Delayed Coker Unit
Total Page:16
File Type:pdf, Size:1020Kb
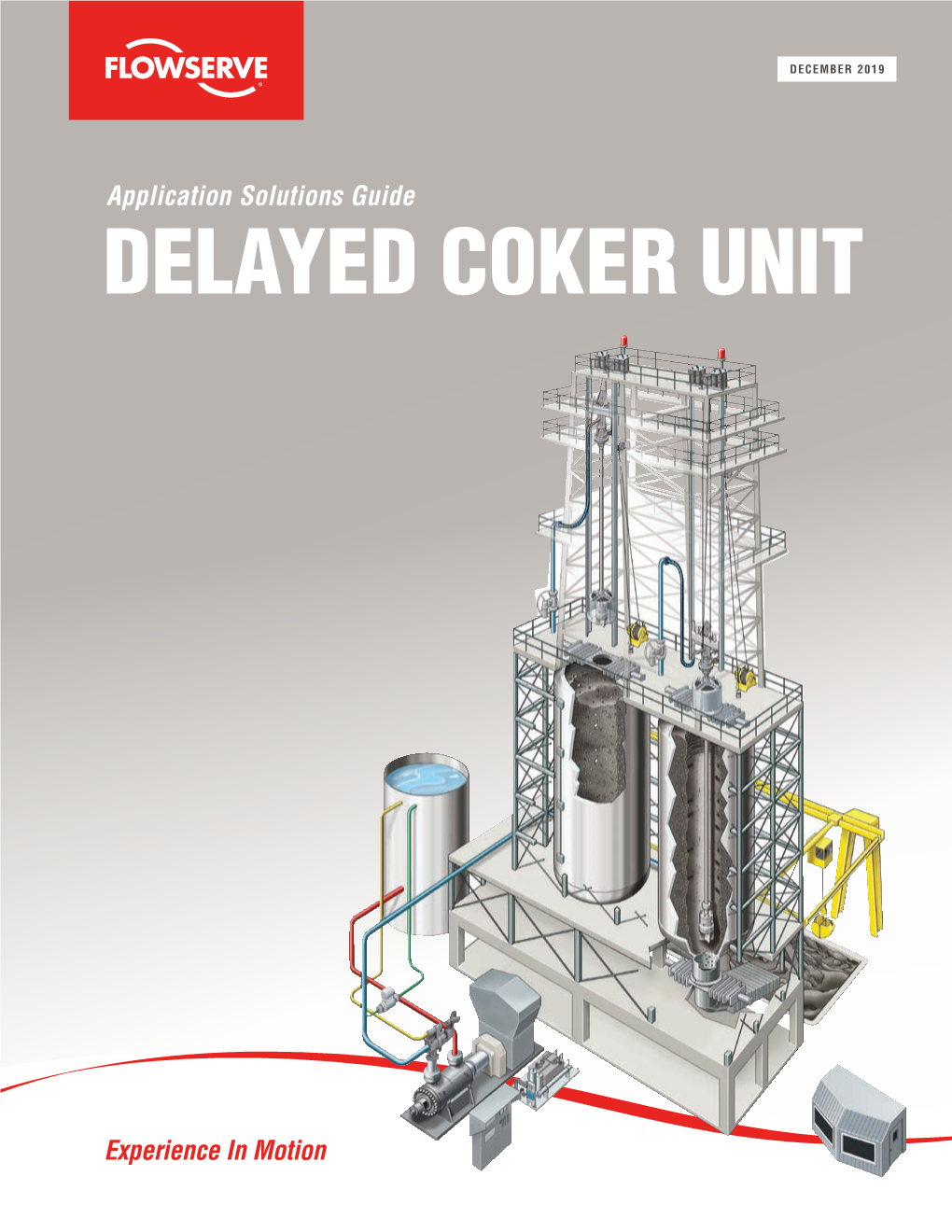
Load more
Recommended publications
-
Converting Visbreakers to Delayed Cokers - an Opportunity for European Refiners
Converting Visbreakers to Delayed Cokers - An Opportunity for European Refiners European Coking.com Conference Sept. 30 - Oct. 2, 2008 Alex Broerse Lummus Technology a CB&I company © Lummus Technology Overview Introduction Delayed Coking Delayed Coking vs. Visbreaking Case Study Conclusions © Lummus Technology Converting Visbreakers to Delayed Cokers - 2 Fuel Oil Market General trend: reduction of sulfur content in fuel oil Typically 1.0-1.5 wt% S International Maritime Organization introduced SOx Emission Control Areas: . Sulfur content of fuel oil on board ships < 1.5 wt% . 1st SECA: Baltic Sea (effective 2006) . North Sea end of 2007 . More to follow Similar trend in other fuel oil application areas End of bunker fuel oil as sulfur sink? © Lummus Technology Converting Visbreakers to Delayed Cokers - 3 European Fuels Market Increased demand for ULS diesel Gradually decreasing fuel oil market Price gap between low sulfur crudes and opportunity crudes Re-evaluation of bottom-of-the-barrel strategy maximize diesel and minimize/eliminate fuel oil production What are the options? © Lummus Technology Converting Visbreakers to Delayed Cokers - 4 Bottom-of-the-Barrel Conversion Technologies Non Catalytic Catalytic Delayed coking Atm. / vac. resid hydrotreating Fluid / flexicoking Ebullated bed hydrocracking Gasification Resid FCC © Lummus Technology Converting Visbreakers to Delayed Cokers - 5 Lummus Capabilities for Bottom-of-the-Barrel Lummus Technology – Houston Delayed coking Resid FCC Chevron Lummus Global JV – Bloomfield Atmospheric/vacuum residue hydrotreating LC-FINING ebullated bed hydrocracking Lummus Technology – Bloomfield / The Hague Refinery planning studies (e.g., grassroots, revamps, processing of opportunity crudes) © Lummus TechnologyExtensive experience in heavy crude upgrade Converting Visbreakers to Delayed Cokers - 6 scenarios Overview Introduction Delayed Coking Delayed Coking vs. -
Upgrading of Coker Distillate Under Variable Hydrotreating Operating Conditions
View metadata, citation and similar papers at core.ac.uk brought to you by CORE provided by Elsevier - Publisher Connector Egyptian Journal of Petroleum (2011) 20, 25–31 Egyptian Petroleum Research Institute Egyptian Journal of Petroleum www.elsevier.com/locate/egyjp www.sciencedirect.com Upgrading of coker distillate under variable hydrotreating operating conditions H.A. Elsayed *, H.S. Ahmed, M.F. Monufy Refining Department, Egyptian Research Institute, Nasr City, Cairo, Egypt Received 28 February 2010; accepted 2 January 2011 Available online 19 October 2011 KEYWORDS Abstract Studies on hydrotreating coker distillates, produced from a delayed coker unit were done Hydrotreating; using a commercially available CoMo/c-Al2O3 catalyst, on which 0.2 wt% P2O5 was added in order Hydrotreating catalyst; to improve its characteristics. The experimental studies were conducted in a fixed-bed continuous- Coker distillate; reactor (cata-test unit) at temperatures (300–400 °C) and total hydrogen pressure (40–65 bar). These Hydrodesulfurization conditions have affected the feedstock characteristics and great reduction of sulfur, aromatics and boiling ranges. Other improvements were obtained in diesel index (DI) due to hydrogenation reac- tion of aromatics and desulfurization of its sulfur contents. ª 2011 Egyptian Petroleum Research Institute. Production and hosting by Elsevier B.V. Open access under CC BY-NC-ND license. 1. Introduction in fuels and gas oil or diesel to <0.01 wt%. The removal of sulfur containing compounds, such as thiophenes, mercaptans, In recent years, sulfur reduction from light gas oil or diesel fuel dibenzothiophene and especially its alkyl substituted deriva- using catalytic hydrodesulfurization (HDS) is a routine opera- tives is necessary in order to minimize the polluting effects of tion in petroleum refining process due to environmental regu- containing gases such as SO2 that may be released into the lations and to improve the combustion qualities of automotive atmosphere during combustion [1]. -
Residuum Processing
CHAPTER SIX Residuum Processing DELAYED COKING Delayed coking is a thermal process in which the vacuum residue from crude distillation is heated in a furnace then confined in a reaction zone or coke drum under proper operating conditions of temperature and pressure until the unvaporized portion of the furnace effluent is converted to vapor and coke. Delayed coking is an endothermic reaction, with the furnace supplying the necessary heat for the coking reactions. The reactions in the delayed coking are complex. In the initial phase, the feed is partially vaporized and cracked as it passes through the furnace. In the next step, cracking of the vapor occurs as it passes through the drum. In the final step, succes- sive cracking and polymerization of the liquid confined in the drum takes place at high temperatures, until the liquid is converted into vapor and coke. The coke produced in the delayed coker is almost pure carbon contain- ing some of the impurities of the feed, such as sulfur and metals. THE DELAYED COKING PROCESS The reduced crude or vacuum resid enters the coke fractionator bottom surge zone (see Figure 6-1). The feed is mixed with recycle condensed in the bottom section of the fractionator and pumped by heater charge pump P-04 through coke heater H-Ol, where the charge is rapidly heated to the desired temperature for coke formation in the coke drums. Steam is injected in each heater coil to maintain the required minimum velocity and residence time and suppress the formation of coke in the heater coils. BLOWDOWN CONDENSER BLOWDOWN SETTLING DRUM V-05 E-02 TO FLARE BLOWDOWN DECOKING WATER BLOWDOWN WATER SLOP OIL STORAGETANK CIRCULATION PUMP PUMP T-01 P-08 OIL COOLER P-09 SLOP OIL E-01 COKER RAW WATER BLOWDOW^ DRUM V-04 COKER GAS FRACTIONATOR N. -
Environmental, Health, and Safety Guidelines for Petroleum Refining
ENVIRONMENTAL, HEALTH, AND SAFETY GUIDELINES PETROLEUM REFINING November 17, 2016 ENVIRONMENTAL, HEALTH, AND SAFETY GUIDELINES FOR PETROLEUM REFINING INTRODUCTION 1. The Environmental, Health, and Safety (EHS) Guidelines are technical reference documents with general and industry-specific examples of Good International Industry Practice (GIIP).1 When one or more members of the World Bank Group are involved in a project, these EHS Guidelines are applied as required by their respective policies and standards. These industry sector EHS Guidelines are designed to be used together with the General EHS Guidelines document, which provides guidance to users on common EHS issues potentially applicable to all industry sectors. For complex projects, use of multiple industry sector guidelines may be necessary. A complete list of industry sector guidelines can be found at: www.ifc.org/ehsguidelines. 2. The EHS Guidelines contain the performance levels and measures that are generally considered to be achievable in new facilities by existing technology at reasonable costs. Application of the EHS Guidelines to existing facilities may involve the establishment of site-specific targets, with an appropriate timetable for achieving them. 3. The applicability of the EHS Guidelines should be tailored to the hazards and risks established for each project on the basis of the results of an environmental assessment in which site-specific variables— such as host country context, assimilative capacity of the environment, and other project factors—are taken into account. The applicability of specific technical recommendations should be based on the professional opinion of qualified and experienced persons. 4. When host country regulations differ from the levels and measures presented in the EHS Guidelines, projects are expected to achieve whichever is more stringent. -
Tutorial: Delayed Coking Fundamentals
Tutorial: Delayed Coking Fundamentals Paul J. Ellis Christopher A. Paul Great Lakes Carbon Corporation Port Arthur, TX Prepared for presentation at the AIChE 1998 Spring National Meeting New Orleans, LA March 8-12, 1998 Topical Conference on Refinery Processing Tutorial Session: Delayed Coking Paper 29a Copyright 1998 Great Lakes Carbon Corporation UNPUBLISHED March 9, 1998 1 ABSTRACT Great Lakes Carbon Corporation has worked closely with refineries producing delayed coke in all forms, fuel grade (shot or sponge), anode grade (sponge), and electrode grade (needle) since start-up of the company's first calcining operation in 1937. With on-going research in the area of delayed coking since 1942, Great Lakes Carbon (GLC) has operated delayed coking pilot units including an excellent large-scale pilot unit with a coke drum 0.3 meter (1 ft) diameter by 2.1 meters (7 ft) long and has developed physical models which explain coke formation in coke drums. Knowledge of commercial delayed coking units as well as that of the GLC Pilot Delayed Coker is used in this tutorial paper to describe the formation and uses of the three types of structures of delayed petroleum coke: needle, sponge, and shot. Troubleshooting tips are included on many aspects of the delayed coking drum cycle including: steam stripping, water quenching, coke cutting, drum warm-up, and drum switching technique. Suggestions and descriptions of delayed coking unit hardware are included. The objective of this tutorial paper is to acquaint the non-refinery technologist and further the knowledge of refinery personnel with the delayed coking operation, delayed coking unit hardware, types of coke that can be produced, coke formation models, and the uses of petroleum coke. -
Delayed Coking of South African Petroleum Heavy Residues for the Production of Anode Grade Coke and Automotive Fuels
DELAYED COKING OF SOUTH AFRICAN PETROLEUM HEAVY RESIDUES FOR THE PRODUCTION OF ANODE GRADE COKE AND AUTOMOTIVE FUELS John Graham Clark A dissertation submitted to the Faculty of Engineering and the Built Environment, University of the Witwatersrand, in fulfilment of the requirements for the degree of Master of Science in Engineering Johannesburg, 2008 2 DECLARATION I declare that this dissertation is my own unaided work. It is being submitted to the Degree of Master of Science in Engineering to the University of the Witwatersrand, Johannesburg. It has not been submitted before for any degree or examination to any other University ……………………………………………… (Signature of Candidate) ………………. day of …………………… year…………… (day) (month) (year) 3 ABSTRACT A laboratory scale delayed coking process was used to produce petrol precursors, diesel precursors, methane rich gas, green and calcined coke from five previously untested South African heavy petroleum residues. The ash content of the heavy petroleum residues was found to be detrimental to the microstructure of the green coke and Coefficient of Thermal Expansion (CTE) of the calcined coke. The sulphur content of the calcined cokes produced was found to be in-line with typical global anode grade cokes. De-ashing of the feedstock would be necessary to produce anode grade fillers for the aluminium industry. The local production of anode grade coke would serve to reduce imports and supply the aluminium smelters on the east coast of South Africa. The heavy petroleum residues (also known as heavy fuel oil) are currently used as bunker fuel in the shipping industry and are responsible for substantial air pollution. Delayed coking of these residues could extend the production of petrol and diesel per barrel of imported crude oil and reduce the effect on South Africa’s balance of payments deficit and impact the environment in a beneficial manner with respect to carbon dioxide and sulphur emissions. -
Coker Distillate(S)
STUDY ON HYDROTREATING OF COKER DISTILLATE(S) Mohamed F. Menoufy', Galal M. Abdel- Aleim2,MohamedS. Ebrahim and Mohamed Abdel-Aaty 1. Petroleum Refining Division, Egyptian Petroleum Research Institute, NasrCity.Cairo, Egypt 2. Petrochemicals and Refining Engineering Dcpt, Faculty of Petroleum Engineering and Mining, Suez canal University, Suez-Egypt. 3. Suez Oil Processing Company 4. Chemist, Nasr Petroleum Company. ABSTRACT The primary method to remove sulfur , improve cetane index and reduce aromatic content of gas oil / diesel is hydroprocessing. Therefore, the significant advancements in hydrotreating of light coker gas oil (LCGO) derived from delayed coker unit at Suez Oil Processing Company have been performed in a cata-test fixed bed micro-reactor unit, using a commercial CoMo/AljOj Catalyst after sulfidation. The operating conditions were varied in order to study the impact of these processes conditions (temperature;275-400"C, hydrogen pressure;30-85 bar, and hourly space velocity; 0.5-1.5h"' ) on the yield , and quality of gas oil within hydrotreating regime, which is the important to aid the optimization of the process from the environmental regulations and national market demands point of view. The present investigation is conducted on the LCGO, which was selected as a hydrotreated feedstock due to its higher unsaturated hydrocarbon contents ( aromatics and olefins) and heteroatom (sulfur and nitrogen), in order to produce an upgraded gas oil acceptable as transportation fuel according to the TESCE, Vol. 30, No.2 <s^ >' December 2004 environmental and national regulations, and / or the world wide fuel charter December 2002. 1-INTRODUCTION In recent years, the development and use" of "environmentally friendly" fuels has had high priority throughout the world. -
Petroleum Residue Upgrading Via Delayed Coking: a Review
Petroleum Residue Upgrading Via Delayed Coking: A Review Ashish N. Sawarkar, Aniruddha B. Pandit, Shriniwas D. Samant and Jyeshtharaj B. Joshi* Institute of Chemical Technology, University of Mumbai, N. P. Marg, Matunga, Mumbai, Maharashtra, 400019, India World petroleum residue processing capacity has reached about 725 million metric tons per annum (MMTPA). The high demand for transportation fuels and the ever-rising heavy nature of crude oil have resulted in a renewed interest in the bottom-of-the-barrel processing using various conver- sion processes. Delayed coking, known for processing virtually any refi nery stream (which not only poses a serious threat to environment, but also involves a disposal cost) has garnered tremendous importance in the current refi ning scenario. Needle coke obtained from delayed coking process is a highly sought-after product, which is used in electric arc furnaces (in the form of graphite electrodes) in steel making applications. In the present communication, the published literature has been extensively analyzed and a state-of-the-art review has been written that includes: (1) importance and place of delayed coking as a residue upgrading process in the current refi ning scenario; (2) coking mechanism and kinetics; (3) design aspects; (4) feedstocks suitable for the production of needle coke; (5) characteristics of needle coke; (6) factors affecting needle coke quality and quantity; and (7) future market for needle coke. An attempt has been made to get the above-mentioned aspects together in a coherent theme so that the information is available at a glance and could be of signifi cant use for researchers and practising refi ners. -
Refinery Scheme's Mass Targeting and Bottom
REFINERY SCHEME’S MASS TARGETING AND BOTTOM SECTION SYNTHESIS FOR HEAVY OIL A Thesis by ABDULAZIZ ABDULKAREEM A ALNAJJAR Submitted to the Office of Graduate and Professional Studies of Texas A&M University in partial fulfillment of the requirements for the degree of MASTER OF SCIENCE Chair of Committee, Mahmoud M.El-Halwagi Committee Members, M. Sam Mannan Sergiy Butenko Head of Department, M. Nazmul Karim December 2015 Major Subject: Chemical Engineering Copyright 2015 Abdulaziz A. Alnajjar ABSTRACT This work evaluates the introduction of heavy oil in a refinery as a first step. The first step will yield an increase in the production of the bottom products (vacuum residue, gas oil and diesel). It will also reduce the production of the light products (gases, LPG and naphtha) from ADU/VDU for oil with API above 20. However, we showed that if the heavy oil is below 20 API, the vacuum residue will be the only increasing product. This also reflects on the unit capital cost. The power and steam required by the refinery should also increase as crude oil becomes heavier due to the high amount of steam used in the delayed coker unit. Nevertheless, the fuel for the fire heaters does not show the expected change as compared to the model. The report goes to a further step by replacing bottom product processes with gasification and syngas routes. This step results to reduce the total production of fuel. Therefore, the fuel gasification paths MTG, DME (direct and indirect), and FT are more valuable than other gasification paths. All fuel paths showed a similar amount of fuel production, yielding extra production around 100,000 lb/hr compared to the base case. -
Leo D. Brown, Baton Rouge. LA (US); CE E. E
US00787.1510B2 (12) United States Patent (10) Patent No.: US 7,871,510 B2 Leta et al. (45) Date of Patent: Jan. 18, 2011 (54) PRODUCTION OF AN ENHANCED RESID 3,684,697 A 8, 1972 Gamison COKER FEED USING ULTRAFLTRATION 3,707.459 A 12, 1972 Mason et al. 3,769,200 A 10, 1973 Folkins (75) Inventors: Daniel P. Leta, Flemington, NJ (US); 3,852,047 A 12/1974 Schlinger et al. MichaelLeo D. Brown, Siskin, Baton Randolph, Rouge. NJ LA (US) (US); 4,115.465CE A 9,E. 1978 ElferE. et al. (73) Assignee: ExxonMobil Research & Engineering 4,134,824.4,120,900 A 10,1/1979 1978 knE tal.A. Co., Annadale, NJ (US) 4,140,623 A 2/1979 Sooter et al. 4,169,782 A 10/1979 Thompson (*) Notice: Subject to any disclaimer, the term of this patent is extended or adjusted under 35 (Continued) U.S.C. 154(b) by 276 days. FOREIGN PATENT DOCUMENTS (21) Appl. No.: 11/980,158 CA 2185264 9, 1996 (22) Filed: Oct. 30, 2007 (Continued) (65) Prior Publication Data OTHER PUBLICATIONS US 2009/OO57196A1 Mar. 5, 2009 PCT International Search Report. (Continued) Related U.S. Application Data Primary Examiner Walter D Griffin (60) Provisional application No. 60/966,518, filed on Aug. Assistant Examiner—Renee Robinson 28, 2007. (74) Attorney, Agent, or Firm Glenn T. Barrett; Malcolm D. K (51) Int. Cl. e CIG 55/04 (2006.01) (57) ABSTRACT BOID 6/6 (2006.01) (52) U.S. Cl. ........................... 208/88: 208/85; 208/13.1; This invention relates to a high-pressure ultrafiltration pro 21 Ofé51 cess to produce an improved coker feed for producing a (58) Field of Classification Search .................. -
Petroleum Refining Water/Wastewater Management
Petroleum refining Operations Best Practice water/wastewater Series use and management 2010 www.ipieca.org The global oil and gas industry association for environmental and social issues 5th Floor, 209–215 Blackfriars Road, London SE1 8NL, United Kingdom Telephone: +44 (0)20 7633 2388 Facsimile: +44 (0)20 7633 2389 E-mail: [email protected] Internet: www.ipieca.org © IPIECA 2010 All rights reserved. No part of this publication may be reproduced, stored in a retrieval system, or transmitted in any form or by any means, electronic, mechanical, photocopying, recording or otherwise, without the prior consent of IPIECA. This publication is printed on paper manufactured from fibre obtained from sustainably grown softwood forests and bleached without any damage to the environment. Petroleum refining water/wastewater use and management IPIECA Operations Best Practice Series This document was prepared by AECOM, Inc. on behalf of the IPIECA Refinery Water Management Task Force. The assistance of M. Venkatesh of ENSR–AECOM is gratefully acknowledged. Cover photographs reproduced courtesy of the following (clockwise from top left): ExxonMobil; Nexen; Photodisc Inc.; iStockphoto; Corbis; Shutterstock.com. IPIECA Contents Introduction 2 Effluent treatment 25 Process wastewater pretreatment 25 Refinery water overview 3 Desalter effluent treatment 25 Overall refinery water balance 3 Wastewater segregation 27 Sources of water 3 Primary treatment 28 Water leaving the refinery 4 First stage: separation Raw water treatment: 5 (oil/water separators, API separators) -
Volume 1: Section 3
Volume 1: Project Description TOTAL Upgrader Project Section 3: Project Description 3 Project Description 3.1 Introduction This section provides the following information about the TOTAL Upgrader: • a process description • mass and energy balances, measurement and required materials • the estimated quantities and properties of the upgrader’s products and byproducts along with an overview of air emissions and mitigation measures • the plot plan for the upgrader and the consideration given during design to safety, environmental protection and equipment integrity • the utilities and offsites required to support the upgrader • alternative design considerations 3.2 Process Description After an extensive evaluation process, TOTAL has selected an upgrader configuration with the following components: • distillation: • diluent recovery unit (DRU) • vacuum distillation unit (VDU) – Phase 2 • coking: • delayed coker unit (DCU) • unsaturated gas plant (USGP) • hydrotreatment and desulphurization: • naphtha hydrotreater (NHT) • distillate hydrotreater (DHT) • mild hydrocracker (MHC) – Phase 2 • hydrogen production units • saturated gas plant (SGP) • amine regeneration unit (ARU) • sour water stripping units (SWS) • sulphur recovery units (SRU) including a tail gas treating unit (TGTU) For an overview of the process, see Figure 3.2-1. For an evaluation of alternatives to this configuration, see Section 3.7. The upgrader will be developed in two phases. All the process units listed will be constructed in Phase 1 except for those identified to be constructed in Phase 2. The VDU, MHC and additional components of the DRU, DCU, ARU, hydrogen unit and SRU will be constructed in Phase 2. For information on the site construction sequence, see Section 4.3.6.1 and Table 4.3-1.