Evolved Expendable Launch Vehicle Program
Total Page:16
File Type:pdf, Size:1020Kb
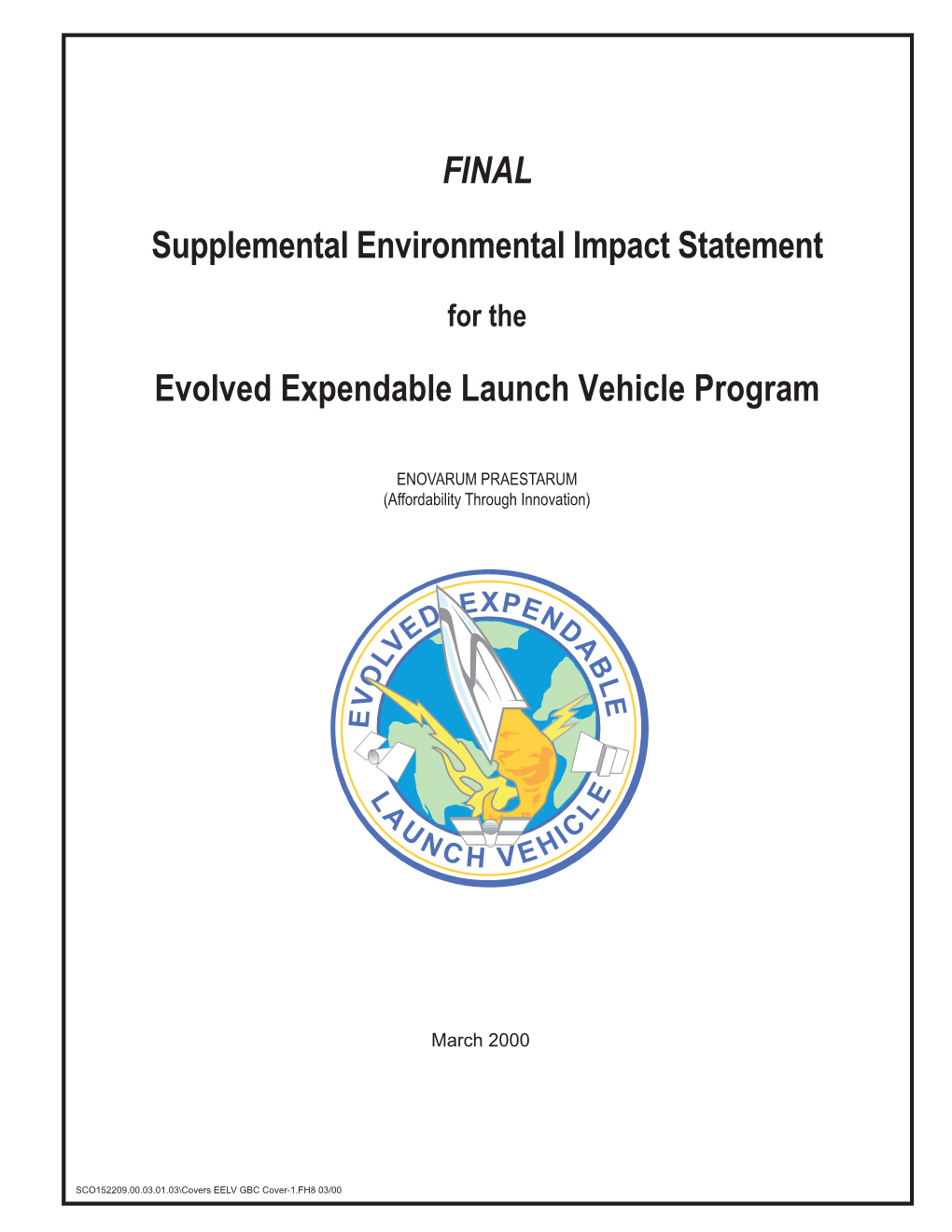
Load more
Recommended publications
-
NASA Manned Launch Vehicle Lightning Protection Development
https://ntrs.nasa.gov/search.jsp?R=20090037586 2019-08-30T08:05:42+00:00Z View metadata, citation and similar papers at core.ac.uk brought to you by CORE provided by NASA Technical Reports Server NASA Manned Launch Vehicle Lightning Protection Development Matthew B. McCollum NASA Marshall Space Flight Center, Huntsville, Alabama, USA Steven R. Jones NASA Marshall Space Flight Center, Huntsville, Alabama, USA Jonathan D. Mack NASA Marshall Space Flight Center, Huntsville, Alabama, USA ABSTRACT understanding of the lightning environment has highlighted the vulnerability of the protection Historically, the National Aeronautics and Space schemes and associated risk to the vehicle, which Administration (NASA) relied heavily on lightning has resulted in lost launch opportunities and avoidance to protect launch vehicles and crew from increased expenditures in manpower to assess lightning effects. As NASA transitions from the Space Shuttle vehicle health and safety after Space Shuttle to the new Constellation family of lightning events at the launch pad. launch vehicles and spacecraft, NASA engineers are imposing design and construction standards on the Because of high-percentage launch availability and spacecraft and launch vehicles to withstand both the long-term on-pad requirements, LCC constraints are direct and indirect effects of lightning. no longer considered feasible.[5] The Constellation vehicles must be designed to withstand direct and A review of current Space Shuttle lightning indirect effects of lightning. A review of the vehicle constraints and protection methodology will be design and potential concerns will be presented as presented, as well as a historical review of Space well as the new catenary lightning protection system Shuttle lightning requirements and design. -
General Assembly Distr.: General 29 January 2001
United Nations A/AC.105/751/Add.1 General Assembly Distr.: General 29 January 2001 Original: English Committee on the Peaceful Uses of Outer Space National research on space debris, safety of space objects with nuclear power sources on board and problems of their collisions with space debris Note by the Secretariat* Addendum Contents Chapter Paragraphs Page I. Introduction........................................................... 1-2 2 Replies received from Member States and international organizations .................... 2 United States of America ......................................................... 2 European Space Agency.......................................................... 7 __________________ * The present document contains replies received from Member States and international organizations between 25 November 2000 and 25 January 2001. V.01-80520 (E) 020201 050201 A/AC.105/751/Add.1 I. Introduction 1. At its forty-third session, the Committee on the Peaceful Uses of Outer Space agreed that Member States should continue to be invited to report to the Secretary- General on a regular basis with regard to national and international research concerning the safety of space objects with nuclear power sources, that further studies should be conducted on the issue of collision of orbiting space objects with nuclear power sources on board with space debris and that the Committee’s Scientific and Technical Subcommittee should be kept informed of the results of such studies.1 The Committee also took note of the agreement of the Subcommittee that national research on space debris should continue and that Member States and international organizations should make available to all interested parties the results of that research, including information on practices adopted that had proved effective in minimizing the creation of space debris (A/AC.105/736, para. -
Launch and Deployment Analysis for a Small, MEO, Technology Demonstration Satellite
46th AIAA Aerospace Sciences Meeting and Exhibit AIAA 2008-1131 7 – 10 January 20006, Reno, Nevada Launch and Deployment Analysis for a Small, MEO, Technology Demonstration Satellite Stephen A. Whitmore* and Tyson K. Smith† Utah State University, Logan, UT, 84322-4130 A trade study investigating the economics, mass budget, and concept of operations for delivery of a small technology-demonstration satellite to a medium-altitude earth orbit is presented. The mission requires payload deployment at a 19,000 km orbit altitude and an inclination of 55o. Because the payload is a technology demonstrator and not part of an operational mission, launch and deployment costs are a paramount consideration. The payload includes classified technologies; consequently a USA licensed launch system is mandated. A preliminary trade analysis is performed where all available options for FAA-licensed US launch systems are considered. The preliminary trade study selects the Orbital Sciences Minotaur V launch vehicle, derived from the decommissioned Peacekeeper missile system, as the most favorable option for payload delivery. To meet mission objectives the Minotaur V configuration is modified, replacing the baseline 5th stage ATK-37FM motor with the significantly smaller ATK Star 27. The proposed design change enables payload delivery to the required orbit without using a 6th stage kick motor. End-to-end mass budgets are calculated, and a concept of operations is presented. Monte-Carlo simulations are used to characterize the expected accuracy of the final orbit. -
New Pad Constructed for Smaller Rocket Launches
PROGRAM HIGHLIGHTS • JULY 2015 At NASA’s Kennedy Space Center in Florida, the Ground Systems Development and Operations (GSDO) Program Office is leading the center’s transfor- mation from a historically government-only launch complex to a spaceport bustling with activity involving government and commercial vehicles alike. GSDO is tasked with developing and using the complex equipment required to safely handle a variety of rockets and spacecraft during assembly, transport and launch. For more information about GSDO accomplishments happening around the center, visit http://go.nasa.gov/groundsystems. New Pad Constructed for Smaller Rocket Launches NASA's Kennedy Space Center in Florida took another step forward in its transformation to a 21st century multi-user spaceport with the completion of the new Small Class Vehicle Launch Pad, designated 39C, in the Launch Pad 39B area. This designated pad to test smaller rockets will make it more affordable for smaller aerospace companies to develop and launch from the center, and to break into the commercial spaceflight market. Kennedy Director Bob Cabana and representatives from the Ground Systems Development and Operations (GSDO) Program and the Center Planning and Development (CPD) and Engineering Directorates marked the completion of the new pad during a ribbon-cutting ceremony July 17. NASA Kennedy Space Center Director Bob Cabana, center, helps cut the ribbon on the new Small Class Vehicle Launch Pad, designated 39C, at Kennedy Space Center in Florida. Also helping to cut the ribbon are, from left, Pat Simpkins, director, Engineering and Technology Directorate; Rich Koller, senior vice president of design firm Jones Edmunds; Scott Col- loredo, director, Center Planning and Development; and Michelle Shoultz, president of Frazier Engineering. -
Proposal to Construct and Operate a Satellite Launching Facility on Christmas Island
Environment Assessment Report PROPOSAL TO CONSTRUCT AND OPERATE A SATELLITE LAUNCHING FACILITY ON CHRISTMAS ISLAND Environment Assessment Branch 2 May 2000 Christmas Island Satellite Launch Facility Proposal Environment Assessment Report - Environment Assessment Branch – May 2000 3 Table of Contents 1 INTRODUCTION..............................................................................................6 1.1 GENERAL ...........................................................................................................6 1.2 ENVIRONMENT ASSESSMENT............................................................................7 1.3 THE ASSESSMENT PROCESS ...............................................................................7 1.4 MAJOR ISSUES RAISED DURING THE PUBLIC COMMENT PERIOD ON THE DRAFT EIS .................................................................................................................9 1.4.1 Socio-economic......................................................................................10 1.4.2 Biodiversity............................................................................................10 1.4.3 Roads and infrastructure .....................................................................11 1.4.4 Other.......................................................................................................12 2 NEED FOR THE PROJECT AND KEY ALTERNATIVES ......................14 2.1 NEED FOR THE PROJECT ..................................................................................14 2.2 KEY -
This Boeing Team's Skills at Producing Delta IV Rocket Fairings Helped
t’s usually the tail end of the rocket that gets all the early atten- other work. But they’d jump at the chance to work together again. tion, providing an impressive fiery display as the spacecraft is Their story is one of challenges and solutions. And they attribute hurled into orbit. But mission success also depends on what’s their success to Lean+ practices and good old-fashioned teamwork. Ion top of the rocket: a piece of metal called the payload fairing “The team took it upon themselves to make an excellent that protects the rocket’s cargo during the sometimes brutal ride product,” said program manager Thomas Fung. “We had parts to orbital speed. issues and tool problems, but the guys really stepped up and took “There’s no room for error,” said Tracy Allen, Boeing’s manu- pride and worked through the issues.” facturing production manager for a Huntington Beach, Calif., team The aluminum fairing team went through a major transition that made fairings for the Delta IV. The fairing not only protects the when Boeing merged its Delta Program with Lockheed Martin’s payload from launch to orbit but also must jettison properly for Atlas Program to form United Launch Alliance in 2006. deployment of the satellite or spacecraft. “There were a lot of process changes in the transition phase Allen and his colleagues built the 65-foot-long (20-meter-long) because we were working with a new company,” Fung said. “We aluminum isogrid fairings for the Delta IV heavy-lift launch vehicle. had part shortages because of vendor issues, and that caused The design was based on 41 similar fairings Boeing made for the an impact to the schedule. -
Commercial Space Transportation Developments and Concepts: Vehicles, Technologies and Spaceports
Commercial Space Transportation 2006 Commercial Space Transportation Developments and Concepts: Vehicles, Technologies and Spaceports January 2006 HQ003606.INDD 2006 U.S. Commercial Space Transportation Developments and Concepts About FAA/AST About the Office of Commercial Space Transportation The Federal Aviation Administration’s Office of Commercial Space Transportation (FAA/AST) licenses and regulates U.S. commercial space launch and reentry activity, as well as the operation of non-federal launch and reentry sites, as authorized by Executive Order 12465 and Title 49 United States Code, Subtitle IX, Chapter 701 (formerly the Commercial Space Launch Act). FAA/AST’s mission is to ensure public health and safety and the safety of property while protecting the national security and foreign policy interests of the United States during commercial launch and reentry operations. In addition, FAA/AST is directed to encour- age, facilitate, and promote commercial space launches and reentries. Additional information concerning commercial space transportation can be found on FAA/AST’s web site at http://ast.faa.gov. Federal Aviation Administration Office of Commercial Space Transportation i About FAA/AST 2006 U.S. Commercial Space Transportation Developments and Concepts NOTICE Use of trade names or names of manufacturers in this document does not constitute an official endorsement of such products or manufacturers, either expressed or implied, by the Federal Aviation Administration. ii Federal Aviation Administration Office of Commercial Space Transportation 2006 U.S. Commercial Space Transportation Developments and Concepts Contents Table of Contents Introduction . .1 Significant 2005 Events . .4 Space Competitions . .6 Expendable Launch Vehicles . .9 Current Expendable Launch Vehicle Systems . .9 Atlas 5 - Lockheed Martin Corporation . -
L AUNCH SYSTEMS Databk7 Collected.Book Page 18 Monday, September 14, 2009 2:53 PM Databk7 Collected.Book Page 19 Monday, September 14, 2009 2:53 PM
databk7_collected.book Page 17 Monday, September 14, 2009 2:53 PM CHAPTER TWO L AUNCH SYSTEMS databk7_collected.book Page 18 Monday, September 14, 2009 2:53 PM databk7_collected.book Page 19 Monday, September 14, 2009 2:53 PM CHAPTER TWO L AUNCH SYSTEMS Introduction Launch systems provide access to space, necessary for the majority of NASA’s activities. During the decade from 1989–1998, NASA used two types of launch systems, one consisting of several families of expendable launch vehicles (ELV) and the second consisting of the world’s only partially reusable launch system—the Space Shuttle. A significant challenge NASA faced during the decade was the development of technologies needed to design and implement a new reusable launch system that would prove less expensive than the Shuttle. Although some attempts seemed promising, none succeeded. This chapter addresses most subjects relating to access to space and space transportation. It discusses and describes ELVs, the Space Shuttle in its launch vehicle function, and NASA’s attempts to develop new launch systems. Tables relating to each launch vehicle’s characteristics are included. The other functions of the Space Shuttle—as a scientific laboratory, staging area for repair missions, and a prime element of the Space Station program—are discussed in the next chapter, Human Spaceflight. This chapter also provides a brief review of launch systems in the past decade, an overview of policy relating to launch systems, a summary of the management of NASA’s launch systems programs, and tables of funding data. The Last Decade Reviewed (1979–1988) From 1979 through 1988, NASA used families of ELVs that had seen service during the previous decade. -
Learning from Other People's Mistakes
Learning from Other People’s Mistakes Most satellite mishaps stem from engineering mistakes. To prevent the same errors from being repeated, Aerospace has compiled lessons that the space community should heed. Paul Cheng and Patrick Smith he computer onboard the Clementine spacecraft froze immediately after a thruster was commanded to fire. A “watchdog” algorithm designed to stop “It’s always the simple stuff the thrusters from excessive firing could not execute, and CTlementine’s fuel ran out. !e mission was lost. Based on that kills you…. With all the this incident, engineers working on the Near Earth Asteroid Rendezvous (NEAR) program learned a key lesson: the testing systems, everything watchdog function should be hard-wired in case of a com- puter shutdown. As it happened, NEAR suffered a similar computer crash during which its thrusters fired thousands looked good.” of times, but each firing was instantly cut off by the still- —James Cantrell, main engineer operative watchdog timer. NEAR survived. As this example illustrates, insights from past anoma- for the joint U.S.-Russian Skipper lies are of considerable value to design engineers and other mission, which failed because program stakeholders. Information from failures (and near its solar panels were connected failures) can influence important design decisions and pre- vent the same mistakes from being made over and over. backward (Associated Press, 1996) Contrary to popular belief, satellites seldom fail because of poor workmanship or defective parts. Instead, most failures are caused by simple engineering errors, such as an over- looked requirement, a unit mix-up, or even a typo in a docu- ment. -
Materials for Liquid Propulsion Systems
https://ntrs.nasa.gov/search.jsp?R=20160008869 2019-08-29T17:47:59+00:00Z CHAPTER 12 Materials for Liquid Propulsion Systems John A. Halchak Consultant, Los Angeles, California James L. Cannon NASA Marshall Space Flight Center, Huntsville, Alabama Corey Brown Aerojet-Rocketdyne, West Palm Beach, Florida 12.1 Introduction Earth to orbit launch vehicles are propelled by rocket engines and motors, both liquid and solid. This chapter will discuss liquid engines. The heart of a launch vehicle is its engine. The remainder of the vehicle (with the notable exceptions of the payload and guidance system) is an aero structure to support the propellant tanks which provide the fuel and oxidizer to feed the engine or engines. The basic principle behind a rocket engine is straightforward. The engine is a means to convert potential thermochemical energy of one or more propellants into exhaust jet kinetic energy. Fuel and oxidizer are burned in a combustion chamber where they create hot gases under high pressure. These hot gases are allowed to expand through a nozzle. The molecules of hot gas are first constricted by the throat of the nozzle (de-Laval nozzle) which forces them to accelerate; then as the nozzle flares outwards, they expand and further accelerate. It is the mass of the combustion gases times their velocity, reacting against the walls of the combustion chamber and nozzle, which produce thrust according to Newton’s third law: for every action there is an equal and opposite reaction. [1] Solid rocket motors are cheaper to manufacture and offer good values for their cost. -
Atlas V Cutaway Poster
ATLAS V Since 2002, Atlas V rockets have delivered vital national security, science and exploration, and commercial missions for customers across the globe including the U.S. Air Force, the National Reconnaissance Oice and NASA. 225 ft The spacecraft is encapsulated in either a 5-m (17.8-ft) or a 4-m (13.8-ft) diameter payload fairing (PLF). The 4-m-diameter PLF is a bisector (two-piece shell) fairing consisting of aluminum skin/stringer construction with vertical split-line longerons. The Atlas V 400 series oers three payload fairing options: the large (LPF, shown at left), the extended (EPF) and the extra extended (XPF). The 5-m PLF is a sandwich composite structure made with a vented aluminum-honeycomb core and graphite-epoxy face sheets. The bisector (two-piece shell) PLF encapsulates both the Centaur upper stage and the spacecraft, which separates using a debris-free pyrotechnic actuating 200 ft system. Payload clearance and vehicle structural stability are enhanced by the all-aluminum forward load reactor (FLR), which centers the PLF around the Centaur upper stage and shares payload shear loading. The Atlas V 500 series oers 1 three payload fairing options: the short (shown at left), medium 18 and long. 1 1 The Centaur upper stage is 3.1 m (10 ft) in diameter and 12.7 m (41.6 ft) long. Its propellant tanks are constructed of pressure-stabilized, corrosion-resistant stainless steel. Centaur is a liquid hydrogen/liquid oxygen-fueled vehicle. It uses a single RL10 engine producing 99.2 kN (22,300 lbf) of thrust. -
Phase Change: Titan’S Disappearing Lakes
Phase Change: Titan’s Disappearing Lakes Investigation Notebook NYC Edition © 2018 by The Regents of the University of California. All rights reserved. No part of this publication may be reproduced or transmitted in any form or by any means, electronic or mechanical, including photocopy, recording, or any information storage or retrieval system, without permission in writing from the publisher. Teachers purchasing this Investigation Notebook as part of a kit may reproduce the book herein in sufficient quantities for classroom use only and not for resale. These materials are based upon work partially supported by the National Science Foundation under grant numbers DRL-1119584, DRL-1417939, ESI-0242733, ESI-0628272, and ESI-0822119. The Federal Government has certain rights in this material. Any opinions, findings, and conclusions or recommendations expressed in this material are those of the author(s) and do not necessarily reflect the views of the National Science Foundation. These materials are based upon work partially supported by the Institute of Education Sciences, U.S. Department of Education, through Grant R305A130610 to The Regents of the University of California. The opinions expressed are those of the authors and do not represent views of the Institute or the U.S. Department of Education. Developed by the Learning Design Group at the University of California, Berkeley’s Lawrence Hall of Science. Amplify. 55 Washington Street, Suite 800 Brooklyn, NY 11201 1-800-823-1969 www.amplify.com Phase Change: Titan’s Disappearing Lakes