An Overview of Ball Aerospace Cryogen Storage and Delivery Systems
Total Page:16
File Type:pdf, Size:1020Kb
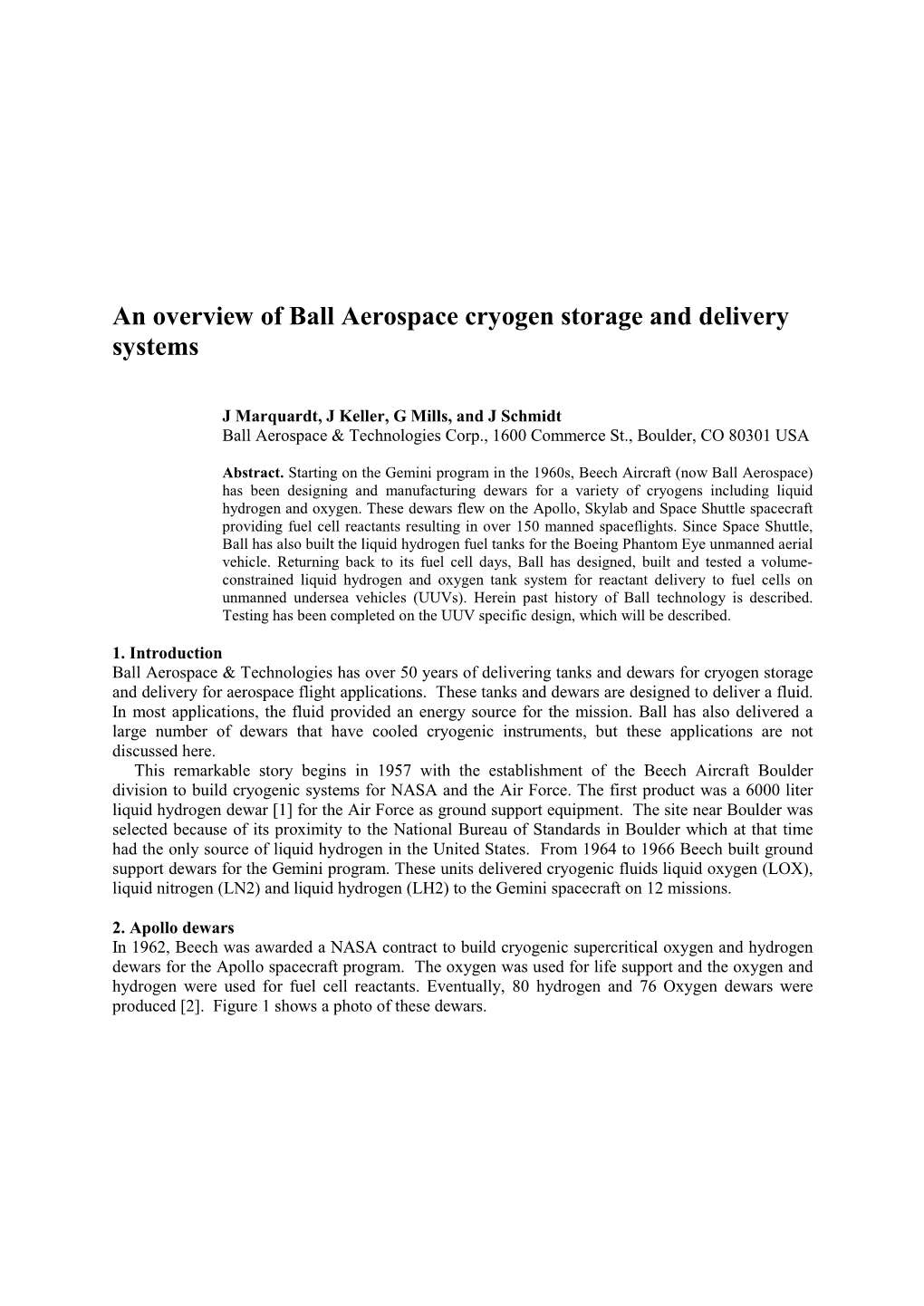
Load more
Recommended publications
-
Safety Consideration on Liquid Hydrogen
Safety Considerations on Liquid Hydrogen Karl Verfondern Helmholtz-Gemeinschaft der 5/JULICH Mitglied FORSCHUNGSZENTRUM TABLE OF CONTENTS 1. INTRODUCTION....................................................................................................................................1 2. PROPERTIES OF LIQUID HYDROGEN..........................................................................................3 2.1. Physical and Chemical Characteristics..............................................................................................3 2.1.1. Physical Properties ......................................................................................................................3 2.1.2. Chemical Properties ....................................................................................................................7 2.2. Influence of Cryogenic Hydrogen on Materials..............................................................................9 2.3. Physiological Problems in Connection with Liquid Hydrogen ....................................................10 3. PRODUCTION OF LIQUID HYDROGEN AND SLUSH HYDROGEN................................... 13 3.1. Liquid Hydrogen Production Methods ............................................................................................ 13 3.1.1. Energy Requirement .................................................................................................................. 13 3.1.2. Linde Hampson Process ............................................................................................................15 -
9 Xenon Handling and Cryogenics
9 Xenon Handling and Cryogenics 9.1 Overview The Xe handling and cryogenics strategy of LZ derives strongly from the successful LUX program and takes maximum advantage of key technologies demonstrated there: chromatographic krypton removal, high-flow online purification, high-efficiency two-phase heat exchange, sensitive in situ monitoring of Xe purity, and thermosyphon cryogenics. In many cases, the primary technical challenge of the LZ implementation is how to best scale up from LUX. Two classes of impurities are of concern: electronegatives such as O2 and H2O that suppress charge and light transport in the TPC, and radioactive noble gases such as 85Kr, 39Ar, and 222Rn that create backgrounds that are not amenable to self-shielding. Both types of impurities may be found in the vendor- supplied Xe, and both may also be introduced into the detector during operations via outgassing and emanation. The purity goals are summarized in Table 9.1.1. We have three mitigation techniques to control these impurities. First, electronegatives are suppressed during operations by continuous circulation of the Xe in gaseous form through a hot (450 oC) zirconium getter. Gettering in the gas phase is made practical by a two-phase heat exchanger. A metal-diaphragm gas pump drives the circulation and the system is capable of purifying the entire Xe stockpile in 2.3 days. Second, the problematic radioactive species, 85Kr and 39Ar, which have relatively long half-lives (10.8 years and 269 years, respectively) and no supporting parents, can be removed from the vendor-supplied Xe prior to the start of operations. -
Cryogenics in Space
— 37 — Cryogenics in space Nicola RandoI Abstract Cryogenics plays a key role on board space-science missions, with a range of applications, mainly in the domain of astrophysics. Indeed a tremendous progress has been achieved over the last 20 years in cryogenics, with enhanced reliability and simpler operations, thus matching the needs of advanced focal-plane detectors and complex science instrumentation. In this article we provide an overview of recent applications of cryogenics in space, with specific emphasis on science missions. The overview includes an analysis of the impact of cryogenics on the spacecraft system design and of the main technical solutions presently adopted. Critical technology developments and programmatic aspects are also addressed, including specific needs of future science missions and lessons learnt from recent programmes. Introduction H. Kamerlingh-Onnes liquefied 4He for the first time in 1908 and discovered superconductivity in 1911. About 100 years after such achievements (Pobell 1996), cryogenics plays a key role on board space-science missions, providing the environ- ment required to perform highly sensitive measurements by suppressing the thermal background radiation and allowing advantage to be taken of the performance of cryogenic detectors. In the last 20 years several spacecraft have been equipped with cryogenic in- strumentation. Among such missions we should mention IRAS (launched in 1983), ESA’s ISO (launched in 1995) (Kessler et al 1996) and, more recently, NASA’s Spitzer (formerly SIRTF, launched in 2006) (Werner 2005) and the Japanese mis- sion Akari (IR astronomy mission launched in 2006) (Shibai 2007). New missions involving cryogenics are the ESA missions Planck (dedicated to the mapping of the cosmic background radiation) and Herschel (far infrared and sub-millimetre observatory), carrying instruments operating at temperatures of 0.1 K and 0.3 K, respectively (Crone et al 2006). -
Cryogenics – the Basics Or Pre-Basics Lesson 1 D
Cryogenics – The Basics or Pre-Basics Lesson 1 D. Kashy Version 3 Lesson 1 - Objectives • Look at common liquids and gases to get a feeling for their properties • Look at Nitrogen and Helium • Discuss Pressure and Temperature Scales • Learn more about different phases of these fluids • Become familiar with some cryogenic fluids properties Liquids – Water (a good reference) H2O density is 1 g/cc 10cm Total weight 1000g or 1kg (2.2lbs) Cube of water – volume 1000cc = 1 liter Liquids – Motor Oil 10cm 15W30 density is 0.9 g/cc Total weight 900g or 0.9 kg (2lbs) Cube of motor oil – volume 1000cc = 1 liter Density can and usually does change with temperature 15W30 Oil Properties Density Curve Density scale Viscosity scale Viscosity Curve Water density vs temperature What happens here? What happens here? Note: This plot is for SATURATED Water – Discussed soon Water and Ice Water Phase Diagram Temperature and Pressure scales • Fahrenheit: 32F water freezes 212 water boils (at atmospheric pressure) • Celsius: 0C water freezes and 100C water boils (again at atmospheric pressure) • Kelvin: 273.15 water freezes and 373.15 water boils (0K is absolute zero – All motion would stop even electrons around a nucleus) • psi (pounds per square in) one can reference absolute pressure or “gage” pressure (psia or psig) • 14.7psia is one Atmosphere • 0 Atmosphere is absolute vacuum, and 0psia and -14.7psig • Standard Temperature and Pressure (STP) is 20C (68F) and 1 atm Temperature Scales Gases– Air Air density is 1.2kg/m3 => NO Kidding! 100cm =1m Total weight -
Cryogenicscryogenics Forfor Particleparticle Acceleratorsaccelerators Ph
CryogenicsCryogenics forfor particleparticle acceleratorsaccelerators Ph. Lebrun CAS Course in General Accelerator Physics Divonne-les-Bains, 23-27 February 2009 Contents • Low temperatures and liquefied gases • Cryogenics in accelerators • Properties of fluids • Heat transfer & thermal insulation • Cryogenic distribution & cooling schemes • Refrigeration & liquefaction Contents • Low temperatures and liquefied gases ••• CryogenicsCryogenicsCryogenics ininin acceleratorsacceleratorsaccelerators ••• PropertiesPropertiesProperties ofofof fluidsfluidsfluids ••• HeatHeatHeat transfertransfertransfer &&& thermalthermalthermal insulationinsulationinsulation ••• CryogenicCryogenicCryogenic distributiondistributiondistribution &&& coolingcoolingcooling schemesschemesschemes ••• RefrigerationRefrigerationRefrigeration &&& liquefactionliquefactionliquefaction • cryogenics, that branch of physics which deals with the production of very low temperatures and their effects on matter Oxford English Dictionary 2nd edition, Oxford University Press (1989) • cryogenics, the science and technology of temperatures below 120 K New International Dictionary of Refrigeration 3rd edition, IIF-IIR Paris (1975) Characteristic temperatures of cryogens Triple point Normal boiling Critical Cryogen [K] point [K] point [K] Methane 90.7 111.6 190.5 Oxygen 54.4 90.2 154.6 Argon 83.8 87.3 150.9 Nitrogen 63.1 77.3 126.2 Neon 24.6 27.1 44.4 Hydrogen 13.8 20.4 33.2 Helium 2.2 (*) 4.2 5.2 (*): λ Point Densification, liquefaction & separation of gases LNG Rocket fuels LIN & LOX 130 000 m3 LNG carrier with double hull Ariane 5 25 t LHY, 130 t LOX Air separation by cryogenic distillation Up to 4500 t/day LOX What is a low temperature? • The entropy of a thermodynamical system in a macrostate corresponding to a multiplicity W of microstates is S = kB ln W • Adding reversibly heat dQ to the system results in a change of its entropy dS with a proportionality factor T T = dQ/dS ⇒ high temperature: heating produces small entropy change ⇒ low temperature: heating produces large entropy change L. -
Materials for Liquid Propulsion Systems
https://ntrs.nasa.gov/search.jsp?R=20160008869 2019-08-29T17:47:59+00:00Z CHAPTER 12 Materials for Liquid Propulsion Systems John A. Halchak Consultant, Los Angeles, California James L. Cannon NASA Marshall Space Flight Center, Huntsville, Alabama Corey Brown Aerojet-Rocketdyne, West Palm Beach, Florida 12.1 Introduction Earth to orbit launch vehicles are propelled by rocket engines and motors, both liquid and solid. This chapter will discuss liquid engines. The heart of a launch vehicle is its engine. The remainder of the vehicle (with the notable exceptions of the payload and guidance system) is an aero structure to support the propellant tanks which provide the fuel and oxidizer to feed the engine or engines. The basic principle behind a rocket engine is straightforward. The engine is a means to convert potential thermochemical energy of one or more propellants into exhaust jet kinetic energy. Fuel and oxidizer are burned in a combustion chamber where they create hot gases under high pressure. These hot gases are allowed to expand through a nozzle. The molecules of hot gas are first constricted by the throat of the nozzle (de-Laval nozzle) which forces them to accelerate; then as the nozzle flares outwards, they expand and further accelerate. It is the mass of the combustion gases times their velocity, reacting against the walls of the combustion chamber and nozzle, which produce thrust according to Newton’s third law: for every action there is an equal and opposite reaction. [1] Solid rocket motors are cheaper to manufacture and offer good values for their cost. -
Atlas V Cutaway Poster
ATLAS V Since 2002, Atlas V rockets have delivered vital national security, science and exploration, and commercial missions for customers across the globe including the U.S. Air Force, the National Reconnaissance Oice and NASA. 225 ft The spacecraft is encapsulated in either a 5-m (17.8-ft) or a 4-m (13.8-ft) diameter payload fairing (PLF). The 4-m-diameter PLF is a bisector (two-piece shell) fairing consisting of aluminum skin/stringer construction with vertical split-line longerons. The Atlas V 400 series oers three payload fairing options: the large (LPF, shown at left), the extended (EPF) and the extra extended (XPF). The 5-m PLF is a sandwich composite structure made with a vented aluminum-honeycomb core and graphite-epoxy face sheets. The bisector (two-piece shell) PLF encapsulates both the Centaur upper stage and the spacecraft, which separates using a debris-free pyrotechnic actuating 200 ft system. Payload clearance and vehicle structural stability are enhanced by the all-aluminum forward load reactor (FLR), which centers the PLF around the Centaur upper stage and shares payload shear loading. The Atlas V 500 series oers 1 three payload fairing options: the short (shown at left), medium 18 and long. 1 1 The Centaur upper stage is 3.1 m (10 ft) in diameter and 12.7 m (41.6 ft) long. Its propellant tanks are constructed of pressure-stabilized, corrosion-resistant stainless steel. Centaur is a liquid hydrogen/liquid oxygen-fueled vehicle. It uses a single RL10 engine producing 99.2 kN (22,300 lbf) of thrust. -
Phase Change: Titan’S Disappearing Lakes
Phase Change: Titan’s Disappearing Lakes Investigation Notebook NYC Edition © 2018 by The Regents of the University of California. All rights reserved. No part of this publication may be reproduced or transmitted in any form or by any means, electronic or mechanical, including photocopy, recording, or any information storage or retrieval system, without permission in writing from the publisher. Teachers purchasing this Investigation Notebook as part of a kit may reproduce the book herein in sufficient quantities for classroom use only and not for resale. These materials are based upon work partially supported by the National Science Foundation under grant numbers DRL-1119584, DRL-1417939, ESI-0242733, ESI-0628272, and ESI-0822119. The Federal Government has certain rights in this material. Any opinions, findings, and conclusions or recommendations expressed in this material are those of the author(s) and do not necessarily reflect the views of the National Science Foundation. These materials are based upon work partially supported by the Institute of Education Sciences, U.S. Department of Education, through Grant R305A130610 to The Regents of the University of California. The opinions expressed are those of the authors and do not represent views of the Institute or the U.S. Department of Education. Developed by the Learning Design Group at the University of California, Berkeley’s Lawrence Hall of Science. Amplify. 55 Washington Street, Suite 800 Brooklyn, NY 11201 1-800-823-1969 www.amplify.com Phase Change: Titan’s Disappearing Lakes -
Introducing the 787 - Effect on Major Investigations - and Interesting Tidbits
Introducing the 787 - Effect on Major Investigations - And Interesting Tidbits Tom Dodt Chief Engineer – Air Safety Investigation ISASI September, 2011 COPYRIGHT © 2010 THE BOEING COMPANY Smith, 7-April-2011, ESASI-Lisbon | 1 787 Size Comparison 767-400 787-8 777-300 ~Pax 3-Class 245 250 368 ~Span 170 ft 197 ft 200 ft ~Length 201 ft 186 ft 242 ft ~MTGW 450,000 lbs 500,000 lbs 660,000 lbs ~Range 5,600 NM 7,650 NM 6,000 NM Cruise Mach 0.80 0.85 0.84 COPYRIGHT © 2010 THE BOEING COMPANY Smith, 7-April-2011, ESASI-Lisbon | 2 By weight 787 777 - Composites 50% 12% Composite Structure - Aluminum 20% 50% Other Carbon laminate Steel 5% Carbon sandwich 10% Fiberglass Titanium 15% Composites Aluminum 50% Aluminum/steel/titanium pylons Aluminum 20% COPYRIGHT © 2010 THE BOEING COMPANY Smith, 7-April-2011, ESASI-Lisbon | 3 COPYRIGHT © 2010 THE BOEING COMPANY Smith, 7-April-2011, ESASI-Lisbon | 4 787 Wing Flex - On-Ground On-Ground 0 ft COPYRIGHT © 2010 THE BOEING COMPANY Smith, 7-April-2011, ESASI-Lisbon | 5 787 Wing Flex - 1G Flight 1G Flight ~12 ft On-Ground 0 ft 1G Flight COPYRIGHT © 2010 THE BOEING COMPANY Smith, 7-April-2011, ESASI-Lisbon | 6 787 Wing Flex Ultimate-Load ~26 ft 1G Flight ~12 ft On-Ground 0 ft Max-Load COPYRIGHT © 2010 THE BOEING COMPANY Smith, 7-April-2011, ESASI-Lisbon | 7 787 Static Load Test @ Ultimate Load COPYRIGHT © 2010 THE BOEING COMPANY Smith, 7-April-2011, ESASI-Lisbon | 8 Investigations with Composite Materials • Terms: Composites Aluminum disbond fatigue delaminate beach marks inter-laminar shear striation counts water absorbsion corrosion fiber architecture metallurgical prop. -
Limitations of Spacecraft Redundancy: a Case Study Analysis
44th International Conference on Environmental Systems Paper Number 13-17 July 2014, Tucson, Arizona Limitations of Spacecraft Redundancy: A Case Study Analysis Robert P. Ocampo1 University of Colorado Boulder, Boulder, CO, 80309 Redundancy can increase spacecraft safety by providing the crew or ground with multiple means of achieving a given function. However, redundancy can also decrease spacecraft safety by 1) adding additional failure modes to the system, 2) increasing design “opaqueness”, 3) encouraging operational risk, and 4) masking or “normalizing” design flaws. Two Loss of Crew (LOC) events—Soyuz 11 and Challenger STS 51-L—are presented as examples of these limitations. Together, these case studies suggest that redundancy is not necessarily a fail-safe means of improving spacecraft safety. I. Introduction A redundant system is one that can achieve its intended function through multiple independent pathways or Aelements 1,2. In crewed spacecraft, redundancy is typically applied to systems that are critical for safety and/or mission success3,4. Since no piece of hardware can be made perfectly reliable, redundancy—in theory—allows for the benign (e.g. non-catastrophic) failure of critical elements. Redundant elements can be 1) similar or dissimilar to each other, 2) activated automatically (“hot spare”) or manually (“cold spare”), and 3) located together or separated geographically5-7. U.S. spacecraft have employed redundancy on virtually all levels of spacecraft design, from component to subsystem7,8. Redundancy has a successful history of precluding critical and catastrophic failures during human spaceflight. A review of NASA mission reports, from Mercury to Space Shuttle, indicates that redundancy has saved the crew or extended the mission over 160 times, or roughly once per flight9. -
Cryogenic Technology & Rocket Engines
ISSN (O): 2393-8609 International Journal of Aerospace and Mechanical Engineering Volume 2 – No.5, August 2015 Cryogenic Technology & Rocket Engines AKHIL GARG KARTIK JAKHU KISHAN SINGH ABHINAV B.Tech – Aerospace B.Tech – Aerospace B.Tech – Aerospace MAURYA Engg. Engg. Engg. B.Tech – Aerospace PUNJAB PUNJAB PUNJAB Engg. TECHNICAL TECHNICAL TECHNICAL PUNJAB UNIVERSITY, UNIVERSITY, UNIVERSITY, TECHNICAL JALANDHAR JALANDHAR JALANDHAR UNIVERSITY, akhilgarg.313@g kartik.lphawk@g kishansngh1996 JALANDHAR mail.com mail.com @gmail.com abhinavguru123 @gmail.com ABSTRACT 3.2 What is Cryogenic Rocket Engine? This paper is all about the rocket engine involving the use of A cryogenic rocket engine is a rocket engine that cryogenic technology at a cryogenic temperature (123K). This uses a cryogenic fuel or oxidizer, that is, its fuel or basically uses the liquid oxygen and liquid hydrogen as an oxidizer (or both) is gases liquefied and stored at oxidizer and fuel, which are very clean and non-pollutant very low temperatures. Notably, these engines were fuels compared to other hydrocarbon fuels like petrol, diesel, one of the main factors of the ultimate success in gasoline, LPG, CNG, etc., sometimes, liquid nitrogen is also reaching the Moon by the Saturn V rocket. used as an fuel. During World War II, when powerful rocket engines were first considered by the German, American and Keywords Soviet engineers independently, all discovered that Rocket engine, Cryogenic technology, Cryogenic temperature, rocket engines need high mass flow rate of both Liquid hydrogen and Oxygen. oxidizer and fuel to generate a sufficient thrust. At that time oxygen and low molecular weight 1. -
An Evidenced-Based Approach for Estimating Decompression Sickness Risk in Aircraft Operations
https://ntrs.nasa.gov/search.jsp?R=19990062137 2020-06-15T21:35:43+00:00Z View metadata, citation and similar papers at core.ac.uk brought to you by CORE provided by NASA Technical Reports Server NASA/TM--1999-209374 An Evidenced-Based Approach for Estimating Decompression Sickness Risk in Aircraft Operations Ronald R. Robinson Joseph P. Dervay Lyndon B. Johnson Space Center Houston, Texas 77058 Johnny Conkin National Space Biomedical Research Institute Houston, Texas 77030-3498 National Aeronautics and Space Administration Lyndon B. Johnson Space Center Houston, Texas 77058-4406 July 1999 Acknowledgments The authors wish to acknowledge Stephen Feaster and Charies Justiz, NASA Aircraft Operations Directorate, and Col. Bernard Burklund, Jr., Vice Commander, Headquarters Air Force Safety Center, for their assistance with aircraft operational data, and Dr. Alan Feiveson, NASA/Johnson Space Center, for his assistance with statistical analysis. Available from: NASA Center for AeroSpace Information National Technical Information Service 7121 Standard Drive 5285 Port Royal Road Hanover, MD 21076-1320 Springfield, VA 22161 301-621-0390 703-605-6000 This report is also available in electronic form at http://techreports.larc.nasa.gov/cgi-bin/NTRS Contents Contents ...................................................................................................................................... iii Introduction ................................................................................................................................ 1 Methods