Environmental Impacts of Phosphorus Recovery from a ``Product
Total Page:16
File Type:pdf, Size:1020Kb
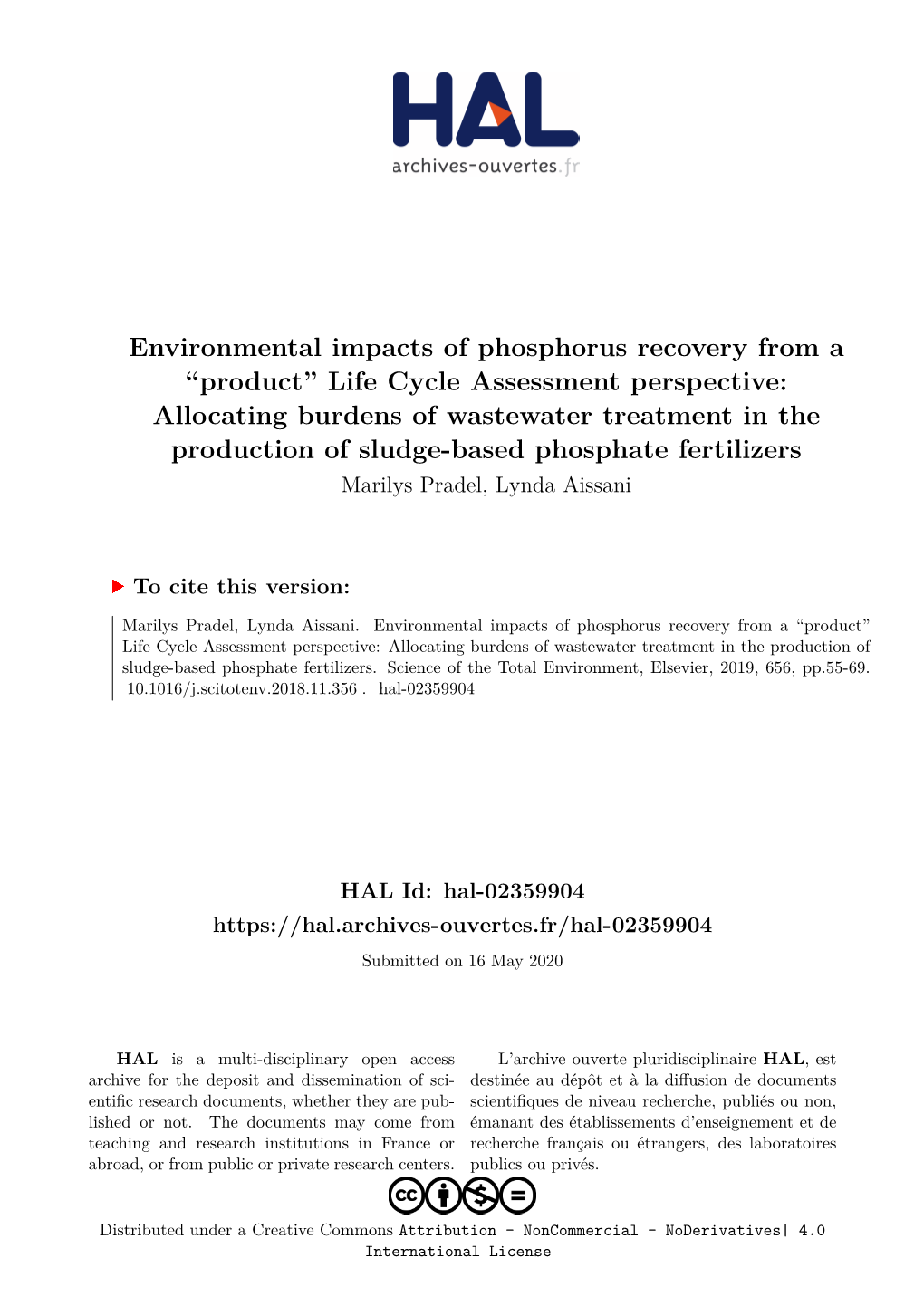
Load more
Recommended publications
-
Global Availability of Phosphorus and Its Implications for Global Food Supply: an Economic Overview by Markus Heckenmüller, Daiju Narita, Gernot Klepper
Global Availability of Phosphorus and Its Implications for Global Food Supply: An Economic Overview by Markus Heckenmüller, Daiju Narita, Gernot Klepper No. 1897 | January 2014 Kiel Institute for the World Economy, Hindenburgufer 66, 24105 Kiel, Germany Kiel Working Paper No. 1897 | January 2014 Global Availability of Phosphorus and Its Implications for Global Food Supply: An Economic Overview Markus Heckenmüller, Daiju Narita, Gernot Klepper Abstract: Being of crucial importance for agricultural production and also having experienced significant price volatility, phosphate and its future availability have drawn growing attention from both academics and the public over the last years. This paper overviews the recent literature and data on the availability of phosphorus and discusses the economic aspects of phosphate scarcity by describing major price determinants of the global phosphate market. We show that past price fluctuations of phosphate rock and phosphate fertilizers are not a reflection of physical phosphate rock depletion but rather attributable to numerous other demand- and supply-side factors. Given the current reserve estimates for phosphate rock, neither an exhaustion of global reserves nor a peak event is likely to occur within this century. However, these estimates are subject to a significant degree of uncertainty. Moreover, the global distribution of phosphate production and reserves is highly skewed and has the potential to pose a threat to food security in developing countries through factors such as the volatility -
Peak Phosphorus – the Next Inconvenient Truth
Peak Phosphorus – The Next Inconvenient Truth Arno Rosemarin Stockholm Environment Institute Phosphorus Seminar Gamla Stan May 19, 2010 The linear path of phosphorus in modern times (Princeton Univ.) Vaccari, 2009 countries as well, mainly in the north; so th the north; so well, mainly in countries as Sulfuric acid which is usedin 90% of the Phosphorus Reserves are in 90% ofthePhosphorus 5 Countries extracting the phosphorus is extracting ere are several geopolitical us challenges ahead of ere are several found in a limited number of a found in Caldwell, SEI, based on USGS, 2009 Phosphate Rock Economic Reserves, 1997-2009 (from USGS summaries) 20 000 000 18 000 000 16 000 000 China k 14 000 000 12 000 000 China Moroc c o & W. Sahara osphate roc South Africa hh 10 000 000 United States Morocco/West Sahara Jordan 8 000 000 Other countries 00 tonnes p 00 1 6 000 000 4 000 000 2 000 000 0 1997 1998 1999 2000 2001 2002 2003 2004 2005 2006 2007 2008 2009 The definition of economic rock reserves is not standardised. China has changed the definition twice after joining the WTO in 2003. In 2009 they downgraded their economic reserve by 30%. There is a need for a world standard and global governance – still non-existent. Depletion of Global Economic Phosphorus Reserves 16000000 14000000 12000000 10000000 years from 2008 tons cc reserve (2% scenario) 8000000 2% annual increase in extraction reserve (1% scenario) 00 metri 00 1% annual increase in extraction 1 6000000 4000000 010 22 2000000 rin, SEI n USGS data aa oo 0 Rosem Based 1 4 7 10131619222528313437404346495255586164 -
Phosphate Rocks!
Essay By: Jacob Kollen Phosphate Rocks! INTRODUCTION On approximately two thirds of the world’s arable land, phosphorus is a plant growth limiting nutrient (Lambers et al., 2013). Agriculture utilizes roughly 80% of the mined phosphate rock as fertilizer, with the remaining 20% being utilized in products such animal feed supplements, food preservatives, pesticides, fungicides, herbicides, water treatments, cosmetics, and metallurgy (Sattari, 2012). Currently we derive approximately 63% of our phosphorus fertilizer from phosphate rock, with the remainder being derived from animal manure, sewage sludge, and guano (Rittman, 2011). Phosphate rock reserves are finite, which leads to a predicament: we will run out of phosphate rock eventually. The concept, stressed by peak resource theory, is that once global reserves are depleted by half, economic factors will drive resource prices high and unattainable by many (Cordell and White, 2013). Phosphorus does not have a substitute in biomass production. Unlike energy resources, we cannot look to other resources to mitigate our dependency upon phosphate rock (Gilbert, 2009). Phosphorus has potential to be recycled (Rittman, 2011). On a large scale, if agriculture gears itself to derive phosphorus fertilizer from recycled phosphorus we can avoid phosphorus resource scarcity. BACKGROUND Low levels of phosphorus in soils results in phosphorus deficiencies in crops which will grow poorly and can be diagnosed by observing leaves turning a blue-green color. Farmers apply phosphorus fertilizers to agricultural soils to mitigate crop growth limitation by phosphorus. Known global phosphate rock reserves are concentrated in just a handful of countries. Phosphate rock reserves that contain at least 8.5 x 1013 tons of phosphate rock are located in Morocco, China, Algeria, Syria, Jordan, South Africa, the United States and Russia (Jasinski, 2013). -
Capturing the Lost Phosphorus
Marquette University e-Publications@Marquette Civil and Environmental Engineering Faculty Civil, Construction, and Environmental Research and Publications Engineering, Department of 8-2011 Capturing the Lost Phosphorus Bruce E. Rittmann Arizona State University at the Tempe Campus Brooke Mayer Marquette University, [email protected] Paul Westerhoff Arizona State University at the Tempe Campus Mark Edwards Arizona State University at the Polytechnic Campus Follow this and additional works at: https://epublications.marquette.edu/civengin_fac Part of the Civil and Environmental Engineering Commons Recommended Citation Rittmann, Bruce E.; Mayer, Brooke; Westerhoff, Paul; and Edwards, Mark, "Capturing the Lost Phosphorus" (2011). Civil and Environmental Engineering Faculty Research and Publications. 34. https://epublications.marquette.edu/civengin_fac/34 Marquette University e-Publications@Marquette Civil, Construction and Environmental Engineering Faculty Research and Publications/College of Engineering This paper is NOT THE PUBLISHED VERSION; but the author’s final, peer-reviewed manuscript. The published version may be accessed by following the link in the citation below. Chemosphere, Vol. 84, No. 6 (August 2011): 846-853. DOI. This article is © Elsevier and permission has been granted for this version to appear in e-Publications@Marquette. Elsevier does not grant permission for this article to be further copied/distributed or hosted elsewhere without the express permission from Elsevier. Capturing the Lost Phosphorus Bruce E. Rittmann -
Peak Phosphorus
Peak Phosphorus A Potential Food Security Crisis TARIEL MÓRRÍGAN Global Climate Change, Human Security, and Democracy Global & International Studies University of California Social Sciences & Media Studies Building, Room 2006 Santa Barbara, CA 93106-7065 [email protected] ~ February 21, 2010 Peak Phosphorus “There are no substitutes for phosphorus in agriculture.” ~ United States Geological Survey, 2009 Summary • Phosphorus is an element necessary for all life . Phosphorus is one of the three major nutrients required for plant growth: nitrogen (N), phosphorus (P), and potassium (K). • Global phosphorus production most likely peaked in 1989 . If global phosphorus production has not yet peaked, it will likely do so by 2033. • The quality of remaining phosphate rock is decreasing and the production costs are increasing. • Global reserves will start to run out within 50–100 years . • Once phosphorus supplies are exhausted, phosphorus will need to be recovered and reused in order to avoid a massive global food security crisis . There are no substitutes for phosphorus in agriculture . • In 2007–2008, the price of phosphate rock increased dramatically worldwide due to increased agricultural demand and limited supplies of phosphate rock. The average U.S. price in 2008 was more than double that of 2007, and was four-times greater than that of 2004. Average spot prices from North Africa and other exporting regions increased more than five-times the average price in 2007. • Most of the world's farms do not have or do not receive adequate amounts of phosphorus . Feeding the world's increasing population will accelerate the rate of depletion of phosphate reserves. -
Missing Global Governance of a Critical Resource Preliminary Findings from 2 Years of Doctoral Research
Paper prepared for SENSE Earth Systems Governance, Amsterdam, 24th-31st August, 2008 The Story of Phosphorus: missing global governance of a critical resource Preliminary findings from 2 years of doctoral research Dana Cordell PhD Candidate [email protected] Institute for Sustainable Futures, University of Technology Sydney, Australia and Department of Water and Environmental Studies, Linköping University, Sweden Abstract Phosphorus is a critical resource for food production in the form of fertilizers, yet current global phosphate reserves could be depleted this century. More concerning is a global peak in phosphorus production – peak phosphorus – based on current official estimates of world resources, is estimated to occur around 2030, only decades after the likely peak in oil production. The situation for phosphorus is worse than for oil however, as there is no substitute for phosphorus in food production. Demand for phosphorus will increase over the next 50 years as the world population is projected to increase by 50% and with changing diets. While the exact timing of peak production might be disputed, it is widely known within the industry that the quality of remaining phosphate rock is decreasing, and costs are increasing. The price of phosphate rock has increased 700% in 14 months alone. Yet unlike water, energy and nitrogen, there is no international organisation which has taken on responsibility for the long-term stewardship or management of phosphorus resources for global food security. Institutional arrangements surrounding the global phosphorus cycle are fragmented and phosphorus sustainability is perceived quite differently by different stakeholders. In the absence of any deliberate international oversight, phosphorus resources are governed by the forces of the international market and national interest. -
From Waste to Plate: Examining the Role of Urban Biosolids in Recycling Phosphorus
FROM WASTE TO PLATE: EXAMINING THE ROLE OF URBAN BIOSOLIDS IN RECYCLING PHOSPHORUS A THESIS PRESENTED TO THE FACULTY OF ARCHITECTURE, PLANNING, AND PRESERVATION COLUMBIA, UNIVERSITY Submitted IN partial FULFILLMENT OF THE REQUIREMENT FOR THE DEGREE MASTER OF SCIENCE IN URBAN PLANNING MARLA WEINSTEIN May, 2013 ABSTRACT Phosphorus, a nutrient found in soil, is vital to plant life and therefore essential to our global food supply. Naturally recycled by ecosystem services, human cities have interrupted this cycle as phosphorus now accumulates in urban areas rather than returning to the land. In turn, we have turned to mined phosphates to supplement fertilizers and ensure our global food supply. As phosphorus deposits are a limited resource, however, we face future phosphorus shortages and threats to the security of our food supply. Biosolids, or treated waste, is a byproduct of our sewage treatment system and represent an opportunity for phosphorus recovery and recycling. This research (1) examines the role of biosolids in replenishing the natural phosphorus cycle and reducing our dependence on mined-phosphates by (2) examining the case study of NYC biosolid management in order to gain insight that can be extracted and applied to other global cities. Ultimately findings suggest biosolids can relink the natural cycle, framing biosolids as a resource, rather than a waste, for urban areas and recommend cities promote biosolid demand through contracting, land application siting, and investments in nutrient recovery technologies. ACKnowledgements A special thanks to: Professor Elliott Sclar, Thesis Advisor Professor Steve Cohen, Thesis Reader Michael, Nancy, & Bethany Weinstein Rebecca Kuss, Samantha Lazar, & Lorie Grushka EXECUTIVE SUMMARY 5 BACKGROUND 6 METHODOLOGY 13 FINDINGS 14 ANALYSIS 17 CONCLUSIONS 20 EXECUTIVE SUMMARY Simply stated, ecosystem services are the benefits we receive from healthy functioning ecosystems. -
The Current Peak Oil Crisis
PEAK ENERGY, CLIMATE CHANGE, AND THE COLLAPSE OF GLOBAL CIVILIZATION _______________________________________________________ The Current Peak Oil Crisis TARIEL MÓRRÍGAN PEAK E NERGY, C LIMATE C HANGE, AND THE COLLAPSE OF G LOBAL C IVILIZATION The Current Peak Oil Crisis TARIEL MÓRRÍGAN Global Climate Change, Human Security & Democracy Orfalea Center for Global & International Studies University of California, Santa Barbara www.global.ucsb.edu/climateproject ~ October 2010 Contact the author and editor of this publication at the following address: Tariel Mórrígan Global Climate Change, Human Security & Democracy Orfalea Center for Global & International Studies Department of Global & International Studies University of California, Santa Barbara Social Sciences & Media Studies Building, Room 2006 Mail Code 7068 Santa Barbara, CA 93106-7065 USA http://www.global.ucsb.edu/climateproject/ Suggested Citation: Mórrígan, Tariel (2010). Peak Energy, Climate Change, and the Collapse of Global Civilization: The Current Peak Oil Crisis . Global Climate Change, Human Security & Democracy, Orfalea Center for Global & International Studies, University of California, Santa Barbara. Tariel Mórrígan, October 2010 version 1.3 This publication is protected under the Creative Commons (CC) "Attribution-NonCommercial-ShareAlike 3.0 Unported" copyright. People are free to share (i.e, to copy, distribute and transmit this work) and to build upon and adapt this work – under the following conditions of attribution, non-commercial use, and share alike: Attribution (BY) : You must attribute the work in the manner specified by the author or licensor (but not in any way that suggests that they endorse you or your use of the work). Non-Commercial (NC) : You may not use this work for commercial purposes. -
The Challenge to Produce More Food and Energy with Less Pollution
Our Nutrient World The challenge to produce more food and energy with less pollution Prepared by the Global Partnership on Nutrient Management Global Overview on Nutrient Management on Nutrient Global Overview in collaboration with the International Nitrogen Initiative Our Nutrient World_reflowed.indd 1 30/01/2013 10:26:10 Published by the Centre for Ecology and Hydrology (CEH), Edinburgh UK, on behalf of the Global Partnership on Nutrient Management (GPNM) and the International Nitrogen Initiative (INI). ISBN: 978-1-906698-40-9 © Centre for Ecology and Hydrology, 2013. This publication is in copyright. It may be quoted and graphics reproduced subject to appropriate citation. Recommended citation: Sutton M.A., Bleeker A., Howard C.M., Bekunda M., Grizzetti B., de Vries W., van Grinsven H.J.M., Abrol Y.P., Adhya T.K., Billen G.,. Davidson E.A, Datta A., Diaz R., Erisman J.W., Liu X.J., Oenema O., Palm C., Raghuram N., Reis S., Scholz R.W., Sims T., Westhoek H. & Zhang F.S., with contributions from Ayyappan S., Bouwman A.F., Bustamante M., Fowler D., Galloway J.N., Gavito M.E., Garnier J., Greenwood S., Hellums D.T., Holland M., Hoysall C., Jaramillo V.J., Klimont Z., Ometto J.P., Pathak H., Plocq Fichelet V., Powlson D., Ramakrishna K., Roy A., Sanders K., Sharma C., Singh B., Singh U., Yan X.Y. & Zhang Y. (2013) Our Nutrient World: The challenge to produce more food and energy with less pollution. Global Overview of Nutrient Management. Centre for Ecology and Hydrology, Edinburgh on behalf of the Global Partnership on Nutrient Management and the International Nitrogen Initiative. -
Phosphorus Recovery and Recycling from Municipal Wastewater Sludge
Aalto University School of Science and Technology Department of Civil and Environmental Engineering Jenni Nieminen PHOSPHORUS RECOVERY AND RECYCLING FROM MUNICIPAL WASTEWATER SLUDGE A Master of Science thesis Submitted for inspection in Espoo, 7 May 2010 Supervisor: Professor Riku Vahala Instructor: M.Sc. (Tech.) Pirjo Rantanen ABSTRACT OF THE MASTER’S THESIS Author and the name of the thesis: Jenni Nieminen Phosphorus recovery and recycling from municipal wastewater sludge Date: 7 May 2010 Number of pages: 96 Department: Civil and Environmental Professorship: Water and Wastewater Engineering Engineering Supervisor: Professor Riku Vahala Instructor: M.Sc. (Tech.) Pirjo Rantanen Keywords : Phosphorus recovery, phosphorus recycling, municipal wastewater sludge, sewage sludge, crystallization, struvite The past decades have witnessed a rising awareness of the finite phosphorus resources and the importance of phosphorus recovery. The world phosphorus resources are estimated to deplete in 60 to 240 years and the world phosphorus production to peak in 2033, creating a need to discover alternative materials to replace phosphate ore. Municipal wastewater sludge is a phosphorus source worth considering, since modern technologies can transfer over 90% of the phosphorus from the wastewater to the sludge fraction. The aim of this thesis is to discuss and overview the current methods for phosphorus recovery from municipal wastewater sludge, ash from sludge incineration, and the liquid phase after anaerobic treatment containing phosphorus in soluble form. The methods for recovery include crystallization and precipitation, wet chemical methods, and thermo•chemical methods. The crystallization and precipitation methods convert phosphorus into solid form with a chemical dosage and pH adjustment. The wet chemical methods recover the phosphorus bound in sludge or ash by leaching it with acid or base, and recovering the resulting dissolved phosphorus with various methods, the most common being the precipitation. -
A Case Study of the Netherlands
sustainability Article An Assessment of the Drivers and Barriers for the Deployment of Urban Phosphorus Recovery Technologies: A Case Study of The Netherlands Marissa A. de Boer *, Anjelika G. Romeo-Hall, Tomas M. Rooimans and J. Chris Slootweg Van’t Hoff Institute for Molecular Sciences, University of Amsterdam, Science Park 904, NL-1098 XH Amsterdam, The Netherlands; [email protected] (A.G.R.-H.); [email protected] (T.M.R.); [email protected] (J.C.S.) * Correspondence: [email protected]; Tel.: +31-(0)6-2850-2959 Received: 8 April 2018; Accepted: 22 May 2018; Published: 29 May 2018 Abstract: Phosphorus (P), being one of the building blocks of life, is essential for a multitude of applications, primarily for fertilizer usage. Sustainable management of phosphorus is becoming increasingly important in light of adverse environmental effects, ambiguous reserves, increasing global demand and unilateral dependence. Recovery of phosphorus from the biggest loss stream, communal wastewater, has the potential to tackle each of these problems. The implementation of phosphorus recovery technologies at wastewater treatment plants is not widespread, despite prolonged efforts primarily done by researchers over the past decade. This study aimed to assess the drivers and barriers of a phosphorus recovery transition. Several key stakeholders involved in this transition in The Netherlands were interviewed. The Netherlands was taken as a case study, since it serves as a frontrunner in the implementation of phosphorus recovery technologies. This study shows that the main barriers from the point of view of fertilizer companies are the different and unclear characteristics of the phosphorus recovery product struvite compared to common fertilizers. -
Price Volatility and Food Security Price Volatility and Food Security
Cover photo: ©FAO/G.Napolitano HLPE REPORT 1 Price volatility and food security Price volatility and food security A report by A report by The High Level Panel of Experts The High Level Panel of Experts on Food Security and Nutrition on Food Security and Nutrition July 2011 July 2011 Secretariat HLPE c/o FAO Viale delle Terme di Caracalla 00153 Rome, Italy Website: www.fao.org/cfs/cfs-hlpe E-mail: [email protected] HLPE REPORT 1 Price volatility and food security A report by The High Level Panel of Experts on Food Security and Nutrition July 2011 Committee on World Food Security High Level Panel of Experts on Food Security and Nutrition Rome, 2011 HLPE Steering Committee members (July 2011) MS Swaminathan (Chair) Maryam Rahmanian (Vice-Chair) Catherine Bertini Tewolde Berhan Gebre Egziabher Lawrence Haddad Martin S. Kumar Sheryl Lee Hendriks Alain de Janvry Renato Maluf Mona Mehrez Aly Carlos Perez del Castillo Rudy Rabbinge Huajun Tang Igor Tikhonovich Niracha Wongchinda HLPE Project Team members Benoit Daviron (Team Leader) Niama Nango Dembele Sophia Murphy Shahidur Rashid This report by the High Level Panel of Experts on Food Security and Nutrition (HLPE) has been approved by the HLPE Steering Committee. The views expressed do not necessarily reflect the official views of the Committee on World Food Security, of its members, participants, or of the Secretariat. This report is made publicly available and its reproduction and dissemination is encouraged. Non- commercial uses will be authorized free of charge, upon request. Reproduction for resale or other commercial purposes, including educational purposes, may incur fees.