Piezoelectric Negative Capacitance
Total Page:16
File Type:pdf, Size:1020Kb
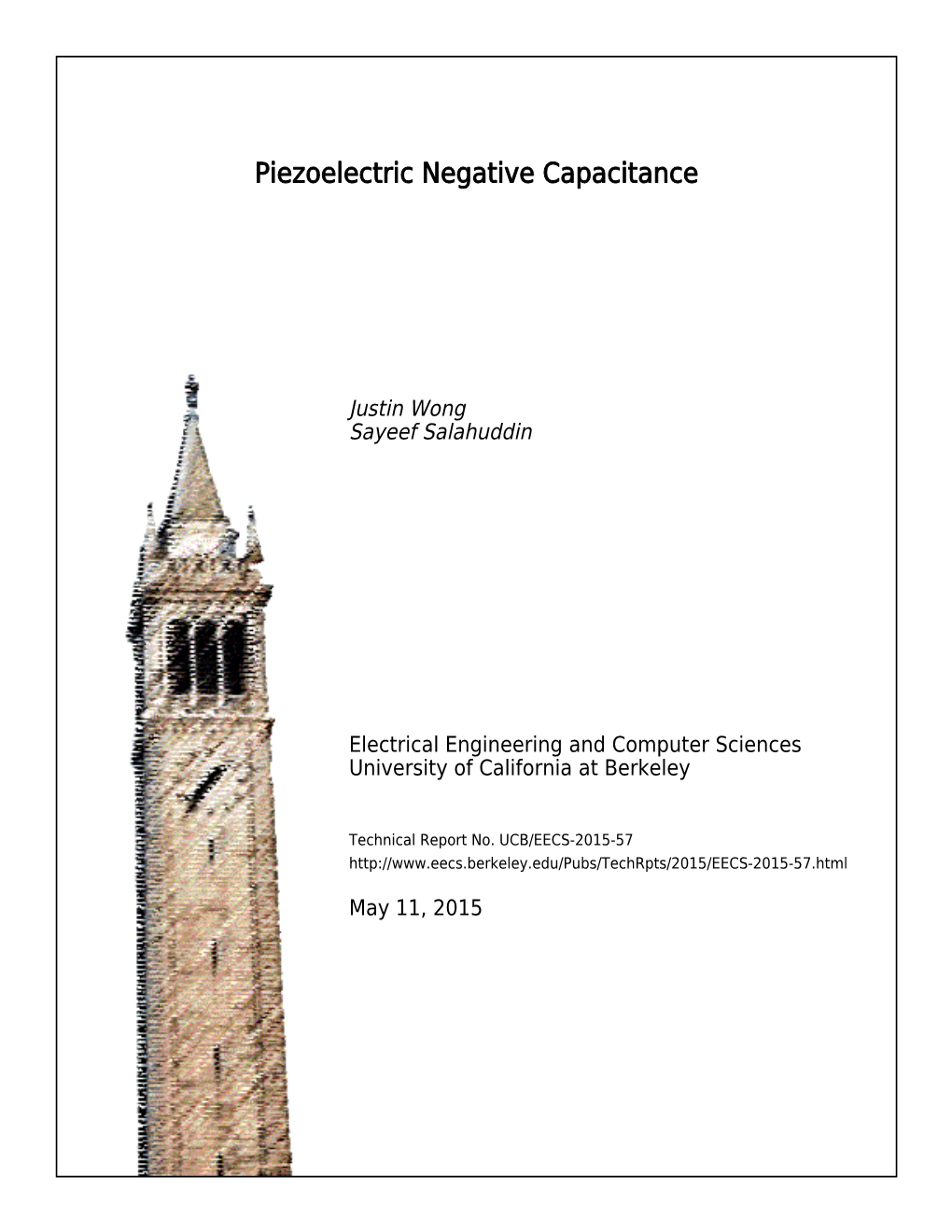
Load more
Recommended publications
-
PHYSICS Glossary
Glossary High School Level PHYSICS Glossary English/Haitian TRANSLATION OF PHYSICS TERMS BASED ON THE COURSEWORK FOR REGENTS EXAMINATIONS IN PHYSICS WORD-FOR-WORD GLOSSARIES ARE USED FOR INSTRUCTION AND TESTING ACCOMMODATIONS FOR ELL/LEP STUDENTS THE STATE EDUCATION DEPARTMENT / THE UNIVERSITY OF THE STATE OF NEW YORK, ALBANY, NY 12234 NYS Language RBERN | English - Haitian PHYSICS Glossary | 2016 1 This Glossary belongs to (Student’s Name) High School / Class / Year __________________________________________________________ __________________________________________________________ __________________________________________________________ NYS Language RBERN | English - Haitian PHYSICS Glossary | 2016 2 Physics Glossary High School Level English / Haitian English Haitian A A aberration aberasyon ability kapasite absence absans absolute scale echèl absoli absolute zero zewo absoli absorption absòpsyon absorption spectrum espèk absòpsyon accelerate akselere acceleration akselerasyon acceleration of gravity akselerasyon pezantè accentuate aksantye, mete aksan sou accompany akonpaye accomplish akonpli, reyalize accordance akòdans, konkòdans account jistifye, eksplike accumulate akimile accuracy egzatitid accurate egzat, presi, fidèl achieve akonpli, reyalize acoustics akoustik action aksyon activity aktivite actual reyèl, vre addition adisyon adhesive adezif adjacent adjasan advantage avantaj NYS Language RBERN | English - Haitian PHYSICS Glossary | 2016 3 English Haitian aerodynamics ayewodinamik air pollution polisyon lè air resistance -
Piezoelectric Solutions: Piezo Components & Materials
Piezoelectric Solutions Part I - Piezo Components & Materials Part II - Piezo Actuators & Transducers BAUELEMENTE, TECHNOLOGIE, ANSTEUERUNG Part III - Piezo Actuator Tutorial PIEZOWWW.PICERAMIC.DE TECHNOLOGY Contents Part I - Piezo Components & Materials .......... .3 Part II - Piezo Actuators & Transducers . .40 Part III - Piezo Actuator Tutorial ........ .73 Imprint PI Ceramic GmbH, Lindenstrasse, 07589 Lederhose, Germany Registration: HRB 203 .582, Jena local court VAT no .: DE 155932487 Executive board: Albrecht Otto, Dr . Peter Schittenhelm, Dr . Karl Spanner Phone +49 36604-882-0, Fax +49-36604-882-4109 info@piceramic .com, www .piceramic .com Although the information in this document has been compiled with the greatest care, errors cannot be ruled out completely . Therefore, we cannot guarantee for the information being complete, correct and up to date . Illustrati- ons may differ from the original and are not binding . PI reserves the right to supplement or change the information provided without prior notice . All contents, including texts, graphics, data etc ., as well as their layout, are subject to copyright and other protective laws . Any copying, modification or redistribution in whole or in parts is subject to a written permission of PI . The following company names and brands are registered trademarks of Physik Instrumente (PI) GmbH & Co . KG : PI®, PIC®, NanoCube®, PICMA®, PILine®, NEXLINE®, PiezoWalk®, NEXACT®, Picoactuator®, PIn- ano®, PIMag® . The following company names or brands are the registered trademarks of their -
Piezoelectric Crystal Experiments for High School Science and En- Gineering Students
Paper ID #14540 MAKER: Piezoelectric Crystal Experiments for High School Science and En- gineering Students Mr. William H. Heeter, Porter High School Engineering Dept. My name is William (Bill) Heeter. I graduated from Texas A&M with an Engineering degree in 1973. I worked in Industrial Distribution for over 30 years before becoming a high school pre-engineering teacher. I have been teaching engineering and technology for the past 13 years. I have been a Master Teacher for ”Project Lead the Way”, CTE co-Director, CTE Building Chair, Technology Teacher. My students have received many awards and college scholarships. One group of students received a provisional U.S. Patent. Several students have seen their work actually produced by industry, including the ordering touch screens used by Bucky’s. Dr. Sheng-Jen ”Tony” Hsieh, Texas A&M University Dr. Sheng-Jen (”Tony”) Hsieh is a Professor in the Dwight Look College of Engineering at Texas A&M University. He holds a joint appointment with the Department of Engineering Technology and the De- partment of Mechanical Engineering. His research interests include engineering education, cognitive task analysis, automation, robotics and control, intelligent manufacturing system design, and micro/nano manufacturing. He is also the Director of the Rockwell Automation laboratory at Texas A&M University, a state-of-the-art facility for education and research in the areas of automation, control, and automated system integration. Dr. Jun Zou, Department of Electrical and Computer Engineering, Texas A&M University Jun Zou received his Ph.D. degree in electrical engineering from the University of Illinois at Urbana- Champaign in 2002. -
Piezoelectricity of Single-Atomic-Layer Mos2 for Energy Conversion and Piezotronics
LETTER doi:10.1038/nature13792 Piezoelectricity of single-atomic-layer MoS2 for energy conversion and piezotronics Wenzhuo Wu1*, Lei Wang2*, Yilei Li3, Fan Zhang4, Long Lin1, Simiao Niu1, Daniel Chenet4, Xian Zhang4, Yufeng Hao4, Tony F. Heinz3, James Hone4 & Zhong Lin Wang1,5 The piezoelectric characteristics of nanowires, thin films and bulk The strain-induced polarization charges in single-layer MoS2 can also crystals have been closely studied for potential applications in sensors, modulate charge carrier transport at the MoS2–metal barrier and enable transducers, energy conversion and electronics1–3.Withtheirhighcrys- enhanced strain sensing. In addition, we have also observed large piezo- 4–6 tallinity and ability to withstand enormous strain , two-dimensional resistivity in even-layer MoS2 with a gauge factor of about 230 for the materials are of great interest as high-performance piezoelectric mate- bilayer material, which indicates a possible strain-induced change in band 18 rials. Monolayer MoS2 is predicted to be strongly piezoelectric, an structure . Our study demonstrates the potential of 2D nanomaterials effect that disappears in the bulk owing to the opposite orientations in powering nanodevices, adaptive bioprobes and tunable/stretchable of adjacent atomic layers7,8. Here we report the first experimental electronics/optoelectronics. study of the piezoelectric properties of two-dimensional MoS2 and In our experiments, MoS2 flakes were mechanically exfoliated onto show that cyclic stretching and releasing of thin MoS2 flakes with an a polymer stack consisting of water-soluble polyvinyl alcohol and poly odd number of atomic layers produces oscillating piezoelectric volt- (methyl methacrylate) on a Si substrate, with the total polymer thickness age and current outputs, whereas no output is observed for flakes with tuned to be 275 nm for good optical contrast. -
Intrinsic Piezoelectricity in Two-Dimensional Materials † † Karel-Alexander N
Letter pubs.acs.org/JPCL Intrinsic Piezoelectricity in Two-Dimensional Materials † † Karel-Alexander N. Duerloo, Mitchell T. Ong, and Evan J. Reed* Department of Materials Science and Engineering, Stanford University, Stanford, California 94305, United States ABSTRACT: We discovered that many of the commonly studied two-dimensional monolayer transition metal dichalcogenide (TMDC) nanoscale materials are piezoelectric, unlike their bulk parent crystals. On the macroscopic scale, piezoelectricity is widely used to achieve robust electromechanical coupling in a rich variety of sensors and actuators. Remarkably, our density-functional theory calculations of the piezoelectric coefficients of monolayer BN, MoS2, MoSe2, MoTe2,WS2, WSe2, and WTe2 reveal that some of these materials exhibit stronger piezoelectric coupling than traditionally employed bulk wurtzite structures. We find that the piezoelectric coefficients span more than 1 order of magnitude, and exhibit monotonic periodic trends. The discovery of this property in many two- dimensional materials enables active sensing, actuating, and new electronic components for nanoscale devices based on the familiar piezoelectric effect. SECTION: Physical Processes in Nanomaterials and Nanostructures anoelectromechanical systems (NEMS) and nanoscale adsorption20 or introduction of specific in-plane defects,21 N electronics are the final frontier in the push for paving the way to a strong miniaturization and site-specific miniaturization that has been among the dominant themes of engineering of familiar piezoelectric technology using graphene. technological progress for over 50 years. Enabled by We now report that a family of widely studied atomically thin increasingly mature fabrication techniques, low-dimensional sheet materials are in fact intrinsically piezoelectric, elucidating materials including nanoparticles, nanotubes, and (near- an entirely new arsenal of “out of the box” active components )atomically thin sheets have emerged as the key components for NEMS and piezotronics. -
Piezoelectricity
Piezoelectricity • Polarization does not disappear when the electric field removed. • The direction of polarization is reversible. Polarization saturation Ps Remenent polarization Pr +Vc Voltage Coercive voltage Figure by MIT OCW FRAM utilize two stable positions. Figure by MIT OCW 15 Sang-Gook Kim, MIT Hysterisis ) 2 m c / C µ ( n o i t a z i r a l o P Electric Field (kV/cm) Ferroelectric (P-E) hysteresis loop. The circles with arrows indicate the polarization state of the material for different fields. 16 Sang-Gook Kim, MIT Figure by MIT OCW. Domain Polarization • Poling: 100 C, 60kV/cm, PZT • Breakdown: 600kV/cm, PZT •Unimorphcantilever Sang-Gook Kim, MIT 17 Piezoelectricity Direct effect D = Q/A = dT E = -gT T = -eE Converse effect E = -hS S = dE g = d/ε = d/Kε o • D: dielectric displacement, electric flux density/unit area • T: stress, S: strain, E: electric field • d: Piezoelectric constant, [Coulomb/Newton] Free T d = (∂S/∂E) T = (∂D/∂T) E Boundary Conditions Short circuit E g = (-∂E/∂T) D = (∂S/∂D) T Open circuit D e = (-∂T/∂E)S = (∂D/∂S) E h = (-∂T/∂D) = (-∂E/∂S) Clamped S S D Sang-Gook Kim, MIT 18 Principles of piezoelectric Electric field(E) g β Ele -h c tr ct ε o fe - f th e e c r ri Dielectric m t a Displacement(D) l ec e el f o d fe -e c iez d t P g -e Strain(S) Entropy -h s Stress(T) c Temperature Thermo-elastic effect Sang-Gook Kim, MIT 19 Equation of State Basic equation E d-form Sij = sijkl Tkl+dkijEk cE = 1/sE T E Di = diklTkl+ εik Ek e = dc g-form S = sDT+gD E T E ε = ε -dc dt T E = -gT+ β D βT = 1/εT E T e-form Tij -
IEEE-NMDC 2012 Conference Paper
Proceedings of the 2012 IEEE Nanotechnology Material and Devices Conference October 16-19, 2012, Hawaii, USA Investigation of PVDF-TrFE Nanofibers for Energy Harvesting Sumon Dey, Mohsen Purahmad*, Suman Sinha Ray Alexander L. Yarin, Mitra Dutta, Fellow, IEEE *[email protected] Abstract- We have investigated the copolymer polyvinylidene energy harvesting, the generated pulse width is a critical fluoride, (PVDF-trifluoroethylene) for energy harvesting. parameter which should be considered during interface circuit Polyvinylidene fluoride (PVDF) nanofibers were electrospun on indium tin oxide (ITO) coated plastic. The electrical response of design and it can strongly affect the operation of interface nanofibers at different frequencies was investigated. The circuit and the net energy gain. experimental results demonstrate that the duty cycle of electrical The aim of this paper is to describe the effect of frequency response pulses is increased as the frequency of vibration is on the generated pulse widths from randomly oriented PVDF- increased. By using the fast Fourier transform (FFT) of the TrFE nanofibers. Experimental results demonstrate the change response pulses, the maximum power extracted has been calculated. of pulse widths on changing the frequency of the applied mechanical pressure. In addition, we also calculated maximum attainable power from PVDF-TrFE nanofibers. NTRODUCTION I. I A promising method of energy harvesting is the use II. PIEZOELECTRICITY EFFECT piezoelectric materials to capitalize on the ambient vibrations. Since the demand for high-performance wireless sensors is Piezoelectricity is the result of the rearrangement of increasing continuously, energy harvesting has been the focus electronic charges in materials with no inversion symmetry of much research for this application. -
A Review on Mechanisms for Piezoelectric-Based Energy Harvesters
energies Review A Review on Mechanisms for Piezoelectric-Based Energy Harvesters Hassan Elahi ∗,† ID , Marco Eugeni † and Paolo Gaudenzi † Department of Mechanical and Aerospace Engineering, Sapienza University of Rome, Via Eudossiana 18, 00184 Rome, Italy; [email protected] (M.E.); [email protected] (P.G.) * Correspondence: [email protected]; Tel.: +39-327-6544166 † These authors contributed equally to this work. Received: 23 May 2018; Accepted: 28 June 2018; Published: 14 July 2018 Abstract: From last few decades, piezoelectric materials have played a vital role as a mechanism of energy harvesting, as they have the tendency to absorb energy from the environment and transform it to electrical energy that can be used to drive electronic devices directly or indirectly. The power of electronic circuits has been cut down to nano or micro watts, which leads towards the development of self-designed piezoelectric transducers that can overcome power generation problems and can be self-powered. Moreover, piezoelectric energy harvesters (PEHs) can reduce the need for batteries, resulting in optimization of the weight of structures. These mechanisms are of great interest for many researchers, as piezoelectric transducers are capable of generating electric voltage in response to thermal, electrical, mechanical and electromagnetic input. In this review paper, Fluid Structure Interaction-based, human-based, and vibration-based energy harvesting mechanisms were studied. Moreover, qualitative and quantitative analysis of existing PEH mechanisms has been carried out. Keywords: piezoelectric; energy harvesting; vibrations; aeroelastic; smart material; fluid structure interaction; piezoelectricity; review 1. Introduction The phenomenon of energy harvesting based on piezoelectric transducers can be defined as the transformation of energy absorbed by a transducer from an operating environment to electric voltage that be used on the spot for actuation or stored in batteries for future usage [1–4]. -
Structure and Properties of Lead Zirconate Titanate Thin Films by Pulsed Laser Deposition GOH WEI CHUAN
Structure and Properties of Lead Zirconate Titanate Thin Films by Pulsed Laser Deposition GOH WEI CHUAN (B.Sc (Hons), NUS) A THESIS SUBMITTED FOR THE DEGREE OF Doctoral of Philosophy Department of Physics National University of Singapore 2005 Acknowledgements I would like to express my deepest gratitude to my supervisors, Prof. Ong Chong Kim and Dr. Yao Kui. I would like to thank Prof. Ong for giving me the opportunity to study and perform research work in the Center of Superconducting and Magnetic Materials (CSMM). His passion and enthusiasm in the search for understanding the underlying physics of the experiments have deeply influenced my mindset in conducting experiments and will continue to be my source of inspiration and guidance. Without Prof. Ong’s constant guidance and criticism, I would have lost my bearing in the vast sea of knowledge, and would not have reached this far. I would also like to express my greatest appreciation to Dr. Yao Kui in Institute of Material Research and Engineering (IMRE). His constant advice and meticulous attention to the theoretical and experimental details had deeply influenced my way of research both in designing experiments and interpreting the results. Without his supervision and encouragements in countless hours of his time, it would not be possible for me to complete my publications and thesis. For that I am in debt to him and will forever remember his advice when pursuing my future endeavors. I am indebted to my fellow colleagues in CSMM, IMRE and Department of Physics, NUS, including A/P Sow Chorng Haur, Xu Sheng Yong, Wang Shi Jie, Li Jie, Yang Tao, Tan Chin Yaw, Rao Xue Song, Chen Lin Feng, Yan Lei, Kong Lin Bing, Liu Hua Jun, Lim Poh Chong, Yu Shu Hui, Gan Bee Keen and all those have shared their time helping me and discussing with me in this project. -
THE PIEZOELECTRIC QUARTZ RESONATOR Kanr- S. Vaw Dvrn*
THE PIEZOELECTRIC QUARTZ RESONATOR Kanr- S. Vaw Dvrn* CoNtsxrs Page 214 I. The Contributing Properties of Quartz . d1A A. Highly Perfect Elastic Properties. B. The Piezoelectric Property 216 C. ThePiezoelectricResonator. 2t6 D. Other Factors in the Common Circuit Use of Quartz 2r8 IL The Mdchanism of Circuit Influence by Quartz. 219 A. The Piezoelectric Strain-Current Relation 219 B. The Several Circuit Uses of a Crystal Resonator. ' '. 220 C. Crystal-Controlled Oscillators. 221 III. The Importance of Constant Frequencies in Communication ' ' ' " 223 A. Carrier Current Versus Simple Telephone Circuits. 223 ,14 B. The Carrier Principle in Radio Telephony . ' ' nnA C. Precision of Frequencies Essential. D. Tactical Benefits frorn Crystal Control . 225 IV. Thelmportanceof the Orientation of Quartz Radio Elements' " ' " " ' " ' 226 A. Orientation for Desired Mechanical Properties. ... 226 B. Predimensioning: Precise Duplication of Orientation and Dimensions' " ' ' 227 C. The Efiects of Orientation on Piezoelectric Properties. 228 D. The ObliqueCuts......... 229 V. The Ranges of the Characteristics in Quartz Crystal Units ' ' ' 229 A. Size of Crystal Plate or Bar.. ' 230 B. Frequency. 230 C. Type of Vibration. 230 232 D. "Cuts". .... E. Temperature Coeffcients of Frequenry. 234 F. Temperature Range. 235 G. Load Circuit. 235 H. Activity. 2s6 I. Voltage and Power Dissipation. 237 239 J. Finish, Surface, and Mounting of Quartz Resonators ' K. Holders. 240 VI. A Commenton the Future of PiezoelectricResonators' 241 VII. ListinEs of a Few Referencesin the GeneralField of This Paper' 243 L TnB CoNrnrnurrNc PRoPERTTESoF Quanrz A. Highly Perfect Elastic Properties The excellenceof quartz for use in frequency control is expressedin the large numerical values of Q in q\r.artzresonators, which the use of this * Director of Research, Long Branch Signal Laboratory, U' S' Army Signal Corps' Also, Professor of Physics, Wesleyan University, on leave of absence' 214 PIEZOELECTRTCIUARTZ RESONATOR 2tS highly elastic material makes possible. -
High Performance Piezoelectric MEMS Microphones
High Performance Piezoelectric MEMS Microphones by Robert John Littrell A dissertation submitted in partial fulfillment of the requirements for the degree of Doctor of Philosophy (Mechanical Engineering) in The University of Michigan 2010 Doctoral Committee: Professor Karl Grosh, Chair Professor David R. Dowling Professor Khalil Najafi Assistant Professor Kenn Richard Oldham TABLE OF CONTENTS LIST OF FIGURES ............................... iv LIST OF TABLES ................................ vii LIST OF ABBREVIATIONS ......................... viii LIST OF SYMBOLS .............................. x CHAPTER I. Introduction .............................. 1 1.1 Capacitive and Piezoelectric MEMS Microphones . 1 1.2 Noise ............................... 3 1.3 Sensitivity ............................ 5 1.4 Linearity ............................. 8 1.5 Piezoelectric Materials . 9 1.6 Capacitive Microphone Embodiments . 11 1.7 Piezoelectric Microphone Embodiments . 12 1.8 GapsintheLiterature...................... 13 II. Modeling ................................ 15 2.1 Noise ............................... 16 2.1.1 Microphone Transducer Noise . 16 2.1.2 Microphone Circuitry Noise . 22 2.2 Sensitivity ............................ 25 2.2.1 Cantilever Transducer Sensitivity . 25 2.2.2 Diaphragm Transducer Sensitivity . 31 2.3 Linearity ............................. 35 2.3.1 THD of a Common Source Amplifier . 36 2.3.2 THDMeasurementResonator . 37 2.4 Combining Piezoelectric Elements . 38 2.5 Microphone Optimization . 41 ii 2.5.1 CantileverTransducer. 42 2.5.2 -
A New PZT (Lead Zirconate Titanate) Piezoelectric Transducer Performances Analysis
International Journal of Research Studies in Science, Engineering and Technology Volume 1, Issue 6, September 2014, PP 1-7 ISSN 2349-4751 (Print) & ISSN 2349-476X (Online) A new PZT (Lead Zirconate Titanate) Piezoelectric Transducer Performances Analysis Pande A.S1, Prof (Dr.) Kushare B.E.2, Prof. A.K.Pathak3 1Electrical Engineering Dept. K. K. Wagh Institute of Engineering Education and Research, Nashik (MS), India. (Research Schola) 2Professor & H.O.D., Electrical Engineering Dept, K. K. Wagh Institute of Engineering Education and Research, Nashik (MS), India 3Electrical Engineering Dept. AVCOE, Sanagamner, Ahmednagar (MS), India Abstract: Presently there is number of Current measuring devices/ instrument are widely use for measurement of low and high current measurement. In the past decades there was surprisingly low attention of Electrical sensor, this sensor are very useful for replacing some kind of equipment in our existing power system. These measuring requirements are fulfill by using conventional sources out of which Piezoelectric Transducer is having major contribution in future. Considering the rate at which conventional sources are being consumed more power, cost, size and their life into control of power system, it is necessary to adopt alternate current measure ring technology for sustainable development. Out of various current measuring systems, Piezoelectric Transducer is most cost effective in addition to its various advantages. Considering the increasing share of Piezoelectric Transducer interfaced into the system it is necessary to study the power quality and current quality and stability issues. In case of conventional type CT use of copper is cost effective way is essential. This paper presents the operating principle, the performance MATLAB/SIMULATION, and the design of a piezoelectric transducer for measuring high currents.