Design, Fabrication, and Characterization of Carbon Nanotube Field Emission Devices for Advanced Applications
Total Page:16
File Type:pdf, Size:1020Kb
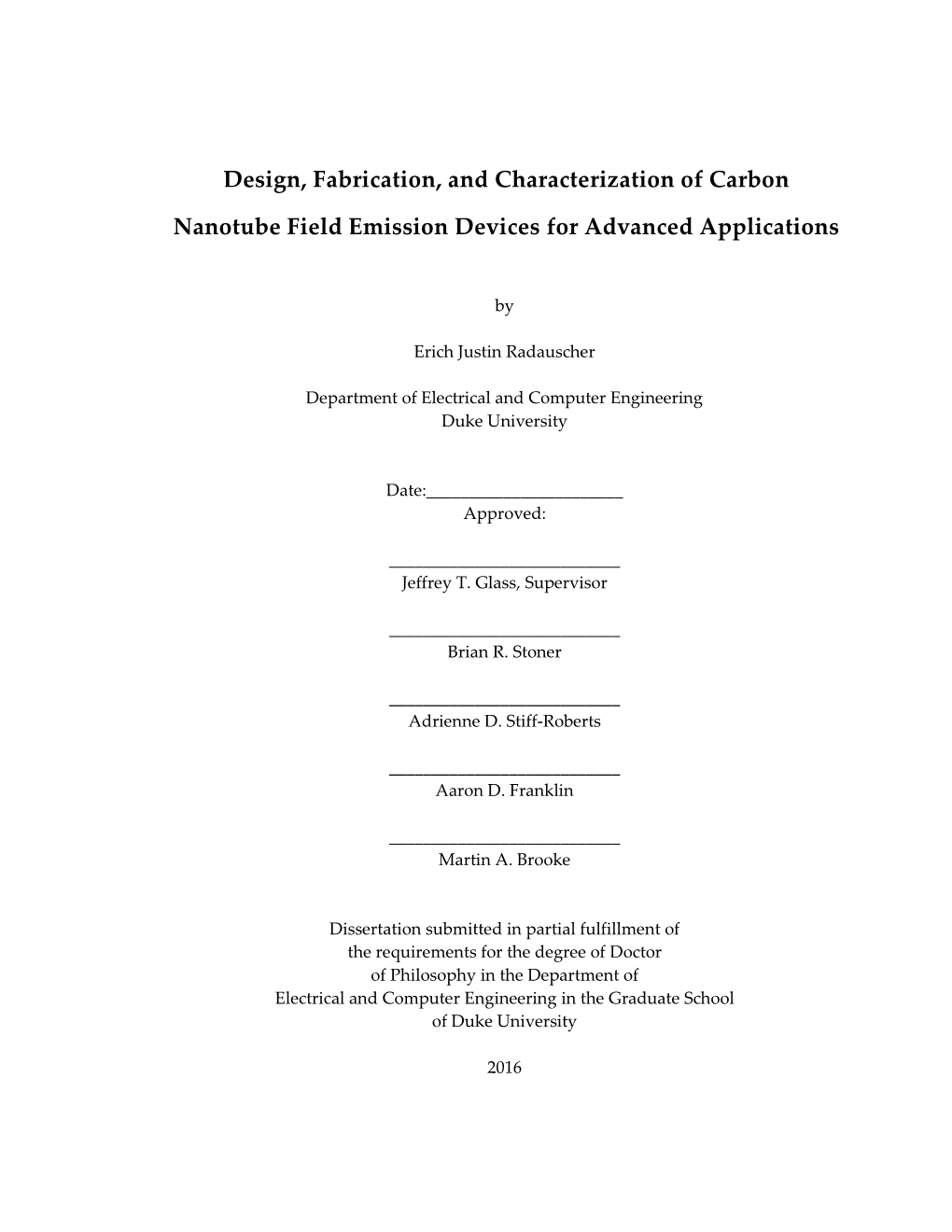
Load more
Recommended publications
-
UNIT CONVERSION FACTORS Temperature K C 273 C 1.8(F 32
Source: FUNDAMENTALS OF MICROSYSTEMS PACKAGING UNIT CONVERSION FACTORS Temperature K ϭ ЊC ϩ 273 ЊC ϭ 1.8(ЊF Ϫ 32) ЊR ϭ ЊF ϩ 460 Length 1 m ϭ 1010 A˚ ϭ 3.28 ft ϭ 39.4 in Mass 1 kg ϭ 2.2 lbm Force 1 N ϭ 1 kg-m/s2 ϭ 0.225 lbf Pressure (stress) 1 P ϭ 1 N/m2 ϭ 1.45 ϫ 10Ϫ4 psi Energy 1 J ϭ 1W-sϭ 1 N-m ϭ 1V-C 1Jϭ 0.239 cal ϭ 6.24 ϫ 1018 eV Current 1 A ϭ 1 C/s ϭ 1V/⍀ CONSTANTS Avogadro’s Number 6.02 ϫ 1023 moleϪ1 Gas Constant, R 8.314 J/(mole-K) Boltzmann’s constant, k 8.62 ϫ 10Ϫ5 eV/K Planck’s constant, h 6.63 ϫ 10Ϫ33 J-s Speed of light in a vacuum, c 3 ϫ 108 m/s Electron charge, q 1.6 ϫ 10Ϫ18 C SI PREFIXES giga, G 109 mega, M 106 kilo, k 103 centi, c 10Ϫ2 milli, m 10Ϫ3 micro, 10Ϫ6 nano, n 10Ϫ9 Downloaded from Digital Engineering Library @ McGraw-Hill (www.digitalengineeringlibrary.com) Copyright © 2004 The McGraw-Hill Companies. All rights reserved. Any use is subject to the Terms of Use as given at the website. Source: FUNDAMENTALS OF MICROSYSTEMS PACKAGING CHAPTER 1 INTRODUCTION TO MICROSYSTEMS PACKAGING Prof. Rao R. Tummala Georgia Institute of Technology ................................................................................................................. Design Environment IC Thermal Management Packaging Single Materials Chip Opto and RF Functions Discrete Passives Encapsulation IC Reliability IC Assembly Inspection PWB MEMS Board Manufacturing Assembly Test Downloaded from Digital Engineering Library @ McGraw-Hill (www.digitalengineeringlibrary.com) Copyright © 2004 The McGraw-Hill Companies. -
July 2019 Newsletter GEARS Founded August 13, 1939 News
July 2019 Newsletter GEARS Founded August 13, 1939 News Field day was a success. This year GARS joined us out at the Masonic Lodge. The weather was very comfortable for a change. While band conditions were difficult at first, they improved by the morning. We haven’t totaled the points yet, however it seems that we did better than last year. We also got coverage from Action News and the Chico Enterprise Record. See photos below. My house was struck by lighting on May 30th, hitting my antenna and traveling down the feed line, through the radios and discharged into the house wiring. Fortunately the fire department put out the fire quickly and minimized damage. I’m off the air until repairs are completed to the house. See photo below. The GEARS/GARS new repeater project is proceeding along. The equipment has been ordered. We are waiting for approval from the US Forest Service before we can begin installation. At our next GEARS meeting Kevin Fullerton WB7SKS will be talking about emergency operations for the Camp Fire. He has some very interesting experiences to tell us about, and suggestions for preparing for emergencies. The Steak Bake is Sep.7th at Wildwood picnic area in Chico at 3:30pm - 7pm. This month our feature article is about Sir John Ambrose Fleming’s invention of the vacuum tube. ‘73 Join GEARS on Facebook Jim Matthews K6EST www.facebook.com For timely [email protected] news and additional information. 530-893-3314 July 2019 Calendar Sun Mon Tue Wed Thu Fri Sat 1 2 3 4 5 6 7pm GARS Net 7:30pm GEARS Net 7pm Simplex Net 8pm -
1990-04: Sir Ambrose Fleming
When 1 Think Back.. by Neville Williams Sir John Ambrose Fleming: He invented radio valves - or did he? Dr/Professor Sir John Ambrose Fleming is remembered primarily as the inventor of the Fleming thermionic, diode and the 'father' of radio valves, which were fundamental to the subsequent development of the industry. Whether or not this is strictly correct is debateable but, either way, Ambrose Fleming made a very considerable contribution to basic electrical and electronic technology. Curiously, one finds scant mention, in patent rights in respect to the ther- relevant textbooks, of Fleming's per- mionic diode; but more about that later! sonal background or his academic ca- Sir John Ambrose Fleming - a gifted reer. Beyond the fact that he was born Fleming the academic scientist of his day. in 1849, the texts to which I had access Curious about Fleming's academic ca- make little or no reference to his birth- reer, I checked through a number of old I have little doubt that the 'rules-of- place, his family or the steps in his ca- reference books in my possession. thumb' we were invited to memorise in reer which led to his ultimate knight- First off, a brief entry in a 60-year old other days were devised by John Am- hood. Pear's encyclopedia indicated that Flem- brose Fleming, the subject of this pre- The British technical writer/consultant ing's involvement with the University sent article. S. Handel comes closest in The Elec- College spanned 40-odd years, from There is no ambiguity, however, tronic Revolution (Penguin Books, UK, 1885 to 1926, by which time he would about the Dr J.A. -
Birth of the Valve.Indd 68 25/01/2019 08:21 Attention to the Problem of Developing an Eff Cient Receiving Detector
Feature by Dr Bruce Taylor HB9ANY ● E-mail: [email protected] Birth of the Thermionic Valve n the archives of Marconi’s Dr Bruce Taylor HB9ANY relates how chance, ingenuity Wireless Telegraph Company and confl ict created the technology that dominated radio for November 1904, there is a handwritten letter that communication for half a century. concludes: “I have not mentioned Ithis to anyone yet, as it may become useful”. The letter is signed by the English scientist John Ambrose Fleming and it describes how he had found a method of detecting oscillatory electrical currents in an antenna using a thermionic valve. “It may become useful” was perhaps the understatement of the century! While the saga of the thermionic valve had a large cast, the two principal roles were initially played by Fleming and the American experimenter Lee de Forest. The characters of these two men could hardly have been more different. De Forest was an enterprising inventor but a f amboyant showman unashamedly motivated by a desire for fame, fortune and a luxurious life style. He was lucky in his discoveries, but not in his private life or his somewhat unethical business practices, and he died in 1961 without achieving the f nancial success of which he dreamed. Fleming, on the other hand, was the careful archetypal physicist, methodical in his investigations and A 1915 advertisement by Elmer Cunningham explains that, unlike the de Forest Audion, his AudioTron motivated to earn the esteem and can be bought alone. recognition of his peers for advancing scientif c knowledge. He achieved his aim, he patented the device as a means for The Fleming Diode and was knighted in 1929, but he wasn’t controlling mains voltage but made no In 1899, Fleming had been appointed interested in vigorously exploiting his mention of its rectifying properties, for he scientif c advisor to Marconi and became discoveries and left Marconi and others was promoting DC rather than AC power responsible for the design of part of the to prof t from their commercialisation. -
Sir John Ambrose Fleming
Supplement to the Histelec News No. S59 April 2015 SIR JOHN AMBROSE FLEMING By Peter Lamb Ambrose Fleming, as he was generally known, interests me greatly, because he was a man of many parts, although he is known as the inventor of the Thermionic Valve and the “father of electronics”, he managed to fit in quite a bit of consultancy work, which is where I have come across him several times. - - - - - - - - - - - - - - - - - - - - - - - - - - - - - - - - - - - - - - - - - - - - - - - - - - - - - - - - - - - - - - - - - - - John Ambrose Fleming was born in He then obtained a post as Professor of November 1849 at Lancaster, the son of a Physics and Maths at Nottingham University, Congregational Minister. His parents moved but only stayed for less than a year, wanting shortly afterwards to North London, where he to return to London. It transpired that he had a was educated being sent to a private school cousin Arnold White who was secretary of the first. At the age of eleven he started at Edison Telephone Company and through him University College School in Gower Street in Fleming was offered the post of assistant the West End. It is said that he was keen to be consultant or scientific adviser with Dr an engineer at a very early age and had his Hopkinson for the Edison Electric Light own workshop where he made model boats company advising on DC systems and also and engines. His schooling enabled him to Ferranti’s AC systems. One of his major tasks enrol at University College, London (UCL) was representing Edison in the combine set up and obtained a BSc at the age of 20. -
Development of Telecommunication
DEVELOPMENT OF TELECOMMUNICATION YEAR/PERIOD EVENT PERSON/ SCIENTIST PLACE 1791 Obtained permission The Chappe Brothers France to set up a signaling system so they could send messages to each other 1791-1872 the creator of a single Samuel Finley Breese United States of wire telegraph system, Morse was America 1816-1892 Siemens invented a Ernst Werner von Germany telegraph that used a Siemens needle to point to the right letter 1858 begins to sell electric Burglar Alarm - Edwin Boston U.S.A burglar alarms T. Holmes 1867 communications are Cyrus Field established with the successful laying of the first telegraph cable 1870 invents multiplex Thomas Edison U.S.A telegraphy. 1875 First word transmitted by telephonr March 1876 Invented the Alexander Graham Boston, Massachusetts Telephone bell 1881 The conversation U.S.A under ground cable 34 miles. 1884 Patent for T.V using Paul Nipkow Germany selenium cell and a mechanical scanning disk 1884 Conversation by Hard-Down Copper From Boston / New overhead line York 1887 electromagnetic Heinrich Hertz Germany waves exist 1888 Produced radio waves Heinrich Hertz Germany 1891 Invention of 1,000 line switch with disc bank having ten concentric rows of line contacts. “Telephone Exchance” 1893 An early form of broadcasting was started 1894 Invention of gear- Laporte, Indiana U.S.S driven switch with "zither" (piano wire) line banks. 1895 The radio was Guglielmo Marconi Italy invented 1896 Patents wireless Guglielmo Marconi Italy photographs 1900 installs loading coils Michael Pupin 1901 First use of “slip multiple.” 1904 nvents the two- John Ambrose Fleming U.S.A element "Fleming Valve". -
Battery Life and How to Improve It
Battery Life and How To Improve It Battery and Energy Technologies Technologies Battery Life (and Death) Low Power Cells High Power Cells For product designers, an understanding of the factors affecting battery life is vitally important for managing both product Chargers & Charging performance and warranty liabilities particularly with high cost, high power batteries. Offer too low a warranty period and you won't Battery Management sell any batteries/products. Overestimate the battery lifetime and you could lose a fortune. Battery Testing Cell Chemistries FAQ That batteries have a finite life is due to occurrence of the unwanted chemical or physical changes to, or the loss of, the active materials of which Free Report they are made. Otherwise they would last indefinitely. These changes are usually irreversible and they affect the electrical performance of the cell. Buying Batteries in China Battery life can usually only be extended by preventing or reducing the cause of the unwanted parasitic chemical effects which occur in the cells. Choosing a Battery Some ways of improving battery life and hence reliability are considered below. How to Specify Batteries Battery cycle life is defined as the number of complete charge - discharge cycles a battery can perform before its nominal capacity falls below Sponsors 80% of its initial rated capacity. Lifetimes of 500 to 1200 cycles are typical. The actual ageing process results in a gradual reduction in capacity over time. When a cell reaches its specified lifetime it does not stop working suddenly. The ageing process continues at the same rate as before so that a cell whose capacity had fallen to 80% after 1000 cycles will probably continue working to perhaps 2000 cycles when its effective capacity will have fallen to 60% of its original capacity. -
The Genesis of the Thermionic Valve
1 THE GENESIS OF THE THERMIONIC VALVE A lecture given to the Institution of Electrical Engineers in 1954 on the fiftieth anniversary of the invention of the thermionic valve. By Professor G. W. O. HOWE, D.Sc., LL.D., Member Prof. Howe is Emeritus Professor of Electrical Engineering, University of Glasgow. Lecture delivered before The Institution 16th November, 1954 I FEEL honoured in being invited to give the opening lecture at this celebration of the jubilee of the invention of the thermionic valve. I feel that I cannot begin the lecture in a more appropriate manner than by trying to give you a picture of the inventor himself, for I realize that to many of the younger members of The Institution he is little more than a name. John Ambrose Fleming was born at Lancaster in 1849, but when he was five years old the family moved to North London. His father, a clergyman and a doctor of divinity, was born at Kelso, in Scotland, of an old Scottish family of Flemish origin, as the name shows. At the age of 14 young John was sent to University College School , a day school conducted at that time in a wing of University College in Gower Street, where he was later to be Professor of Electrical Engineering. Although his interests were mainly in machinery and scientific matters, he had to work hard at Latin and Greek in order to pass the London Matriculation examination, which he did when he was 16. He was then entered as a science student at the College. -
Final Tech Section 1-16
Views, Comments, Opinions 1904 – 2004 : 100 years (and more) of electronics by Dirk J Vermeulen, vice-chairman, SAIEE Historical Section Electronics is generally considered to have started with the application of the valve (vacuum tube in America). The first valve was the thermionic diode and this began to find practical use in 1904. This year has thus been widely associated with the beginning of electronics. Much relevant fundamental work had been engineer of the British Post Office, was the known devices but found that they were done before 1904. In particular in 1895 present and persuaded Edison to part with only suitable for low frequencies. JJ Thompson discovered the electron that is several of these modified lamps so that he In October 1904 he recalled that rectification the whole basis for the subject - but none of could demonstrate the phenomenon to the was associated with the Edison Effect and tried this work had yet lead to a practical outcome. Royal Society in England. one of his modified lamps. It worked and he The origins of the diode can be found in work John Ambrose Fleming, consultant to the developed a series of diodes, seeking a done on the electric lamp by Edison in 1883. Edison Electric Light Company of London, had configuration suitable for wireless telegraphy. The glass envelope of early lamps suffered visited Edison in 1884 and was probably In November 1904 Fleming applied for a from progressive blackening which obscured shown the Edison Effect. Fleming may also patent on his “oscillation valve”, as he named the light to such an extent that lamps were have been present when Preece presented it, and ceded the rights to the Marconi often discarded before the filament failed. -
Guglielmo MARCONI (25 April 1874-20 July 1937)
1 Guglielmo MARCONI (25 April 1874-20 July 1937) PART 1: HIS LIFE AND COMPANY Introduction Wireless telegraphy was the outcome of a chain of effort formed by the mathematician, the laboratory experimenter, the inventor, and the capitalist. For instance: in 1864, James Clerk Maxwell (1831-1879) working on purely theoretical lines, reached the conclusion that an electric spark or disruptive discharge," would set up oscillations in the ether”. In 1887, Heinrich Hertz (1857-1894) proved by experiments that Clerk Maxwell's theory was correct. He demonstrated that an electric spark “brings about the radiation of etheric waves” which may be reflected, refracted, and polarised like those of light. In 1895, Guglielmo Marconi began his attempts to utilise these waves for signalling purposes. In 1896, he took out the first of the patents which were later acquired by Marconi's Wireless Telegraph Company, and utilised in the development of a world-wide system of wireless telegraphy by land and sea. 1. THE EARLY YEARS (a),[3] 1.1. Guglielmo Marconi’s youth On April 25, 1874, an event occurred which would change the world forever: on that day Guglielmo Marconi was born in Bologna, Italy. His first influences proved unusual: His father, Giuseppe, was an able, dignified Catholic Italian businessman. His mother, Annie a Protestant Irish girl of Daphne Castle, County Wexford, was descended from a family of well-known Jameson whiskey distillers in Dublin. Their first child, Alfonso, had been born nine years before Guglielmo. Neat, tidy, studious and obedient, he was nearly the opposite of his younger brother. -
Leeds Thesis Template
View metadata, citation and similar papers at core.ac.uk brought to you by CORE provided by White Rose E-theses Online Beyond Marconi: the roles of the Admiralty, the Post Office, and the Institution of Electrical Engineers in the invention and development of wireless communication up to 1908. Elizabeth Mary Bruton Submitted in accordance with the requirements for the degree of PhD. The University of Leeds School of Philosophy, Religion, and History of Science December 2012 The candidate confirms that the work submitted is her own and that appropriate credit has been given where reference has been made to the work of others. This copy has been supplied on the understanding that it is copyright material and that no quotation from the thesis may be published without proper acknowledgement. © 2012 The University of Leeds and Elizabeth Mary Bruton The right of Elizabeth Mary Bruton to be identified as Author of this work has been asserted by her in accordance with the Copyright, Designs and Patents Act 1988. ii Acknowledgements First and foremost, I would like to express my sincere thanks and gratitude to my supervisors, Professor Graeme Gooday and Dr Stephen Lax, for their assistance with the production of this PhD. Their support, encouragement, and feedback have been invaluable during the production of this thesis and have been very much appreciated. In particular, Professor Gooday has been more than generous with his time, expertise, and academic connections, for which I am especially grateful and thankful. Thanks are also due to my two examiners – Dr Jonathan Topham and Dr Ben Marsden – for their constructive and helpful comments on my thesis. -
Revolutionary of Radio W
COMMENT BOOKS & ARTS TECHNOLOGY Revolutionary of radio W. Bernard Carlson hails a life of driven communications pioneer Guglielmo Marconi. s inventor of the wireless telegraph, head Italy’s national research council; later, Guglielmo Marconi was a central fig- he became president of the new academy of ure in the development of twentieth- science. Using records recently discovered in Acentury communications. Yet how should we the government archives in Rome, Raboy pro- view him? As Nobel laureate? Entrepreneur? vides a detailed account of Marconi’s involve- Fascist? In his grand, wide-ranging biogra- ment in Fascism, including his tacit approval phy Marconi, Marc Raboy reveals a complex of excluding Jewish scientists from the acad- individual who played all these parts. By emy. In the 1930s, Marconi conducted radio examining them, Raboy seeks to show how experiments from his yacht, Elettra, and built radio came to be intertwined with big busi- a powerful radio station for the Vatican. He AGENCY/GETTY GENERAL PHOTOGRAPHIC ness, imperialism and global politics in ways died in 1937, and various companies contin- that still define electronic communications. ued to use his name until Marconi plc was Marconi was born to privilege in 1874: his purchased by Ericsson in 2006. father was an Italian aristocrat, his mother Raboy superbly traces every twist and turn a member of the Jameson Irish-whiskey of Marconi’s life, showing us his influences, dynasty. Educated in England and Italy, Mar- business strategies and shrewd management coni decided at age 20 to study the electro- of his own public persona. Raboy skilfully magnetic waves predicted by James Clerk locates his activities in the context of commu- Maxwell in the 1860s and verified experi- nications policy, the arms race between Brit- mentally by German physicist Heinrich Hertz ain and Germany, and popular culture.