Long Term Displacement Data of Woven Fabric Webbings Under Constant Load for Inflatable Structures
Total Page:16
File Type:pdf, Size:1020Kb
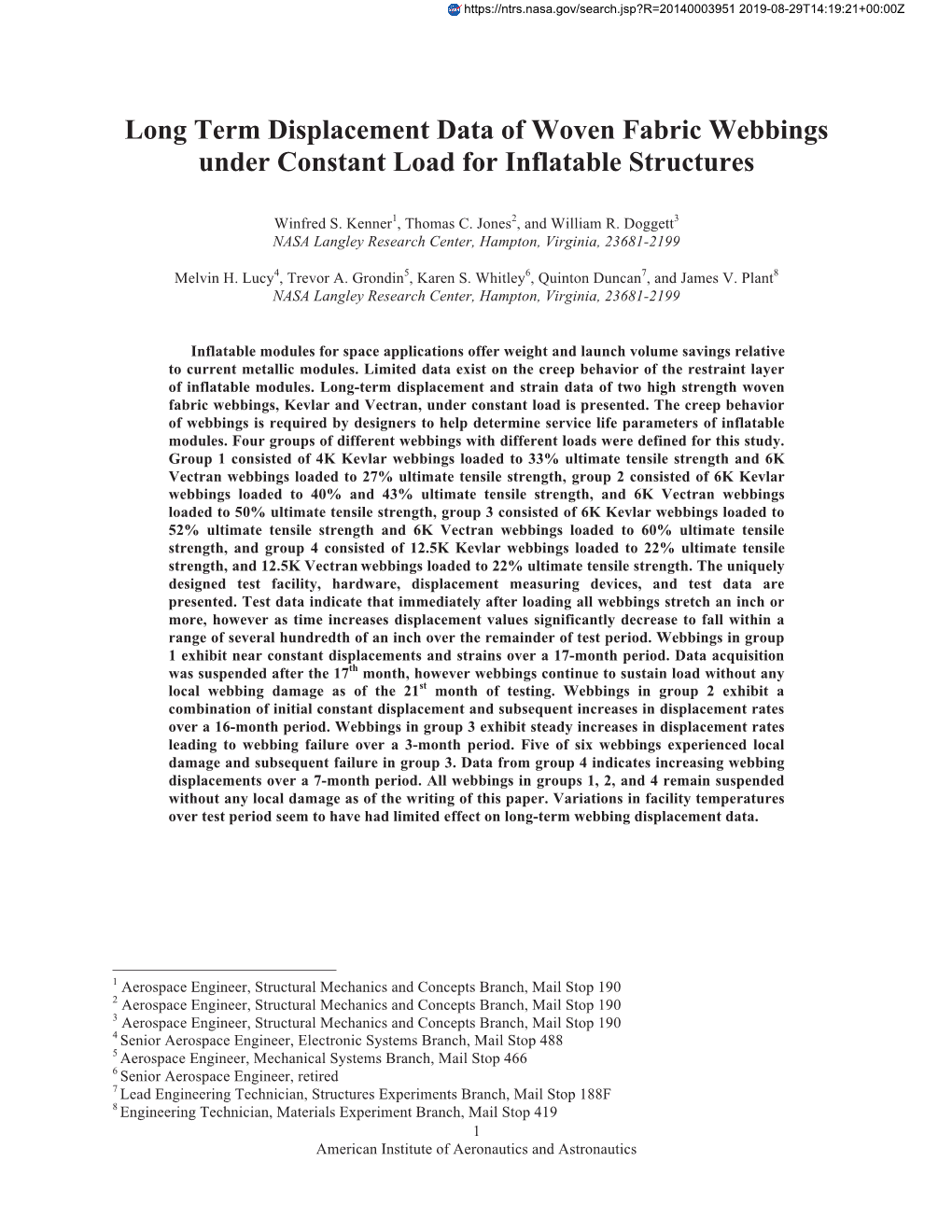
Load more
Recommended publications
-
Long Term Loading and Additional Material Properties of Vectran Fabric for Inflatable Structure Applications
Graduate Theses, Dissertations, and Problem Reports 2010 Long Term Loading and Additional Material Properties of Vectran Fabric for Inflatable Structure Applications Timothy L. Weadon Jr. West Virginia University Follow this and additional works at: https://researchrepository.wvu.edu/etd Recommended Citation Weadon, Timothy L. Jr., "Long Term Loading and Additional Material Properties of Vectran Fabric for Inflatable Structure Applications" (2010). Graduate Theses, Dissertations, and Problem Reports. 4669. https://researchrepository.wvu.edu/etd/4669 This Thesis is protected by copyright and/or related rights. It has been brought to you by the The Research Repository @ WVU with permission from the rights-holder(s). You are free to use this Thesis in any way that is permitted by the copyright and related rights legislation that applies to your use. For other uses you must obtain permission from the rights-holder(s) directly, unless additional rights are indicated by a Creative Commons license in the record and/ or on the work itself. This Thesis has been accepted for inclusion in WVU Graduate Theses, Dissertations, and Problem Reports collection by an authorized administrator of The Research Repository @ WVU. For more information, please contact [email protected]. Long Term Loading and Additional Material Properties of Vectran Fabric for Inflatable Structure Applications Timothy L Weadon, Jr Thesis submitted to the College of Engineering and Mineral Resources at West Virginia University in partial fulfillment of the requirements -
A Perspective on High-Performance CNT Fibres for Structural Composites
A Perspective on High-performance CNT fibres for Structural Composites Anastasiia Mikhalchan, Juan José Vilatela IMDEA Materials Institute, C/Eric Kandel 2, Getafe, Madrid, Spain, 28906 This review summarizes progress on structural composites with carbon nanotube (CNT) fibres. It starts by analyzing their development towards a macroscopic ensemble of elongated and aligned crystalline domains alongside the evolution of the structure of traditional high- performance fibres. Literature on tensile properties suggests that there are two emerging grades: highly aligned fibres spun from liquid crystalline solutions, with high modulus (160 GPa/SG) and strength (1.6 GPa/SG), and spun from aerogels of ultra-long nanotubes, combining high strength and fracture energy (up to 100J/g). The fabrication of large unidirectional fabrics with similar properties as the fibres is presently a challenge, which CNT alignment remaining a key factor. A promising approach is to produce fabrics directly from aerogel filaments without having to densify and handle individual CNT fibres. Structural composites of CNT fibres have reached longitudinal properties of about 1 GPa strength and 140 GPa modulus, however, on relatively small samples. In general, there is need to demonstrate fabrication of large CNT fibre laminate composites using standard fabrication routes and to study longitudinal and transverse mechanical properties in tension and compression. Complementary areas of development are interlaminar reinforcement Corresponding Author. E-mail: [email protected] (Anastasiia Mikhalchan) Corresponding Author. E-mail: [email protected] (Juan José Vilatela) 1 with CNT fabric interleaves, and multifunctional structural composites with energy storage or harvesting functions. 2 TABLE OF CONTENTS PART 1. State-of-the-art of CNT fibres 5 1.1 Synthesis and hierarchical structure of CNT fibres 5 1.2 Mechanical properties of CNT fibres 8 1.3 Historical retrospective on R&D of commercial high-performance fibres and CNT 11 fibres PART 2. -
Industrial Fabric Yarn Fibers Processes Products
MOVING HIGH PERFORMANCE FIBERS FORWARD INDUSTRIAL FABRIC YARN FIBERS PROCESSES PRODUCTS WHY FIBER-LINE®FIBER INDUSTRIAL OPTICAL FABRIC CABLES YARN? Key Features Overview • Available Flat or Twisted • FIBER-LINE®’s offering of Industrial Fabric Yarn are utilized in a wide • Material can be “Rolled flat” to remove range of applications. FIBER-LINE®’s marriage of high-performance false or producers’ twist fibers and additional processing create unique products that extend • Metered lengths and various spool sizes the life of our customer’s end use product. available • Our yarn have been processed in a variety of different ways utilizing: Knitting, weaving, braiding. FIBER-LINE® FIBERS FOR INDUSTRIAL FABRIC YARN Packaging • Kevlar® Para-Aramid FIBER-LINE® Industrial Fabric Yarn are supplied on a variety of card- • Nomex® Meta-Aramid board tubes to meet your equipment needs. Contact us today • Vectran® Liquid Crystal Polymer (LCP) with tube dimensions you require. Packages can be supplied on colored, • Carbon Fiber embossed and/or slit tubes. Plastic or metal reels are also available. • Fiberglass • Technora® FIBER-LINE® PERFORMANCE ADDING COATINGS • FIBER-LINE® Colorcoat™: Vibrant Colors for Aesthetic Applications • FIBER-LINE® Wearcoat™: Abrasion & High-Temperature Resistance • FIBER-LINE® Bondcoat™: Adhesion Promotion • FIBER-LINE® Repelcoat™: Water Repellancy • FIBER-LINE® Protexcoat™: UV Degradation Prevention MOVING HIGH PERFORMANCE FIBERS FORWARD POPULAR INDUSTRIAL FABRIC YARN PRODUCTS FIBER-LINE® Nominal Product ID Base Fiber Nominal -
High Performance Fibers
High Performance Fibers One step ahead High Performance Fibers are engineered for extreme uses; whether the requirement is exceptional strength, stiffness, heat resistance and/or chemical resistance. EuroFibers is proud distribution partner of the leading brands in this industry with the ability to tailor these tough fibers to the need of our customers, whether it be coating, twisting, assembling, plying or cutting. HMPE Fiber Para-Aramid Fiber Ultra high molecular weight polyethylene (UHMwPE), high modulus Para-aramid fibers are a class of heat-resistant and extremely strong polyethylene (HMPE) or high performance polyethylene fibers (HPPE) synthetic fibers. The ultimate strength of some aramid fibers can are extremely strong and are the lightest of all ultra-strong fibers. exceed 3500 MPa. Aramid has an outstanding strength-to-weight The ultimate strength can exceed 3000 MPa. However, due to its low ratio, even better than carbon, and excellent dimensional stability melting point of about 150°C (295°F) they are not suitable for elevated due to the high young’s modulus. Para-aramid has a decomposition temperature applications. The fiber is mainly used in protective temperature of ± 500 ºC. Technora® is a para-aramid fiber made clothing like ballistic vests, helmets, cut-resistant glove and tension from copolymers and is produced in the different process from PPTA members like ropes, slings and fishing lines. (poly-paraphenylene terephthalamide). EuroFibers is the premium distributor of DSM offering the extensive EuroFibers is the premium distributor of Teijin® offering their Dyneema® and Trevo® portfolio to our customer base. exceptional aramid fibers Twaron® and Technora® to a wide variety of customers. -
All About Fibers
RawRaw MaterialsMaterials ¾ More than half the mix is silica sand, the basic building block of any glass. ¾ Other ingredients are borates and trace amounts of specialty chemicals. Return © 2003, P. Joyce BatchBatch HouseHouse && FurnaceFurnace ¾ The materials are blended together in a bulk quantity, called the "batch." ¾ The blended mix is then fed into the furnace or "tank." ¾ The temperature is so high that the sand and other ingredients dissolve into molten glass. Return © 2003, P. Joyce BushingsBushings ¾The molten glass flows to numerous high heat-resistant platinum trays which have thousands of small, precisely drilled tubular openings, called "bushings." Return © 2003, P. Joyce FilamentsFilaments ¾This thin stream of molten glass is pulled and attenuated (drawn down) to a precise diameter, then quenched or cooled by air and water to fix this diameter and create a filament. Return © 2003, P. Joyce SizingSizing ¾The hair-like filaments are coated with an aqueous chemical mixture called a "sizing," which serves two main purposes: 1) protecting the filaments from each other during processing and handling, and 2) ensuring good adhesion of the glass fiber to the resin. Return © 2003, P. Joyce WindersWinders ¾ In most cases, the strand is wound onto high-speed winders which collect the continuous fiber glass into balls or "doffs.“ Single end roving ¾ Most of these packages are shipped directly to customers for such processes as pultrusion and filament winding. ¾ Doffs are heated in an oven to dry the chemical sizing. Return © 2003, P. Joyce IntermediateIntermediate PackagePackage ¾ In one type of winding operation, strands are collected into an "intermediate" package that is further processed in one of several ways. -
VECTRAN TECH.FNL[FINAL]-QXD 10/26/99 10:13 AM Page 2
ENGINEERING DATA VECTRAN TECH.FNL[FINAL]-QXD 10/26/99 10:13 AM Page 2 GGrasprasp ThThee WWorldorld OOff TTomorrowomorrow ENGINEERING DATA ENGINEERING DATA VECTRAN TECH.FNL[FINAL]-QXD 10/26/99 10:13 AM Page 3 TABLE OF CONTENTS Page 1: Introduction Page 2: Vectra Polymer Page 3: Tensile Properties Page 4: Thermal Properties Page 6: Chemical Resistance Page 10: Creep Page 11: Abrasion Resistance Page 14: Compression /Flex Fatigue Page 16: Pin Diameter Page 17: Vibration Damping /Impact Resistance Page 19: Cut Resistance Page 19: Twist Page 21: UV Resistance VECTRAN TECH.FNL[FINAL]-QXD 10/26/99 10:13 AM Page 4 ® L IQUID C RYSTAL P OLYMER F IBER Vectran is a high-performance liquid crystal polymer (LCP) fiber offering a balance of properties unmatched by other performance fibers. Some of these unique properties were discovered through 20 years of research and development of the polymer Vectra®. Celanese committed to developing a thermotropic (melt processable) LCP in the mid 1970’s and commercialized the Vectra family of resins in 1985. The molecules of the liquid crystal polymer are rigid and position themselves into randomly oriented domains.The polymer exhibits anisotropic behavior in the melt state, thus the term “liquid crystal polymer.” Upon extrusion of the molten polymer through small spinnerette holes, the molecular domains align parallel to each other along the fiber axis.The highly oriented fiber structure results in high tensile properties. A schematic diagram of the molecular chain structure is shown in Figure 1. Figure 1: Schematic Of Molecular Chain Structure Of Fiber Conventional Liquid Crystal The attributes of Vectra, such as excellent Polyester Polymer mechanical properties, property retention over a wide range of temperatures, excellent chemical resistance, and low moisture pick-up, carry Melt Spinning Melt And Spinning over to the fiber.The fiber also exhibits no Heat Drawing measurable creep when loaded up to 50% of the threadline breaking load. -
Mer Landing.Qxd
NATIONAL AERONAUTICS AND SPACE ADMINISTRATION Mars Exploration Rover Landings Press Kit January 2004 Media Contacts Donald Savage Policy/Program Management 202/358-1547 Headquarters [email protected] Washington, D.C. Guy Webster Mars Exploration Rover Mission 818/354-5011 Jet Propulsion Laboratory, [email protected] Pasadena, Calif. David Brand Science Payload 607/255-3651 Cornell University, [email protected] Ithaca, N.Y. Contents General Release …………………………………………………………..................................…… 3 Media Services Information ……………………………………….........................................…..... 5 Quick Facts ………………………………………………………................................……………… 6 Mars at a Glance ……………………………………………………….................................………. 7 Historical Mars Missions ………………………………………………….....................................… 8 Mars: The Water Trail ………………………………………………………………….................…… 9 Where We've Been and Where We're Going …………………………………................ 14 Science Investigations .............................................................................................................. 17 Landing Sites ............................................................................................................................. 23 Mission Overview ……………...………………………………………..............................………. 28 Spacecraft ................................................................................................................................. 38 Program/Project Management …………………………………………….................................… -
Melt-Spun Fibers for Textile Applications
materials Review Melt-Spun Fibers for Textile Applications Rudolf Hufenus 1,*, Yurong Yan 2, Martin Dauner 3 and Takeshi Kikutani 4 1 Laboratory for Advanced Fibers, Empa, Swiss Federal Laboratories for Materials Science and Technology, Lerchenfeldstrasse 5, CH-9014 St. Gallen, Switzerland 2 Key Lab Guangdong High Property & Functional Polymer Materials, Department of Polymer Materials and Engineering, South China University of Technology, No. 381 Wushan Road, Tianhe, Guangzhou 510640, China; [email protected] 3 German Institutes of Textile and Fiber Research, Körschtalstraße 26, D-73770 Denkendorf, Germany; [email protected] 4 Tokyo Institute of Technology, 4259-J3-142, Nagatsuta-cho, Midori-ku, Yokohama, Kanagawa 226-8503, Japan; [email protected] * Correspondence: [email protected]; Tel.: +41-58-765-7341 Received: 19 August 2020; Accepted: 23 September 2020; Published: 26 September 2020 Abstract: Textiles have a very long history, but they are far from becoming outdated. They gain new importance in technical applications, and man-made fibers are at the center of this ongoing innovation. The development of high-tech textiles relies on enhancements of fiber raw materials and processing techniques. Today, melt spinning of polymers is the most commonly used method for manufacturing commercial fibers, due to the simplicity of the production line, high spinning velocities, low production cost and environmental friendliness. Topics covered in this review are established and novel polymers, additives and processes used in melt spinning. In addition, fundamental questions regarding fiber morphologies, structure-property relationships, as well as flow and draw instabilities are addressed. Multicomponent melt-spinning, where several functionalities can be combined in one fiber, is also discussed. -
Quality and Innovation, Our Reason for Being
Quality and innovation, our reason for being CATALOGUE HIGH PERFORMANCE ROPES america’s cup line america’s cup line racer zylon Halyard/Sheet REF. 07000 Top rope, designed for high competition sailing, ideal for regattas as World Race, America’s Cup, Med Cup… Zylon PBO is specially developed to prevent surface melting. A new developed coating provides cover-core slipping, which withstand temperatures up to 650ºC. Applications · Runner tails · Running backstays REF. XS · Gennaker · Spinnaker sheets, afterguys Features REF. LS · Extremely high temperature resistance up to 650ºC · Regatta Coating System, which provides a long durability and prevents surface melting · UV protection · Stretch <1,5% · Excellent grip between core and cover · Design XS, LS Core: Dyneema SK-90 Composition ® REGATTA HSS Core: dyed 100% Dyneema SK-90 coating, heat stretch system Heat Stretch System Cover: 100% Zylon® REGATTA CS Construction: Core: 12-plaited 1:1 Coating System Cover: 32-plaited 1:1 Technical Information Ø mm Breaking strength (kg) Stretch Weight g/m Length 8 4500 < 1,5% 51 100m 10 6500 < 1,5% 66 100m 12 10000 < 1,5% 96 100m 14 13000 < 1,5% 140 100m 16 14500 < 1,5% 180 100m 18 17900 < 1,5% 230 100m 20 20800 < 1,5% 270 100m 22 24600 < 1,5% 320 100m Slipping Cover Core Graph showing improved performance of grip between cover and core using Regatta coating system over Standard PU 4 america’s cup line platinium-90 NEW Halyard/Sheet REF. 09099 New rope line developed for high competition with Technora® and high tenacity polyester. High twisted, that offers high abrasion resistance and an excellent grip when passing by clam cleats and winches. -
1.2 Textile Fibres
1 Fundamental Aspects of Textile Fibres 1.1 Textiles The modern definition of the word textile, namely (n.) a type of cloth or woven fabric [1], reflects the early seventeenth century origins of the word as relating to a woven fabric and the process of weaving. Nowadays, the word has more extensive meanings and associations, such as textile-filament,-fibre,-yarn and -fabric, and relates to the preparation of knitted, tufted and non-woven fabrics, as well as woven fabrics. In a similar vein, the modern definition of the word fibre,asa thread or filament from which a vegetable tissue, mineral substance, or textile is formed [1], also is the result of considerable linguistic evolution since its origins in the early fifteenth century [2] to describe lobes of the liver and entrails [1]. Essentially, textile materials can be considered as principally cohesive, fibrous assemblies in which individual fibres are assembled via friction. A wide range of textiles is commercially available, the different types of such products varying, markedly, in terms of both the geometric arrangement of the fibrous materials (e.g. woven fabric, yarn and non-woven) and the derivation, structure, physical characteristics and chemical properties of the component textile fibres. Since, in its broadest sense, the theory of the dyeing of textiles concerns the nature of the interactions that operate between such fibrous assemblies and dyes, these interactions can be considered in terms of three aspects: (1) the gross structural arrangement of the fibrous assembly (e.g. yarn, woven fabric and garment); (2) the constituents of the fibrous assembly (i.e. -
Vectran Fiber Time-Dependent Behavior and Additional Static Loading Properties
NASA/TM—2004-212773 Vectran Fiber Time-Dependent Behavior and Additional Static Loading Properties R.B. Fette M.F. Sovinski National Aeronautics and Space Administration Goddard Space Flight Center Greenbelt, Maryland 20771 December 2004 The NASA STI Program Offi ce … in Profi le Since its founding, NASA has been ded i cated to the • CONFERENCE PUBLICATION. Collected ad vancement of aeronautics and space science. The pa pers from scientifi c and technical conferences, NASA Sci en tifi c and Technical Information (STI) symposia, sem i nars, or other meetings spon sored Pro gram Offi ce plays a key part in helping NASA or co spon sored by NASA. maintain this impor tant role. • SPECIAL PUBLICATION. Scientifi c, tech ni cal, The NASA STI Program Offi ce is operated by or historical information from NASA pro grams, Langley Research Center, the lead center for projects, and mission, often concerned with sub- NASAʼs scientifi c and technical in for ma tion. The jects having substan tial public interest. NASA STI Program Offi ce pro vides ac cess to the NASA STI Database, the largest collec tion of • TECHNICAL TRANSLATION. En glish-language aero nau ti cal and space science STI in the world. trans la tions of foreign scien tifi c and tech ni cal ma- The Pro gram Offi ce is also NASAʼs in sti tu tion al terial pertinent to NASAʼs mis sion. mecha nism for dis sem i nat ing the results of its research and devel op ment activ i ties. These results Specialized services that complement the STI Pro- are published by NASA in the NASA STI Report gram Offi ceʼs diverse offerings include cre at ing Series, which includes the following report types: custom thesau ri, building customized data bas es, organizing and publish ing research results . -
Fabric Development Inc. Brochure
INC. INC. OVERVIEW Providing specialty fabric applications since 1972 Fabric Development, Inc. (FDI) was established in 1972 to manufacture specialty woven fabrics to meet specialty end use requirements. In time, FDI has greatly expanded its capabilities to work with all high performance fibers, including Carbon (standard to ultra-high modulus), Aramid (Kevlar&Twaron), Spectra, Ceramics, Quartz, Teflon, Nomex and Vectran. FDI has manufactured these fibers in a variety of fabric geometries, hybrid structures, polar weaves and multilayer fabric structures. This capability allows FDI to serve the expanding needs of specialty fabric applications. FDI works with material property requirements, drawings and cost considerations to recommend yarns, fabric construction and weave design best suited to your application. Not only can FDI manufacture a fabric for a specialized application, it can then transition those unique structures into a high volume production run. Today, Fabric Development Inc., operating as a Kordsa company, offers a robust manufacturing capability to meet the demand for specialty fabric applications throughout the world. PRODUCTS Manufacturing over 2000 different style fabrics in a wide range of widths and thicknesses STANDARD PRODUCTS 645 PLAIN 34X34 195 DENIER 195 DENIER 58 gsm KEVLAR 49 378 PLAIN 17X17 1140 DENIER 1140 DENIER 170 gsm FABRICS 646 4HS 17X17 1140 DENIER 1140 DENIER 170 gsm 613 PLAIN 13X13 1420 DENIER 1420 DENIER 162 gsm KEVLAR 29 O95 PLAIN 31X31 1000 DENIER 1000 DENIER 280 gsm FABRICS 411 LENO 20x6 1500 DENIER 1500 DENIER 217 gsm 824 PLAIN 24x24 1K 1K 125 gsm C105 PLAIN 12.5x12.5 3K 3K 193 gsm 1116 2X2 TWILL 13X13 3K 3K 198 gsm CARBON FABRICS 1001 2X2 TWILL 12X12 6K 6K 370 gsm 1300 5HS 12x12 6K 6K 370 gsm 1266 2x2 TWILL 10.5x10.5 12K 12K 650 gsm 1843/1 PLAIN 8X8 12K 3K 310 gsm TAPES----C105 is in stock in widths ranging from 1” to 6”.