Processes for Micromachining
Total Page:16
File Type:pdf, Size:1020Kb
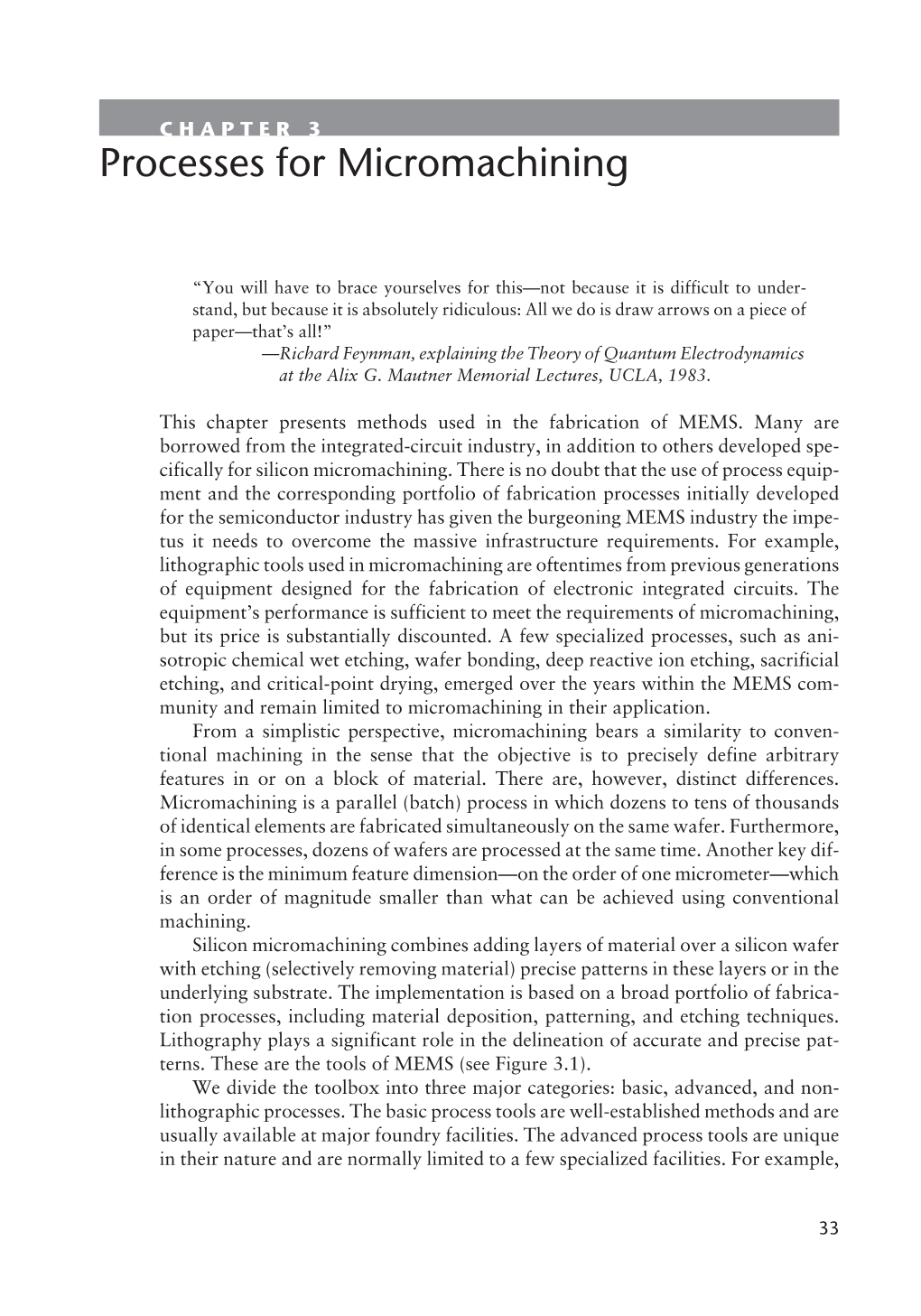
Load more
Recommended publications
-
The American Ceramic Society 25Th International Congress On
The American Ceramic Society 25th International Congress on Glass (ICG 2019) ABSTRACT BOOK June 9–14, 2019 Boston, Massachusetts USA Introduction This volume contains abstracts for over 900 presentations during the 2019 Conference on International Commission on Glass Meeting (ICG 2019) in Boston, Massachusetts. The abstracts are reproduced as submitted by authors, a format that provides for longer, more detailed descriptions of papers. The American Ceramic Society accepts no responsibility for the content or quality of the abstract content. Abstracts are arranged by day, then by symposium and session title. An Author Index appears at the back of this book. The Meeting Guide contains locations of sessions with times, titles and authors of papers, but not presentation abstracts. How to Use the Abstract Book Refer to the Table of Contents to determine page numbers on which specific session abstracts begin. At the beginning of each session are headings that list session title, location and session chair. Starting times for presentations and paper numbers precede each paper title. The Author Index lists each author and the page number on which their abstract can be found. Copyright © 2019 The American Ceramic Society (www.ceramics.org). All rights reserved. MEETING REGULATIONS The American Ceramic Society is a nonprofit scientific organization that facilitates whether in print, electronic or other media, including The American Ceramic Society’s the exchange of knowledge meetings and publication of papers for future reference. website. By participating in the conference, you grant The American Ceramic Society The Society owns and retains full right to control its publications and its meetings. -
Understanding Composition–Structure– Bioactivity Correlations
Understanding Composition–Structure– Bioactivity Correlations in Bioactive Glasses Yang Yu Academic dissertation for the Degree of Doctor of Philosophy in Physical Chemistry at Stockholm University to be publicly defended on Wednesday 12 December 2018 at 13.00 in De Geersalen, Geovetenskapens hus, Svante Arrhenius väg 14. Abstract Bioactive glasses integrate with bone/tooth tissues by forming a layer of hydroxy-carbonate apatite (HCA), which mimics the composition of bone mineral. In the current thesis, we investigated composition–structure–bioactivity correlations of phosphosilicate and borophosphosilicate (BPS) glasses. Bioactive phosphosilicate glasses extend the compositional space of the ”45S5 Bioglass®”, which has been in clinical use for decades. Recently developed bioactive BPS glasses with SiO2→B2O3 substitutions transform more completely into HCA and their glass dissolution behaviors can be tuned by varying the relative contents of B and Si. It is known that the average silicate network connectivity NSi and the phosphate content (x(P2O5)) affect the apatite formation (in vitro bioactivity) of phosphosilicate glasses, but the details remain poorly explored. Three series of phosphosilicate glasses were designed by independently varying NSi and x(P2O5). After immersion of the glasses in a simulated body fluid (SBF) for 24 hours, different degrees of their apatite formation were quantified by Fourier-transform infrared (FTIR) spectroscopy. The results revealed that a high P content widened the NSi range that generated optimum amounts of apatite and also mitigated the detrimental effects associated with using glass particles with < 50 μm. The amounts of apatite derived from FTIR agreed with those from 31P magic angle spinning (MAS) nuclear magnetic resonance (NMR) spectroscopy. -
Fabrication and Characteristics of Yb-Doped Silica Fibers Produced by the Sol-Gel Based Granulated Silica Method
fibers Article Fabrication and Characteristics of Yb-Doped Silica Fibers Produced by the Sol-Gel Based Granulated Silica Method Ali El Sayed 1,2,*, Soenke Pilz 1, Hossein Najafi 1, Duncan T. L. Alexander 3,4 , Martin Hochstrasser 5 and Valerio Romano 1,2,* 1 Institute for Applied Laser, Photonics and Surface Technologies (ALPS), Bern University of Applied Sciences, Pestalozzistrasse 20, 3400 Burgdorf, Switzerland; [email protected] (S.P.); hossein.najafi@bfh.ch (H.N.) 2 Institute of Applied Physics (IAP), University of Bern, Sidlerstrasse 5, 3012 Bern, Switzerland 3 Electron Spectrometry and Microscopy Laboratory (LSME), Institute of Physics (IPHYS), Ecole Polytechnique Fédérale de Lausanne (EPFL), 1015 Lausanne, Switzerland; duncan.alexander@epfl.ch 4 Interdisciplinary Centre for Electron Microscopy (CIME), Ecole Polytechnique Fédérale de Lausanne (EPFL), 1015 Lausanne, Switzerland 5 Reseachem GmbH, Pestalozzistrasse 20, 3400 Burgdorf, Switzerland; [email protected] * Correspondence: [email protected] (A.E.); [email protected] (V.R.); Tel.: +41-34-426-4347 (A.E.); +41-31-631-8940 (V.R.) Received: 7 September 2018; Accepted: 19 October 2018; Published: 23 October 2018 Abstract: Combining the sol-gel method for fiber material production with the granulated silica method for preform assembly results in a robust method that offers a high degree of freedom regarding both the composition and the geometry of the produced fiber. Using this method, two types of Yb-doped silica glass composition, that feature an excess in P concentration with respect to Al, have been prepared. The elemental distributions in a fiber core were analyzed by scanning transmission electron microscopy (STEM). -
Phosphate-Doped Borosilicate Enamel Coating Used to Protect Reinforcing Steel from Corrosion
Scholars' Mine Doctoral Dissertations Student Theses and Dissertations Fall 2014 Phosphate-doped borosilicate enamel coating used to protect reinforcing steel from corrosion Xiaoming Cheng Follow this and additional works at: https://scholarsmine.mst.edu/doctoral_dissertations Part of the Materials Science and Engineering Commons Department: Materials Science and Engineering Recommended Citation Cheng, Xiaoming, "Phosphate-doped borosilicate enamel coating used to protect reinforcing steel from corrosion" (2014). Doctoral Dissertations. 2339. https://scholarsmine.mst.edu/doctoral_dissertations/2339 This thesis is brought to you by Scholars' Mine, a service of the Missouri S&T Library and Learning Resources. This work is protected by U. S. Copyright Law. Unauthorized use including reproduction for redistribution requires the permission of the copyright holder. For more information, please contact [email protected]. 2 PHOSPHATE-DOPED BOROSILICATE ENAMEL COATING USED TO PROTECT REINFORCING STEEL FROM CORROSION by XIAOMING CHENG A DISSERTATION Presented to the Faculty of the Graduate School of the MISSOURI UNIVERSITY OF SCIENCE AND TECHNOLOGY In Partial Fulfillment of the Requirements for the Degree DOCTOR OF PHILOSOPHY in MATERIALS SCIENCE AND ENGINEERING 2014 Approved by: Richard K. Brow, Advisor Genda Chen Delbert E. Day Matthew J. O’Keefe Mark E. Schlesinger 3 2014 XIAOMING CHENG All Rights Reserved iii PUBLICATION DISSERTATION OPTION This dissertation consists of a section of introduction, four papers and a section of appendix. Papers I (pages 20-57) will be submitted for publication in the Journal of Non- Crystalline Solids. Papers II (pages 58-88) will be submitted for publication in the Journal of Non- Crystalline Solids. Papers III (pages 89-120) will be submitted for publication in the Journal of Non- Crystalline Solids. -
A Review of Selected Nanofabricated Thin Film Platforms for Spectroscopy, Imaging, and Detection Jason R
Through a window, brightly: A review of selected nanofabricated thin film platforms for spectroscopy, imaging, and detection Jason R. Dwyer and Maher Harb Corresponding authors: Jason R. Dwyer, ORCID 0000-0002- 2938-2888, 140 Flagg Road, Department of Chemistry, University of Rhode Island, Kingston, RI, 02881; Maher Harb, ORCID 0000-0002- 6853-9454, Departments of Physics and Materials Science & Engineering, Drexel University, Philadelphia, PA, 19104. Abstract We present a review of the use of selected nanofabricated thin films to deliver a host of capabilities and insights spanning bioanalytical and biophysical chemistry, materials science, and fundamental molecular-level research. We discuss approaches where thin films have been vital, enabling experimental studies using a variety of optical spectroscopies across the visible and infrared spectral range; electron microscopies and related techniques such as electron energy loss spectroscopy; x-ray photoelectron spectroscopy; and single-molecule sensing. We will anchor this broad discussion by highlighting two particularly exciting exemplars: a thin-walled nanofluidic sample cell concept that has advanced the discovery horizons of ultrafast spectroscopy, and of electron microscopy investigations of in-liquid samples; and a unique class of thin-film-based nanofluidic devices, designed around a nanopore, with expansive prospects for single-molecule sensing. Free-standing, low-stress silicon nitride membranes are a canonical structural element for these applications, and we will elucidate the fabrication and resulting features—including mechanical stability, optical properties, x-ray and electron scattering properties, and chemical nature—of this material in this format. We also outline design and performance principles, and include a discussion of underlying material preparations and properties suitable for understanding the use of alternative thin-film materials such as graphene. -
Composition Structure Property Relationships in Bioactive Glasses
COMPOSITION STRUCTURE PROPERTY RELATIONSHIPS IN BIOACTIVE GLASSES Sally Watts Doctor of Philosophy Department of Materials Imperial College London London SW7 2AZ United Kingdom COMPOSITION STRUCTURE PROPERTY RELATIONSHIPS IN BIOACTIVE GLASSES Sally Watts A thesis submitted in partial fulfilment of the requirements for the degree of Doctor of Philosophy And the Diploma of Imperial College Supervised by: Professor Robert Hill and Dr. Rob Law Department of Materials Imperial College London London SW7 2AZ United Kingdom February 2010 2 Hench developed the first bioactive material, Bioglass®, based on a soda-lime phospho-silicate glass. Most materials, elicit a neutral response when implanted into the human body. Bioglass®, however, was seen to create a positive response by depositing the body’s natural bone substance, Hydroxyapatite on its surface. Although it is recognised that compositional modifications effect bioactivity, there is very little comprehension of the composition-structure- property relationships that result in such bioactivity. The objective of this investigation, therefore, was to study such fundamental relationships with respect to two components often found in bioactive glass compositions – P2O5 and MgO. The first component studied was P2O5. The design of two series was undertaken – the first, a straight substitution of silicon for phosphorus, varying the network connectivity, NC, and the second, a charge compensating series, keeping the NC constant. 31P and 29Si MAS NMR of the two series provided evidence that the glasses were phase separated, with a predominantly Q2 silicate structure co-existing with phosphorus in a predominantly Q0 orthophosphate environment. Raman, FTIR, density measurements, differential thermal analysis and dilatometric analysis all further supported the existence of this structure. -
Compact and Efficient O-Band Bismuth-Doped Phosphosilicate Fiber Amplifier for Fiber-Optic Communications
www.nature.com/scientificreports OPEN Compact and efcient O‑band bismuth‑doped phosphosilicate fber amplifer for fber‑optic communications Sergei V. Firstov1*, Aleksandr M. Khegai1, Alexander V. Kharakhordin1, Sergey V. Alyshev1, Elena G. Firstova1, Yan J. Ososkov1, Mikhail A. Melkumov1, Lyudmila D. Iskhakova1, Elena B. Evlampieva3, Alexey S. Lobanov2, Mikhail V. Yashkov2 & Alexey N. Guryanov2 During last decades there has been considerable interest in developing a fber amplifer for the 1.3‑µ m spectral region that is comparable in performance to the Er‑doped fber amplifer operating near 1.55 µ m. It is due to the fact that most of the existing fber‑optic communication systems that dominate terrestrial networks could be used for the data transmission in O‑band (1260–1360 nm), where dispersion compensation is not required, providing a low‑cost increase of the capacity. In this regard, signifcant eforts of the research laboratories were initially directed towards the study of the praseodymium‑doped fuoride fber amplifer having high gain and output powers at the desired wavelengths. However, despite the fact that this type of amplifers had rapidly appeared as a commercial amplifer prototype it did not receive widespread demand in the telecom industry because of its low efciency. It stimulated the search of novel optical materials for this purpose. About 10 years ago, a new type of bismuth‑doped active fbers was developed, which turned out to be a promising medium for amplifcation at 1.3 µ m. Here, we report on the development of a compact and efcient 20‑dB (achieved for signal powers between −40 and −10 dBm) bismuth‑doped fber amplifer for a wavelength region of 1300–1350 nm in the forward, backward and bi‑directional confgurations, which can be pumped by a commercially available laser diode at 1230 nm with an output power of 250 mW. -
Atmospheric Pressure Chemical Vapor Deposition of Functional Oxide Materials for Crystalline Silicon Solar Cells
University of Central Florida STARS Electronic Theses and Dissertations, 2004-2019 2015 Atmospheric Pressure Chemical Vapor Deposition of Functional Oxide Materials for Crystalline Silicon Solar Cells Kristopher Davis University of Central Florida Part of the Electromagnetics and Photonics Commons, and the Optics Commons Find similar works at: https://stars.library.ucf.edu/etd University of Central Florida Libraries http://library.ucf.edu This Doctoral Dissertation (Open Access) is brought to you for free and open access by STARS. It has been accepted for inclusion in Electronic Theses and Dissertations, 2004-2019 by an authorized administrator of STARS. For more information, please contact [email protected]. STARS Citation Davis, Kristopher, "Atmospheric Pressure Chemical Vapor Deposition of Functional Oxide Materials for Crystalline Silicon Solar Cells" (2015). Electronic Theses and Dissertations, 2004-2019. 69. https://stars.library.ucf.edu/etd/69 ATMOSPHERIC PRESSURE CHEMICAL VAPOR DEPOSITION OF FUNCTIONAL OXIDE MATERIALS FOR CRYSTALLINE SILICON SOLAR CELLS by KRISTOPHER O. DAVIS B.S. in Electrical Engineering, University of Central Florida, 2007 M.S. in Optics, University of Central Florida, 2011 A dissertation submitted in partial fulfillment of the requirements for the degree of Doctor of Philosophy in the College of Optics and Photonics at the University of Central Florida Orlando, Florida Spring Term 2015 Major Professor: Winston V. Schoenfeld © 2015 Kristopher O. Davis ii ABSTRACT Functional oxides are versatile materials that can simultaneously enable efficiency gains and cost reductions in crystalline silicon (c-Si) solar cells. In this work, the deposition of functional oxide materials using atmospheric pressure chemical vapor deposition (APCVD) and the integration of these materials into c- Si solar cells are explored. -
Case File Opy
NASA USES OF CERAMICS IN MICROELECTRONICS A SURVEY CASE FILE OPY NATIONAL AERONAUTICS AND SPACE ADMINISTRATION . NASA SP-5097 USES OF CERAMICS IN MICROELECTRONICS A SURVEY By W. R. Bratschun A. J. Mountvala A. G. Pincus HT Research Institute Prepared under contract for the NASA Technology Utilization Office Technology Utilization Office ' - 1971- NATIONAL AERONAUTICS AND SPACE ADMINISTRATION Washington, D.C. NOTICE • This document was prepared under the sponsorship of the National Aeronautics and Space Administration. Neither the United States Govern- ment nor any person acting on behalf of the United States Government as- sumes any liability resulting from the use of the information contained in this document, or warrants that such use will be free from privately owned rights. For sale by the Superintendent of Documents, U.S. Government Printing Office, Washington, D.C. 20402 Price $1.00 STOCK NUMBER 3300-0388 Library of Congress Catalog Card Number 78-611801 Foreword This survey is one of a series issued by the National Aeronau- tics and Space Administration as part of its Technology Utiliza- tion Program to disseminate information useful for general industrial applications. Uses of Ceramics in Microelectronics is addressed to management personnel concerned with electronic circuitry. It describes advances in the state of the art of passive components (insulators, resistors, and capacitors) of electronic devices. Requirements for the exploration of space have accel- erated such advances, and they can be helpful in many additional ways. The electronics industry has become highly dependent on the interface between materials and devices. Improvements in pas- sive components have kept pace with advances in active devices. -
Glossary and Symbols
GLOSSARY AND SYMBOLS The ISHM Glossary of Hybrid-Circuit Terms (Updated edition Summer 1987) by G.S. Szekely provided the foundation for this glossary. Definitions have in some cases been modified to fit this work. Other terms used by the authors and the packaging profession have been added and some terms in the original work have not been deleted. Material chemical symbols are found at the end of this glossary. A ACCELERATED STRESS TEST. A test conducted at a stress, e.g., chemical or physical, higher than that encountered in normal operation, for the purpose of producing a measurable effect, such as a fatigue failure, in a shorter time than experienced at operating stresses. ACCELERATOR. An organic compound which is added to an epoxy resin to shorten the cure time. ACTIVE COMPONENTS. Electronic components, such as transistors, diodes, electron tubes, thyristors, etc., which can operate on an applied electrical signal so as to change its basic characteristics, i.e., rectification, amplification, switch ing, etc. ADDITIVE PLATING. Processing a hybrid circuit substrate by sequentially plating conductive, resistive, and insulative materials, each through a mask, thus defining the areas of traces, pads, and elements. ADVANCED STATISTICAL ANALYSIS PROGRAM (ASTAP). The "Ad vanced Statistical Analysis Program" is the mM circuit analysis simulation program. It performs DC, time domain, and frequency domain simulations. Statis tics can be applied to all simulations to predict operating tolerances. Among its many features is a transmission line analysis program. Also see SPICE. 11-932 GLOSSARY AND SYMBOLS ALLOY. A solid-state solution or compound formation of two or more metals. -
Development of Highly Photosensitive Low Loss Inorganic Sol‑Gel Films for Direct Ultraviolet‑Imprinting of Planar Waveguides
This document is downloaded from DR‑NTU (https://dr.ntu.edu.sg) Nanyang Technological University, Singapore. Development of highly photosensitive low loss inorganic sol‑gel films for direct ultraviolet‑imprinting of planar waveguides Rajni 2008 Rajni. (2008). Development of highly photosensitive low loss inorganic sol‑gel films for direct ultraviolet‑imprinting of planar waveguides. Doctoral thesis, Nanyang Technological University, Singapore. https://hdl.handle.net/10356/4113 https://doi.org/10.32657/10356/4113 Nanyang Technological University Downloaded on 04 Oct 2021 19:26:37 SGT ATTENTION: The Singapore Copyright Act applies to the use of this document. Nanyang Technological University Library Development of Highly Photosensitive Low Loss Inorganic Sol-Gel Films for Direct Ultraviolet- Imprinting of Planar Waveguides Rajni School of Electrical and Electronic Engineering A thesis submitted to the Nanyang Technological University in fulfilment of the requirement for the degree of Doctor of Philosophy 2008 ATTENTION: The Singapore Copyright Act applies to the use of this document. Nanyang Technological University Library To My Family For affectionate support in all my endeavours........ ATTENTION: The Singapore Copyright Act applies to the use of this document. Nanyang Technological University Library Acknowledgements This is indeed a privilege and a great pleasure to express my gratitude and deep regards to my supervisor Prof. Kantisara Pita for giving me the opportunity to associate myself with the exciting academic atmosphere of photonics research group (School of Electrical and Electronics) of Nanyang Technological University (NTU) as a Doctor of Philosophy student. It will be always less whatever I say, however I express myself to honour his invaluable guidance, keen interest and encouragement throughout my research work. -
Yan Colostate 0053A 10673.Pdf
DISSERTATION A CMOS COMPATIBLE OPTICAL BIOSENSING SYSTEM BASED ON LOCAL EVANESCENT FIELD SHIFT MECHANISM Submitted by Rongjin Yan Department of Electrical and Computer Engineering In partial fulfillment of the requirements For the Degree of Doctor of Philosophy Colorado State University Fort Collins, Colorado Fall 2011 Doctoral Committee: Advisor: Kevin L. Lear David S. Dandy V Chandrasekar Branislav Notaros Copyright by Rongjin Yan 2011 All Rights Reserved ABSTRACT A CMOS COMPATIBLE OPTICAL BIOSENSING SYSTEM BASED ON LOCAL EVANESCENT FIELD SHIFT MECHANISM The need for label-free integrated optical biosensors has dramatically increased in recent years. Integrated optical biosensors have many advantages, including low-cost, and portability. They can be applied to many fields, including clinical diagnostics, food safety, environmental monitoring, and biosecurity applications. One of the most important applications is point-of-care diagnosis, which means the disease could be tested at or near the site of patient care rather than in a laboratory. We are exploring the issues of design, modeling and measurement of a novel chip-scale local evanescent array coupled (LEAC) biosensor, which is an ideal platform for point-of-care diagnosis. Until now, three generations of LEAC samples have been designed, fabricated and tested. The 1st generation of LEAC sensor without a buried detector array was characterized using a commercial near field scanning optical microscope (NSOM). The sample was polished and was end-fire light coupled using single mode fiber. The field shift mechanism in this proof-to- concept configuration without buried detector arrays has been validated with inorganic adlayers[1], photoresist[2] and different concentrations of CRP proteins[3].