Revisiting the Origins of Coade Stone
Total Page:16
File Type:pdf, Size:1020Kb
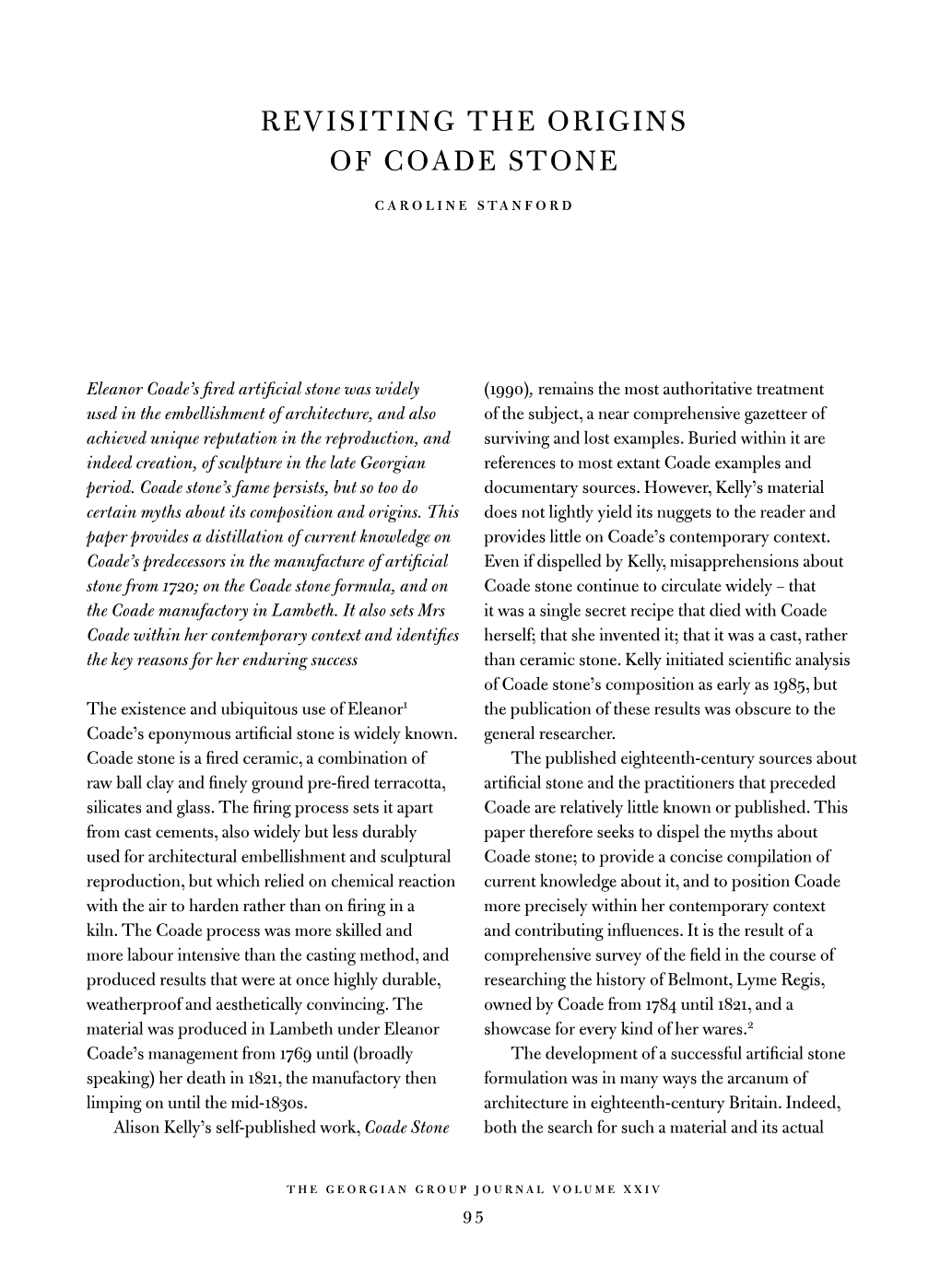
Load more
Recommended publications
-
+44 (0)1844 277188 +44 (0) 20 7394 2100 +44 (0)20 7394 8061 [email protected] [email protected] [email protected]
ROPEWALK THREE PIGEONS BRUNSWICK HOUSE Arch 52, London Road, 30 Wandsworth Road, Maltby Street, Milton Common, Vauxhall, Bermondsey, Oxfordshire OX9 2JN London SW8 2LG London SE1 3PA www.lassco.co.uk +44 (0)1844 277188 +44 (0) 20 7394 2100 +44 (0)20 7394 8061 [email protected] [email protected] [email protected] SIR WILLIAM CHAMBERS' DOORCASE An important carved Portland Stone doorcase c.1769, by Chambers (1723-1796) for his own house in Berners Street Westminster the triangular pediment with dentil mouldings above the rusticated cushion moulded frieze centred by a keystone in Coade Stone modelled in relief with a female mask, the jambs constructed with alternating rusticated quoins, DIMENSIONS: 432cm (170") High, 244cm (96") Wide, 198 (78.5) wide at jambs, Aperture = 315 x 152cm (124 x 59.75 STOCK CODE: 43528 HISTORY Sir William Chambers (1723-96) is one of the most revered of Georgian neo-classical architects. In his early career he was appointed architectural tutor to the Prince of Wales, later George III. In 1766, he became Architect to the King, (this being an unofficial title, rather than an actual salaried post with the Office of Works). He worked for Augusta, Dowager Princess of Wales building exotic garden buildings at Kew (the pagoda is his), and in 1757 he published a book of Chinese designs which had a significant influence on contemporary taste. He developed his Chinese interests further with his Dissertation on Oriental Gardening (1772), a fanciful elaboration of contemporary English ideas about the naturalistic style of gardening in China. -
Collection Development Policy 2012-17
COLLECTION DEVELOPMENT POLICY 2012-17 CONTENTS Definition of terms used in the policy 3 Introduction 5 An historical introduction to the collections 8 The Collections Archaeology 11 Applied and Decorative Arts 13 Ceramics 13 Glass 14 Objets d‘Art 14 Jewellery 15 Furniture 16 Plate 16 Uniforms, Clothing and Textiles 17 Flags 18 Coins, Medals and Heraldry 20 Coins and Medals 20 Ship Badges, Heraldry and Seal Casts 21 Ethnography, Relics and Antiquities 23 Polar Equipment 23 Relics and Antiquities 23 Ethnographic Objects 24 Tools and Ship Equipment 26 Tools and Equipment 26 Figureheads and Ship Carvings 27 Cartography 30 Atlases, Charts, Maps and Plans 30 Globes and Globe Gores 31 Fine Arts 33 Oil Paintings 33 Prints and Drawings 34 Portrait Miniatures 35 Sculpture 36 Science and Technology 40 Astronomical Instruments 40 Navigational Instruments and Oceanography 42 Horology 43 Weapons and Ordnance 46 Edged Weapons 46 Firearms 47 Ordnance 49 Photographs and Film 52 Historic Photographs 52 Film Archive 54 Ship Plans and Technical Records 57 1 Boats and Ship Models 60 Boats 60 Models 60 Ethnographic Models 61 Caird Library and Archive 63 Archive Collections 63 Printed Ephemera 65 Rare Books 66 Legal, ethical and institutional contexts to acquisition and disposal 69 1.1 Legal and Ethical Framework 69 1.2 Principles of Collecting 69 1.3 Criteria for Collecting 70 1.4 Acquisition Policy 70 1.5 Acquisitions not covered by the policy 73 1.6 Acquisition documentation 73 1.7 Acquisition decision-making process 73 1.8 Disposal Policy 75 1.9 Methods of disposal 77 1.10 Disposal documentation 79 1.11 Disposal decision-making process 79 1.12 Collections Development Committee 79 1.13 Reporting Structure 80 1.14 References 81 Appendix 1. -
The Invisible “Sculpteuse”: Sculptures by Women in the Nineteenth-Century Urban Public Space—London, Paris, Brussels
Marjan Sterckx The Invisible “Sculpteuse”: Sculptures by Women in the Nineteenth-century Urban Public Space—London, Paris, Brussels Nineteenth-Century Art Worldwide 7, no. 2 (Autumn 2008) Citation: Marjan Sterckx, “The Invisible ‘Sculpteuse’: Sculptures by Women in the Nineteenth- century Urban Public Space—London, Paris, Brussels,” Nineteenth-Century Art Worldwide 7, no. 2 (Autumn 2008), http://www.19thc-artworldwide.org/autumn08/90-the-invisible- sculpteuse-sculptures-by-women-in-the-nineteenth-century-urban-public-spacelondon-paris- brussels. Published by: Association of Historians of Nineteenth-Century Art Notes: This PDF is provided for reference purposes only and may not contain all the functionality or features of the original, online publication. ©2008 Nineteenth-Century Art Worldwide Sterckx: Sculptures by Women in the Nineteenth-Century Urban Public Space–London, Paris, Brussels Nineteenth-Century Art Worldwide 7, no. 2 (Autumn 2008) The Invisible “Sculpteuse”: Sculptures by Women in the Nineteenth-century Urban Public Space—London, Paris, Brussels[1] by Marjan Sterckx Introduction The Dictionary of Employment Open to Women, published by the London Women’s Institute in 1898, identified the kinds of commissions that women artists opting for a career as sculptor might expect. They included light fittings, forks and spoons, racing cups, presentation plates, medals and jewelry, as well as “monumental work” and the stone decoration of domestic facades, which was said to be “nice work, but poorly paid,” and “difficult to obtain without -
Issue 07 April 2016 Click Here
JARDINIQUE Garden Antiques ______________________________________________________________________________________________ What’s New at Jardinique this Spring? Come and See for Yourselves – A Warm Welcome Awaits! Our Coade Stone Collection Over the past 21 years we have come across many delightful pieces of garden antiques, but have been particularly pleased to find a number of Coade Stone pieces on our travels. As a result we now have two fine examples of a lion and figure of Venus on display for sale, the details of which are shown here and on our website. Coade Stone stems from the mid 18th century, and is a manufactured stone or stoneware resembling limestone. It comprises a mixture of ground glass, flint, sand, clay and petrified clay, a combination that often turned out to be more durable than the stone it was imitating. Poured into moulds, dried, fired at high temperatures in kilns and finished by hand, the process produced some wonderful, and at times quite complex, sculptures. Eleanor Coade’s artificial stone manufactory was established in 1769 at Lambeth - now the site of the Royal Festival Hall, manufacturing Coade Stone decorative sculpture and ornaments. Eleanor (1708-1796) and her daughter, also Eleanor (1733-1821), were both part of a handful of independent and enterprising 18th century women who established their own businesses. The Coade business flourished, and grew under its lead designer the neoclassical sculptor John Bacon who held the role until his death in 1799. In 1796 following the death of her mother, the younger Eleanor Coade went into partnership with John Sealy and subsequently her cousin William Croggan until her death in 1821. -
Westminster Lions Cycle Ride
WESTMINSTER Lions CYCLe ride I N W E S T MCYC I N S T E R A seven mile ride, best done on a END Sunday morning as much of the ride is on major streets, observing a few L of Westminster’s lions. More can be ING found in START ‘London Pride, the 10,000 Lions of London’ by Valerie Colin-Russ. A Lion-head mooring rings aLong the Victoria embankment. Designed by the sculptor Gilbert Bayes, the lions are considered to mark the point of a dangerously high tide, ‘When the lions drink, London will sink’. B south bank Lion At the south end of Westminster Bridge, visible from the Victoria Embankment, this 1837 Lion by W.F. Woodington originally stood atop the Red Lion Brewery on the South Bank site. When the brewery was demolished for the 1951 Festival of Britain, the lion was moved to Station Approach Waterloo - British Rail had a Lion logo at this time. In 1966 the lion was moved to its present location, the red paint having been Mooring rings removed to reveal the statue is made from Coade Stone, a tough, artificial stone that several lions on this trip are made from. Mrs Coade’s factory was also on the South Bank. C roof of oLd home office buiLding, Whitehall (just by the Cenotaph) Queen Victoria sits atop the building with a lion to one side and a unicorn to the other D red Lion pub While this building is Victorian there has been a tavern on this site since 1434, though it has not always been the Red Lion. -
Alison Kelly, 'Eleanor Coade at Stowe', the Georgian Group Jounal
Alison Kelly, ‘Eleanor Coade at Stowe’, The Georgian Group Jounal, Vol. II, 1992, pp. 97–100 TEXT © THE AUTHORS 1992 ELEANOR CO ADE AT STOWE Alison Kelly towe is famous as the creation of many of the most eminent English architects, sculptors and garden designers, but one name rarely mentioned is that of Mrs SEleanor Coade.1 And yet Stowe had a range of Coade objects apparendy unrivalled at any other country house, stretching across nearly half a century from the 17 70s to at least 1814. Many of the Coade stone objects left Stowe at the sale of 1921, others have been overlooked thanks to Coade stone’s similarity to natural, fine-grained limestone, while the poor cataloguing of the 250,000 Stowe documents in the Huntington Library, San Marino, means that individual bills cannot be identified.2 Nevertheless, it is possible to give some impression of the range of Coade-stone objects at Stowe. In 1776 George Nugent-Temple-Grenville, later 1st Marquess of Buckingham, wrote to his uncle 2nd Earl Temple: “I have however seen a lion in artificial stone which I think will answer our purpose, and as the mold need not in this instance be destroyed I think we may have the pair for £100, perhaps this may be the cheapest way.”3 In fact the lions only came to £40 but the bill, dated 1778, does not specify the type of lion sent.4 The lions on the north portico, now in front of the school sports pavilion, were definitely Coade stone (Fig. I). -
A Walking Tour of Building Stones from Senate House to Tottenham Court Road
A Walking Tour of Building Stones from Senate House to Tottenham Court Road London Illustrated News Dr Ruth Siddall UCL Earth Sciences Gower Street London WC1E 6BT r.siddall@ ucl.ac.uk Ruth Siddall, 1 UCL Earth Sciences 2012 A Walking Tour of Building Stones from Senate House to Tottenham Court Road Ruth Siddall This guide is an update of parts of Eric Robinson’s tour, originally published in 1985. Tottenham Court Road has transformed since then, but many of the stones still remain. The Walk Start Point: Senate House, University of London. 1. Senate House Senate House and Library where designed by Charles Holden and built during 1932-37. This is actually a paired-down version of Holden’s original plans which included buildings occupying the land now taken by Birkbeck College, ULU and the piazza behind these buildings, leading from Byng Place. Nevertheless Senate House is a striking building. The major building material is dressed Portland Stone which has retained a good white colour. The lower courses are of axe-dressed Cornish Granite, probably from Carnsew Quarry. The spacious foyer is both paved and clad with Tivoli Travertine. Leave Senate House via the main entrance onto Malet Street, cross over and continue straight ahead along Keppel Street, pausing at the entrance to the London School of Hygiene and Tropical Medicine on the corner of Keppel Street and Gower Street. 2. London School of Hygiene and Tropical Medicine Also built primarily of beautifully dressed Portland Stone, the London School of Hygiene and Tropical Medicine’s building is of interest architecturally. -
100 Years Commitment to Craftsmanship Terracotta and Faience
100 YEARS COMMITMENT TO CRAFTSMANSHIP TERRACOTTA AND FAIENCE Lambs are a specialist manufacturer of hand pressed architectural terracotta and faience. The company manufactures bespoke ceramics to match all architectural periods. Every piece of Lambs terracotta and faience is individually hand formed to a meticulous standard by our highly skilled craftsmen. Our ceramicists are passionate about their profession. They are sculptors and mould makers who can hand press and finish architectural ceramics to the highest standards. Their works are comparable to the craftsmen of James Stiff and Son, Coade Stone and Doulton. The skills of Lambs’ ceramicists have been honed through years of experience yet their foundation is a deep academic understanding of design, manufacture, historical methods and cutting edge techniques. Every item of Lambs terracotta and faience is personally signed; something our ceramicists are simply not prepared to do unless it is perfect. We have purchased computer-controlled kilns to ensure the colour and size consistency of our ceramics. We can produce a range of colour samples for your approval within days. When we are fully satisfied with a piece of terracotta or faience we take the same care delivering it to you as we have creating it. The products Lambs make are a testament to our skill, and their longevity a reflection of our commitment to quality. “When we urgently required replacement architectural terracotta only Lambs were able to help. They surveryed the damaged existing material and delivered high quality replacements on time and on budget.” MARTIN NORTHEY OF COLLINSTOWN CONSTRUCTION Large: Faience detail from the Bluebird Café where Malcolm Campbell built his famous car, showing the legendary Bluebird motif and the floral detail Small left: Pineapple unit from Ipswich Town Hall soon after being drawn from the kiln Small right: Pedestal unit being finished at the Lambs terracotta workshop BRICKS AND ARCHES For Lambs, brick making isn’t merely a business; it is in our blood. -
Winchester Stone by Dr John Parker (PDF)
Winchester Stone by John Parker ©2016 Dr John Parker studied geology at Birmingham and Cambridge universities. He is a Fellow of the Geological Society of London. For over 30 years he worked as an exploration geologist for Shell around the world. He has lived in Winchester since 1987. On retirement he trained to be a Cathedral guide. The Building of Winchester Cathedral – model in the Musée de la Tapisserie, Bayeux 1 Contents Introduction page 3 Geological background 5 Summary of the stratigraphic succession 8 Building in Winchester Romano-British and Anglo-Saxon periods 11 Early medieval period (1066-1350) 12 Later medieval period (1350-1525) 18 16th to 18th century 23 19th to 21st century 24 Principal stone types 28 Chalk, clunch and flint 29 Oolite 30 Quarr 31 Caen 33 Purbeck 34 Beer 35 Upper Greensand 36 Portland 38 Other stones 40 Weldon 40 Chilmark 41 Doulting 41 French limestones 42 Coade Stone 42 Decorative stones, paving and monuments 43 Tournai Marble 43 Ledger stones and paving 44 Alabaster 45 Jerusalem stone 45 Choice of stone 46 Quarries 47 A personal postscript 48 Bibliography and References 50 ~~~~~~~~~~~~~~~~~~~~~~~~~~~~~~~~~~~~~~~~~~~~~~~~~~~~~ Photographs and diagrams are by the author, unless otherwise indicated 2 Introduction Winchester lies in an area virtually devoid of building stone. The city is on the southern edge of the South Downs, a pronounced upland area extending from Salisbury Plain in the west to Beachy Head in the east (Figs. 1 & 2). The bedrock of the Downs is the Upper Cretaceous Chalk (Fig. 3), a soft friable limestone unsuited for major building work, despite forming impressive cliffs along the Sussex coast to the east of Brighton. -
The Making of the Radcliffe Observatory’, the Georgian Group Journal, Vol
Geoffrey Tyack, ‘The making of the Radcliffe Observatory’, The Georgian Group Journal, Vol. X, 2000, pp. 122–140 TEXT © THE AUTHORS 2000 THE MAKING OF THE RADCLIFFE OBSERVATORY GEOFFREY TYACK he Radcliffe Observatory in Oxford has long maker, presented what is reckoned to be the first Tbeen recognised as an important monument telescope to the States General of Holland in , of early neo-classical architecture. But, for all its and in an observatory was built on the roof of historical interest, its striking appearance and its the University of Leiden, followed by others at excellent state of preservation, it remains surprisingly Utrecht and elsewhere, including one built by King little known, even to architectural historians . This is Christian IV of Denmark in in the form of a - partly because of its location, outside the centre of the ft-high tower next to the church of Holy Trinity, city, squashed up against the dreary th-century Copenhagen . The first tower observatories were not wards of a hospital, and only accessible through the very sophisticated buildings, but in Claude grounds of one of the lesser-known colleges of Oxford Perrault, himself a scientist, built a more elaborate University. It is also perhaps because of its unusual observatory at Paris which still survives in an altered functions and complicated building history, both of form; it was a two-storeyed structure with a flat roof, which repay investigation. projections at the corners for the telescopes, a room According to Anthony Wood the first observatory for larger astronomical instruments, and a meeting in Oxford was the ancient medieval gatehouse known room for the members of Colbert’s recently-established as Friar Bacon’s Study, guarding the southern approach Académie des Sciences. -
The Bucks Gardener
The Bucks Gardener Issue 23 The Newsletter of the Buckinghamshire Gardens Trust Spring 2006 Visit to Halton House & Gardens 2pm, Tuesday 9 May We have been invited to visit by kind permission of the Station Room an appropriately Moorish scheme, and the Billiard Commander, RAF Halton. Room is panelled with lavishly carved and gilded woodwork. A The House recurring motif throughout the house is the marigold. Baron Lionel de Rothschild bought the Halton Estate from Sir Originally the house was only intended to last for perhaps fifty George Dashwood in 1853. The Baron died in 1879 and soon years. It was only used at weekends, for entertaining, not to live afterwards his son Baron Alfred Charles began to build the new house we see today. It is an ‘ambitious’ mansion, in the free French style, mainly Contents a mix of C17 & C18 influences. Contemporaries found it to be Activities 2006 … 1 to 3 ‘terribly vulgar’ but that was probably as much on account of the From the Chair … 2 lavishness of its contents as for the architecture. The architect Eythrope: from the Journal of Horticulture, 1890 … 4 was William R Rogers of William Cubitt & Co, who had just Cliveden: how the Estate developed … 8 built 5 Hamilton Place, in London, for Alfred’s brother Charles, Cliveden revealed … 10 and it was finished in 1883. It is now listed at Grade II*. Rogers What’s on at Waddesdon … 11 used Ashlar stone, from Oxfordshire, with steep slate roofs, New year’s day flower count … 11 iron crestings and finials and a prominent porte-cochère on the Note from Stowe … 11 southeast front (otherwise it’s the same as the garden front). -
Revisiting the Origins of Coade Stone’, the Georgian Group Journal, Vol
Caroline Stanford, ‘Revisiting the origins of Coade Stone’, The Georgian Group Journal, Vol. XXIV, 2016, pp. 95–116 TEXT © THE AUTHORS 2016 REVISITING THE ORIGINS OF CoaDE StoNE CAROLINE STANFORD Eleanor Coade’s fired artificial stone was widely (1990), remains the most authoritative treatment used in the embellishment of architecture, and also of the subject, a near comprehensive gazetteer of achieved unique reputation in the reproduction, and surviving and lost examples. Buried within it are indeed creation, of sculpture in the late Georgian references to most extant Coade examples and period. Coade stone’s fame persists, but so too do documentary sources. However, Kelly’s material certain myths about its composition and origins. This does not lightly yield its nuggets to the reader and paper provides a distillation of current knowledge on provides little on Coade’s contemporary context. Coade’s predecessors in the manufacture of artificial Even if dispelled by Kelly, misapprehensions about stone from 1720; on the Coade stone formula, and on Coade stone continue to circulate widely – that the Coade manufactory in Lambeth. It also sets Mrs it was a single secret recipe that died with Coade Coade within her contemporary context and identifies herself; that she invented it; that it was a cast, rather the key reasons for her enduring success than ceramic stone. Kelly initiated scientific analysis of Coade stone’s composition as early as 1985, but he existence and ubiquitous use of Eleanor1 the publication of these results was obscure to the TCoade’s eponymous artificial stone is general researcher. widely known. Coade stone is a fired ceramic, a The published eighteenth-century sources about combination of raw ball clay and finely ground artificial stone and the practitioners that preceded pre-fired terracotta, silicates and glass.