Design and Performance Evaluation of Chain Wheel Drive of Bicycle by Using Alternate Material
Total Page:16
File Type:pdf, Size:1020Kb
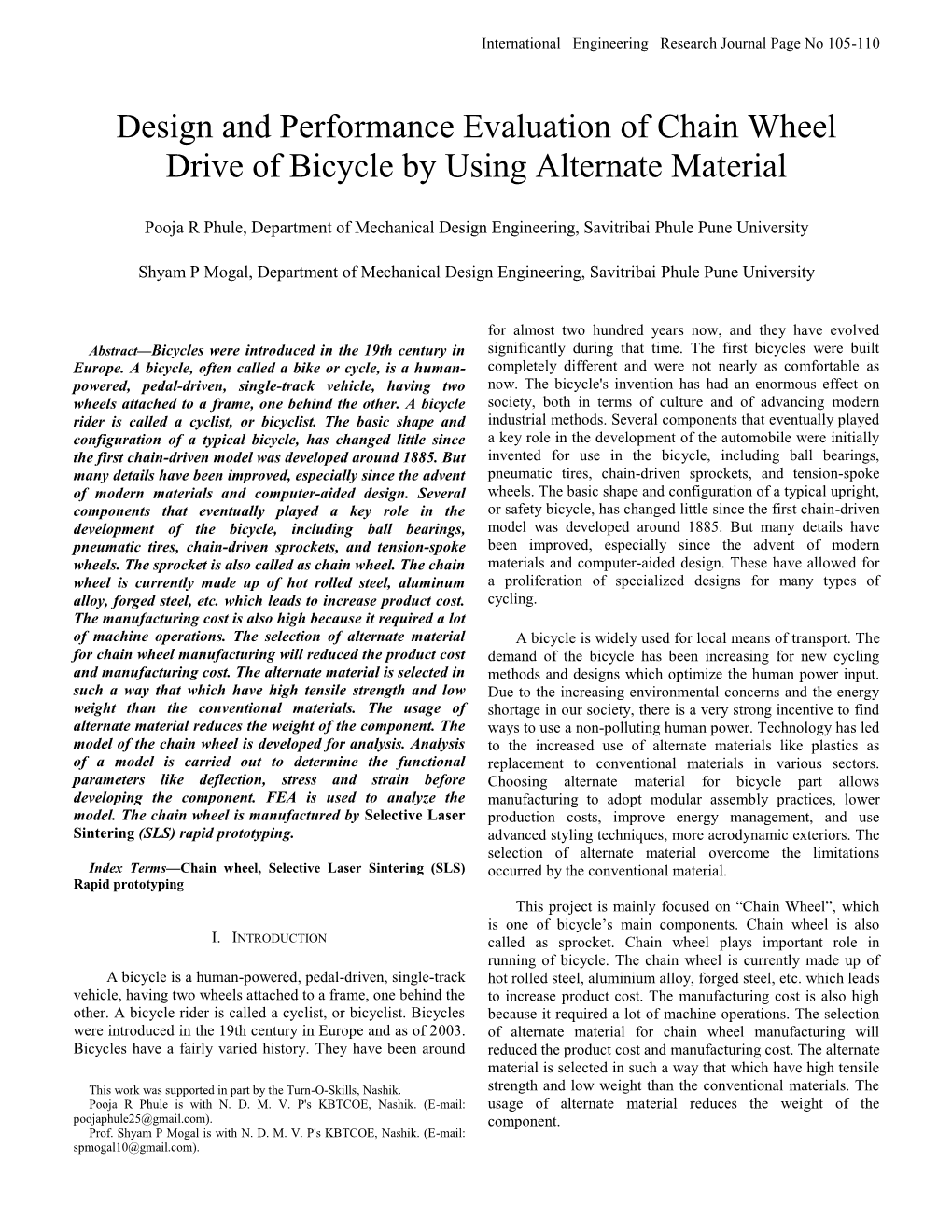
Load more
Recommended publications
-
Forklift Differentials
Forklift Differentials Forklift Differential - A mechanical device which could transmit rotation and torque through three shafts is known as a differential. At times but not at all times the differential would use gears and will operate in two ways: in automobiles, it provides two outputs and receives one input. The other way a differential works is to combine two inputs in order to produce an output that is the sum, average or difference of the inputs. In wheeled vehicles, the differential enables all tires to be able to rotate at various speeds while supplying equal torque to all of them. The differential is intended to drive a pair of wheels with equivalent torque while enabling them to rotate at various speeds. While driving around corners, a car's wheels rotate at different speeds. Several vehicles such as karts operate without using a differential and use an axle instead. If these vehicles are turning corners, both driving wheels are forced to spin at the same speed, normally on a common axle which is driven by a simple chain-drive mechanism. The inner wheel should travel a shorter distance compared to the outer wheel while cornering. Without using a differential, the effect is the outer wheel dragging and or the inner wheel spinning. This puts strain on drive train, causing unpredictable handling, difficult driving and damage to the tires and the roads. The amount of traction necessary to move the car at whichever given moment depends on the load at that moment. How much drag or friction there is, the car's momentum, the gradient of the road and how heavy the automobile is are all contributing factors. -
Flexible Wheel Chair
GRD Journals- Global Research and Development Journal for Engineering | Volume 1 | Issue 8 | July 2016 ISSN: 2455-5703 Flexible Wheel Chair Mahantesh Tanodi Department of Mechanical Engineering Hirasugar Institute of Technology, Nidasoshi, Karnataka (India) Sujata Huddar S. B. Yapalaparvi Department of Electrical and Electronics Engineering Department of Mechanical Engineering Hirasugar Institute of Technology, Nidasoshi, Karnataka Hirasugar Institute of Technology, Nidasoshi, Karnataka (India) (India) Abstract The wheelchair is one of the most commonly used assistive devices for enhancing personal mobility, which is a precondition for enjoying human rights and living in dignity and assists people with disabilities to become more productive members of their communities. For many people, an appropriate, well-designed and well-fitted wheelchair can be the first step towards inclusion and participation in society. When the need is not met, people with disabilities are isolated and do not have access to the same opportunities as others within their own communities. Providing wheelchairs that are fit for the purpose not only enhances mobility but begins a process of opening up a world of education, work and social life [1]. The development of national policies and increased training opportunities in the design, production and supply of wheelchairs are essential next steps. Every human being need to move from one place another to fulfill his requirements and to accomplish that requirements he will travel from one place to another place by walking which is a basic medium of transportation. But it is exceptional in case of physically disables (Persons don’t have both legs). In order to support and help such a person’s we designed a special manually lever operated wheel chair. -
ASME/ANSI RS Roller Chain Technical Information
U.S. TSUBAKI RS ROLLER CHAIN U.S. TSUBAKI ROLLER CHAIN — A SOLID DIFFERENCE ASME/ANSI RS Roller Chain A - DRIVE CHAINS RS ROLLER CHAIN RS11 ˜ RS240 Longer Wear Life Higher Horsepower Ratings Greater Fatigue Strength U.S. Tsubaki Roller Chain lasts up to U.S. Tsubaki ASME/ANSI Chains handle U.S. Tsubaki ASME/ANSI Chains are twice as long as our previous chain in up to 33 percent more horsepower so you designed to have higher fatigue strength. many applications. Advanced technology can increase drive performance without The wider waist of the link plates puts allows us to combine the strength, increasing chain size. In fact, depending more metal where you need it — running durability, and reliability of a solid bushing on your application, you may be able to your application. There is less downtime with our patented lube groove on the transmit the same horsepower with a because chains operate longer. Operating inner surface of sizes RS80 through smaller, less costly chain. The costs are reduced because chains RS140. The solid bushings are precise improvement comes from a U.S. Tsubaki perform more efficiently. These benefits round cylinders, which means better exclusive ring coining process for the slip go right to your bottom line. contact between the pin and bushing. The fit connecting link and special processing lube grooves hold oil where chain needs on the two-pitch offset link. S-N Curve it most. The result is longer lasting chain. Horsepower Ratings Wear Elongation Curve A & a: Fatigue strength B & b: Tensile strength Improved Tsubaki B Chain b Competitor A Competitor B Previous Improved Previous Tsubaki Tsubaki Tsubaki Improved Tsubaki Chain Chain Chain Chain 1.5 33% Increase in Horespower Rating 1.0 RS80-RS140 Other roller chain A .05 "S" Chain load a HP HP 2 3 4 5 6 7 Elongation (%) * Ratings are for RS80-RS240 Roller Chains 1 10 10 0 50 100 150 200 Revs Per Minute (RPM) 10 10 10 10 10 Time (Hours) "N" Number of times load is applied Save Time & Money Wear in the pin-bushing joint can lead to elongation and replacement. -
Chapter 1 Introduction
國立交通大學 機械工程研究所 碩士論文 變速自行車鏈條設計 Design of Chains on Multi-speed Bicycles 研究生:張崇銘 指導教授:曾錦煥 教授 中華民國九十三年六月 變速自行車鏈條設計 Design of Chains on Multi-speed Bicycles 研究生:張崇銘 Student: Chung-Ming Chang 指導教授:曾錦煥 Advisor: Ching-Huan Tseng 國立交通大學 機械工程研究所 碩士論文 A Thesis Submitted to Institute of Mechanical Engineering College of Engineering National Chiao Tung University in Partial Fulfillment of the Requirements for the Degree of Master of Science in Mechanical Engineering June 2004 Hsinchu, Taiwan, Republic of china 中華民國九十三年六月 變速自行車鏈條設計 研究生:張崇銘 指導教授:曾錦煥 國立交通大學機械工程研究所 摘要 本論文主要研究對象為自行車上傳動系統中的鏈條元件,由於自行車飛 輪受到車架、騎乘姿勢所形成的空間限制,必須在有限空間內增加飛輪片 數增加齒數比,達到變速換檔的舒適性。因此,為了配合這樣緊密的飛輪, 鏈條寬度的縮減是必須的。經過專利的整理後,確定空間尺寸和強度為初 步設計的主要需求;提出不同的概念設計,並利用新的鏈條連結機構來達 到鏈條寬度的縮減。 本文提出概念設計較目前市面上自行車最窄的鏈條寬度更窄,強度部份 利用有限元素分析法做定性分析,比較各個設計的相對強度;此外也經由 原型的製作,檢視其機構的問題。 i Design of Chain on Multi-speed Bicycle Student: Chung-Ming Chang Advisor: Ching-Huan Tseng Institute of Mechanical Engineering National Chiao Tung University ABSTRACT This study focuses on the chain for the multi-speed bicycle. Design space for the freewheel on bicycle is limited by frame, riding posture, etc. However, the number of gear ratios in this design space increased with added more sprockets are the trend on the bicycles. Therefore, reduction of chain width is necessary for working with this compact freewheel. Space and strength are main requirements in the beginning of design according to literatures and patents review. Several new concepts are proposed, and these concepts use the linkage mechanism to achieve the reduction of chain width. Chain width of these concepts proposed in this study can be reduced under the assumption for fixed design space and thickness of sprockets. The finite element method is used to compare the trend of strength among these concepts. -
Friction-Producing Mechanisms of a Bicycle Chain
Friction-Producing Mechanisms of a Bicycle Chain _ Effectiveness of Chain Lubricants for Reducing Frictional Losses Copyright ©2014 Friction Facts, LLC rev 5-13-14 Overview The friction-producing mechanisms of a bicycle chain moving through a derailleur-style drivetrain are unique and relatively complex. These friction- producing mechanisms arise from friction created in individual links, which are subjected to multiple regions of both high and low pressure, reciprocating sliding forces, and stiction. As such, testing methods for chain efficiency and chain lubricants must address these complex mechanisms. This paper explores the details of how friction is created in a bicycle chain in a modern-derailleur style drivetrain, the role of chain lubricants to minimize friction in a chain, and the limitations of commonly-used friction test methods. This paper also suggests a testing process to analyze the efficiency of a chain and lubricant in a manner specifically relevant to chain friction-producing mechanisms. Friction-Producing Mechanisms of a Chain From a simplified standpoint, the friction created (wasted energy) by a roller chain is generally proportional to: [chain tension] x [sine of lateral deflection] x [link articulation angle at a given engagement or disengagement point] x [number of link articulations per unit time at that point] x [total engagement and disengagement points in the complete drivetrain]. This basic formula has been demonstrated by multiple drivetrain studies and, more recently, by tests performed by Friction Facts. Essentially, friction is created each time an individual link, under a finite level of tension, bends (articulates) as it engages or disengages the teeth of a cog, pulley, or chainring. -
Technical Engineering Guide
TTEECHCHNINICALCAL EN ENGGINEEINEERRININGG 89 www.diamondchain.com TECHNICAL ENGINEERING General Drive Considerations One of the main advantages of the roller chain drive is its ability to perform well under widely varying conditions. Despite this ability, there are a number of rules of good design practice which, if considered early in the design pro- cess, will enable the user to obtain desirable results. Basic dimensions and minimum ultimate tensile requirements for single-pitch, double-pitch and attachment roller chains are specified by various standards organizations worldwide. ASME/ANSI, The American Society of Mechanical Engineers and The American National Standards Institute, defines dimensions such as: pitch, roller width, roller diameter, link plate height, link plate thickness and pin diameter. The primary purpose of the standard is to ensure that manufacturers will produce chains and sub-assemblies that are similar dimensionally and therefore interchangeable. In addition, the standard does offer the user some assurance of quality by defining a minimum ultimate tensile strength for each model of chain. However, tensile strength is not always a valid method to differentiate one manufacturer’s product from another. It is very important to remember that dimensional standardization does not define quality or performance characteristics. Minimum Ultimate Tensile Strength: Minimum Ultimate Tensile Strength, MUTS, is the static load required to break the chain. Tensile strength values shown in this catalog are not allowable working loads. Load or tension applied 1 to the chain in service should never exceed ⁄6 th of the UTS. If exceeding this value is necessary for a specific applica- tion, contact Diamond Chain. -
Bike Tune Up
Bike Tune Up March 14, 2007 Contents What You Will Need For Tuning Your Bicycle: . 3 What if you get in over your head? . 3 Step 1: Adjust Headset . 4 Step 2: Bottom Bracket Adjustment . 6 Pedals . 7 Step 3: Adjust The Front Wheel Bike Hub . 9 Step 4: Adjust Rear Wheel Hubs . 11 Coaster Brake . 11 Three-Speed Wheels . 11 Derailleur-Equipped and BMX Bicycle Wheels . 11 Overhauling . 12 Freewheels - Overhaul, General Care and Troubleshooting . 12 Step 5: Wheel Truing . 14 Unbending A Bicycle Bent Wheel . 15 Flat Spots . 16 Kinks . 17 Broken Spokes . 17 Step 6: Bike Brake Adjustment . 19 If It Is A Sidepull Or Centerpull Brake: . 21 If It Is A Cantilever Bike Brake: . 21 Replacing A Cable . 22 The Brake Pads . 25 Diagnosing Brake Stickiness . 25 Hand Levers . 25 Step 7: Adjust The Rear Derailleur . 27 Replacing a Cable . 29 Step 8: Adjust The Front Derailleur . 31 Replacing a Cable . 33 Step 9: Finish The Tune-Up . 34 1 2 What You Will Need For Tuning Your Bicycle: • This Presentation • An adjustable wrench or set of wrenches • Tongue and groove pliers, sometimes called ”channellocks” • Bicycle bearing cone wrenches (approx. $8 at bike stores) Figure 1: cone wrench • Oil, grease, and non-flammable, non-toxic cleaning solvent • A couple of screwdrivers • A freewheel remover (maybe) Figure 2: Freewheel Remover • Patience - This is the most important ingredient What if you get in over your head? Ask a friend, or call the mechanic at the local bike shop for advice. In the worst case, you would have to take the bike into the shop and pay for professional help, which would still cost less than a complete tune-up anyway. -
WT Series Actuator Operations Manual WATCH TECHNOLOGIES W T S E R I E S Actuator Operations Manual
Water Control Devices WT Series Actuator Operations Manual WATCH TECHNOLOGIES W T S E R I E S Actuator Operations Manual Watch Technologies 2185 NE Spalding Ave, #10 Grants Pass, OR 97526 Phone 541.472.8095 06/2016 Contents Introduction ………………………………………………............ 1 Theory of Operation ………………………………………. 1 Installation and Start-up ………………………………………… 3 Safety Information ………………………………………… 3 Installation – Rising Stem ………………………………… 4 Installation – Horizontal Gearlift …………………………. 12 Seasonal Start-Up ………………………………………………. 16 Operation ………………………………………………………… 18 Manual Operation ………………………………………… 19 Automated Operation Using Internal RTU ……………… 20 Handwheel Operation …………………………………….. 20 Maintenance and Troubleshooting ……………………………. 21 Troubleshooting Guide …………………………………… 22 Shut-Down and Storage ………………………………………... 23 System Integration and Options ………………………………. 24 Electrical System …………………………………………. 24 Gate Blade Position Sensor ………………………………25 Solar Panel and Charge Controller ……………………... 27 RUG3 Remote Terminal Unit ……………………………. 28 WT Actuator and Gearmotor Specifications ……………29 – 39 Warranty Information …………………………………………… 41 WATER CONTROL DEVICE S Introduction The WT Series of gate control actuators from Watch Technologies have been developed for the ultimate control of a wide variety of applications. he WT Series consists of five distinct models to address the needs of both vertical rising stem gate users as well as systems utilizing T horizontal shaft gear lifts. A wide variety of drive motors enable the WT Series to align with specific torque requirements. The WT Series can also be configured with an embedded Remote Terminal Unit (RTU) which enables the actuator to function as a stand-alone, smart device that can remotely control gates based upon user-defined control points and water status parameters (flow, level). Theory of Operation The philosophy behind each Watch Technologies product is providing long- lived, reliable devices that can be easily installed, maintained, adjusted and upgraded by our customers using simple tools and basic skills. -
Roller Drive Chain Selection and Engineering Information
sec_29.3_29.4_TI 11/19/08 12:45 PM Page 231 Roller Drive Chain Selection 29 Roller Drive Chain Selection and Engineering Information Required information for drive selection: Table 1: Service Factors 1. Type of input power (electric motor, internal combustion Type of Input Power engine, etc.). Internal Internal 2. Type of equipment to be driven. Class of Driven Combustion Combustion Electric Motor 3. Horsepower (HP) to be transmitted. Load Engine with Engine with or Turbine Information Technical Mechanical 4. Full load speed of the fastest running shaft (RPM). Hydraulic Drive Drive 5. Desired speed of the slow-running shaft. NOTE: If the speeds are variable, determine the horsepower to be Uniform 1 1 1.2 transmitted at each speed. Moderate 1.2 1.3 1.4 6. Diameters of the driver and driven shafts. Heavy 1.4 1.5 1.7 7. Center distance of the shafts. NOTE: If this distance is adjustable, determine the Step 3: Calculate the Design Horsepower. amount of adjustment. Design Horsepower = HP x Service Factor 8. Position of drive and space limitations (if any). 9. Conditions of the drive. Drives with more than two The design horsepower equals the horsepower to be sprockets, idlers, or unusual conditions such as severely transmitted times the service factor found in Table 1. abrasive or corrosive environments, severely high or low temperatures, widely fluctuating loads, frequent starts Step 4: Select the Chain Pitch. and stops, etc., require special attention. It is advisable From the Quick Selector Chart on page 234, make a to consult with Renold Jeffrey engineering personnel in tentative chain selection as follows: these situations. -
Mechanical Clutches and Torque Overload Devices Catalog
MECHANICAL CLUTCHES AND TORQUE OVERLOAD DEVICES CATALOG Regal Power Transmission Solutions 7120 New Buffington Road Florence, KY 41042 Customer Service: 800-626-2120 Fax: 800-262-3292 Technical Service: 800-626-2093 www.RegalPTS.com APPLICATION CONSIDERATIONS MECHANICAL CLUTCHES The proper selection and application of power transmission products and components, including the related area of product safety, is the responsibility of the customer. Operating and performance requirements and potential associated issues will vary appreciably depending upon the use and application of such products and components. The scope of the technical and application information included in this publication is necessarily limited. Unusual operating environments and conditions, lubrication requirements, loading supports, and other factors can materially affect the application and operating results of the products and components and the customer should carefully review its requirements. Any technical advice or review furnished by Regal-Beloit America, Inc. and AND TORQUE OVERLOAD its affiliates with respect to the use of products and components is given in good faith and without charge, and Regal assumes no obligation or liability for the advice given, or results obtained, all such advice and review being given and accepted at customer’s risk. For a copy of our Standard Terms and Conditions of Sale, Disclaimers of Warranty, Limitation of Liability and Remedy, please contact Customer Service at 1-800-626-2120. These terms and conditions of sale, disclaimers and limitations of liability apply to any person who may buy, acquire or use a Regal Beloit America Inc. product referred to herein, including any person who buys from a licensed DEVICES CATALOG distributor of these branded products. -
1700 Animated Linkages
Nguyen Duc Thang 1700 ANIMATED MECHANICAL MECHANISMS With Images, Brief explanations and Youtube links. Part 1 Transmission of continuous rotation Renewed on 31 December 2014 1 This document is divided into 3 parts. Part 1: Transmission of continuous rotation Part 2: Other kinds of motion transmission Part 3: Mechanisms of specific purposes Autodesk Inventor is used to create all videos in this document. They are available on Youtube channel “thang010146”. To bring as many as possible existing mechanical mechanisms into this document is author’s desire. However it is obstructed by author’s ability and Inventor’s capacity. Therefore from this document may be absent such mechanisms that are of complicated structure or include flexible and fluid links. This document is periodically renewed because the video building is continuous as long as possible. The renewed time is shown on the first page. This document may be helpful for people, who - have to deal with mechanical mechanisms everyday - see mechanical mechanisms as a hobby Any criticism or suggestion is highly appreciated with the author’s hope to make this document more useful. Author’s information: Name: Nguyen Duc Thang Birth year: 1946 Birth place: Hue city, Vietnam Residence place: Hanoi, Vietnam Education: - Mechanical engineer, 1969, Hanoi University of Technology, Vietnam - Doctor of Engineering, 1984, Kosice University of Technology, Slovakia Job history: - Designer of small mechanical engineering enterprises in Hanoi. - Retirement in 2002. Contact Email: [email protected] 2 Table of Contents 1. Continuous rotation transmission .................................................................................4 1.1. Couplings ....................................................................................................................4 1.2. Clutches ....................................................................................................................13 1.2.1. Two way clutches...............................................................................................13 1.2.1. -
Chain Drive Installation 1
CHAIN DRIVE INSTALLATION THIS DRIVE IS TO BE INSTALLED BY A QUALIFIED HD MECHANIC. FAILURE TO FOLLOW THESE INSTRUCTIONS WILL VOID OUR WARRANTY AND LIABILITY FOR THIS PRODUCT. 1. BDL’s drives are to be used with stock OEM parts. Use of aftermarket parts may require other modifications or may cause starter and alignment problems. (Aftermarket starters may cause premature wear on our starter gear) 2. Fill out our BDL’s registration card. 3. A starter pinion gear is enclosed and is for use on all 1994-up models only. You must replace the stock pinion gear with BDL’s pinion gear on all 1994 up models. 4. You must inspect the drive after the first 100 miles and every 2500 miles after for proper chain tension. 5. Disconnect battery, remove spark plugs and support bike so it will not fall. 6. Remove primary drive if you are replacing an existing drive. (Refer to HD manual) 7. Inspect new drive and check for fit. Install both sprockets and make sure motor and transmission shafts are square with each other. Align sprockets using a 5/16” drill rod or other sturdy straight edge to check for proper alignment. Remove sprockets at this time. 1 8. Install chain adjuster assembly if this is a new installation. 9. Re-install front sprocket and rear clutch basket assembly with chain. 10. Tighten engine nut and transmission mainshaft nut to HD specifications using red loctite. 11. Adjust chain to proper tension. (Refer to HD manual) 12. Soak clutch plates for 15 minutes. We recommend ATF type F or check the HD manual for whichever is recommended for a clutch lubricant.