Interaction of High Aspect-Ratio Micro-Pillars with Wall Turbulence
Total Page:16
File Type:pdf, Size:1020Kb
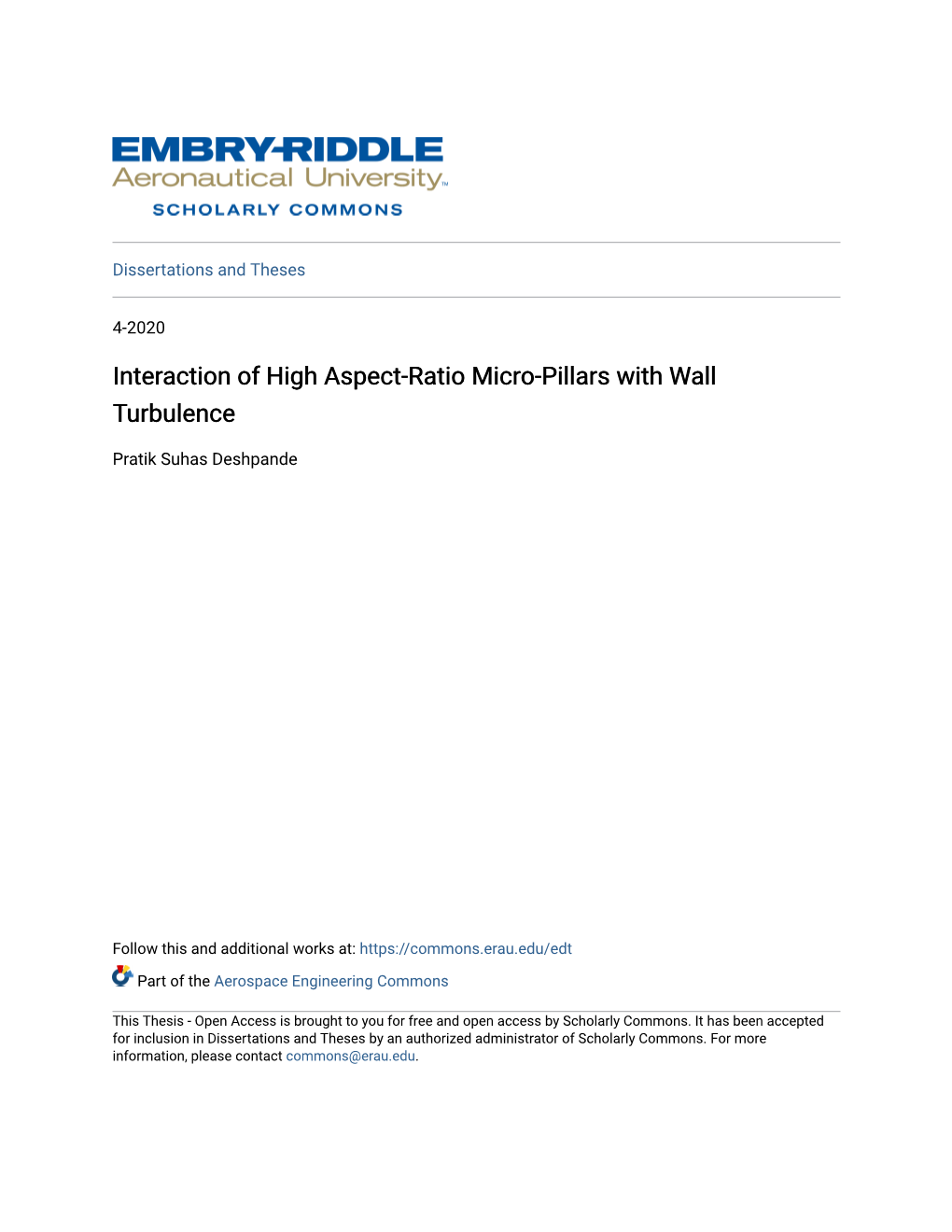
Load more
Recommended publications
-
TOC Page 1 TABLE of CONTENTS
Back to TOC Page 1 TABLE OF CONTENTS *** CLICK A TOPIC TO GO DIRECTLY TO THE PAGE *** DAYANG GROUP MEASUREMENT OPTIONS PARENT COMPANY 3 M4U - MADE FOR YOU 25 INTERNATIONAL PARTNERS 4 FIT TOOLS 26 PROPRIETARY FACTORIES 5 GARMENT MEASUREMENTS 27 PRODUCTION 6 POSTURE / BALANCE 28 CAPACITY 7 STYYLcart TAILORING QUALITY IMAGES ON DEMAND 29 UNPARALLELED VALUE 8 SELL WITH CONFIDENCE 30 CONSTRUCTION 9 CREATE SALES 31 GARMENT MAKES 10 SALES HISTORY 32 INTERIOR COMPONENTS 11 CUSTOM LINING FIT / PATTERN ULTIMATE PERSONALIZATION 33 MODERN FIT 12 SPECIAL OCCASIONS 34 RANGE OF FITS 13 CORPORATE SALES 35 JACKET 14 ART EXPRESSION 36 TROUSER 15 OVERCOAT 16 FABRICS IN STOCK 37 QUICK DELIVERY ITALIAN MILLS 38 IN STOCK / CMT FABRIC 17 ONLINE TRACKING 18 CMT WORK WITH THE FINEST 39 DESIGN DETAILS SELECTION 19 PRIVATE LABEL CATEGORY DETAILS 20 BRAND IDENTITY 40 MATERIALS PACKAGE 21 COMPETE 41 PRESET MODELS PRIVATE INVENTORY INCLUDED TEMPLATES 22 IMPROVED MARGIN 42 SAVE YOUR OWN 23 QUICK SAVE 24 WOMEN’S M4U NOT JUST FOR MEN 43 PRODUCTS 44 Back to TOC Page 2 DAYANG GROUP PARENT COMPANY Dayang Group is the Global Leader of MTM garment production. Founded in 1979 by Madam Li Giulian. Dayang now has 24 branch compa- nies. Back to TOC Page 3 DAYANG GROUP INTERNATIONAL PARTNERS Successful brands around the world choose Dayang as their manufacturing partner. Reliable, trustworthy and competent. Stability your business can count on. Back to TOC Page 4 DAYANG GROUP PROPRIETARY FACTORIES All factories are company-owned and operated. Garments are made to the company’s strict production standards. -
Pianta Della Fiera | Elenco Espositori 30^ Milano Unica
PIANTA DELLA FIERA | ELENCO ESPOSITORI General Map | List of exhibitors 30^ MILANO UNICA Primavera - Estate | Spring - Summer 2021 Febbraio / February 4.5.6, 2020 20 16 12 8 Porta Ovest Porta Est West Gate East Gate TIM Auditorium Centro Servizi Service Center Porta Sud South Gate TIM milanounica.it IDEABIELLA 20 16 12 8 Pad. Hall 20 D C B A C 20 C 15 C 13 A 18 A 17 MU RESTAURANT C 18 C 11 A 16 C 16 E B 07 A 14 A 15 D 09 C 09 C 14 MU Cafè LOUNGE D 07 B 06 A 13 C 12 A 12 E 15 D 10 A 11 E 18 C 10 C 07 B 05 A 10 E 16 E 14 E 13 D 08 A 08 A 09 E 12 E 11 D 06 LOUNGE IDEABIELLA E 10 / E 08 E 09 LOUNGE LOUNGE A 07 MU E 06 E 07 MEETING C 08 IDEABIELLA SECRETARIAT ROOM C 05 B 04 A 05 E 05 D 04 D 05 C 03 A 03 C 06 A 06 E 04 B 03 E 03 D 03 C 01 A 04 C 04 B 02 A 01 E 02 E 01 D 02 D 01 A 02 C 02 B 01 E D C B A Milano Unica 30^ edizione / 2 IDEABIELLA 20 16 12 8 ABRAHAM MOON D10 MARLANE - MARZOTTO GROUP A11 LANERIE AGNONA C15 MARLING & EVANS B02 ALFRED BROWN D06 GMF MARZOTTO FABRICS - MARZOTTO GROUP A15 ANGELICO B01 MILIOR A04 LANIFICIO FRATELLI BACCI A16 LANIFICIO MOESSMER A08 LANIFICIO CARLO BARBERA D02 PAULO DE OLIVEIRA C04 CARLO BONOMI 1860 - DIV. -
Egister Volume Lxix, No
EGISTER VOLUME LXIX, NO. 30. EED BANK, N. J., THURSDAY, JANXTARY .16, 1947 SECTION ONE—PAGES 1. TO The Register Again Red Bank Savings Father And Daughter ^acred Concert Monmouth PaYk Gets Heads The List Killed By Train Triplets, All Boys, ] A sample check up'.of 49 of the And Loan Ass'n Word, has been received of the Sunday Night In better weekly newspapers of the sudden passing of Worth Rhodes June 19 -July 30 Date nation, all members of the Audit Has Good Year Bushnell, 42, and his soven-year-old For Episcopal Rector Bureau of Circulation and the daughter Parmly of Mendenhall, Methodist Church Greater Weeklies division of the Pa., who were instantly killed Sat- American Press association, shows Statement By Its urday, January 4, near their home. Elizabeth Waddell Local-Track Is In Excellent Shape— that the average of this group .ran Mr. Busnell and his daughter were Rev. And Mrs. Spofford, Jr., 6,117 lines of national advertising President Offered To in their car and stopped at a cross- Of Fair Haven Is during November. They ranged ing to allow a train to go by. just Are The Proud Parents • . Racing Commission Issues Schedule torn a high of 20,207 lines to a low Tho Public as the train approached tho cross- Soloist Of Evening of 1,358 lines. ing the Bushnell car suddenly •+• Timothy Spofford, 15-montl Monmouth Park will. open its It is pleasing to the publisher Assets of the Red Bank Sayings sprang ahc^d right In front of the A sacred concert sponsored , by son of Rev. -
Assembly Beats Polish Move Ban Economic
Vf' V r P ■' r / V“ ■* ■ ■•• / ’■ *1 V WEDNESDAY, NOVEMBER 24, 1W8 , A V*- rA Q E S m E B K iKattrbfstfr lEnfinins IfrraUi Average DaBy Wet Preas Ran Far the Meutb sT Oeteber. t t t t stor Rsymimd B. Baldarla. Rsuel The PoUah-Amerlcan Club la The M ary Cheney and WWton St. Mary’s Churcli Kalghn, chslrmsn of the Greater holding a Thankaglvlng Bve dance Memetial Ubrarlea will be closed Hartford Inter-Church Canvass, 9,594 A bout Tow n ttle evening at Ita clubrooma at all day tomorrow., Thankaglvlng No Herald and the Rev. Arthur H. Richard day. Annual Breakfast Florence and Clinton etreeta. son, Headmaster o f Brent School, b rm lB ( Onaniat tad Choir Director tlvttlea w ill get under way at 8t80 Tomorrow BegUlo, Philippine Islands, have NEWLYt BUILT HOME IProdarlc Werner hw • re- Mre. J«din Shea o f Benton atreet The annual Advent Men’s Cor been among the speakers. Manehester—^A City o f Vtttage Charm p. m. and Mra. Milton Wagner of Camp- liMreel oC the eomblned choire at porate Oomnninion win be held In This year’s committee for the 120 HAW lUORf^ STREET Center church fo r tomorrow mom- field rcMul are co^nairmen of a Advent Men’s Communion and The Emanuel Choir wiD have a large committee from OlbboM SL Mary's Bpiacopal church this AdvevtWag ea Page U ) MANCHESTER, CONN„ FRIDAY, NOVEMBER 29, 1948 (TWENTY PAGES) j Inc at t o’clock, proeedlnf the Joint rebearaal thla evening at tte There will be no Issue of breakfast consists of Austin H. -
Milano Unica Banks on Stretch Fabrics, Sustainability, Digital
12/2/2019 Milano Unica Spotlights Performance, Sustainability, Digital Services – WWD FASHION / TEXTILES Milano Unica Banks on Stretch Fabrics, Sustainability, Digital Services to Gain Traction Despite rising prices for raw materials and market instability, the Italian textile industry closed 2018 with sales of 7.86 billion euros and exhibitors at the trade show were optimistic about future prospects. By Martino Carrera on February 11, 2019 ESSENTIALIST TODAY'S MUST READ Sale of Sears Complete — Eddie Lampert Owns Sears LATEST GALLERIES The trend area at the 28th edition of textile trade show Milano Unica. Courtesy Photo. MILAN — A breeze of cautious optimism ran through the hallways of the Milano-Rho fairgrounds during the 28th edition of the Milano Unica textile trade show, which closed here on Feb. 7. The 467 exhibitors at the fair presented their collections for spring 2020 focusing on high-tech performance fabrics, sustainable innovations, as well as on the implementation of https://wwd.com/fashion-news/textiles/milano-unica-banks-stretch-fabrics-sustainability-digital-services-1203011496/ Privacy setti1ng/9s 12/2/2019digital services. Milano Unica Spotlights Performance, Sustainability, Digital Services – WWD Despite soaring prices for raw materials — especially wool — currency fluctuations and uneven trade performances, the textile sector held momentum in 2018, with sales expected to close at 7.86 billion euros, substantially in line with the previous year, according to preliminary data released by Confindustria Moda for the January-to-October period. Exports to China, Hong Kong and Japan were up 3 percent, 6.1 percent and 8.6 percent, respectively, while the U.S. lagged behind, down 12.6 percent compared to 2017. -
Sustainability Report 2018-2019 Content
SUSTAINABILITY REPORT 2018-2019 CONTENT 1 DON’T JUST FIT IN, FIND YOUR OWN PERFECT FIT 1.1 Philosophy 04 1.2 Company Performance 05 1.3 Company Structure & Governance 06 1.4 Suitsupply In Numbers 07 1.5 Where To Find Us 08 2 THE UNITED NATIONS SUSTAINABLE DEVELOPMENT GOALS 11 3 RAW MATERIALS & FABRIC MANUFACTURING 3.1 Raw Materials 13 3.2 Mills & Weavers 2018 15 4 GARMENT MANUFACTURING 4.1 CMT Factory Production 2018 17 4.2 Due Dilligence 18 4.3 Leverage & Purchasing Practices 19 4.4. Monitoring Treshold 19 4.5 Audits In 2018 20 5 ANIMAL WALFARE 5.1 Suitsupply Animal Walfare Policy 23 5.2 Sustainawool 24 6 TAKING A STAND FOR THE ENVIRONMENT 6.1 CO2 Our Carbon Footprint - Our Carbon Journey 25 6.2 Towards A Green Supply Chain 26 6.3 Chemicals 27 6.4 Paper Less & Paper Better 28 6.5 It’s in the details 29 7 SUSTAINABLE TRANSPARENT CRAFTMANSHIP 30 8 STAKEHOLDER ENGAGEMENT 31 9 SUITSUPPLY’S STANDARD & POLICIES 32 APPENDIX 36 GRI GENERAL STANDARD DISCLOSURES 36 SUPPLIER INFORMTATION (TIER 1 & 2, PACKAGING & TRIMMING SUPPLIERS) 40 AUDIT SUMMARIES 52 2 SUSTAINABILITY REPORT 2018-2019 “WE AIM FOR SUSTAINABLE GROWTH THROUGH ETHICAL BUSINESS PRACTICES, BY CREATING AND SHARING VALUE WITH OUR CUSTOMERS, SOCIETY, AND WITHIN OUR SUPPLY CHAINS.” FOKKE DE JONG CEO SUITSUPPLY & SUISTUDIO 3 SUSTAINABILITY REPORT 2018-2019 1. DON’T JUST FIT IN, FIND YOUR OWN PERFECT FIT 1.1 PHILOSOPHY Suitsupply is a global European brand renowned for its focus on expert crafted tailoring. Suitsupply helps its clients find their own perfect fit through attainable and transparent craftsmanship, radically personal service, exciting tailoring and fast, effective and direct sales channels. -
Diplomatic List – Fall 2018
United States Department of State Diplomatic List Fall 2018 Preface This publication contains the names of the members of the diplomatic staffs of all bilateral missions and delegations (herein after “missions”) and their spouses. Members of the diplomatic staff are the members of the staff of the mission having diplomatic rank. These persons, with the exception of those identified by asterisks, enjoy full immunity under provisions of the Vienna Convention on Diplomatic Relations. Pertinent provisions of the Convention include the following: Article 29 The person of a diplomatic agent shall be inviolable. He shall not be liable to any form of arrest or detention. The receiving State shall treat him with due respect and shall take all appropriate steps to prevent any attack on his person, freedom, or dignity. Article 31 A diplomatic agent shall enjoy immunity from the criminal jurisdiction of the receiving State. He shall also enjoy immunity from its civil and administrative jurisdiction, except in the case of: (a) a real action relating to private immovable property situated in the territory of the receiving State, unless he holds it on behalf of the sending State for the purposes of the mission; (b) an action relating to succession in which the diplomatic agent is involved as an executor, administrator, heir or legatee as a private person and not on behalf of the sending State; (c) an action relating to any professional or commercial activity exercised by the diplomatic agent in the receiving State outside of his official functions. -- A diplomatic agent’s family members are entitled to the same immunities unless they are United States Nationals. -
Las Religiosas Hijas De Ia Iglesia Estafcieesráfi En Bslorado Usa Casa
TALLERES GRAFICOS «Diarto Boi^m» Diario de GARANTIZAN LA MAXIMA PERFEGCIOH EN TODA CLASE DE TRABAJOS TIPOGRAFICOS yutffte» u — xtAéftm ¿03 LXX. —Núm. 31.279 APARTADO - s B U B G O 8 ^pósito legal: BU - 5- 1958 MIERCOLES, 14 DE SEPTIEMBBE DE 1960 núm. 46 Redacción: TELE??^91280. —Administración1 : 2015 lf20 PESÍÍA5 su esposa Lanzamiento i 1 [81 u [mu EH EL [c/e ofro saiélife 20 a las norteamericano Ahora, Lumumba consigue del Parlamento "plenos poderes" coronesas Con el fin da recuperar y Kasavubu ordena la detención del jefe del Ejército otra vez la cápsula Audiencia civil y militar del Jefe que pesa 150 kilos del Estado en el Pazo de Meirás Hoy se reunirá el Come/o de Seguridad para tratar de la grave crisis El mes próximo será enviado El Cairo.— La agencia Oriente anular el decreto del. presidente juzgado en una forma justa, a pe• paradero de Lumumba, pero que Medio informa que 200 soldados Kasavubu, en el que destituye a sar de los. daños y sufrimientos podía afirmar que no se encon• un mono al espacio congoleses equipados con "jeeps" Lumumba y se nombra a Ileo jeíe que ha impuesto al Congo". traba en su residencia particular y ametralladoras, han ocupado el del Gobierno congolés—Efe. " Jean Bollkange, nombrado mi• de Leopoldville ni tampoco en la Base de las fuerzas aéreas de aeropuerto de Leopoldvjlie.—Efe. "LUMUMBA SERA DETENIDO" nistro de Información por Ileo, oficial. Vandenberg.—Se ha llevado a ca-^ DOS DELEGACIONES CONGO• Leopoldville.—,E1 Gobierno de dijo por Radio Leopoldville que Tres soldados congoleses vigi• bo en esta base el sexto lanza• LESAS EN LA O. -
Reda Signifies the Passion for 100% Made-In-Italy Wool
Reda signifies the passion for 100% Made-In-Italy wool Established since 1865, Reda wool mill based in Biella, signifies elegance and quality as it values style, innovation, state-of-the-art eco sustainable technologies to achieve beautiful fabrics for the world’s leading fashion houses. The communication team at Reda welcomed the journalists. Mr. Fabrizio Alessandro Goggi and Mr. Enrico Ciccone, are both passionate about the Reda fabric quality, which is the skilful culmination of 100% Italian expertise and craftsmanship, in which “Made in Italy” stands for attention to detail, respect for traditions as well as a fresh look on the Reda expands choice of Jacket Fabrics dictates of fashion. Reda’s business has with Spring/Summer 2015 COLLECTION been well established in Europe, Japan Reda had devoted an extensive and North America and it is now looking selection of its finest fabrics to develop towards new markets such as Russia, this item of clothing, which is increasingly China, India and South America with important for today’s modern man; who growing interest. refuses to compromise on style and wants Mr. Fabrizio Alessandro Goggi during different collections for his favourite type ensures high-performance and crease a factory visit explained to the journalist of blazer. proof fabrics. The fabrics created for the that Reda manages and controls the traveller jacket are natural tones and a The Spring 2015 collection ranges entire production chain from fleece to smooth hand, giving a three-dimensional from the classic jacket, embellished with a finished fabric from its Valle Mosso base. As for the college blazers, the jersey effect printed with a macro factory near Biella. -
Delta Dental Premier®
Delta Dental of Minnesota Delta Dental Premier® 2016 Dentist Directory Dentist Directory - Premier® Delta Dental of Minnesota Welcome to Delta Dental Premier® In-Network: When you choose a dentist from this This directory is intended as a guide for selecting a directory, your dental care provider is “in-network” Delta Dental Premier dentist. The Delta Dental Premier and you will receive important benefit advantages, Network offers the largest dental network in the including lower costs by receiving the maximum level country with over 145,000 participating providers. It of benefits available to you. Should you require care is also the largest provider network in Minnesota, with from a dentist outside of the Minnesota service area, more than 3,100 participating dentists and specialists please use the “Find A Dentist” feature and search for in 87 Minnesota counties and border communities. By providers in the Premier Network selecting a dentist listed in the Delta Dental Premier by going to www.deltadentalmn.org/uofm. directory, you will ensure that you receive your maximum dental benefits. Out-of-Network: If you receive dental care from a dentist not listed in this directory, your provider is considered “out-of-network.” By utilizing an out-of- network dentist, your care will be covered at a lower reimbursement and you will have greater out-of-pocket expenses. Please note that not all dentists working in the same clinic or office may be participating network dentists. If dental services are received from an out-of- network dentist, you will be responsible for paying the dentist for all costs above the Delta Dental allowable charge for services and Delta Dental will reimbursement you directly. -
Sustainability Report 2017-2018 Content
SUSTAINABILITY REPORT 2017-2018 CONTENT 1 DON’T FIT IN, FIND YOUR PERFECT FIT 04 1.1 Philosophy 04 1.2 Company structure 05 1.3 Company performance 06 1.4 New European HQ in the making 07 1.5 Our Company in numbers 08 1.6 Sustainability highlights 2017 09 2 THE UN SUSTAINABLE DEVELOPMENT GOALS 10 3 SUSTAINABLE SOURCING& MANUFACTURING 12 3.1 Raw Materials 12 3.2 Our 4 most used fibers explained 13 3.3 Mills & weaves 2017 15 4 GARMENT SUPPLIER MANUFACTURING 17 4.1 CMT factory production 2017 17 4.2 Due dilligence 18 4.3 Leverage & purchasing practises 19 4.4. Monitoring threshold 20 4.5 Audits in 2017 21 5 TAKE ACTION: HOW WE ACT ON WORLDWIDE DEVELOPMENTS 27 5.1 Refugee policy Italy& Turkey 27 5.2 Child labour and refugee policy 27 6 ANIMAL WELFARE 28 6.1 Animal welfare policy 30 6.2 Sustainawool 30 7 CHEMICALS 31 7.1 Chemical policy 31 8 OUR PLEA FOR INDUSTRY TRANSPARANCY 32 8.1 Our plea for industry transparency 32 9 CO2 EMISSION- OUR CARBON JOURNEY 33 9.1 Our carbon journey 2017 33 10 CIRCULARITY & RECYCLING 34 10.1 Circularity 34 10.2 GFA Commitment, scopes & approach 35 10.3 End of life responsibility - recycling 37 11 STAKEHOLDER ENGAGEMENT 40 2 SUSTAINABILITY REPORT 2017-2018 “WE AIM TO ADVANCE OUR SUSTAINABILITY INITIATIVES AND GROW OUR BUSINESS THROUGH THE DEVELOPMENT OF ETHICAL BUSINESS PRACTIC- ES. BY CREATING AND SHARING VALUE WITH OUR CUSTOMERS, WE CAN POSITIVELY IMPACT OUR SUPPLY CHAINS, THIS INDUSTRY AND SOCIETY.” ROOS FLEUREN- CHIEF PRODUCT OFFICER SUITSUPPLY & SUISTUDIO 3 SUSTAINABILITY REPORT 2017-2018 1. -
Letter from the Chair
LETTER FROM THE CHAIR From Halloween to Christmas and New Year this is a very busy time for all of us. Remembrance Sunday was well attended and a wreath was laid by Geoff Howland on behalf of the Society at the War Memorial. He cleaned up our Poppy Memorial in Elmfield Gardens which provides a focal point of remembrance in the High Street and is particularly apt as this year is the centenary of the Battle of Passchendaele. Did you notice all the huge red poppies on lamp posts throughout the town put up by Shane Thompson of Holmes & Daughters and the Royal British Legion? Next year Shane means to turn the whole town red! Some of us have changed our roles in the Society. Judy Asher is now maintaining the website and has handed Minuting over to Nick Picton. Photo journalist Peter Denton has joined us as Vice Chairman. Most importantly as you will read overleaf we are saying goodbye and thanks for all the good tidings to Donald Bell who has raised the standard of our quarterly magazine hugely and will be extremely hard to replace. If you would like to step into his shoes please get in touch with me. Teddington800 comes to a close but leaves behind wonderful memories, lots of new friends made and new members for the Society. Huge congratulations to Anne McTear and the Organising Committee. We'll give a round up of their events and successes next time. Meanwhile our History Banners will go on show next year. A tour de force by Paddy Ching with input from Ken Howe, John Sheaf, Pieter Morpurgo and me they've been much admired at the NPL, the Landmark and the Library.