Cylinder Linings
Total Page:16
File Type:pdf, Size:1020Kb
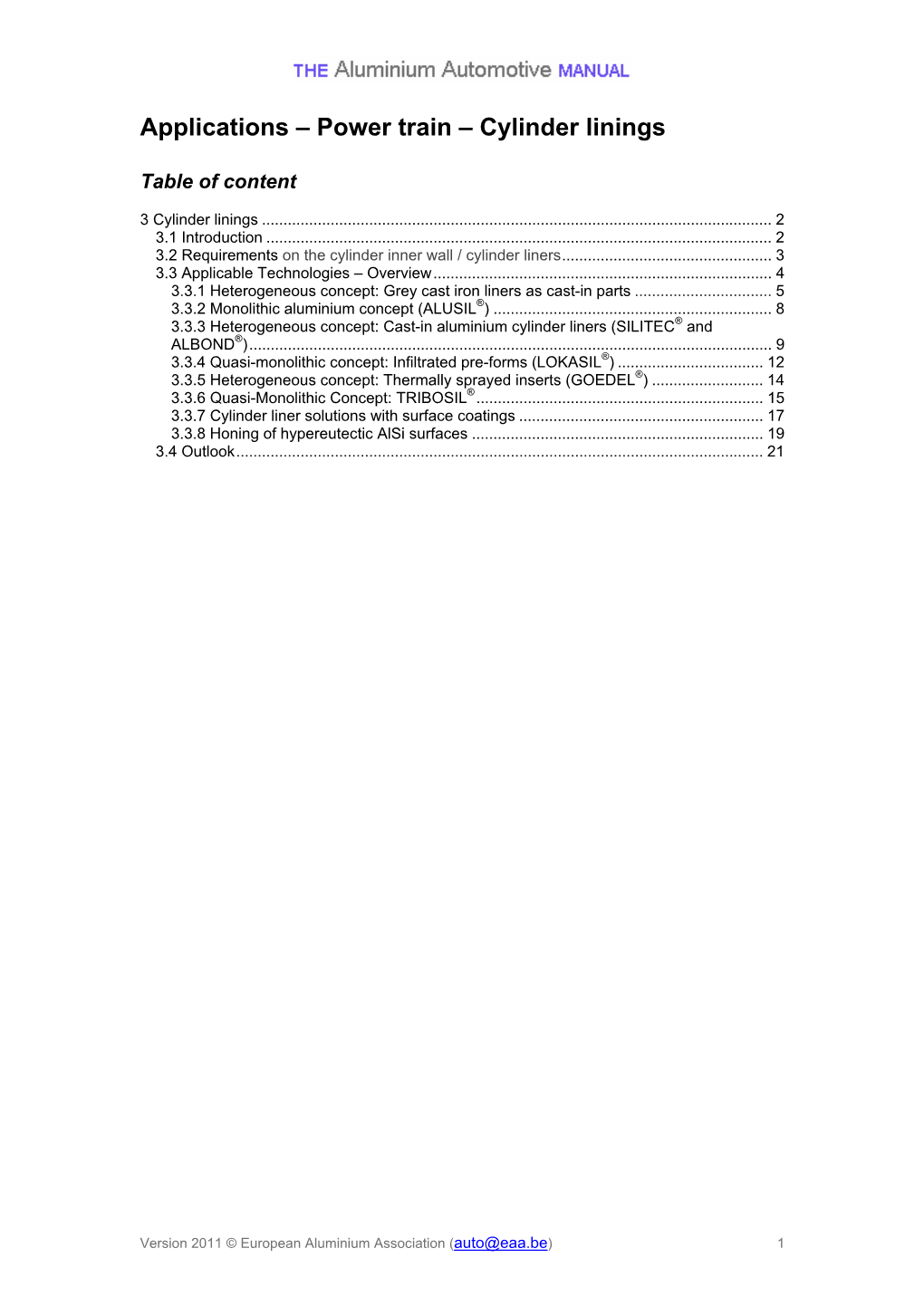
Load more
Recommended publications
-
Reconditioning of Aluminium Engines Reconditioning of Aluminium Engine Blocks Impressum
Service Tips & Information Reconditioning of Aluminium Engines Reconditioning of Aluminium Engine Blocks Impressum MSI Motor Service International. Und was dahinter steckt. Die MSI Motor Service International GmbH ist die Vertriebsorganisation für die weltweiten Aftermarket-Aktivitäten der KOLBENSCHMIDT PIERBURG AG. Unter den Premium-Marken KOLBEN- SCHMIDT, PIERBURG und TRW liefern wir ein umfassendes, bedarfsgerech- tes Sortiment von Produkten im und am Motor. Den Werkstätten und Moto- reninstandsetzern stehen Motorkom- ponenten für über 2000 verschiedene Motoren zur Verfügung. Alle Produkte erfüllen den hohen Anspruch an Qualität, Wirtschaftlich- keit und Umweltschutz. Die KOLBENSCHMIDT PIERBURG AG als weltweit bedeutender Automobilzuliefe- rer entwickelt innovative Lösungen für Komponenten, Module und Systeme rund um den Motor für fast alle Hersteller. An 23 Fertigungsstandorten in Europa, Nord-und Südamerika sowie in China werden 11400 Mitarbeiter beschäftigt. Date 08.06 1. Edition Artikel-Nr. 50 003 804-02 ISBN 978-3-86522-197-1 Published by: © MSI Motor Service International GmbH Untere Neckarstraße 74172 Neckarsulm, Germany Editors: Alexander Schäfer Uwe Schilling Simon Schnaibel Technical Contributors: Reiner Holwein Johann Szopa Bernd Waldhauer Ullrich Zucker Dr. Eduard Köhler Willi Pröschle Graphical design: Uwe Schilling Simon Schnaibel Production: Margot Schneider Hela Werbung GmbH, Heilbronn Wir bedanken uns für die freundliche Unterstützung der KS Aluminium Technologie AG. This document must not be reprinted, duplicated or translated in full or in part without our prior written con- sent and without reference to the source of the material. All content including pictures and diagrams is subject to alteration. We accept no liability. 2 | Reconditioning of Aluminium Engine Blocks MSI Motor Service International Reconditioning of Aluminium Engine Blocks FOREWORD Aluminium engine blocks – the trend Since they were fi rst introduced, engines with aluminium engine blocks have continued to enjoy increasing popularity. -
Alusil, Lokasil, Silitec, Diasil, Mercosil, ALBOND—These Sound
Alusil, Lokasil, Silitec, DiASil, Mercosil, ALBOND—these sound like a foreign language, but they are all trade names or trademarks for what is generically known as hypereutectic aluminum, which is a new/old material for cylinder bore wear surfaces. Hypereutectic aluminum is both new and old. Its cousins, hypoeutectic and eutectic aluminum, have been used for pistons and connecting rods for a number of years. One of the earliest applications of hypereutectic aluminum was as the wear surface in an unlined cylinder in some Porsche engines in the 1960s. The 1971 Chevrolet Vega was the first true production automotive engine with a linerless hypereutectic aluminum cylinder bore as the wear surface. Despite the car’s reputation, the cylinder concept was ahead of its time. When properly finished, hypereutectic aluminum cylinder bores present a surface to the piston rings that is roughly equivalent to glass. The resulting engine has lower friction, excellent sealing, improved dimensional stability, improved heat dissipation, reduced weight, better recyclability, lower manufacturing cost and higher durability compared to the traditional aluminum block with cast iron cylinder liners. Aluminum Cylinder Evolution Since the first time gasoline burned and forced a piston down a cylinder, aluminum has been the metal of choice when light weight was the most critical requirement for an internal combustion engine. This is as true today as it was in 1902 when the Wright Brothers were unable to purchase a suitable commercial engine for their experimental airplane and instead built their own, casting the aluminum block. Automotive OEMs seized upon aluminum for the same reason and found manufacturing advantages, too, in that it is less costly to cast and easier to machine. -
Metallurgical Abstracts (General and Non-Ferrous)
METALLURGICAL ABSTRACTS (GENERAL AND NON-FERROUS) Volume 1 JUNE 1934 Part 6 I.—PROPERTIES OF METALS (Continued from pp. 225-230.) ♦Change in Properties of Deformed Polycrystalline [Aluminium] During Recovery [Erholung]. M. O. Kornfeld (Zhumal eksperimentalnoy i teoreti- cheskoy Fiziki (Journal of Experimental and Theoretical Physics), 1933, 3, (6), 563-566).—[In Russian.] Annealing of deformed polycrystalline aluminium in the region of “ pure recovery ” does not restore the original properties. The processes which take place during recovery lead to a highly stable con dition characterized by a yield-point higher than that of the original material due to the residual distortion of the lattice after recovery. Laue photo grams indicate that during recovery there is no noticeable shift in the boundaries between grains. It may therefore be concluded that any change in properties during recovery is determined mainly by processes taking place within the grain.—N. A. ♦On the Question of the Allotropic Transition of Bismuth at 75° C. Shin Tchi Aoyama and Gohei Monna (Sci. Rep. Tdhoku Imp. Univ., 1934, [i], 23, 52-61 [in English] ; and Kinzoku no Kenkyu, 1934, 11, 203-209 [in Japanese]). —Investigations by means of thermal analysis, thermal expansion, thermo- electromotive force, and oil dilatometry, indicate that the alleged allotropic transition of bismuth at 75° C. does not exist.—E. S. H. Preparation and Properties of Cadmium. Edmund T. Richards (Metall- borse, 1934, 24, 242-243).-—A review.—A. R. P. ♦The Electrolytic Valve Action of Columbium and Tantalum on A.C. Circuits. D. F. Calhane and A. J. Laliberte (Electrochem. Soc. Preprint, 1934, (April), 287-293).—Oscillograph records are given showing the film behaviour of tantalum and columbium in dilute sulphuric acid on a.c. -
Research of Combined Rolling-Extrusion Process for Production of Long Deformed Semi-Finished Products from Aluminium Alloys of Various Alloying Systems
RESEARCH OF COMBINED ROLLING-EXTRUSION PROCESS FOR PRODUCTION OF LONG DEFORMED SEMI-FINISHED PRODUCTS FROM ALUMINIUM ALLOYS OF VARIOUS ALLOYING SYSTEMS TABLE OF CONTENTS 1. CURRENT STATUS AND DEVELOPMENT TRENDS OF TECHNOLOGIES AND EQUIPMENT FOR COMBINED PROCESSING OF ALUMINIUM ALLOYS 1.1. METHODS AND TECHNOLOGIES FOR CONTINUOUS PROCESSING OF ALUMINIUM ALLOYS 1.2 ANALYSIS OF RESEARCH RESULTS FOR IDENTIFICATION OF DEFORMATION AND POWER PARAMETERS IN COMBINATION OF ROLLING AND EXTRUSION 1.3 SELECTION OF MATERIALS FOR RESEARCH 1.4. CONCLUSIONS AND SETTING OF OBJECTIVES 2. SIMULATION AND ANALYTICAL STUDIES OF COMBINED ROLLING- EXTRUSION OF ALLUMINIUM ALLOYS 2.1. SIMULATION OF COMBINED ROLLING-EXTRUSION PROCESS 2.2. RESEARCH OF GEOMETRICAL SHAPE OF DEFORMATION ZONE AND FEASIBILITY OF ROLLING-EXTRUSION PROCESS 2.3. CHARACTERIZATION OF RHEOLOGICAL PROPERTIES OF EXPERIMENTAL ALUMINIUM ALLOYS 2.4. CALCULATION OF POWER PARAMETERS OF ROLLING-EXTRUSION 3. EXPERIMENTAL RESEARCH OF COMBINED ROLLING-EXTRUSION PROCESS 3.1 DESCRIPTION OF EQUIPMENT AND METHODS OF EXPERIMENTAL RESEARCH 3.2. RESULTS OF EXPERIMENTAL RESEARCH AND THEIR ANALYSIS 3.3. RESEARCH OF STRUCTURE AND PROPERTIES OF PRODUCTS MADE BY CRE (COMBINED ROLLING-EXTRUSION) METHOD OF EXPERIMENTAL ALLOYS 3.4. PRACTICAL APPLICATION OF RESEARCH RESULTS CONCLUSION REFERENCE LIST 2 INTRODUCTION High production volumes of long-length deformed semi-finished products of relatively small cross-section made of aluminum and its alloys (wire rods, bars and wire) have conditioned the creation of new technologies of combined processing with the use of continuous methods of casting and basic metal-forming operations which for production of the above-mentioned products are advisable to be applied as rolling and extrusion [1-4]. -
Engine Blocks
Applications – Power train – Engine blocks Table of Contents 2 Engine blocks ......................................................................................................................... 2 2.1 Introduction ...................................................................................................................... 2 2.2 Requirements for aluminium engine blocks..................................................................... 4 2.3 Design features................................................................................................................ 6 2.3.1 Basic engine concept ................................................................................................ 6 2.3.2 Bolting concept.......................................................................................................... 8 2.3.3 Open and closed deck concepts ............................................................................... 9 2.4 Pre-cast features and add-on parts ................................................................................. 9 2.5 Cast-in inserts ................................................................................................................ 11 2.6 Criteria for alloy selection............................................................................................... 13 2.7 Alloys: Composition and heat treatment ........................................................................ 14 2.8 Applicable casting processes........................................................................................ -
Determining Features of Application of Functional
Materials Science UDC 621.793:621.357.7 Проаналізовано підходи щодо застосуван- DOI: 10.15587/1729-4061.2019.171787 ня електрохімічних покривів в технологіях поверхневої обробки. Показано, що спрямова- не модифікування поверхні дозволяє розшири- DETERMINING FEATURES ти функціональні властивості оброблюваного матеріалу, зокрема підвищити показники міц- OF APPLICATION ності, зносостійкості, корозійної тривкості, каталітичної активності. OF FUNCTIONAL Запропоновано спосіб поверхневої обробки нелегованих сталей та чавунів шляхом фор- ELECTROCHEMICAL мування тонкоплівкових покривів тернарни- ми сплавами заліза та кобальту з молібденом COATINGS IN і вольфрамом. Показано, що введення туго- плавких металів до 37 ат. % в поверхневий шар призводить до зміни фазової структури TECHNOLOGIES OF покриття. Виявлено, що це забезпечує підви- щення зносостійкості на 40 %, мікротвердості SURFACE TREATMENT у 2,5–3,5 рази, а також зменшення коефіцієн- ту тертя в 3–4 рази порівняно з матеріалом A. Karakurkchi підкладки. Сформовані матеріали можуть PhD, Senior Researcher бути використані для зміцнення і захисту Department of General and Inorganic Chemistry* поверхонь в різних галузях промисловості. E-mail: [email protected] Для модифікування поверхні поршневих M. Sakhnenko силумінів запропоновано використовувати ме- Doctor of Technical Sciences, тод плазмово-електролітичного оксидуван- Professor, Head of Department ня із формуванням керамікоподібних покривів. Department of Physical Chemistry* Показано, що в гальваностатичному режимі M. Ved із лужних розчинів електролітів, що містять Doctor of Technical Sciences, Professor солі мангану та кобальту, можливо одержу- Department of General and Inorganic Chemistry* вати рівномірні щільні з високою адгезією до основного металу оксидні покриви, допова- I. Yermolenko ні каталітичними компонентами, вміст яких Doctor of Technical Sciences, Senior Researcher варіюється в межах 25–35 ат. %. Показано, що Research Laboratory* морфологія та фазова структура поверхневих S. -
Reconditioning of Aluminium Engines Contents
Reconditioning of Aluminium Engines Contents Page Chapter 1: General 3 1.1 Reasons for using aluminium cylinder blocks 3 1.2 Known brands of aluminium alloys for cylinder blocks 3 1.3 Vehicles/engines with aluminium cylinder blocks 3 1.4 Design details 3 1.5 Composite materials for cylinder liners. Aluminium/ cast iron 4 1.6 Use of Cr-coated piston rings 4 1.7 KS cylinder liners for Alusil engines 4 Chapter 2: Reconditioning an Alusil®cylinder block 5 2.1 Preparatory machining of the cylinder block 5 2.2 Installation of the Alusil 6 cylinder liner 2.2.1 Installation with dry ice 6 2.2.2 Installation with liquid nitrogen 6 2.2.3 Preheating of the cylinder block 6 2.2.4 Fitting the cylinder liner 7 2.3 Planing of the cylinder block 7 2.4 Prehoning, finish honing, polishing 8 2.5 Silicon lapping 8 2.6 Tables 9 Chapter 3: Reconditioning a Lokasil cylinder block based on the example of the Porsche Boxster engine 14 Chapter 4: Reconditioning the threads for the cylinder head bolts 16 Chapter 1: General 1.1 Reasons for using alumin- 1.3 Vehicles/engines with alu- 1.4 Design details ium engine blocks minium cylinder blocks Alusil: It has always been a challenge • Alusil base material is expensi- for engine designers to make, GALNIKAL / NIKASIL ve and difficult to machine due besides cylinder heads and pis- to the high silicon content tons, the entire cylinder block BMW • Boring the cylinder block is from aluminium without addition- 2.0 Litre 6 cylinders possible al cylinder liners or surface rein- 2.5 Litre 6 cylinders M52 • Oversized pistons are availa- forcements. -
Employment Equity Act (55/1998): Public Register Notice 40996
STAATSKOERANT, 21 JULIE 2017 No. 40996 111 Labour, Department of/ Arbeid, Departement van DEPARTMENT OF LABOUR NO. 715 21 JULY 2017 715 Employment Equity Act (55/1998): Public register notice 40996 REGISTER REGISTER NOTICE PUBLIC PUBLIC 1998) 1998) NO. NO. OF EMPLOYMENT EMPLOYMENT EQUITY ACT, ACT, 1998 (ACT 55 55 Schedule Schedule the the attached in in of of Oliphant, Oliphant, Minister Labour, Labour, publish Nelisiwe Nelisiwe Mildred Mildred 1, 1, Equity Equity Employment Employment of of of of Section the the 41 41 terms terms register register maintained in in hereto, hereto, the the that that submitted submitted have have of of of of designated employers 1998) 1998) (Act (Act Act, Act, 1998 55 55 No. No. Equity Equity Act, Act, of of Employment Employment Section Section the 21, 21, of of employment employment equity terms terms reports reports in in amended. amended. Act Act of of 1998 1998 55 55 No. No. as as OLIPHANT OLIPHANT MN MN MINISTER MINISTER LABOUR LABOUR OF OF o o 7 7,10/7 7,10/7 SASEREJISTRI SASEREJISTRI SOLUNTU ISAZISO ISAZISO (UMTHETHO (UMTHETHO YINOMBOLO KULUNGELELANISA KULUNGELELANISA INGQESHO, INGQESHO, 8) 8) ndipapasha ndipapasha uMphathiswa uMphathiswa wezabasebenzi, kule Iisiwe Iisiwe Oliphant, yeCandelo yeCandelo ngokwemiqathango ngokwemiqathango 41 41 apha apha irejista egcina shelwe shelwe oyiNombolo oyiNombolo ka-1998 ka-1998 (urnThetho yama- yama- ungelelanisa ungelelanisa iNgqesho, zokuLungelelanisa zokuLungelelanisa iingxelo iingxelo 'khundla 'khundla zabaqeshi abangenise abangenise wokuLungelelanisa wokuLungelelanisa yeCandelo yeCandelo IomThetho IomThetho 21, 21, emigaqo emigaqo tho tho oyiNombolo yama-55 ka-1998. ka-1998. ti r m z N CM Z =o 7) D * m N m M r/) m CO , o o V J `wZ Ó This gazette is also available free online at www.gpwonline.co.za 112 No. -
Government Gazette Staatskoerant REPUBLIC of SOUTH AFRICA REPUBLIEK VAN SUID AFRIKA
Government Gazette Staatskoerant REPUBLIC OF SOUTH AFRICA REPUBLIEK VAN SUID AFRIKA Regulation Gazette No. 10177 Regulasiekoerant March Vol. 633 29 2018 No. 41534 Maart PART 1 OF 6 ISSN 1682-5843 N.B. The Government Printing Works will 41534 not be held responsible for the quality of “Hard Copies” or “Electronic Files” submitted for publication purposes 9 771682 584003 AIDS HELPLINE: 0800-0123-22 Prevention is the cure STAATSKOERANT, 29 MAART 2018 No. 41534 65 List of designated employers who reported for the 01 September 2017 reporting cycle Description of terms: No: This represents sequential numbering of designated employers and bears no relation to an employer. (The list consists of 6069 large employers and 21094 small employers). Business name: This is the name of the designated employer who reported Status code: 0 means no query. EE Reference Number: This is the reference number of all employers who reported successfully. No Business Name Status Code EE Ref No: 1 0307 FILMS (PTY) LTD 0 821489 2 08600PLUMBER 0 817804 3 08XCONNECT COM 0 822716 4 1 UP DESIGN (PTY) LTD 0 813173 5 1 WAY 0 790271 6 1000 HILLS SPAR 0 786733 7 10X INVESTMENTS (PTY) LTD 0 817048 8 123 CONSULTING (PTY)LTD 0 823025 9 15 ON ORANGE HOTEL 0 813019 10 180 DEGREE DIGITAL PRINT CC 0 815011 11 180 DEGREES DONE TO PERFECTION 0 824828 12 1KZNTV 0 820196 13 1ST CONTACT MONEY 0 819272 14 1ST CONTACT SERVICES CC 0 141174 15 2 CANA SOLUTIONS PTY LTD 0 523173 16 2 RIVER BOERDERY 0 820222 17 2016223694 SOUTH AFRICA (PTY) LTD 0 824533 18 21ST CENTURY PAY SOLUTIONS COMPANY -
A Study on Material Properties of Intermetallic Phases in a Multicomponent Hypereutectic Al-Si Alloy with the Use of Nanoindentation Testing
materials Article A Study on Material Properties of Intermetallic Phases in a Multicomponent Hypereutectic Al-Si Alloy with the Use of Nanoindentation Testing Mirosław Tupaj 1,* , Antoni Władysław Orłowicz 2, Marek Mróz 2 , Andrzej Trytek 1 , Anna Janina Dolata 3,* and Andrzej Dziedzic 4 1 Faculty of Mechanics and Technology, Rzeszow University of Technology, ul. Kwiatkowskiego, 37-450 Stalowa Wola, Poland; [email protected] 2 Faculty of Mechanical Engineering and Aeronautics, Rzeszow University of Technology, al. Powsta´nców 8, 35-959 Rzeszów, Poland; [email protected] (A.W.O.); [email protected] (M.M.) 3 Faculty of Materials Engineering, Silesian University of Technology, ul. Krasi´nskiego 8, 40-019 Katowice, Poland 4 Institute of Physics, University of Rzeszow, Pigonia 1, 35-310 Rzeszow, Poland; [email protected] * Correspondence: [email protected] (M.T.); [email protected] (A.J.D.) Received: 15 November 2020; Accepted: 7 December 2020; Published: 9 December 2020 Abstract: The paper concerns modeling the microstructure of a hypereutectic aluminum-silicon alloy developed by the authors with the purpose of application for automobile cylinder liners showing high resistance to abrasive wear at least equal to that of cast-iron liners. With the use of the nanoindentation method, material properties of intermetallic phases and matrix in a hypereutectic Al-Si alloy containing Mn, Cu, Cr, Ni, V, Fe, and Mg as additives were examined. The scanning electron microscope equipped with an adapter for chemical composition microanalysis was used to determine the chemical composition of intermetallics and of the alloy matrix. Intermetallic phases, such as Al(Fe,Mn,M)Si, Al(Cr,V,M)Si, AlFeSi, AlFeNiM, AlCuNi, Al2Cu, and Mg2Si, including those supersaturated with various alloying elements (M), were identified based on results of X-ray diffraction (XRD) tests and microanalysis of chemical composition carried out with the use of X-ray energy dispersive spectroscopy (EDS). -
Understanding Bore Scoring in Al-Si Cylinder Systems
UNDERSTANDING BORE SCORING IN AL-SI CYLINDER SYSTEMS Charles Navarro LN Engineering LLC Copyright ©2019 LN Engineering LLC. Abstract The basic requirements for a cylinder lining are as follows: wear resistance for the liner, rings, and pistons, as well as resistance to galling and minimal oil consumption. In the beginning, internal combustion engines favored heavy, dense, thermally stable cast iron engine blocks for their durability in meeting these criteria. Besides being heavier than a modern all-aluminum engine, those made from cast iron provide poor cooling, limited performance, and are nowhere near as efficient or powerful as today’s engines designed to meet tightening emissions and fuel economy requirements.1 As aluminum has four times the thermal conductivity of cast iron or steel, it’s the logical choice to overcome these thermal performance limitations.2 However, Al-Si cylinder systems require special surface preparation and piston coatings, not to mention specific lubrication needs. Balancing these requirements has always been a challenge for engineers, especially when cost is the driving motivator for OEMs when utilizing liner-less cylinder technologies. Innovations built upon an all-aluminum engine designed to maximize efficiency and reduce emissions, coupled with hybrid technologies, will extend the life of the internal combustion engine as we transition to an all-electric future. Keywords: Al-Si Alloys, Hypereutectic Aluminum Alloys, Internal Combustion Engine, Combustion Engine Cylinder Liners, MMC, Lokasil, Alusil, Bore Scoring, All-Aluminum Engine Block, Coatings, Piston, Piston Rings, Heat Transfer, Tribofilm, Boundary Lubrication, Wear Mechanisms, ZDDP, Friction Modifiers 1 Improving Heat Transfer and Reducing Mass In a Gasoline Piston Using Additive Manufacturing. -
Nikasil® and Alusil a Primer on Some of the More Common Specialty Coatings and Cylinder Materials Found in Small Displacement Engines
EP 10-2008 18-32 10/6/08 7:46 PM Page 18 FEATURE Nikasil® and Alusil A primer on some of the more common specialty coatings and cylinder materials found in small displacement engines BY JOHN GOODMAN This issue of Engine Professional is Background What Nikasil® and other similar dedicated to specialty engines and niche Any shop considering a cylinder repair coatings are not remains the center of marketing opportunities. Part of that that has been coated with Nikasil® confusion. Alusil’s like Lokasil®, market involves small displacement should be aware of a few material Mercasil® and other high silica substrates engines of all types and configurations. properties and some of the confusion are not coatings at all but rather Past experience with these small bore surrounding them. It will not be the aluminum metal alloys. These alloys have engines has demonstrated a need to purpose of this article to cover many also been referred to as hypereutectic understand materials and coating in a manufacturing details but developing aluminum due to the percent of silica particles contained in the alloy. It is a way quite different from the run-of-the- application and machining do’s and don’ts subtle distinction but Alusil alloys do not mill gasoline engine. Motorcycle, water will be fundamental. contain silica carbide like nickel plating sport, snow mobile, off-road, stationary Let’s begin by covering what Nikasil® does. Instead of silica carbide, Alusil power plant and other specialty engines is. Nikasil® or NiCom® (1967 Mahle employs glass-like silica particles similar offer a machine shop many high profit trademark) is electrodeposited oleophilic to sand.