Guide to Glass - the Selection Process Thermal ● Optical ● Chemical ● Electrical ● Mechanical
Total Page:16
File Type:pdf, Size:1020Kb
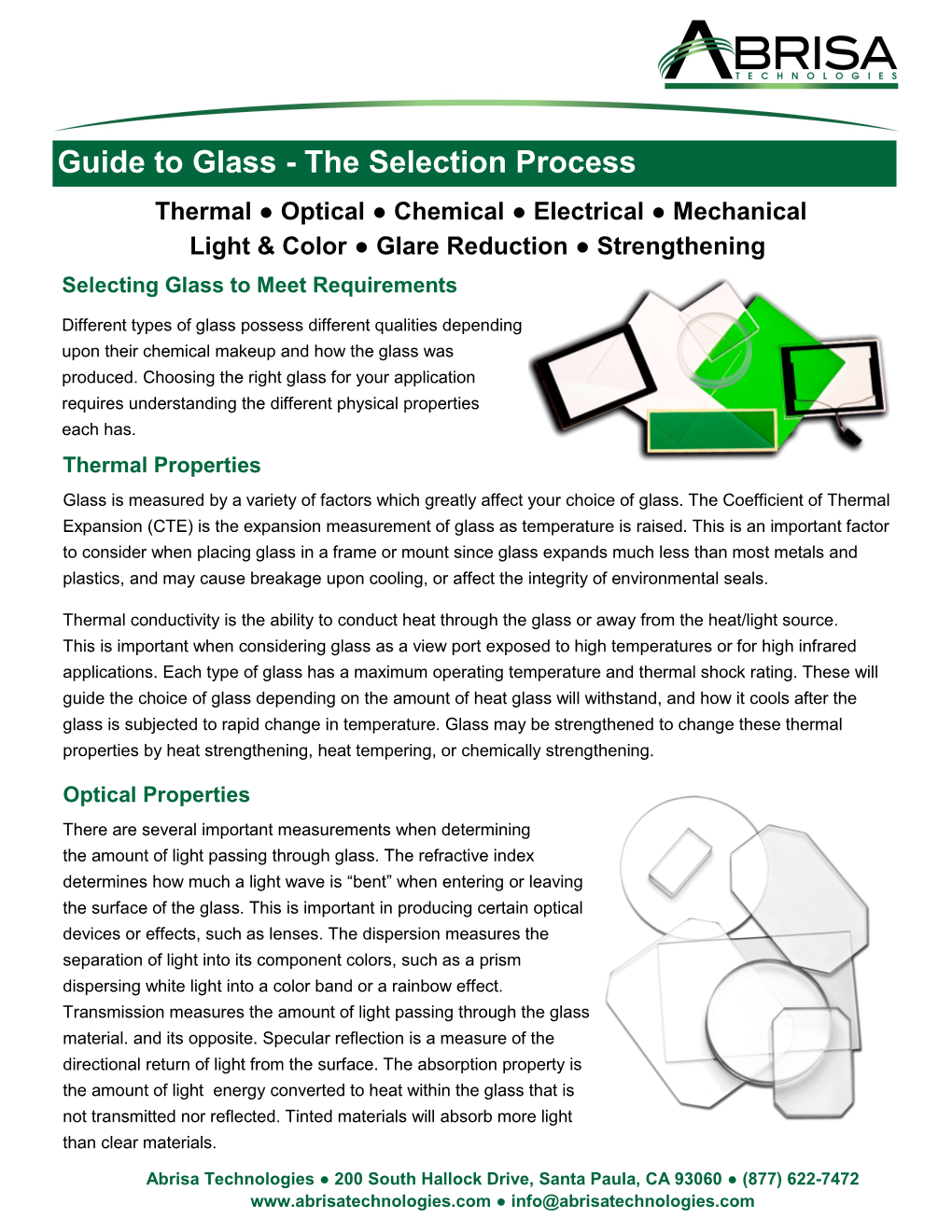
Load more
Recommended publications
-
High-Precision Micro-Machining of Glass for Mass-Personalization and Submitted in Partial Fulfillment of the Requirements for the Degree Of
High-precision micro-machining of glass for mass-personalization Lucas Abia Hof A Thesis In the Department of Mechanical, Industrial and Aerospace Engineering Presented in Partial Fulfillment of the Requirements For the Degree of Doctor of Philosophy (Mechanical Engineering) at Concordia University Montreal, Québec, Canada June 2018 © Lucas Abia Hof, 2018 CONCORDIA UNIVERSITY School of Graduate Studies This is to certify that the thesis prepared By: Lucas Abia Hof Entitled: High-precision micro-machining of glass for mass-personalization and submitted in partial fulfillment of the requirements for the degree of Doctor of Philosophy (Mechanical Engineering) complies with the regulations of the University and meets the accepted standards with respect to originality and quality. Signed by the final examining committee: ______________________________________ Chair Dr. K. Schmitt ______________________________________ External Examiner Dr. P. Koshy ______________________________________ External to Program Dr. M. Nokken ______________________________________ Examiner Dr. C. Moreau ______________________________________ Examiner Dr. R. Sedaghati ______________________________________ Thesis Supervisor Dr. R. Wüthrich Approved by: ___________________________________________________ Dr. A. Dolatabadi, Graduate Program Director August 14, 2018 __________________________________________________ Dr. A. Asif, Dean Faculty of Engineering and Computer Science Abstract High-precision micro-machining of glass for mass- personalization Lucas Abia Hof, -
Fusing Fusing
® Artist Robert Wiener FusingFusing ToolsTools && AccessoriesAccessories ProductProduct CatalogCatalog www.dlartglass.com © 2019 D&L Art Glass Supply © 2019 D&L Art Glass Artist Nancy Bonig 303.449.8737 • 800.525.0940 Table of Contents About the Artwork Cover - Artist: Robert Wiener, DC Art Glass Series: Colorbar Murrine Series Title: Summer Salsa Size: 6" square (approx.) Website: www.dcartglass.com Photographer: Pete Duvall Table of Contents- Alice Benvie Gebhart Title: Distant Fog Size: 6 x 8" Website: www.alicegebhart.com Kilns ..........................................................................1-16 Tabletop Kilns .......................................................................................................... 1–3 120 Volt Kilns ............................................................................................................1-5 240 Volt Kilns ........................................................................................................ 6-12 Kiln Controllers at a Glance .....................................................................................13 Kiln Shelves .......................................................................................................... 14–15 Kiln Furniture and Accessories ................................................................................16 Kiln Working Supplies ....................................... 17-20 Primers & Shelf Paper ...............................................................................................17 Fiber Products & Release -
Simultaneous Chemical Vapor Deposition and Thermal Strengthening of Glass Abstract 1. Introduction
Accepted Manuscript: for final journal publication see https://doi.org/10.1016/j.tsf.2018.11.028 1 Simultaneous chemical vapor deposition and thermal strengthening 2 of glass 3 4 Peter Sundberg1, Lina Grund Bäck1, Robin Orman2, Jonathan Booth2, Stefan Karlsson1* 5 1RISE Research Institutes of Sweden, Built Environment Division, Glass Section, SE-351 96 Växjö, 6 Sweden 7 2Johnson Matthey Technology Centre, Blounts court, Sonning Common, Reading, RG4 9NH, United 8 Kingdom 9 *Corresponding author: [email protected] 10 11 Keywords: Chemical vapour deposition, thermal strengthening, crack resistance, contact angle, 12 hardness 13 14 Declaration of interest: none. 15 16 Abstract 17 In the current paper we present a concept combining metal organic chemical vapor deposition with 18 thermal strengthening process of flat glass. As the flat glass is heated to be thermally strengthened, 19 which takes a few minutes, there is an opportunity for performing a surface modification. We describe 20 the application of transparent and amorphous Al2O3 thin films during the thermal strengthening process. 21 Al2O3 was chosen due to the following desirable properties: increased surface mechanical properties 22 and increased chemical durability, the latter has not been investigated in the current paper. The residual 23 surface compressive stresses after performed strengthening of the coated glasses were quantified to 24 be in the range of 80-110 MPa. The Al2O3 content in the surface was measured using the Surface 25 Ablation Cell employed with Inductively Coupled Plasma Atomic Emission Spectroscopy and found to 26 be at least doubled at the surface and having an increased Al2O3 content at least 0.5 µm underneath 27 the glass surface. -
Chemical and Pharmaceutical Sight Glass Application Handbook
Chemical and Pharmaceutical Sight Glass Application Handbook How to Specify and Understand Sight Glasses for Process Observation L.J. Star Incorporated provides an extensive line of process observation equipment—sight glasses, lights, sanitary fittings, and level gage instrumentation. Product lines include Metaglas® Safety Sight Windows, Lumiglas® Explosion Proof Lights and Cameras, Visual Flow Indicators, Sight Ports, Sanitary Clamps, Magnetic Level Gages and Gage Glass. Metaglas is the #1 selling fused sight glass, proven in thousands of installations around the world. Unlike some other sight glasses, it meets stringent DIN 7079 and DIN 7080 quality standards, and has been tested and proven to meet The USP Type I standard. Table of Contents Introduction ii General Properties of Glass 1 Glass Types 1 Chemical Resistance 3 Toughened (Tempered) Glass 5 Fused-Glass Sight Glass 7 Sight Glass Design and Application 8 Determining Sight Glass Thickness 11 Critical Standards for Specifying Sight Glasses 11 Lighting Considerations 13 Factors of Reflected Light 15 Installation and Maintenance Tips 18 i Chemical and Pharmaceutical Sight Glass Applications Handbook This handbook is dedicated to the memory of Edward K. Lofberg, a glass expert with Corning Glassworks for more than 40 years who was instrumental in helping L.J. Star develop expertise in the application of glass for process observation. Introduction Improperly specified, installed or maintained, sight glasses can easily become the weakest link in a chemical or pharmaceutical processing system. They may provide less than needed observation capabilities, they may require frequent maintenance and replacement, they may be difficult to illuminate and, in worst case, they may actually fail, endangering workers and causing extensive destruction and downtime. -
Borosilicate Glass 3.3 – DIN 7080
Continental Trade Sp. z o.o. Krasnobrodzka 5; 03-214 Warszawa POLAND tel. : +48 22 6701181, +48 22 6190733 fax : +48 22 6185938 www.continentaltrade.com.pl INFORMATION SHEET [email protected] Borosilicate Glass 3.3 – DIN 7080 Main ingredients of this glass are sodium oxide Na2O, boron oxide B2O3, silicon dioxide SiO2. In those ingredients, boron and silicon have high content: boron 12,5 – 13,5 %, silicon 78 – 80 %. SiO2 80 % B2O3 13 % Na2O 4 % Al2O3 2 % K2O 1 % Trade The feature of borosilicate glass 3.3 is that it has low thermal expansion coefficient, good thermal stability, chemical durability and electric property. Therefore, it’s chemical resistant, heat resistant and mechanical property is excellent. So borosilicate glass is also called heat resistance glass. Borosilicate glass 3.3 can be milled, drilled, grounded and toughened. Its low coefficient of thermal expansion, high thermal shock resistance and ability to work at temperatures up to 450 ° C for a long period of time, make this type of glass particularly suitable for use in stable temperature conditions. Is suitable for operation at low temperatures. This glass can withstand the temperature to about -196 °C (is suitable for use in contact with liquid nitrogen). During thawing ensure that the temperature difference does not exceed 100 K. In general is recommended for use down to - 70 °C. This glass is extremely resistant to water, alkalis, acids and organic substances. Properties Mechanical Performance Density 2.23 ±0.02 g/cm3 Bending strength 160 N/mm2 Surface compressive stress 100 N/mm2 Young’s modulus 64 GPa Poisson’s ratio 0,2 Hardness 5.5 Mohs, (470 Knopp, 580 Vickers) Thermodynamic Performance ContinentalThermal expansion coefficient (0 – 300 °C) 3.3 ±0.1×10-6K-1 (@ 0 – 300 °C) Softening point 815 ±10 °C Strain point 560 ±10 °C Caloricity (20 – 100 °C) 0.83 KJ× (kgxK)-1 (@ 20 – 100 °C) Thermal coefficient 1.2 WxmxK-1 Thermal shock resistance 180K While every attempt has been made to verify the source of the information, no responsibility is accepted for accuracy of data. -
Glass for the Future
glass for the future www.controlglass.com With the experience obtained in the last 20 years, Control Glass has suc- ceeded in gathering all the processes a glass processor of the 21st cen- tury should offer to the glass professionals. With the new plant in Platea (Teruel) for the production of curved laminated and tempered glass we have become one of the most polyvalent glass groups in Europe, being able to offer the widest range of processed products, with the capacity to combine different processes such as laminating, tempering, bending, double glazing or printed with ceramic inks. We have over 50.000 m2 between factories, warehouses and technical offices, distributed around all over Europe, enabling us to deliver our pro- ducts to any point of the world. All our glasses meet the high demands of the applicable European Norms and also the Technical Building Code, which through the European Directive “Products for Buildings” 89/106/CE imposes the marking and declaration of technical characteristics of buil- ding products permanently incorporated in the building site. The “Obligatory CE Marking” allows for the manufacture and sale of the products within the European Union and requires a satisfactory evaluation of the products in accor- dance with the corresponding harmonized norms and with the applicable certificate of conformity. You can request the obligatory CE Marking of the products that Control Glass manufac- tures and selles through their web site: www.controlglass.com On the other hand, Control Glass has proved its commitment through the quality of its products and its customer care by obtaining the voluntary product certification for APPLUS double glazing units for all its factory units, as well as the global voluntary cer- tification according to the Quality Assurance System ISO 9001-2008, supported by the British Standards Institution certifying authority. -
S41467-021-22595-1.Pdf
ARTICLE https://doi.org/10.1038/s41467-021-22595-1 OPEN Explosive fragmentation of Prince Rupert’s drops leads to well-defined fragment sizes ✉ Stefan Kooij 1 , Gerard van Dalen2, Jean-François Molinari 3 & Daniel Bonn1 Anyone who has ever broken a dish or a glass knows that the resulting fragments range from roughly the size of the object all the way down to indiscernibly small pieces: typical fragment size distributions of broken brittle materials follow a power law, and therefore lack a char- 1234567890():,; acteristic length scale. The origin of this power-law behavior is still unclear, especially why it is such an universal feature. Here we study the explosive fragmentation of glass Prince Rupert’s drops, and uncover a fundamentally different breakup mechanism. The Prince Rupert’s drops explode due to their large internal stresses resulting in an exponential frag- ment size distribution with a well-defined fragment size. We demonstrate that generically two distinct breakup processes exist, random and hierarchical, that allows us to fully explain why fragment size distributions are power-law in most cases but exponential in others. We show experimentally that one can even break the same material in different ways to obtain either random or hierarchical breakup, giving exponential and power-law distributed fragment sizes respectively. That a random breakup process leads to well-defined fragment sizes is surprising and is potentially useful to control fragmentation of brittle solids. 1 Van der Waals-Zeeman Institute, University of Amsterdam, Amsterdam, The Netherlands. 2 Unilever Research and Development Vlaardingen, Olivier van Noortlaan, Vlaardingen, The Netherlands. -
Temperature Dependent Load Bearing Capacity of Laminated Glass Panes 2010 54 1 11 Influences the Strength of Glass Pane
Ŕ periodica polytechnica Temperature dependent load bearing Civil Engineering capacity of laminated glass panes 54/1 (2010) 11–22 doi: 10.3311/pp.ci.2010-1.02 Kinga Pankhardt / György L. Balázs web: http://www.pp.bme.hu/ci c Periodica Polytechnica 2010 RESEARCH ARTICLE Received 2009-11-11, accepted 2010-03-30 Abstract An experimental programme with numerous single and lam- inated glass specimens was carried out to study the tempera- ture dependent behaviour of laminated glasses. The difference of load bearing capacities between the laminate manufactured from ordinary float (laminated glass) or tempered glass layers (safety laminated glass) were also studied in four-point bending. Fig. 1. Glass separation wall When glass laminate fractures, the interlayer can keep the frag- ments in place. Different types of interlayer materials, both resin 1 Introduction and foil (type EVA) were studied in safety and non safety lami- Tendency of architecture is to use larger size glass panes or nated glass specimens. Glasses are used not only in the interior to expose it to carry high loads e.g. glass slabs with carry loads but also in exterior places. Therefore, the effect of temperature of cars. Therefore, appropriate laminated glass panes should be of -20˚C, +23˚C and +60˚C were investigated on bending char- selected in order to avoid excessive deflections, and the effect acteristics of glasses. The main influencing factors on the load of temperature – especially at outdoor conditions – has to be bearing capacity and bending characteristics of the glass spec- taken into account to the calculations. Glass is often used as a imens were investigated e.g. -
Intermac REWRITING PRODUCTION STANDARDS; PUSHING PLANNING and DESIGN
THE LEADING MAGAZINE FOR THE INTERNATIONAL FLAT GLASS INDUSTRY #8EL8IP <9IL8IPa2<8Ia'F Intermac REWRITING PRODUCTION STANDARDS; PUSHING PLANNING AND DESIGN LiSEC NEW LOGISTICS SOLUTION TO REVOLUTIONIZE INSULATING GLASS HANDLING CUGHER GLASS PRINTING TWO GLASSES AT THE SAME TIME A+W 2 - Copia omaggio € HELPING A COMPANY UÊÊ REINVENT ITSELF – FROM VILLAGE GLASS TO EUROVIEW Neptun CUSTOMIZATION ON AN INDUSTRIALIZED SCALE Poste Italiane Spa - Spedizione in abbonamento postale - 70% - LO/MI www.glassonline.com 31/01/18 12 MULTIGLASS MULTI-ROLLER COATING MACHINE FOR THE ENAMELLING AND DESIGN PRINTING OF FLOAT GLASS SHEEETS Rollmac a division of Gemata S.p.A. - Via Postale Vecchia, 77 - 36070 Trissino (VI) Italy Tel. +39 0445.490618 - Fax +39 0445.490639 - E-mail: [email protected] - www.rollmac.it Take it easy. Bystronic glass handling equipment guarantee a fl exible Try the Easy-Lift WINDOW at FENSTERBAU 2018 and economic use for all fl at glass processing sectors and in Nuremberg (Germany): window manufacturing. Glass handling with minimum physical effort required by the operator. Choose the most appropriate vacuum generation product for your individual needs. FENSTERBAU FRONTALE Hall 3A Booth No. 303 Get more information and fi nd your personal consultant by visiting www.bystronic-glass.com/handling IR medium wave twin tubes emitters for: iÃÊ +Õ>ÀÌâÊ >ÃÊ «À`ÕViÃÊ } ÞÊ Ê UÊ >>Ì}Êià >««ÀiV>Ìi`Ê iµÕ«iÌÊ vÀÊ Ì iÊ }>ÃÃÊ Ê UÊ ÀÀÀ}Êià industry such as manual and au- Ê UÊ `ÀÞÊÃVÀiiÊ«ÀÌ}Êià tomatic tin side detectors and UV polymerization units. IR medium wave single tube emitters for: Ê UÊ Li`}ÊvÕÀ>ViÃ Ê UÊ vÕÃÊvÕÀ>Vi IR fast medium wave twin tube emitters for: Ê UÊ >>Ìi`Ê}>ÃÃÊVÕÌÌ}Ê>V ià www.heliosquartz.com Helios Quartz Group SA Helios Italquartz S.r.l. -
Glasses Refractories Abrasives Cements Products Ceramics
CERAMIC MATERIALS I Asst. Prof. Dr. Ayşe KALEMTAŞ [email protected], [email protected], Phone: 211 19 17 Metallurgical and Materials Engineering Department INTRODUCTION MATERIALS CERAMIC METAL POLYMER COMPOSITE D CLAY ADVANCED GLASSES REFRACTORIES ABRASIVES CEMENTS PRODUCTS CERAMICS Glass- Glasses ceramics Asst. Prof. Dr. Ayşe KALEMTAŞ INTRODUCTION HISTORY DEFINITION PROPERTIES APPLICATIONS Asst. Prof. Dr. Ayşe KALEMTAŞ INTRODUCTION Four of the major technological achievements in glass which have had the most profound impact on mankind. Glass window – which enables sunlight to come into dwelling unit . Lenses – opthamics for improved vision, microscope, telescope optics . Light bulb envelope - lighting . Semiconducting glasses – for computer memory, solar cell, photocopiers Asst. Prof. Dr. Ayşe KALEMTAŞ Well Known Glass Products www.whitersstreetglass.com.au Glass splashbacks http://www.wickedreport.com Hirom Glass Violin is a product of Hario www.toxel.com Glass Co. Ltd., Japan. And also, The Glass Bathtub world’s first hand made glass violin. http://freshome.com http://worlds-interior-design.blogspot.com Superdurable tempered glass Wall-to-wall glass windows Asst. Prof. Dr. Ayşe KALEMTAŞ Well Known Glass Products Asst. Prof. Dr. Ayşe KALEMTAŞ Well Known Glass Products Tempered glass table http://freshome.com http://www.ifjk.org www.aarticommercial.com/prod www.tripadvisor.com ucts.php Heat resistant Glass sink cabinets in the bathroom Laminated Windscreen Glass glass door Asst. Prof. Dr. Ayşe KALEMTAŞ Well Known Glass Products http://www.wolfard.com Classic Wolfard Oil Lamp Heat resistant glass lid Heat resistant glassware Tempered Glass (microwave safe) Cutting Board Asst. Prof. Dr. Ayşe KALEMTAŞ INTRODUCTION Any material that exhibits only a short-range order of atoms or ions is an amorphous material; that is, a noncrystalline one. -
Shattering Glass Cookware Sur- Efaced As an Issue of Concern During the Past Two Decades, and Reports of Problems Have Been Chron- Icled in Several News Stories
Remnants of soda lime silicate ) glass cookware failure, from Consumer Reports testing. Consumer Reports. (Credit: xploding† or shattering glass cookware sur- Efaced as an issue of concern during the past two decades, and reports of problems have been chron- icled in several news stories. Collectively, the accumu- Shattering lated complaints suggest that there may be a fracture problem with some glass cookware products. However, glass cookware none of the coverage has specifically addressed the R.C. Bradt and R.L. Martens scientific aspects of the reported failures. This article examines the technical aspects of the sudden, explo- sion-like failure of glass cookware products. The shattering of glass cookware in house- Background hold kitchens has been reported in Consumer Corning Inc. pioneered the development and market for glass cookware. The Reports articles,1,2 television documentaries, glass cookware products originally manufactured by Corning were made of a low thermal expansion borosilicate glass eventually marketed as Pyrex.5 (Many complaints to the United States Consumer glass scientists also associate the name Pyrex with the original borosilicate glass Products Safety Commission3 and Internet post- products. Even today, Corning still produces high-quality borosilicate laboratory ings.4 This article examines the issue from a glassware under the name and trademark of Pyrex.) The original Pyrex cookware was promoted as “oven to icebox” or “ice- three fold technical perspective: (i) reviewing box to oven” cookware,6 presumably because the low coefficient of thermal the reported scenarios of the incidents, which expansion of the borosilicate glass made it highly resistant to the thermal are suggestive of thermal stress fracture; (ii) stresses that develop during these types of temperature changes. -
Sponso Ed Capture Clarity
A METAL & GLAZING ® MAGAZINE Supplement GlassA GUIDE TO Codes YOUR GUIDE TO UNDERSTANDING: • Energy Codes • Safety Glazing Codes • Wildlife Codes • Fire Safety Codes • And More Sponsoed Capture clarity. Fit the bill—and the build—with new Acuity™ Low-Iron Glass. Elevate aesthetics for a modest investment, without sacrificing performance. New Acuity™ Glass by Vitro Architectural Glass (formerly PPG Glass) is an affordable low-iron solution available with Solarban® solar control low-e coatings, offering vivid views with no green cast. Where conventional clear glass was once a given, pure clarity is now within reach. Request samples and learn more at vitroglazings.com/acuity A METAL & GLAZING ® MAGAZINE Supplement Contents GlassA GUIDE TO Codes YOUR GUIDE TO UNDERSTANDING: Glass • Energy Codes • Safety Glazing Codes • Wildlife Codes Take a closer look at the unique beauty of glass. • Fire Safety Codes 2 • And More Codes for the Planet Glass can help architectural building projects look good and increase 4 energy performance at the same time. Understanding the energy Sponsored code requirements is key to designing an attractive, efficient building that features ample use of glass. Codes that Bind What you need to know about the structural performance 8 requirements of building codes governing the use of glass and On the Cover glazing materials. The Daimler Trucks North America Headquarters in Codes for Safety and Health Portland, Ore., features Vitro Architectural Glass’ Solarban® Safety glazing codes are designed to preserve the lives of and/or re- R100 Solarblue® glass fabricated 12 duce injuries to any individual who comes in contact with glass in a by Hartung Glass and installed particular opening.