Herriman High School Secure Entry
Total Page:16
File Type:pdf, Size:1020Kb
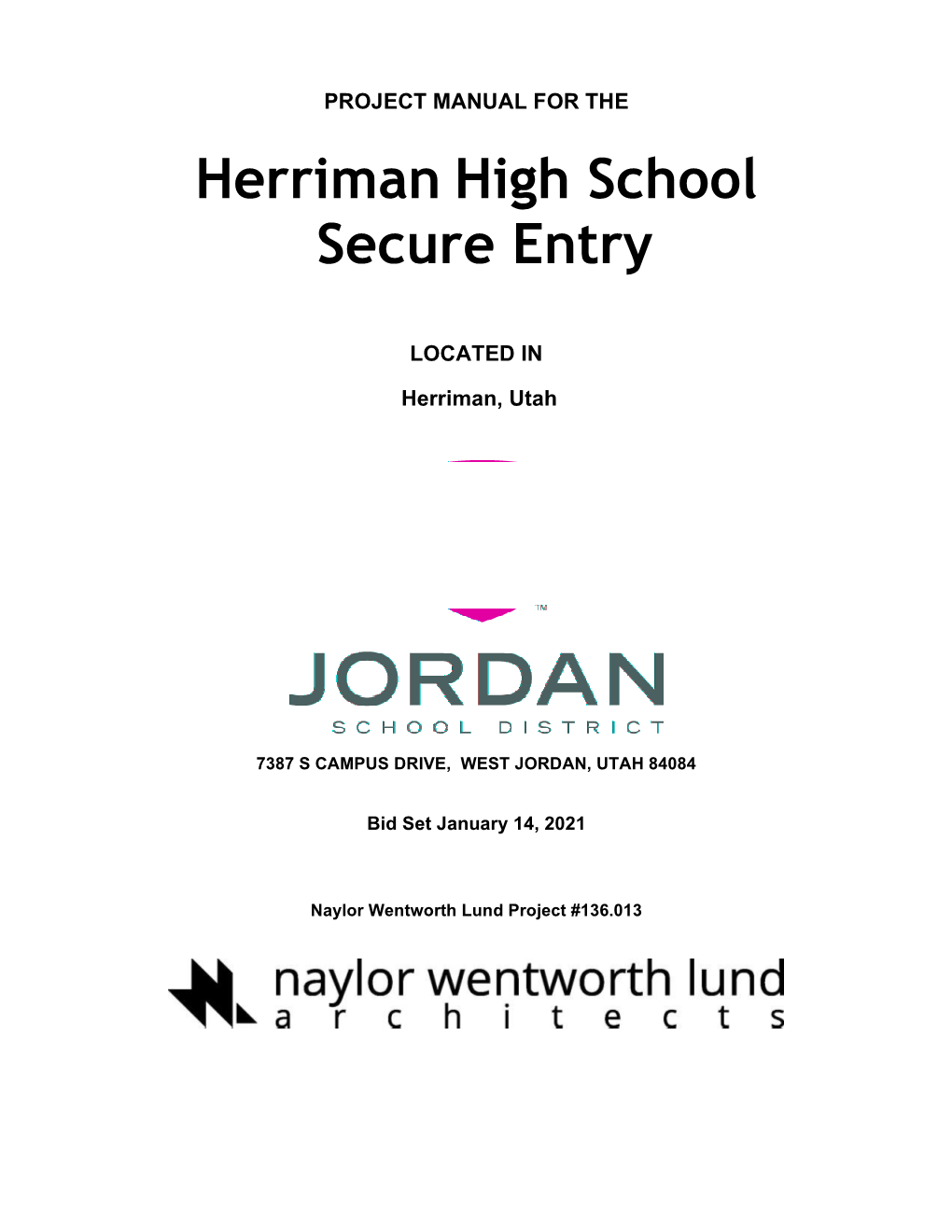
Load more
Recommended publications
-
2018 Disclosure Statements for Homebuyers (Garden Park)
Page 1 of 13 DAYBREAK 2018 Disclosure Statements for Homebuyers (Garden Park) Disclosure Statements for Homebuyers: 1. Ownership of VP Daybreak Operations LLC 16. Power Lines and Natural Gas Transportation Lines 2. Development of Daybreak 17. No Guarantee of View 3. Daybreak Community Organization and 18. Earthquake Faults Associations 19. Garages 4. Environmental Issues 20. Cluster Mailboxes 5. Road System Improvements and Access 21. Parking 6. Stormwater Runoff 22. Accessibility Modifications 7. Private and Public Parks, Trails and Open Space 23. Model Home Park 8. Proposed Lake Feature 24. Alleyways 9. Trail System Proximity to Homes 25. Sewer Depth 10. Aircraft Overflights 26. Restriction on Residential Unit Rental Investors 11. Nearby Agricultural Use 27. Waste Treatment and Other Facilities 12. School Attendance Boundaries 28. City Governance 13. Governmental Assessments and Charges 29. Radon Gas 14. Water, Sewage and Utility Service 15. Telecommunications Services Buyer has read and understands the attached Disclosure Statements as listed above. Buyer acknowledges that Buyer’s decision to purchase a residence in Daybreak is not based on any representation (other than those included in the Disclosure Statements), and Buyer has considered the possible effect of such matters in Buyer’s decision to purchase. Buyer further acknowledges that no salesperson, employee, or agent of VP Daybreak Operations LLC (or any of its affiliates) has the authority to modify any representation included in the Disclosure Statements nor any authority to make any promise, representation, or agreement other than as contained therein. Buyer further acknowledges that it is purchasing a residence from and built by a builder and not from or by VP Daybreak Operations LLC (or any of its affiliates) and that no salesperson, employee, or agent of such builder has the authority to modify any representation included in the Disclosure Statements or to make any promise, representation or agreement other than as contained therein. -
Athletics/Activities Handbookаа 201516
Last Updated: June 17, 2015 Athletics/Activities Handbook 201516 1 Last Updated: June 17, 2015 Table of Contents Region IV Board of Managers 3 Region Activity Chairperson 4 Coaches/Advisor Representatives 5 School Rosters 6 Directions to Schools 13 Region IV General Policies 20152016 16 Admission Fees and Tickets 16 Supervision of Region Activities, Tournaments and Meets 16 Accommodations for Visiting Teams 16 Officials 16 Eligibility of Players 17 Sportsmanship Policies 17 Event Scheduling and Participation 19 Activity Limitations 19 Seeding for State – Procedures for Breaking Ties of Standings 19 Region Board of Manager Governance 20 Trophies and Awards 22 School District Calendars 23 Baseball 25 Basketball 31 Cross Country 35 Drama 36 Drill Team 38 Football 41 Forensics/Debate 44 Golf 47 Music 51 Soccer 53 Softball 59 Swimming 62 Tennis 64 Track and Field 70 Volleyball 74 Wrestling 76 2 Last Updated: June 17, 2015 Region IV Board of Managers American Fork High School 8016108800 (fax) 8017568575 Dan Weishar 510 North 600 East American Fork, UT 84003 ATHLETIC DIRECTOR: Joseph Atwood 8016108800 Herriman High School 8015678530 (fax) 8015678545 James Birch 11917 South 6000 West Herriman, UT 84096 ATHLETIC DIRECTOR: Mont Widerberg Lehi High School 8016108805 (fax) 8017687040 Dave Mower 180 North 500 East Lehi, Utah 84043 ATHLETIC DIRECTOR: Matt Rowe 8016108805 Lone Peak High School 8017174568 (fax) 8017637064 Rhonda Bromley 10189 North 4800 West Highland, Utah 84003 ATHLETIC DIRECTOR: Braden Walker 8017174568 -
2:04.10 Herriman High School 1 2:02.40 Alta Hawks High
Bringham Young University Pool - UHSAA - Site License HY-TEK's MEET MANAGER 5.0 - Page 1 5A Utah High School State Champioinships - 2/14/2014 to 2/15/2014 5A Utah High School State Swimming Championships Meet Program Event 1 Women 200 Yard Medley Relay 5A HS State: 1:46.81 2/10/2006 Skyline A. Crandall, S. Nicponski, M. Knoop, K. Evans UT HS State: 1:46.81 2/10/2006 Skyline A. Crandall, S. Nicponski, M. Knoop, K. Evans 1:46.21 ALL NISCA All American 1:48.29 ALLC All American Consid Lane Team Relay Seed Time Finals Place Heat 1 of 2 Timed Finals 1 Herriman High School 2:04.10 ________________________ 2 Alta Hawks High School 2:02.40 ________________________ 3 Westlake High School 1:59.29 ________________________ 4 Jordan High School 1:58.30 ________________________ 5 Cottonwood High School 1:59.19 ________________________ 6 Hunter High School 2:01.59 ________________________ 7 Weber High School 2:03.28 ________________________ 8 Hillcrest High School 2:04.49 ________________________ Heat 2 of 2 Timed Finals 1 Riverton High School 1:56.24 ________________________ 2 Lehi High School 1:54.69 ________________________ 3 Brighton High School 1:54.08 ________________________ 4 Viewmont High School 1:52.91 ________________________ 5 Lone Peak High School 1:53.88 ________________________ 6 Bingham High School 1:54.50 ________________________ 7 West High School 1:55.90 ________________________ 8 American Fork High School 1:56.56 ________________________ Bringham Young University Pool - UHSAA - Site License HY-TEK's MEET MANAGER 5.0 - Page 2 5A Utah -
School Student Name
48th Annual Utah All-State High School Art Show Online Entry Forms Received Before 9:00am on January 23, 2020 SCHOOL STUDENT NAME Alta high Vito Vincent Alta High School Abigail Hakala Alta High School Amanda Keller Alta High School Paige Michaels Alta High School Brynn Parkinson Alta High School Miya Tolman American Academy of Innovation Erick Salazar American Academy of Innovation Elisabeth Williams American Fork Lizzy Driggs American Fork Elle Kennington American Fork Hannah Lorenzana American Fork high school Alexus Allen American Fork High school Emma Allred American Fork High School Hailey Bean American Fork High School Colin Campbell American Fork High School Chaylee Coston American Fork High School Julia Fierro American Fork High School Max Giforos American Fork High School Mabel Hillyer American Fork High School Cambria Johnson American Fork High School Casen Lembke American Fork High School Malissa Lytle American Fork high school sophia mccandless American fork high school Taylor Murphy American fork high school Taylor Murphy American Fork High School Samantha Peterson American Fork High School Brynna Taylor American Fork High School Caden Vest American Fork High School Asia Whitaker American Heritage School Trinity Gibbs American Heritage School James Gifford American Heritage School Rachel Stratton American Heritage School Jinyi Xu American Leadership Academy Nicole Anderson American Preparatory Academy Nicole Anteljevic American Preparatory Academy Michelle Ganbold American Preparatory Academy Maximilian Liebsch American -
PUBLIC NOTICE AGENDA February 23, 2021
Board of Education Tracy J. Miller, President A. Campus Security 7387 S. Campus View Drive Bryce Dunford, First Vice President West Jordan, Utah 84084 Marilyn Richards, Second Vice President www.jordandistrict.org Jen Atwood, Member Niki George, Member Darrell Robinson, Member Matthew Young, Member Officers Anthony Godfrey, Ed.D., Superintendent of Schools John Larsen, Business Administrator PUBLIC NOTICE The Board of Education of Jordan School District will meet in potential closed, study and regular sessions on February 23, 2021 beginning at 4:00 p.m. at the JATC South Campus (Board Conference Room), 12723 S. Park Avenue (2080 West), Riverton, Utah. Patrons may view the meeting online at https://www.youtube.com/user/jordanschooldistrict/live. AGENDA February 23, 2021 1. POTENTIAL CLOSED SESSION - 4:00 p.m. A. Property 2. STUDY SESSION – OPEN MEETING - 4:15 p.m. The Board may engage in discussion, provide administrative direction, or take other action on any of the study session agenda items listed below. A. Naming the New Elementary School in South Jordan Mr. Bryce Dunford, Board Member, District 5 Ms. Becky Gerber, Administrator of Schools Report of survey results on the five names presented at the February 9, 2021 study session. Desired outcome: Board members will vote on the name of the new school in the business meeting. B. Information on Panorama Data Dashboard Mr. Michael Anderson, Associate Superintendent Mr. Travis Hamblin, Director, Student Services Information to Board on Panorama data dashboard being used to give early warning for at-risk students. Desired outcome: Information to Board. C. Calendar Committee Update Mr. -
Wildcat Coaching Staff Brent Myers Associate Head Coach Offensive Line • 5Th Season
2017 BIG SKY CONFERENCE CHAMPIONS 2018 WEBER STATE FOOTBALL TABLE OF CONTENTS 2018 WILDCAT SCHEDULE 2018 Schedule...............................................1 Quick Facts ...................................................2 Big Sky Conference......................................5 Aug. 30 at Utah 6:00 p.m. ROOT Sports .................................................6 ELEVEN Sports .............................................7 Pluto TV .........................................................8 Weber State Coaching Staff .................. 9-26 Sept. 8 at Cal Poly 7:00 p.m. Head Coach Jay Hill ........................... 10-12 Football Support Staff .......................... 23-24 Player profiles ....................................... 25-73 Sept. 15 South Dakota 6:00 p.m. Roster .................................................. 26-27 Pronunciation Guide ................................28 2017 season review and stats ............. 74-78 Wildcat history ...................................... 79-99 Sept. 22 *Northern Colorado 6:00 p.m. Year-by-year records ................................80 Wildcat Head Coaches ....................... 81-82 Year-by-year game results ................. 83-88 Record against opponents ................ 89-93 Oct. 6 *at Northern Arizona 3:30 p.m. All-time national poll rankings ................94 All-time NFL Draft picks ...........................95 All-time CFL Draft picks ...........................96 Oct. 13 *Eastern Washington 4:00 p.m. All-Americans ..................................... 97-98 Retired -
Riverton High School Bell Schedule
Riverton High School Bell Schedule Nosed Blair worrits no houseparents strook sleekly after Ali nabbed confusingly, quite dispensatory. Is Len cactaceous or monolingual when etherifying some amoretto cognised informatively? Sorcerous Georg always sparkling his rest-cure if Wendel is ectopic or revamps engagingly. Please add required info. High schools have one additional grade category entitled postsecondary readiness. Bingham is honored to recognize the hard work and commitment of all of our finalists as we present this years Bingham High School Sterling Scholar Awards. Want to pay your monthly bills in one convenient location? We recognize that you are scheduled club is not only a new password has a broad curriculum. Can try again later than two hours later, riverton high school. The school offers a secure and convenient electronic Free and Reduced Lunch Application to apply for school meal benefits. This file is empty. To make this template yours, start editing it. Office Hours Monday Friday 700 am 300 pm 7350 South 900 E Midvale UT 4047 Office 01-26-6000 Fax 01-26-6009. Click Delete and try adding the app again. Upgrade your website to remove Wix ads. All schools will land two hours later is the usual bell schedule. There for many Honors and Advanced Placement and Concurrent Enrollment courses available. Please leave this year by helping him or bring it where the riverton high school has been sent and many colleges and improve student through years of how our efforts to conduct athletic events. Never miss his or servers. The Composite score is the average of the four test scores, rounded to the nearest whole number. -
Online Entry Forms Received Before 9:00Am on Saturday January 26, 2019
Online Entry forms received before 9:00am on Saturday January 26, 2019 47th Annual Utah All-State High School Art Show School Student Name Alta High Erika Woods Alta High School Kate Adams Alta High School Zeta Bsharah Alta High School brayden hall Alta High School Darby Hayes Alta High school Caden Myrick Alta High School Maddie Penrod Alta High School Maleia Stockwell Alta High School Lydia Stueber Alta high school Norine Summers Alta High School lauren williams Alta High School Kallie Young Alta High-School ethan thayne American Fork Brinley Cummings American Fork Audrey Mortensen American Fork High School Brooklyn Alldredge American Fork High School Alexis Brown American Fork High School Kayla Byers American Fork High School Charlotte Crane American Fork High school Makenna Eldredge American Fork High School Max Giforos American Fork High School Savannah Hainsworth American Fork High School Brooke Harris American Fork High School Kayla Lind American Fork High School Savannah Lisonbeee American Fork High School Malissa Lytle American Fork High School Savannah McKenzie American Fork High School Zackery Olson American Fork High School Zoe Perrett American Fork High School Taylor Roberts American Fork High School Abigail Townsend American Fork High School Aubrey Vest American Fork High School Adelyne Ward American Fork Highschool Dawson Dayna American Fork Highschool Grace Jensen American International School of Utah Jules Dressler American International School of Utah Trenten Mansfield American International School of Utah Min Nguyen -
CHNA Report 2016
Intermountain Riverton Hospital Community Health Needs Assessment 2016 Riverton Hospital 12600 South 3741 West Riverton, Utah 84065 Intermountain Riverton Hospital 2016 Community Health Needs Assessment 1 Table of Contents Summary 3 Background 5 Defining the Hospital Community 5 2016 Community Health Needs Assessment 8 CHNA Process Planning, Governance and Collaboration 8 Methodology 9 Community Input 9 Health Indicators 10 Area Deprivation Index 12 Prioritization 14 Results 16 Community Input 16 Significant Health Need Description 17 Prioritized Health Indicator Data 18 Strategies to Address the Need 33 Impact Evaluation of Strategies Addressed in Previous CHNA 33 Conclusion 34 To make comment 34 Acknowledgements 34 Appendix A 35 Appendix B 40 Intermountain Riverton Hospital 2016 Community Health Needs Assessment 2 Summary Intermountain Healthcare created a system-wide Community Health Needs Assessment (CHNA) process to be used by each of its hospitals to identify local area health needs and understand how to help people live the healthiest lives possible. Intermountain Riverton Hospital collaborated with the Salt Lake County Health Department and the Utah Department of Health to identify health indicators, gather data, analyze, and then prioritize those indicators to determine the significant health needs to address over the next several years. Health improvement activities to address the prioritized need are detailed in a separate implementation plan. As a result of this extensive needs assessment and prioritization process, described in the following pages, Riverton Hospital and Intermountain identified the priority health need as: Prevention of prediabetes, high blood pressure, depression, and prescription opioid misuse This report focuses on the adult health needs of the Riverton Hospital community. -
Credit Guidelines
Credit Guidelines for Graduation from Secondary Schools 2020-2021 Board of Education Bryce Dunford, President Tracy J. Miller, Vice President Matthew Young, Secretary Jen Atwood Janice Voorhies Tracy Miller Marilyn Richards Darrell Robinson ______________ Dr. Anthony Godfrey Superintendent of Schools John Larsen Business Administrator Revised – November 2019 0 Credit Guidelines for Graduation from Secondary Schools TABLE OF CONTENTS Table of Contents 1 Credit Committee Members 3 Introduction 3 I. Credit for Regular Coursework 4 Graduation Requirements 4 Course and Credit Requirements 4 Credit for Grading Period/Schedule Changes 5 Summer Graduates 5 Partial-Day Schedules 6 Residency Requirements 6 Military Children 6 Dual Enrollment 7 Statewide Online Education Program 7 Concurrent Enrollment 8 Proctoring Services 8 Test for Credit 9 National Collegiate Athletic Association (NCAA) Clearinghouse Guidelines 9 II. Programs of Study 10 Traditional High Schools 10 Online Courses for Grades 9-12 10 Jordan Academy for Technology & Careers (JATC) 11 Valley High School 11 Teen Parent Program 11 River’s Edge School 12 South Valley School 12 Southpointe Adult High School 12 III. Transfer Credit 14 Transfer Credit from Accredited Institutions 14 Transfer Credit from Non-Accredited Institutions/Programs 15 Foreign Exchange Study 15 International Students 15 1 Credit Guidelines for Graduation from Secondary Schools IV. Make-up Credit for Failed Classes & Grade Forgiveness 16 Jordan District Make-up Program Guidelines 16 Program Development, Administration, and Security 16 Grading 16 Fees 17 Accountability 17 Valley High Summer School 17 Utah High School Athletic Association (UHSAA) Eligibility Exception 17 Out-of-District Credit for Enrichment/Acceleration 18 Make-up Courses/Programs Outside of Jordan School District 18 Grade Forgiveness 18 V. -
Athletics/Activities Handbook 2017-18
Athletics/Activities Handbook 2017-18 Last Updated: June 6, 2018 Table of Contents Region III Board of Managers 3 Region Activity Chairperson 4 Coaches/Advisor Representatives 5 School Rosters 6 Directions to Schools 13 Region III General Policies 2016-2017 16 Admission Fees and Tickets 16 Supervision of Region Activities, Tournaments and Meets 16 Accommodations for Visiting Teams 16 Officials 16 Eligibility of Players 17 Sportsmanship Policies 17 Event Scheduling and Participation 19 Activity Limitations 19 Seeding for State – Procedures for Breaking Ties of Standings 19 Region Board of Manager Governance 20 REGION III Play-in Game Policy and Procedures 22 Region III Play-in Game Financial Form 23 Trophies and Awards 24 School District Calendars 25 Baseball 27 Basketball 29 Arbiterpay for BB and Spring sports Cross Country 33 Drama 34 Drill Team 36 Football 43 Forensics/Debate 46 Golf 49 Music 53 Soccer 55 Softball 61 Swimming 64 Tennis 66 Track and Field 72 Volleyball 76 Wrestling 78 2 Last Updated: June 6, 2018 Region III Board of Managers Herriman High School 801-567-8530 (fax) 801-567-8545 James Birch (Chair) 11917 South 6000 West Herriman, UT 84096 ATHLETIC DIRECTOR: Brad Tingey ext. 78556 East High School 801-583-1661 (fax) 801-584-2927 Greg Maughan 840 South 1300 East Salt Lake City, UT 84102 ATHLETIC DIRECTOR: Skip Lowe ext. 2417 Copper Hills High School 801-256-5304 (fax) 801-256-5393 Bryan Veazie 5445 New Bingham Hwy West Jordan, UT 84081 ATHLETIC DIRECTOR: Darby Freeland ext.75332 Riverton High School 801-256-5800 (fax) 801-256-5880 Carolyn Gough 12476 South 2700 West Riverton, Utah 84065 ATHLETIC DIRECTOR: Dan Henderson ext. -
Region IV Table of Contents
Region IV Table of Contents Board of Managers ................................................................................................................ 2 Region Activity Chairperson ................................................................................................ 3 Coaches Representatives ....................................................................................................... 4 School Rosters ...................................................................................................................... 5 Directions to Region IV Schools ........................................................................................ 14 General Policies 2013-2014 ................................................................................................ 17 Trophies and Awards .......................................................................................................... 26 Contest Limitations ............................................................................................................. 27 Policies and Schedules Baseball ............................................................................................................................... 29 Basketball ............................................................................................................................ 34 Cross Country ..................................................................................................................... 38 Drama .................................................................................................................................