Timing Belts Vs Chain
Total Page:16
File Type:pdf, Size:1020Kb
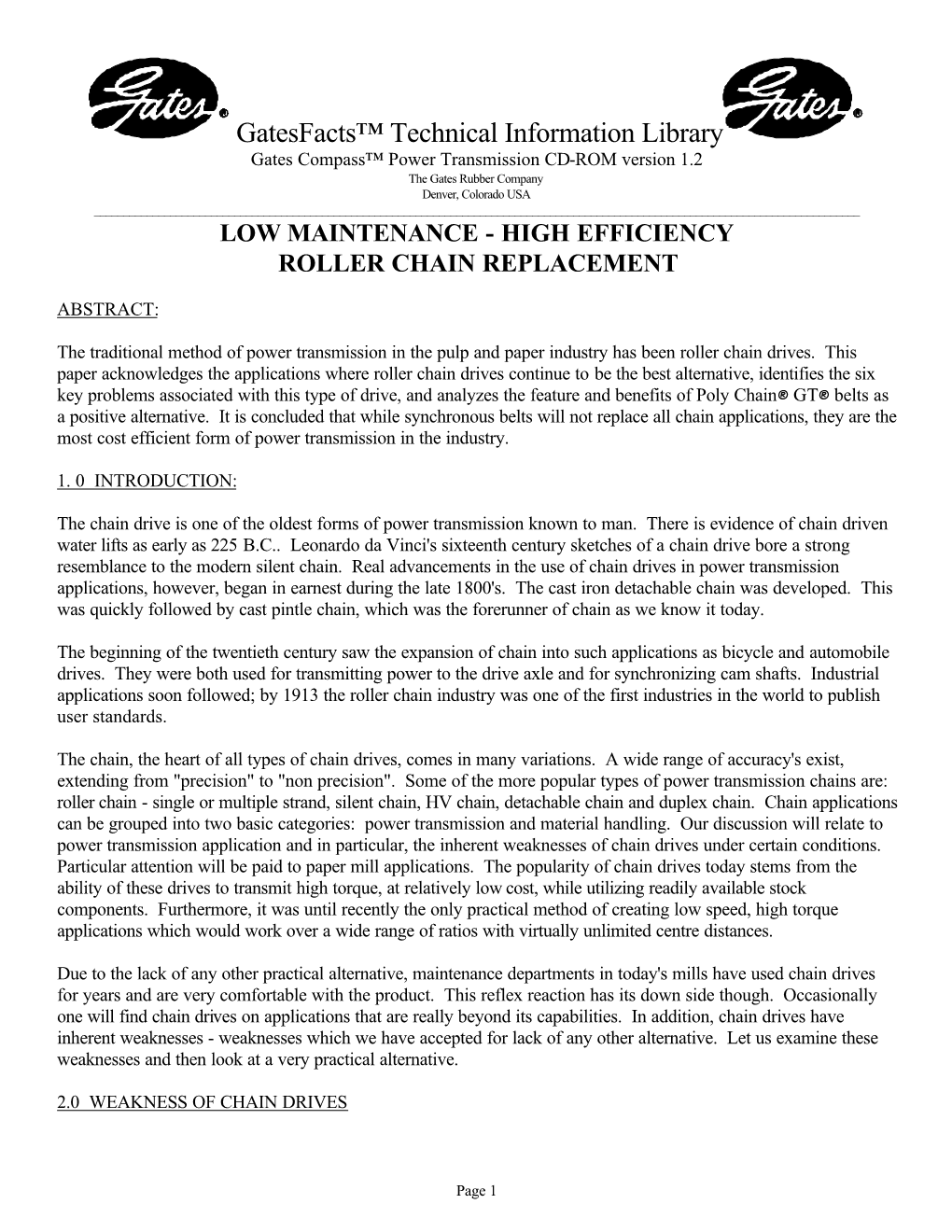
Load more
Recommended publications
-
ASME/ANSI RS Roller Chain Technical Information
U.S. TSUBAKI RS ROLLER CHAIN U.S. TSUBAKI ROLLER CHAIN — A SOLID DIFFERENCE ASME/ANSI RS Roller Chain A - DRIVE CHAINS RS ROLLER CHAIN RS11 ˜ RS240 Longer Wear Life Higher Horsepower Ratings Greater Fatigue Strength U.S. Tsubaki Roller Chain lasts up to U.S. Tsubaki ASME/ANSI Chains handle U.S. Tsubaki ASME/ANSI Chains are twice as long as our previous chain in up to 33 percent more horsepower so you designed to have higher fatigue strength. many applications. Advanced technology can increase drive performance without The wider waist of the link plates puts allows us to combine the strength, increasing chain size. In fact, depending more metal where you need it — running durability, and reliability of a solid bushing on your application, you may be able to your application. There is less downtime with our patented lube groove on the transmit the same horsepower with a because chains operate longer. Operating inner surface of sizes RS80 through smaller, less costly chain. The costs are reduced because chains RS140. The solid bushings are precise improvement comes from a U.S. Tsubaki perform more efficiently. These benefits round cylinders, which means better exclusive ring coining process for the slip go right to your bottom line. contact between the pin and bushing. The fit connecting link and special processing lube grooves hold oil where chain needs on the two-pitch offset link. S-N Curve it most. The result is longer lasting chain. Horsepower Ratings Wear Elongation Curve A & a: Fatigue strength B & b: Tensile strength Improved Tsubaki B Chain b Competitor A Competitor B Previous Improved Previous Tsubaki Tsubaki Tsubaki Improved Tsubaki Chain Chain Chain Chain 1.5 33% Increase in Horespower Rating 1.0 RS80-RS140 Other roller chain A .05 "S" Chain load a HP HP 2 3 4 5 6 7 Elongation (%) * Ratings are for RS80-RS240 Roller Chains 1 10 10 0 50 100 150 200 Revs Per Minute (RPM) 10 10 10 10 10 Time (Hours) "N" Number of times load is applied Save Time & Money Wear in the pin-bushing joint can lead to elongation and replacement. -
Chapter 1 Introduction
國立交通大學 機械工程研究所 碩士論文 變速自行車鏈條設計 Design of Chains on Multi-speed Bicycles 研究生:張崇銘 指導教授:曾錦煥 教授 中華民國九十三年六月 變速自行車鏈條設計 Design of Chains on Multi-speed Bicycles 研究生:張崇銘 Student: Chung-Ming Chang 指導教授:曾錦煥 Advisor: Ching-Huan Tseng 國立交通大學 機械工程研究所 碩士論文 A Thesis Submitted to Institute of Mechanical Engineering College of Engineering National Chiao Tung University in Partial Fulfillment of the Requirements for the Degree of Master of Science in Mechanical Engineering June 2004 Hsinchu, Taiwan, Republic of china 中華民國九十三年六月 變速自行車鏈條設計 研究生:張崇銘 指導教授:曾錦煥 國立交通大學機械工程研究所 摘要 本論文主要研究對象為自行車上傳動系統中的鏈條元件,由於自行車飛 輪受到車架、騎乘姿勢所形成的空間限制,必須在有限空間內增加飛輪片 數增加齒數比,達到變速換檔的舒適性。因此,為了配合這樣緊密的飛輪, 鏈條寬度的縮減是必須的。經過專利的整理後,確定空間尺寸和強度為初 步設計的主要需求;提出不同的概念設計,並利用新的鏈條連結機構來達 到鏈條寬度的縮減。 本文提出概念設計較目前市面上自行車最窄的鏈條寬度更窄,強度部份 利用有限元素分析法做定性分析,比較各個設計的相對強度;此外也經由 原型的製作,檢視其機構的問題。 i Design of Chain on Multi-speed Bicycle Student: Chung-Ming Chang Advisor: Ching-Huan Tseng Institute of Mechanical Engineering National Chiao Tung University ABSTRACT This study focuses on the chain for the multi-speed bicycle. Design space for the freewheel on bicycle is limited by frame, riding posture, etc. However, the number of gear ratios in this design space increased with added more sprockets are the trend on the bicycles. Therefore, reduction of chain width is necessary for working with this compact freewheel. Space and strength are main requirements in the beginning of design according to literatures and patents review. Several new concepts are proposed, and these concepts use the linkage mechanism to achieve the reduction of chain width. Chain width of these concepts proposed in this study can be reduced under the assumption for fixed design space and thickness of sprockets. The finite element method is used to compare the trend of strength among these concepts. -
Technical Engineering Guide
TTEECHCHNINICALCAL EN ENGGINEEINEERRININGG 89 www.diamondchain.com TECHNICAL ENGINEERING General Drive Considerations One of the main advantages of the roller chain drive is its ability to perform well under widely varying conditions. Despite this ability, there are a number of rules of good design practice which, if considered early in the design pro- cess, will enable the user to obtain desirable results. Basic dimensions and minimum ultimate tensile requirements for single-pitch, double-pitch and attachment roller chains are specified by various standards organizations worldwide. ASME/ANSI, The American Society of Mechanical Engineers and The American National Standards Institute, defines dimensions such as: pitch, roller width, roller diameter, link plate height, link plate thickness and pin diameter. The primary purpose of the standard is to ensure that manufacturers will produce chains and sub-assemblies that are similar dimensionally and therefore interchangeable. In addition, the standard does offer the user some assurance of quality by defining a minimum ultimate tensile strength for each model of chain. However, tensile strength is not always a valid method to differentiate one manufacturer’s product from another. It is very important to remember that dimensional standardization does not define quality or performance characteristics. Minimum Ultimate Tensile Strength: Minimum Ultimate Tensile Strength, MUTS, is the static load required to break the chain. Tensile strength values shown in this catalog are not allowable working loads. Load or tension applied 1 to the chain in service should never exceed ⁄6 th of the UTS. If exceeding this value is necessary for a specific applica- tion, contact Diamond Chain. -
WT Series Actuator Operations Manual WATCH TECHNOLOGIES W T S E R I E S Actuator Operations Manual
Water Control Devices WT Series Actuator Operations Manual WATCH TECHNOLOGIES W T S E R I E S Actuator Operations Manual Watch Technologies 2185 NE Spalding Ave, #10 Grants Pass, OR 97526 Phone 541.472.8095 06/2016 Contents Introduction ………………………………………………............ 1 Theory of Operation ………………………………………. 1 Installation and Start-up ………………………………………… 3 Safety Information ………………………………………… 3 Installation – Rising Stem ………………………………… 4 Installation – Horizontal Gearlift …………………………. 12 Seasonal Start-Up ………………………………………………. 16 Operation ………………………………………………………… 18 Manual Operation ………………………………………… 19 Automated Operation Using Internal RTU ……………… 20 Handwheel Operation …………………………………….. 20 Maintenance and Troubleshooting ……………………………. 21 Troubleshooting Guide …………………………………… 22 Shut-Down and Storage ………………………………………... 23 System Integration and Options ………………………………. 24 Electrical System …………………………………………. 24 Gate Blade Position Sensor ………………………………25 Solar Panel and Charge Controller ……………………... 27 RUG3 Remote Terminal Unit ……………………………. 28 WT Actuator and Gearmotor Specifications ……………29 – 39 Warranty Information …………………………………………… 41 WATER CONTROL DEVICE S Introduction The WT Series of gate control actuators from Watch Technologies have been developed for the ultimate control of a wide variety of applications. he WT Series consists of five distinct models to address the needs of both vertical rising stem gate users as well as systems utilizing T horizontal shaft gear lifts. A wide variety of drive motors enable the WT Series to align with specific torque requirements. The WT Series can also be configured with an embedded Remote Terminal Unit (RTU) which enables the actuator to function as a stand-alone, smart device that can remotely control gates based upon user-defined control points and water status parameters (flow, level). Theory of Operation The philosophy behind each Watch Technologies product is providing long- lived, reliable devices that can be easily installed, maintained, adjusted and upgraded by our customers using simple tools and basic skills. -
Roller Drive Chain Selection and Engineering Information
sec_29.3_29.4_TI 11/19/08 12:45 PM Page 231 Roller Drive Chain Selection 29 Roller Drive Chain Selection and Engineering Information Required information for drive selection: Table 1: Service Factors 1. Type of input power (electric motor, internal combustion Type of Input Power engine, etc.). Internal Internal 2. Type of equipment to be driven. Class of Driven Combustion Combustion Electric Motor 3. Horsepower (HP) to be transmitted. Load Engine with Engine with or Turbine Information Technical Mechanical 4. Full load speed of the fastest running shaft (RPM). Hydraulic Drive Drive 5. Desired speed of the slow-running shaft. NOTE: If the speeds are variable, determine the horsepower to be Uniform 1 1 1.2 transmitted at each speed. Moderate 1.2 1.3 1.4 6. Diameters of the driver and driven shafts. Heavy 1.4 1.5 1.7 7. Center distance of the shafts. NOTE: If this distance is adjustable, determine the Step 3: Calculate the Design Horsepower. amount of adjustment. Design Horsepower = HP x Service Factor 8. Position of drive and space limitations (if any). 9. Conditions of the drive. Drives with more than two The design horsepower equals the horsepower to be sprockets, idlers, or unusual conditions such as severely transmitted times the service factor found in Table 1. abrasive or corrosive environments, severely high or low temperatures, widely fluctuating loads, frequent starts Step 4: Select the Chain Pitch. and stops, etc., require special attention. It is advisable From the Quick Selector Chart on page 234, make a to consult with Renold Jeffrey engineering personnel in tentative chain selection as follows: these situations. -
U.S. Tsubaki Engineering Chain Division Engineering Class Chains
U.S. TSUBAKI A – ENGINEERING CLASS CHAINS ENGINEERING CHAIN DIVISION ENGINEERING CLASS CHAINS Contents Page DRIVE CHAINS A-1 ~ A-16 INTRODUCTION A-1 ~ A-2 DRIVE CHAIN SPECIFICATIONS A-3 ~ A-4 DRIVE CHAIN SELECTION GUIDELINES A-5 ~ A-16 ROLLER CONVEYOR CHAINS A-17 ~ A-52 INTRODUCTION A-17 ~ A-18 ROLLER CONVEYOR CHAIN SPECIFICATIONS A-19 ~ A-20 ROLLER CONVEYOR CHAIN ATTACHMENTS A-21 ~ A-34 APRON CONVEYORS A-35 ~ A-42 ROLLER CONVEYOR CHAIN SELECTION GUIDELINES A-43 ~ A-52 STEEL BUSHED CHAINS A-53 ~ A-60 INTRODUCTION AND SPECIFICATIONS A-53 ~ A-54 ATTACHMENTS A-55 ~ A-60 CAST COMBINATION CHAINS A-61 ~ A-64 INTRODUCTION A-61 ~ A-62 SPECIFICATIONS AND ATTACHMENTS A-63 ~ A-64 WELDED STEEL CHAINS A-65 ~ A-74 INTRODUCTION A-65 WELDED STEEL MILL CHAIN AND ATTACHMENTS A-66 ~ A-72 WELDED STEEL DRAG CHAIN AND ATTACHMENTS A-73 ~ A-74 DROP FORGED RIVETLESS CHAINS A-75 ~ A-82 INTRODUCTION AND SPECIFICATIONS A-75 ~ A-76 ULTRA WEAR LIFE CHAINS A-77 BARLOOP CHAINS A-78 ATTACHMENTS AND SPROCKETS A-79 ~ A-80 CATERPILLAR DRIVE CHAINS A-81 ~ A-82 BAR AND PIN CHAINS A-83 ~ A-86 INTRODUCTION A-83 DRAW BENCH CHAINS A-84 DOUBLE FLEX CHAINS A-85 ~ A-86 SPECIALTY CHAINS A-87 ~ A-114 INTRODUCTION A-87 ~ A-88 RF CONVEYOR CHAIN BASIC METRIC SERIES A-89 ~ A-92 FLOW CONVEYOR CHAINS A-93 ~ A-98 FOR FC TYPE HORIZONTAL FLOW CONVEYOR A-93 ~ A-94 FOR LC TYPE INCLINED FLOW CONVEYOR A-95 FOR FK TYPE FLOW CONVEYOR FOR GRAIN A-96 NF BLOCK CHAIN FOR FLOW CONVEYOR A-97 ~ A-98 OUTBOARD ROLLER CONVEYOR CHAINS A-99 RFD DEEP LINK CHAINS A-100 SANITATION CHAINS A-101 ~ A-102 ACR 810 COLLECTOR TANK CHAINS A-103 ~ A-104 JAC TYPE BAR SCREEN CHAINS A-105 ~ A-106 ACS TYPE HEAVY DUTY COLLECTOR CHAINS A-107 ~ A-108 BEARING ROLLER CONVEYOR CHAINS A-109 ~ A-110 LARGE SIZE STEEL DOUBLE PLUS® CHAINS A-111 ~ A-112 BEARING BUSH CHAINS A-113 ~ A-114 A-iii UNION CHAIN DIVISION - DRIVE CHAINS Drive Chains ENGINEERING CLASS DRIVE CHAIN A – ENGINEERING CLASS CHAINS Keep Your Operation Moving with Union Chain Union Drive Chains are designed to exceed the listed ultimate Reduce Maintenance Costs and Downtime strength ratings. -
Design Guide
sec_29.2_TI 11/19/08 11:51 AM Page 215 Design Guide 29 Development of Early Roller Chain As the industrial revolution gained pace, the need for higher performance chain ensured that the product did not stand still. A quick look at the 1880 patent would give the impression that there is no difference between it and modern chain. In concept, this is true. However, early chain performance was very much constrained by design knowledge, material sophistication, and production processes. For example, in order to achieve a close tolerance on round parts, Hans Technical Information Technical Renold also pioneered centerless grinding and, at one time, had a whole section devoted to grinding cold drawn bar to size before further processing. The shortcomings of available technology meant that, compared with modern chain, there were low strength to weight ratios, erratic pitch control, poor engagement Offset link chain, like conveyor chain, is intended to run characteristics, and a tendency toward point loading; only at low speeds, since the presence of an offset link causing high bearing pressures, wear, and failure. The plate will reduce fatigue life. This chain tends to be used ever-increasing number of applications for chain resulted in conveying applications where harsh environmental in a continuous refinement of our production processes conditions prevail, in mineral excavation, for example. and the introduction of heat treatment, improving Renold Chain to meet these new and arduous demands. Leaf chain is similar in construction to the old Galle chain, except that plates are interleaved in various configurations right across the width of the pin. -
NEW 2021 Performance Parts Quick Reference Guide
PERFORMANCE PARTS 2021 QUICK REFERENCE GUIDE FOLLOW US! facebook.com/toro twitter.com/TheToroCompany twitter.com/ToroGolf youtube.com/toro linkedin.com/company/the-toro-company toro.com 800-803-8676 ©2021 The Toro Company. Bloomington, MN 55420 All rights reserved. Printed in the USA. Part Number 21-113-T Products depicted in this literature are for demonstration purposes only. Actual products offered for sale may vary in use, design, required attachments and safety features. We reserve the right to improve our products and make changes in specifications, design and standard equipment without notice and without incurring obligation. See your dealer for details on all our warranties. WHAT’S NEW? Within this catalog, you’ll find the Genuine Toro® Parts and accessories you’ll need to keep your Toro equipment operating at its full potential. Our expanded WHAT myTurf® Pro Asset Management. parts inventory offers: • Competitive market pricing Equipment connectivity. MATTERS • Quality & Reliability – meets the highest standards Maintenance notifications. Parts ordering 24/7. • Expanded – Quick Reference Guide NEW FOR 2021 • Now under 150 pages! • Updated Featured Items • New MVP Kits MOST Improving staff efficiency. Reducing overall maintenance costs. Enhancing your reputation. What Matters Most to You Matters Most to Us. myTurf Pro is a powerful and easy-to-use, application that seamlessly connects your assets and your maintenance program, regardless of brand. Provide your team with the tools to become more efficient by automating routine tasks, easily ordering parts, managing maintenance assignments and tracking task completion. “At a glance” overviews keep you informed of asset status. Connect. Manage. Maintain. Simplify. -
Retro Direction Bicycle
International Research Journal of Engineering and Technology (IRJET) e-ISSN: 2395-0056 Volume: 06 Issue: 03 | Mar 2019 www.irjet.net p-ISSN: 2395-0072 RETRO DIRECTION BICYCLE Patil Rutik Raghunath1, Jadhav Mukesh Santosh2, Kharabe Vikas Babasaheb3, Kanade kedar Somnath4, Jadhav Sandesh Rajaram5, Mr. Sabde Abhijit Manoharrao6 1,2,3,4,5Student of Diploma in Mechanical Engineering Department Vishweshwarayya Abhiyantriki Padvika Mahavidhyalay, Almala, Maharashtra, India 6Guide Lecturer in Mechanical Engineering Department, Vishweshwarayya Abhiyantriki Padvika Mahavidhyalay, Almala, Maharashtra, India. ---------------------------------------------------------------------***--------------------------------------------------------------------- Abstract:- Retro-direct is a gearing mechanism used on unloading the materials from the trailer. They have some bicycles in the early 20th century, which provides a mainly focused on above difficulty. Hence a prototype second gear ratio when pedaled backwards. Retro-direct of suitable arrangement has been designed. The was developed by French inventor Paul de Martin de Viviés vehicles can be unloaded from the trailer in three (1833–1911). An early two-chain version was patented by axes without application of any impact force. The in 1869 by Barberon and Meunier. A single-chain version Direction control valve which activates the ram of the was patented in 1903 by the bicycle manufacturer hydraulic cylinder which lifting the trailer cabin in Hirondelleome hobbyists have converted modern bicycles require side. Further modifications and working to use retro-direct gearing. A bicycle, also called limitations will put this work in. a cycle or bike, is a human-powered, pedal-driven, single- track vehicle, having two wheels attached to a frame, one PROCEDURE/ METHODOLOGY behind the other. A bicycle rider is called a cyclist, or bicyclist. -
Drives® Chain Product Catalog Index
DRIVES® CHAIN PRODUCT DRIVESI ABOUT DRIVES DRIVES ® CHAIN Drives, the world leader in manufactured chain products, PRODUCT CATALOG INDEX offers a broad line of superior quality precision roller chains, attachment chains and engineered conveyor chains for the DRIVES OVERVIEW ...................................................................................1 world’s toughest applications. Providing the most CHAIN PRODUCT INTRODUCTION ........................................................2 comprehensive line of quality chain products, Drives delivers HOW TO USE THIS CATALOG ..................................................................4 leading edge solutions with nearly 60 years of advanced DISCLAIMER/CONTACT INFORMATION ...............................................5 engineering knowledge and experience. Committed to manufacturing world class products, outstanding engineering WARNINGS ...............................................................................................5 and manufacturing support and total customer service, Drives TECHNICAL SECTION ...............................................................................7 utilizes the highest quality materials, technologies, equipment Chain Selection .....................................................................................8 and craftsmanship to produce quality products. Drives Roller Chain Dimensions and Horsepower Tables – Inch .......16 manufacturing facility is located in Fulton, Illinois. Roller Chain Dimensions and Horsepower Tables – Inch · Heavy -
Mounting Sprockets and Pulleys on Pilot Style Clutches
Mounting Sprockets and Pulleys On Pilot Style Clutches Considerations & Guidelines www.machiii.com 1 Clutches are commonly connected to a drive system through roller chains and belting. This requires that a sprocket or pulley be mounted directly to the clutch. A pilot style clutch is made for this purpose; providing a projection onto which the sprocket or pulley will seat and a series of tapped holes along a bolt circle where the sprocket or pulley will be attached. Pilot Clutch Coupling Clutch Adapter Clutch NEMA Frame Clutch Photo 1: A Comparison of Clutch Styles This document discusses the factors which must be taken into consideration when selecting, machining and mounting a sprocket or pulley for a pilot style clutch. When proper mounting and installation procedures are followed, optimal performance and wear life are assured. www.machiii.com 2 Service (Safety) Factor When selecting a clutch for an application, a service factor must be taken into consideration. A service factor (also known as a safety factor) is the overload capacity that a component can handle without failing. With respect to clutches, this translates to the total load the clutch can handle without slipping. A service factor of 1.5 to 2 (50% to 100% more torque than is required to drive the load) is recommended by most clutch manufacturers. Example: Torque required to drive the load = 500 pound inches 1.5 Service Factor = 500 x 1.5 = 750 pound inches 2.0 Service Factor = 500 x 2.0 = 1000 pound inches The clutch selected for the application should have a torque capacity of between 750 and 1000 pound inches. -
Installation & Maintenance Guide
INSTALLATION & MAINTENANCE GUIDE INSTALLATION CATALOGUE M CATALOGUE INSTALLATION & MAINTENANCE GUIDE ROLLER-, ATTACHMENT- AND CONVEYOR CHAIN CATALOGUE M | 2015 LEADING PRODUCTS AND EXCELLENT SERVICE At TSUBAKI we know that customers want the best. We are also aware that each and every one of our customers has unique requirements. Therefore, we take pride in our ability to deliver an extensive product line-up that satisfies these high expectations. We believe that in coming years there will be an increase in demand for quality in pro- ducts as well as in services. With an eye on these future trends, we are committed to take on the challenge of technical innovation. Key products such as BS/DIN, ANSI drive chains, small pitch at- tachment and large pitch conveyor chains for industrial applica- tions through to high efficiency timing chains and tensioners for automotive engine primary drives ensure Tsubaki stays at the fo- refront of engineering excellence. Specific products such as pio- neering Lambda lube free chain, N.E.P. chain for corrosion pro- tection and specialist chains such as engineering plastic help Tsubaki provide chain solutions to many of the world’s most de- manding industries and applications. The same can be said for Tsubaki TEM products such as cam clutches, couplings, overload protection devices, reducers & linear actuators. Tsubaki care does not stop at the design & manufacture stage or even at the receipt of the product by the final customer. For pro- ducts to fulfil their planned lifecycle Tsubaki sees the initial installa- tion, ongoing customer maintenance & aftercare support programs Tsubakimoto Europe B.V.