Features of the High Field Magnet Laboratory at The
Total Page:16
File Type:pdf, Size:1020Kb
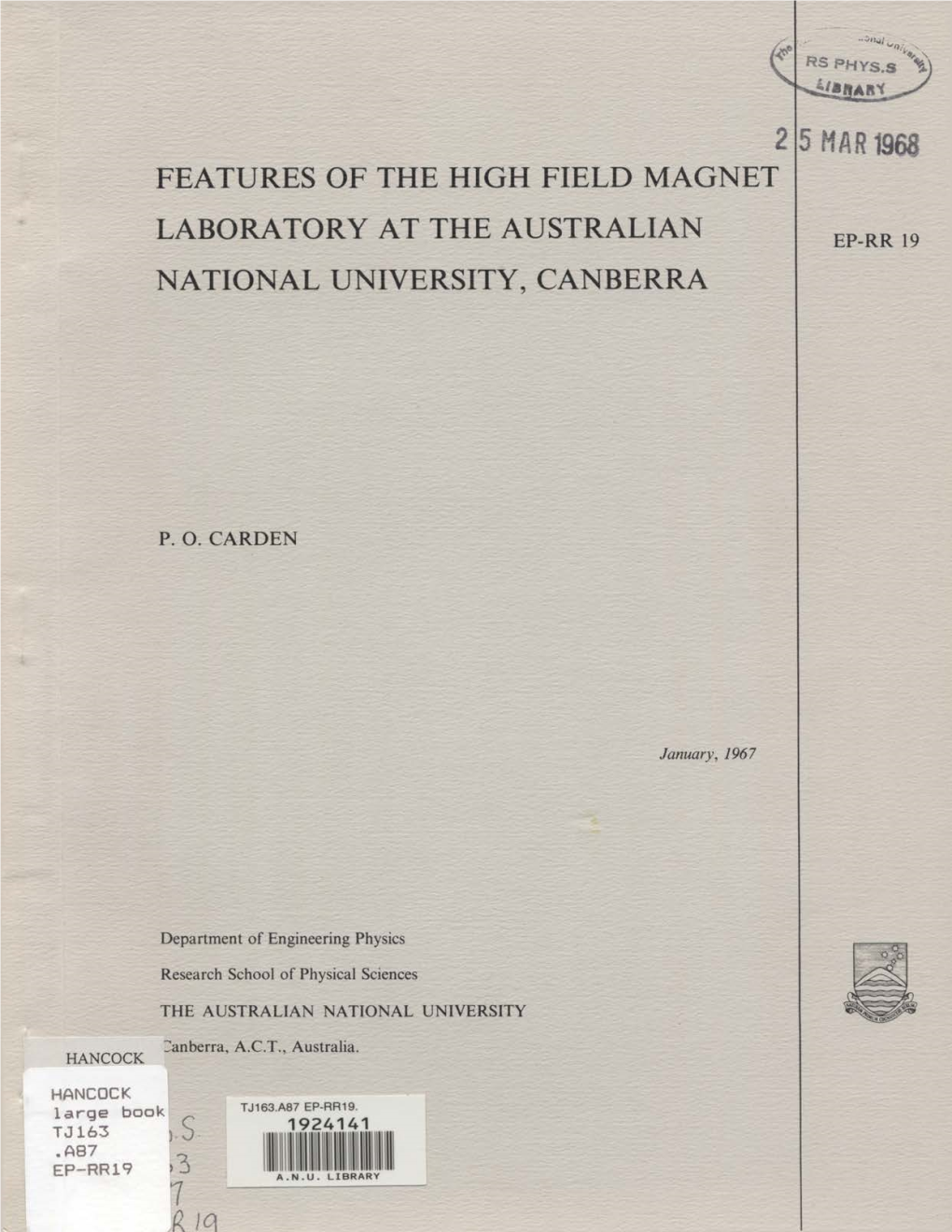
Load more
Recommended publications
-
N O T I C E This Document Has Been Reproduced From
N O T I C E THIS DOCUMENT HAS BEEN REPRODUCED FROM MICROFICHE. ALTHOUGH IT IS RECOGNIZED THAT CERTAIN PORTIONS ARE ILLEGIBLE, IT IS BEING RELEASED IN THE INTEREST OF MAKING AVAILABLE AS MUCH INFORMATION AS POSSIBLE gg50- y-^ 3 (NASA-CH-163584) A STUDY OF TdE N80 -32856 APPLICABILITY/COMPATIbIL1TY OF INERTIAL ENERGY STURAGE SYSTEMS TU FU'IUAE SPACE MISSIONS Firnal C.eport (Texas Univ.) 139 p Unclas HC A07/MF AJ1 CSCL 10C G3/44 28665 CENTER FOR ELECTROMECHANICS OLD ^ l ^:' ^sA sit ^AC^utY OEM a^ 7//oo^6^^, THE UNIVERSITY OF TEXT COLLEGE OF ENGINEERING TAYLOR NAIL 167 AUSTIN, TEXAS, 71712 512/471-4496 4l3 Final Report for A Study of the Applicability/Compatibility of Inertial Energy Storage Systems to Future Space Missions Jet Propulsion Laboratory ... Contract No. 955619 This work was {performed for the Jet Propulsion Laboratory, California Institute of Technology Sponsored by The National Aeronautics and Space Administration under Contract NAS7-100 by William F. Weldon r Technical Director Center for Electromechanics The University of Texas at Austin Taylor Hall 167 Austin, Texas 18712 (512) 471-4496 August, 1980 t c This document contains information prepared by the Center for Electromechanics of The University of Texas at Austin under JPL sub- contract. Its content is not necessarily endorsed by the Jet Propulsion Laboratory, California Institute of Technology, or its sponsors. QpIrS r^r^..++r•^vT.+... .. ...^r..e.^^..^..-.^...^^.-Tw—.mss--rn ^s^w . ^A^^v^T'^'1^^w'aw^.^^'^.R!^'^rT-.. _ ..,^.wa^^.-.-.^.w r^.-,- www^w^^ -- r f Si i ABSTRACT The applicability/compatibility of inertial energy storage systems, i.e. -
Arxiv:1701.07063V2 [Physics.Ins-Det] 23 Mar 2017 ACCEPTED by IEEE TRANSACTIONS on PLASMA SCIENCE, MARCH 2017 1
This work has been accepted for publication by IEEE Transactions on Plasma Science. The published version of the paper will be available online at http://ieeexplore.ieee.org. It can be accessed by using the following Digital Object Identifier: 10.1109/TPS.2017.2686648. c 2017 IEEE. Personal use of this material is permitted. Permission from IEEE must be obtained for all other uses, including reprinting/republishing this material for advertising or promotional purposes, collecting new collected works for resale or redistribution to servers or lists, or reuse of any copyrighted component of this work in other works. arXiv:1701.07063v2 [physics.ins-det] 23 Mar 2017 ACCEPTED BY IEEE TRANSACTIONS ON PLASMA SCIENCE, MARCH 2017 1 Review of Inductive Pulsed Power Generators for Railguns Oliver Liebfried Abstract—This literature review addresses inductive pulsed the inductor. Therefore, a coil can be regarded as a pressure power generators and their major components. Different induc- vessel with the magnetic field B as a pressurized medium. tive storage designs like solenoids, toroids and force-balanced The corresponding pressure p is related by p = 1 B2 to the coils are briefly presented and their advantages and disadvan- 2µ tages are mentioned. Special emphasis is given to inductive circuit magnetic field B with the permeability µ. The energy density topologies which have been investigated in railgun research such of the inductor is directly linked to the magnetic field and as the XRAM, meat grinder or pulse transformer topologies. One therefore, its maximum depends on the tensile strength of the section deals with opening switches as they are indispensable for windings and the mechanical support. -
Modelling and Simulation of a Simple Homopolar Motor of Faraday's Type
FACTA UNIVERSITATIS (NIS)ˇ SER.: ELEC. ENERG. vol. 24, no. 2, August 2011, 221-242 Modelling and Simulation of a Simple Homopolar Motor of Faraday's Type Dedicated to Professor Slavoljub Aleksic´ on the occasion of his 60th birthday Hartmut Brauer, Marek Ziolkowski, Konstantin Porzig, and Hannes Toepfer Abstract: During the application of simulation tools of computational electromag- netics it is sometimes difficult to decide whether the problems can be solved by the computation of electromagnetic fields or circuit simulation tools have to be applied ad- ditionally. The paper describes a typical situation in an electromagnetic CAD course, not only for beginners. The modelling and numerical simulation of a simple homopo- lar motor, similar to that what has been presented by Michael Faraday in 1821 firstly, was used as an example. To simulate the current flow in the permanent magnet the FEM software codes COMSOL Multiphysics including the integrated SPICE module and MAXWELL have been used. The correct simulation of the entire electric circuit as well as the precise modelling of the impressed current and of the electrode contacts turned out to be very important. Keywords: Homopolar motor; homopolar generator; Faraday’s motor principle; FEM software. 1 Introduction S is so often the case with invention, the credit for development of the elec- A tric motor is belongs to more than one individual. It was through a process of development and discovery beginning with Hans Christian Oersted’s discovery of electromagnetism in 1820 and involving additional work by William Sturgeon, Manuscript received on June 8. 2011. The authors are with Ilmenau University of Technology, Faculty of Electrical Engineer- ing and Information Technology, Dept. -
Inexpensive Inertial Energy Storage Utilizing Homopolar Motor- Generators
Missouri University of Science and Technology Scholars' Mine UMR-MEC Conference on Energy 09 Oct 1975 Inexpensive Inertial Energy Storage Utilizing Homopolar Motor- Generators W. F. Weldon H. H. Woodson H. G. Rylander M. D. Driga Follow this and additional works at: https://scholarsmine.mst.edu/umr-mec Part of the Electrical and Computer Engineering Commons, Mechanical Engineering Commons, Mining Engineering Commons, Nuclear Engineering Commons, and the Petroleum Engineering Commons Recommended Citation Weldon, W. F.; Woodson, H. H.; Rylander, H. G.; and Driga, M. D., "Inexpensive Inertial Energy Storage Utilizing Homopolar Motor-Generators" (1975). UMR-MEC Conference on Energy. 88. https://scholarsmine.mst.edu/umr-mec/88 This Article - Conference proceedings is brought to you for free and open access by Scholars' Mine. It has been accepted for inclusion in UMR-MEC Conference on Energy by an authorized administrator of Scholars' Mine. This work is protected by U. S. Copyright Law. Unauthorized use including reproduction for redistribution requires the permission of the copyright holder. For more information, please contact [email protected]. INEXPENSIVE INERTIAL ENERGY STORAGE UTILIZING HOMOPOLAR MOTOR-GENERATORS W.F. Weldon, H.H. Woodson, H.G. Rylander, M.D. Driga Energy Storage Group 167 Taylor Hall The University of Texas at Austin Austin, Texas 78712 Abstract The pulsed power demands of the current generation of controlled thermonuclear fusion experiments have prompted a great interest in reliable, low cost, pulsed power systems. The Energy Storage Group at the University of Texas at Austin was created in response to this need and has worked for the past three years in developing inertial energy storage systems. -
Electrification and the Ideological Origins of Energy
A Dissertation entitled “Keep Your Dirty Lights On:” Electrification and the Ideological Origins of Energy Exceptionalism in American Society by Daniel A. French Submitted to the Graduate Faculty as partial fulfillment of the requirements for the Doctor of Philosophy Degree in History _________________________________________ Dr. Diane F. Britton, Committee Chairperson _________________________________________ Dr. Peter Linebaugh, Committee Member _________________________________________ Dr. Daryl Moorhead, Committee Member _________________________________________ Dr. Kim E. Nielsen, Committee Member _________________________________________ Dr. Patricia Komuniecki Dean College of Graduate Studies The University of Toledo December 2014 Copyright 2014, Daniel A. French This document is copyrighted material. Under copyright law, no parts of this document may be reproduced without the express permission of the author. An Abstract of “Keep Your Dirty Lights On:” Electrification and the Ideological Origins of Energy Exceptionalism in American Society by Daniel A. French Submitted to the Graduate Faculty as partial fulfillment of the requirements for the Doctor of Philosophy Degree in History The University of Toledo December 2014 Electricity has been defined by American society as a modern and clean form of energy since it came into practical use at the end of the nineteenth century, yet no comprehensive study exists which examines the roots of these definitions. This dissertation considers the social meanings of electricity as an energy technology that became adopted between the mid- nineteenth and early decades of the twentieth centuries. Arguing that both technical and cultural factors played a role, this study shows how electricity became an abstracted form of energy in the minds of Americans. As technological advancements allowed for an increasing physical distance between power generation and power consumption, the commodity of electricity became consciously detached from the steam and coal that produced it. -
130 Electrical Energy Innovations
130 Electrical Energy Innovations Gary Vesperman (Author) Advisor to Sky Train Corporation www.skytraincorp.com 588 Lake Huron Lane Boulder City, NV 89005-1018 702-435-7947 [email protected] www.padrak.com/vesperman TABLE OF CONTENTS Title Page INTRODUCTION ............................................................................................................. 1 BRIEF SUMMARIES ....................................................................................................... 2 LARGE GENERATORS ............................................................................................... 13 Hydro-Magnetic Dynamo ............................................................................................ 13 Focus Fusion ............................................................................................................... 19 BlackLight Power’s Hydrino Generator ..................................................................... 19 IPMS Thorium Energy Accumulator .......................................................................... 22 Thorium Power Pack ................................................................................................... 22 Magneto-Gravitational Converter (Searl Effect Generator) ..................................... 23 Davis Tidal Turbine ..................................................................................................... 25 Magnatron – Light-Activated Cold Fusion Magnetic Motor ..................................... 26 Wireless Power and Free Energy from Ambient -
Parameter Study of an Inductively Powered Railgun Oliver Liebfried, Paul Frings
18TH INTERNATIONAL SYMPOSIUM ON ELECTROMAGNETIC LAUNCH TECHNOLOGY, OCTOBER 24-28, WUHAN, CHINA 1 Parameter study of an inductively powered railgun Oliver Liebfried, Paul Frings Abstract—This article deals with the numerical simulation parameter optimization. Richard T. Meyer et al. maximize of an inductively powered railgun in order to determine the efficiency for a given railgun system in dependance of a electrical parameters of the inductive storage of the pulsed variable muzzle velocity by means of variable charging voltage power supply. A numerical model was set up and validated by experimental results. A parameter sweep was performed by and trigger times of a given capacitive pulse forming network. varying the time constant of the coil, the initial current and The optimization was performed by using MATLAB’s fmin- the initially stored energy. The results show that the generated con function [8]. Hundertmark et al. simulated a capacitive pulse shape, and thus the transfer efficiency and electromagnetic power supply for the same railgun artillery scenario as used forces, strongly depend on the inductance of the storage coil. On in this paper [9]. A Pspice circuit to determine the size and the contrary, the dependency on the coil time constant, and thus on the coil volume for a given coil shape and conductor material, trigger times of the PFN was used. The influence of the is small and can be neglected for high time constants. series resistance of the current conducting path on the railgun performance was shown. Many more paper are dealing with the parameter opti- I. INTRODUCTION mization of railgun systems. -
Projectile 45
4%.* A FEASIBILITY STUDY OF A HYPERSONIC REAL-GAS FACILITY FINAL REPORT Submitted To: Grants Officer NASA Langley Research Center Office of Grants and University Affairs Hampton, VA 23665 Grant d NAG1-721 January 1, 1987 to May 31, 1987 Submitted by: J. H. Gully Co-principal Investigator M. D. Driga Co-principal Investigator W. F. Weldon Co-principal Investigator (NBSA-CR-180423) A FEASIBILITY STUDY OF A N88-10043 HYPEBSOUIC RBAL-SAS FACILITY Final Report (Texas tJniv.1 154 p Avail: NTIS AC A08/tlP A01 CSCL 14s Uacl as G3/09 0 103727 Center for Electromechanico The University of Texas at Austin Balcones Research Center EME 1.100, Building 133 Austin, TX 78758-4497 (512)471-4496 CONTENTS Page INTRODUCTION 1 Discu ssion 2 HIGH ENERGY LAUNCHER FOR BALLISTIC RANGE 5 Introduction 5 Launch Concepts and Theory 6 COAXIAL ACCELERATOR 9 Introduction 9 System Description 10 System Analysis 13 Main Parameters 13 Launcher Configurations 15 Electromechanical Considerations 17 Power Supplies 22 Electromagnetic Principles 25 STATOR WINDING DESIGN 31 Starter Coil (Secondary Current Initiation) 35 Power Supply Characteristics 41 Projectile 45 RAILGUN ACCELERATOR 50 Introduction 50 Background 50 Railgun Construction 53 Synchronous Switching of Energy Store 58 Initial Acceleration 58 Method for Decelerating Sabot 60 Power Source 60 Inductor Design 69 Railgun Performance 75 Sa bot De sign 75 Plasma Bearings 78 Armature Consideration 80 Maintenance 82 Model Design 82 INSTRUMENTATION 84 Electromagnetic Launch Model Electronics 84 Data Acquisition 85 Circuit -
Energy Conservation and Poynting&Apos;S Theorem in the Homopolar Generator
Energy conservation and Poynting's theorem in the homopolar generator Christopher F. Chyba, Kevin P. Hand, and Paul J. Thomas Citation: American Journal of Physics 83, 72 (2015); doi: 10.1119/1.4895389 View online: http://dx.doi.org/10.1119/1.4895389 View Table of Contents: http://scitation.aip.org/content/aapt/journal/ajp/83/1?ver=pdfcov Published by the American Association of Physics Teachers Articles you may be interested in Energy Blocks — A Physical Model for Teaching Energy Concepts Phys. Teach. 54, 31 (2016); 10.1119/1.4937969 Interference and the Law of Energy Conservation Phys. Teach. 52, 428 (2014); 10.1119/1.4895362 • Energy Conservation, Energy Literacy and the DoE eere.energy.gov/education/energy_literacy.html Phys. Teach. 51, 446 (2013); 10.1119/1.4820873 Conserving energy in physics and society: Creating an integrated model of energy and the second law of thermodynamics AIP Conf. Proc. 1513, 114 (2013); 10.1063/1.4789665 Energy conservation Phys. Teach. 49, 520 (2011); 10.1119/1.3651743 This article is copyrighted as indicated in the article. Reuse of AAPT content is subject to the terms at: http://scitation.aip.org/termsconditions. Downloaded to IP: 128.112.200.107 On: Sun, 24 Apr 2016 00:14:33 Energy conservation and Poynting’s theorem in the homopolar generator Christopher F. Chybaa) Department of Astrophysical Sciences and Woodrow Wilson School of Public and International Affairs, Princeton University, Princeton, New Jersey 08544 Kevin P. Handb) Jet Propulsion Laboratory, California Institute of Technology, Pasadena, California 91109 Paul J. Thomasc) Department of Physics and Astronomy, University of Wisconsin, Eau Claire, Wisconsin 54702 (Received 13 February 2013; accepted 27 August 2014) Most familiar applications of Poynting’s theorem concern stationary circuits or circuit elements. -
The Homopolar Generator: an Analytical Example
The homopolar generator: an analytical example Hendrik van Hees August 7, 2014 1 Introduction It is surprising that the homopolar generator, invented in one of Faraday’s ingenious experiments in 1831, still seems to create confusion in the teaching of classical electrodynamics. This is the more surprising as the problem of the “electromagnetism of moving bodies” has been solved more than 100 years ago by Einstein in his famous paper, introducing his Special Theory of relativity (1905), and mathematically consolidated by Minkowski hin his famous talk on space and time (1908). Also one can still find some misleading, if not even wrong, statements on the issue in the more re- cent literature, and I could not find any paper using the local (differential) Maxwell equations and the Lorentz-force Law which is always valid, as suggested in the Feynman Lectures (vol. II) in connection ~ ~ ~ with the use of Faraday’s flux law (the integral form of one of the Maxwell equations, E = @t B=c, see App. A). r× − Here, I try to provide precisely such a study for the most simple arrangement showing the effects, namely the rotating homogeneously magnetized sphere. 2 The one-piece Faraday generator It is surprising that the so-called Faraday paradox is still a source of confusion although the “electrody- namics of moving bodies” is well understood with Einstein’s famous special-relativity paper. Here, I try to give an explanation by avoiding the use of the integral form of Maxwell’s equation, which seems to be the main source of the confusion. I’ll comment on this in Appendix A. -
Energy Conservation and Poynting's Theorem in the Homopolar Generator
Energy conservation and Poynting’s theorem in the homopolar generator Christopher F. Chybaa) Department of Astrophysical Sciences and Woodrow Wilson School of Public and International Affairs, Princeton University, Princeton, New Jersey 08544 Kevin P. Handb) Jet Propulsion Laboratory, California Institute of Technology, Pasadena, California 91109 Paul J. Thomasc) Department of Physics and Astronomy, University of Wisconsin, Eau Claire, Wisconsin 54702 (Received 13 February 2013; accepted 27 August 2014) Most familiar applications of Poynting’s theorem concern stationary circuits or circuit elements. Here, we apply Poynting’s theorem to the homopolar generator, a conductor moving in a background magnetic field. We show that the electrical power produced by the homopolar generator equals the power lost from the deceleration of the rotating Faraday disk due to magnetic braking and review the way that magnetic braking arises within Poynting’s theorem. VC 2015 American Association of Physics Teachers. [http://dx.doi.org/10.1119/1.4895389] I. INTRODUCTION from the deceleration of the rotating Faraday disk due to magnetic braking. We then review how this magnetic brak- 1 Poynting’s theorem for electric field E, magnetic flux ing arises within Poynting’s theorem. density B, and current density J follows from Maxwell’s equations (Faraday’s and Ampe`re’s laws) and the vector identity E ðrBÞ¼B ðrEÞrÁðE Â BÞ.2,3 The theorem states that the rate at which work is done on the II. POWER DISSIPATION IN THE HOMOPOLAR electrical charges within a volume is equal to the decrease in GENERATOR energy stored in the electric and magnetic fields, minus the The homopolar generator, or Faraday disk, produces an energy that flowed out through the surface bounding the vol- electromotance (emf) by rotating a conducting disk in a ume. -
A Synchronous Homopolar Machine for High-Speed Applications
A Synchronous Homopolar Machine for High-Speed Applications Perry Tsao, Matthew Senesky, and Seth Sanders Department of Electrical Engineering University of California, Berkeley Berkeley, CA 94720 www-power.eecs.berkeley.edu Abstract— The design, construction, and test of a high-speed TABLE I. MACHINE DESIGN PARAMETERS synchronous homopolar motor/alternator, and its associated high efficiency six-step inverter drive for a flywheel energy storage Power 30 kW system are presented in this paper. The work is presented as an RPM 50kRPM- 100kRPM integrated design of motor, drive, and controller. The Energy storage capacity 140 W.hr performance goal is for power output of 30 kW at speeds from 50 System mass 36 kg kRPM to 100 kRPM. The machine features low rotor losses, high Power density 833 W/kg efficiency, construction from robust and low cost materials, and a Energy density 3.9 W.hr/kg rotor that also serves as the energy storage rotor for the flywheel II. SYNCHRONOUS HOMOPOLAR MACHINE DESIGN system. The six-step inverter drive strategy maximizes inverter efficiency, and the sensorless controller works without position or A. Application Requirements flux estimation. A prototype of the flywheel system has been constructed, and experimental results for the system are High efficiency, low rotor losses, and a robust rotor presented. structure are the key requirements for the flywheel system’s motor/alternator. High efficiency is required over the entire Keywords—Homopolar machine; Flywheel energy storage; range of operation, in this case 50,000 to 100,000 RPM, with a Six-step drive; Sensorless control power rating of 30 kW.