Corporate Responsibility Report at a Glance
Total Page:16
File Type:pdf, Size:1020Kb
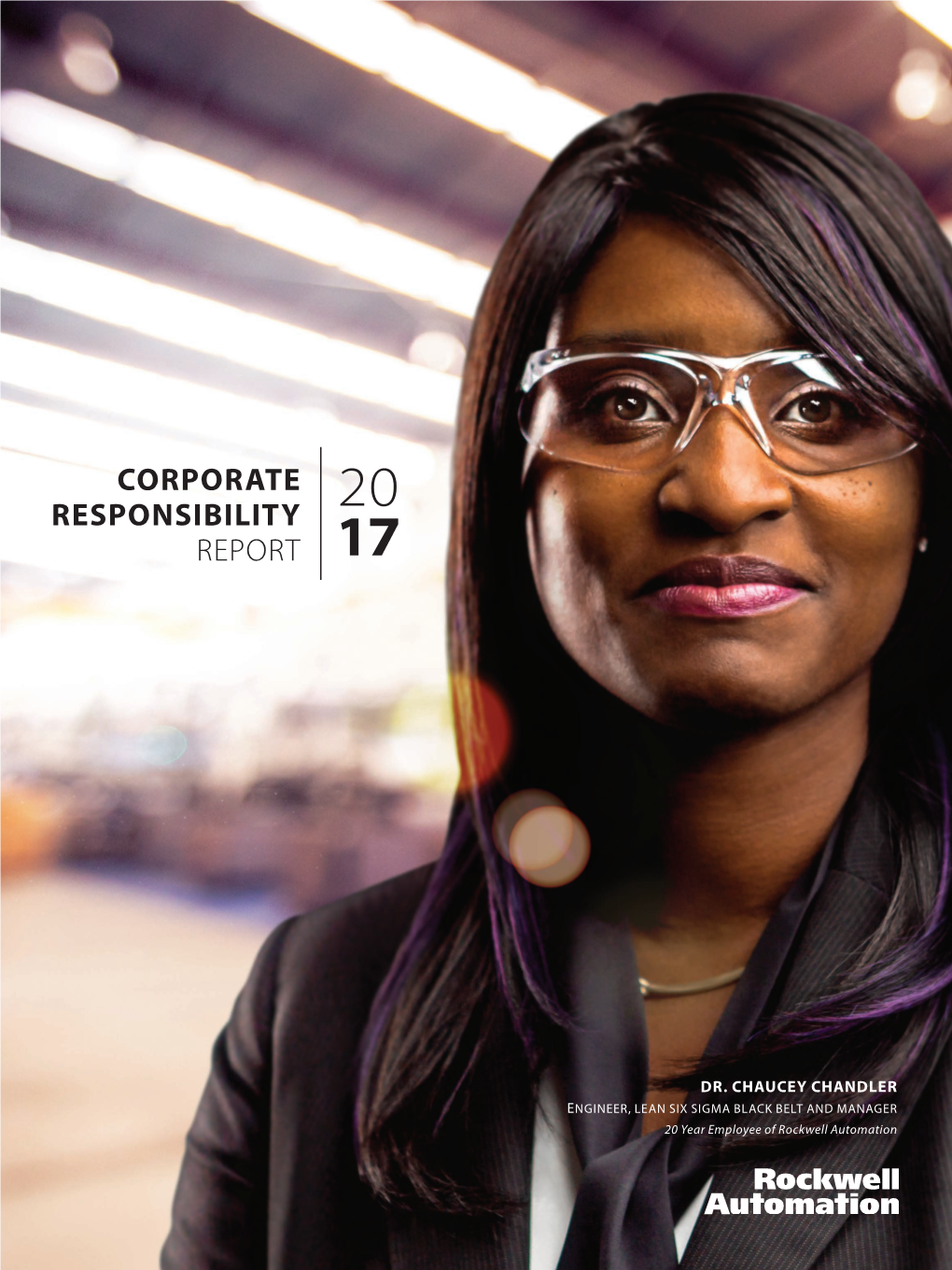
Load more
Recommended publications
-
Human Capital Management Industry Update Winter 2019
HUMAN CAPITAL MANAGEMENT STAFFING & RECRUITMENT – INDUSTRY UPDATE | Winter 2019 Houlihan Lokey Human Capital Management Houlihan Lokey is pleased to present its third Human Capital Management (HCM) Industry Update. Once again, we are happy to share industry insights, a public markets overview, a snapshot of relevant macroeconomic indicators, transaction announcements, and related detail. We believe this newsletter will provide you with the most important and relevant information you need to stay up to date with the HCM industry. We would also like to encourage you to meet with us at the SIA Executive Forum in Austin, Texas on February 25-28, 2019 where we would be happy to share recent market developments and further insights. If there is additional content that you would find useful for future updates, please do not hesitate to contact us with your suggestions. Regards, Thomas Bailey Jon Harrison Andrew Shell Managing Director Managing Director Vice President [email protected] [email protected] [email protected] 404.495.7056 +44 (0) 20 7747 7564 404.495.7002 Additional Human Capital Management Contacts Larry DeAngelo Pat O’Brien Alex Scott Bennett Tullos Mike Bertram Head of Business Services Associate Financial Analyst Financial Analyst Financial Analyst [email protected] [email protected] [email protected] [email protected] [email protected] 404.495.7019 404.495.7042 404.926.1609 404.926.1619 404.495.7040 Human Capital Management – Coverage by Subsector Staffing & VMS/MSP/RPO Talent Payroll/ HR Consulting/ Recruitment Management & PEO Benefits Admin Development -
Employing People with Intellectual and Developmental Disabilities
Employing People with Intellectual and Developmental Disabilities A Report by the Institute for Corporate Productivity (i4cp) Talent that drives business results pg. 7 A ready pool of ideal workers pg. 10 A good fit that exceeds expectations pg. 12 Fewer challenges and more support than expected pg. 16 Employers featured: In partnership with: Peers. Research. Tools. Data. © 2014 by the Institute for Corporate Productivity (i4cp). All rights reserved. No part of this publication may be reproduced, distributed, or transmitted in any form or by any means, including photocopying, recording, or other electronic or mechanical methods, without the prior written permission of the publisher, except in the case of brief quotations embodied in critical reviews and certain other noncommercial uses permitted by copyright law. For permission requests, write to i4cp.com/contact. i4cp RESEARCH Chief Research and Marketing Officer: Kevin Martin Senior Vice President of Research: Jay Jamrog Senior Researcher: Joe Jamrog Data Analyst and Survey Manager: Andrew Dixon i4cp EDITORIAL Managing Editor & Director of Research Services: Lorrie Lykins Creative Director & Senior Editor: Eric Davis Employing People with Intellectual and Developmental Disabilities FOREWORD Anthony Kennedy Shriver For over 25 years, Best Buddies International has focused its efforts on the inclusion of individuals with intellectual and developmental disabilities (IDD). Tremendous progress has been made in creating opportunities for friendships between people with and without IDD in middle schools, high schools, and colleges. Further expansion has taken place with our Citizens program, and people in communities around the world are experiencing the gifts that come from building meaningful relationships with people with IDD. -
Manpowergroup Employment Outlook Survey Global
ManpowerGroup Employment Outlook Survey Global Q1 2018 SMART JOB NO: 16003 QUARTER 1 2018 CLIENT: MANPOWERGROUP SUBJECT: MEOS Q118 – GLOBAL – TWO COLOUR – A4 SIZE: A4 DOC NAME: 16003_Global_2COL_A4_Q118 PAGE: 1 ARTWORK SIZE: 297mm x 210mm DATE: 23.11.17 87 CHARTERHOUSE STREET • LONDON EC1M 6HJ • TEL +44 (0)20 7553 4744 ManpowerGroup interviewed nearly 59,000 employers across 43 countries and territories to forecast labor market activity in Quarter 1 2018. All participants were asked, “How do you anticipate total employment at your location to change in the three months to the end of March 2018 as compared to the current quarter?” (Additional details on page 2) Contents Global Employment Outlook 1 International Comparisons – Americas 3 International Comparisons – Asia Pacific 7 International Comparisons – EMEA 10 About the Survey 17 About ManpowerGroup® 18 Global Employment Outlook SMART JOB NO: 16003 QUARTER 1 2018 CLIENT: MANPOWERGROUP SUBJECT: MEOS Q118 – GLOBAL – TWO COLOUR – A4 SIZE: A4 DOC NAME: 16003_Global_2COL_A4_Q118 PAGE: 2 ARTWORK SIZE: 297mm x 210mm DATE: 23.11.17 87 CHARTERHOUSE STREET • LONDON EC1M 6HJ • TEL +44 (0)20 7553 4744 Global Employment Outlook Qtr on Qtr Change Yr on Yr Change Quarter 1 2018 Q4 2017 to Q1 2018 Q1 2017 to Q1 2018 Quarter 1 2018 Net Employment Outlook % -15-10 -5 0510 15 20 25 30 35 40 45 Americas Taiwan +25% Argentina 9 (8)1 2 (0)1 2 (2)1 Japan +24% Brazil 5 (6)1 4 (4)1 13 (13)1 India +22% Canada 8 (11)1 2 (1)1 2 (1)1 United States +19% Colombia 5 (9)1 -2 (2)1 -1 (0)1 + Costa Rica 20 (18)1 3 (-1)1 -
Hrexecutive.Com September 2019
SEPTEMBER 2019 • $ 8 . 9 5 Chief People Officer David Fairhurst is playing a key role as the storied brand adapts to a changing business. McDonald’s PAGE 14 New Golden Age What Drives The Case for a HR’s Elite: Tech Adoption? Specialty-Drug Strategy Class of 2018 Page 18 Page 25 Page 28 H9-19p01_FC.indd 1 8/8/2019 2:09:35 PM B:10.625” T:10.25” S:9.375” B:13.875” S:12.75” T:13.5” “I’m working for beauty that begins with nature.” — Valerie Vilbon, Boutique Manager L’Occitane en Provence The things we work for are what define us. At ADP we’re designing a better way to work, so you can achieve what you’re working for. HR, Talent, Time Management, Benefits & Payroll. Informed by data and designed for people. Learn more at design.adp.com ADP, the ADP logo, and Always Designing for People are trademarks of ADP, LLC. H9-19p02_ADP.indd 2 8/5/2019 2:42:51 PM HN16425_ADP168_M02.indd Created: 6-18-2019 5:32 PM 1_Final Path:Premedia:Prepress:_ADP:2019:16425_ADP168:Final:Prepress:HN16425_ADP168_M02.indd Modified:6-19-2019 10:19 AM Proof Job Description Mechanical Specifications Colors Font Families Contacts Initial Date Billing#: HN16425 Artist: Jorge.Soto Cyan Taub Sans (Light, Regular Italic, Regular, Medium; OpenType) Studio Manager H. WEINTRAB/M. JOHNSON Labor: HN16425 Previous: Chin.Liew Magenta Proofreader None Proofreading: HN16425 Bleed: 10.625” x 13.875” Yellow Print Producer Arianna Talan OOP: HN16425 Trim: 10.25” x 13.5” Black Account Executive None Tracking#: ADP168_M02 Safety: 9.375” x 12.75” Art Director None Client: ADP Viewing: None Copywriter None Brand: None Gutter: None Product: None Scale: None Media: Magazine Final Size10.25 x 13.5 Caption: L’Occitane Links Mode PPI Links Mode PPI Production Notes ADP_ADP168_01b_SW_LOccitane_a0561_V1.tif 1672 ppi CMYK None adp_logo_tagline_0111.eps RELEASE_STAMP.ai Please contact Arianna Talan at 212.886.4100 with any questions regarding these materials. -
2020 Milwaukee Business Journal Insert
COMMUNITY PARTNER RECOGNITION 2020 COMMUNITY CAMPAIGN Every year, thousands of organizations support United Way’s Publication Sponsor: Community Campaign through workplace campaigns, corporate gifts, sponsorships, and more. We thank everyone who helped create lasting change in our community. You are the example of what it means to Live United. THANK YOU 2020 COMMUNITY CAMPAIGN ALL-STARS TOTAL COMBINED GIVING $4.8 MILLION $3.6 MILLION $3.4 MILLION $3.2 MILLION $2.5 MILLION $2.3 MILLION $1.8 MILLION $1.7 MILLION $1.6 MILLION $1 MILLION $1 MILLION UnitedWayGMWC.org Thank you to all the organizations who ran a workplace campaign and/or supported 2020 TOTAL COMBINED GIVING United Way with a sponsorship, in-kind donation, corporate gift, foundation gift, or treasury gift. SUPER STARS Meijer GUARDIAN raSmith Michael Best & Friedrich LLP Regal Beloit Corporation - Grafton $500,000 - $999,999 Milwaukee County $10,000 - $24,999 Rite Hite Corporation Foundation Milwaukee Journal Sentinel Rogers Behavioral Health Foundation Children’s Wisconsin Advicent Pieper Electric, Inc./Ideal Mechanical RSM US LLP Foley & Lardner LLP AHEAD R&R Insurance Services, Inc. Ruekert & Mielke, Inc. GE Healthcare Alight Solutions State of Wisconsin S & C Electric Company Harley-Davidson Motor Company American Red Cross STRATTEC Security Corporation salesforce.com Johnson Financial Group in Southeastern Wisconsin Target Schlossmann’s Automotive Group ManpowerGroup Anderson Packaging, LLC University of Wisconsin - Milwaukee School District of Waukesha MGIC Investment Corporation Avaya, Inc. UW Credit Union Sentry Equipment Corp. Quarles & Brady LLP Briohn Building Corporation von Briesen & Roper, s.c. ServiceNow, Inc. U.S. Bank Carroll University Wells Fargo Shorewest Realtors Check Point Sikich LLP CIBC Cleary Gull SoftwareONE, Inc. -
University of Wisconsin-Milwaukee Is Committed to and Community, and Learn a New STUDENTS Global Engagement Through Its Curriculum, Research Activities, Language
A WORLD-CLASS UNIVERSITY UNIVERSITY OF WISCONSIN MILWAUKEE ONE OF ONLY TWO PUBLIC UNIVERSITIES IN WISCONSIN OFFERING DOCTORAL FIVE FORTUNE 500 DEGREES TOP 131 welcomeNOTABLE UWM CORPORATIONS RESEARCH UNIVERSITIES ALUMNI INCLUDE IN MILWAUKEE CARNEGIE CLASSIFICATION OF INSTITUTIONS OF HIGHER EDUCATION SATYA NADELLA NORTHWESTERN MUTUAL RANKED #4 IN (CEO of Microsoft) MANPOWERGROUP HIGHEST PERCENTAGE OF LUIS ARREAGA WEC ENERGY GROUP ENGINEERING DOCTORAL (U.S. ambassador) HARLEY-DAVIDSON DEGREES AWARDED TO FOREIGN NATIONALS MITCH WHITMORE ROCKWELL AUTOMATION 1,000+ (Olympic speedskater) BY SCHOOL THE AMERICAN SOCIETY OF UNDERGRADUATE KIMBERLEY CHONGYON MOTLEY ENGINEERING EDUCATION IN 2017 (First foreign lawyer working in Afghanistan) RESEARCH JIM RYGIEL OPPORTUNITIES (Academy Award-winner, visual effects for Lord of the Rings) 30,000 works of art at the 800 MILWAUKEE + ART MUSEUM MUSICAL ACTS PERFORM AT SUMMERFEST, one of the largest music festivals in the world UWM.EDU uwm and milwaukee WELCOME Milwaukee is the largest city in Wisconsin with a regional population of 1.5 million people and the center of business, industry and culture in the state. The city is known for its year-round festivals, beautiful lakefront, friendly community and historic architecture. UWM is located in a quiet, safe and attractive residential area and is within walking distance of Lake Michigan. Milwaukee’s downtown is a short car or bus ride away. All UWM students have access to the B.O.S.S. safe ride pick- up service, which provides students with secure transportation every day, and U-PASS, a transit program through the Milwaukee County bus system. From outdoor concerts and film festivals to food trucks and 24-hour bike races, there’s always something to see and do in Milwaukee. -
2013 Cws Summit - Berlin Delegates by Company
2013 CWS SUMMIT - BERLIN DELEGATES BY COMPANY Countries associated with Summit delegates and Staffing Industry AstraZeneca Pharmaceuticals LP | Hone, Victoria - Global Analysts personnel denote country of residence and not individual Resourcing - UK nationality, nor area of job responsibility Atos | Arnold, Andreas - Procurement Line Manager - Germany A Atos | Campserveux, Anna - Staffing, Subcontractors & Indirects Purchasing Manager - France ABB Inc | Kaneberg, Mats - Country Contract Manager - Sweden Atos | Kromer, Christian - Commodity Manager, Strategic Buyer - ABB Inc | Lindell, Tony - Contract Manager Staffing Services - Germany Sweden Atos | Lawrenson, Ian - Global Buyer, Contingent Workforce - UK ABB Management Services Ltd | Baechli, Roland - Country Supply Atos Origin | Aylott, Martin - Global Category Manager Staffing Chain Manager - Switzerland Services - UK ABB Management Services Ltd | Schmid, Thomas - Head Global B Contracted Services Commodity - Switzerland ABN AMRO Bank | Henselmans, Marc - Team Manager External Babcock International | Waters, Naomi - Procurement, Group HR Staffing - Netherlands Category - UK ABN AMRO Bank | Neher, Frank - Category Manager - Baker Hughes | Schwalbe, Martin - Senior Staffing Representative Netherlands - Germany Adecco Group France | Koch, Yann - International Account Balfour Beatty | Lee, Nick - Resourcing & HR Business Partner - Director - France UK Advantage xPO | Browne, Karen - President, Advantage xPO - USA Bank of America | LeBret, Kerry - Vendor Relationship Manager - Advantage -
30 Nov Hires Report
Hire Heroes USA Confirmed Hires 2017 Through November 30 Service (Last) Branch Service Rank Other Hiring Company Name Position Hired For Army CW-2 Special Security Officer Navy CW-4 Black Knight Financial Services IT Production Manager Army CW-4 ASM Research Benefits Lead Army 0-1 General Dynamics Manufacturing Engineer Army 0-1 Scribe America Medical Scribe Gwinnett County Office of Strategy & Army 0-1 Performance Mgmt. Business Analyst Marines 0-1 Campus Hollywood Instructor- Theater History and Acting Air Force 0-1 Global Threat & Risk Analyst Navy 0-1 Advanced Systems Development Help Desk Specialist Army W-5 United Airlines Pilot Marines W-5 San Diego Passport Agency Passport Support Associate Army W-5 Selective Service System Program Analyst Marines W-5 Ulta Beauty Warehouse Manager Army W-5 DOD Pilot Military Program Analyst-Organization and Personnel Force Development Army W-5 US Army DOD Directorate Army W-5 NES Associates Technical Director Army W-5 Program Manager Army W-5 AFS Army Fleet Service Test Flight Pilot Army W-5 Investigator Navy W-5 R3 Strategic support Group Manager Army W-5 AFSC/Magellan Federal Training Center Manager Navy W-5 Naval Systems Incorporated Senior Logistics Analyst Army W-5 Aviation Specialties Unlimited Aviator Marines W-5 District Manager Army W-4 TFW - Tsay Ferguson-Williams Deputy Project Manager Army W-4 CACI International Lessons Learned Analyst Army W-4 Colorado Springs Police Department Criminal Investigator Army W-4 Intel Corporation D1D Manufacturing Technician Army W-4 Erickson Air Crane -
MANPOWERGROUP INC. (Name of Registrant As Specified in Its Charter)
Table of Contents UNITED STATES SECURITIES AND EXCHANGE COMMISSION Washington, D.C. 20549 SCHEDULE 14A INFORMATION Proxy Statement Pursuant to Section 14(a) of the Securities Exchange Act of 1934 (Amendment No. ) Filed by the Registrant ☒ Filed by a Party other than the Registrant ☐ Check the appropriate box: ☐ Preliminary Proxy Statement ☐ Confidential, for Use of the Commission Only (as permitted by Rule 14a-6(e)(2)) ☒ Definitive Proxy Statement ☐ Definitive Additional Materials ☐ Soliciting Material under § 240.14a-12 MANPOWERGROUP INC. (Name of registrant as specified in its charter) (Name of person(s) filing proxy statement, if other than the registrant) Payment of Filing Fee (Check the appropriate box): ☒ No fee required. ☐ Fee computed on table below per Exchange Act Rules 14a-6(i)(1) and 0-11. (1) Title of each class of securities to which the transaction applies: (2) Aggregate number of securities to which the transaction applies: (3) Per unit price or other underlying value of the transaction computed pursuant to Exchange Act Rule 0-11 (set forth the amount on which the filing fee is calculated and state how it was determined): (4) Proposed maximum aggregate value of the transaction: (5) Total fee paid: ☐ Fee paid previously with preliminary materials. ☐ Check box if any part of the fee is offset as provided by Exchange Act Rule 240.0-11(a)(2) and identify the filing for which the offsetting fee was paid previously. Identify the previous filing by registration statement number, or the Form or Schedule and the date of its filing. (1) Amount Previously Paid: (2) Form, Schedule or Registration Statement No.: (3) Filing Party: (4) Date Filed: Table of Contents Notice of 2018 Annual Meeting of Shareholders and Proxy Statement Table of Contents MANPOWERGROUP INC. -
Moving the Needle 2020 Research Report
ADVANCINGADVANCING INCLUSIVEINCLUSIVE LEADERSHIPLEADERSHIP MOVING THE NEEDLE 2020 RESEARCH REPORT MWi’s GOAL: 25% WOMEN DIRECTORS IN THE TOP 50 25% BY 2025 WISCONSIN PUBLIC COMPANIES BY 2025 2020 RESEARCH REPORT KEY FINDINGS: PERCENTAGE OF WOMEN ON BOARDS CONTINUES TO INCREASE BENEFITS OF GENDER-BALANCED BOARDS DIRECTORS Women need to hold at least 3 board seats Top 50 Wisconsin Public Companies to maximize diversity benefits Research from scholars and organizations has found 21.1% of board members are women, up • that women need to hold at least 3 board seats to from 20.8% in 2019 create a “critical mass,” which can lead to better financial • 26% (13/50) of companies have 3 or more performance and create an environment in which women directors, compared to 30% in innovative ideas can spring from gender diversity. 2019. Decrease largely due to women Source: Catalyst, Quick Take: Women on Corporate Boards (March 13, 2020). board members retiring • 8% of companies (4/50) have 4 or more women board members, compared to 6.7% in 2019 POWER OF 3 2015-2020 WISCONSIN COMPANIES WITH 28% (9/32) of newly elected directors • 3 OR MORE WOMEN DIRECTORS are women 15 12 9 EXECUTIVES Top 50 Wisconsin Public Companies 6 • 21.9% of company executives are women, an increase from 21.2% in 2019 3 • 38% of companies (19/50) have 3 or more women executives, up 12% from 2019 2015 2016 2017 2018 2019 2020 Note: 2020 decrease largely due to women board members retiring GENDER DIVERSITY OF S&P 500 COMPANIES S&P 500 COMPARED TO WISCONSIN TOP 50 COMPANIES Wisconsin Top 50 PERCENTAGE OF BOARD SEATS HELD BY WOMEN REACHES ALL-TIME HIGH Source: ISS Analytics 27% 26.5% 24% 22% 21% 20% 19% 18% 21.1% 17% 20.8% 16% 16% 18.9% 16.9% 17.6% 15.5% 15.8% 14.4% 14.5% 14% 12.8% 2010 2011 2012 2013 2014 2015 2016 2017 2018 2019 2020 2 WOMEN DIRECTORS STEADILY INCREASING TOTAL DIRECTORS WOMEN DIRECTORS % WOMEN ManpowerGroup Inc. -
The Securities and Exchange Commission Has Not Necessarily Reviewed the Information in This Filing and Has Not Determined If It Is Accurate and Complete
The Securities and Exchange Commission has not necessarily reviewed the information in this filing and has not determined if it is accurate and complete. The reader should not assume that the information is accurate and complete. OMB APPROVAL UNITED STATES SECURITIES AND EXCHANGE COMMISSION OMB Number: 3235-0006 Washington, D.C. 20549 Oct 31, FORM 13F Expires: 2018 FORM 13F COVER PAGE Estimated average burden hours per 23.8 response: Report for the Calendar Year or Quarter Ended: 06-30-2014 Check here if Amendment Amendment Number: This Amendment (Check only one.): is a restatement. adds new holdings entries. Institutional Investment Manager Filing this Report: Name: US BANCORP \DE\ Address: U.S.BANCORP 800 NICOLLET MALL MINNEAPOLIS, MN 55402 Form 13F File 028-00551 Number: The institutional investment manager filing this report and the person by whom it is signed hereby represent that the person signing the report is authorized to submit it, that all information contained herein is true, correct and complete, and that it is understood that all required items, statements, schedules, lists, and tables, are considered integral parts of this form. Person Signing this Report on Behalf of Reporting Manager: Name: Beverly A. Antonich Title: Vice President Phone: 612-344-6230 Signature, Place, and Date of Signing: Beverly A. Antonich Minneapolis, MN 08-13-2014 [Signature] [City, State] [Date] Report Type (Check only one.): X 13F HOLDINGS REPORT. (Check here if all holdings of this reporting manager are reported in this report.) 13F NOTICE. (Check here if no holdings reported are in this report, and all holdings are reported by other reporting manager(s).) 13F COMBINATION REPORT. -
Live United®
2016 COMMUNITY PARTNER RECOGNITION LIVE UNITED® Publication Sponsor: UnitedWayGMWC.org 2016 THANK YOU ALL-STARS $ 5.7 M $ 4.1 M $ 3.1 M $ 3.0 M $ 2.6 M $ 1.9 M $ 1.7 M $ 1.6 M $ 1.3 M $ 1.2 M $ 1.1 M 2 2016 COMBINED GIVING SUPER STARS Roundy’s Supermarkets, Inc CMA/Flodyne/Hydradyne Vesta, Inc. State of Wisconsin COA Youth & Family Centers VJS Construction Services $500,000 - $999,999 Target Collective Goods Wal-Mart, Inc. United Community Center, Inc. Community Health Charities Wenthe-Davidson Engineering Company Adient US LLC United Way of Greater Milwaukee of Wisconsin West Allis - West Milwaukee School Ascension Wisconsin & Waukesha County, Inc. Cramer-Krasselt District Bon-Ton Stores, Inc. von Briesen & Roper, s.c. Crivello Carlson S.C. Western Products a Division of Douglas Children’s Hospital of Wisconsin D+H Dynamics LLC Foley & Lardner LLP Davis & Kuelthau, S.C. Western States Envelope Company Froedtert Health FUTURE STARS Diversified Insurance Solutions Willis Towers Watson ManpowerGroup DRS Power & Control Technologies Wipfli LLP Marcus Corporation $25,000 - $49,999 Elliott’s Ace Hardware Wixon, Inc. MGIC Investment Corporation Elmbrook School District YWCA Southeast Wisconsin Quarles & Brady LLP Badger Mutual Insurance Company BloodCenter of Wisconsin EMC Insurance Companies Inc. U.S. Bank Equitable Bank SSB Wells Fargo Bostik, Inc. Bradley Center Sports Faustel, Inc. ADVOCATE & Entertainment Corp. Fiduciary Real Estate Development Inc. $5,000 - $9,999 SHINING STARS Bruno Independent Living Aids, Inc. First Business Bank - Milwaukee CBRE Fiserv, Inc. A.B. Data, Ltd. $250,000 - $499,999 Century Fence Company Geis Building Products Inc.