Recycling of Aircraft: State of the Art in 2011
Total Page:16
File Type:pdf, Size:1020Kb
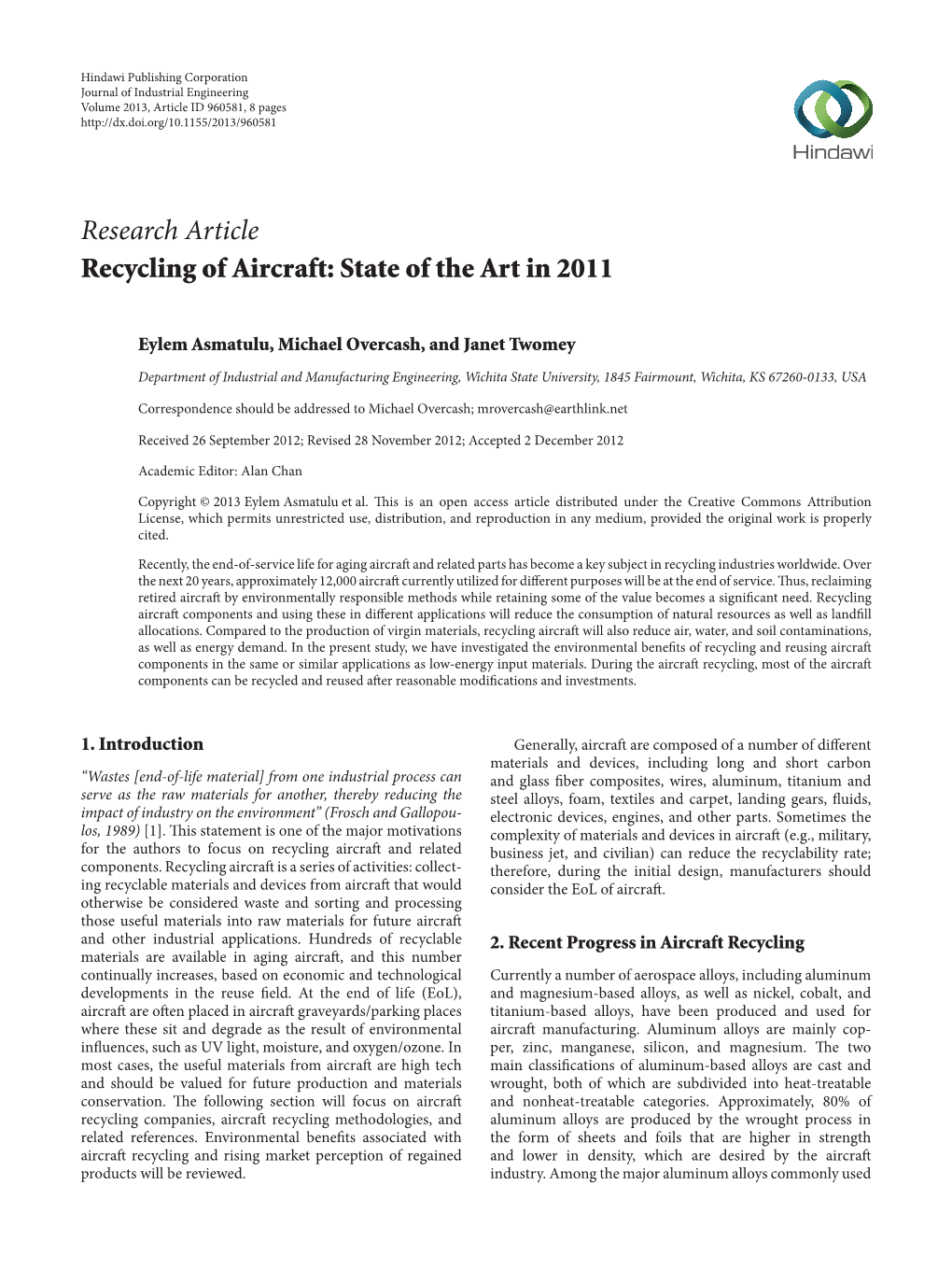
Load more
Recommended publications
-
Titanium Recycling in the United States in 2004
U.S. Department of the Interior U.S. Geological Survey Titanium Recycling in the United States in 2004 By Thomas G. Goonan U.S. GEOLOGICAL SURVEY CIRCULAR 1196–Y FLOW STUDIES FOR RECYCLING METAL COMMODITIES IN THE UNITED STATES II U.S. Department of the Interior KEN SALAZAR, Secretary U.S. Geological Survey Marcia K. McNutt, Director U.S. Geological Survey, Reston, Virginia: 2010 For product and ordering information: World Wide Web: http://www.usgs.gov/pubprod Telephone: 1–888–ASK–USGS For more information on the USGS—the Federal source for science about the Earth, its natural and living resources, natural hazards, and the environment: World Wide Web: http://www.usgs.gov Telephone: 1–888–ASK–USGS Any use of trade, product, or firm names is for descriptive purposes only and does not imply endorsement by the U.S. Government. Although this report is in the public domain, permission must be secured from the individual copyright owners to reproduce any copyrighted materials contained within this report. Suggested citation: Goonan, T.G., 2010, Titanium recycling in the United States in 2004, chap. Y of Sibley, S.F., ed., Flow studies for recy- cling metal commodities in the United States: U.S. Geological Survey Circular 1196, p. Y1–Y16, available online at http://pubs.usgs.gov/circ/circ1196-Y/. III FOREWORD As world population increases and the world economy expands, so does the demand for natural resources. An accurate assessment of the Nation’s mineral resources must include not only the resources available in the ground but also those that become available through recycling. -
2008 Environment Report
2008 Environment Report Creating Pioneering a better future new technologies Measuring Reducing our progress our environmental footprint 2008 Environment Report CEO Message | Pioneering Technologies | Stewardship | Operational Performance | Community Investment » Jim McNerney Chairman, President and Message from Jim McNerney Chief Executive Officer Mary Armstrong Vice President of Environment, Health and Safety Environmental Affiliations Boeing participates in focused, progressive and action-oriented programs to improve environmental performance. Climate change and pollution are serious global concerns. Recognizing that, Boeing has set a clear strategy to take action on protecting our eco-system. Our task is to find a way to reduce the environmental impact of our operations and of our products and services. It’s a momentous challenge. Aerospace is an essential part of modern life; it helps drive economic growth and prosperity, and it brings the people of the world closer together. Because of the tremendous benefits aerospace brings to the world, our industry— and our company with it—is growing. So we have charted a pathway with clearly defined actions for Boeing to address our impact on the environment: • As a technology leader, we will continue to pioneer environmentally progressive products and services and bring them to market. • As a leader in aerospace, we are bringing the industry together to become more aligned on environmental-improvement opportunities. • And as a responsible corporate citizen and neighbor, we are focused on reducing energy use, greenhouse gas emissions, pollution and waste at our facilities even as our business grows. Page 2 2008 Environment Report CEO Message | Pioneering Technologies | Stewardship | Operational Performance | Community Investment » Jim McNerney Chairman, President and (continued from page 2) Chief Executive Officer Boeing has a strong legacy of improving fuel efficiency and reducing noise in its Mary Armstrong products. -
Scrapping and Recycling
ICAO HQ, Montréal, Canada 9 − 10 SEPTEMBER 2014 • Europe’s largest Aeronautics Research Programme ever • Environmental objectives, mainly CO2 and noise reduction (from ACARE) • €1.6B value, split 50/50 between the Commission (cash) and Clean Sky members and partners (in kind) • 570 participants • Integrated breakthrough technologies, up to full scale demonstrators • CleanSky2 is coming…. (€4bn) AiMeRe Project • AIrcraft MEtals REcycling aimereproject.org • Eco-Design topic area of CleanSky • Goals: Assess the dismantling process and propose process improvements, provide recommendations for Design for Environment – WP1: State of the art – WP2: Dismantling process – WP3: Processing and metallurgical trials – WP4: Potential industrial applications – WP5: Dissemination Aircraft End of Life • Why recycle aircraft? – Prevent image loss – Avoid parking costs – Minimize env. impacts – Make money from part-out and metal sales Materials – Create new European recovery industry process • New ‘urban mine’ Materials Recovery Process I. Decontamination II. Part-out (under EASA Part 145) III. Transfer to the dismantling platform IV. Extraction of landing gears V. Preparation of dismantling VI. Interior stripping VII. Customer cuts VIII. Specific materials extraction IX. Scrapping X. Shredding and sorting Dismantling Process video http://www.euronews.com/2013/09/16/aviation-from-scrap- to-eco-design/ Recycling Routes Today’s challenges in aircraft recycling • Manual vs mechanical separation of materials – Quality vs cost • Missing end-use applications -
Sustainable Aviation – a Decade of Progress 2005-2015
SUSTAINABLE AVIATION A DECADE OF PROGRESS 2015 2005 www.sustainableaviation.co.uk Progress Report 2015 Executive summary In 2005 the UK aviation industry was a world first in coming together to establish Sustainable Aviation (SA) committed to working together towards a sustainable future. In 2015, 10 years on, the industry remains committed to making a positive contribution to the British economy, and meeting the needs of society for air transport whilst minimising environmental and social impacts. In this time, significant steps have been taken to reduce UK aviation’s environmental impacts - for example reducing SA airline carbon emissions by 20 million tonnes since 2005 whilst carrying 19% more passengers. This is SA’s 5th Progress Report highlighting 10 years of achievement by this unique coalition of UK industry. Our progress against the seven key goals of the SA strategy is presented in this report with the key highlights presented in the infographic on the next page. The timeline below and infographic overleaf, summarise key highlights from SA’s work. SA will continue its focus on working together to reduce environmental impacts, including: Updating the SA CO2 Road-Map Publishing discussion papers on air quality and the social-economic impacts of the industry Working with the UK Government to realise the opportunities shown in our Road-Maps. Specifically this will involve; o Maintaining financial investment in UK aerospace research and development o Enabling airspace modernisation in the UK o Supporting the development of sustainable fuels for aviation in the UK SA looks forward to working with a wide range of stakeholders in delivering this future work, from both within and outside the aviation sector. -
Doing Business in Mississippi Fdi Resource Guide Doing Business in Mississippii
DOING BUSINESS IN MISSISSIPPI FDI RESOURCE GUIDE DOING BUSINESS IN MISSISSIPPII Mississippi boasts a business-friendly environment, where we do what is necessary to help companies increase speed to market, limit risk, and increase profitability. As a foreign company, it can be intimidating to enter a new market, but we are here to help. This document provides guidance on doing business in the state of Mississippi. 1 Nissan’s Vehicle Assembly Plant located in Canton, JAPAN Mississippi employs more than 6,500 Mississippians. CONTENT 01 Geography 02 Infrastructure 03 Legal 04 Permitting 05 Taxation 06 Operating Costs 07 Data 08 International Directory 09 Contact 21 01 | GEOGRAPHY Mississippi is located in the southeastern region of the United States and is bordered by the states of Alabama, Tennessee, Arkansas, Louisiana, the Mississippi River, and the Gulf of Mexico. Centrally located between the East and West Coasts, Mississippi provides easy access to major U.S. markets, including Mobile, New Orleans, Dallas, Atlanta, Nashville, Houston, St. Louis, and Memphis - a United States distribution hub. Like most states in the United States, Mississippi is divided into administrative subdivisions called counties. There are 82 counties in Mississippi, each comprised of multiple cities or municipalities. The state capital is the city of Jackson, located in Hinds County. Distance from Jackson, Mississippi, to Major U.S. Markets City Distance (km) Atlanta, Georgia 613 Dallas, Texas 646 Houston, Texas 709 Chicago, Illinois 1,190 Detroit, Michigan 1,520 3 CANADA UNITED STATES MS MEXICO 4 02 | INFRASTRUCTURE ROADS AIRPORTS The primary mode of transportation in Six commercial airports, two of which Mississippi is the automobile. -
2016 Hamidrezazahedi.Pdf
UNIVERSITÉ DE MONTRÉAL END-OF-LIFE EFFICIENT DISASSEMBLY OF COMPLEX STRUCTURES USING PRODUCT AND PROCESS FOCUSED APPROACH HAMIDREZA ZAHEDI DÉPARTEMENT DE GÉNIE MÉCANIQUE ÉCOLE POLYTECHNIQUE DE MONTRÉAL THÈSE PRÉSENTÉE EN VUE DE L’OBTENTION DU DIPLÔME DE PHILOSOPHIAE DOCTOR (GÉNIE MÉCANIQUE) AÔUT 2016 © Hamidreza Zahedi, 2016. UNIVERSITÉ DE MONTRÉAL ÉCOLE POLYTECHNIQUE DE MONTRÉAL Cette thèse intitulée : END-OF-LIFE EFFICIENT DISASSEMBLY OF COMPLEX STRUCTURES USING PRODUCT AND PROCESS FOCUSED APPROACH présentée par : ZAHEDI Hamidreza en vue de l’obtention du diplôme de : Philosophiae Doctor a été dûment acceptée par le jury d’examen constitué de : M. BOUKHILI Rachid, Doctorat, président M. MASCLE Christian, Doctorat, membre et directeur de recherche M. BAPTISTE Pierre, Doctorat, membre et codirecteur de recherche Mme BROCHU Myriam, Ph. D., membre M. VARNIER Christophe, Doctorat, membre externe iii DEDICATION This thesis is gratefully dedicated to my parents Zahra and Asghar, beloved wife Audrey and wonderful sister Sima, for all your support along the way. iv ACKNOWLEDGEMENTS The author wishes to express his sincere gratitude to his advisors, Dr. Christian Mascle and Dr. Pierre Baptiste for their endless guidance, insightful comments and moral support throughout every step of this research. I would like to thank Centre Technologique en Aérospatiale (CTA) in Montréal and specially Mr. Yves Chamberlan and Paul-Anthony Ashby. Throughout my studies, I have had the pleasure of working with them, being trained and a member of their team. I am very appreciative of my parents for their enthusiasm, my wife for supporting this endeavor from the day we met, and my sister for her positive energy. -
Sustainable Decommissioning: Wind Turbine Blade Recycling
1 SUSTAINABLE DECOMMISSIONING: WIND TURBINE BLADE RECYCLING REPORT FROM PHASE 1 OF THE ENERGY TRANSITION ALLIANCE BLADE RECYCLING PROJECT With contributions from: 3 CONTENTS SUMMARY Acknowledgements 2 Thirty years ago, it would have been hard to imagine that Summary 3 offshore wind could power every home in the UK. Today, Report Scope 6 that target is one of the key pillars of the UK Government’s Anatomy of a Wind Turbine Blade 8 climate change policy. This vision has been driven by the passion of wind industry pioneers to forge this new sector Defining ‘Circular’ and ‘Recycling’ 10 and make renewable energy a commercial reality. Governance Landscape 12 Future Market Opportunity 16 Current Methods of Blade Disposal 24 Composites Sector by Sector 28 With this has come an unrelenting drive to develop systems on oil and gas rigs. Both now face the challenge high-performance, next-generation wind turbines that of finding good solutions for decommissioning these Review of Composite Recycling Methods 36 will achieve the necessary energy capture and cost materials in the coming decades. Mechanical 39 efficiency. For the blades, composite layers of stiff For the wind sector, that is an urgent challenge here and carbon or glass fibres in a resin matrix were found to be now as the first generation of wind farms are starting to Thermal 40 the optimal material, delivering exceptional strength, reach the end of their service life. Longer term, by 2050, stiffness-to-density and flexibility in processing. Chemical 42 the global offshore wind industry will decommission As the wind industry has grown, it has become a major up to 85GW of capacity (cumulatively, and assuming Reprocessing 44 user of these materials, which have long been a solution a 25-year lifecycle). -
2013 Environmental Report
The Boeing Company 2013 Environment Report Building a Better Planet At Boeing, we aspire to be the strongest, best and best-integrated aerospace- based company in the world— for today and tomorrow. The Boeing Company Contents Boeing is the world’s largest aerospace Our Commitment 1 company and leading manufacturer Performance Targets 2 of commercial airplanes and defense, space and security systems. The top Designing the Future 3 U.S. exporter, Boeing supports airlines Cover photo: The and U.S. and allied government custom- Innovating to Zero 10 innovative Phantom ers in more than 150 countries. Our Inspiring Global Collaboration 16 Eye is powered by products and tailored services include clean-burning commercial and military aircraft, satel- Results 21 hydrogen and emits only water in the lites, weapons, electronic and defense atmosphere. systems, launch systems, advanced (Boeing photo) information and communication sys- tems, and performance-based logistics Photo above: The and training. With corporate offices in 737 MAX, currently Chicago, Boeing employs more than in development, features a 13 percent 174,000 people across the United smaller carbon States and in 70 countries. In addition, footprint than today’s our enterprise leverages the talents of most fuel-efficient hundreds of thousands of skilled people single-aisle airplanes. working for Boeing suppliers worldwide. (Boeing photo) Our Commitment: Leadership Message Five years ago, we set ambitious goals to reduce our environmental footprint while significantly growing our business. Jim McNerney Chairman, President and Chief Executive Officer The Boeing Company Kim Smith Boeing Vice President Environment, Health and Safety Thanks to the dedication and hard work of and solid waste sent to landfills, and zero high-altitude aircraft runs on clean-burning everyone at Boeing, we met those goals, revenue-adjusted growth in hazardous hydrogen and leaves only water vapor in and are prepared to make further progress materials, by 2017. -
RECYCLING ALUMINUM AEROSPACE ALLOYS Subodh K
Title of Publication Edited by TMS (The Minerals, Metals & Materials Society), Year RECYCLING ALUMINUM AEROSPACE ALLOYS Subodh K. Das and J. Gilbert Kaufman Secat, Inc., 1505 Bull Lea Road, Lexington, KY 40511 Keywords: Aluminum alloys; Recycling, Aircraft Abstract idle in “graveyards” around the USA. Yet it ha s been impractical to reuse the metal in these planes because of the combination of the differences in compositions of older obsolete aircraft and Abstract: For decades, thousands of obsolete private, civil, and those of new aircraft, often having special performance military aircraft have been sitting in “graveyards,” while the requirements requiring specialized alloy compositions. demand for recycled aluminum continues to increase. The aircraft provide an obvious source of valuable metal. However cost- Driving Forces for This Study effective recycling of aircraft is complex because aircraft alloys are (a) typically relatively high in alloying elements and (b) The driving forces for this study to enable large-scale recycling of contain relatively higher levels of impurities than required of aluminum aircraft alloys are very clear and very strong. many newer aircraft alloys to optimize their toughness and other performance characteristics. This paper describes (a) potential • The production of aluminum as “secondary metal” (i.e., aircraft recycling process, (b) the technical and logistic producing it by recycling) requires o nly about 2.8 challenges, and (c) options to address those challenges in a kWh/kg of metal produced while primary aluminum practical and cost-effective manner. A program addressing these production requires about 45 kWh/kg of metal issues is laid out in this paper. -
Air Quality and Greenhouse Gas Goals Support
Air Quality and Greenhouse Gas Goals Support Final Report Prepared for: Maryland Department of Transportation Maryland Aviation Administration February 2018 [Blank Page] Task 1 Air Emissions & Greenhouse Gas Goals Formulation Report Prepared for: Maryland Department of Transportation Maryland Aviation Administration July 2017 [Blank Page] EXECUTIVE SUMMARY This Task 1 Report is the first among six tasks that will collectively provide the Maryland Department of Transportation’s Maryland Aviation Administration (MDOT MAA) with overall guidance and specific recommendations aimed at reducing air emissions and greenhouse gasses (GHGs) considered appropriate for Baltimore/Washington International Thurgood Marshall Airport (BWI Marshall) and Martin State Airport (MTN). In particular, this initial undertaking focused on achieving the following Targets (or Steps): . Describe Goal-Setting Process - Outline the approach to Task 1; . Describe Existing Policy and Measures - Identify relevant policies and measures already in- place (or planned) by MDOT MAA at BWI Marshall and MTN; . Compare to Other Airports - Evaluate initiatives at other U.S. and international airports for potential inclusion into the MDOT MAA program; . Formulate MDOT MAA Goals - Develop and assess effectiveness and feasibility of added or expanded emission and GHG reduction measures; . Develop Strategy - Designate objectives and measures for advancing and achieving these goals; and . Set Up Task 2 - Lay out the approach and endpoints for undertaking this second task. Given the breadth of possible goals (or “end-points”) directed at air quality and GHGs, a hierarchical approach to setting MDOT MAA candidate goals is based on the criteria of Appropriate, Meaningful and Achievable. From this, the two principal goals of (i.) Air Emission Reductions at BWI Marshall and Martin State Airports and (ii.) Minimizing MDOT MAA’s Carbon Footprint serve as “bridges” to the corresponding and requisite objectives and supporting measures. -
100 Pioneers for Efficient Resource Management PDF
CRONIMET Ferroleg. 100 Pioneers for Efficient GmbH Resource Management Karlsruhe Examples of excellence in Baden-Württemberg from all parts of industry Best practice case of CRONIMET Ferroleg. GmbH www.springer.com/de/book/9783662567449 Recycling industry Development of systems and technology for aircraft engine and landing gear recycling in Baden-Württemberg CRONIMET Ferroleg. GmbH, Karlsruhe Technology/Process Technology: Aircraft recycling Measure: Secondary raw material extraction of economically critical raw materials Background and objectives The recycling (urban mining) of engines and Decommissioned aircraft are a source of high landing gear from old aircraft extracts numer- quality components and materials. Some of ous relevant technology metals and thus these engine and landing gear components serves particularly to ensure the availability of have a limited service life and must be raw materials. In the study analysing critical replaced after a defined number of revolu- raw materials for Baden-Württemberg’s state tions, operating hours and landings in aircraft strategy for resource efficiency, titanium, for maintenance hangars. Before the materials example, was classified as critical. Strategically can be introduced into the secondary raw important raw materials are to be recycled material cycle, the components must be ren- through the interventions. In concrete terms, dered unusable through a documented pro- high-temperature super alloys, titanium and cess. The reason for this process is to prevent high-quality aluminium and stainless steel suspected unapproved parts and inferior imi- super alloys are to be recovered from engines tations (bogus parts) from appearing on the and used to secure Baden-Württemberg‘s world market. The materials in question accu- raw materials supply. -
Toward a Strategic Approach to End-Of-Life Aircraft Recycling Projects a Research Agenda in Transdisciplinary Context
Journal of Management and Sustainability; Vol. 3, No. 3; 2013 ISSN 1925-4725 E-ISSN 1925-4733 Published by Canadian Center of Science and Education Toward a Strategic Approach to End-of-Life Aircraft Recycling Projects A Research Agenda in Transdisciplinary Context Samira Keivanpour1, Daoud Ait-Kadi1 & Christian Mascle2 1 Mechanical Engineering Department, Faculty of Science and Engineering, Laval University, Quebec, Canada 2 Mechanical Engineering Department, ÉcolePolytechnique de Montréal, Montreal, Canada Correspondence: Samira Keivanpour, Mechanical Engineering Department, Faculty of Science and Engineering, Laval University, Quebec, G1V 0A6, Canada. Tel:1-418-656-2131. E-mail: [email protected] Received: March 8, 2013 Accepted: April 1, 2013 Online Published: July 3, 2013 doi:10.5539/jms.v3n3p76 URL: http://dx.doi.org/10.5539/jms.v3n3p76 Abstract The number of planes at the end of life is increasing. Innovative management practice of aircraft at the end of life can be considered as a transdisciplinary context. Moreover, regarding dynamics and multidimensionality of aircraft recycling projects, conventional management systems cannot be sufficient and responsive. The purpose of this paper is to address a research agenda that support various aspects of dynamics and transdisciplinarity of end of life aircraft recycling projects (EOLARP) by a strategic conceptual framework. Four sections of the framework including business model, market and industry, knowledge management and performance measurement make a basis for addressing the essential issues in EOLARP business ecosystem, which needs an incorporated approach of different disciplines and players. Further studies and works on each arena in this framework are valuable in overcoming difficulties facing managers and strategic partners in EOLARP.