Methoxy Poly (Ethylene Glycol) Methacrylate - Based
Total Page:16
File Type:pdf, Size:1020Kb
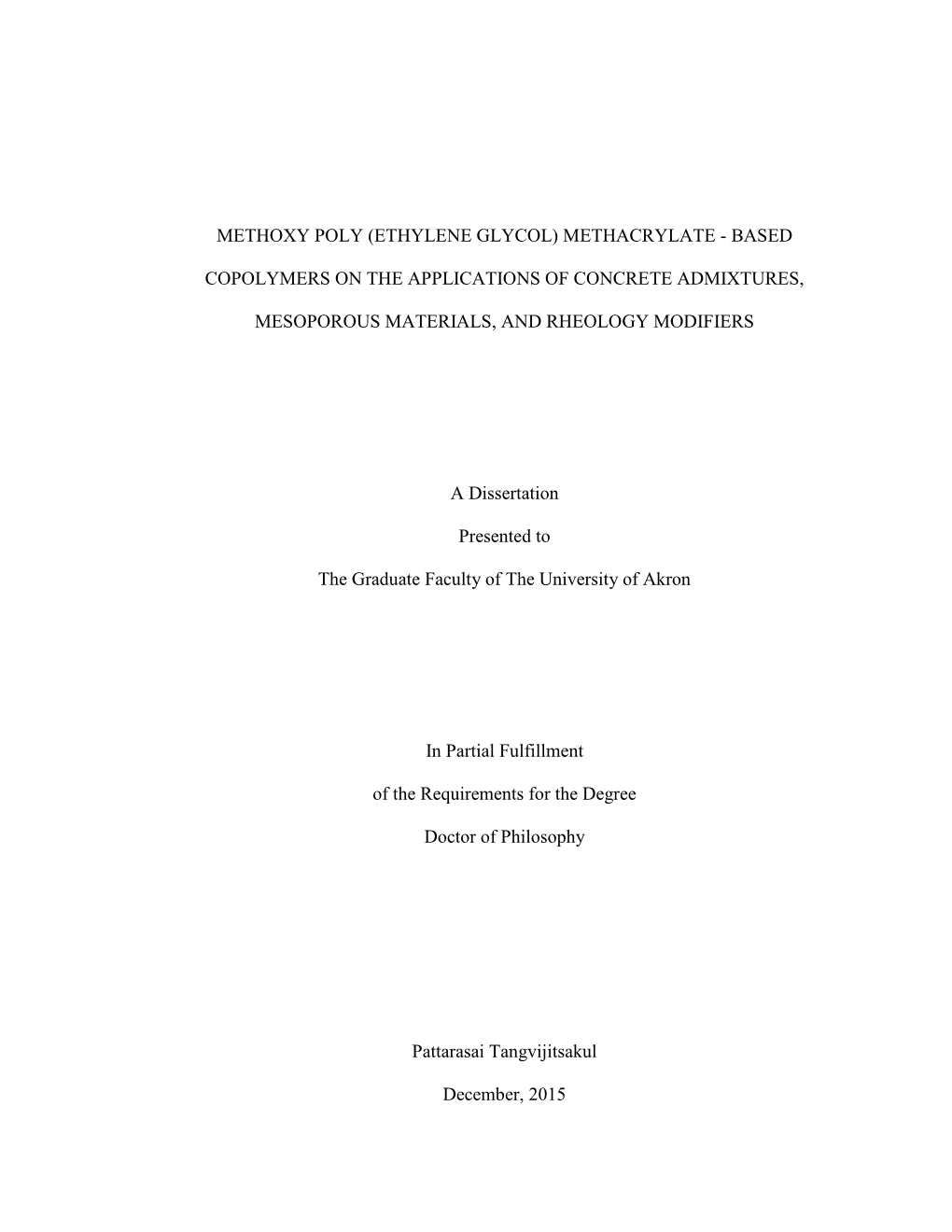
Load more
Recommended publications
-
Acid-Base Properties, Deactivation, and in Situ Regeneration of Condensation Catalysts for Synthesis of Methyl Methacrylate
ACID-BASE PROPERTIES, DEACTIVATION, AND IN SITU REGENERATION OF CONDENSATION CATALYSTS FOR SYNTHESIS OF METHYL METHACRYLATE MAKARAND R. GOGATE', JAMES J. SPIVEY', AND JOSEPH R. ZOELLER2 'Research Triangle Institute, 3040 Cornwallis Road, RTP, NC 27709-2 194 2Eastman Chemical Company, Kingsport, TN, 37662-5 150 ABSTRACT Condensation reaction of a propionate with formaldehyde is a novel route for synthesis of methyl methacrylate (MMA). The reaction mechanism involves a proton abstraction from the propionate on the basic sites and activation of the aliphatic aldehyde on the acidic sites of the catalyst. The acid-base properties of ternary V-Si-P oxide catalysts and their relation to the MMA yield in the vapor phase condensation of formaldehyde with propionic anhydride has been studied for the first time. Five different V-Si-P catalysts with different atomic ratios of vanadium, silicon, and phosphorous were synthesized, characterized, and tested in a fixed-bed microreactor system. A V-Si-P 1:10:2.8 catalyst gave the maximum condensation yield of 56% based on HCHO fed at 300 "C and 2 atm and at a space velocity of 290 cc/g cateh. A parameter called the "q-ratio" has been defined to correlate the condensation yields to the acid-base properties. The correlation of q-ratio with the condensation yield shows that higher q-ratios are more desirable. The long-term deactivation studies on the V-Si-P 1: 10:2.8 catalyst at 300 "C and 2 atm and at a space velocity of 290 cc/g cat-h show that the catalyst activity drops by a factor of nearly 20 over a 180 h period. -
SYNTHESIS and PROPERTIES of SOME ARALKYL Hymoperoxides
SYNTHESIS AND PROPERTIES OF SOME ARALKYL HYmOPEROXIDES DISSERTATION Presented in Partial Fulfillment of the Requirements for the Degree Doctor of Philosophy in the Graduate School of The Ohio State University By ARLO d / bCGGS, B.S., M.S. The Ohio State University 1954 Approved by: Department of Chemistry ACKNOWLEDGEMENT The author wishes to express sincere appreciation to Professor Cecil E. Boord for his advice and counsel during this investigation* Thanks also are due Dr. Kenneth W*. Greenlee for his continual interest and guidance and his cooperation in ex tending the facilities of the American Petroleum Institute Research Project 4-5* The financial support of this work by the Firestone Tire and Rubber Company is gratefully acknowledged* ii TABLE OF CONTENTS Page I. INTRODUCTION................................ 1 II. LITERATURE S URVEY ............... 2 III. STATEMENT OF THE PROBLEM.................... 10 IV. DISCUS5IŒ ........................... 11 A. Methods of Preparing Hydroperoxides .... 12 1. Preparation of hydroperoxides from alcohols ............. 12 a. a-methylbenzyl hydroperoxide ...... 12 b. benzyl hydroperoxide .......... l6 c. cinnamyl and a-phenylallyl hydroperoxides 17 d. 1,2,3,4-tetrahydro-l-naphthyl hydro peroxide ............ 22 e. a-indanyl hydroperoxide ........ 23 f. 0-, m- and p-methylbenzyl hydroperoxides 24 g. m- and p-methoxybenzyl hydroperoxides. 28 h. 1,1-diphenylmethyl hydroperoxide .... 31 i. 1,2-diphenylethyl hydroperoxide .... 32 j. 1-a-naphthyl- and l-J3-naphthylethyl hydroperoxides ........ 33 k. 1-styrylethyl hydroperoxide 35 1. 4-a-dimethylbenzyl and 4-methoxy-a- methylbenzyl hydroperoxides ...... 36 m. a-ethylbenzyl and a-ethyl-p-methylbenzyl hydroperoxides ....... ........ 36 n. a-n-propylbenzyl and a-isopropylbenzyl hydroperoxides .................... 37 0. a-2,5“trimethylbenzyl hydroperoxide . -
Ethylene Dichloride (Edc) Handbook
ETHYLENE DICHLORIDE (EDC) HANDBOOK OXYCHEM TECHNICAL INFORMATION 11/2014 Dallas-based Occidental Chemical Corporation is a leading North American manufacturer of basic chemicals, vinyls and performance chemicals directly and through various affiliates (collectively, OxyChem). OxyChem is also North America's largest producer of sodium chlorite. As a Responsible Care® company, OxyChem's global commitment to safety and the environment goes well beyond compliance. OxyChem's Health, Environment and Safety philosophy is a positive motivational force for our employees, and helps create a strong culture for protecting human health and the environment. Our risk management programs and methods have been, and continue to be, recognized as some of the industry's best. OxyChem offers an effective combination of industry expertise, experience, on line business tools, quality products and exceptional customer service. As a member of the Occidental Petroleum Corporation family, OxyChem represents a rich history of experience, top-notch business acumen, and sound, ethical business practices. 1 Table of Contents Page Introduction to Ethylene Dichloride ............................................................................................................ 3 Manufacturing .................................................................................................................................................. 3 Ethylene Dichloride (EDC) — Uses ................................................................................................................ -
One-Pot Syntheses of Irida-Polycyclic Aromatic Hydrocarbons† Cite This: Chem
Chemical Science View Article Online EDGE ARTICLE View Journal | View Issue One-pot syntheses of irida-polycyclic aromatic hydrocarbons† Cite this: Chem. Sci.,2019,10, 10894 a a a b a All publication charges for this article Yu Xuan Hu,‡ Jing Zhang,‡ Xiaoyan Wang, Zhengyu Lu, Fangfang Zhang, have been paid for by the Royal Society Xiaofei Yang,a Zhihua Ma,a Jun Yin, *a Haiping Xia b and Sheng Hua Liu *a of Chemistry Metalla-analogues of polycyclic aromatic hydrocarbons (PAHs) have captivated chemists with their fascinating structures and unique electronic properties. To date, metallabenzene, metallanaphthalene and metallaanthracene have been reported. Metalla-analogues with more complicated fused rings have rarely been reported. Herein, we have successfully synthesized a series of new iridafluoranthenes and fused-ring iridafluoranthenes ranging from pentacyclic to heptacyclic metallaaromatic hydrocarbons in Received 6th August 2019 high yields under mild reaction conditions for the first time. Their photophysical and redox properties Accepted 12th October 2019 were also explored using UV-vis spectroscopy and electrochemistry combined with TD-DFT DOI: 10.1039/c9sc03914g calculations. The present work may offer an important guideline for the design and construction of new rsc.li/chemical-science polycyclic metallaaromatic hydrocarbons and metalla-nanographenes. Creative Commons Attribution-NonCommercial 3.0 Unported Licence. Introduction carbeneiridium compound by using an intramolecular C–H activation reaction.6b In 2018, they further developed irida- Polycyclic aromatic hydrocarbons (PAHs), as important compo- phenanthrene, iridanaphthalene and iridaanthracene from nents in the eld of organic chemistry, have attracted a signi- their corresponding methoxy(alkenyl)carbeneiridium inter- * cant amount of attention due to their wide range of applications mediates via reactions of [IrCp Cl(NCMe) (PMe3)]PF6 with 8 in organic light-emitting diodes,1 eld-effect transistors2 and diarylpropargyl alcohols. -
Toxicological Profile for Ethylbenzene
ETHYLBENZENE 151 5. PRODUCTION, IMPORT/EXPORT, USE, AND DISPOSAL 5.1 PRODUCTION Ethylbenzene is primarily produced by the alkylation of benzene with ethylene in liquid-phase slurry reactors promoted with aluminum chloride catalysts or by vapor-phase reaction of benzene with dilute ethylene-containing feedstock with a boron trifluoride catalyst supported on alumina (Cannella 2007; Clayton and Clayton 1981; HSDB 2009; Welch et al. 2005; Ransley 1984). Newer versions of the method employ synthetic zeolites in fixed-bed reactors as catalysts for alkylation in the liquid phase or narrow pore synthetic zeolites in fixed-bed reactors in the vapor phase (Welch et al. 2005). Other methods of manufacturing ethylbenzene include preparation from acetophenone, dehydrogenation of naphthenes, catalytic cyclization and aromatization, separation from mixed xylenes via fractionation, reaction of ethylmagnesium bromide and chlorobenzene, extraction from coal oil, and recovery from benzene-toluene-xylene (BTX) processing(Clayton and Clayton 1981; HSDB 2009; Ransley 1984; Welch et al. 2005). Commercial grades of ethylbenzene may contain small amounts of m-xylene, p-xylene, cumene, and toluene (HSDB 2009). Ethylbenzene is traditionally ranked as one of the top 50 chemicals produced in the United States. Table 5-1 shows the historical production volumes of ethylbenzene from 1983 to 2005 (C&EN 1994a, 1994b, 1995, 2006; Kirschner 1995). Table 5-2 lists the facilities in each state that manufacture or process ethylbenzene, the intended use, and the range of maximum amounts of ethylbenzene that are stored on site. There are currently 3,755 facilities that produce, process, or use ethylbenzene in the United States. The data listed in Table 5-2 are derived from the Toxics Release Inventory (TRI06 2008). -
ETHYLENE from METHANE (January 1994)
Abstract Process Economics Program Report No. 208 ETHYLENE FROM METHANE (January 1994) This report evaluates two routes for the production of ethylene from methane: the direct synthesis based on the oxidative coupling of methane, and the less direct chemistry of converting methanol (which is derived from methane via synthesis gas) in the presence of an aluminophosphate molecular sieve catalyst. Our evaluations indicate that at the present state of development, the economics of both routes are unattractive when compared with the steam pyrolysis of hydrocarbons. We analyze the results of our evaluations to define the technical targets that must be attained for success. We also present a comprehensive technical review that examines not only the two routes evaluated, but also some of the more promising alternative approaches, such as synthesis gas conversion via a modified Fischer-Tropsch process, ethanol synthesis by the homologation of methanol, and ethylene production via methyl chloride. This report will be of interest to petrochemical companies that produce or consume ethylene and to energy-based companies (or equivalent government organizations in various countries) that have access to or control large resources of methane-rich natural gas. PEP’91 SCN CONTENTS 1 INTRODUCTION 1-1 2 SUMMARY 2-1 TECHNICAL REVIEW 2-1 Oxidative Coupling 2-1 Methanol Conversion to Ethylene 2-3 Modified Fischer-Tropsch (FT) Process 2-3 Methanol Homologation 2-3 Conversion via Methyl Chloride 2-4 SRI’S PROCESS CONCEPTS 2-4 Ethylene from Methane by Oxidative -
Submitted To
I 1 RTI PROJECT NO. 9611-6048 DOE Contract No. DE-AC22-94PC94065 January 1,1995 through March 31,1995 SYNTHESIS OF ACRYLATES AND METHACRLYATES FROM COAL-DERIVED SYNGAS Quarterly Technical Progress Report Submitted to US. Department of Energy Pittsburgh Energy Technology Center P. 0. Box 10940 Pittsburgh, Pennsylvania 15236-0940 Submitted by Research Triangle Institute P. 0. Box 12194 Research Triangle Park, NC 27709 DOE COR: Richard E. Tischer RTI Project Manager: James J. Spivey DISCLAIMER This report was prepared as an account of work sponsored by an agency of the United States Government. Neither the United States Government nor any agency thereof, nor any of their employees, makes any warranty, express or implied, or assumes any legal liability or responsi- bility for the accuracy, completeness, or usefulness of any information, apparatus, product, or process disclosed, or represents that its use would not infringe privately owned rights. Refer- ence herein to any specific commercial product, process, or service by trade name, trademark, manufacturer, or otherwise does not necessarily constitute or imply its endorsement, recom- mendation, or favoring by the United States Government or any agency thereof. The views and opinions of authors expressed herein do not necessarily state or reflect those of the DiCJTRlBfllQN THIS DOWMENT mm United States Government or any agency thereof. OF %”/ - DISCLAIMER Portions of this document may be illegible in electronic image products. Images are produced from the best available original document. Executive Summary Task 1-Synthesis of Propionates The objective of this Task is to develop the technology for the synthesis of low-cost propionates. -
Detection of Phenethylamine, Amphetamine, and Tryptamine Imine By-Products from an Acetone Extraction
Detection of Phenethylamine, Amphetamine, and Tryptamine Imine By-Products from an Acetone Extraction Mary A. Yohannan* and Arthur Berrier U.S. Department of Justice Drug Enforcement Administration Special Testing and Research Laboratory 22624 Dulles Summit Court Dulles, VA 20166 [email: mary.a.yohannan -at- usdoj.gov] ABSTRACT: The formation of imine by-products from phenethylamines, amphetamines, and tryptamines upon an acetone extraction is presented. These imine by-products were characterized using GC/MSD and exhibited preferential cleavage at the α-carbon of the alkyl chain. Further characterization of the imine by-products of phenethylamine and tryptamine was done using IR and NMR. KEYWORDS: phenethylamine, tryptamine, imine, acetone, schiff base, drug chemistry, forensic chemistry In most forensic laboratories, the solvents used to extract at the α-carbon on the alkyl chain. In addition to GC/MS, the drugs are chosen based upon their solubility properties and their imines formed from phenethylamine base and tryptamine base ability to not interact with the drug. In fact, there are very few were characterized by Fourier transform-infrared spectroscopy publications where a solvent used to extract a drug reacts with (FTIR) and nuclear magnetic resonance (NMR) spectroscopy. the drug and forms by-products [1-3]. This laboratory recently discovered that an additional Experimental component was formed when acetone was used to extract a Solvents, Chemicals, and Materials sample containing a known tryptamine. Analysis by gas Acetone was ACS/HPLC grade from Burdick and Jackson chromatography/mass spectroscopy (GC/MS) of the acetone Laboratories (Muskegon, MI). Phenethylamine base and extract yielded an extra peak in the total ion chromatogram that tryptamine base were obtained from Sigma-Aldrich Chemicals was approximately half the abundance of the known tryptamine (Milwaukee, WI). -
Hydrogenation of Ethylene on Metallic Catalysts
S ro Hating Bure* M “"“^ piu&« Ubwu, Ml ®min’ JUN 2 1 1S68 A 1 1 1 2 mbESD NATX INST OF STANDARDS & TECH R.I.C. NSRDS-NBS 13 NSRDS 11 021 46250 ™SRDS.NB^ QC100 -U573 V13;1968 C.1 sH *- NBS-PUB-C 1964 ^f#Cf DftU NBS 'USUCATfONS Hydrogenation of Ethylene Metallic Catalysts U.S. DEPARTMENT OF COMMERCE NATIONAL BUREAU OF STANDARDS National Standard Reference Data Series National Bureau of Standards National Standard Reference Data System, Plan of Operation, NSRDS-NBS 1 — 15 cents* Thermal Properties of Aqueous Uni-univalent Electrolytes NSRDS-NBS 2 — 45 cents* Selected Tables of Atomic Spectra, Atomic Energy Levels and Multiplet Tables — Si II, Si ill, Si iv, NSRDS-NBS 3, Section 1—35 cents* Selected Tables of Atomic Spectra, Atomic Energy Levels and Multiplet Tables — Si I NSRDS — NBS 3, Section 2 — 20 cents* Atomic Transition Probabilities, Volume I, Hydrogen Through Neon, NSRDS-NBS 4 — $2.50* The Band Spectrum of Carbon Monoxide, NSRDS-NBS 5 — 70 cents* Tables of Molecular Vibrational Frequencies. Part 1, NSRDS-NBS 6 — 40 cents* High Temperature Properties and Decomposition of Inorganic Salts. Part 1. Sulfates, NSRDS-NBS 7-35 cents* Thermal Conductivity of Selected Materials, NSRDS-NBS 8 — $1.00* Tables of Biomolecular Gas Reactions, NSRDS-NBS 9 — $2.00* Selected Values of Electric Dipole Moments for Molecules in the Gas Phase, NSRDS- NBS 10 — 40 cents* Tables of Molecular Vibrational Frequencies, Part 2, NSRDS-NBS 11 — 30 cents* Tables for the Rigid Asymmetric Rotor: Transformation Coefficient from Symmetric to Asymmetric Bases Expectation Values of P\ and 4 NSRDS-NBS 12 — in press. -
Acetylene and Ethylene Hydrogenation on Alumina Supported Pd-Ag Model Catalysts
Catalysis Letters Vol. 108, Nos. 3–4, May 2006 (Ó 2006) 159 DOI: 10.1007/s10562-006-0041-y Acetylene and ethylene hydrogenation on alumina supported Pd-Ag model catalysts N.A. Khan,* S. Shaikhutdinov, and H.-J. Freund Department of Chemical Physics, Fritz-Haber-Institut der Max-Planck-Gesellschaft, Faradayweg 4-6, Berlin 14195, Germany Received 20 December 2005; accepted 20 January 2006 Adsorption and co-adsorption of ethylene, acetylene and hydrogen on Pd-Ag particles, supported on thin alumina films, have been studied by temperature programmed desorption (TPD). The TPD results show that adding of Ag to Pd suppresses overall hydrogenation activity but increases selectivity towards ethylene, i.e. similar to that observed on real catalysts. The results are rationalized on the basis of a complex interplay between surface and subsurface hydrogen species available in the system, whereby the latter species are the most critical for total hydrogenation of acetylene to ethane. KEY WORDS: hydrogenation; bimetallic catalysts; acetylene; palladium; silver. The selective hydrogenation of acetylene is an alumina film both at low pressures (with TPD) and high industrially important catalytic process in the large-scale pressures (up to 1 bar, using gas chromatography [16– production of polyethylene, where a small quantity of 18]. Under both conditions, the ethylene hydrogenation acetylene (<3%) is present in ethylene feedstock. reaction was found to be structure insensitive. In Commercially, it is preferred to reduce the acetylene contrast, hydrogenation of 2-pentenes exhibited a sig- content to less than 10 ppm, which needs 99% acet- nificant particle size effect [19]. These studies have ylene conversion in the excess of ethylene [1]. -
Gas Phase Ion/Molecule Reactions As Studied by Fourier Transform Ion Cyclotron Resonance Mass Spectrometry
INIS-mf—10165 GAS PHASE ION/MOLECULE REACTIONS AS STUDIED BY FOURIER TRANSFORM ION CYCLOTRON RESONANCE MASS SPECTROMETRY STEEN INGEMANN J0RGENSEN GAS PHASE ION/MOLECULE REACTIONS AS STUDIED BY FOURIER TRANSFORM ION CYCLOTRON RESONANCE MASS SPECTROMETRY ACADEMISCH PROEFSCHRIFT ter verkrijging van de graad van doctor in de Wiskunde en Natuurwetenschappen aan de Universiteit van Amsterdam, op gezag van de Rector Magnificus dr. D.W. Bresters, hoogleraar in de Faculteit der Wiskunde en Natuurwetenschappen, in het openbaar te verdedigen in de Aula der Universiteit (tijdelijk in het Wiskundegebouw, Roetersstraat 15) op woensdag 12 juni 1985 te 16.00 uur. door STEEN INGEMANN J0RGENSEN geboren te Kopenhagen 1985 Offsetdrukkerij Kanters B.V., Alblasserdam PROMOTOR: Prof. Dr. N.M.M. Nibbering Part of the work described in this thesis has been accomplished under the auspices of the Netherlands Foundation for Chemical Research (SON) with the financial support from the Netherlands Organization for the Advancement of Pure Research (ZWO). STELLINGEN 1. De door White e.a. getrokken conclusie, dat het cycloheptatrieen anion omlegt tot het benzyl anion in de gasfase, is onvoldoende ondersteund door de experimentele gegevens. R.L. White, CL. Wilkins, J.J. Heitkamp, S.W. Staley, J. Am. Chem. Soc, _105, 4868 (1983). 2. De gegeven experimentele methode voor de lithiëring van endo- en exo- -5-norborneen-2,3-dicarboximide is niet in overeenstemming met de ge- postuleerde vorming van een algemeen dianion van deze verbindingen. P.J. Garratt, F. Hollowood, J. Org. Chem., 47, 68 (1982). 3. De door Barton e.a. gegeven verklaring voor de observaties, dat O-alkyl- -S-alkyl-dithiocarbonaten reageren met N^-dimethylhydrazine onder vor- ming van ^-alkyl-thiocarbamaten en ^-alkyl-thiocarbazaten, terwijl al- koxythiocarbonylimidazolen uitsluitend £-alkyl-thiocarbazaten geven, is hoogst twijfelachtig. -
Kinetic Study of the Selective Hydrogenation of Acetylene Over Supported Palladium Under Tail-End Conditions
catalysts Article Kinetic Study of the Selective Hydrogenation of Acetylene over Supported Palladium under Tail-End Conditions Caroline Urmès 1,2, Jean-Marc Schweitzer 2, Amandine Cabiac 2 and Yves Schuurman 1,* 1 IRCELYON CNRS, UMR 5256, Univ Lyon, Université Claude Bernard Lyon 1, 2 avenue Albert Einstein, 69626 Villeurbanne Cedex, France; [email protected] 2 IFP Energies nouvelles, Etablissement de Lyon, Rond-point de l’échangeur de Solaize, BP3, 69360 Solaize, France; [email protected] (J.-M.S.); [email protected] (A.C.) * Correspondence: [email protected]; Tel.: +33-472445482 Received: 9 January 2019; Accepted: 31 January 2019; Published: 14 February 2019 Abstract: The kinetics of the selective hydrogenation of acetylene in the presence of an excess of ethylene has been studied over a 0.05 wt. % Pd/α-Al2O3 catalyst. The experimental reaction conditions were chosen to operate under intrinsic kinetic conditions, free from heat and mass transfer limitations. The data could be described adequately by a Langmuir–Hinshelwood rate-equation based on a series of sequential hydrogen additions according to the Horiuti–Polanyi mechanism. The mechanism involves a single active site on which both the conversion of acetylene and ethylene take place. Keywords: power-law; Langmuir–Hinshelwood; kinetic modeling; Pd/α-Al2O3 1. Introduction Ethylene is the largest of the basic chemical building blocks with a global market estimated at more than 140 million tons per year with an increasing growth rate. It is used mainly as precursor for polymers production, for instance polyethylene, vinyl chloride, ethylbenzene, or even ethylene oxide synthesis.