THE GENESIS of an EXPERIMENT Or the Framework of Experimental Development
Total Page:16
File Type:pdf, Size:1020Kb
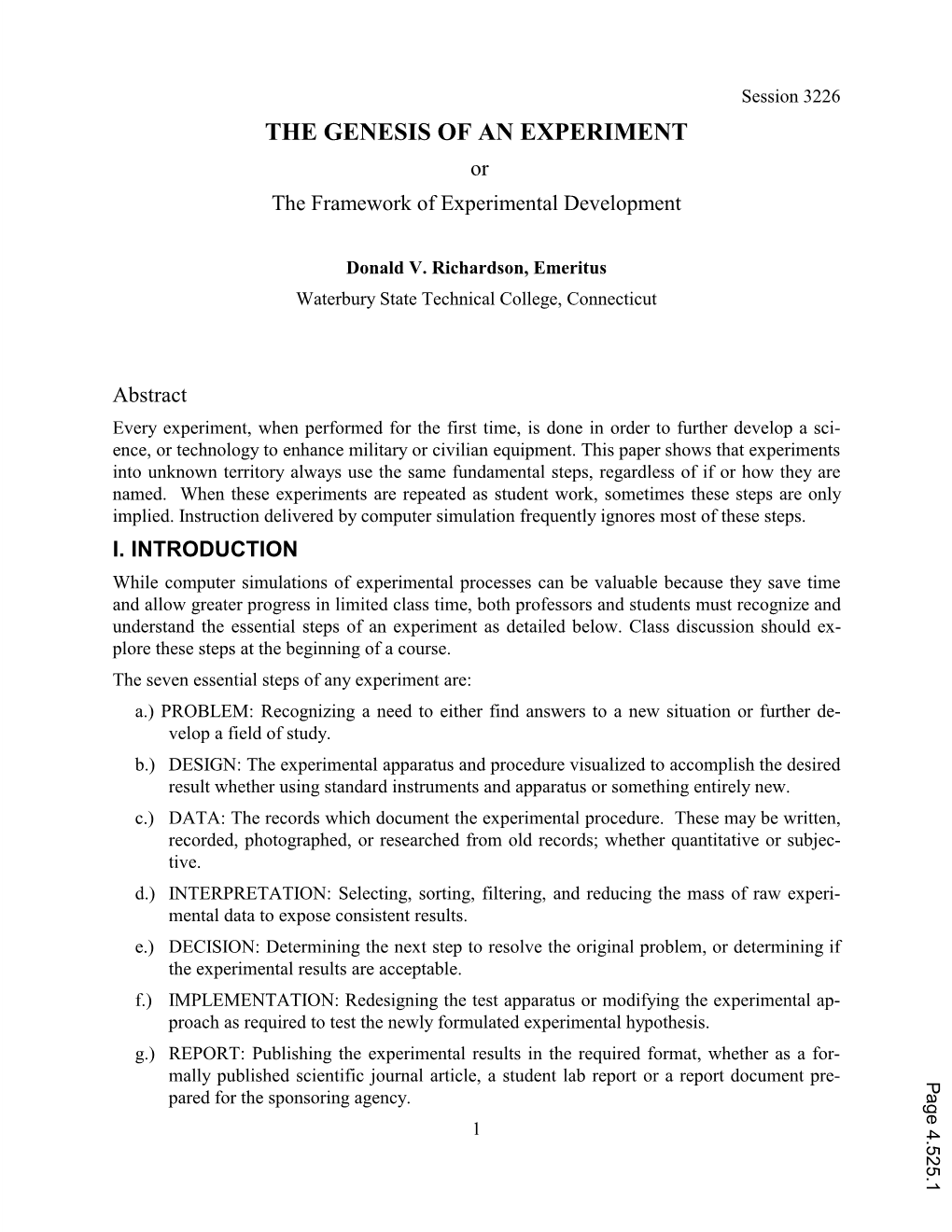
Load more
Recommended publications
-
Vought - Wikipedia
10/27/2020 Vought - Wikipedia Vought Vought was the name of several related American aerospace firms. These have included, in the past, Lewis and Vought Corporation, Chance Vought, Vought Vought-Sikorsky, LTV Aerospace (part of Ling-Temco-Vought), Vought Aircraft Companies, and Vought Aircraft Industries. The first incarnation of Vought was established by Chance M. Vought and Birdseye Lewis in 1917. In 1928, it was acquired by United Aircraft and Transport Corporation, which a few years later became United Aircraft Corporation; this was the first of many reorganizations and buyouts. During the 1920s and 1930s, Vought Aircraft and Chance Vought specialized in carrier-based aircraft for the United States Navy, by far its biggest customer. Chance Vought produced thousands of planes during World War II, including the F4U Corsair. Vought became independent again in 1954, and was purchased by Ling- Temco-Vought (LTV) in 1961. The company designed and produced a variety of The VE-7 was the first aircraft to planes and missiles throughout the Cold War. Vought was sold from LTV and owned launch from a U.S. Navy aircraft in various degrees by the Carlyle Group and Northrop Grumman in the early 1990s. It carrier was then fully bought by Carlyle, renamed Vought Aircraft Industries, with Industry Aerospace headquarters in Dallas, Texas. In June 2010, the Carlyle Group sold Vought to the Triumph Group. Founded 1917 Founders Birdseye Lewis Chance M. Vought Contents Key Rex Beisel people History Boone Guyton Chance Vought years 1917–1928 Charles H. Zimmerman 1930s–1960 Parent United Aircraft and LTV acquisition 1960–1990 Transport Corporation 1990s to today (1928-1954) Products Ling-Temco-Vought Aircraft (1962-1992) Unmanned aerial vehicles Missiles Rockets Workshare projects References External links History Chance Vought years 1917–1928 The Lewis and Vought Corporation was founded in 1917 and was soon succeeded by the Chance Vought Corporation in 1922 when Birdseye Lewis retired. -
Desind Finding
NATIONAL AIR AND SPACE ARCHIVES Herbert Stephen Desind Collection Accession No. 1997-0014 NASM 9A00657 National Air and Space Museum Smithsonian Institution Washington, DC Brian D. Nicklas © Smithsonian Institution, 2003 NASM Archives Desind Collection 1997-0014 Herbert Stephen Desind Collection 109 Cubic Feet, 305 Boxes Biographical Note Herbert Stephen Desind was a Washington, DC area native born on January 15, 1945, raised in Silver Spring, Maryland and educated at the University of Maryland. He obtained his BA degree in Communications at Maryland in 1967, and began working in the local public schools as a science teacher. At the time of his death, in October 1992, he was a high school teacher and a freelance writer/lecturer on spaceflight. Desind also was an avid model rocketeer, specializing in using the Estes Cineroc, a model rocket with an 8mm movie camera mounted in the nose. To many members of the National Association of Rocketry (NAR), he was known as “Mr. Cineroc.” His extensive requests worldwide for information and photographs of rocketry programs even led to a visit from FBI agents who asked him about the nature of his activities. Mr. Desind used the collection to support his writings in NAR publications, and his building scale model rockets for NAR competitions. Desind also used the material in the classroom, and in promoting model rocket clubs to foster an interest in spaceflight among his students. Desind entered the NASA Teacher in Space program in 1985, but it is not clear how far along his submission rose in the selection process. He was not a semi-finalist, although he had a strong application. -
Celebrating the Centennial of Naval Aviation in 1/72 Scale
Celebrating the Centennial of Naval Aviation in 1/72 Scale 2010 USN/USMC/USCG 1/72 Aircraft Kit Survey J. Michael McMurtrey IPMS-USA 1746 Carrollton, TX [email protected] As 2011 marks the centennial of U.S. naval aviation, aircraft modelers might be interested in this list of US naval aircraft — including those of the Marines and Coast Guard, as well as captured enemy aircraft tested by the US Navy — which are available as 1/72 scale kits. Why 1/72? There are far more kits of naval aircraft available in this scale than any other. Plus, it’s my favorite, in spite of advancing age and weakening eyes. This is an updated version of an article I prepared for the 75th Anniversary of US naval aviation and which was published in a 1986 issue of the old IPMS-USA Update. It’s amazing to compare the two and realize what developments have occurred, both in naval aeronautical technology and the scale modeling hobby, but especially the latter. My 1986 list included 168 specific aircraft types available in kit form from thirty- three manufacturers — some injected, some vacuum-formed — and only three conversion kits and no resin kits. Many of these names (Classic Plane, Contrails, Eagle’s Talon, Esci, Ertl, Formaplane, Frog, Griffin, Hawk, Matchbox, Monogram, Rareplane, Veeday, Victor 66) are no longer with us or have been absorbed by others. This update lists 345 aircraft types (including the original 168) from 192 different companies (including the original 33), many of which, especially the producers of resin kits, were not in existence in 1986, and some of which were unknown to me at the time. -
Variations in the Airfoil Trace the History of Flight
Variations in the airfoil trace the history of flight. By Walter J. Boyne INGS have always captured the wing, or the elimination of all or W human imagination. The my- part of the wing. thology of flight is found in every culture. Despite this fascination, it Aerodynamic Magic was not until the nineteenth century Since the late 1940s, aerodynamic that scientists began to use precise progress has accelerated at an ever mathematics to compute the opti- greater rate, so much so that modern mum size and shape of wings for a engineering methods and materials flying machine. have combined with new require- Orville and Wilbur Wright did it ments to create totally new wing best with their 1903 Flyer, forcing configurations. Now, elaborate high- competitors to try wings of all shapes, lift devices are tucked into wing lead- styles, and dimensions to avoid in- ing and trailing edges to deploy dur- fringing on their patents. Some went ing the approach to landing, with the to multiple wings—triplanes, quadra- slats and flaps folding out like hand- planes, and more. Others altered the kerchiefs from a magician's sleeve. shape of wings to sweptback, tan- Some by-products have become dem, joined, and cruciform. perhaps too sophisticated. Where Most of the results were too inef- the thick wing of a Douglas C-47 ficient to fly; some were capable of "Gooney Bird" would let you plow generating just enough lift to stag- through cold, wet clouds forever, ger through the air if coupled with a shaking off the ice buildup with sufficiently powerful engine, and a pneumatic boots, some modern air- very few were both stable and effi- foils—as on the Aerospatiale/Alenia cient. -
Conceptual Design of High-Lift Propeller Systems for Small Electric Aircraft
CONCEPTUAL DESIGN OF HIGH-LIFT PROPELLER SYSTEMS FOR SMALL ELECTRIC AIRCRAFT A Dissertation Presented to The Academic Faculty by Michael D. Patterson In Partial Fulfillment of the Requirements for the Degree Doctor of Philosophy in the School of Aerospace Engineering Georgia Institute of Technology August 2016 Copyright c 2016 by Michael D. Patterson CONCEPTUAL DESIGN OF HIGH-LIFT PROPELLER SYSTEMS FOR SMALL ELECTRIC AIRCRAFT Approved by: Professor Brian J. German, Advisor Dr. Nicholas K. Borer School of Aerospace Engineering Aeronautics Systems Analysis Branch Georgia Institute of Technology NASA Langley Research Center Professor Marilyn J. Smith Dr. Erik D. Olson School of Aerospace Engineering Aeronautics Systems Analysis Branch Georgia Institute of Technology NASA Langley Research Center Professor Lakshmi N. Sankar Date Approved: 27 April 2016 School of Aerospace Engineering Georgia Institute of Technology To the One \who is able to do immeasurably more than all we ask or imagine"1 and to my son Isaac who is living proof of His immeasurable power 1Ephesians 3:20 (NIV) ACKNOWLEDGEMENTS This work would not have been completed without the help and encouragement of many people. There is simply not sufficient time or space to acknowledge everyone who has helped me make it through graduate school and finish this document. First and foremost, my wife, Laura, has helped keep me sane throughout the many stressful times and transitions that have occurred in my life since beginning grad school. From providing me encouragement when things were getting overwhelming, to picking up the slack around our home when I was slammed with work, to being an awesome mother to our kids, she has helped me more than any other person to complete this work. -
Philosophy and Ethics of Aerospace Engineering
UNIVERSIDADE DA BEIRA INTERIOR Engenharia Philosophy and Ethics of Aerospace Engineering António Luis Martins Mendes Tese para obtenção do Grau de Doutor em Aeronautical Engineering (3º ciclo de estudos) Orientador: Prof. Doutor Jorge Manuel Martins Barata Covilhã, Dezembro de 2016 ii Dedicatória Gostaria de dedicar esta tese a minha Avó Rosa e aos meus Pais por acreditarem em mim e pelo apoio estes anos todos desde a primeira classe até agora. Obrigado por tudo! ii Acknowledgments My deepest gratitude to Professor Jorge Barata for the continuous support throughout college since I was invited to become a member of his Research and Development team until the present days. His patience, motivation, knowledge, individual and family values have been a mark on my own professional and personal life. His teaching and guidance allowed me to succeed in life to extents I never thought it could have happened. I could have not imagined having a better advisor and mentor for my PhD study. Beside my mentor, I would like to say thank you to Professor André Silva and my colleague and friend Fernando Neves for all the good and bad moments throughout college and life events. I would like to recognize some other professors that made a difference in my studies and career paths – Professor Koumana Bousson, Professor Jorge Silva, Professor Pedro Gamboa, Professor Miguel Silvestre, Professor Aomar Abdesselam, Professor Sarychev and my colleague Maria Baltazar. Last but not least, I would like to thank my family: my wife Kristie, my kids (AJ and Bela) and my neighbor Fred LaCount for the spiritual support throughout this study and phase of my life. -
Plans Index June 22Nd
Aircraft Name Model By Pg. No. Post No. Span (inch) ½ A Twin Harold DeBolt 288 4309 ½ Wave 301 4515 Help file 1 - 1 Master Plan Index Link - 1 1 Help file 1 - Air Age Gas Models book scan 164 2449 Help file 1 - Colin Usher old Model Mag Link 143 2139 1 - Combat Models Ref. article 141 2104 Help file 1 - Cover art for Mushroom Model 210 3154 Help file 1 - COVERING W/ TISSUE - ADD ON Sundancer 192 2880 1 - COVERING WITH TISSUE Planeman 192 2873 Help file 1 - Covering with Tissue Word Doc.& PDF Planeman 192 2879 Help file 1 - Download Manager Link Free 201 3004 Help file 1 - Harold Towner list of plans 167 2498 1 - help file Advanced pdf passwd recovry 104 1552 Help file 1 - How-to Flight Trim Jim Kirkland 201 3011 Help file 1 - Image - tricks of the trade Planeman 199 2974 1 - Info: How to Rotate a Scaled Plan Ka-6BR 281 4214 Help file 1 - International Model Airplane Coop link 192 2874 Help file 1 - link to Aerofred - plans,pdf etc 160 2397 Help file 1 - Link to colin usher mag.index 190 2837 Help file 1 - Link to Cover Art 294 4401 Help file 1 - Link to free PDF converter 198 2966 38 1 - Link to Gimp book (how to) 185 2764 Help file 1 - Link to Gimp Tutorials 185 2767 Help file 1 - Link to Gimpshop (feels like photoshp) 184 2755 1 - link to Globe Swift Plans CAD Earl Stahl 51 753 1 - link to golden age 157 2346 Help file 1 - link to irfanview 154 2308 1 - link to Keith Laumer Plans Dave Fritzke 111 1656 1 - Link to Kits and Plans Welli & Lancas 223 3334 1 - Link to PDF Converter 207 3097 1 - Link to Plans & 3-views 235 3523 1 - Link to Plans Avro Lancaster Aeromodeller 223 3331 Help file 1 - link to Plans French website 164 2447 1 - Link to Rcgroup control line plans 222 3321 1 - link to Republic P-47 31inch. -
Amphibious Aircrafts
Amphibious Aircrafts ...a short overview i Title: Amphibious Aircrafts Subtitle: ...a short overview Created on: 2010-06-11 09:48 (CET) Produced by: PediaPress GmbH, Boppstrasse 64, Mainz, Germany, http://pediapress.com/ The content within this book was generated collaboratively by volunteers. Please be advised that nothing found here has necessarily been reviewed by people with the expertise required to provide you with complete, accurate or reliable information. Some information in this book may be misleading or simply wrong. PediaPress does not guarantee the validity of the information found here. If you need specific advice (for example, medical, legal, financial, or risk management) please seek a professional who is licensed or knowledge- able in that area. Sources, licenses and contributors of the articles and images are listed in the section entitled ”References”. Parts of the books may be licensed under the GNU Free Documentation License. A copy of this license is included in the section entitled ”GNU Free Documentation License” All third-party trademarks used belong to their respective owners. collection id: pdf writer version: 0.9.3 mwlib version: 0.12.13 ii Contents Articles 1 Introduction 1 Amphibious aircraft . 1 Technical Aspects 5 Propeller.............................. 5 Turboprop ............................. 24 Wing configuration . 30 Lift-to-drag ratio . 44 Thrust . 47 Aircrafts 53 J2F Duck . 53 ShinMaywa US-1A . 59 LakeAircraft............................ 62 PBYCatalina............................ 65 KawanishiH6K .......................... 83 Appendix 87 References ............................. 87 Article Sources and Contributors . 91 Image Sources, Licenses and Contributors . 92 iii Article Licenses 97 Index 103 iv Introduction Amphibious aircraft Amphibious aircraft Canadair CL-415 operating on ”Fire watch” out of Red Lake, Ontario, c. -
2019 June Newsletter
AMA Chapter #341 June 2019 Figure : First day ATTENTION! of : Joe Nall 2019 at Triple Tree We encourage Aerodrome, any comments South Carolina as well as content for monthly issues Please email [email protected] for submissions. Thank you. The club encourages all our members to visit the club’s Facebook page and check out the latest content, announcements and club event’s www.facebook.com/groups/148353592007739. Also check out the clubs website at www.hampshirecountyrc.com Hampshire County Radio Controllers Business Meeting of May 2, 2019 MINUTES The meeting was brought to order by V.P. Santiago M. after pizza was brought in from Florence Pizza for the small group attending. As was noted, the weather was a factor in moving to the VFW when May’s meeting is usually held at the field. The attendance was 10 including two of the club officers, so the meeting rules for voting were suspended due to a lack of a quorum. As the secretary mentioned; the only time a vote is valid without a quorum is when an applicant for membership is presented. Santiago then asked the secretary to read the minutes (waived by consensus) and the treasurer’s financial report for the month of April. As there were no objections or change the financial report was accepted as read. Under Old Business , Santiago said we would forgo the usual 50/50 raffle but would have a free raffle of donated hobby items later in the meeting. Next, he went over some of the tasks completed at the Spring Clean-Up that included: new bleacher seating (metal frame donated by the SPARKS CLUB) needing completely new wood for the seats and steps. -
Innovation in Carrier Aviation
U.S. Naval War College U.S. Naval War College Digital Commons Newport Papers Special Collections 8-2011 Innovation in Carrier Aviation Thomas C. Hone Norman Friedman Mark D. Mandeles Follow this and additional works at: https://digital-commons.usnwc.edu/usnwc-newport-papers Recommended Citation Hone, Thomas C.; Friedman, Norman; and Mandeles, Mark D., "Innovation in Carrier Aviation" (2011). Newport Papers. 37. https://digital-commons.usnwc.edu/usnwc-newport-papers/37 This Book is brought to you for free and open access by the Special Collections at U.S. Naval War College Digital Commons. It has been accepted for inclusion in Newport Papers by an authorized administrator of U.S. Naval War College Digital Commons. For more information, please contact [email protected]. NAVAL WAR COLLEGE NEWPORT PAPERS 37 NAVAL WAR COLLEGE WAR NAVAL Innovation in Carrier Aviation NEWPORT PAPERS NEWPORT S NNA ESE AVV TT AA A A LL T T WW S S AA D D R R E E C C T T I I O O L N L N L L U U E E E E G G H H E E T T II VIVRIRIBIUBU OORR AA SS CCTT M MAARRI I V VII 37 T homas C. Hone Norman Friedman Mark D. Mandeles Color profile: Disabled Composite Default screen U.S. GOVERNMENT Cover OFFICIAL EDITION NOTICE This perspective aerial view of Newport, Rhode Island, drawn and published by Galt & Hoy of New York, circa 1878, is found in the American Memory Online Map Collections: 1500–2003, of the Library of Congress Geography and Map Division, Washington, D.C. -
Chance Vought XF5U Skimmer
Was Sie schon immer mal wissen wollten – oder die letzten Geheimnisse der Luftfahrt Eine lose Folge von Dokumentationen vom Luftfahrtmuseum Hannover-Laatzen Stand Frühjahr 2014 - Seite 1 Diese Dokumentationen werden Interessenten auf Wunsch zur Verfügung gestellt und erscheinen in einer losen Folge von Zeiträumen. Compiled and edited by Johannes Wehrmann 2014 Source of Details Wikipedia and Internet Chance Vought XF5U Skimmer AIC = 1.022.2752.20.10 Typ Jagdflugzeug-Prototyp Entwurfsland: USA Hersteller: Chance Vought Erstflug: nur Rollversuche Stückzahl: 1 Entwicklungsgeschichte Die Chance Vought XF5U (Werksbezeichnung VS-315) war der Prototyp eines geplanten extrem kurzstartfähigen (ESTOL) Jagdflugzeugs des US-amerikanischen Herstellers Chance Vought aus den 1940er Jahren. Der inoffizielle Beiname Flying Flapjack (Fliegender Pfannkuchen) rührt von der ungewöhnlichen konstruktiven Auslegung mit einer angenähert kreisförmigen Tragfläche her. Die Entwicklung der XF5U basierte auf den Ergebnissen des Erprobungsträgers Chance Vought V-173. Nachdem bereits die V-173 inoffiziell als „Zimmer-Skimmer“ (nach ihrem Konstrukteur Zimmerman) bezeichnet wurde, trug die XF5U auch den Beinamen „Skimmer“. Bereits vor dem Erstflug der V-173 erteilte die US Navy am 17. September 1942 Chance Vought den Auftrag zum Bau eines auf der V-173 basierenden Jagdflugzeug-Prototyps XF5U-1. Die V-173 diente bei über 200 Flügen als Testflugzeug, den Schritt zur Erprobung der Senkrechtstartfähigkeit wurde jedoch nicht unternommen; hierzu hätte es einer grundlegenden Umkonstruktion der Maschine bedurft. Der Auftrag umfasste den Bau einer Bruchzelle und eines Prototyps für die Flugerprobung. Verantwortlicher Konstrukteur war E. J. Greenwood. Eine aus Holz aufgebaute Attrappe konnte am 7. Juni 1943 inspiziert werden, wobei noch Dreiblatt-propeller mit 4,88 m Durchmesser verwendet wurden, die später gegen eine Vierblattausführung ausgetauscht wurden. -
Ahs 2013 Kurara
AHS 2013 KURARA 30th Annual American Helicopter Society Student Design Competition-2013 Graduate Category KIRAN.G INDIA By In response to 30th Annual American Helicopter Society Student Design Competition-2013 Graduate Category Name: Kiran G Type: Individual Entry College: Auden Technology and management Academy Branch: Information Science and Engineering Personal Address: Kiran G S/o Ganesha D #2/6, Sri Banashankari Nilayam, Banjappa Layout, Arekere, Bannerghatta Road Bangalore-560076. Karnataka, India Email id: [email protected] / [email protected] Contact No.: +91-7204401790 Signature: KURARA[AHS-2013] ACKNOWLEDGMENT KURARA is design belonged to KIRAN G B.E graduate from Auden Technology and Management Academy in Information Science and Engineering branch, INDIA. It is an Individual effort on completing the design, but it couldn’t have been completed so easily being from a software field without the help of some people who helped me understand some of the basic concepts and way of designing. Aerospace engineering is my ambition in life for which I have planned my higher studies to go with interdisciplinary branch in my masters; for which I’m considering this design to be a stepping stone. I would like to thank my parents and these people who supported me and helped me in the process. Mr. Sudeer Hegade, Employee, Hindustan Aeronautics Ltd. Helicopter maintenance division Mr. Shashi Kumar A, Deputy General Manager, Hindustan Aeronautics Ltd. Aerospace division Mr. Shikar Chaturvedi, Employee, Taneja Aerospace and Aviation Ltd. Mr. Rakesh, Employee, Taneja Aerospace and Aviation Ltd. Maintenance division Prof. Shivram, Senior scientist, Indian Institute of Astrophysics Mrs. Joslin Josh, Senior Lecturer, Physics, St.