(12) Patent Application Publication (10) Pub
Total Page:16
File Type:pdf, Size:1020Kb
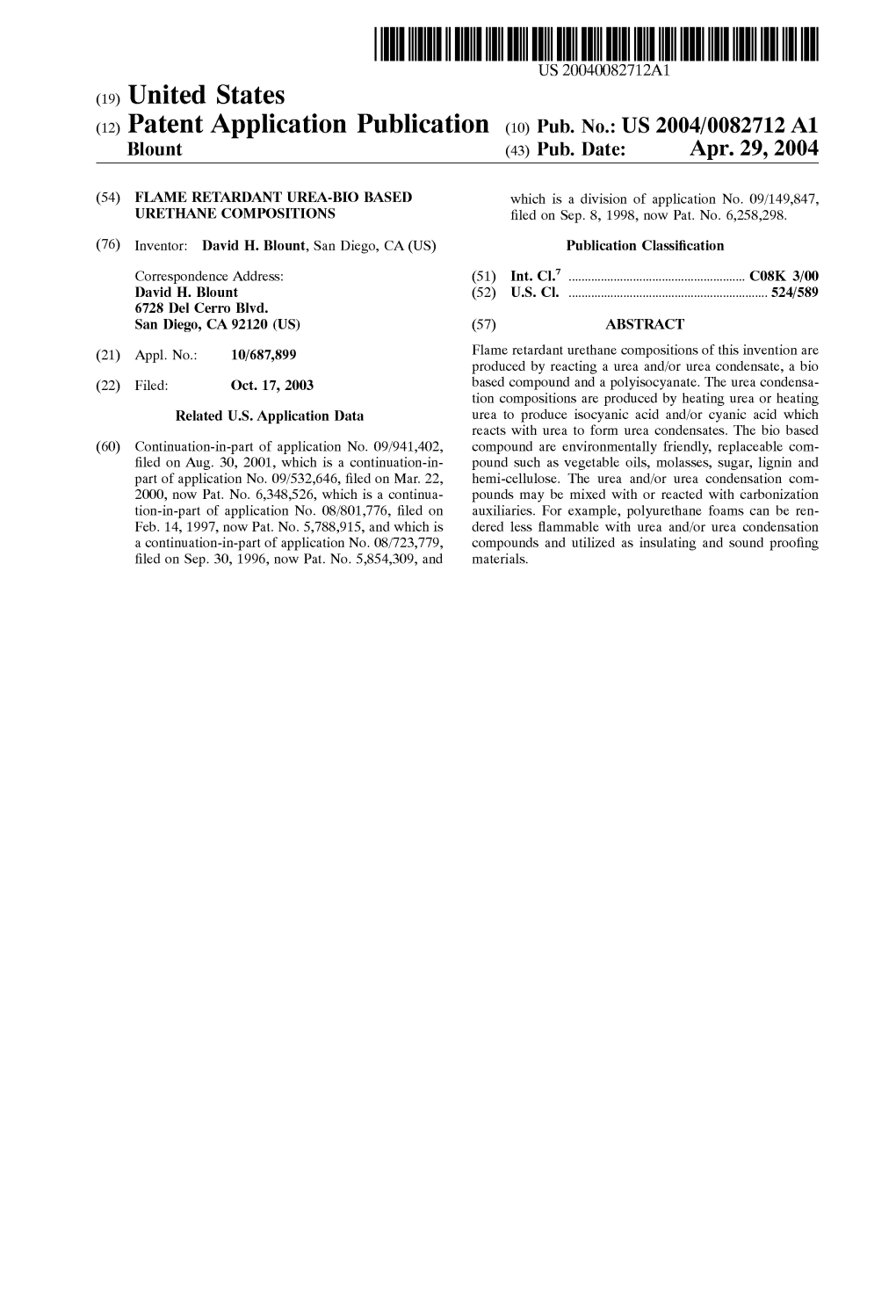
Load more
Recommended publications
-
Appendix H EPA Hazardous Waste Law
Appendix H EPA Hazardous Waste Law This Appendix is intended to give you background information on hazardous waste laws and how they apply to you. For most U.S. Environmental Protection Agency (EPA) requirements that apply to the University, the Safety Department maintains compliance through internal inspections, record keeping and proper disposal. In Wisconsin, the Department of Natural Resources (DNR) has adopted the EPA regulations, consequently EPA and DNR regulations are nearly identical. EPA defines This Appendix only deals with "hazardous waste" as defined by the EPA. hazardous waste as Legally, EPA defines hazardous waste as certain hazardous chemical waste. This hazardous chemical Appendix does not address other types of regulated laboratory wastes, such as waste; radioactive, infectious, biological, radioactive or sharps. Chapter 8 descibes disposal procedures infectious and biohazardous waste for animals. Chapter 9 describes disposal procedures for sharps and other waste that are regulated by can puncture tissue. Chapter 11 discusses Radiation and the Radiation Safety for other agencies. Radiation Workers provides guidelines for the disposal of radioactive waste. Procedures for medical waste are written by the UW Hospital Safety Officer. The Office of Biological Safety can provide guidance for the disposal of infectious and biological waste. EPA regulations focus on industrial waste streams. As a result, many laboratory chemical wastes are not regulated by EPA as hazardous chemical waste. However, many unregulated chemical wastes do merit special handling and disposal If a waste can be procedures. Thus, Chapter 7 and Appendix A of this Guide recommend disposal defined as: procedures for many unregulated wastes as if they were EPA hazardous waste. -
APPENDIX G Acid Dissociation Constants
harxxxxx_App-G.qxd 3/8/10 1:34 PM Page AP11 APPENDIX G Acid Dissociation Constants § ϭ 0.1 M 0 ؍ (Ionic strength ( † ‡ † Name Structure* pKa Ka pKa ϫ Ϫ5 Acetic acid CH3CO2H 4.756 1.75 10 4.56 (ethanoic acid) N ϩ H3 ϫ Ϫ3 Alanine CHCH3 2.344 (CO2H) 4.53 10 2.33 ϫ Ϫ10 9.868 (NH3) 1.36 10 9.71 CO2H ϩ Ϫ5 Aminobenzene NH3 4.601 2.51 ϫ 10 4.64 (aniline) ϪO SNϩ Ϫ4 4-Aminobenzenesulfonic acid 3 H3 3.232 5.86 ϫ 10 3.01 (sulfanilic acid) ϩ NH3 ϫ Ϫ3 2-Aminobenzoic acid 2.08 (CO2H) 8.3 10 2.01 ϫ Ϫ5 (anthranilic acid) 4.96 (NH3) 1.10 10 4.78 CO2H ϩ 2-Aminoethanethiol HSCH2CH2NH3 —— 8.21 (SH) (2-mercaptoethylamine) —— 10.73 (NH3) ϩ ϫ Ϫ10 2-Aminoethanol HOCH2CH2NH3 9.498 3.18 10 9.52 (ethanolamine) O H ϫ Ϫ5 4.70 (NH3) (20°) 2.0 10 4.74 2-Aminophenol Ϫ 9.97 (OH) (20°) 1.05 ϫ 10 10 9.87 ϩ NH3 ϩ ϫ Ϫ10 Ammonia NH4 9.245 5.69 10 9.26 N ϩ H3 N ϩ H2 ϫ Ϫ2 1.823 (CO2H) 1.50 10 2.03 CHCH CH CH NHC ϫ Ϫ9 Arginine 2 2 2 8.991 (NH3) 1.02 10 9.00 NH —— (NH2) —— (12.1) CO2H 2 O Ϫ 2.24 5.8 ϫ 10 3 2.15 Ϫ Arsenic acid HO As OH 6.96 1.10 ϫ 10 7 6.65 Ϫ (hydrogen arsenate) (11.50) 3.2 ϫ 10 12 (11.18) OH ϫ Ϫ10 Arsenious acid As(OH)3 9.29 5.1 10 9.14 (hydrogen arsenite) N ϩ O H3 Asparagine CHCH2CNH2 —— —— 2.16 (CO2H) —— —— 8.73 (NH3) CO2H *Each acid is written in its protonated form. -
Hydrolysis and Atmospheric Oxidation Reactions of Perfluorinated Carboxylic Acid Precursors
Hydrolysis and Atmospheric Oxidation Reactions of Perfluorinated Carboxylic Acid Precursors by Derek A. Jackson A thesis submitted in conformity with the requirements for the degree of Doctor of Philosophy Graduate Department of Chemistry University of Toronto © Copyright by Derek A. Jackson 2013 Hydrolysis and Atmospheric Oxidation Reactions of Perfluorinated Carboxylic Acid Precursors Derek Andrew Jackson Doctor of Philosophy Department of Chemistry University of Toronto 2013 Abstract This dissertation explores a number of different environmentally relevant reactions that lead to the production of perfluorocarboxylic acids (PFCAs), a family of environmental pollutants that does not undergo any further degradation pathways. The compound perfluoro-2-methyl-3-pentanone (PFMP) is a new fire fighting fluid developed by 3M that is designed as a Halon replacement. The environment fate of PFMP with regards to direct photolysis, abiotic hydrolysis and hydration was determined using a combination of laboratory experiments and computational modeling. PFMP was found to undergo direct photolysis giving a lifetime of 4-14 days depending on latitude and time of year. Offline samples confirmed PFCA products and a mechanism was proposed. Polyfluorinated amides (PFAMs) are a class of chemicals produced as byproducts of polyfluorinated sulfonamide synthesis via electrochemical fluorination (ECF). Using synthesized standards of four model compounds, PFAMs were detected and quantified in a variety of legacy commercial materials synthesized by ECF. PFAMs were hypothesized to undergo biological hydrolysis reactions, suggesting their importance as historical PFOA precursors. ii The PFAMs were also investigated with regards to their environmental fate upon atmospheric oxidation. Using a smog chamber, the kinetics and degradation mechanisms of N- ethylperfluorobutyramide (EtFBA) were elucidated. -
United States Patent 19 11 4,289,699 Oba Et Al
United States Patent 19 11 4,289,699 Oba et al. 45 Sep. 15, 1981 54 PROCESS FOR THE PRODUCTION OF Primary Examiner-Donald G. Daus N-(HYDROXYPHENYL) MALEIMEDES Assistant Examiner-D. B. Springer 75 Inventors: Masayuki Oba; Motoo Kawamata; Attorney, Agent, or Firm-Fisher, Christen & Sabol Hikotada Tsuboi; Nobuhito Koga, all 57 ABSTRACT of Yokohama, Japan N-(hydroxyphenyl) maleimides of the general formula 73 Assignee: Mitsui Toatsu Chemicals, Incorporated, Tokyo, Japan 21 Appl. No.: 88,825 (22 Filed: Oct. 26, 1979 N CO-m-CH Related U.S. Application Data (HO) 62) Division of Ser. No. 956,971, Nov. 2, 1978, Pat. No. 4,231,934. where R' stands for H, CH3, C2H5, F, Cl, Br or I and in 30 Foreign Application Priority Data is an integer of 1-5 are produced by treating the corre sponding maleamic acid or by treating the ester of said Nov. 2, 1977 (JP) Japan ................................ 52-130905 N-(hydroxyphenyl) maleimide at a temperature of Nov. 4, 1977 (JP Japan ................................ 52-3504 0-150° C. in the presence of at least one dehydrating 51) Int. Cl. .......................................... C07D 207/.452 agent selected for the group consisting of oxides and (52) U.S. Cl. .......................................... 260/326.5 FM oxyacids of sulfur or phosphorus and alkali metal and 58) Field of Search .............................. 260/326.5 FM alkaline earth metal salts of the said oxyacids. The cor responding maleamic acid can be obtained by reacting 56) - References Cited an aminophenol having one or more hydroxyl groups U.S. PATENT DOCUMENTS on its phenyl nucleus with maleic anhydride. -
An Interstellar Synthesis of Phosphorus Oxoacids
ARTICLE DOI: 10.1038/s41467-018-06415-7 OPEN An interstellar synthesis of phosphorus oxoacids Andrew M. Turner1,2, Alexandre Bergantini 1,2, Matthew J. Abplanalp1,2, Cheng Zhu 1,2, Sándor Góbi 1,2, Bing-Jian Sun3, Kang-Heng Chao3, Agnes H.H. Chang3, Cornelia Meinert 4 & Ralf I. Kaiser 1,2 Phosphorus signifies an essential element in molecular biology, yet given the limited solubility of phosphates on early Earth, alternative sources like meteoritic phosphides have been proposed to incorporate phosphorus into biomolecules under prebiotic terrestrial conditions. Here, we report on a previously overlooked source of prebiotic phosphorus from interstellar 1234567890():,; phosphine (PH3) that produces key phosphorus oxoacids—phosphoric acid (H3PO4), phos- phonic acid (H3PO3), and pyrophosphoric acid (H4P2O7)—in interstellar analog ices exposed to ionizing radiation at temperatures as low as 5 K. Since the processed material of molecular clouds eventually enters circumstellar disks and is partially incorporated into planetesimals like proto Earth, an understanding of the facile synthesis of oxoacids is essential to untangle the origin of water-soluble prebiotic phosphorus compounds and how they might have been incorporated into organisms not only on Earth, but potentially in our universe as well. 1 Department of Chemistry, University of Hawaii at Manoa, Honolulu, HI 96822, USA. 2 W.M. Keck Laboratory in Astrochemistry, University of Hawaii at Manoa, Honolulu, HI 96822, USA. 3 Department of Chemistry, National Dong Hwa University, Shoufeng, 974 Hualien, Taiwan. 4 Université Côte d’Azur, CNRS, Institut de Chimie de Nice, Nice, France. Correspondence and requests for materials should be addressed to R.I.K. -
Scientific Opinion on the Safety Evaluation of the Active Substances
EFSA Journal 2013;11(6):3245 SCIENTIFIC OPINION Scientific Opinion on the safety evaluation of the active substances, iron, polyethyleneglycol, disodium pyrophosphate, monosodium phosphate and sodium chloride for use in food contact materials1 EFSA Panel on Food Contact Materials, Enzymes, Flavourings and Processing Aids (CEF)2, 3 European Food Safety Authority (EFSA), Parma, Italy ABSTRACT This scientific opinion of EFSA Panel on Food Contact Materials, Enzymes, Flavourings and Processing Aids deals with the safety evaluation of an iron based oxygen absorber, comprising polyethyleneglycol, disodium pyrophosphate, monosodium phosphate and sodium chloride. This mixture is incorporated in polyethylene (PE) or polypropylene (PP) articles intended to be in contact with foodstuffs for hot fill/pasteurisation and/or long term storage at room temperature. For dried and fatty foods, direct contact with the materials is envisaged whereas other food types will be separated from the active material by a layer that does not contain the active components. All the substances constituting the oxygen absorber system have been evaluated and authorised for use as plastic food contact materials, as food additives or as food supplements. Based on migration results, the specific migration limits for iron, polyethyleneglycol, pyrophosphoric acid salts, phosphoric acid salts and sodium chloride, and the tolerable intake of phosphorus (phosphate) are not expected to be exceeded when the oxygen absorber system is used under the intended conditions of use, notably -
19650003847.Pdf
NATIONAL BUREAU OF STANDARDS REPO RT 8595 PRELIMINARY REPORT ON A SURVEY OF THERMODYNAMIC PROPERTIES OF THE COMPOUNDS OF THE ELEMENTS CHNOPS i N65 2 CACC£S$IO NUMB£:R) CTHRU) ~ ___f£ / I- (PAGES) (CdOEI ::; ~ CIU - d -P?02c2/ :33 (NASA CR OR TMX OR AD NUMBER) (CATEQORY) Progress Report for the Period 1 August to 31 October 1964 to National Aeronautics and Space Administration GPO PRICE $ _____ OTS PRICE(S) $ 1 November 1964 Hard copy (He) of· cJV r Microfiche (MF) __....;... : .:::.j~I?J~_ <@> U.S. DEPARTMENT OF COMMERCE NATIONAL BUREAU OF STANDARDS THE NATIONAL BUREAU OF STANDARD S The ational Bureau of Standards is a principal focal point in the Federal Government for assuring maximum application of the physical and engineering sciences to the advancement of technology in industry and commerce. It responsibilities include development and main tena nce of the national stand· ards of measurement, and the provisions of means for making measurements consi tent with those standard ; determination of physical constants and properties of materials; development of methods for testing materials, mechanisms, and structures, and making such tests as may be nece sary, particu larl: for ~overn ment agencies; cooperation in the establi hment of standard practices for incorpora tion in codes and specifications; advisory service to government agencies on scientific and technical problems; invention and development of device to serve special needs of the Government: assi tance to indus! r). business. and consumers in the development and acceptance of commercial tandard and simplified trade practice recommendations; administration of programs in cooperation with United tates bu iness groups and standards organizations for the development of international standard of practice; and maintenance of a clearinghouse for the collection and dis emination of scientific, tech nical. -
1301:7-9-03 Reporting Requirements for Hazardous Substances and List of Hazardous Substances
1301:7-9-03 Reporting requirements for hazardous substances and list of hazardous substances. (A) Purpose. For the purpose of prescribing rules pursuant to section 3737.88 of the Revised Code, the fire marshal hereby adopts this rule to establish reporting requirements for underground storage tank systems that contain hazardous substance(s) and to list those substances which are hereby identified as hazardous substances. This rule is adopted by the fire marshal in accordance with Chapter 119. of the Revised Code and shall not be considered a part of the "Ohio Fire Code". (B) Definitions. For the purpose of this rule: (1) "Release of a hazardous substance" means: (a) Any spilling, leaking, emitting, discharging, escaping, leaching or disposing of a hazardous substance(s) from an underground storage tank system into the ground water, a surface water body, subsurface soils or otherwise into the environment; (b) Any spilling, leaking, emitting, discharging, escaping, or disposing of a hazardous substance(s) into ground water, a surface water body, subsurface soils or otherwise into the environment while transferring or attempting to transfer a hazardous substance(s) into an underground storage tank system; or (c) Contamination of subsurface soils or ground water on the UST site by a hazardous substance(s) found and confirmed through laboratory analysis of samples from the UST site. (2) "Suspected release of a hazardous substance" means evidence of a release of a hazardous substance(s) obtained through one or more of the following events: (a) -
LIGAND FORMULA INDEX Order of Elements: C,Il,O,N, Others In
LIGAND FORMULA INDEX Order of elements: C,Il,O,N, others in alphabetical order. - AsF6 74 HO 1 Br - 115 HOBr 134 Br6Ir 135 HOC1 134 HOI 134 CHON 28 H02N 47 CHN 26 H0 2C1 134 CHNS 29 H031 126 CH203 37 H04NF 2S2 135 - CH2N2 135 H0 4S 79 CH2S3 131 H0 4Se 93 CH2S4 131 H0 4Tc 135 CH2Se3 131 HF 96 CNSe 35 HN3 45 C2N3 36 H20Z 75 C4H204Fe 135 H2OZN2 53, 135 - C4N3 36 H203N2 135 C5H05Mn 135 H203FP 132 C6H4 N6Fe 21 H203S 78 3- C6N6Co 24 HZ03SZ 86 3- C6N6Fe 22 HZ03Se 91 C8H3N8W 135 H204Cr 17 C8H4N8W 135 H204Mn 135 H204Mo 18 C1 104 H204S2 135 3- C1 6Ir 135 H204W 19 H205S 133 F6P 74 H208S2 89 253 254 LIGAND FORMULA INDEX H2S 76 H4N2 43 H2S4 133 H50NlS 132 H2S5 133 H502Nl 132 H2Se 90 H505Sb 133 H2Te 94 H505Ta 135 H30N 44 H506NP 2 71 H302P 54 H5061 129 H303NS 88 H501oP3 63 H303As 132 H606N3P3 72 H303B 25 H606Te 134 H30l 55 H6013P4 66 H30lS 132 H6018P6 70 H304NS 133 H708Nl3 71 H304As 133 H7016P5 135 H304P 56 H8019Nb 6 131 H304V 15 H8019P6 135 H305P 131 H8024P8 70 H309P3 68 H1604l14 135 H3N 40 H620121P60 135 HlS4 132 H403NP 132 I 122 H404Ge 131 H404Si 39 ON 135 H 0 Te - 4 4 95 °3N 48 H 0 P 4 6 2 72, 73 °3Br 121 H 0 P S 4 6 2 2 135 °3C1 113 H 0 P 2- 4 7 2 59 °3SSe 88 H 0 P 4 8 2 73 °4C1 114 H 0 FP - 4 9 3 135 °4Mn 135 H 0 P 69 - 4 12 4 °4Re 20 LIGAND NAME INDEX Ammonia, 40 Hydrogen amidophosphate, 132 Antimonic acid, 133 Hydrogen amidosu1fate, 88 Arsenic acid, 133 Hydrogen antimonate, 133 Arsenous acid, 132 Hydrogen arsenate, 133 Hydrogen arsenite, 132 Boric acid, 25 Hydrogen azide, 45 Bromate ion, 121 Hydrogen borate, 25 Bromide ion, 115 Hydrogen carbonate, -
United States Patent Office Atented Sept
3,151,150 United States Patent Office atented Sept. 28, 1964 1. 2 cussed in Chemical Week (September 27, 1958), pp. 3,554,450 53-54, Chemical Engineering (June 1, 1957), pp. 42-44, PROCESS FOR THE MANUEFACTURE OF ACRYELONTRLE Chemical and Engineering News (December 1, 1958), pp. onas Karact, New York, N.Y.; Edna Yadven. Kamiet, 49 and 98, and by Sennewald and Steil in Chemie-In executrix of said Josias Kanet, deceased, assignor, by genieur-Technik, 30, #7, 440-446 (1958). mesne assign eats, to Edia Y. Kaanet, doing business It is the purpose of my invention to provide a process as The Kainie Laboratories, New York, N.Y. for the manufacture of acrylonitrile from acetaldehyde No Drawing. Fied Sept. 4, 1959, Ser. No. 839,570 and hydrogen cyanide which does not require reagents 4 Clains. (C. 260-465.9) other than acetaldeyhde and HCN and does not involve O by-product recovery, which does not require concentra This invention relates to a process for the manufacture tion and re-constitution of intermediates, and which gives of acrylonitrile. More particularly, this invention relates yields in excess of 90% of theory. to a process whereby acrylonitrile may be manufactured, The basis of my invention is the finding that acryloni in good yields, from cheap and readily available industrial trile may be obtained in excellent yield by the steps of: intermediates-acetaldehyde and hydrogen cyanide. (a) reacting lactonitrile (made from acetaldehyde and hy Acrylonitrile has become an extremely important chem drogen cyanide) with pre-formed acrylonitrile, in the ical article of commerce, widely used in the manufacture, presence of a basic catalyst, to form alpha,beta'-dicyano of synthetic rubbers, plastics, fibers, films, plasticizers, dye diethyl ether (alpha,beta'-oxydipropionitrile): stuffs, pharmaceuticals, solvents and other products. -
United States Patent Office 202,838
Patented Jan. 14, 1936 2,027,838 UNITED STATES PATENT OFFICE 202,838. sTABILIZING HYDROGENPEROXDE solu TONS WITH PYROPHOSPORIC ACD Joseph S. Reichert, Niagara Falls, N.Y., assignor to E. I. du Pont de Nemours & Company, Inc., Wilmington, Del, a corporation of Delaware 49 No Drawing. Application September 12, 1932, Seria No. 632,796 8 Claims. (CI. 23-251) This invention relates to the stabilization of shipped in commerce, i.e. about 10-volume or hydrogen peroxide solutions and more specifi-. higher, and to provide a high concentration per cally to the stabilization of the high concentra oxide solution which can be shipped and stored tion acid hydrogen peroxide Solution as COm for relatively long periods without serious losses. monly transported. I have discovered that pyrophosphoric acid is In general it should be stated that hydrogen an excellent stabilizer for hydrogen peroxide sor peroxide solutions are of two kinds, the first lutions of the nature described above. By stabil those which are transported and which are usu izing hydrogen peroxide solutions with pyropros ally of relatively high concentrations, e. g. 10 phoric acid, the combined stabilizing effect of voluné or stronger, and which have been acidi the hydrogen ion and the pyrophosphate ion is 10 10 fied in Order to have maximum stability, and obtained. Hydrogen peroxide solutions stabilized secondly, the more dilute, alkaline hydrogen per with pyrophosphoric acid show only very small Oxide Solutions, losses when stored for long periods of time even bleaching purposes.as . are. commonly used for at temperatures higher than the normal storage 5 For bleaching purposes it has been found more temperature. -
Which the Phosphorylating Entity Derives from a Diester of Phosphoric Acid, and (2) Downloaded by Guest on September 25, 2021 1390 CHEMISTRY: A
VOL. 45, 1959 CHEMISTRY: A. TODD 1389 14 Jervis, R. E., D. R. Muir, J. P. Butler, and A. R. Gordon, J. Am. Chem. Soc., 75, 2855 (1953); Davies, J. A., R. L. Kay, and A. R. Gordon, J. Chem. Phys., 19, 149 (1951). 15 Sadek, H., and R. M. Fuoss, J. Am. Chem. Soc., 76,5897 (1954). 16 Evers, C. E., and A. G. Knox, J. Am. Chem. Soc., 73, 1739 (1951). 17 Gilkerson, W. R., J. Chem. Phys., 25, 1199 (1956). 18 Accascina, F., A. D'Aprano, and R. M. Fuoss, J. Am. Chem. Soc., 81, 1058 (1959). 19 Fuoss, R. M., J. B. Berkowitz, E. Hirsch, and S. Petrucci, these PROCEEDINGS, 41, 27 (1958). 20 Ref. 1, Table 17.1, p. 241. 21 Mead, D. J., R. M. Fuoss, and C. A. Kraus, Trans. Faraday Soc., 32, 594 (1936); Tucker, L. M., and C. A. Kraus, J. Am. Chem. Soc., 69, 454 (1947). 22 Burgess, D. S., and C. A. Kraus, J. Am. Chem. Soc., 70, 706 (1948); Luder, W. F., and C. A. Kraus, ibid., 69, 248 (1947). 23 McDowell, M. J., and C. A. Kraus, J. Am. Chem. Soc., 73, 329 (1951); Reynolds, M. B., and C. A. Kraus, Ibid., 70, 1709 (1948). 24 Fuoss, R. M., and C. A. Kraus, J. Am. Chem. Soc., 79, 3304 (1957). SOME ASPECTS OF PHOSPHATE CHEMISTRY* By SIR ALEXANDER TODD UNIVERSITY CHEMICAL LABORATORY, CAMBRIDGE, ENGLAND Communicated July 17, 1959 During the past fifteen to twenty years a very large amount of work has been done on organic phosphates and polyphosphates.