Empennage Statistics and Sizing Methods for Dorsal Fins
Total Page:16
File Type:pdf, Size:1020Kb
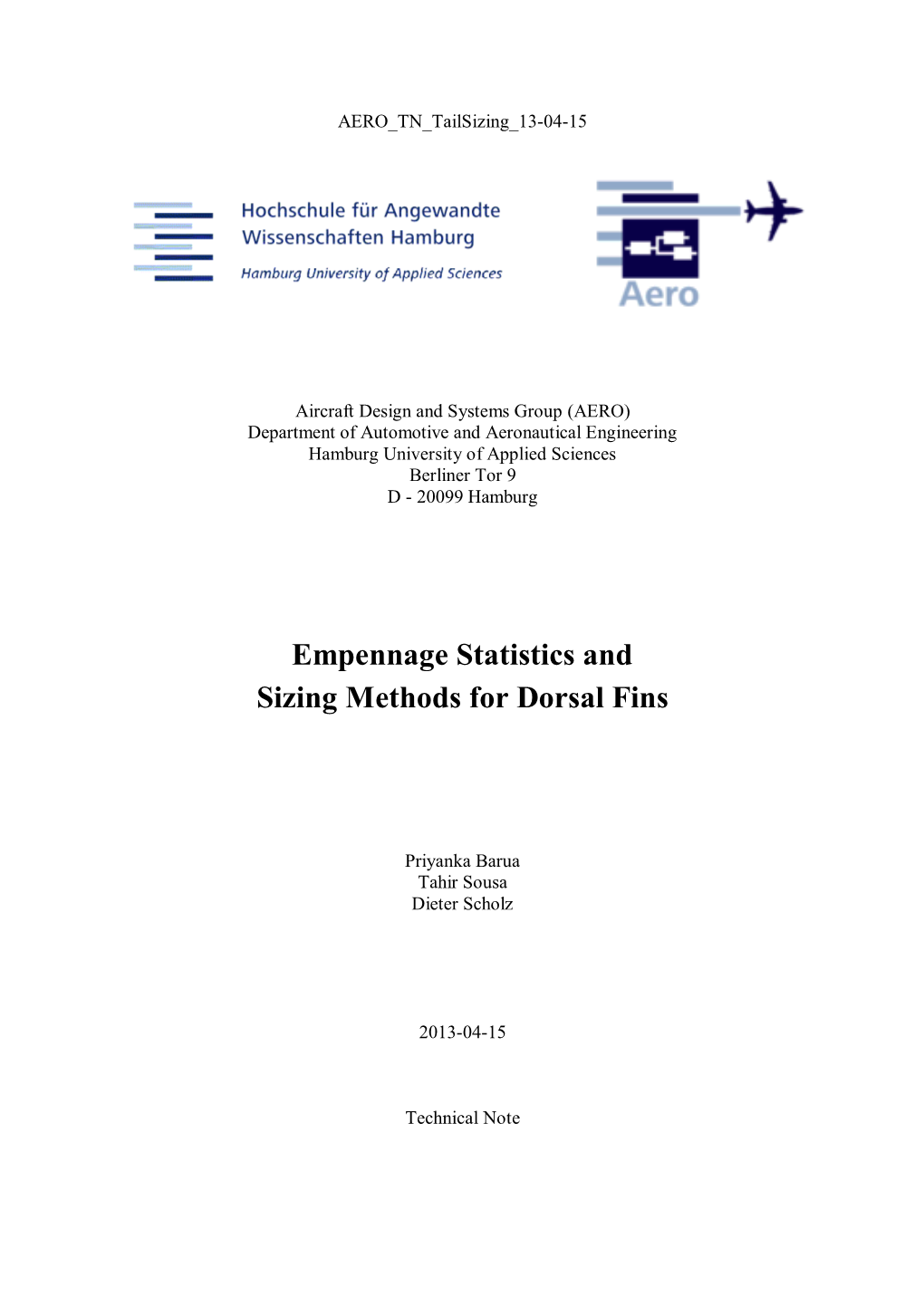
Load more
Recommended publications
-
CAAM 3 Report
3rd Technical Report On Propulsion System and Auxiliary Power Unit (APU) Related Aircraft Safety Hazards A joint effort of The Federal Aviation Administration and The Aerospace Industries Association March 30, 2017 Questions concerning distribution of this report should be addressed to: Federal Aviation Administration Manager, Engine and Propeller Directorate. TABLE OF CONTENTS Page Table of Contents iii List of Figures v I. Foreword 1 II. Background 1 III. Scope 2 IV. Discussion 3 V. Relationship to Previous CAAM Data 7 VI. General Notes and Comments 8 VII. Fleet Utilization 11 VIII. CAAM3 Team Members 12 IX. Appendices List of Appendices 13 Appendix 1: Standardized Aircraft Event Hazard Levels and Definitions 14 • General Notes Applicable to All Event Hazard Levels 19 • Rationale for Changes in Severity Classifications 19 • Table 1. Historical Comparison of Severity Level Descriptions and Rationale for CAAM3 Changes 21 Appendix 2: Event Definitions 39 Appendix 3: Propulsion System and Auxiliary Power Unit (APU) Related Aircraft Safety Hazards (2001 through 2012) 44 • Uncontained Blade 44 • Uncontained Disk 50 • Uncontained – Other 56 iii • Uncontained – All Parts 62 • High Bypass Comparison by Generation 63 • Relationship Among High Bypass Fleet 64 • Case Rupture 66 • Case Burnthrough 69 • Under-Cowl Fire 72 • Strut/Pylon Fire 76 • Fuel Leak 78 • Engine Separation 82 • Cowl Separation 85 • Propulsion System Malfunction Recognition and Response (PSMRR) 88 • Crew Error 92 • Reverser/Beta Malfunction – In-Flight Deploy 96 • Fuel Tank Rupture/Explosion 99 • Tailpipe Fire 102 • Multiple-Engine Powerloss – Non-Fuel 107 • Multiple-Engine Powerloss – Fuel-Related 115 • Fatal Human Ingestion / Propeller Contact 120 • IFSD Snapshot by Hazard Level – 2012 Data Only 122 • RTO Snapshot by Hazard Level – 2012 Data Only 123 • APU Events 123 • Turboprop Events 124 • Matrices of Event Counts, Hazard Ratios and Rates 127 • Data Comparison to Previous CAAM Data 135 [ The following datasets which were collected in CAAM2 were not collected in CAAM3. -
Home at Airbus
Journal of Aircraft and Spacecraft Technology Original Research Paper Home at Airbus 1Relly Victoria Virgil Petrescu, 2Raffaella Aversa, 3Bilal Akash, 4Juan M. Corchado, 2Antonio Apicella and 1Florian Ion Tiberiu Petrescu 1ARoTMM-IFToMM, Bucharest Polytechnic University, Bucharest, (CE), Romania 2Advanced Material Lab, Department of Architecture and Industrial Design, Second University of Naples, 81031 Aversa (CE), Italy 3Dean of School of Graduate Studies and Research, American University of Ras Al Khaimah, UAE 4University of Salamanca, Spain Article history Abstract: Airbus Commerci al aircraft, known as Airbus, is a European Received: 16-04-2017 aeronautics manufacturer with headquarters in Blagnac, in the suburbs of Revised: 18-04-2017 Toulouse, France. The company, which is 100% -owned by the industrial Accepted: 04-07-2017 group of the same name, manufactures more than half of the airliners produced in the world and is Boeing's main competitor. Airbus was Corresponding Author: founded as a consortium by European manufacturers in the late 1960s. Florian Ion Tiberiu Petrescu Airbus Industry became a SAS (simplified joint-stock company) in 2001, a ARoTMM-IFToMM, Bucharest subsidiary of EADS renamed Airbus Group in 2014 and Airbus in 2017. Polytechnic University, Bucharest, (CE) Romania BAE Systems 20% of Airbus between 2001 and 2006. In 2010, 62,751 Email: [email protected] people are employed at 18 Airbus sites in France, Germany, the United Kingdom, Belgium (SABCA) and Spain. Even if parts of Airbus aircraft are essentially made in Europe some come from all over the world. But the final assembly lines are in Toulouse (France), Hamburg (Germany), Seville (Spain), Tianjin (China) and Mobile (United States). -
The Effects of Design, Manufacturing Processes, and Operations Management on the Assembly of Aircraft Composite Structure by Robert Mark Coleman
The Effects of Design, Manufacturing Processes, and Operations Management on the Assembly of Aircraft Composite Structure by Robert Mark Coleman B.S. Civil Engineering Duke University, 1984 Submitted to the Sloan School of Management and the Department of Aeronautics and Astronautics in Partial Fulfillment of the Requirements for the Degrees of Master of Science in Management and Master of Science in Aeronautics and Astronautics in conjuction with the LEADERS FOR MANUFACTURING PROGRAM at the MASSACHUSETTS INSTITUTE OF TECHNOLOGY June 1991 © 1991, MASSACHUSETTS INSTITUTE OF TECHNOLOGY ALL RIGHTS RESERVED Signature of Author_ .• May, 1991 Certified by Stephen C. Graves Professor of Management Science Certified by A/roJ , Paul A. Lagace Profes s Aeron icand Astronautics Accepted by Jeffrey A. Barks Associate Dean aster's and Bachelor's Programs I.. Jloan School of Management Accepted by - No U Professor Harold Y. Wachman Chairman, Department Graduate Committee Aero Department of Aeronautics and Astronautics MASSACHiUSEITS INSTITUTE OFN Fr1 1'9n.nry JUJN 12: 1991 1 UiBRARIES The Effects of Design, Manufacturing Processes, and Operations Management on the Assembly of Aircraft Composite Structure by Robert Mark Coleman Submitted to the Sloan School of Management and the Department of Aeronautics and Astronautics in Partial Fulfillment of the Requirements for the Degrees of Master of Science in Management and Master of Science in Aeronautics and Astronautics June 1991 ABSTRACT Composite materials have many characteristics well-suited for aerospace applications. Advanced graphite/epoxy composites are especially favored due to their high stiffness, strength-to-weight ratios, and resistance to fatigue and corrosion. Research emphasis to date has been on the design and fabrication of composite detail parts, with considerably less attention given to the cost and quality issues in their subsequent assembly. -
University of Oklahoma Graduate College Design and Performance Evaluation of a Retractable Wingtip Vortex Reduction Device a Th
UNIVERSITY OF OKLAHOMA GRADUATE COLLEGE DESIGN AND PERFORMANCE EVALUATION OF A RETRACTABLE WINGTIP VORTEX REDUCTION DEVICE A THESIS SUBMITTED TO THE GRADUATE FACULTY In partial fulfillment of the requirements for the Degree of Master of Science Mechanical Engineering By Tausif Jamal Norman, OK 2019 DESIGN AND PERFORMANCE EVALUATION OF A RETRACTABLE WINGTIP VORTEX REDUCTION DEVICE A THESIS APPROVED FOR THE SCHOOL OF AEROSPACE AND MECHANICAL ENGINEERING BY THE COMMITTEE CONSISTING OF Dr. D. Keith Walters, Chair Dr. Hamidreza Shabgard Dr. Prakash Vedula ©Copyright by Tausif Jamal 2019 All Rights Reserved. ABSTRACT As an airfoil achieves lift, the pressure differential at the wingtips trigger the roll up of fluid which results in swirling wakes. This wake is characterized by the presence of strong rotating cylindrical vortices that can persist for miles. Since large aircrafts can generate strong vortices, airports require a minimum separation between two aircrafts to ensure safe take-off and landing. Recently, there have been considerable efforts to address the effects of wingtip vortices such as the categorization of expected wake turbulence for commercial aircrafts to optimize the wait times during take-off and landing. However, apart from the implementation of winglets, there has been little effort to address the issue of wingtip vortices via minimal changes to airfoil design. The primary objective of this study is to evaluate the performance of a newly proposed retractable wingtip vortex reduction device for commercial aircrafts. The proposed design consists of longitudinal slits placed in the streamwise direction near the wingtip to reduce the pressure differential between the pressure and the suction sides. -
79952 Federal Register / Vol
79952 Federal Register / Vol. 75, No. 244 / Tuesday, December 21, 2010 / Rules and Regulations Unsafe Condition DEPARTMENT OF TRANSPORTATION 1601 Lind Avenue, SW., Renton, (d) This AD was prompted by an accident Washington 98057–3356; telephone and the subsequent discovery of cracks in the Federal Aviation Administration (425) 227–1137; fax (425) 227–1149. main rotor blade (blade) spars. We are issuing SUPPLEMENTARY INFORMATION: 14 CFR Part 39 this AD to prevent blade failure and Discussion subsequent loss of control of the helicopter. [Docket No. FAA–2009–0864; Directorate We issued a supplemental notice of Compliance Identifier 2008–NM–202–AD; Amendment 39–16544; AD 2010–26–05] proposed rulemaking (NPRM) to amend (e) Before further flight, unless already 14 CFR part 39 to include an AD that done: RIN 2120–AA64 would apply to the specified products. (1) Revise the Limitations section of the That supplemental NPRM was Airworthiness Directives; DASSAULT Instructions for Continued Airworthiness by published in the Federal Register on AVIATION Model Falcon 10 Airplanes; establishing a life limit of 8,000 hours time- July 27, 2010 (75 FR 43878). That Model FAN JET FALCON, FAN JET in-service (TIS) for each blade set Remove supplemental NPRM proposed to FALCON SERIES C, D, E, F, and G each blade set with 8,000 or more hours TIS. correct an unsafe condition for the Airplanes; Model MYSTERE-FALCON (2) Replace each specified serial-numbered specified products. The MCAI states: 200 Airplanes; Model MYSTERE- blade set with an airworthy blade set in During maintenance on one aircraft, it was accordance with the following table: FALCON 20–C5, 20–D5, 20–E5, and 20– F5 Airplanes; Model FALCON 2000 and discovered that the overpressure capsules were broken on both pressurization valves. -
1.1 Goals and Objectives
Chapter One INVENTORY Rock Hill/York County Airport (Bryant Field – UZA) (the Airport) is a publicly owned general aviation facility located approximately four miles north of the central business district of the City of Rock Hill, South Carolina (the City, refer to Figures 1-1 and 1-2, pages 1-2 and 1-3). The Airport is owned and operated by the City of Rock Hill. In order to establish a planning guideline for future airport development, the owner has contracted this Airport Master Plan (Master Plan), which will satisfy future aviation demand in a financially feasible manner. 1.1 GOALS AND OBJECTIVES The Airport Master Plan presents both short- and long-term development for the Airport and graphically displays and reports the data and logic upon which the Master Plan is based. The goal of the Master Plan is to provide guidelines for future airport development, which will satisfy aviation demand in a cost-effective, feasible manner, while resolving aviation, environmental, and socioeconomic issues of the community. Objectives are attainable targets that are action-oriented and designed to address specific elements consistent with attainment of the goal. The objectives for Rock Hill/York County Airport (Bryant Field) are based on an initial evaluation of the Airport and its surrounding environs and meetings with Airport staff, City staff, South Carolina Department of Commerce Division of Aeronautics (SCDOA), and Federal Aviation Administration (FAA). As information is developed during data gathering efforts, objectives for the Airport Master -
Electrically Heated Composite Leading Edges for Aircraft Anti-Icing Applications”
UNIVERSITY OF NAPLES “FEDERICO II” PhD course in Aerospace, Naval and Quality Engineering PhD Thesis in Aerospace Engineering “ELECTRICALLY HEATED COMPOSITE LEADING EDGES FOR AIRCRAFT ANTI-ICING APPLICATIONS” by Francesco De Rosa 2010 To my girlfriend Tiziana for her patience and understanding precious and rare human virtues University of Naples Federico II Department of Aerospace Engineering DIAS PhD Thesis in Aerospace Engineering Author: F. De Rosa Tutor: Prof. G.P. Russo PhD course in Aerospace, Naval and Quality Engineering XXIII PhD course in Aerospace Engineering, 2008-2010 PhD course coordinator: Prof. A. Moccia ___________________________________________________________________________ Francesco De Rosa - Electrically Heated Composite Leading Edges for Aircraft Anti-Icing Applications 2 Abstract An investigation was conducted in the Aerospace Engineering Department (DIAS) at Federico II University of Naples aiming to evaluate the feasibility and the performance of an electrically heated composite leading edge for anti-icing and de-icing applications. A 283 [mm] chord NACA0012 airfoil prototype was designed, manufactured and equipped with an High Temperature composite leading edge with embedded Ni-Cr heating element. The heating element was fed by a DC power supply unit and the average power densities supplied to the leading edge were ranging 1.0 to 30.0 [kW m-2]. The present investigation focused on thermal tests experimentally performed under fixed icing conditions with zero AOA, Mach=0.2, total temperature of -20 [°C], liquid water content LWC=0.6 [g m-3] and average mean volume droplet diameter MVD=35 [µm]. These fixed conditions represented the top icing performance of the Icing Flow Facility (IFF) available at DIAS and therefore it has represented the “sizing design case” for the tested prototype. -
Vanished Planes
FIU Law Review Volume 10 Number 2 Article 13 Spring 2015 Vanished Planes Robert M. Jarvis Nova Southeastern University Follow this and additional works at: https://ecollections.law.fiu.edu/lawreview Part of the Other Law Commons Online ISSN: 2643-7759 Recommended Citation Robert M. Jarvis, Vanished Planes, 10 FIU L. Rev. 519 (2015). DOI: https://dx.doi.org/10.25148/lawrev.10.2.13 This Article is brought to you for free and open access by eCollections. It has been accepted for inclusion in FIU Law Review by an authorized editor of eCollections. For more information, please contact [email protected]. 37333-fiu_10-2 Sheet No. 86 Side A 01/11/2016 08:19:25 JARVIS (DO NOT DELETE)1/4/166:38PM Vanished Planes Robert M. Jarvis* I. INTRODUCTION The history of aviation is marked by aircraft that have disappeared without a trace.1 Such flights leave a host of legal issues in their wake, and * Professor of Law, Nova Southeastern University ([email protected]). 1 It generally is agreed that Matías Pérez was the first person in history to vanish in flight—on June 29, 1856, he took off from Havana, Cuba, in a hot air balloon and was never seen again. Even today, when someone or something disappears, it is common for locals to invoke Pérez’s name. See Emma Álvarez-Tabío Albo, The City in Midair, in HAVANA BEYOND THE RUINS:CULTURAL MAPPINGS AFTER 1989, at 149, 167 (Anke Birkenmaier & Esther Vhitfield eds., Eric Felipe-Barkin trans., 2011) (explaining that Pérez “is immortalized in the colloquial phrase ‘Voló como Matías Pérez’ (He flew [away] like Matías Pérez)”). -
Of the 90 YEARS of the RAAF
90 YEARS OF THE RAAF - A SNAPSHOT HISTORY 90 YEARS RAAF A SNAPSHOTof theHISTORY 90 YEARS RAAF A SNAPSHOTof theHISTORY © Commonwealth of Australia 2011 This work is copyright. Apart from any use as permitted under the Copyright Act 1968, no part may be reproduced by any process without prior written permission. Inquiries should be made to the publisher. Disclaimer The views expressed in this work are those of the authors and do not necessarily reflect the official policy or position of the Department of Defence, the Royal Australian Air Force or the Government of Australia, or of any other authority referred to in the text. The Commonwealth of Australia will not be legally responsible in contract, tort or otherwise, for any statements made in this document. Release This document is approved for public release. Portions of this document may be quoted or reproduced without permission, provided a standard source credit is included. National Library of Australia Cataloguing-in-Publication entry 90 years of the RAAF : a snapshot history / Royal Australian Air Force, Office of Air Force History ; edited by Chris Clark (RAAF Historian). 9781920800567 (pbk.) Australia. Royal Australian Air Force.--History. Air forces--Australia--History. Clark, Chris. Australia. Royal Australian Air Force. Office of Air Force History. Australia. Royal Australian Air Force. Air Power Development Centre. 358.400994 Design and layout by: Owen Gibbons DPSAUG031-11 Published and distributed by: Air Power Development Centre TCC-3, Department of Defence PO Box 7935 CANBERRA BC ACT 2610 AUSTRALIA Telephone: + 61 2 6266 1355 Facsimile: + 61 2 6266 1041 Email: [email protected] Website: www.airforce.gov.au/airpower Chief of Air Force Foreword Throughout 2011, the Royal Australian Air Force (RAAF) has been commemorating the 90th anniversary of its establishment on 31 March 1921. -
DASSAULT AVIATION Model Falcon 10 Airplanes
43878 Federal Register / Vol. 75, No. 143 / Tuesday, July 27, 2010 / Proposed Rules Applicability New Requirements of This AD: Actions Bulletin SBF100–27–092, dated April 27, (c) This AD applies to Fokker Services B.V. (h) Within 30 months after the effective 2009; and Goodrich Service Bulletin 23100– Model F.28 Mark 0100 airplanes, certificated date of this AD, do the actions specified in 27–29, dated November 14, 2008; for related in any category, all serial numbers. paragraphs (h)(1) and (h)(2) of this AD information. concurrently. Accomplishing the actions of Issued in Renton, Washington, on July 21, Subject both paragraphs (h)(1) and (h)(2) of this AD 2010. (d) Air Transport Association (ATA) of terminates the actions required by paragraph Jeffrey E. Duven, America Code 27: Flight Controls. (g) of this AD. (1) Remove the tie-wrap, P/N MS3367–2– Acting Manager, Transport Airplane Reason 9, from the lower bolts of the horizontal Directorate, Aircraft Certification Service. (e) The mandatory continuing stabilizer control unit, in accordance with the [FR Doc. 2010–18399 Filed 7–26–10; 8:45 am] airworthiness information (MCAI) states: Accomplishment Instructions of Fokker BILLING CODE 4910–13–P Two reports have been received where, Service Bulletin SBF100–27–092, dated April during inspection of the vertical stabilizer of 27, 2009. F28 Mark 0100 aeroplanes, one of the bolts (2) Remove the lower bolts, P/N 23233–1, DEPARTMENT OF TRANSPORTATION that connect the horizontal stabilizer control of the horizontal stabilizer control unit and unit actuator with the dog-links was found install bolts, P/N 23233–3, in accordance Federal Aviation Administration broken (one on the nut side & one on the with the Accomplishment Instructions of Goodrich Service Bulletin 23100–27–29, head side). -
Avions Civils
SOMMAIRE DU VOLUME I LA CONDUITE DES PROGRAMMES CIVILS AVANT-PROPOS ET REMERCIEMENTS........................................................................... 3 PREFACE.............................................................................................................................. 5 PRESENTATION GENERALE ............................................................................................. 9 CHAPITRE 1 PRESENTATION DE L’ACTIVITE...................................................................................... 11 LE MARCHE DU TRANSPORT AERIEN .................................................................................. 11 Le passager et l’évolution du trafic.......................................................................................... 11 Les compagnies et la flotte d’avions ....................................................................................... 13 LA CONSTRUCTION DES AVIONS CIVILS .............................................................................. 14 Les caractéristiques de l’activité.............................................................................................. 14 La compétition et son évolution............................................................................................... 18 La dimension économique et monétaire ................................................................................. 20 L’ ADMINISTRATION ET SES MISSIONS ................................................................................. 22 La tutelle militaire de -
Aeronautical Engineering
NASA SP-7037 (36) ND AERONAUTICAL ENGINEERING A SPECIAL BIBLIOGRAPHY WITH INDEXES Supplement 36 OCTOBER 1973 ZkS&-Sp-7037 (36) EROAUTIC&L N74-14702 0GIEEG A SPCILL BIBLIOGMPHY WITH INDEXES, SUPPLENgIT 36 (N3AS) $5.25 Unclas 00/01 27136 NATIONAL AERONAUTICS AND SPACE ADMINISTRATION ACCESSION NUMBER RANGES Accession numbers cited in this Supplement fall within the following ranges: IAA (A-10000 Series) A73-34073 -- A73-37144 STAR (N-10000 Series) N73-25997 - N 73-27884 This bibliography was prepared by the NASA Scientific and Technical Information Facility operated for the National Aeronautics and Space Administration by Informatics Tisco, Inc. The Administrator of the National Aeronautics and Space Administration has determined that the publication of this periodical is necessary in the transaction of the public business required by law of this Agency. Use of funds for printing this periodical has been approved by the Director of the Office of Management and Budget through July 1, 1974. N74-14702 AERONAUTICAL ENGINEERING - A SPECIAL BIBLIOGRAPHY (SUPPLEMENT 36) National Aeronautics and Space Administration Washington, DC Oct 73 N74-14702 1. Report No. 2. Governmmnt Accession No. 3. Recipient's Catalog No. NASA SP-7037 (36) 4. Titleand Subtitle 5. Report Date October 1973 AERONAUTICAL ENG INEERING e.Performing Organization Code A Special Bibliography (Supplement 36) 7. Author(s) 8. Performing Organization Report No. 10. Work Unit No. 9. Performing Organization Name and Address National Aeronautics and Space Administration 11. Contractor Grant No. Washington, D. C; 20546 13. Type of Report and Period Covered 12. Sponsoring Agency Name and Address 14. Sponsoring Agency Code 15.