Docstec 11695.Pdf Size
Total Page:16
File Type:pdf, Size:1020Kb
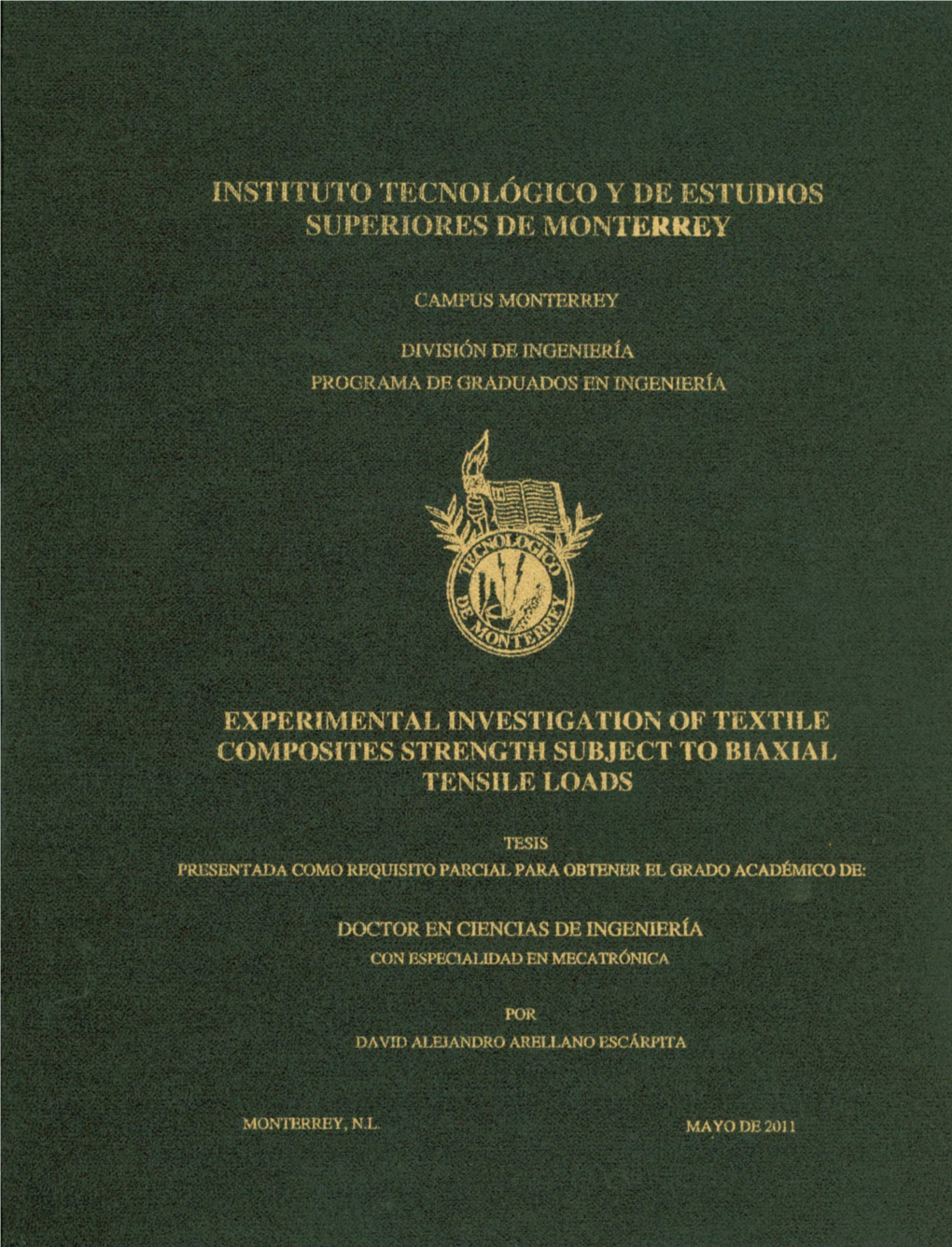
Load more
Recommended publications
-
Bio Construction, Quincha, Thermal Performance
International Journal of Construction Engineering and Management 2018, 7(2): 53-64 DOI: 10.5923/j.ijcem.20180702.01 Thermal Performance of “Quincha” Constructive Technology in a Mountainous Region Cuitiño Guadalupe1,*, Esteves Alfredo1, Barea Gustavo1, Marín Laura2, Bertini Renato3 1Environment, Habitat and Energy Institute Mendoza - CONICET, Av. Ruiz Leal s/n, Argentina 2Independent Architect, Mendoza, Argentina 3Green Village Tudunqueral Srl, Mendoza, Argentina Abstract Increasingly, families are choosing to build their homes using earth-based technologies. This is the case in Tudunqueral Ecovilla (eco village) located in Uspallata Valley, Mendoza, Argentina. In this Andes Mountain Area, the houses primarily have been built with “Quincha” (also known as “wattle and daub”). Specifically, this paper aims to evaluate the thermal performance of the eco village’s Multi-Purpose Centre (MPC) which is a “Quincha” construction. Indoor temperature and relative humidity measurements and all external variables of climate (temperature, relative humidity, solar radiation and wind speed and direction) has been registered for winter and summer seasons. Thermography to evaluate local thermal situations of walls, ceilings and floors has been used. An interesting feature is that MPC has a Trombe Wall as passive solar system for heating it. Implementing energy conservation strategies coupled with the use of “quincha” as constructive technology allow for excellent results in the face of the rigorous climate of the mountain environment. It has proven that although low outdoor temperatures of -6°C were recorded, at the same time indoor temperatures was near 10°C, that means a temperature difference (in-out) of around 16°C. As well, while outdoor thermal amplitude reached 26°C, with the optimization of the MPC the thermal range indoors was 6.25°C. -
From Vulnerability to Resilience, a Framework for Analysis and Action To
From Vulnerability to Resilience PRAISE FOR THIS BOOK ‘It is rare to fi nd a book so accessible that combines theory and practice. The V2R offers a succinct yet usable framework that can be applied by a range of development actors at every level from local to national and even international.’ Nick Hall, Disaster Risk Reduction Adviser, Plan International ‘This is a very impressive and admirable piece of work. By balancing the various elements of live- lihoods, vulnerability, governance, hazards, uncertainty, resilience, it fi lls a big gap. V2R makes resilience seem more manageable.’ Dr John Twigg, Senior Research Associate, Department of Civil, Environmental and Geomatic Engineering, University College London From Vulnerability to Resilience A framework for analysis and action to build community resilience Katherine Pasteur Practical Action Publishing Ltd Schumacher Centre for Technology and Development Bourton on Dunsmore, Rugby, Warwickshire CV23 9QZ, UK www.practicalactionpublishing.org © Practical Action Publishing, 2011 ISBN 978 1 85339 718 9 All rights reserved. No part of this publication may be reprinted or reproduced or utilized in any form or by any electronic, mechanical, or other means, now known or hereafter invented, including photocopying and recording, or in any information storage or retrieval system, without the written permission of the publishers. A catalogue record for this book is available from the British Library. The author has asserted her rights under the Copyright Designs and Patents Act 1988 to be identifi ed as authors of this work. Since 1974, Practical Action Publishing (formerly Intermediate Technology Publications and ITDG Publishing) has published and disseminated books and information in support of international development work throughout the world. -
Montículos Arqueológicos, Actividades Y Modos De Habitar. Vivienda Y Uso Del Espacio Doméstico En Santiago Del Estero (Tierras Bajas De Argentina)
ARQUEOLOGÍA DE LA ARQUITECTURA, 13, enero-diciembre 2016, e040 Madrid / Vitoria ISSN-L: 1695-2731 doi: http://dx.doi.org/10.3989/arq.arqt.2016.003 ESTUDIOS / STUDIES Montículos arqueológicos, actividades y modos de habitar. Vivienda y uso del espacio doméstico en Santiago del Estero (tierras bajas de Argentina) Archaeological mounds, activities and ways to inhabit. Dwellings and domestic space use in Santiago del Estero (Argentine lowlands) Constanza Taboada Instituto Superior de Estudios Sociales (ISES) del Consejo Nacional de Investigaciones Científicas y Técnicas de la República Argentina (CONICET) / Instituto de Arqueología y Museo (IAM) de la Universidad Nacional de Tucumán (UNT) e-mail: [email protected] RESUMEN Este artículo aborda la definición del espacio habitacional de las poblaciones indígenas que vivieron en la llanura de Santiago del Estero (Argentina) y su vinculación con los montículos característicos de la región. Parte de trabajos arqueológicos de campo y pone en juego una estrategia teórico-metodológica que apunta a superar las limitaciones de una arquitectura perecedera. Como resultado se identificó un ámbito doméstico techado, con el primer registro para la región de un techo de torta y un piso posiblemente preparado. En articulación con la reinterpretación de datos bibliográficos, se definieron situaciones diferenciadas en cuanto a actividades, construcciones y modos de habitar, que habilitan una nueva lectura sobre la diversidad y características de las poblaciones de la región. Los casos analizados amplían el conocimiento de la diversidad y distribución de las construcciones monticulares de las tierras bajas de Sudamérica, y aportan elementos sobre arquitectura doméstica, poco estudiada para los mismos. Palabras clave: arqueología de unidades domésticas; arquitectura; estratigrafía; prehispánico; colonial; tierras bajas sudamericanas. -
Quincha Architecture: the Development of an Antiseismic Structural System in Seventeenth Century Lima
Proceedings of the First International Congress on Construction History, Madrid, 20th-24th January 2003, ed. S. Huerta, Madrid: I. Juan de Herrera, SEdHC, ETSAM, A. E. Benvenuto, COAM, F. Dragados, 2003. Quincha architecture: The development of an antiseismic structural system in seventeenth century Lima Humberto Rodríguez Camilloni The introduction of quincha construction in the City of Kings or Lima during the middle of the seventeenth century marked a decisive turning point in the devel- opment of Spanish co]onia] architecture along the Peruvian coast. Not only did this ingenious antiseismic structural system provide a definitive solution to the earthquake problem that had plagued several generations of builders since the founding of the vicerega] capital by Francisco Pizarro in 1535, but it also permitted the creation of monumenta] and lofty interior spaces which paraJleled and even rivaled European designs. Surprising]y, however, quincha construction has received only a general and inadequate treatment in the artistic literature of Spanish colonia] architecture; its fuJl impact stilI awaiting recognition in the history of construction. I In an effort to help fill this void, this paper investigates the earthquake-proof system of quincha and its formal implications, as a cornerstone in the history of South American colonial architecture. In the viceroyalty of Peru, possibly no greater chalIenge confronted the colonia] architects than that of designing buildings that could withstand the frequent earthquakes. Time and again European and viceregal architects had seen the failure of their efforts, incJuding the anachronistic use of Gothic ribbed vaulting in the Cathedral of Lima folJowing ] the earthquake of 609 because it was believed it Figure 1 2 wou]d provide a more resistant structura] system. -
No. 28393-A Gaceta Oficial Digital, Martes 24 De Octubre De 2017 1 No
No. 28393-A Gaceta Oficial Digital, martes 24 de octubre de 2017 1 No. 28393-A Gaceta Oficial Digital, martes 24 de octubre de 2017 2 No. 28393-A Gaceta Oficial Digital, martes 24 de octubre de 2017 3 No. 28393-A Gaceta Oficial Digital, martes 24 de octubre de 2017 4 N° RUC NOMBRE 200001 1946328-1-730987 PUENTE HOMBRE INC 200002 1404708-1-628668 PUENTE INTEROCEANICO CORP 200003 1254337-1-593980 PUENTE NUEVO S A 200004 557725-1-444493 PUENTE TERRESTRE INTEROCEANICO DE GUATEMALA S A 200005 1736696-1-693515 PUENTECOM S A 200006 1132217-1-567403 PUENTEDEY HOLDING CORP 200007 1925690-1-727154 PUENTES & PAZ S A 200008 1632763-1-672175 PUENTES MARITIMOS LTD INC 200009 644659-1-458767 PUENTES MEDIA SOLUTIONS S A 200010 2240483-1-779636 PUENTES Y COMPONENTES S A 200011 1333660-1-613507 PUENTES Y DRAGADOS DE PANAMA S A 200012 1341869-1-615188 PUERCOMER S A 200013 1427913-1-633491 PUERTA A PUERTA S A 200014 1210710-1-584251 PUERTA DE SAN VICENTE S A 200015 1038922-1-544557 PUERTA NUEVA CO S A 200016 451-484-101603 PUERTA NUEVA, S.A. 200017 1212669-1-584681 PUERTA SUR S A 200018 1459573-1-639647 PUERTA Y PERSINA S A 200019 2565688-1-828585 PUERTAS AL OCEANO S A 200020 1881003-1-719109 PUERTAS BETHEL S A 200021 2507309-1-819820 PUERTAS PORTONES PANAMA S A 200022 2096506-1-756044 PUERTAS Y ACABADOS DEL MUNDO S A 200023 1590203-1-664247 PUERTAS Y VENTANAS CATHERINE S A 200024 865379-1-507913 PUERTO ANTIGUO S A 200025 849599-1-505064 PUERTO ARMUELLES ADVENTURE CORP 200026 2553983-1-826691 PUERTO ARMUELLES CONCEPTS S A 200027 1801676-1-705391 PUERTO AZUL -
Posthumanism, New Materialism and Feminist Media Art
Posthumanism, New Materialism and Feminist Media Art María Fernández Cornell University [email protected] Abstract process of change. Consequently this subjectivity is Some scholars understand the theoretical orientations of chaotic rather than in control, distributed rather than posthumanism and new materialisms to be in tension if not in autonomous and located in consciousness. [4] In more distinct opposition to previous feminisms. This essay explores recent work she posits that in our era, digital technologies select works by two contemporary artists to suggest that are integrated in our daily lives and communications posthumanism and new materialism have antecedents in infrastructure to such a great extent that we have evolved previous feminist media arts. This proposition encourages the recognition of feminist contributions to the history of with them and it is difficult to differentiate human from posthumanist and post anthropocentric art practices. nonhuman agencies. [5] Similarly, the philosopher Rosi Braidotti Introduction associates humanism with a universalizing notion of the subject (white, male, able bodied), and proposes a critical posthumanism with special attention to subjectivity. Her The work of women artists working with technology is critical posthuman subject is relational, constituted in and poorly represented in the art historical record. [1] Even by multiplicity and is simultaneously embodied and today when both digital media and feminism have located, not only geographically, but also affectively become popular, few publications about this art exist. along hierarchies or gender, race and class. Critical The paucity of recognition in the art world posthumanism for her involves interconnections between notwithstanding, new media art by women continuously humans, nonhumans, and the environment as well as the proliferates. -
Construction Manual for Earthquake-Resistant Houses Built Of
Gernot Minke Construction manual for earthquake-resistant houses built of earth Published by GATE - BASIN (Building Advisory Service and Information Network) at GTZ GmbH (Gesellschaft für Technische Zusammenarbeit) P.O.Box 5180 D-65726 Eschborn Tel.: ++49-6196-79-3095 Fax: ++49-6196-79-7352 e-mail: [email protected] Homepage: http://www.gtz.de/basin December 2001 Contents Acknowledgement 4 Introduction 5 1. General aspects of earthquakes 6 1.1 Location, magnitude, intensity 6 1.2 Structural aspects 6 2. Placement of house in the case of 8 slopes 3. Shape of plan 9 4. Typical failures, 11 typical design mistakes 5. Structural design aspects 13 6. Rammed earth walls 14 6.1 General 14 6.2 Stabilization through mass 15 6.3 Stabilization through shape of16 elements 6.4 Internal reinforcement 19 7. Adobe walls 22 7.1 General 22 7.2 Internal reinforcement 24 7.3 Interlocking blocks 26 7.4 Concrete skeleton walls with 27 adobe infill 8. Wattle and daub 28 9. Textile wall elements filled with 30 earth 10. Critical joints and elements 34 10.1 Joints between foundation, 34 plinth and wall 10.2 Ring beams 35 10.3 Ring beams which act as roof support 36 11. Gables 37 12. Roofs 38 12.1 General 38 12.2 Separated roofs 38 13. Openings for doors and windows 41 14. Domes 42 15. Vaults 46 16. Plasters and paints 49 Bibliographic references 50 3 Acknowledgement This manual was first published in Spanish within the context of the research and development project Viviendas sismorresistentes en zonas rurales de los Andes, supported by the German organizations Deutsche Forschungsgemeinschaft, Bonn (DFG), and Deutsche Gesellschaft für Technische Zusammenarbeit (GTZ) GmbH, Eschborn (gtz). -
Análisis De Microhuellas De Uso Mediante Microscopio Electrónico
Revista de Antropología N° 26, 2do Semestre, 2012: 129-150 Análisis de Microhuellas de Uso Mediante Microscopio Electrónico de Barrido (MEB) de Artefactos Óseos de un Sitio Arcaico Tardío del Valle de Mauro (Región de Coquimbo, Chile): Aportes para una Reconstrucción Contextual Use-Wear Analysis Through Scanning Electron Microscope (SEM) of Bone Tools from a Late Archaic Site in the Mauro Valley (Coquimbo Region, Chile): Contributions to a Contextual Reconstruction. Boris Santanderi y Patricio López M.ii Resumen Este trabajo presenta los resultados del análisis mediante Microscopio Electrónico de Barrido (MEB) realizado sobre siete artefactos óseos provenientes del sitio Arcaico Tardío (c.a. 4000-2000 a.p.) MAU085 (31º 57´S – 71º 01´O, Región de Coquimbo, Chile). Este análisis tuvo por objetivos identificar funcionalidades de un conjunto de artefactos óseos diversos y sus relaciones con la variedad de morfologías identificadas. Asimismo, se buscó relacionar los artefactos óseos con las evidencias artefactuales y ecofactuales, específicamente los restos líticos, ya que la hipótesis inicial de la funcionalidad de los artefactos óseos del sitio refiere su uso a herramientas para la talla y reavivado de bordes de puntas de proyectil y artefactos de corte. El análisis mediante Microscopio Electrónico de Barrido indica que los artefactos óseos fueron usados tanto en líticos así como en restos blandos como pieles y fibras textiles ampliando el uso de artefactos tradicionalmente asignados a retocadores. Palabras clave: Microscopio Electrónico de Barrido, Artefactos óseos, Arcaico Tardío, Norte Semiárido, Chile. i Grupo Quaternário e Pré-História do Centro de Geociências (uID 73 - FCT Portugal), Portugal. Programa de Doctorado en Cuaternario y Prehistoria, Universitat Rovira i Virgili, España. -
Interpreting the Architectonics of Power and Memory at the Late Formative Center of Jatanca, Jequetepeque Valley, Peru
University of Kentucky UKnowledge University of Kentucky Doctoral Dissertations Graduate School 2010 INTERPRETING THE ARCHITECTONICS OF POWER AND MEMORY AT THE LATE FORMATIVE CENTER OF JATANCA, JEQUETEPEQUE VALLEY, PERU John P. Warner University of Kentucky, [email protected] Right click to open a feedback form in a new tab to let us know how this document benefits ou.y Recommended Citation Warner, John P., "INTERPRETING THE ARCHITECTONICS OF POWER AND MEMORY AT THE LATE FORMATIVE CENTER OF JATANCA, JEQUETEPEQUE VALLEY, PERU" (2010). University of Kentucky Doctoral Dissertations. 72. https://uknowledge.uky.edu/gradschool_diss/72 This Dissertation is brought to you for free and open access by the Graduate School at UKnowledge. It has been accepted for inclusion in University of Kentucky Doctoral Dissertations by an authorized administrator of UKnowledge. For more information, please contact [email protected]. ABSTRACT OF DISSERTATION John Powell Warner The Graduate School University of Kentucky 2010 INTERPRETING THE ARCHITECTONICS OF POWER AND MEMORY AT THE LATE FORMATIVE CENTER OF JATANCA, JEQUETEPEQUE VALLEY, PERU ____________________________________ ABSTRACT OF DISSERTATION ____________________________________ A dissertation submitted in partial fulfillment of the requirements for the degree of Doctor of Philosophy in the College of Arts and Sciences at the University of Kentucky By John Powell Warner Lexington, Kentucky Co-Directors: Dr. Tom D. Dillehay, Professor of Anthropology and Dr. Chris Pool, Professor of Anthropology Lexington, Kentucky 2010 Copyright © John Powell Warner 2010 ABSTRACT OF DISSERTATION INTERPRETING THE ARCHITECTONICS OF POWER AND MEMORY AT THE LATE FORMATIVE CENTER OF JATANCA, JEQUETEPEQUE VALLEY, PERU This works examines the Late Formative Period site of Jatanca (Je-1023) located on the desert north coast of the Jequetepeque Valley, Peru. -
Earthquake Resistant Housing
EARTHQUAKE RESISTANT HOUSING Adopting the sophisticated building regulations of the developed world in poor countries has done little to prevent poor people's housing from collapsing in earthquakes. There are many ways of making stone and adobe buildings better able to resist earthquakes which are within the reach of people on low incomes. Earthquakes cause a lot of casualties and damage. In the twentieth century alone, they have accounted for around 1.5 million casualties, 90 per cent of which occurred in housing for people with a low income. The economic losses have been staggering as well: they may have exceeded one trillion US dollars. The particular vulnerability of poor people's housing is caused by a number of factors, of which the most important are: Figure 1 - Typical domestic tapial dwelling destroyed by earthquake (Megan Lloyd-Laney) • Poverty, which prevents the use of better materials or skills. It also makes people extend and improve their houses in stages, and in the case of a house that has got off to a bad start it is often hard to improve its earthquake resistance. • A lack of political power, which stops people building on more secure sites or Figure 2 – Earthquake resistant quincha house (Theo gaining assistance. Schilderman) • Scarcity of both appropriate materials and skills for earthquake-resistant construction. • A lack of disaster consciousness in situations where daily survival is a major problem, and where, for example, the removal of subsidies on food is a much greater disaster for poor people than the eventual earthquake. Practical Action, The Schumacher Centre for Technology and Development, Bourton on Dunsmore, Rugby, Warwickshire, CV23 9QZ, UK T +44 (0)1926 634400 | F +44 (0)1926 634401 | E [email protected] | W www.practicalaction.org ___________________________________________________________________________________________________________ Practical Action is a registered charity and company limited by guarantee. -
Structural Health Assessment of Timber Structures
STRUCTURAL HEALTH ASSESSMENT OF TIMBER STRUCTURES Proceedings of the International Conference September 20-22, 2017 Istanbul, Turkey Organized by HASAN KALYONCU UNIVERSITY FACULTY of FINE ARTS and ARCHITECTURE (HKU-GSMF) & YILDIZ TECHNICAL UNIVERSITY RESEARCH CENTER for PRESERVATION of HISTORICAL HERITAGE (TA-MIR) Edited by E. Görün ARUN SHATIS’17 Structural Health Assessment of Timber Structures September 2017 The papers herein are published in the form as submitted by the authors after scientific reviewing. Minor changes have been made where obvious errors and discrepancies were met. Cover Design: Ali Osman Kuruşcu © Hasan Kalyoncu University Havalimanı Yolu 27410 Şahinbey, Gaziantep, Turkey Sponsor: ISBN: 978-605-62703-7-6 Baskı / Printed and Bound: PREFACE The SHATIS International Conference on Structural Health Assessment of Timber Structures is a meeting organized every two years by countries with a rich history in timber structures and an advanced industrial and academic background in the wood sector. After 3 successful conferences in Portugal, Italy and Poland the 4th edition of the SHATIS in 2017 is in Istanbul, Turkey. Timber is a gift of nature offering a lot of benefits mainly as a construction material to build vehicles, ships, dwellings and larger structures since early history. It was also used together with masonry to improve masonry’s structural behavior due to its high tensile strength as compared to masonry. Timber roofs and domes covered architectural spaces with masonry walls. There are diverse applications of timber in all ancient cultures all over the world and Anatolia or Asia Minor, has a very rich heritage in this respect. For example, the 2800-years old Gordion Tumulus near Eskişehir-Ankara, which is still standing, is completely in timber. -
HOUSING REPORT Vivienda De Bahareque
World Housing Encyclopedia an Encyclopedia of Housing Construction in Seismically Active Areas of the World an initiative of Earthquake Engineering Research Institute (EERI) and International Association for Earthquake Engineering (IAEE) HOUSING REPORT Vivienda de Bahareque Report # 141 Report Date 10-08-2007 Country EL SALVADOR Housing Type Timber Building Housing Sub-Type Timber Building : Walls with bamboo/reed mesh and post (Wattle and Daub) Author(s) Dominik Lang, Roberto Merlos, Lisa Holliday, Manuel A. Lopez M. Reviewer(s) Qaisar Ali Important This encyclopedia contains information contributed by various earthquake engineering professionals around the world. All opinions, findings, conclusions & recommendations expressed herein are those of the various participants, and do not necessarily reflect the views of the Earthquake Engineering Research Institute, the International Association for Earthquake Engineering, the Engineering Information Foundation, John A. Martin & Associates, Inc. or the participants' organizations. Summary The bahareque construction type refers to a mixed timber, bamboo and mud wall construction technique which was the most frequently used method for simple houses in El Salvador before the 1965 earthquake (Levin, 1940; Yoshimura and Kuroki, 2001). According to statistics of the Vice-ministry of Housing and Urban Development in the year 1971 bahareque buildings had a share of 33.1 % of all buildings in El Salvador, while in 1994 the percentage of bahareque declined to about 11 % (JSCE, 2001b) and in 2004 to about 5 % (9 % in rural areas; according to Dowling, 2004). The term 'bahareque' (also 'bajareque') has no precise equivalent in English, however in some Latin American countries this construction type is known as 'quincha' (engl.: wattle and daub).