35.1 SPACE RIDER, the Reusable Orbital & Re-Entry Vehicle For
Total Page:16
File Type:pdf, Size:1020Kb
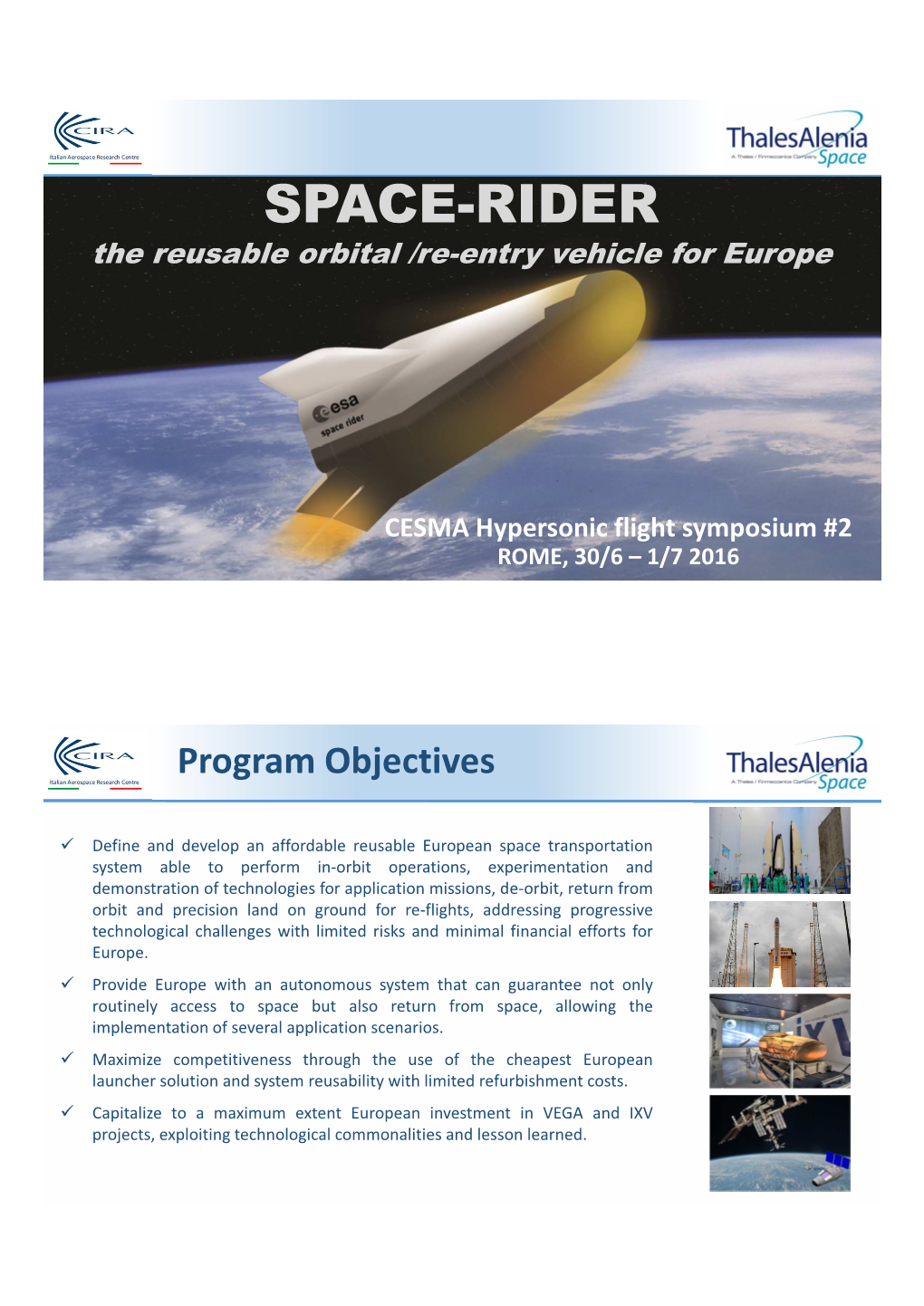
Load more
Recommended publications
-
Gnc 2021 Abstract Book
GNC 2021 ABSTRACT BOOK Contents GNC Posters ................................................................................................................................................... 7 Poster 01: A Software Defined Radio Galileo and GPS SW receiver for real-time on-board Navigation for space missions ................................................................................................................................................. 7 Poster 02: JUICE Navigation camera design .................................................................................................... 9 Poster 03: PRESENTATION AND PERFORMANCES OF MULTI-CONSTELLATION GNSS ORBITAL NAVIGATION LIBRARY BOLERO ........................................................................................................................................... 10 Poster 05: EROSS Project - GNC architecture design for autonomous robotic On-Orbit Servicing .............. 12 Poster 06: Performance assessment of a multispectral sensor for relative navigation ............................... 14 Poster 07: Validation of Astrix 1090A IMU for interplanetary and landing missions ................................... 16 Poster 08: High Performance Control System Architecture with an Output Regulation Theory-based Controller and Two-Stage Optimal Observer for the Fine Pointing of Large Scientific Satellites ................. 18 Poster 09: Development of High-Precision GPSR Applicable to GEO and GTO-to-GEO Transfer ................. 20 Poster 10: P4COM: ESA Pointing Error Engineering -
Glex-2021 – 6.1.1
Global Space Exploration Conference (GLEX 2021), St Petersburg, Russian Federation, 14-18 June 2021. Copyright ©2021 by Christophe Bonnal (CNES). All rights reserved. GLEX-2021 – 6.1.1 Human spaceflight from Guiana Space Center Ch. Bonnal1* – J-M. Bahu1 – Ph. Berthe2 – J. Bertrand1 – Ch. Bonhomme1 – M. Caporicci2 J-F. Clervoy3 – N. Costedoat4 – E. Coletti5 – G. Collange5 – G. Debas5 – R. Delage6 – J. Droz5 E. Louaas1 – P. Marx8 – B. Muller6 – S. Perezzan1 – I. Quinquis5 – S. Sandrone7 D. Schmitt2 – V. Taponier1 1 CNES Launcher Directorate, Pairs, France – 2 ESA Human & Robotic Exploration Directorate, ESTEC, Noordwijk, Netherlands – 3 Astronaut Novespace, Paris, France – 4CNES Guiana Space Center, Kourou, France 5ArianeGroup, Les Mureaux, France – 6Airbus Defence & Space, Toulouse, France – 7Airbus Defence & Space, Bremen Germany – 8Consultant, Paris, France * Corresponding Author Abstract The use of Space has drastically evolved these last ten years. Tomorrow will see easier and cheaper access to Space, satellite servicing, in-orbit manufacturing, human private spaceflights to ever increasing number of Orbital Stations, road to the Moon, Asteroids, Mars. It seems fundamental to make sure we can rely on robust, reliable, frequent and affordable access to and from LEO with both automatic systems and human missions; such systems are the bricks with which all the future operations in Space will be built. Independent human access to space from Europe for our astronauts is a key to any future in Space. It has been studied in depth since the 80's with Hermes Spaceplane, then through numerous studies, pre- development activities, and demonstrations such as ARD, X38-CRV or IXV, which now allow Europe to reconsider such an endeavor with a much higher confidence. -
→ Esrin's Value to Italy
→ ESRIN’S VALUE TO ITALY Authored by: Gustavo Piga, Simone Borra, Alessandro Locatelli and Andrea Salustri Department of Economics and Finance University of Rome Tor Vergata Designed & edited by: ESA – EOGB (Earth Observation Graphic Bureau) Copyright: © 2018 European Space Agency content Executive Summary 04 1. A historical overview of ESRIN 06 The foundation of ESRIN (1964 – 1974) 06 The first steps of ESRIN within the European Space Agency (1975 – 1985) 06 The development of ESRIN and the consolidation of its role (1986 – 1995) 06 ESA corporate functions, EO international cooperation and new programmes (1996 – 2005) 07 ESRIN’s recent history (2006 – present) 08 2. ESRIN’s programme and activities 16 An in-depth analysis of Earth Observation at ESRIN 16 An in-depth analysis of the VEGA Programme 28 3. ESRIN’s economic benefits to Italy 35 The economic and strategic value of ESRIN to Italy 35 The direct, indirect and induced economic impact of ESRIN to Italy 52 The relational and scientific value of ESRIN to Italy 59 Selected literature 75 ESRIN’S VALUE TO ITALY 3 1) ESRIN, ESA Centre for Earth Observation European Defence Agency (EDA) and the European Global Navigation Satellite Systems Agency (GSA). ESRIN, located in Frascati, Italy, is the ESA Centre for Earth Observation and the reference centre for other space-related ESRIN site is managed using environmentally friendly innovation activities (VEGA, the European Small Launcher Programme, technologies (e.g. water consumption, earthquakes regulations Space Rider, the Near Earth Objects Coordination Centre) as well and renewable energy). The new ESRIN Host Agreement was as corporate functions (Information Technology, Communication signed in 2010, and its implementation, still ongoing, offers a and Security). -
ESPI Insights Space Sector Watch
ESPI Insights Space Sector Watch Issue 16 May 2021 THIS MONTH IN THE SPACE SECTOR… MARS LANDING CEMENTS CHINA’S POSITION AS MAJOR SPACE POWER ................................................................ 1 POLICY & PROGRAMMES .................................................................................................................................... 2 ESA awards €150 million in contracts to continue development of Prometheus and Phoebus .......... 2 European Commission targets second study for its space-based secure connectivity project .......... 2 South Korea joins Artemis accords and strengthens partnership with the U.S. ..................................... 2 May marks busy month in UK space sector................................................................................................... 3 NASA temporarily suspends SpaceX’s HLS contract following protests on the award ........................ 3 Spain eyes creation of a National Space Agency .......................................................................................... 3 Space Force awards $228 million GPS contract extension to Raytheon Intelligence and Space ...... 4 China officially establishes company to develop and operate broadband mega constellation ........... 4 Lithuania signs Association Agreement with ESA ........................................................................................ 4 CNES and Bundeswehr University Munich (UniBw) launch SpaceFounders accelerator ..................... 4 The Brazilian Space Agency selects Virgin Orbit -
Lessons Learned from the Use of Sysml in Space Systems at SENER Aeroespacial
Model Based Space System and Software Engineering, MBSE 2020, 28-29 September 2020, ESTEC Lessons learned from the use of SysML in Space Systems at SENER Aeroespacial L. Tarabini-Castellani, V. Gómez, J. Fombellida, S. Ramirez, N. Puente, R. Contreras, R. Haya Sener Aeroespacial S.A., C. Severo Ochoa 4, 28760, Tres Cantos (Spain) EXTENDED ABSTRACT The practical application of the SysML language in engineering processes of stablished organizations is a relevant feedback to steer the evolution and consolidation of the associated methods and tools. SENER started using SysML for Space Systems in 2014. The first project to use SysML was the ESA Proba-3 formation flying demonstration mission. SysML methodology was used for the system design of the ground segment and operations. Since then the number of SENER projects adopting this technique has grown, bringing to a cross fertilization and to the internal standardization of the SysML modeling approach (Figure 1). This paper deals with the evolution of the SysML use in SENER describing for representative projects, covering from full flight systems and subsystems to equipment, the reasons to implement this standard, the benefit achieved and the main lessons learned from its adoption. Figure 1: SENER SysML adoption timeline Proba-3 is a complex ESA formation flying demonstration mission. In 2014, at the beginning of phase C, SENER as prime contractor was in charge to define the ground segment and operations approach. The challenge was to adapt the Redu ground station and the Proba1&2 operations environment to the demanding and highly autonomous Proba-3 formation flying operations. A Mission Operation Concept Document (MOCD) was required in a very short time frame since these activities were not included in the previous phase for budgetary reasons. -
The European Space Agency
THE EUROPEAN SPACE AGENCY UNITED SPACE IN EUROPE ESA facts and figures . Over 50 years of experience . 22 Member States . Eight sites/facilities in Europe, about 2300 staff . 5.75 billion Euro budget (2017) . Over 80 satellites designed, tested and operated in flight Slide 2 Purpose of ESA “To provide for and promote, for exclusively peaceful purposes, cooperation among European states in space research and technology and their space applications.” Article 2 of ESA Convention Slide 3 Member States ESA has 22 Member States: 20 states of the EU (AT, BE, CZ, DE, DK, EE, ES, FI, FR, IT, GR, HU, IE, LU, NL, PT, PL, RO, SE, UK) plus Norway and Switzerland. Seven other EU states have Cooperation Agreements with ESA: Bulgaria, Cyprus, Latvia, Lithuania, Malta and Slovakia. Discussions are ongoing with Croatia. Slovenia is an Associate Member. Canada takes part in some programmes under a long-standing Cooperation Agreement. Slide 4 Activities space science human spaceflight exploration ESA is one of the few space agencies in the world to combine responsibility in nearly all areas of space activity. earth observation launchers navigation * Space science is a Mandatory programme, all Member States contribute to it according to GNP. All other programmes are Optional, funded ‘a la carte’ by Participating States. operations technology telecommunications Slide 5 ESA’s locations Salmijaervi (Kiruna) Moscow Brussels ESTEC (Noordwijk) ECSAT (Harwell) EAC (Cologne) Washington Houston Maspalomas ESA HQ (Paris) ESOC (Darmstadt) Oberpfaffenhofen Santa Maria -
Space Transportation and Exploitation Missions Offered by the VEGA Transportation System That Could Reshape the European Space Industry
DEGREE PROJECT IN MECHANICAL ENGINEERING, SECOND CYCLE, 30 CREDITS STOCKHOLM, SWEDEN 2019 Space Transportation and Exploitation Missions offered by the VEGA Transportation System that could reshape the European Space Industry ADRIAN BUZDUGAN KTH ROYAL INSTITUTE OF TECHNOLOGY SCHOOL OF ENGINEERING SCIENCES 1 Space Transportation and Exploitation Missions offered by the VEGA Transportation System that could reshape the European Space Industry Adrian Buzdugan, Department of Aeronautical and Vehicle Engineering, KTH Royal Institute of Technology, SE-100 44, Stockholm, Sweden e-mail: [email protected] Abstract—The aim of the thesis is to provide the mission utvecklingen samt den tankta¨ marknaden for¨ systemet. Det requirements for the VEGA Transportation System (VTS), the diskuteras hur flera rymduppdrag kan slas˚ ihop sa˚ att sa˚ fa˚ equivalent of Phase 0 of a space project. The decrease in system som mojligt¨ kan hantera dessa uppdrag. Slutligen gors¨ en sizes and masses of the satellites opened the opportunity for jamf¨ orelse¨ mellan arbetet inom AVIO-projektet med ett REXUS- the light capability VEGA launchers to contribute and reshape sondraketprojekt, med tankar och lardomar¨ fran˚ bada˚ projekten. the European space value chain. VTS is envisaged to be an Slutsatser dras utifran˚ portfoljen¨ av uppdrag som tagits for¨ VTS extension of the services offered by the VEGA launcher family, i studien. VTS kommer framover¨ att fortsatta¨ analyseras samt by providing solutions and services of space transportation and motiveras med flera argument for¨ dess forb¨ attring.¨ orbital exploitation. The elaboration of this thesis followed closely a methodology for defining complex space missions discussed by Index Terms—AVIO, VEGA, VTS, VSS, Requirements, Kit authors in Methodology for requirements definition of complex approach, Modularity, Mission, Services, Space, Europe. -
The European Space Agency an Overview
The European Space Agency An overview Nathalie Tinjod, External Relations Department, Director General’s services Phil Airey, Industry, Procurement and Legal services Directorate Zagreb, Croatia, 11 March 2019 ESA UNCLASSIFIED - For Official Use Croatian heart-shaped island of Galešnjak c. JAXA, ESA (ALOS, Japan EO mission, supported by ESA as a third party mission ESA UNCLASSIFIED - For Official Use ESA facts and figures . Over 50 years of EXPERIENCE . From 11 to 22 Member States . Eight facilities in Europe, about 2300 staff . 5.7 billion Euro budget (2019) . Almost 100 satellites designed, tested and operated in flight . ‘coopetition’ : as space is powered by competition but enabled by cooperation, over 500 agreements were concluded since 1975 . Circa 500 satellites/probes sent by Ariane since 1979, or Vega after 2012, from Europe’s spaceport (Kourou) Slide 3 Purpose of ESA “To provide for and promote, for exclusively peaceful purposes, cooperation among European states in space research and technology and their space applications.” Article 2 of ESA Convention Slide 4 Member States Established in 1975, succeeding ESRO and ELDO, ESA currently has 22 Member States 20 states of the European Union, plus Norway and Switzerland By order or ratification, from 1976 to 2015: Sweden, Switzerland, Germany, Denmark, Italy, United Kingdom, Belgium, The Netherlands, Spain, France, Ireland, Austria, Norway, Finland, Portugal, Greece, Luxembourg, Czech Republic, Romania, Poland, Estonia, Hungary Canada takes part in some programmes under a long-standing -
Infinite Worlds Issue 4.Pdf
Infinite Worlds High Flight Oh! I have slipped the surly bonds of Earth And danced the skies on laughter-silvered wings; Sunward I’ve climbed, and joined the tumbling mirth Of sun-split clouds, — and done a hundred things You have not dreamed of — wheeled and soared and swung High in the sunlit silence. Hov’ring there, I’ve chased the shouting wind along, and flung My eager craft through footless halls of air . Up, up the long, delirious burning blue I’ve topped the wind-swept heights with easy grace Where never lark, or ever eagle flew — And, while with silent, lifting mind I’ve trod The high untrespassed sanctity of space, Put out my hand, and touched the face of God. John Gillespie Junior The e-magazine of the Exoplanets Division Of the Asteroids and Remote Planets Section Issue 4 2019 September 1 High Flight, written by John Gillespie Magee Junior (1922-1941) while still a teenager, is one of the world's best-known poems loved by aviators and astronauts. He was born in Shanghai, China, to an English mother and an American father. At the age of eighteen, he enlisted in the Royal Canadian Air Force, trained as a pilot, and was sent to England to fly a Supermarine Spitfire with 412 Fighter Squadron. After a high-altitude test flight, John wrote his parents a letter and enclosed a poem, this one, that the flight inspired Background image. Hubble Deep Field – Credit NASA/ESA. Contents Section officers Meetings BBC program Sky at Night Projects Observations Software Discoveries – latest news On-line courses Web sites of interest Astrobiology Exoplanet space missions Space Section officers ARPS Section Director Dr Richard Miles Assistant Director (Astrometry) Peter Birtwhistle Assistant Director (Occultations) Tim Haymes Assistant Director (Exoplanets) Roger Dymock Exoplanet Technical Advisory Group (ETAG) Peta Bosley, Simon Downs, George Faillace, Steve Futcher, Paul Leyland, David Pulley, Mark Salisbury, Americo Watkins My thanks to those who have contributed to this issue. -
List of PECS Activities
Portugal Space 2030 Strategy Lisbon, September 2020 “Portugal Space Strategy 2020-2030”: Current Implementation Status and a Guide for the Future Prepared by Portugal Space (the Portuguese Space Agency) in collaboration with the Office of the Minister for Science, Technology and Higher Education 14 September 2020 Executive Summary Since the creation of the National Space Agency, Portugal Space, the increased ambition of the country has been transformed into an evolved implementation strategy which, anchored through the successful ESA Ministerial Meeting, Space19+ (November 27-28, 2019), has now resulted into an articulated plan involving other funding frameworks, including EU funds, EU structural funds (ANI, FCT, international partnerships), H2020, FCT (grants and projects), and Portuguese investments in the European Southern Observatory (ESO). The current document, which is split into four parts provides an overview of the current status of implementation of the national space strategy, the main great challenges set as well as a guide for the future. Portugal Space 2030 Strategy Lisbon, September 2020 Table of Contents Part I: Ongoing actions and future main “Great Challenges” ......................................... 3 Part II: Summary of Ongoing Projects .......................................................................... 17 Part III: Guide for the Future beyond the Great Programmatic Challenges ................. 21 Policy Dimension .................................................................................................. -
Spaceplane HERMES Europe’S Dream of Independent Manned Spaceflight More Information About This Series at Luc Van Den Abeelen
Spaceplane HERMES Europe’s Dream of Independent Manned Spaceflight More information about this series at http://www.springer.com/series/4097 Luc van den Abeelen Spaceplane HERMES Europe’s Dream of Independent Manned Spaceflight © CNES/ESA Luc van den Abeelen Hilversum, The Netherlands SPRINGER-PRAXIS BOOKS IN SPACE EXPLORATION Springer Praxis Books ISBN 978-3-319-44470-3 ISBN 978-3-319-44472-7 (eBook) DOI 10.1007/978-3-319-44472-7 Library of Congress Control Number: 2016951211 © Springer International Publishing AG 2017 This work is subject to copyright. All rights are reserved by the Publisher, whether the whole or part of the material is concerned, specifically the rights of translation, reprinting, reuse of illustrations, recitation, broadcasting, reproduction on microfilms or in any other physical way, and transmission or information storage and retrieval, electronic adaptation, computer software, or by similar or dissimilar methodology now known or hereafter developed. The use of general descriptive names, registered names, trademarks, service marks, etc. in this publication does not imply, even in the absence of a specific statement, that such names are exempt from the relevant protective laws and regulations and therefore free for general use. The publisher, the authors and the editors are safe to assume that the advice and information in this book are believed to be true and accurate at the date of publication. Neither the publisher nor the authors or the editors give a warranty, express or implied, with respect to the material contained -
Space Rider Aerodynamics and Aerothermodynamics from Hypersonic to Subsonic Flight
DOI: 10.13009/EUCASS2019-990 8TH EUROPEAN CONFERENCE FOR AERONAUTICS AND SPACE SCIENCES (EUCASS) Space Rider Aerodynamics and Aerothermodynamics from hypersonic to subsonic flight Olivier LAMBERT* and Marie-Christine BERNELIN** *Dassault Aviation, Saint-Cloud, France [email protected] **Dassault Aviation, Saint-Cloud, France [email protected] Abstract This paper summarizes aerodynamic and aerothermodynamic studies conducted in the frame of Space Rider program. Building on IXV heritage, which successfully flew on February, 11th 2015, IXV aeroshape “as-it-is” has been elected as a suitable candidate capable of fulfilling Space Rider new mission requirements. Flight domain has been extended to transonic and subsonic Mach numbers thanks to WTT conducted at INCAS trisonic facility in Bucharest, Romania. For the hot part of the reentry, in order to counterbalance a significantly higher mass for Space Rider than for IXV, IXV flight data analyses have been conducted to allow thermal margins policy revision. 1. Introduction Space Rider aims to provide Europe with an affordable, independent, reusable end-to-end integrated space transportation system for routine access and return from low earth orbit. It will transport payloads for an array of applications, orbit altitudes and inclinations. The Space Rider will be launch on VEGA-C and land smoothly and safely on ground thanks to Descent and Recovery System based on piloted parafoil. The Space Rider will be able to stay in orbit up to two months and will be reusable. The Space Rider vehicle design inherits from technology developed for the ESA IXV vehicle which performed a successful aero-controlled atmospheric re-entry trajectory on the 11th of February 2015.