Explosion Shock Waves and High Strain Rate Phenomena
Total Page:16
File Type:pdf, Size:1020Kb
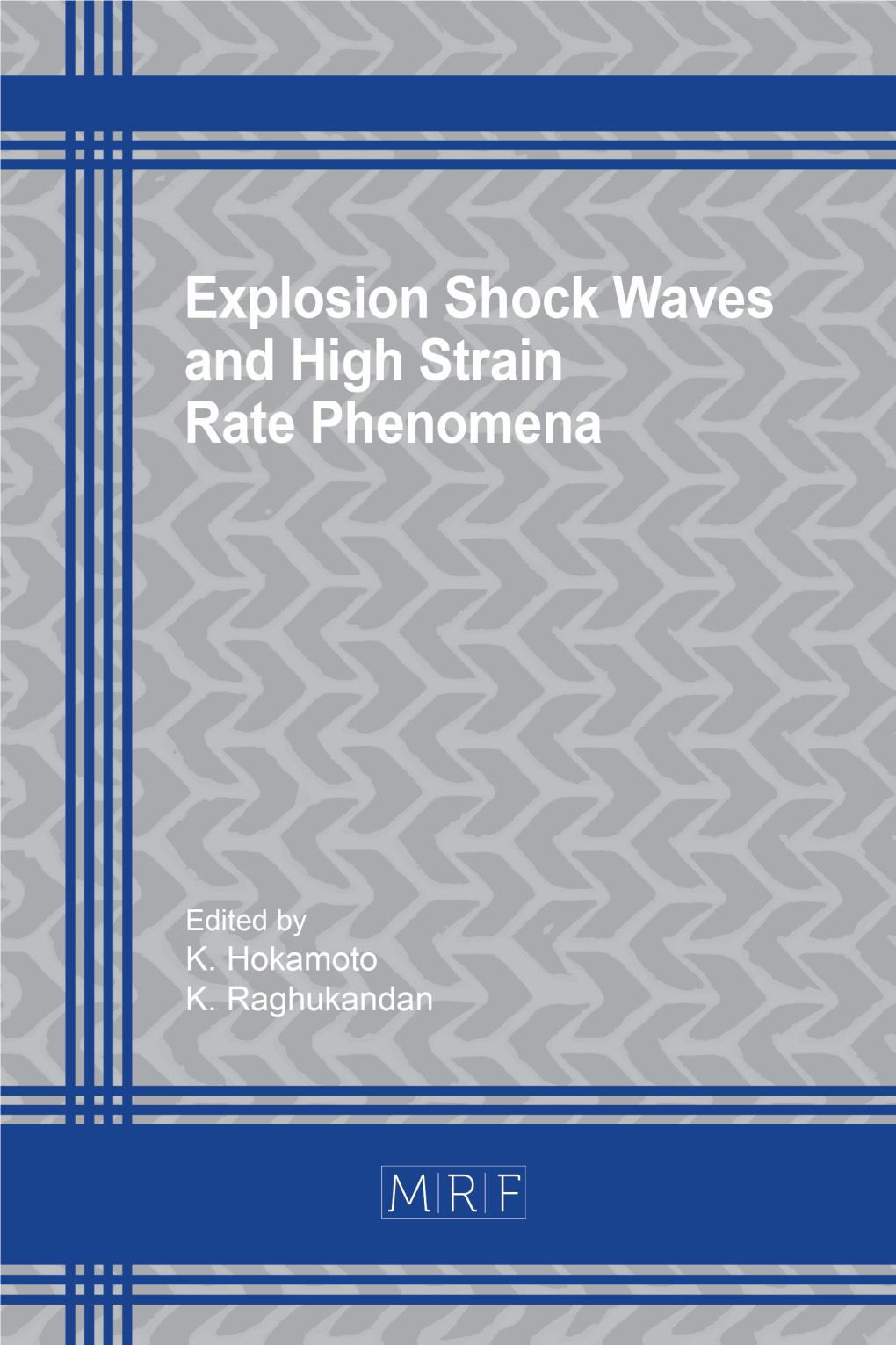
Load more
Recommended publications
-
Nuclear Weapons FAQ (NWFAQ) Organization Back to Main Index
Nuclear Weapons FAQ (NWFAQ) Organization Back to Main Index This is a complete listing of the decimally numbered headings of the Nuclear Weapons Frequently Asked Questions, which provides a comprehensive view of the organization and contents of the document. Index 1.0 Types of Nuclear Weapons 1.1 Terminology 1.2 U.S. Nuclear Test Names 1.3 Units of Measurement 1.4 Pure Fission Weapons 1.5 Combined Fission/Fusion Weapons 1.5.1 Boosted Fission Weapons 1.5.2 Staged Radiation Implosion Weapons 1.5.3 The Alarm Clock/Sloika (Layer Cake) Design 1.5.4 Neutron Bombs 1.6 Cobalt Bombs 2.0 Introduction to Nuclear Weapon Physics and Design 2.1 Fission Weapon Physics 2.1.1 The Nature Of The Fission Process 2.1.2 Criticality 2.1.3 Time Scale of the Fission Reaction 2.1.4 Basic Principles of Fission Weapon Design 2.1.4.1 Assembly Techniques - Achieving Supercriticality 2.1.4.1.1 Implosion Assembly 2.1.4.1.2 Gun Assembly 2.1.4.2 Initiating Fission 2.1.4.3 Preventing Disassembly and Increasing Efficiency 2.2 Fusion Weapon Physics 2.2.1 Candidate Fusion Reactions 2.2.2 Basic Principles of Fusion Weapon Design 2.2.2.1 Designs Using the Deuterium+Tritium Reaction 2.2.2.2 Designs Using Other Fuels 3.0 Matter, Energy, and Radiation Hydrodynamics 3.1 Thermodynamics and the Properties of Gases 3.1.1 Kinetic Theory of Gases 3.1.2 Heat, Entropy, and Adiabatic Compression 3.1.3 Thermodynamic Equilibrium and Equipartition 3.1.4 Relaxation 3.1.5 The Maxwell-Boltzmann Distribution Law 3.1.6 Specific Heats and the Thermodynamic Exponent 3.1.7 Properties of Blackbody -
Cranfield University the Development of a Laser
CRANFIELD UNIVERSITY THE DEVELOPMENT OF A LASER DETONATOR SYSTEM DEFENCE COLLEGE OF MANAGEMENT AND TECHNOLOGY PhD THESIS MIKE BOWDEN CRANFIELD UNIVERSITY DEFENCE COLLEGE OF MANAGEMENT AND TECHNOLOGY DEPARTMENT OF MATERIALS AND APPLIED SCIENCES PhD THESIS Mike Bowden The Development of a Laser Detonator System Supervisor: Professor J Akhavan Industrial Supervisor: Dr R. C. Drake January 2014 © Crown Copyright 2014. All rights reserved. No part of this publication may be reproduced without the written permission of the copyright holder. ABSTRACT Laser detonators offer several advantages over traditional electrical detonators, such as exploding bridgewire and slapper detonators, in terms of both safety and performance. Laser detonators remove the electrical conduction path to the energetic material, providing immunity from threats such as electrostatic discharge and lightning. A larger separation between the initiating energy source and the explosive devices is possible, up to several tens of metres, compared to a few metres for electrical slapper detonators. A laser detonator system has been developed, with laser-driven flyer plates used to shock initiate the explosive. All aspects of the system, including coupling into an optical fibre, used to transmit the laser energy to the detonator, the optical fibre, the flyer plate launch and acceleration and subsquent shock into the explosive, and the explosive initiation have been investigated, with an understanding of the underlying principles and processes developed. Shock initiation of two secondary explosives, hexanitrostilbene and pentaerythritol tetranitrate, has been studied at extremely high shock pressures, comparable to the detonation pressure, and the critical energy fluence required for initiation establised. The laser detonator system is robust and optimised, with design tools developed to enable efficient design of future systems. -
Australian Official Journal Of
Vol: 34 , No: 47 26 November 2020 AUSTRALIAN OFFICIAL JOURNAL OF PATENTS The Australian Official Journal of Patents is part of the Official Journal issued by the Commissioner of Patents for the purpose of the Patents Act 1990, the Trade Marks Act 1995 and the Designs Act 2003. (ISSN 0819-1794) AUSTRALIAN OFFICIAL JOURNAL OF PATENTS 26 November 2020 Contents General Information & Notices Amendments Applications for Amendment ...................................................................................... 6674 Amendments Made ...................................................................................................... 6674 Alteration of Name(s) of Applicant(s)/Patentee(s) .................................................... 6676 Amendments Made Under Section 105 ......................................................................6677 Applications Accepted Name Index ................................................................................................................... 6794 Numerical Index ............................................................................................................6826 IPC Index .......................................................................................................................6829 Applications with amended filing dates Reg 3.5(A). ................... 6669 Applications Lapsed, Refused or Withdrawn, Patents Ceased or Expired ........................................................... 6670 Applications Open to Public Inspection Name Index .................................................................................................................. -
Kinetics of Materials at Extreme Conditions: Understanding the Time Dependent Approach to Equilibrium at Marie
LLNL-TR-729606 L L NKinetics of Materials at L - XExtreme Conditions: X XUnderstanding the Time X - XDependent Approach to X X XEquilibrium at MaRIE X Unclassified April 21, 2017 Richard Kraus, Dennis Mcnabb, Mukul Kumar, Jon Eggert, John Borg, Ellen Cerreta, Dana Dattelbaum, Larry Fried, Carl Greeff, James Stolken Kinetics of Materials at Extreme Conditions: Understanding the Time Dependent Approach to Equilibrium at MaRIE Disclaimer This document was prepared as an account of work sponsored by an agency of the United States government. Neither the United States government nor Lawrence Livermore National Security, LLC, nor any of their employees makes any warranty, expressed or implied, or assumes any legal liability or responsibility for the accuracy, completeness, or usefulness of any information, apparatus, product, or process disclosed, or represents that its use would not infringe privately owned rights. Reference herein to any specific commercial product, process, or service by trade name, trademark, manufacturer, or otherwise does not necessarily constitute or imply its endorsement, recommendation, or favoring by the United States government or Lawrence Livermore National Security, LLC. The views and opinions of authors expressed herein do not necessarily state or reflect those of the United States government or Lawrence Livermore National Security, LLC, and shall not be used for advertising or product endorsement purposes. Lawrence Livermore National Laboratory is operated by Lawrence Livermore National Security, LLC, for the U.S. Department of Energy, National Nuclear Security Administration under Contract DE-AC52- 07NA27344. Lawrence Livermore National Laboratory Unclassified ii Kinetics of Materials at Extreme Conditions: Understanding the Time Dependent Approach to Equilibrium at MaRIE Table of Contents Section 1. -
THE ROCKETEER Receives Award 8 THURSDAY, MAY 29, 1997 NAVAL AIR WARFARE CENTER WEAPONS Dtvlsion CHINA Lake Voc 53, No
16 T HE R OCKETEER May 29, 1997 Bill ......F811ile¥11Ml ""P----------4 his retirement Frank Markarian THE ROCKETEER receives award 8 THURSDAY, MAY 29, 1997 NAVAL AIR WARFARE CENTER WEAPONS DtVlSION CHINA lAKE Voc 53, No. 11 Division's ranges expand tracking capabilities MAC SPECIALS GREAT STARTERS! DVDSYSTEMS week, with system utilization increasing as additional forth to cover surges in testing. Logistic support of the By Derwin " DEX" Hansard programs request GPS-based TSPI." system is greatly reduced due to the standardization on GPS Ra"9El Applications Program Syslems Eng1neer DV-500 ARDS is a tri-service Central Test And Evaluation Department of Defense T &E ranges. PowerMac 7300 180 K5133 16MB/1GB 12xCD PI 0 NEER ccording to Navy GPS Program Manager for Investment Programllmprovement and Modernization ARDS is a differentially corrected precision code • 1801\IHz Processor • K5 133 Processor 512K & MotherBoard Features: Range Applications Program Dick Dickson, pro Procurement, and is currently in use at II Army, Navy GPS-based tracking system which can support multiple • 16MB RAM .....;, 4.,~~<:"-'fl»:~ • 1GB Hard Drive • Multiple Story Endings viding range customers with quality global posi and Air Force test and evaluation ranges across the simultaneous test operations. It can simultaneously sup • 2GB Hard Drive • 1MB PCI Video Card "' A • 12xCD ROM • 15" .28 Nl Color Monitor • Multiple Aspect Rat1os ~ tioning system (GPS)-based time space position infor United States. "lnteroperability between services was a port a total of 25 participants, providing precision 1OHz Super Power for Business! • 104 Windows 95 Keyboard • Mult.,le Angles mation (TSPI) and altitude data is a primary goal of the primary driver for this system," said Ron Smith, Sea TSPI throughout NAWCWPNS air space using a time • Windows 95 • Mouse • Parental Lock Range GPS project manager for RAP. -
Propagation of Axially Symmetric Detonation Waves*
Propagation of Axially Symmetric Detonation Waves* Robert L. Druce, Franklin Roeske, Jr., P. Clark Souers, Craig M. Tarver, Charles T. S. Chow, Ronald S. Lee, Estella M. McGuire, George E. Overturf III and Peter A. Vitello Lawrence Livermore National Laboratory Livermore, CA 94550 We have studied the non-ideal propagation of detonation waves in LX-10 and in the insensitive explosive TATB. Explosively-driven, 5.8-mm-diameter, 0.125-mm-thick aluminum flyer plates were used to initiate 38-mm-diameter, hemispherical samples of LX-10 pressed to a density of 1.86 g/cm3 and of TATB at a density of 1.80 g/cm3. The TATB powder was a grade called ultrafine (UFTATB), having an arithmetic mean particle diameter of about 8-10 µm and a specific surface area of about 4.5 m2/g. Using PMMA as a transducer, output pressure was measured at 5 discrete points on the booster using a Fabry-Perot velocimeter. Breakout time was measured on a line across the booster with a streak camera. Each of the experimental geometries was calculated using the Ignition and Growth Reactive Flow Model, the JWL++ Model and the Programmed Burn Model. Boosters at both ambient and cold (-20 °C and –54 °C) temperatures have been experimentally and computationally studied. A comparison of experimental and modeling results is presented. INTRODUCTION hemisphere of UFTATB with an average density of 3 The properties of non-ideal explosives 1.80+0.005 g/cm . The boosters are formed by sometimes make them more difficult to utilize, but uniaxially compacting a known mass of UFTATB 2 these same properties greatly reduce the chance of powder (8 µm mean particle size, 4.5 m /g specific unintended reaction or detonation, both in surface area) into a hemispherical die of known utilization and in storage. -
An Expanding Role for AGEX: Above-Ground Experiments For
An Expanding Role for AGEX Above-Ground Experiments for Nuclear Weapons Physics Philip D. Goldstone Procyon, the high-explosive pulsed-power generator at Los Alamos or the last fifty years U.S. ex- Imagine, twenty years from now, a bilities of others), if we are without pertise in nuclear-weapons de- military commander or a member of any fully integrated nuclear tests and Fsign and engineering was a nat- a stockpile-surveillance team notic- without ongoing development pro- ural by-product of an active develop- ing that one of the weapons being grams. It will be necessary, but not ment and testing program. With the stored has changed in appearance. sufficient, for the scientists and engi- end of the cold war, the development They will want to know, “is this still neers involved in this enterprise to of agreements to retire most of the safe, and would it work if needed?” do research; the research itself must U.S. and former Soviet weapon stock- They will call the Laboratory and stress their judgement in weapons piles, and plans to phase out U.S. nu- ask the experts regarding this science and engineering. Further- clear testing by 1996, the way the nu- weapon. Will they be able to rely on more, to prevent losing capability clear weapons program has operated the answer they get? A competent within a generation, these research is changing dramatically. However, technical capability—including the programs must be technically inter- nuclear weapons will remain a pres- honed expertise and judgement of esting to attract and train new scien- ence in the world for the foreseeable weapon designers and engineers—is tists and engineers. -
AGEX I: the Explosives Regime of Weapons Physics
AGEX I the explosives regime of weapons physics Timothy R. Neal he history of explosives re- hitherto not contemplated. The such as triaminotrinitrobenzene search and above-ground ex- achievement of those goals left Los (TATB)—can be dropped from great Tperimentation for nuclear Alamos, at the end of World War II, heights and will shatter but not ex- weapons began with the Manhattan uniquely in possession of the most plode. If exposed to fire in an acci- Project. During the hectic, almost advanced explosive-fabrication tech- dent, TATB will burn, but it is ex- frantic, war days at Los Alamos, it nology on earth and a mission to tremely unlikely to undergo a transi- became clear that, if possible, the fis- make nuclear weapons safer and tion from burning to deflagration or sionable material in the weapon more efficient—a mission that has detonation. Even when exposed to should be plutonium. It was equally continued into the present. high temperature, extreme pressures, apparent that the critical mass of plu- For a long period of time, the or shocks, these materials resist ex- tonium needed to produce a nuclear work on weapons implosions has plosion. Thus, they can be handled explosion would have to be assem- utilized conventional plastic-bonded quite safely with simple precautions. bled in the weapon through a spheri- high explosives, which could be pre- In addition to safety, the stability cal implosion driven by powerful ex- cisely machined. Improvements and reliability of nuclear weapons in plosives (Figure 1). Thus from the were continually made to increase the nation’s stockpile have been on- beginning the development of nuclear the accident resistance of these ma- going concerns. -
Explosives Safety
MEASUREMENT SENSITIVE DOE-STD-1212-2012 June 2012 DOE STANDARD EXPLOSIVES SAFETY U.S. Department of Energy AREA SAFT Washington, DC 20585 DISTRIBUTION STATEMENT A. Approved for public release; distribution is unlimited. DOE-STD-1212-2012 TABLE OF CONTENTS CHAPTER I. PURPOSE, SCOPE and APPLICABILITY, EXEMPTIONS, WAIVERS, ABBREVIATIONS, ACRONYMS, AND DEFINITIONS .......... 1 1.0. PURPOSE ............................................................................................................. 1 1.1. Scope and Applicability.............................................................................. 1 2.0. STANDARD ADMINISTRATION AND MANAGEMENT ...................................... 3 3.0. EXEMPTIONS ....................................................................................................... 4 3.1. Exemption Requests .................................................................................. 4 3.2. Exemptions Achieving Equivalent Safety .................................................. 4 3.3. Exemptions Not Achieving Equivalent Safety ............................................ 4 4.0. WAIVERS .............................................................................................................. 6 4.1. Documentation of a Waiver ....................................................................... 6 5.0. AUTHORITY HAVING JURISDICTION ................................................................ 7 6.0. LIST OF MEASUREMENT ABBREVIATIONS ..................................................... 8 7.0. ACRONYMS -
Submitted To. SEISMIC SOURCE Ray Engelke and Robert 0. Hedges
Title: CHEMICAL ENERGY SYSTEM FOR A BOREFIOLE SEISMIC SOURCE Author(s): Ray Engelke and Robert 0. Hedges Submitted to. Los Alamos National Laboratory. an affirmative actionlequal opportunity employer. is operated by the University of California for the US. Oepartment of Energy under contract W-7405-ENG-36. By acceptance of this article. the publisher recognizes that the U.S. Government retains a nonexclusive. royalty-free license 10 publish or reproduce the published form of this contnbution. or lo allow others to do so. for U.S. Government purposes. The Los Alamos National Laboratory identify this article as work performed under the auspices of the US. Department of Energy. Form No. 836 A5 ST2629 la91 1 CHEMICAL ENERGY SYSTEM FOR A BOREHOLE SEISMIC SOURCE Ray Engelke (DX-IO) and Robert 0. Hedges (EES-4) Los Alamos National Laboratory, Los Alamos, N. M., 87544 Abstract We describe a detonation system that will be useful in the seismological examination of geological structures. The explosive component of this system is produced by the mixing of two liquids; these liquids are classified as non-explosive materials by the Department of Transportation. This detonation system could be employed in a borehole tool in which many explosions are made to occur at various points in the borehole. The explosive for each explosion would be mixed within the tool immediately prior to its being fired. Such an arrangement ensures that no humans are ever in proximity to explosives. Initiation of the explosive mixture is achieved with an electrical slapper detonator whose specific parameters are described; this electrical initiation system does not contain any explosive. -
National Nuclear Security Administration FY 2013 PEP
National Nuclear Security Administration FY 2013 PEP Lawrence Livermore National Security, LLC Performance Evaluation Report Livermore Field Office Lawrence Livermore National Laboratory Performance Period: October 2012 – September 2013 November 22, 2013 NNSA Corporate CPEP Process NNSA Lawrence Livermore National Security, LLC PER NNSA/NA-00.2 Livermore Field Office November 22, 2013 Executive Summary This report was produced by the Department of Energy/National Nuclear Security Administration (DOE/NNSA), Livermore Field Office (LFO) in accordance with guidance from the NNSA Office of Infrastructure and Operations (NA-00). The purpose of this report is to provide the NNSA Fee Determination Official (FDO) with an evaluation of the Contractor’s performance for all Performance Incentive requirements under contract DE-AC52-07NA27344 against the NNSA Strategic PEP. The Strategic PEP provides the expectations to evaluate the M&O Contractor’s performance and promotes a performance-based framework based on results tempered by prudent management of risk, accountability, and renewed trust. The evaluation period for this report is from October 1, 2012 through September 30, 2013. The Performance Evaluation Report (PER) is a collaboration of input from all elements of NNSA, including HQ Program Offices. The scope includes adjectival ratings for each of the Performance Objectives (POs) based on performance against Contributing Factors, Site Specific Outcomes, and other criteria as set forth in the Strategic PEP. No recommendations on award fee or award term are provided in accordance with guidance. Adjectival ratings are set forth and defined in Federal Acquisition Regulation (FAR) Subpart 16.4, Table 16-1. It is noted that the evaluation of performance considers unanticipated barriers (e.g., budget restrictions, rule changes, circumstances outside Contractor’s control), accomplishments, and other events in accordance with the Strategic PEP. -
51) International Patent Classification: (71) Applicant: LAWRENCE LIVERMORE NATIONAL F42B 3/12 (2006.0 1) F42B 3/13 (2006.0 1
( 2 (51) International Patent Classification: (71) Applicant: LAWRENCE LIVERMORE NATIONAL F42B 3/12 (2006.0 1) F42B 3/13 (2006.0 1) SECURITY, LLC [US/US]; 7000 East Avenue, P.O. Box 808, L-703, Livermore, California 94550-9234 (US). (21) International Application Number: PCT/US20 19/032536 (72) Inventors: WEST, Connor M.; 15 Meritage Common, Apt 201, Livermore, California 94551 (US). LE, Dat Q.; 5867 (22) International Filing Date: Woodrose Way, Livermore, California 9455 1 (US). 15 May 2019 (15.05.2019) (74) Agent: GALLENSON, Mavis et al.; 4525 Wilshire Boule¬ (25) Filing Language: English vard, Suite 240, Los Angeles, California 90010 (US). (26) Publication Language: English (81) Designated States (unless otherwise indicated, for every (30) Priority Data: kind of national protection av ailable) . AE, AG, AL, AM, 15/982,580 17 May 2018 (17.05.2018) US AO, AT, AU, AZ, BA, BB, BG, BH, BN, BR, BW, BY, BZ, CA, CH, CL, CN, CO, CR, CU, CZ, DE, DJ, DK, DM, DO, (63) Related by continuation (CON) or continuation-in-part DZ, EC, EE, EG, ES, FI, GB, GD, GE, GH, GM, GT, HN, (CIP) to earlier application: HR, HU, ID, IL, IN, IR, IS, JO, JP, KE, KG, KH, KN, KP, US 15/982,580 (CON) KR, KW, KZ, LA, LC, LK, LR, LS, LU, LY, MA, MD, ME, Filed on 17 May 2018 (17.05.2018) MG, MK, MN, MW, MX, MY, MZ, NA, NG, NI, NO, NZ, OM, PA, PE, PG, PH, PL, PT, QA, RO, RS, RU, RW, SA, (54) Title: CHIP SLAPPER DETONATOR (57) Abstract: A method of making a low cost chip slapper detonator includes the steps of: providing a substrate having a substrate top and a substrate bottom;