Erosion Processes and Micro-Particle Production in Gas Discharge Lasers
Total Page:16
File Type:pdf, Size:1020Kb
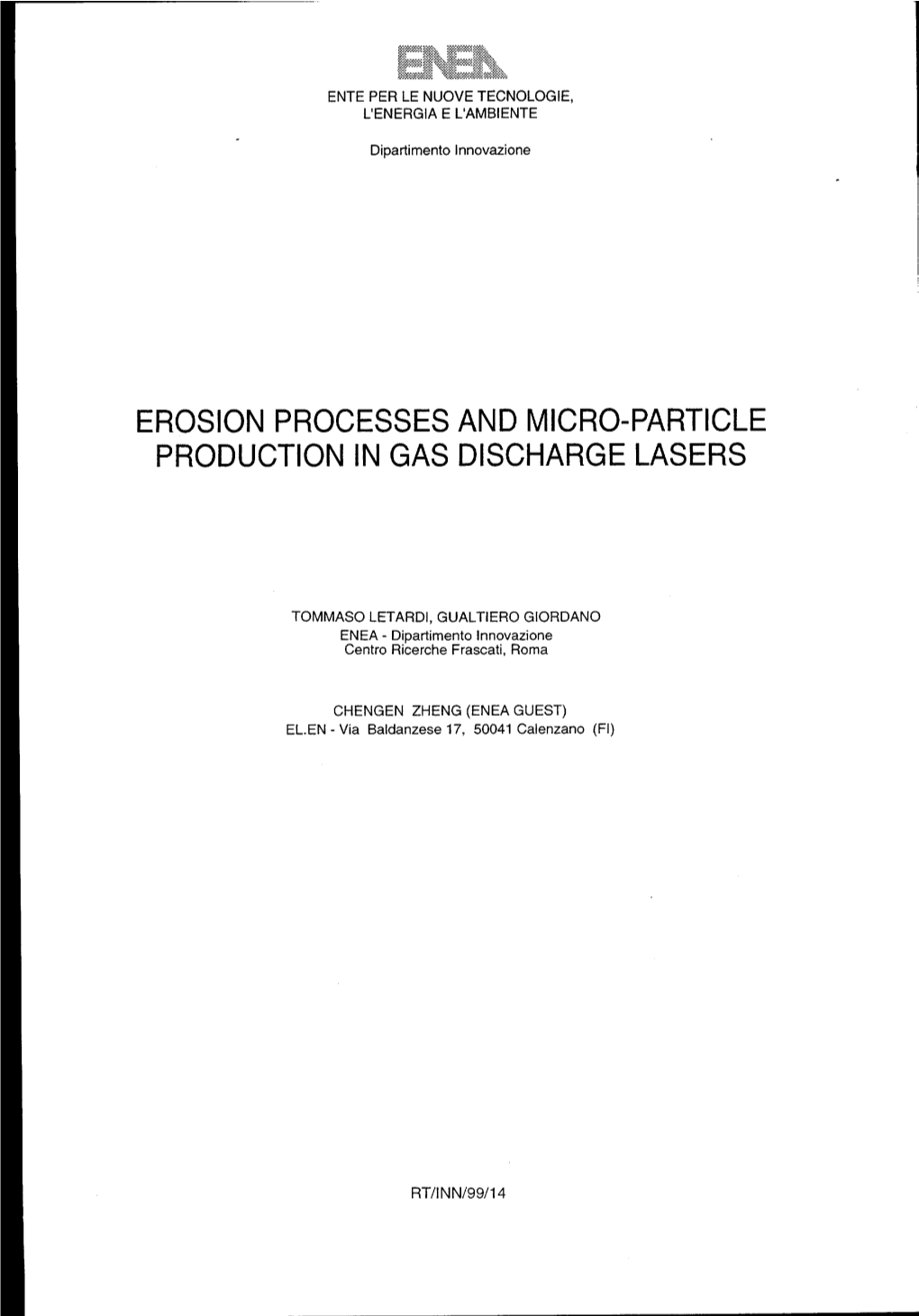
Load more
Recommended publications
-
An Application of the Theory of Laser to Nitrogen Laser Pumped Dye Laser
SD9900039 AN APPLICATION OF THE THEORY OF LASER TO NITROGEN LASER PUMPED DYE LASER FATIMA AHMED OSMAN A thesis submitted in partial fulfillment of the requirements for the degree of Master of Science in Physics. UNIVERSITY OF KHARTOUM FACULTY OF SCIENCE DEPARTMENT OF PHYSICS MARCH 1998 \ 3 0-44 In this thesis we gave a general discussion on lasers, reviewing some of are properties, types and applications. We also conducted an experiment where we obtained a dye laser pumped by nitrogen laser with a wave length of 337.1 nm and a power of 5 Mw. It was noticed that the produced radiation possesses ^ characteristic^ different from those of other types of laser. This' characteristics determine^ the tunability i.e. the possibility of choosing the appropriately required wave-length of radiation for various applications. DEDICATION TO MY BELOVED PARENTS AND MY SISTER NADI A ACKNOWLEDGEMENTS I would like to express my deep gratitude to my supervisor Dr. AH El Tahir Sharaf El-Din, for his continuous support and guidance. I am also grateful to Dr. Maui Hammed Shaded, for encouragement, and advice in using the computer. Thanks also go to Ustaz Akram Yousif Ibrahim for helping me while conducting the experimental part of the thesis, and to Ustaz Abaker Ali Abdalla, for advising me in several respects. I also thank my teachers in the Physics Department, of the Faculty of Science, University of Khartoum and my colleagues and co- workers at laser laboratory whose support and encouragement me created the right atmosphere of research for me. Finally I would like to thank my brother Salah Ahmed Osman, Mr. -
HD DVD: Manufacturing Was Developed.This Recorder Is Equipped with a 257Nm Gas Laser (Frequency Doubled Ar+ Laser)
paper r& white d Six years ago, the LDM 3692 DUV recorder HD DVD: Manufacturing was developed.This recorder is equipped with a 257nm gas laser (frequency doubled Ar+ laser). All options with regards to future for- mats were still open at that time.The recorder features two recording spots, with a wobble The New Format option on both. This recorder is an adequate R&D tool to record HD DVD. BY DR. DICK VERHAART, from 740nm to 400nm. To read these smaller For HD DVD stamper manufacturing, a Singulus Mastering information structures, it is necessary to use recorder with a 266nm solid state laser was PETER KNIPS, blue diode lasers with a wavelength of 405nm developed. This system contains a stable and Singulus EMould instead of the 650nm red lasers used for CD easy to operate solid state laser, with a much DIETER WAGNER, and DVD. longer lifetime than the gas laser. As all pro- Singulus Technologies AG An advanced copy protection system will posed next-generation formats require only The third generation of optical disc formats is give better protection than what was avail- one spot, the system has a single recording set to arrive on the market by the end of this able for CD and DVD with mandatory serializ- spot. Spot deflection, required to create the year.As with Blu-ray Disc, the HD DVD format ing of each single HD DVD. The serialization groove wobble in the recordable and was developed to tremendously increase the will take place on the aluminum covered layer rewritable formats, is available as an option. -
Argon-Ion and Helium-Neon Lasers
Argon-Ion and Helium- Neon Lasers The one source for gas lasers What makes Lumentum the choice for argon-ion and helium-neon (HeNe) lasers? Whether you are involved in medical research, semiconductor manufacturing, high-speed printing, or Your Source for another demanding application, we have the expertise, commitment, and technology to ensure you get the best solution for your need. With more than 35 years of experience, we have an unmatched Successful gas laser production requires extraordinary care understanding of the gas laser market. That understanding has during the manufacturing process. Every individual throughout led us to devote extensive resources to help establish a premier, each production stage, from engineering and procurement to Gas Lasers high-volume manufacturing facility. Located in Thailand, the manufacturing and quality control, is attuned to the highly facility produces lasers of the highest standard. And we maintain sensitive nature of the applications for which these products are that standard through regional quality management, on-site used. Consequently, we can assure the steady supply of quality supplier quality engineering, and regular quality audits. products to our customers around the globe. Our products are being used in customers’ new systems and as replacement components in the large installed base of existing systems. 2 3 Key Gas Laser Applications Known for their longevity and predictable electrical and optical performance characteristics, our lasers are being used in a wide variety of applications. Medical Research University, medical, and government laboratories on the cusp of new discoveries rely on instruments designed with Lumentum argon-ion and HeNe lasers for cell mapping, genome analysis, and DNA sequencing. -
Experimental Results on Advanced Inertial Fusion Schemes Obtained
NUKLEONIKA 2012;57(1):3−10 ORIGINAL PAPER Experimental results Dimitri Batani, Leonida A. Gizzi, Petra Koester, Luca Labate, on advanced inertial fusion Javier Honrubia, Luca Antonelli, Alessio Morace, Luca Volpe, Jorge J. Santos, Guy Schurtz, schemes obtained Sebastien Hulin, Xavier Ribeyre, Philippe Nicolai, Benjamin Vauzour, within the HiPER project Fabien Dorchies, Wiger Nazarov, John Pasley, Maria Richetta, Kate Lancaster, Christopher Spindloe, Martin Tolley, David Neely, Michaela Kozlová, Jaroslav Nejdl, Bedrich Rus, Jerzy Wołowski, Jan Badziak Abstract. This paper presents the results of experiments conducted within the Work Package 10 (fusion experimental programme) of the HiPER project. The aim of these experiments was to study the physics relevant for advanced ignition schemes for inertial confinement fusion, i.e. the fast ignition and the shock ignition. Such schemes allow to achieve a higher fusion gain compared to the indirect drive approach adopted in the National Ignition Facility in United States, which is important for the future inertial fusion energy reactors and for realising the inertial fusion with smaller facilities. Key words: advanced ignition schemes • fast ignition • shock ignition • inertial fusion • propagation of fast electrons • short-pulse ultra-high-intensity laser • shock compressed matter • cylindrical implosions Introduction D. Batani , J. J. Santos, G. Schurtz, S. Hulin, In 2006 the European Strategy Forum on Research X. Ribeyre, P. Nicolai, B. Vauzour, F. Dorchies Infrastructures (ESFRI) included the HiPER Project CELIA, Université de Bordeaux/CNRS/CEA, (European High Power Laser Energy Research Facility) Talence, 33405, France, in the European roadmap for Research Infrastructures. Tel.: +33 0 5 4000 3753, Fax: + 33 0 5 4000 2580, The goals of the HiPER project are to perform a feasi- E-mail: [email protected] bility study, choose a design and then construct a high- -energy laser facility for research on the production of L. -
Laser Applications to Medicine and Biology
BASIC PRINCIPLES OF MEDICAL LASERS leactur 7 Dr.khitam Y. Elwasife special Topics 2019-2020 Layout Fundamentals of Laser • Introduction– Properties of Laser Light– Basic Components of Laser– Basic laser operation– Types of Lasers– Laser Applications Principles – of Medical Lasers Types of Medical Lasers– Laser: Medical Applications– Laser: Surgery and Diagnostics– Laser Hazards– Laser Safety– LASER STAND FOR LIGHT AMPLIFICATION BY STIMULATED EMISSION OF RADIATION Introduction LASER Light Amplification by Stimulated Emission of Radiation. •An optical source that emits photons in a coherent beam. •optical lasers, a device which produces any particles or electromagnetic radiations in a coherent state is called “Laser”, e.g., Atom Laser. •In most cases “laser” refers to a source of coherent photons i.e., light or other electromagnetic radiations. It is not limited to photons in the visible spectrum. There are 3 x-ray lasers, infrared lasers, UV lasers etc. Properties of Laser Light • The light emitted from a laser is monochromatic, that is, it is of one color/wavelength. In contrast, ordinary white light is a combination of many colors • Lasers emit light that is highly directional, that is, laser light is emitted as a relatively narrow beam in a specific direction. Ordinary light, such as from a light bulb, is emitted in many directions away from the source. • The light from a laser is said to be coherent, which means that the wavelengths of the laser light are in phase in space and time. Ordinary light can be a mixture of many wavelengths. Ordinary Light vs. Laser Light Ordinar Laser y Light Light Basic Concepts: Laser is a narrow beam of light of a single wavelength (monochromatic) in which each wave is in phase (coherent) with other near it. -
Excitation of a Gas Laser
Excitation of a gas laser Two main excitation techniques are used for gas lasers: - Electrical Discharge - Optical Pumping Excitation of Gas Laser by Electrical Discharge Applying high voltage to electrodes at both sides of the tube containing the gas causes electrical breakdown through the gas. Electrons are ejected from the cathode, accelerated toward the anode, and collide with the gas molecules along the way. During the collision, the mechanical kinetic energy of the electrons is transferred to the gas molecules, and excites them. (This same method of energy transfer is used in common fluorescent lights). Excitation of Gas Laser by Optical Pumping Exciting a laser medium by optical pumping, requires that the absorption spectrum of the medium will be similar to the emission spectrum of the pumping source, so that a big amount of the radiation will be absorbed. Conventional light sources used for optical pumping have broad emission spectrum, so only a small part of the light is used in the excitation process. Because gas atoms absorb only a small portion of the spectrum, optical pumping is not generally an efficient method for gas lasers. The absorption spectrum of solids are wider than the absorption spectra of gases, so the pumping efficiency of solid state lasers by conventional light sources are higher than that for gas lasers. Thus gas lasers are usually excited by an electric discharge (see previous section).When we want to excite a gas laser by optical pumping; we need to find an optical source with very narrow bandwidth, which fits the narrow absorption spectral lines of the gas. -
TDLAS Monitoring of Carbon Dioxide with Temperature Compensation in Power Plant Exhausts
applied sciences Article TDLAS Monitoring of Carbon Dioxide with Temperature Compensation in Power Plant Exhausts Xiaorui Zhu 1,3, Shunchun Yao 1,3,* , Wei Ren 2 , Zhimin Lu 1,3 and Zhenghui Li 1,3 1 School of Electric Power, South China University of Technology, Guangzhou 510640, China; [email protected] (X.Z.); [email protected] (Z.L.); [email protected] (Z.L.) 2 Department of Mechanical and Automation Engineering, The Chinese University of Hong Kong, Shatin, Hong Kong SAR 2912, China; [email protected] 3 Guangdong Province Engineering Research Center of High Efficiency and Low Pollution Energy Conversion, Guangzhou 501640, China * Correspondence: [email protected]; Tel.: +86-139-2515-0807 Received: 7 January 2019; Accepted: 24 January 2019; Published: 28 January 2019 Featured Application: Applying to complex industrial environment, TDLAS monitoring with temperature compensation can come handy. Abstract: Temperature variations of flue gas have an effect on carbon dioxide (CO2) emissions monitoring. This paper demonstrates accurate CO2 concentration measurement using tunable diode laser absorption spectroscopy (TDLAS) with temperature compensation methods. A distributed feedback diode laser at 1579 nm was chosen as the laser source for CO2 measurements. A modeled flue gas was made referring to CO2 concentrations of 10–20% and temperatures of 298–338 K in the exhaust of a power plant. Two temperature compensation methods based on direct absorption (DA) and wavelength modulation (WMS) are presented to improve the accuracy of the concentration measurement. The relative standard deviations of DA and WMS measurements of concentration were reduced from 0.84% and 0.35% to 0.42% and 0.31%, respectively. -
The Three Phases of Lasers: Solid-State, Gas, and Liquid”, Laser Focus World, July 1995, P
Thomas V. Higgins, “The three phases of lasers: solid-state, gas, and liquid”, Laser Focus World, July 1995, p. 73–85 The three phases of lasers: solid-state, gas, and liquid Since the first demonstration of the ruby laser, a variety of other materials have been found to operate as lasers. Thomas V. Higgins, Contributing Editor When Arthur Schawlow and Charles Townes published their famous theoretical paper "Infra- SOLID-STATE LASERS red and Optical Masers" in The Physical Review Solid-state lasers include all optically pumped in 1958, no one was quite sure what form the lasers in which the gain medium is a solid at first laser would take. In their paper, Schawlow room temperature. Semiconductor lasers do not and Townes had suggested that potassium and belong in this category because these lasers are cesium vapor, or even solid crystals of rare-earth usually electrically pumped and involve different salts, might emit laser light if they were first ir- physical processes (see Back to Basics, April radiated with intense light of just the right wave- 1995, p. 65). In solid-state laser materials, the at- length, a scheme now known as optical pumping. oms responsible for generating laser light are But as fate would have it, Theodore Maiman first excited to higher energy states through the constructed the world’s first laser from a ruby absorption of photons, and the way in which crystal — a material that Schawlow had said these atoms relax from their excited states deter- wouldn’t work. mines the quality and quantity of laser light pro- Since that first ruby laser, researchers have duced (for an overview of this process, see Back discovered laser action in thousands of sub- to Basics, June 1994, p. -
Raman Spectroscopy Using a Gas Laser J.P
Raman spectroscopy using a gas laser J.P. Russell To cite this version: J.P. Russell. Raman spectroscopy using a gas laser. Journal de Physique, 1965, 26 (11), pp.620-626. 10.1051/jphys:019650026011062001. jpa-00206048 HAL Id: jpa-00206048 https://hal.archives-ouvertes.fr/jpa-00206048 Submitted on 1 Jan 1965 HAL is a multi-disciplinary open access L’archive ouverte pluridisciplinaire HAL, est archive for the deposit and dissemination of sci- destinée au dépôt et à la diffusion de documents entific research documents, whether they are pub- scientifiques de niveau recherche, publiés ou non, lished or not. The documents may come from émanant des établissements d’enseignement et de teaching and research institutions in France or recherche français ou étrangers, des laboratoires abroad, or from public or private research centers. publics ou privés. 620 dotted line the intensity ratio here is about 3.2 Discussion times too large. The intensity anomaly is even greater in the case of deuterium where in normal M. THEIMER. - Is the interpretation of the deuterium the observed ratio is as great as 9 times Raman spectrum of hydrogen in terms of exci- the value expected on the basis of isotropic scat- tons different from that in terms of lattice vibra- tering only. Up to the present no plausible expla- tions ? It appears that the assignment of the nation of this curious effect has been forthcoming. different peaks to different nearest neighbor ratios It might be noted that the anomaly is not present of ortho and para molecules is not quite consistent in the high pressure gas at 300 OK and 85 °K. -
The Retinal Effects of Copper Vapor Laser Exposure Shimon Gabay.T Israel Kremer,* Isaac Ben-Sira,* Dan Sagie,T Dov Weinberger,* and Gideon Erezf
Investigative Ophthalmology & Visual Science, Vol. 29, No. 4, April 1988 Copyright © Association for Research in Vision and Ophthalmology The Retinal Effects of Copper Vapor Laser Exposure Shimon Gabay.t Israel Kremer,* Isaac Ben-Sira,* Dan Sagie,t Dov Weinberger,* and Gideon Erezf The copper vapor laser is a pulsed gas laser which emits energy in two wavelengths simultaneously: 510.6 nm (green) and 578.2 nm (yellow). Each pulse has a duration of 15 nsec, maximal energy of 3 mJ and a peak power of more than 100 kW. It is a variably high repetition rate laser, in the range between 1 kHz and more than 20 kHz. We studied its interaction with the rabbit retina, while using two different repetition rates, 4 kHz and 18 kHz. The histological analysis of the lesion produced by 4 kHz repetition rate showed undesired retinal effects, similar to those caused by other pulsed lasers. On the other hand, the histological examination of the lesion produced by the 18 kHz repetition rate showed a desired coagulation effect, limited to the outer retinal layers, and comparable to a lesion produced by a continuous wave (CW) laser. Invest Ophthalmol Vis Sci 29:528-533, 1988 Lasers in ophthalmology are used mainly for reti- above 20 kHz, delivering two wavelengths: 510.6 nm nal coagulation, iridectomy and lens capsulotomy. and 578.2 nm.10 The pulse peak power can be in- Argon laser is now widely in use as a retinal photo- creased by decreasing the repetition rate, while the coagulator,12 as it is well-transmitted by the ocular average power has an optimal level at intermediate media3 and well-absorbed by the retinal pigment epi- repetition rate. -
ACTIVE and PASSIVE MODE LOCKING of CONTINUOUSLY OPERATING RHODAMINE 6G Dye Lasers
NBSIR 73-347 ACTIVE AND PASSIVE MODE LOCKING OF CONTINUOUSLY OPERATING RHODAMINE 6G DYE LASERS Andre Scavennec Norris S. Nahman Electromagnetics Division Institute for Basic Standards National Bureau of Standards Boulder, Colorado 80302 February 1974 NBSIR 73-347 ACTIVE AND PASSIVE MODE LOCKING OF CONTINUOUSLY OPERATING RHODAMINE 6G DYE LASERS Andre Scavennec Norris S. Nahman Electromagnetics Division Institute for Basic Standards National Bureau of Standards Boulder, Colorado 80302 February 1974 U.S. DEPARTMENT OF COMMERCE, Frederick B. Dent, Secretary NATIONAL BUREAU OF STANDARDS Richard W Roberts Director NBSIR 73-347 ACTIVE AND PASSIVE MODE LOCKING OF CONTINUOUSLY OPERATING RHODAMINE 6G DYE LASERS Andre Scavennec Norris S. Nahman Electromagnetics Division Institute for Basic Standards National Bureau of Standards Boulder, Colorado 80302 February 1974 U.S. DEPARTMENT OF COMMERCE, Frederick B. Dent, Secretary NATIONAL BUREAU OF STANDARDS Richard W Roberts Director CONTENTS Ch apter Page 1. INTRODUCTION 2 2. THE CW Rh 6G LASER -- 3 3. MODE LOCKING IN A LASER 11 4. ACTIVE MODE LOCKING OF THE CW Rh 6G LASER 15 5. PASSIVE MODE LOCKING OF THE CW Rh 6G LASER---- 22 6. COMPARISON OF THE TWO TECHNIQUES 2 8 7. CONCLUSION 30 REFERENCES-- 34 LIST OF FIGURES AND TABLES Figure 2-1. Energy level diagram o£ Rh 6G 36 Figure 2-2. CW dye laser 37 Figure 2-3. Dye cells 38 Figure 2-4. Dye circulating system 39 Figure 3-1. Laser modes and mode locked output 40 Figure 4-1. Active mode locking, experimental setup-- 41 Figure 4-2. Acoustooptic modulator 42 Figure 4-3. Modulator driving circuit 43 Figure 4-4. -
Gas Lasers 1St Edition Kindle
GAS LASERS 1ST EDITION PDF, EPUB, EBOOK E W McDaniel | 9781483218687 | | | | | Gas Lasers 1st edition PDF Book This article needs additional citations for verification. Reviews 0. The information bounces off the satellite to a ground earth station, and the data is uploaded into a database. Main article: Ion laser. True, choosing this option allows a fabricator to get the lowest gas price per unit, but rarely are these bulk tanks really the best option for small or medium-sized laser operations. You are connected as. The CO 2 laser, in particular, ranges in cw power from few Watts to kWs, making these lasers ideal for many industrial applications including welding and drilling. Another commonly used gas laser is the argon-ion laser. They are also used in applications, such as holography, where mode stability is important. Carbon monoxide or "CO" lasers have the potential for very large outputs, but the use of this type of laser is limited by the toxicity of carbon monoxide gas. So, another unusual feature of the excimers is that they do not require an optical amplifier. Gas lasers can be classified in terms of the type of transitions that lead to their operation: atomic or molecular. Bennet and D. Chemical lasers are powered by a chemical reaction, and can achieve high powers in continuous operation. Notice the two mirrors that seal the two ends of the bore. Still, because of their long operating lifetime of 20, hours or more and their relatively low manufacturing cost, He-Ne lasers are among the most popular gas lasers.