Statement of Work (Sow)
Total Page:16
File Type:pdf, Size:1020Kb
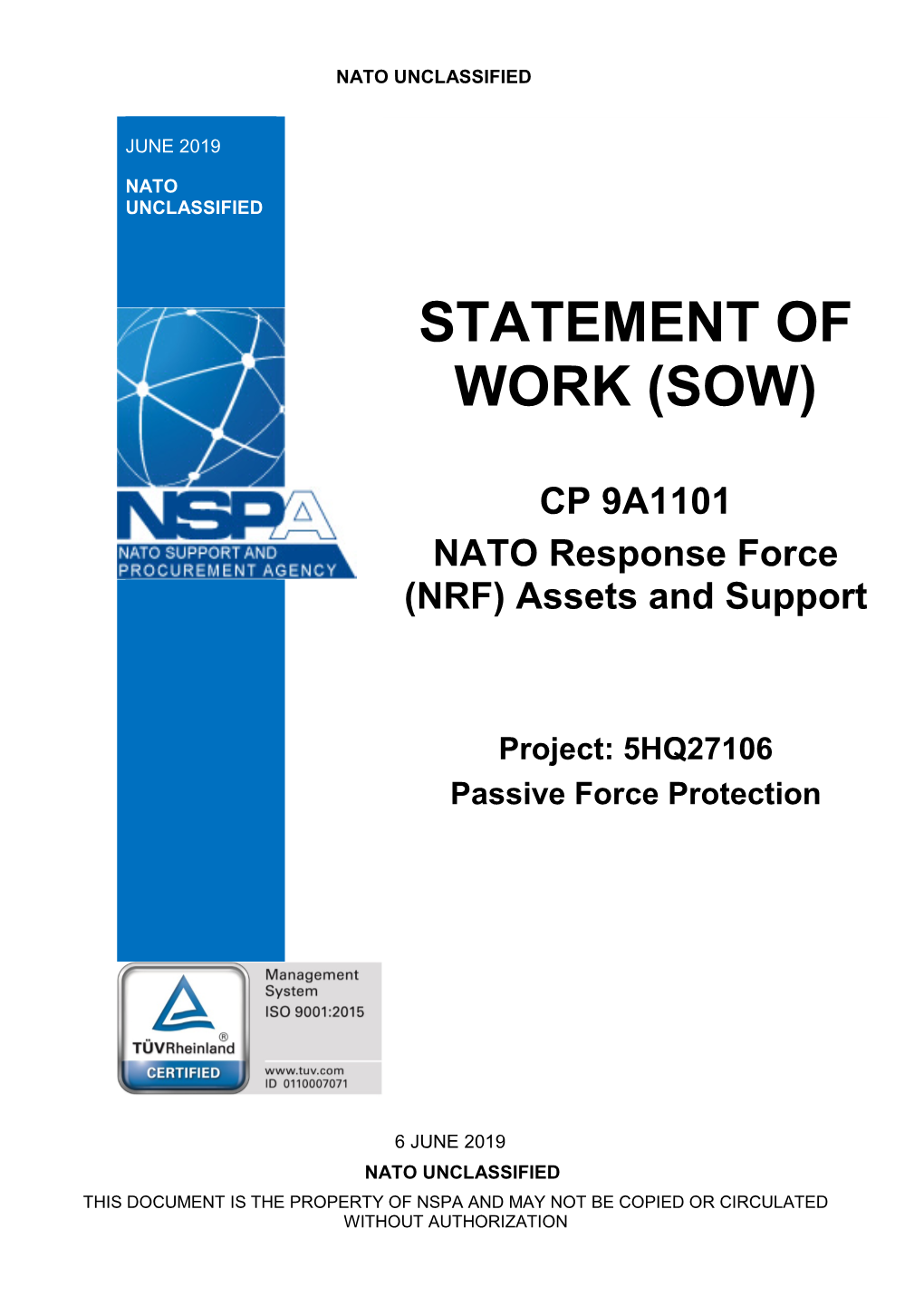
Load more
Recommended publications
-
Adits, Caves, Karizi-Qanats, and Tunnels in Afghanistan: an Annotated Bibliography by R
Adits, Caves, Karizi-Qanats, and Tunnels in Afghanistan: An Annotated Bibliography by R. Lee Hadden Topographic Engineering Center November 2005 US Army Corps of Engineers 7701 Telegraph Road Alexandria, VA 22315-3864 Adits, Caves, Karizi-Qanats, and Tunnels In Afghanistan Form Approved REPORT DOCUMENTATION PAGE OMB No. 0704-0188 Public reporting burden for this collection of information is estimated to average 1 hour per response, including the time for reviewing instructions, searching existing data sources, gathering and maintaining the data needed, and completing and reviewing this collection of information. Send comments regarding this burden estimate or any other aspect of this collection of information, including suggestions for reducing this burden to Department of Defense, Washington Headquarters Services, Directorate for Information Operations and Reports (0704-0188), 1215 Jefferson Davis Highway, Suite 1204, Arlington, VA 22202-4302. Respondents should be aware that notwithstanding any other provision of law, no person shall be subject to any penalty for failing to comply with a collection of information if it does not display a currently valid OMB control number. PLEASE DO NOT RETURN YOUR FORM TO THE ABOVE ADDRESS. 1. REPORT DATE 30-11- 2. REPORT TYPE Bibliography 3. DATES COVERED 1830-2005 2005 4. TITLE AND SUBTITLE 5a. CONTRACT NUMBER “Adits, Caves, Karizi-Qanats and Tunnels 5b. GRANT NUMBER In Afghanistan: An Annotated Bibliography” 5c. PROGRAM ELEMENT NUMBER 6. AUTHOR(S) 5d. PROJECT NUMBER HADDEN, Robert Lee 5e. TASK NUMBER 5f. WORK UNIT NUMBER 7. PERFORMING ORGANIZATION NAME(S) AND ADDRESS(ES) 8. PERFORMING ORGANIZATION REPORT US Army Corps of Engineers 7701 Telegraph Road Topographic Alexandria, VA 22315- Engineering Center 3864 9.ATTN SPONSORING CEERD / MONITORINGTO I AGENCY NAME(S) AND ADDRESS(ES) 10. -
Indian Hieroglyphs
Indian hieroglyphs Indus script corpora, archaeo-metallurgy and Meluhha (Mleccha) Jules Bloch’s work on formation of the Marathi language (Bloch, Jules. 2008, Formation of the Marathi Language. (Reprint, Translation from French), New Delhi, Motilal Banarsidass. ISBN: 978-8120823228) has to be expanded further to provide for a study of evolution and formation of Indian languages in the Indian language union (sprachbund). The paper analyses the stages in the evolution of early writing systems which began with the evolution of counting in the ancient Near East. Providing an example from the Indian Hieroglyphs used in Indus Script as a writing system, a stage anterior to the stage of syllabic representation of sounds of a language, is identified. Unique geometric shapes required for tokens to categorize objects became too large to handle to abstract hundreds of categories of goods and metallurgical processes during the production of bronze-age goods. In such a situation, it became necessary to use glyphs which could distinctly identify, orthographically, specific descriptions of or cataloging of ores, alloys, and metallurgical processes. About 3500 BCE, Indus script as a writing system was developed to use hieroglyphs to represent the ‘spoken words’ identifying each of the goods and processes. A rebus method of representing similar sounding words of the lingua franca of the artisans was used in Indus script. This method is recognized and consistently applied for the lingua franca of the Indian sprachbund. That the ancient languages of India, constituted a sprachbund (or language union) is now recognized by many linguists. The sprachbund area is proximate to the area where most of the Indus script inscriptions were discovered, as documented in the corpora. -
The Kingdom of Afghanistan: a Historical Sketch George Passman Tate
University of Nebraska Omaha DigitalCommons@UNO Books in English Digitized Books 1-1-1911 The kingdom of Afghanistan: a historical sketch George Passman Tate Follow this and additional works at: http://digitalcommons.unomaha.edu/afghanuno Part of the History Commons, and the International and Area Studies Commons Recommended Citation Tate, George Passman The kingdom of Afghanistan: a historical sketch, with an introductory note by Sir Henry Mortimer Durand. Bombay: "Times of India" Offices, 1911. 224 p., maps This Monograph is brought to you for free and open access by the Digitized Books at DigitalCommons@UNO. It has been accepted for inclusion in Books in English by an authorized administrator of DigitalCommons@UNO. For more information, please contact [email protected]. Tate, G,P. The kfn&ean sf Af&mistan, DATE DUE I Mil 7 (7'8 DEDICATED, BY PERMISSION, HIS EXCELLENCY BARON HARDINGE OF PENSHURST. VICEROY AND GOVERNOR-GENERAL OF INDIA, .a- . (/. BY m HIS OBEDIENT, SERVANT THE AUTHOR. il.IEmtev 01 the Asiniic Society, Be?zg-nl, S?~rueyof I~din. dafhor of 'I Seisinqz : A Menzoir on the FJisio~y,Topo~rcrphj~, A7zliquiiies, (112d Peo$Ie of the Cozi?zt~y''; The F/.o?zlic7,.~ of Baluchisia'nn : Travels on ihe Border.? of Pe~szk n?zd Akhnnistnn " ; " ICalnf : A lMe??zoir on t7ze Cozl7~try and Fnrrzily of the Ahntadsai Khn7zs of Iinlnt" ; 4 ec. \ViTkI AN INrPR<dl>kJCTOl2Y NO'FE PRINTED BY BENNETT COLEMAN & Co., Xc. PUBLISHED AT THE " TIMES OF INDIA" OFFTCES, BOMBAY & C.1LCUTT-4, LONDON AGENCY : gg, SI-IOE LANE, E.C. -
Construction Guide V2 LR.Pdf
1 Introduction – protect and survive 2 Basic construction guidelines 3 Design of Concertainer structures 4 Fill selection and characteristics 5 Preconfigured structures 6 Improvised structures 7 Maintenance and repair 8 Product technical information 9 Trial information 10 Packing and shipping 11 Conversion tables 12 Contacts 1 Introduction – protect and survive Introduction – protect and survive 1.01 HESCO® Concertainer® has Delivered flat-packed on standard been a key component in timber skids or pallets, units providing Force Protection since can be joined and extended the 1991 Gulf War. using the provided joining pins and filled using minimal Concertainer units are used manpower and commonly extensively in the protection of available equipment. personnel, vehicles, equipment and facilities in military, Concertainer units can be peacekeeping, humanitarian installed in various configurations and civilian operations. to provide effective and economical structures, tailored They are used by all major to the specific threat and level military organisations around of protection required. Protective the world, including the UK structures will normally be MOD and the US Military. designed to protect against ballistic penetration of direct fire It is a prefabricated, multi- projectiles, shaped charge cellular system, made of warheads and fragmentation. Alu-Zinc coated steel welded HESCO Guide Construction for Engineers mesh and lined with non-woven polypropylene geotextile. Introduction – protect and survive 1.02 Protection is afforded by the fill In constructing protective material of the structure as a structures, consideration must consequence of its mass and be given to normal structural physical properties, allied with design parameters. the proven dynamic properties of Concertainer units. The information included in this guide is given in good faith, Users must be aware that the however local conditions may protection afforded may vary affect the performance of HESCO Guide Construction for Engineers with different fill materials, and structures. -
POETRY OFFERINGS from David W. Mitchell
1 POETRY OFFERINGS from David W. Mitchell 2 Photography of David Mitchell by Ken Roberts Cover photography by Jeremiah Trilli Line drawing by Summer Breeze Published by Motherbird Books Silver City, New Mexico motherbird.com © David W. Mitchell 2008 3 Index A Dark Hole In Time . 8 A Gift . 9 A Lovely Day for Borscht Fish . 10 A Modern Carollette for Dodgson . 11 Abroad Among the Limbless . 12 Adagio in Zzzzz Minor . 13 Afternoon of a Biblioparadisiac . 14 Ah Dylan, Dylan . 15 An Olympian Lesson . 16 Apostatic Succession . 17 Ballad of Saint Louis, the Unfrocked Cardinal 18 Belle Ardoise I, The . 20 Blatissimus . 21 Blue Writer, The . 22 Carmel I . 23 Carmel II . 25 Chelsea . 27 Compass Rose and the Gypsy Will . 28 Compendium Humanum . 29 Concertina in F-Stop Major . 31 Critique . 32 Cursive Reclaimed . 33 Cutting Corners I; Cutting Corners II . 34 Departure of Roses, The . 35 Diasporulation . 36 Disappearance . 37 Drizzle . 38 Doubling Duplicity . 39 Eleven Red-Haired Men . 40 Encampment, The . 41 Epitaph for Floyd . 42 Fangs . 43 Father Time Contemplates Mass . 44 4 Fingersongs- I . 45 For Edna, and John, and All . 46 For Jessica and the Williams . 47 For Mimi Farina: Bread and Roses . 51 From A to Z and Back Again . 52 Goulashification . 53 Heard On the Concertina Wire . 54 Helicocochoidal Figmentation. 55 Hexing the Circle . 56 Hillock and the Holly, The . 57 How I knew What to Do . 59 In Praise of Thumbs . 60 In Praise of Thumbs II . 61 In the Mailstrom . 63 In Sacramental Jeans . 64 Infinite Regress of Dawn, The . -
War Record of the York & Lancaster Regiment, 1900-1902
CHAPTER XII COLUMNS AND BLOCKHOUSES T was now quite evident that the Proclama I tion of August 6th had failed, and there fore fresh measures must be adopted if peace was to be attained. The Boers were directing their energies towards evading any decisive engagement, aiming rather at harassing and annoying us in every possible way, in the vain hope of thereby wearing out our resources, our spirits, and our patience. Their training, together with the nature of the country and their intimate knowledge of it, combined to favour this irregular mode of war fare, and it was no easy task for us to cope with opponents who, whenever the odds were against them, could speedily disperse their forces, large or small, and reassemble at any given spot miles away. To meet these difficulties Lord Kitchener at first tried the plan of increasing the numbers and mobility of the columns, but as time went on and the guerilla warfare still raged, it was determined to perfect the system of block houses already in operation. 176 MATERIALS FOR A BLOCKHOUSE FINISHING A BLOCKHOUSE (NO . 27) Tofacep . 176 COLUMNS AND BLOCKHOUSES 177 Before the blockhouse lines were fairly started, CollllWIS. the columns used either to w@rkindependently of each other or several would combine, con ve,rging simultaneously on a common centre, with a view to inclosing the Boers within a given area. The Boers, however, soon learned to foresee and forestall these manceuvres, and before the circle closed they would slip through and retreat to their hiding-places, of which there were many. -
Notice of Public Meeting City of Albany City Council
NOTICE OF PUBLIC MEETING CITY OF ALBANY OUR MISSION IS CITY COUNCIL “Providing quality public services Council Chambers for a better Albany community.” 333 Broadalbin Street SW Wednesday, March 9, 2011 OUR VISION IS 7:15 p.m. “A vital and diversified community that promotes a high quality of life, AGENDA great neighborhoods, balanced economic growth, and quality public services.” Rules of Conduct for Public Hearing 1. No person shall be disorderly, abusive, or disruptive of the orderly conduct of the hearing. 1. CALL TO ORDER 2. Persons shall not testify without first receiving recognition from the presiding officer and stating their 2. PLEDGE OF ALLEGIANCE TO THE FLAG full name and residence address. 3. No person shall present irrelevant, immaterial, or 3. ROLL CALL repetitious testimony or evidence. 4. There shall be no audience demonstrations such as 4. SCHEDULED BUSINESS applause, cheering, display of signs, or other conduct disruptive of the hearing. a. Legislative Public Hearing 1) Development Code Amendments. [Pages 1-28] a) DC-06-10, amending Ordinance No. 4441, which adopted the City of Albany Development Code and Zoning Map by amending the Development Code text related to allowing electric fences in the Light Industrial and Heavy Industrial zones, allowing barbed wire on livestock fencing, and clarifying the fencing standards, adopting findings, and declaring an emergency. [Pages 1-23] Action: ____________________________________________________________ ORD. NO.__________ b) DC-01-11, amending Ordinance No. 4441, which adopted the City of Albany Development Code and Zoning Map by amending the Development Code text related to providing an alternative perimeter landscaping plan when landscaping can be placed in excess public right-of-way, adopting findings, and declaring an emergency. -
Military Systems and Technology Magazine Edition 23
MILITARY SYSTEMS & TECHNOLOGY GEROH High-quality mobile mast systems & trailer solutions HESCO Rapidly deployable, ground-mounted barrier systems for military protection NOPTEL Development & manufacture of innovative applied optoelectronic solutions PLUS... UNIVAL GROUP GMBH Digital Jamming as part of Multi-level Blast BREAKING Protection NEWS FROM... ANSELL COBHAM SYSTEMATIC DEFENCELL Integrated command & control from joint PELI hq to the tactical edge TELEDYNE Image Courtesy of Ansell 1 www.militarysystems-tech.com T. +44 (0) 1398 351606 E. [email protected] EDITION 23 MILITARY SYSTEMS & TECHNOLOGY MAKING THE WORLD A SAFER PLACE SURPLUS AND OBSOLETE SMALL ARMS AMMUNITION DESTRUCTION In the new global economy many Armed Forces are downsizing to reflect the budgetary constraints of their respective countries. This brings with it surplus items which, because of the reduction in the number of personnel, are put into storage until a suitable method of disposal is found. High on the priority list is ammunition of all types and nature. Small Arms Ammunition (SAA) accounts for a large percentage of any military organisation’s arsenal. It also contributes significantly to the stockpile of surplus, obsolete and shelf life expired ammunition. EOD Solutions Ltd in conjunction with CALDO engineering have developed the Transportable Ammunition Destruction System (TRADS) to destroy SAA in an environmentally responsible manner. There are two systems available, the TRADS 40 and the TRADS 20, both of which employ ceramic filtration backed up TRADS 20 utilises a furnace that allows small quantities of with a catalytic filter to ensure complete cleaning of the gases. ammunition to be destroyed and then emptied into a bin for Recent improvements have allowed the system to clean the further processing such as Free from Explosives Inspection. -
Crime, Histoire & Sociétés / Crime, History & Societies Vol. 18, N°2 | 2014
Crime, Histoire & Sociétés / Crime, History & Societies Vol. 18, n°2 | 2014 Varia Electronic version URL: http://journals.openedition.org/chs/1481 DOI: 10.4000/chs.1481 ISSN: 1663-4837 Publisher Librairie Droz Printed version Date of publication: 1 October 2014 ISBN: 978-2-600-01854-8 ISSN: 1422-0857 Electronic reference Crime, Histoire & Sociétés / Crime, History & Societies, Vol. 18, n°2 | 2014 [Online], Online since 01 October 2017, connection on 24 September 2020. URL : http://journals.openedition.org/chs/1481 ; DOI : https://doi.org/10.4000/chs.1481 This text was automatically generated on 24 September 2020. © Droz 1 TABLE OF CONTENTS Articles Policing the empire / Policing the metropole : Some thoughts on models and types Clive Emsley Homicide and Organised Murder in a Global Perspective Bare Sticks and Naked Pity : Rhetoric and Representation in Qing Dynasty (1644-1911). Capital Case Records Thomas Buoye Figures of Deterrence in Late Imperial China. Frequency, Spatial Repartition, and Types of Crimes Targeted by Dismemberment under the Qing Dynasty Jérôme Bourgon and Julie Erismann Violence in Ming-Qing China : An Overview William T. Rowe Toward a Global History of Homicide and Organized Murder Pieter Spierenburg Forum Review essay Confronting terrorism: British Experiences past and present Georgina Sinclair Reviews Clère (Jean-Jacques), Farcy (Jean-Claude) (dir.), Le juge d’instruction : approches historiques Dijon, Éditions universitaires de Dijon, 2010, 320 pp., ISBN 9 782915 611687 Vincent Fontana Dominique Kalifa, Pierre Karila-Cohen (dir.), Le commissaire de police au XIXe siècle Antoine Renglet Crime, Histoire & Sociétés / Crime, History & Societies, Vol. 18, n°2 | 2014 2 Simon Fieschi, Les gendarmes en Corse 1927-1934. -
Mughals at War: Babur, Akbar and the Indian Military Revolution, 1500 - 1605
Mughals at War: Babur, Akbar and the Indian Military Revolution, 1500 - 1605 A Dissertation Presented in Partial Fulfillment of the Requirements for the Degree of Doctor of Philosophy in the Graduate School of The Ohio State University By Andrew de la Garza Graduate Program in History The Ohio State University 2010 Dissertation Committee: John F. Guilmartin, Advisor; Stephen Dale; Jennifer Siegel Copyright by Andrew de la Garza 2010 Abstract This doctoral dissertation, Mughals at War: Babur, Akbar and the Indian Military Revolution, examines the transformation of warfare in South Asia during the foundation and consolidation of the Mughal Empire. It emphasizes the practical specifics of how the Imperial army waged war and prepared for war—technology, tactics, operations, training and logistics. These are topics poorly covered in the existing Mughal historiography, which primarily addresses military affairs through their background and context— cultural, political and economic. I argue that events in India during this period in many ways paralleled the early stages of the ongoing “Military Revolution” in early modern Europe. The Mughals effectively combined the martial implements and practices of Europe, Central Asia and India into a model that was well suited for the unique demands and challenges of their setting. ii Dedication This document is dedicated to John Nira. iii Acknowledgments I would like to thank my advisor, Professor John F. Guilmartin and the other members of my committee, Professors Stephen Dale and Jennifer Siegel, for their invaluable advice and assistance. I am also grateful to the many other colleagues, both faculty and graduate students, who helped me in so many ways during this long, challenging process. -
Handbook on USSR Military Forces, Chapter VI: Fortifications War Department (USA)
University of Nebraska - Lincoln DigitalCommons@University of Nebraska - Lincoln DOD Military Intelligence U.S. Department of Defense 1-1946 Handbook on USSR Military Forces, Chapter VI: Fortifications War Department (USA) Robert L. Bolin , Depositor University of Nebraska-Lincoln, [email protected] Follow this and additional works at: http://digitalcommons.unl.edu/dodmilintel War Department (USA) and Bolin, Robert L. , Depositor, "Handbook on USSR Military Forces, Chapter VI: Fortifications" (1946). DOD Military Intelligence. 27. http://digitalcommons.unl.edu/dodmilintel/27 This Article is brought to you for free and open access by the U.S. Department of Defense at DigitalCommons@University of Nebraska - Lincoln. It has been accepted for inclusion in DOD Military Intelligence by an authorized administrator of DigitalCommons@University of Nebraska - Lincoln. Technical Manual, TM 30-430 Handbook on USSR Military Forces Chapter VI Fortifications Robert L. Bolin, Depositor University of Nebraska-Lincoln, [email protected] Technical Manual, TM 30-430, Chapter VI 1 January 1946 Handbook on USSR Military Forces Chapter VI Fortifications War Department Washington, DC Comments The copy digitized was borrowed from the Marshall Center Research Library, APO, AE 09053-4502. Abstract TM 30-340, Handbook on USSR Military Forces, was “published in installments to expedite dissemination to the field.” TM30-430, Chapter VI, 1 January 1946, “Fortifications,” is a detailed discussion of earthworks and structures used for defensive purposes. This chapter is illustrated with numerous drawings, diagrams, and charts. This manual is listed in WorldCat under Accession Number: OCLC: 19989681 1 Jan 46 TM 30-430 CHAPTER VI FORTIFICATIONS TABLE OF CONTENTS Page Figure Section I. -
18 Urban Development and Architecture
ISBN 978-92-3-103654-5 URBAN DEVELOPMENT. 18 URBAN DEVELOPMENT AND ARCHITECTURE G. A. Pugachenkova, A. H. Dani and Liu Yingsheng Contents TRANSOXANIA AND KHURASAN ......................... 517 The arrival of the Arabs ................................. 517 The Mongol conquests and their aftermath ....................... 532 SOUTHERN CENTRAL ASIA ............................ 565 The period of Arab rule in Sind ............................. 565 The Ghaznavids in Afghanistan and north-western India ................ 567 The Ghurids ....................................... 572 The Delhi Sultans .................................... 572 Provincial styles: Panjab, Sind and Kashmir ...................... 578 EASTERN CENTRAL ASIA .............................. 581 The Turfan region .................................... 583 Architecture of the towns of the Turfan region ..................... 586 The towns of the eastern end of the Tarim basin .................... 586 The region north of the T’ien Shan mountains ..................... 587 Towns in Mongolia ................................... 591 Conclusion ....................................... 593 516 © UNESCO 1996 ISBN 978-92-3-103654-5 The arrival of the Arabs Part One TRANSOXANIA AND KHURASAN (G. A. Pugachenkova) The arrival of the Arabs When the Arabs arrived in Khurasan and Transoxania they found few towns. The popula- tion lived mainly in the countryside, where there were scattered estates with the fortified kushks (castles) of major and minor dihqan¯ (land-owner)-suzerains and adjacent settle- ments. The ancient towns had either shrunk in size (Samarkand, Merv, Termez, Balkh) or been abandoned. The new towns were few in number, and small (Panjikent). Warfare was rife in the seventh and eighth centuries and, as a consequence, there was a general decline in building activity. This situation only changed in the ninth century, when the sphere of influence of the caliphate finally took in the countries of Central Asia and Islam became solidly established.