Solder Joints at Delphi
Total Page:16
File Type:pdf, Size:1020Kb
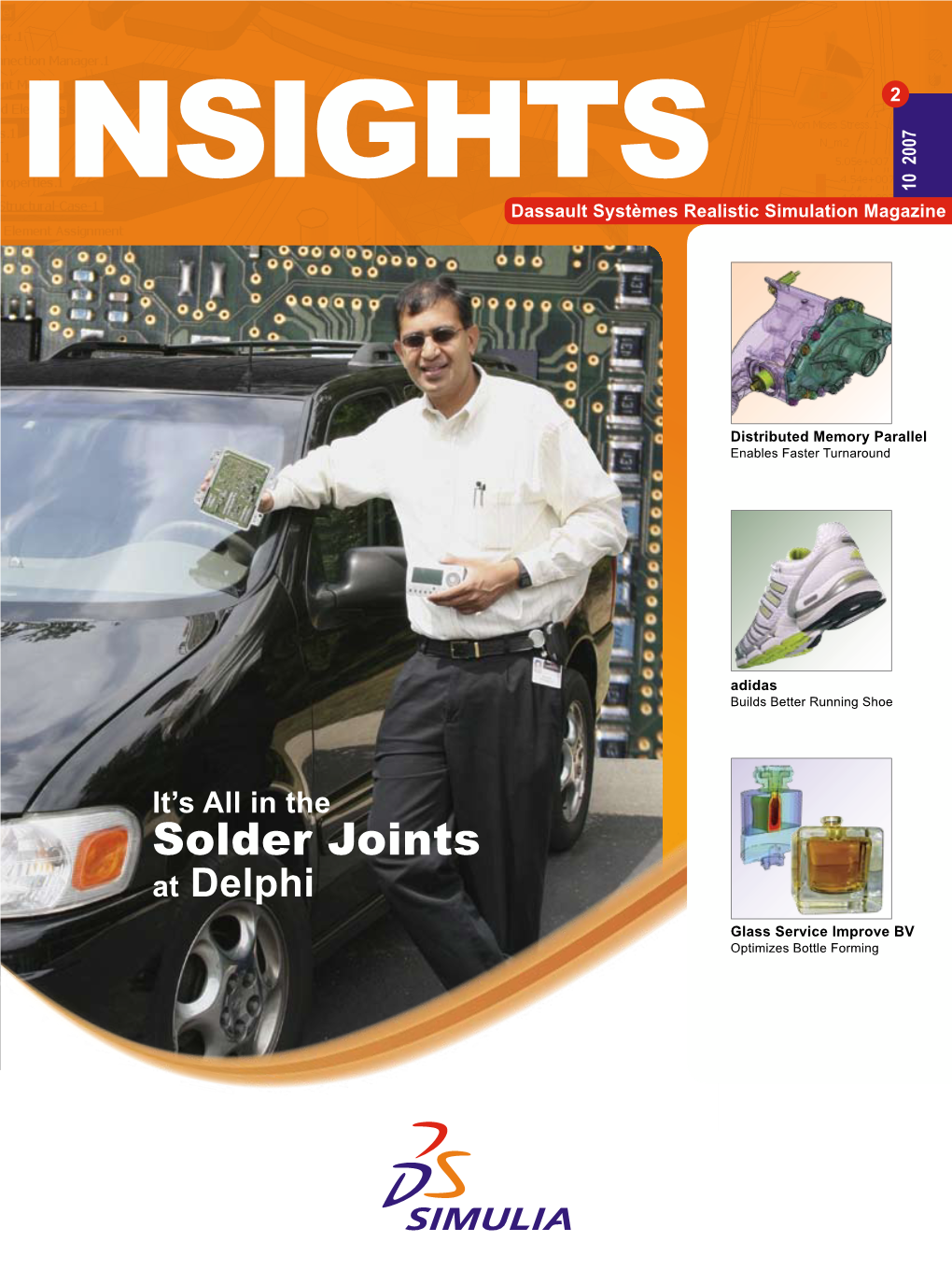
Load more
Recommended publications
-
AALTO UNIVERSITY School of Engineering Engineering Design and Production
AALTO UNIVERSITY School of Engineering Engineering Design and Production Kaur Jaakma Engineering Data Management Thesis submitted in partial fulfillment of the requirements for the degree of Master of Science in Technology Espoo, 29 December 2011 Supervisor: Professor (pro tem) Jari Juhanko Instructor: Andrea Buda, M.Sc. AALTO UNIVERSITY ABSTRACT OF THE MASTER’S THESIS SCHOOLS OF TECHNOLOGY PO Box 11000, FI-00076 AALTO http://www.aalto.fi Author: Kaur Jaakma Title: Engineering Data Management School: School of Engineering Department: Department of Engineering Design and Production Professorship: Machine Design Code: Kon-41 Supervisor: Professor (pro tem) Jari Juhanko Instructor: Andrea Buda, M. Sc. Abstract: To support design decisions in the product development process, companies are increasingly relying on computer aided simulations. However, investments in simulation technologies can not translate directly into benefit without implementing a system able to capture knowledge and value out of each simulation performed. To implement the switch from traditional product development to Simulation Based Design (SBD) and product development, a system that can efficiently manage simulation data is needed. Common situation in industry is to store everything related to simulations in the analyst’s computer or in a shared folder. Currently only CAE (Computer Aided Engineering) departments in aerospace and automotive OEMs are early adopters of SDM (Simulation Data Management) technology. Commercial SDM systems are developed to suits the needs of big enterprises with repetitive processes and product with broadly similar geometries. The cost for deployment and maintenance of this kind of system represents a barrier for small and mid-size companies. The larger companies might not benefit from a system developed and tuned for the needs of the early adopters mentioned above. -
Development of a Coupling Approach for Multi-Physics Analyses of Fusion Reactors
Development of a coupling approach for multi-physics analyses of fusion reactors Zur Erlangung des akademischen Grades eines Doktors der Ingenieurwissenschaften (Dr.-Ing.) bei der Fakultat¨ fur¨ Maschinenbau des Karlsruher Instituts fur¨ Technologie (KIT) genehmigte DISSERTATION von Yuefeng Qiu Datum der mundlichen¨ Prufung:¨ 12. 05. 2016 Referent: Prof. Dr. Stieglitz Korreferent: Prof. Dr. Moslang¨ This document is licensed under the Creative Commons Attribution – Share Alike 3.0 DE License (CC BY-SA 3.0 DE): http://creativecommons.org/licenses/by-sa/3.0/de/ Abstract Fusion reactors are complex systems which are built of many complex components and sub-systems with irregular geometries. Their design involves many interdependent multi- physics problems which require coupled neutronic, thermal hydraulic (TH) and structural mechanical (SM) analyses. In this work, an integrated system has been developed to achieve coupled multi-physics analyses of complex fusion reactor systems. An advanced Monte Carlo (MC) modeling approach has been first developed for converting complex models to MC models with hybrid constructive solid and unstructured mesh geometries. A Tessellation-Tetrahedralization approach has been proposed for generating accurate and efficient unstructured meshes for describing MC models. For coupled multi-physics analyses, a high-fidelity coupling approach has been developed for the physical conservative data mapping from MC meshes to TH and SM meshes. Interfaces have been implemented for the MC codes MCNP5/6, TRIPOLI-4 and Geant4, the CFD codes CFX and Fluent, and the FE analysis platform ANSYS Workbench. Furthermore, these approaches have been implemented and integrated into the SALOME simulation platform. Therefore, a coupling system has been developed, which covers the entire analysis cycle of CAD design, neutronic, TH and SM analyses. -
Book of Abstracts
Book of abstracts 9th PhD Seminar on Wind Energy in Europe September 18-20, 2013 Uppsala University Campus Gotland, Sweden Campus Gotland WIND ENERGY Book of abstracts of 9th PhD Seminar on Wind Energy in Europe Uppsala University Campus Gotland, Sweden Campus Gotland, Wind Energy 621 67 Visby PREFACE The wind energy field is becoming more and more important in relation with future challenges of switching the world energy system to renewables. Therefore it is of high importance that tomorrow’s researchers in the field from all over the word meet and discuss future challenges. The 9th annual EAWE PhD seminar is in 2013 organized by Uppsala University Campus Gotland. This is a very suitable place for this event since it combines a unique historical environment with a sustainable profile and a long tradition of wind energy. Today about 45% of the energy consumption is locally produced by wind energy. Uppsala University Campus Gotland also has more than 10 years experience of teaching and research in the field with a focus on wind power project development. The aim with this seminar is to improve the international communication and information sharing of ongoing activities as well as simplify contact building between young researchers. It is also a perfect opportunity for PhD students to practice and improve their presentation and discussion skills. Associate Professor Stefan Ivanell Director, Wind Energy Uppsala University, Campus Gotland Book of abstracts of 9th PhD Seminar on Wind Energy in Europe September 18-20, 2013, Uppsala University Campus Gotland, Sweden TABLE OF CONTENTS ROTOR & WAKE AERODYNAMICS UNDERSTANDING THE WIND TURBINE BREAKDOWN MECHANISM WITH CFD M. -
NX Advanced Simulation
NX NX Advanced Simulation fact sheet Siemens PLM Software www.siemens.com/nx Summary NX™ Advanced Simulation software combines the power of an integrated NX Nastran® desktop solver with NX Advanced FEM, a comprehensive suite of multi-CAD FE model creation and results visualization tools. Extensive geometry creation, idealization and abstraction capabilities enable the rapid development of complex 3D mathematical models that allow design decisions to be based on insight into real product performance. NX Advanced Simulation enables a true multi-physics environment via tight integration with NX Nastran as well as other industry standard solvers such as Abaqus, Ansys, MSC Nastran and LS-Dyna. Benefits NX Advanced FEM includes the fundamental modeling functions of automatic and manual mesh Build models faster with embedded generation, application of loads and boundary conditions and model development and checking. NX tools for 3D geometry creation, Advanced FEM includes Assembly FEM technology, a distributed model approach to handle large editing and abstraction FEM assemblies. A robust set of visualization tools generates displays quickly, lets you view multiple Make design changes easily with results simultaneously and enables you to easily print the display. In addition, extensive post- Synchronous Technology for quick what-if analysis processing functions enable review and export of analysis results to spreadsheets and provide Enable faster collaboration between extensive graphing tools for gaining an understanding of results. Post-processing also supports analysts and design engineers with the export of JT™ data for collaboration across the enterprise with JT2Go and Teamcenter® for geometry associativity lifecycle visualization software. •Knowledge of design changes •“On-demand” FE model updates NX Advanced FEM provides seamless, transparent based on design geometry support for a number of industry-standard changes solvers, such as NX Nastran, MSC Nastran, Manage and share your CAE data Ansys and Abaqus. -
NX Advanced Simulation Integrating FE Modeling and Simulation Streamlines Product Development Process
Siemens PLM Software NX Advanced Simulation Integrating FE modeling and simulation streamlines product development process Benefits A modern CAE environment unique from all other finite element (FE) • Speed simulation processes NX™ Advanced Simulation software is a preprocessors is its superior geometry by up to 70 percent modern, multidiscipline computer-aided foundation that enables intuitive geometry engineering (CAE) environment for editing and analysis model associativity to • Perform accurate, reliable advanced analysts, workgroups and design- multi-computer-aided design (CAD) data. structural analysis with ers that need to deliver high-quality perfor- The tight integration of a powerful geome- integrated NX Nastran mance insights in a timely fashion to drive try engine with robust analysis modeling solver product decisions. NX Advanced Simulation commands is the key to reducing modeling • Increase product quality by integrates best-in-class analysis modeling time by up to 70 percent compared to rapidly simulating design with the power of an integrated NX traditional FE modeling tools. tradeoff studies Nastran® desktop solver for basic structural Enabling fast, intuitive geometry editing analysis. NX Advanced Simulation also • Lower overall product NX Advanced Simulation is built on the forms the foundation on which you can development costs by same leading geometry foundation that perform additional solutions for advanced reducing costly, late design powers NX. By using NX Advanced structural, thermal, flow, engineering opti- change -
Abaqus for CATIA V5
Abaqus for CATIA V5 R21 CATIA V5 Integration • Temperature-dependent material properties • Thermal properties Integration Features • Linear elasticity • Availability of linear and nonlinear static, dynamic, and thermal • Metal plasticity (isotropic, kinematic, or analysis capabilities within the CATIA V5 environment Johnson-Cook hardening) • Complete geometric associativity • Hyperelasticity • Support for Knowledgeware, publications, and results sensors • Abaqus material user subroutine • Model optimization using the PEO workbench • Abaqus heat generation user subroutine • Support for analysis assembly • Composite properties imported from the CATIA Composite • Complete support for CATIA V5 groups Design workbench • Support for many CATIA V5 advanced connections • Orthotropic composite layups for shell modeling • Visual Basic scripting capabilities for automated workflows • 3-D orthotropic material properties • Gasket material properties Operating Systems • Windows/x86-32 and Windows/x86-64 operating systems Loads (Windows XP Professional SP2, Windows XP Professional x64, • Load application using tabular and smooth-step amplitudes Windows Vista, Windows 7) • Forces and moments can follow nodal rotation • Data mapping available for pressure, heat flux, thermal Abaqus Workbenches film condition, and temperature • Nonlinear Structural Analysis workbench for static, • Imported loads from GPS analysis frequency-extraction, and explicit dynamic simulations • Cartesian, cylindrical, and spherical local coordinate • Thermal Analysis workbench for -
Cranfield University Laszlo Hetey Idealisation Error
CRANFIELD UNIVERSITY LASZLO HETEY IDEALISATION ERROR CONTROL FOR AEROSPACE VIRTUAL STRUCTURAL TESTING SCHOOL OF ENGINEERING PhD THESIS CRANFIELD UNIVERSITY SCHOOL OF ENGINEERING PHD THESIS Academic Year 2008 - 2009 LASZLO HETEY IDEALISATION ERROR CONTROL FOR AEROSPACE VIRTUAL STRUCTURAL TESTING Supervisor: Dr. James Campbell March 2009 © Cranfield University 2009. All rights reserved. No part of this publication may be reproduced without the written permission of the copyright owner. ABSTRACT This thesis addresses idealisation error control for the nonlinear finite element method. The focus is on accurate failure prediction of mid-size aerospace structures. The objective is the development of technologies that shorten the certification process of new airplanes, by replacing expensive and time consuming testing with reliable calculation methods. The SAFESA (Safe Structural Analysis) approach was applied to the collapse analyses of stiffened metal panels. ABAQUS/Standard was thereby the utilised nonlinear solver. Because the original SAFESA procedure is tailored for linear analyses, the methodology needed an update. The first analysis case is a stiffened panel compression test which was arranged as a lecture demonstration at Cranfield University. The analysis behaviour is highly nonlinear due to the thin-walled properties of the panel. The second analysis investigates an Airbus compression panel. Until failure, the panel behaves geometrically less complicated because the major load bearing parts are thick-walled and bend smoothly. The main research work is the critical analysis of important modelling assumptions concerning the used material model, boundary conditions and geometrical imperfections. In both cases, the method helped to identify idealisation errors and to build a reliable FEM model. In order to deal with the nonlinear error sources, minor extensions to the original method had to be made. -
Simulation Comparison Between PTC/Creo and Professional CAE
2017 International Conference on Mechanical and Mechatronics Engineering (ICMME 2017) ISBN: 978-1-60595-440-0 Simulation Comparison Between PTC/Creo and Professional CAE Software Li-xin WANG*, Jun-hui LIU and Lin-kai CHEN School of Mechanical Engineering, Zhengzhou University, Henan Zhengzhou 450001, China *Corresponding author Keywords: PTC/Creo, Mechanism analysis, Structure analysis, Adams, Ansys. Abstract. CAE is an indispensable tool for mechanical design engineers, and is widely used in product development process. This paper discuss the differences and linkages of the two most commonly used mechanism simulation and strength calculation in the design process. For the same model respectively, simulations using PTC/Creo Vs. Ansys and PTC/Creo Vs. MSC Adams are conducted. The results show that PTC/Creo software is simple to use, easy to modify and accurate enough upon the simulation. However, it is a bit rougher and shallower than the professional CAE software .So, for mechanical design engineers, PTC/Creo simulation tools should be preferred, and the profound analysis should be the duty of professional CAE engineers. Introduction With the development and popularization of CAD technology, three-dimensional software design is more and more commonly used in modern mechanical design. At present, the general understanding is that CAD software is responsible for three-dimensional modeling of parts, components and machine assembly, and static interference analysis. Although CAD software also provides integrated CAE tools (mechanism simulation, structural analysis, thermal analysis, etc.). However, most people are accustomed to the simplified model, and export the model to the professional finite element analysis software (Ansys, Nastran, Abaqus) and virtual prototyping software (MSC.Adams, LMS Virtual.Lab, etc.) for analysis. -
An Evaluation of Associative Interface for Solidworks and ABAQUS/CAE Hung-Peng Li and Goang-Ding Shyu Baker Hughes Inc
An Evaluation of Associative Interface for SolidWorks and ABAQUS/CAE Hung-Peng Li and Goang-Ding Shyu Baker Hughes Inc. Abstract: In the modern design and manufacturing world, shorter development cycle times are being demanded. In addition, engineers are being asked to perform more analyses and studies to improve their products. To meet the challenge, engineers will seek more ways to increase robustness and productivity. With the continued integration of computational tools, such as the associative import between SolidWorks and Abaqus/CAE, it is possible to analyze and reiterate designs, materials, and structures in a more productive and efficient fashion. With the assistance of the associative interface capability, one can quickly update design changes into the ABAQUS finite element (FE) pre-processing tool with just one click. This associative importing feature allows tremendous time savings and avoids time-consuming repetitions and mistakes in creating new FE meshes and models for newly imported modified geometries and designs. This new capability allows Abaqus/CAE to update the imported geometries in real time and also to retain the majority of FE analysis model features, such as partitions and meshing seeds, contact interactions, applied loads, and boundary conditions. It also provides the advantage of creating multiple FE models with a reasonable effort for parametric or sensitivity studies to account for design and manufacturing variations, for example, the imperfections of eccentricity and ovality on the effect of collapse pressures. A wide variety of completion tools were evaluated. The interfaces and the process of the associative function between SolidWorks and Abaqus/CAE will be shown. The summary and conclusion including pros and cons will be discussed. -
ANSYS/LS-DYNA Version 5.7" Dated January 18, 2002'
SOFTWARE RELEASE NOTICE 1. SRN Number: 1 (1_i i- - s 0,j - _2'ii 2. Project Title: Analysis of the HI-STORM Project No. Cask S ystem 20-01405-041 l 4Sh#Ucf-z-7 &ft 3. SRN Title: ANSYS / LS-DYNA, version 5.7 4. Originator/Requestor: P. A. Cox Date: 02/26/01 5. Summary of Actions * Release of new software O Release of modified software: 0 Enhancements made 0 Corrections made 0 Change of access software 0 Software Retirement | 6. Persons Authorized Access Name Read Only/Read- Addition/Change/D Write elete P. A. Cox R-W A Asad Chowdhury R-Wy A Janet Banda R9 4/c S-3 -2cy A 7. Element Manager Approva / Date: 8. Remarks: CNWRA Form TOP-6 (05/98) SOFTWARE SUMMARY FORM 01. Summary Date: 02. Summary prepared by (Name and phone) 03. Summary Action: 02/26/01 P. A. Cox, 522-2315 _ __ __ __ _ __ _ _ _ _ _ _ _ _ _ _ _ _ _ _ _ _ _ N E W 04. Software Date: 05. Short Title: ANSYS / LS-DYNA released 02/01 06. Software Title: ANSYS I LS-DYNA, version 5.7 07. Internal Software ID: 08. Software Type: 09. Processing Mode: 10. Application Area [l Automated Data System l Interactive a. General: * Scientific/Engineering El Auxiliary Analyses EComputer Program [1 Batch El Total System PA El Subsystem PA El Other El Subroutine/Module * Combination b. Specific: Structural Dynamics 11. Submitting Organization and Address: 12. Technical Contact(s) and Phone: CNWRA/SwRl P. -
NX Advanced FEM Integrating Geometry and FE Modeling to Streamline the Product Development Process
Siemens PLM Software NX Advanced FEM Integrating geometry and FE modeling to streamline the product development process Benefits Summary Providing finite element modeling for • Speed simulation processes NX™ Advanced FEM software is a modern, experienced CAE analysts by up to 70 percent multidiscipline computer-aided engineering Using NX Advanced FEM drastically reduces (CAE) environment for advanced analysts, the time you spend preparing simulation • Increase product quality by workgroups and designers that need to models. NX delivers all the advanced mesh- rapidly simulating design deliver high-quality performance insights in ing, boundary conditions and solver tradeoff studies a timely fashion to drive product decisions. interfaces that experienced analysts expect • Lower overall product NX Advanced FEM includes a full suite of and need to perform high-end analysis. development costs by direct geometry modeling and editing However, what makes NX Advanced FEM reducing costly, late design tools, and forms the analysis modeling unique from all other finite element (FE) change orders foundation on which you can pre- and post- preprocessors is its superior geometry foun- process analysis models for structural, dation that enables intuitive geometry • Efficiently manage large, thermal, flow, engineering optimization editing and analysis model associativity to complex analysis models and multiphysics analyses. NX Advanced multi-computer-aided design (CAD) data. • Capture and automate best FEM speeds CAE processes with a bi-direc- The tight integration of a powerful geome- practices and commonly tional analysis model to design geometry try engine with robust analysis modeling used processes association that enables users to rapidly commands is the key to reducing modeling update an analysis model when the base time by up to 70 percent compared to tradi- • Pre- and postprocess design changes. -
List of Finite Element Software Packages Wikipedia, the Free Encyclopedia List of Finite Element Software Packages from Wikipedia, the Free Encyclopedia
12/15/2015 List of finite element software packages Wikipedia, the free encyclopedia List of finite element software packages From Wikipedia, the free encyclopedia This is a list of software packages that implement the finite element method for solving partial differential equations or aid in the pre and postprocessing of finite element models. Free/Open source https://en.wikipedia.org/wiki/List_of_finite_element_software_packages 1/8 12/15/2015 List of finite element software packages Wikipedia, the free encyclopedia Operating Name Description License System Multiplatform open source application for the solution of Linux, Agros2D GNU GPL physical problems Windows based on the Hermes library It is an Open Source FEA project. The solver uses a partially compatible ABAQUS Linux, CalculiX file format. The GNU GPL Windows pre/postprocessor generates input data for many FEA and CFD applications is an Open Source software package for Civil and Structural Engineering finite Linux, Code Aster element analysis and GNU GPL FreeBSD numeric simulation in structural mechanics which is written in Python and Fortran is an Open Source software package C/C++ hp Mac OS X, Concepts GNU GPL FEM/DGFEM/BEM Windows library for elliptic equations Comprehensive set of tools for finite QPL up to element codes, release 7.2, Linux, Unix, deal.II scaling from laptops LGPL after Mac OS X, to clusters with that Windows 10,000+ cores. Written in C++. GPL Distributed and Version 2 Unified Numerics Linux, Unix, DUNE with Run Environment, written Mac OS X Time