband access providers. This permits con- sideration of the potential starvation of domestic traffic, which is avoided by applying well-known traffic management techniques. From previous results obtained for a purpose-built WiMAX Fig. 1. A wired ISP access network carries SGLM data. SGLM network, the intuition that a leased broadband access yields lower latencies is verified. In general, the proposed traffic Even though communications architectures connecting model simplifies the design of benchmarks for the comparison of candidate access technologies. households to the SG are usually called Advanced Metering Interfaces (AMI), we prefer to refer to them as Last-Mile net- Index Terms—Communication systems traffic control, diff- works to emphasize that meter reading is simply one possible serv networks, quality of service, smart grids, subscriber loops, WiMAX. application. For instance, AMIs and Distribution Automation Systems (DAS) may coexist in these architectures [5]. In a recent work [6] we assessed the viability of WiMAX for I. -
A Proposal for a Bluetooth Low Energy (BLE) Autoconfigurable Mesh Network Routing Protocol Based on Proactive Source Routing / Julio Humberto León Ruiz
UNIVERSIDADE ESTADUAL DE CAMPINAS Faculdade de Engenharia Elétrica e de Computação Julio Humberto León Ruiz A proposal for a Bluetooth Low Energy (BLE) autoconfigurable mesh network routing protocol based on Proactive Source Routing (Proposta de um protocolo de roteamento autoconfigurável para redes mesh em Bluetooth Low Energy (BLE) baseado em Proactive Source Routing) Campinas 2016 UNIVERSIDADE ESTADUAL DE CAMPINAS Faculdade de Engenharia Elétrica e de Computação Julio Humberto León Ruiz A proposal for a Bluetooth Low Energy (BLE) autoconfigurable mesh network routing protocol based on Proactive Source Routing (Proposta de um protocolo de roteamento autoconfigurável para redes mesh em Bluetooth Low Energy (BLE) baseado em Proactive Source Routing) Thesis presented to the School of Electrical and Computer Engineering of the Univer- sity of Campinas in partial fulfilment of the requirements for the degree of Doctor, in the area of Telecommunications and Telematics. Tese apresentada à Faculdade de Engen- haria Elétrica e Computação da Universi- dade Estadual de Campinas como parte dos requisitos exigidos para a obtenção do título de Doutor em Engenharia Elétrica na área de Telecomunicações e Telemática. Supervisor: Prof. Dr. Yuzo Iano ESTE EXEMPLAR CORRESPONDE À VER- SÃO FINAL DA TESE DEFENDIDA PELO ALUNO JULIO HUMBERTO LEÓN RUIZ, E ORIENTADA PELO PROF.DR.YUZO IANO Campinas 2016 Agência(s) de fomento e nº(s) de processo(s): CAPES Ficha catalográfica Universidade Estadual de Campinas Biblioteca da Área de Engenharia e Arquitetura Rose Meire da Silva - CRB 8/5974 León Ruiz, Julio Humberto, 1985- L553p Le_A proposal for a Bluetooth Low Energy (BLE) autoconfigurable mesh network routing protocol based on proactive source routing / Julio Humberto León Ruiz. -
Redalyc.Efficient Hardware Implementation of a Full COFDM
Revista Facultad de Ingeniería Universidad de Antioquia ISSN: 0120-6230 [email protected] Universidad de Antioquia Colombia López Parrado, Alexander; Velasco Medina, Jaime; Ramírez Gutiérrez, Julián Adolfo Efficient hardware implementation of a full COFDM processor with robust channel equalization and reduced power consumption Revista Facultad de Ingeniería Universidad de Antioquia, núm. 68, febrero-septiembre, 2013, pp. 48- 60 Universidad de Antioquia Medellín, Colombia Available in: http://www.redalyc.org/articulo.oa?id=43029811005 How to cite Complete issue Scientific Information System More information about this article Network of Scientific Journals from Latin America, the Caribbean, Spain and Portugal Journal's homepage in redalyc.org Non-profit academic project, developed under the open access initiative Rev. Fac. Ing. Univ. Antioquia N.° 68 pp. 48-60. Septiembre, 2013 Efficient hardware implementation of a full COFDM processor with robust channel equalization and reduced power consumption Implementación eficiente en hardware de un procesador COFDM completo con ecualización de canal robusta y reducción de consumo de potencia Alexander López Parrado*1,2, Jaime Velasco Medina1, Julián Adolfo Ramírez Gutiérrez2 1Bionanoelectronics Research Group, Universidad del Valle. Edificio 354, Espacio 1011, Ciudad Universitaria Meléndez. Calle 13 No 100-00. C. P. 760033. Santiago de Cali, Colombia. 2GDSPROC Research Group, Bloque de Ingeniería, Tercer Piso, CEIFI. Universidad del Quindío. Carrera 15 Calle 12 Norte. C. P. 630004. Armenia, Colombia. (Recibido el 29 de enero de 2013. Aceptado el 5 de agosto de 2013) Abstract This work presents the design of a 12 Mb/s Coded Orthogonal Frequency Division Multiplexing (COFDM) baseband processor for the standard IEEE 802.11a. -
Digitalization of the Electricity System and Customer Participation
DIGITALIZATION OF THE ELECTRICITY SYSTEM AND CUSTOMER PARTICIPATION Technical Position Paper WG4 DIGITALIZATION OF THE ELECTRICITY SYSTEM AND CUSTOMER PARTICIPATION Photo Alliander (Hans Peter van Velthoven) POSITION PAPER “Digitalization of the Electricity System and Customer Participation” description and recommendations of Technologies, Use Cases and Cybersecurity” ETIP SNET - WG4 September 2018 3 / 174 DIGITALIZATION OF THE ELECTRICITY SYSTEM AND CUSTOMER PARTICIPATION Authors: Working group 4 members from businesses, knowledge institutes, universities, governmental and public organisations. Authors are listed per chapter. Taskforce 1: Antonello Monti, George Huitema, Moamar Sayed-Mouchawe, Aitor Amezua, Liam Beard, Theo Borst, Miguel Carvalho, Angel Conde, Aris Dimeas, Guilaume Giraud, Hengxu Ha, Ludwig Karg, Georges Kariniotakis, Antonio Moreno- Munoz, Peter Nemcek, Eric Suignard, Arjan Wargers Taskforce 2: Elena Boskov-Kovacs, Esther Hardi, Norela Constantinescu, Daniel Mugnier, Asier Moltó, Miguel Carvalho, Sandra Riaño, Henric Larsson, Pierre Serkine, Gerhard Kleineidam, Marco-Robert Schulz, Jan Pedersen, Christian Lechner Taskforce 3: Marcus Meisel, Rolf Apel, Jeff Montagne, Miguel Angel Sanchez Fornie, Bruno Miguel Soares, Manolis Vavalis, Liliana Ribeiro, Arjan Wargers, Moamar-Sayed Mouchaweh, Antonello Monti, and Maher Chebbo Quality check: ETIP SNET EXCo Delivery date: September 2018 DIGITALIZATION OF THE ELECTRICITY SYSTEM AND CUSTOMER PARTICIPATION About ETIP-SNET Find out more at: https://www.etip-snet.eu. European Technology -
IEEE P1905.1 Convergent Digital Home Network Technical Presentation
IEEE P1905.1 Convergent Digital Home Network Technical Presentation 802.1 Plenary Meeting San Diego, CA Jul 2012 Contributed by Philippe Klein PhD, Broadcom [email protected] 802-1-phkl-P1095-Tech-Presentation-1207-v01.pdf Home Networking Requirements (1/2) • Different connectivity technologies are deployed in homes, each with its own advantages and impairments • The Need for Convergence and Abstraction – Ubiquitous Coverage Combining multiple connectivity technologies improves the home coverage. – Ease of installation Simplified security setup unifies the specific security setup method of each technology. Jul 2012 IEEE P1905.1 Technical Presentation - IEEE 802.1 Plenary, San Diego CA 3 Home Networking Requirements (2/2) – High Throughput Load sharing over multiple concurrent paths amalgamates the bandwidth offered by the whole home network topology. – Reliability Directing traffic through another path could lower transmission error rates. Sending some critical traffic on multiple paths and removing duplicates at the receiving end could improve reliability. – Management Local and Remote diagnostics allow to identify network configuration issues. Jul 2012 IEEE P1905.1 Technical Presentation - IEEE 802.1 Plenary, San Diego CA 4 P1905.1 Key Features • Topology Discovery (to help identify bottlenecks & mis‐ configuration) • Diagnostics (both locally and thru WAN accessible TR‐069 data model) • Simplified security setup (common method) • Automatic configuration of secondary Wi‐Fi Access Point(s) • Enabler for enhanced path selection (link metrics information) • Enabler for enhanced power management (by optimizing network power usage across different technologies) Jul 2012 IEEE P1905.1 Technical Presentation - IEEE 802.1 Plenary, San Diego CA 5 P1905.1 is not a replacement … ... for Wi‐Fi, Ethernet, MoCA, HomePlug, and other home network technologies .. -
Competency Models
SCIENCE, TECHNOLOGY, ENGINEERING & MATHEMATICS Architectural and Engineering Managers ACCCP Engineering and Technology Alabama Competency Model Architectural and Engineering Managers Code 1 Tier 1: Personal Effectiveness Competencies 1.1 Interpersonal Skills: Displaying the skills to work effectively with others from diverse backgrounds. 1.1.1 Demonstrating sensitivity/empathy 1.1.1.1 Show sincere interest in others and their concerns. 1.1.1.2 Demonstrate sensitivity to the needs and feelings of others. 1.1.1.3 Look for ways to help people and deliver assistance. 1.1.2 Demonstrating insight into behavior Recognize and accurately interpret the communications of others as expressed through various 1.1.2.1 formats (e.g., writing, speech, American Sign Language, computers, etc.). 1.1.2.2 Recognize when relationships with others are strained. 1.1.2.3 Show understanding of others’ behaviors and motives by demonstrating appropriate responses. 1.1.2.4 Demonstrate flexibility for change based on the ideas and actions of others. 1.1.3 Maintaining open relationships 1.1.3.1 Maintain open lines of communication with others. 1.1.3.2 Encourage others to share problems and successes. 1.1.3.3 Establish a high degree of trust and credibility with others. 1.1.4 Respecting diversity 1.1.4.1 Demonstrate respect for coworkers, colleagues, and customers. Interact respectfully and cooperatively with others who are of a different race, culture, or age, or 1.1.4.2 have different abilities, gender, or sexual orientation. Demonstrate sensitivity, flexibility, and open-mindedness when dealing with different values, 1.1.4.3 beliefs, perspectives, customs, or opinions. -
IEEE Std 1905.1TM-2013, IEEE Standard for a Convergent Digital
IEEE Standard for a Convergent Digital Home Network for Heterogeneous Technologies IEEE Communications Society Sponsored by the Power Line Communications Standards Committee IEEE 3 Park Avenue IEEE Std 1905.1™-2013 New York, NY 10016-5997 USA 12 April 2013 IEEE Std 1905.1TM-2013 IEEE Standard for a Convergent Digital Home Network for Heterogeneous Technologies Sponsor Power Line Communications Standards Committee of the IEEE Communications Society Approved 6 March 2013 IEEE-SA Standards Board Abstract: An abstraction layer for multiple home networking technologies that provides a common interface to widely deployed home networking technologies is defined in this standard: IEEE 1901 over power lines, IEEE 802.11 for wireless, Ethernet over twisted pair cable, and MoCA 1.1 over coax. Connectivity selection for transmission of packets arriving from any interface or application is supported by the 1905.1 abstraction layer. Modification to the underlying home networking technologies is not required by the 1905.1 layer, and hence it does not change the behavior or implementation of existing home networking technologies. Introduced by the 1905.1 specification is a layer between layers 2 and 3 that abstracts the individual details of each interface, aggregates available bandwidth, and facilitates seamless integration. The 1905.1 also facilitates end-to-end quality of service (QoS) while simplifying the introduction of new devices to the network, establishing secure connections, extending network coverage, and facilitating advanced network management features including discovery, path selection, autoconfiguration, and quality of service (QoS) negotiation. Keywords: abstraction layer, access point (AP) autoconfiguration, data models, fragmentation and reassembly, IEEE 802.1 bridge discovery, IEEE 802.11TM, IEEE 1901TM, IEEE 1905.1TM, MoCA, pairwise master key, push button, registration, security, topology discovery protocol, wireless fidelity (Wi-Fi) • The Institute of Electrical and Electronics Engineers, Inc. -
Power Line Communication: Powering Video Surveillance Infrastructure
C M Y K Power Line Communication: Powering Video Surveillance Infrastructure By Anees Ahmed – Chairman & Co-Founder, Mistral Solutions Pvt. Ltd. Introduction he choice between Tdistance and band- width, for a given budget, is one users and vendors constantly battle over when defining requirements and delivering solutions in vid- eo surveillance projects. Users would like the high- est resolution video feeds delivered at their consoles at a price-point of a low bandwidth pipe: an expec- tation vendors struggle to meet. In fixed video surveil- lance infrastructure projects, vendors do have some Figure 1: Power Line Communication (PLC) concept in a home, Credit: HD-PLC Alliance, www.hd-plc.org breathing space; afforded by the ability to lay new wiring at will (in most cases). In the What is Power Line Communication? case of temporary video surveillance infrastructure (or fixed ower Line Communication (PLC), or Broadband over infrastructure where laying new cables is not possible), though, PPowerline (BPL) or Powerline Networking (PLN), is this breathing space is reduced by the operational constraints a concept that describes using electric power transmis- in laying cable. sion lines to carry data. The data can be carried within the This brief will describe the concept of power line com- power transmission network in a house or a premises, or munication, and compare the technology to other alternatives between the premises and the power distribution network. such as wireless networking and PoE, especially when setting PLC can be used for setting up a LAN (as a replacement or up temporary video surveillance local networks. complement to a traditional Ethernet or Wi-fi LAN) or for April 2012 32 www.indiasafe.com C M Y K C M Y K establishing a data connection between an intelligent edge effective data rate of 80 Mbps. -
Overview of Broadband Powerline Communications
January 23, 2015 Overview of broadband powerline communications Jean-Philippe Faure, CEO Progilon Senior consultant at Panasonic System Networks Director Technology Standards at HD-PLC Alliance Biography of Mr Jean-Philippe Faure Founder and CEO of Progilon, consultancy company operating in the Power Line Communications sector since 1994 IEEE activities ! Founding Chair of the IEEE P1901 working group, representing Panasonic (since 2005) ! Member of the IEEE-SA Standards Board (since 2011) ! Chair of the IEEE ComSoc PLC Standards Committee (since 2012) ! Member of the IEEE ComSoc Standards Development Board (since 2010) Other activities ! Founding Chair of the IEC-CISPR group on EMC for BPL (2005-2010) ! Member of CENELEC and ETSI committees ! Consultant for the European Commission: evaluator and reviewer of R&D projects ! Leading positions in collaborative R&D projects 2 Agenda Powerline Communications ! IEEE Standards ! Smart applications (courtesy of the HD-PLC Alliance www.hd-plc.org) 3 Agenda Powerline Communications ! IEEE Standards ! Smart applications (courtesy of the HD-PLC Alliance www.hd-plc.org) 4 5 IEEE PLC Standards Committee Implementation IEEE 2030 : Guide for Smart Grid IEEE 1909.1 : Recommended Interoperability Practice for Smart Grid Communication Equipment Pioneer Standard Applications IEEE 1901 IEEE 1901.2 : Low Frequency/ Narrow Band Broadband over Power PLC for Smart Grid Applications Line MAC/PHY Layers Wide scope Integration •" In-home •" Access IEEE 1905.1 : Convergent Digital Home •" Smart Grid Network for Heterogeneous -
Report by Stratix and TU/E Optical Wireless Communication: Options for Extended Spectrum Use
Report by Stratix and TU/e Optical Wireless Communication: options for extended spectrum use Report commissioned by the Dutch Radio Communications Agency (Agentschap Telecom) Ministry of Economic Affairs and Climate policy Hilversum, 24 December 2017 EPORT R AUTHORS: Ir. Sietse van der Gaast, Henny Xu MSc. (Stratix); Prof. Ir. Ton Koonen, Dr. Ir. Eduward Tangdiongga (Eindhoven University of Technology) CONTRIBUTORS AND REVIEWERS Drs. Rudolf van der Berg, Ir. Paul Brand, Melanie van Cruijsen (Stratix) © Stratix 2017 Optical Wireless Communication: options for extended spectrum use 2 Management summary Optical Wireless Communication (OWC) may be an important alternative option that could ease the pressure on the radio spectrum that is now in use for communications. This report, commis- sioned by the Dutch Radiocommunications Agency gives an overview of current OWC technolo- gies, trends and potentials. The Dutch Radiocommunications Agency aims to contribute these findings to ITU and CEPT. The report primarily focuses on broadband communication for indoor use. There are several OWC technologies that offer a promising solution for indoor wireless broad- band communication over a distance up to a few meters. Potentially OWC is suitable for very high bandwidth communication over these distances. OWC can exploit an enormous amount of yet unregulated spectrum (2600x the size of currently available radio spectrum) and can reuse this huge spectrum easily by spatial multiplexing, because the signal range is limited and in most cases confined to a room. Two main OWC variants can be distinguished: Visible Light Communication and Beam Steered Infrared Light Communication. Visible Light Communication (VLC) typically builds on the existing light-emitting diode (LED) ambient illumination system, and reuses the LEDs for data modulation.