20. Formation and Properties of Knitted Structures
Total Page:16
File Type:pdf, Size:1020Kb
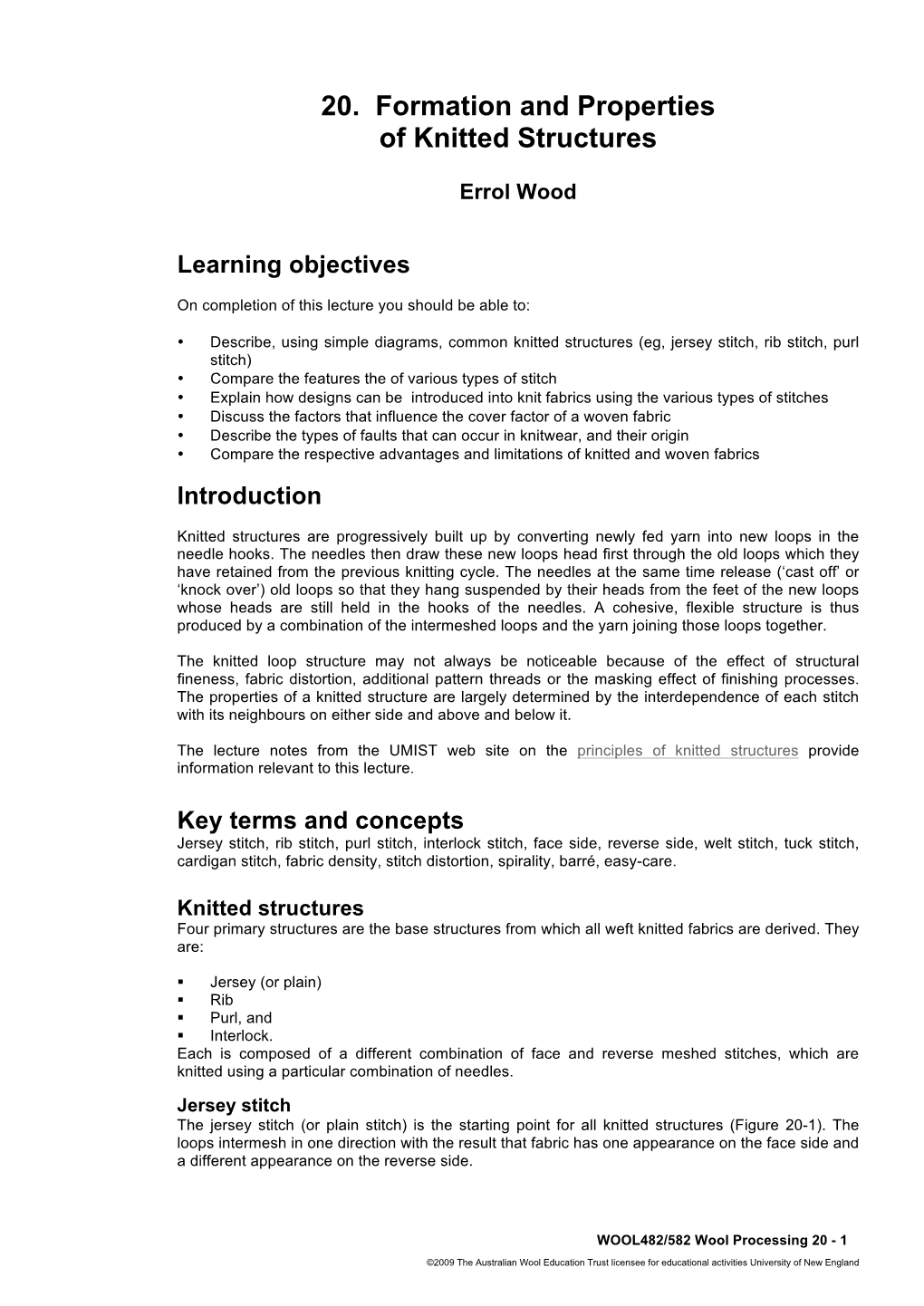
Load more
Recommended publications
-
Two Loom Knitting Projects for Animal Rescue Creating a Basic Pouch and Blanket
Two Loom Knitting Projects for Animal Rescue Creating a basic pouch and blanket Pouch - tight and slow Small blanket - easy and knitting fast knitting What you need: What you need: ● Cotton, bamboo, or wool (not synthetics) - 4 ● Yarn (can be synthetic!) - 8ply/size 4 to 8 ply, in DK/size4 yarn (double yarn knitting), ● A round or long loom, narrow gauge (for ● A round or long loom, medium gauge - tight knitting) is better (I’m using 56cm 38-41pegs diameter, with 56pegs, bought from ● Looming hook (often comes with kit) Spotlight - ● Small scissors to cut yarn https://www.spotlightstores.com/craft-hobbi ● Yarn needle to sew in the ends es/yarn-needle-art/needle-art-tools-accesso ● Tape measure or ruler ries/looms/crafters-choice-knit-weave-loom- kit/80291603) ● Looming hook (often comes with kit) Sources: ● Small scissors to cut yarn Knitting a flat panel - ● Yarn needle to sew in the ends https://youtu.be/pIdNuGMa438 ● Tape measure or ruler Double yarn knitting - https://youtu.be/p0bYlOZT2p4 Sources: Cast-off a flat panel - https://youtu.be/6VKYFkQdr6U Flat knitting: https://youtu.be/2gmUY4y2w34 Weaving in ends - https://youtu.be/v-p4qsiyuI8 Flat Drawstring cast-off: https://youtu.be/ctVBY-1oG8o Weave in ends: https://youtu.be/v-p4qsiyuI8 Instructions: ● Cast-on e-wrap, double yarn 35 pegs as a Instructions: flat panel ● E-wrap all stitches, all rows, in double yarn 1. Loop once around all pegs ● Knit until you have a square, approx 30cm 2. Flat-Knit all pegs long 3. Keep going until you have about 25cm ● Cast-off the flat panel length of knitting ● Using the yarn needle, stitch in ends 4. -
Woven Fabrics
Fabric – Woven Fabrics WOVEN FABRICS Fabrics are made of yarns by weaving them in different combinations. It is mostly done by interlacing two sets of yarn or thread made of fibers called the warp and weft of the loom. It only stretches in the bias directions, between the warp and weft directions, unless the threads are elastic. Lengthwise stronger vertical yarns with more twist are Warp or Picks while widthwise filling yarns are termed as weft or ends. Sidewise edge of fabric is termed as Selvedge. THREE BASIC WEAVES There are three main types of weave: Plain, Twill and Satin Plain weave is a basic weave which is made when the thread is woven on one up and one down principle, some plain weave fabrics are Chambray, Chiffon, Gingham, and Organza etc. Twill weave is made when the thread is placed by varying the order of interlacing the yarns so that diagonal parallel lines are produced across the fabric. Satin Weave is a weave made when each warp yarn floats over four filling yarns and interlaces with fifth filling yarn. Plain weave Twill weave Satin weave Fabric – Weft Knit Fabrics Knitted Fabrics Knitting is the process of construction of a fabric by interlocking loops of yarn by means of hooked needles. Knitted fabric consists of horizontal rows known as courses and vertical columns of loops known as Wales. Knitted fabrics are porous having insulated air pockets giving warmth when worn. Knitted fabrics are very absorbent, wrinkle resistant and lightweight. They shrink more than woven fabrics unless shrink- proofing techniques are used. -
Knitting Daily Presents Exploring the Infinity Scarf Pattern
Exploring the Infinity Scarf Pattern: 7 Free Designs for Knitting Infinity Scarves Exploring the Infinity Scarf Pattern: 7 Free Designs for Knitting Infinity Scarves INFINITY SCARVES ARE ALL THE RAGE, AND FOR GOOD The Maryse Cowl by Amy Christoffers is knit in an easy, REASON. They’re super stylish and adaptable, and they won’t reversible lace pattern that you’ll be able to memorize quickly. ever slip off of your neck and get lost. I love the versatility of the Use a bright color to liven up the winter blahs! infinity scarf—for a swingy, fashionable look, just drape it once around your neck and let it hang free. Or, wrap it twice (or three My Welted Infinity Scarf is quick and easy, and knit entirely times!) around your neck for a cowl-like look. Either way, you’ll in a welted stitch pattern. Welting is simply rows of stockinette look great! followed by rows of reverse stockinette. The technique brings the stockinette rows to the front and pushes the reverse stockinette I’ve gathered seven of our most popular infinity scarf patterns, to the back, creating the welted effect. Knit from a super bulky plus one brand-new design, in this free eBook. yarn, you can make this scarf in a weekend! The Two Ribs Infinity Scarf by Susan Pierce Lawrence is a Jennifer Dassau’s Roam Cowl starts with an innovative Möbius combination of fisherman’s rib and welting. This mix of stitches cast-on. The lace pattern is called a Roman Stripe, which results makes for wonderful textural contrast. -
Knitting V/S Weaving Defined
Initials with comparisons Knitting technology Knitting V/S Weaving Defined Knitting may be defined as Weaving may be defined as: “Inter-looping / Inter-meshing / hook-up / Interlacement of two sets of yarn at right Inter-lock of single or set of yarn moving angle (90o). only in one direction either lengthwise (warp knitting) or cross-wise (weft knitting). Principle The inter-lopping is carried out by needles Weaving is carried out by inter-lacing a (may be Latch or beard or compound series of vertical, parallel threads (the needle etc), the needles are equipped on a warp) with a series of horizontal, parallel cylinder and Needle butt moves between threads (the filling). The warp yarns from the grooves of cams to accomplish a beam pass through the heddles and reed, knitting cycle and producing the fabric. and the filling is shot through the “shed” The shape of the needle cam grooves of warp threads by means of a shuttle or depends on the required knitting pattern. other device and is settled in place by the For more detail see Circular / Flat reed and lay. The woven fabric is then knitting machine or Working principle of wound on a cloth beam. The primary Circular knitting machine (video) distinction between different types of looms is the manner of filling insertion (see WEFT INSERTION Dictionary on home page). The principal elements of any type of loom are the shedding, picking, and beating-up devices. In shedding, a path is formed for the filling by raising some warp threads while others are left down. -
VOGUEKNITTINGLIVE.COM SC HEDULE Thursday, October 23 Registration: 3 P.M
VOGU Eknitting CHICAGO THE ULTIMATE KNITTING EVENT OCTOBER 24 –26 ,2014 • PALMER HOUSE HILTON HOTEL PRINTABLE BROCHURE NEW& INSPIRATIONAL KNITWORTHY HAND KNITTING PRODUCTS CLASSES & LECTURES! VOGUEKNITTINGLIVE.COM SC HEDULE Thursday, October 23 Registration: 3 p.m. –7 p.m. OF EVENTS Classroom Hours: 6 p.m. –9 p.m. Friday, October 24 VOGUEknitting Registration: 8 a.m. –7:30 p.m. 3-hour Classroom Hours: 9 a.m.–12 p.m., 2 p.m.–5 p.m., 6 p.m. –9 p.m. 2-hour Classroom Hours: 9 a.m.–11 a.m., 2 p.m.–4 p.m. Marketplace: 5:00 p.m. –8:30 p.m. Please refer to VogueknittingLIVE.com for complete details. Saturday, October 25 HOTEL INFORMATION Registration: 8 a.m. –6:30 p.m. Vogue Knitting LIVE will be held in 3-hour Classroom Hours: 9 a.m.–12 p.m., 2 p.m.–5 p.m., 6 p.m. –9 p.m. downtown Chicago at the luxurious 2-hour Classroom Hours: Palmer House Hilton Hotel, located 9 a.m.–11 a.m., 2 p.m.–4 p.m. near Millennium Park in the heart of Marketplace: 10 a.m. –6:30 p.m. the theater, financial, and shopping districts of downtown Chicago. The Palmer House Hilton Hotel is within walking distance of the Windy City’s Sunday, October 26 most famous museums, shopping,a government, and corporate buildings. Registration: 8 a.m. –3 p.m. 3-hour Classroom Hours: The Palmer House Hilton Hotel 9 a.m.–12 p.m., 2 p.m.–5 p.m. -
Flat Knitting of Optical Fibres
AUTEX 2009 World Textile Conference 26-28 May, 2009 İzmir, Turkey FLAT KNITTING OF OPTICAL FIBRES Joel Peterson, Folke Sandvik The Swedish School of Textiles, University of Borås, Borås, Sweden, [email protected] ABSTRACT This paper presents an experimental research in the areas of knitting technology and optical fibres. The aim is to explore the possibilities to knit stiff monofilament optical fibres in flat knitting machines. The yarns used were transparent monofilament of polyester and optical fibres of PMMA (Polymethyl Metacrylate). Result shows that a hexagon shaped flat knitted prototype can be produced but also difficulties to knit monofilament yarn with optical fibres. The optical fibres was put into the structure in straight angles as weft insertion, to avoid bending and breakage of the monofilaments. Another problem was the take down device on the knitting machine but a solution of this is presented in the paper. Key Words: Optical fibres, flat knitting, knitting technology, technical textiles 1. INTRODUCTION This paper is about an experimental research in the areas of knitting technology and optical fibres and the aim is to explore the possibilities to knit with stiff monofilament optical fibres. Fibres with high stiffness are known to have a limited knittability and difficult to process in knitting machines [1]. The machine used is an electronic flat knitting machine STOLL CMS 330 TC with special equipment suitable for the feeding of yarn with high stiffness. In order to facilitate the progression of the work, different yarns were used. It was expected to be a challenge to work with optical fibres, and therefore the choice was made to use other yarns with better knittability in a first phase. -
KNITTING Definition Statement Relationship Between Large Subject
D04B KNITTING Definition statement This subclass/group covers: weft knitting machines are covered by D04B 7/00 to D04B 13/00, details of, or auxiliary devices incorporated in such machines are covered by D04B 15/00 and articles made by such machines are covered by D04B 1/00 warp knitting machines are covered by D04B 23/00 to D04B 25/00, details of, or auxiliary devices incorporated in such machines are covered by D04B 27/00 and articles made by such machines are covered by D04B 21/00 details of, or auxiliary devices incorporated in knitting machines not limited to a specific kind of knitting machine are covered by D04B 35/00 miscellaneous knitting machines and articles made by such machines are covered by D04B 39/00 hand knitting equipment is covered by D04B 3/00, D04B 5/00 and D04B 33/00 auxiliary apparatuses or devices for use with knitting machines are covered by D04B 37/00 or for hand knitting equipment are covered by D04B 17/00, D04B 19/00 and D04B 31/00 Relationship between large subject matter areas The difference between the subclass D04B and B32B5 is as follows:layered products including knitted products as such should be classified in B32B5 only; layered products formed by a knitting process featuring specified patterns or information on the composition of the knit article should be classified in D04B. Note that such products may comprise additional coated faces. References relevant to classification in this subclass This subclass/group does not cover: Layered products (i.e. laminates) B32B 5/00 including knitted articles 1 Knitted products of unspecified A41A61F structure or composition, e.g. -
19. Principles of Yarn Requirements for Knitting
19. Principles of Yarn Requirements for Knitting Errol Wood Learning objectives On completion of this lecture you should be able to: • Describe the general methods of forming textile fabrics; • Outline the fibre and yarn requirements for machine knitwear • Describe the steps in manufacturing and preparing yarn for knitting Key terms and concepts Weft knitting, warp knitting, fibres, fibre diameter, worsted system, yarn count, steaming, clearing, winding, lubrication, needle loop, sinker loop, courses, wales, latch needle, bearded needle Introduction Knitting as a method of converting yarn into fabric begins with the bending of the yarn into either weft or warp loops. These loops are then intermeshed with other loops of the same open or closed configuration in either a horizontal or vertical direction. These directions correspond respectively to the two basic forms of knitting technology – weft and warp knitting. In recent decades few sectors of the textile industry have grown as rapidly as the machine knitting industry. Advances in knitting technologies and fibres have led to a diverse range of products on the market, from high quality apparel to industrial textiles. The knitting industry can be divided into four groups – fully fashioned, flat knitting, circular knitting and warp knitting. Within the wool industry both fully fashioned and flat knitting are widely used. Circular knitting is limited to certain markets and warp knitting is seldom used for wool. This lecture covers the fibre and yarn requirements for knitting, and explains the formation of knitted structures. A number of texts are useful as general references for this lecture; (Wignall, 1964), (Gohl and Vilensky, 1985) and (Spencer, 1986). -
Mechanical Behavior Characterization of Knitted Textiles a Thesis
Mechanical Behavior Characterization of Knitted Textiles A Thesis Submitted to the Faculty of Drexel University by Mustafa Oncul in partial fulfillment of the requirements for the degree of Master of Science in Mechanical Engineering December 2017 © Copyright 2017 Mustafa Oncul. All Rights Reserved. ii In the Name of Allah, the Entirely Merciful, the Especially Merciful iii TABLE OF CONTENTS LIST OF TABLES .......................................................................................................... v LIST OF FIGURES ........................................................................................................ vi ABSTRACT .................................................................................................................... x CHAPTER 1: INTRODUCTION ................................................................................... 1 1.1 An Overview ............................................................................................................. 1 1.1.1 Knitted Textiles .................................................................................................. 3 1.2 Testing and Characterization of Textiles .................................................................. 7 1.3 Nonlinear Mechanics of Knitted Textiles ................................................................. 9 1.4 Thesis Structure ....................................................................................................... 12 CHAPTER 2: BACKGROUND AND STATE-OF-THE-ART IN MECHANICAL BEHAVIOR CHARACTERIZATION -
Master of Textile Design (Choice Based Credit System)
RASHTRASANT TUKADOJI MAHARAJ NAGPUR UNIVERSITY NAGPUR (Established by Government of Central Provinces Education Department by Notification No. 513 dated the 1st of August, 1923 & presently a State University governed by Maharashtra Universities Act, 1994) FACULTY OF HOME SCIENCE DIRECTION NO. 79 OF 2016 DIRECTION GOVERNING THE EXAMINATION LEADING TO THE DEGREE OF MASTER OF TEXTILE DESIGN (CHOICE BASED CREDIT SYSTEM) (Issued under section 14(8) of the Maharashtra University Act 1994) Whereas the Maharashtra Universities act No. XXXV of 1994 has come into force with effect from 22nd July, 1994 and was amended from time to time. AND WHEREAS, the University Grants Commission, New Delhi vide letter No.D.O.No.F-2/2008/(XI Plan), dated 31st January 2008 regarding new initiatives under the XI Plan – Academic reforms in the University has suggested for improving quality of higher education and to initiate the academic reform at the earliest, AND Whereas the Task Force in BFD/BTS/BPD in the Faculty of Home Science at its meeting held on 25/08/2016, have recommended for starting of semester pattern and prepared the syllabus and scheme of examination for Master of Textile Design, commensurate with the governing guidelines. AND Whereas the Coordinator, Faculty of Home Science concurred with the recommendations of the Task Force in BFD/BTS/BPD in the Faculty of Home science vide his observations dated 25/08/2016 AND 1 Whereas, the new draft direction and scheme of examination as per semester pattern is to be implemented from the academic session 2016-2017 for Master of Textile Design which is to be regulated by this direction and as such there is no existence and framing of an ordinance for the above examination, AND WHEREAS the Hon‘ble Vice-Chancellor has accepted the syllabus along with draft direction on the behalf of Academic Council on 7-10- 2016 under section 14(7) of Maharashtra University Act 1994. -
Warp and Weft Knitting | Knitting | Basic Knitted Fabrics
Weft vs. Warp Knitting Weft Warp Weft knitting. Weft knitting uses one continuous yarn to form courses, or rows of loops, across a fabric. There are three fundamental stitches in weft knitting: plain-knit, purl and rib. On a machine, the individual yarn is fed to one or more needles at a time. Weft knitting machines can produce both flat and circular fabric. Circular machines produce mainly yardage but may also produce sweater bodies, pantyhose and socks. Flatbed machines knit full garments and operate at much slower speeds. The simplest, most common filling knit fabric is single jersey. Double knits are made on machines with two sets of needles. All hosiery is produced as a filling knit process. Warp Knitting. Warp knitting represents the fastest method of producing fabric from yarns. Warp knitting differs from weft knitting in that each needle loops its own thread. The needles produce parallel rows of loops simultaneously that are interlocked in a zigzag pattern. Fabric is produced in sheet or flat form using one or more sets of warp yarns. The yarns are fed from warp beams to a row of needles extending across the width of the machine (Figure 9b). Two common types of warp knitting machines are the Tricot and Raschel machines. Raschel machines are useful because they can process all yarn types in all forms (filament, staple, combed, carded, etc.). Warp knitting can also be used to make pile fabrics often used for upholstery. Back Knitting To form a fabric by the intermeshing of loops of yam. wale course Wen €hitting Loops are formed by needles knitting the yam across the width Each weft thread is fed at right angles to the direction of fabric formation. -
Taking Advantage of the Design Potential of Digital Printing Technology for Apparel
Volume 4, Issue 3, Spring2005 TAKING ADVANTAGE OF THE DESIGN POTENTIAL OF DIGITAL PRINTING TECHNOLOGY FOR APPAREL J.R. Campbell, Associate Professor, Iowa State University 1073 Lebaron Hall Ames, IA 50011 515-294-0945 Jean Parsons, Assistant Professor, Iowa State University 1071a Lebaron Hall Ames, IA 50011 515-294-4022 ABSTRACT The integration of digital technologies into apparel forms allows designers to explore and visualize new creative possibilities. How the technology is used and how design concepts are perceived in the industry are areas of crucial importance to the technology’s longevity. Our goal, as collaborative artists, focuses on integrating technology into the creative process to create both art and industry-oriented apparel. The applications of digital textile and apparel design have implications for many areas of the industry, but we have focused on three: art-to -wear, custom design, and mass customizable products. The body of research and artwork that we have developed suggests that a systematic approach to integrating new technologies into the textile and apparel design process can be developed, recorded and employed in future design explorations to inspire the most rapid technology integration with the greatest potential for new product conceptualization. Keywords: Digital textile printing, apparel design, design process, art-to -wear The integration of digital technologies into creative process to create both art and industry- apparel forms allows designers to explore and oriented apparel. visualize new creative possibilities. How the technology is used and how design concepts are When we began our collaborative process, the perceived in the industry are areas of crucial use of digital printing for apparel was at a importance to the technology’s longevity.