Ngong Ping 360 Ropeway
Total Page:16
File Type:pdf, Size:1020Kb
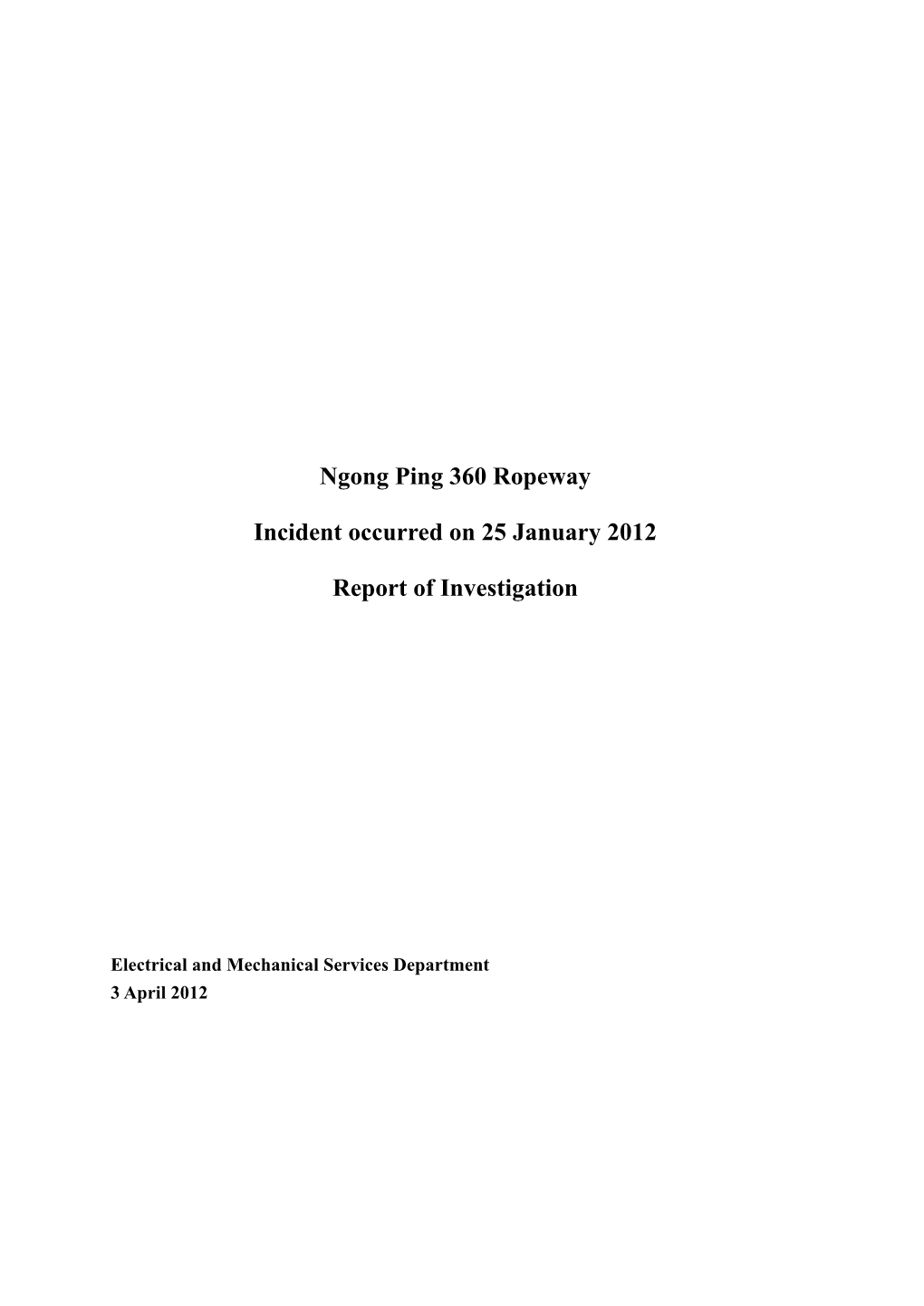
Load more
Recommended publications
-
Tung Chung - Ngong Ping Cable Car Project
Tung Chung - Ngong Ping Cable Car Project PROJECT PROFILE 1. BASIC INFORMATION 1.1 Project Title Tung Chung - Ngong Ping Cable Car Project. 1.2 Purpose and Nature of Project The project comprises the construction and operation of a cable car system between Tung Chung Town Centre and Ngong Ping on Lantau Island. The development of the cable car system aims to further develop Ngong Ping as a major tourist attraction in Hong Kong. 1.3 Name of Project Proponent Hong Kong Island & Islands Development Office, Territory Development Department (TDD). 1.4 Location and Scale of Project A Preliminary Preferred Alignment (PPA) for the cable car system has been identified based on the findings of the feasibility study completed by the Mass Transit Railway Corporation and a subsequent desk top study conducted by TDD. The location of this project is shown on Drawing No. HKI-Z180. On the basis of the PPA, the scope of the project will include the following: (a) construction of a cable car system of about 5.7 km long between Tung Chung Town Centre and Ngong Ping on Lantau Island; (b) construction of associated pylons and other supporting structures, and ancillary works; (c) construction of two terminals, one at Tung Chung Town Centre and the other at Ngong Ping; and - 2 - (d) construction of an intermediate station on the Airport Island and a turning station in the Lantau North Country Park. 1.5 The Subject Site and its Surrounding Environments 1.5.1Based on the PPA, the proposed cable car route between Tung Chung Terminal and the Intermediate Station will run along the northern side of the Chek Lap Kok South Road Bridge. -
Report of the Bills Committee on Tung Chung Cable Car Bill To
立法會 Legislative Council LC Paper No. CB(1)1719/02-03 Ref: CB1/BC/4/02 Report of the Bills Committee on Tung Chung Cable Car Bill Purpose 1 This paper reports on the deliberations of the Bills Committee on Tung Chung Cable Car Bill (the Bill). Background 2. In 1998, the Financial Secretary announced Government's decision to proceed with the construction of a cable car project (the Project) linking Tung Chung and Ngong Ping on Lantau Island as a tourist attraction. The Government subsequently tasked the Mass Transit Railway Corporation (MTRC) (now known as MTR Corporation Limited (MTRCL)) to undertake a feasibility study on the development of the proposal. 3. The MTRC Study concluded that the Project was feasible in both technical and financial terms and would bring about socio-economic benefits to Hong Kong, including additional tourist visits to attractions on Lantau Island, serving as another tourist attraction to enhance visitors' experience in Hong Kong, etc. The Government invited in February 2000 expressions of interest and preliminary proposals on the basis of the alignment as recommended in the MTRC Study. 4. In April 2001, the Executive Council approved the framework for implementing the Project, and on this basis, the Government issued a Project Brief to invite detailed proposals for the finance, design, construction, operation and maintenance of the cable car system. The Government received three proposals upon close of submission in July 2001. The Government short-listed two proponents, including MTRCL, for further negotiations in January 2002. 5. In June 2002, the Executive Council approved the selection of MTRCL as the successful proponent to take forward the Project. -
List of Projects Used in HKIA/ARB Professional Assessment 2007 - 2013
List of projects used in HKIA/ARB Professional Assessment 2007 - 2013 Date of Occupation No Year Name of Company Project Title Address Lot No BD File Ref. Permit / Practical Special Topic Completion (month/year) 1 2007 Aedas Ltd Satellite Earth Station Dai Hei Street at Tai Po Industrial Estate Section G Tai Po Town Lot BD 2/9141/01 (P) Jan 04 IL7076, IL7077, IL971, IL970 Proposed Hotel Development at 31E - 39 Wyndham 31E, 31F, 33-39 Wyndham Street, 2 2007 AGC Design Ltd SARP, IL970RP, BD3/2058/94 PT IV Jul 04 Street, Central Central, Hong Kong IL970SBSS1 RP Extension to the Church of Jesus Christ of Latter Day Tseung Kwan O Lot 45, Area II, Po Lam 3 2007 Aedas Ltd Tseung Kwan O Lot 45 BD 9106/04 31 Oct 2006 Saints at Tseung Kwan O Lane 4 2007 P & T Architects & Engineers Ltd Residential Development At 2 Lok Kwai Path Shatin, 2 Lok Kwai Path, Shatin, N.T. STTL 526 BD 9067/02 Jan 06 / May 06 5 2007 Leung King Partners Ltd Villa Rosa Residents 82 Peak Road, Hong Kong RBL 742 BD 2014/98 Aug 00 6 2007 Dennis Lau & Ng Chun Man Architects & Engineers (HK) Ltd Tuen Mun Area 4C, TMTL 384 King Fung Path, Tuen Mun, N.T. Lot No. 384, Area 4C BD 6/9260/97H (P) Aug 02 Service Apartment Building at Nos. 116-122, Yeung Uk 116-122 Yeung Uk Road, Tsuen Wan, 7 2007 MLA Architects (HK) Ltd TWTL 407 9325/93 28 Aug 06 Road (H-Cube) N.T. -
Tung Chung Cable Car Project Supporting Tower Proposal
Tung Chung Cable Car Project Supporting Tower Proposal MTR Corporation Limited Tung Chung Cable Car Project Supporting Tower Proposal (Revision 7) June 2006 Tung Chung Cable Car Project Supporting Tower Proposal 1 Introduction This Proposal gives a description on the immediate towers which will be provided as part of the cable car system. 2 Tower Locations and Design Total eight immediate towers will be constructed: five towers (Towers 3 to 7) will be located within the Lantau North Country Park and the Proposed Lantau North (Extension) Country Park, two will be on Airport Island (Towers 2A and 2B) and one (Tower 1) at Tung Chung. Location of the towers is shown in Figure 1.1 below. Tower 7 Tower 6 Tower 5 Tower 4 Tower 3 Tower 2B Tower 2A Tower 1 1 Tung Chung Cable Car Project Supporting Tower Proposal The towers will be in lattice form which is preferred from a constructability and engineering perspective. Tower heights range from 18m to 51m. Dimensions of base area of the towers within the country park are given in Table 2.1 below. Please refer to Appendix A for the current design drawings. The steel structure of the towers will have a hot-dipped galvanized coating. Its appearance is similar to the existing CLP’s overhead line towers. Please refer to Appendix B for the photos taken on site showing the appearance and colour of the towers. In general, chain link fence and gate (with padlock) will be provided at the tower base to ensure the security of the towers during operational stage. -
For Discussion on 24 April 2006 Legislative Council Panel On
LC Paper No. CB(1)1303/05-06(05) For discussion on 24 April 2006 Legislative Council Panel on Economic Services Progress of the Ngong Ping 360 Project Purpose This paper briefs Members on the progress of the Ngong Ping 360 Project (formerly known as the Tung Chung Cable Car Project). Background 2. In November 2003, the Government entered into a Project Agreement with the Mass Transit Railway Corporation Limited (MTRCL) for a franchise of 30 years based on a Build-Operate-Transfer model to finance, design, construct, operate and maintain the Ngong Ping Skyrail (formerly known as the Tung Chung Cable Car System) linking Tung Chung and Ngong Ping on Lantau. MTRCL estimates that there will be about 1.5 million visitors in the first year of operation of the Ngong Ping Skyrail. 3. The Government also granted MTRCL a 30-year land lease for the development of complementary tourist facilities in the form of a themed village (viz. the Ngong Ping Village) leading from the Ngong Ping Terminal to the core area of Ngong Ping. 4. MTRCL has appointed the Skyrail-ITM (Hong Kong) Limited (Skyrail) to operate and manage the Facility. Skyrail has rich experience in operating similar projects, notably the Rainforest Cableway in Cairns, Australia. Upon completion, the Ngong Ping Skyrail will improve the accessibility of existing tourist attractions at Ngong Ping including the Po Lin Monastery, the Giant Statue of Buddha and the Wisdom Path. This will also encourage more local residents and overseas visitors to visit other attractions in Lantau. The Facility 5. The Ngong Ping 360 Project comprises the Ngong Ping Skyrail and Ngong Ping Village. -
Background Brief on Ngong Ping 360 (Updated Version As at 20 October 2006)
立法會 Legislative Council LC Paper No. CB(1)121/06-07(04) Ref : CB1/PL/ES Panel on Economic Services Meeting on 23 October 2006 Background brief on Ngong Ping 360 (Updated version as at 20 October 2006) Purpose 1. This paper sets out the background to the development of the Tung Chung Cable Car system (“the Cable Car System”), and the themed cultural village and associated attractions and facilities in Ngong Ping (collectively known as “Ngong Ping 360”), the problems encountered during trial runs of the Cable Car System and the initial operation since its official opening on 18 September 2006. The paper also summarizes members’ deliberations over the related issues. Background 2. In 1998, the Financial Secretary announced Government’s decision to proceed with the construction of a cable car project (“the Project”) linking Tung Chung and Ngong Ping on Lantau Island as a tourist attraction. Under the framework approved for implementing the Project, the Government would grant a 30-year franchise for the financing, design, construction, operation and maintenance of the Cable Car System on a Build-Operate-Transfer basis. The Government also provided the land required for the Cable Car System. 3. In July 2002, the Government entered into a Provisional Agreement with the MTR Corporation Limited (“MTRCL”) to allow the latter to commence preparatory work on the Project before the grant of the franchise. Meanwhile, the Government proceeded with the enactment of the enabling legislation for the franchise and worked with MTRCL to prepare a Project Agreement to provide a legal framework for the granting of the franchise and the construction, operation and maintenance of the Cable Car System. -
For 27 February 2012
For 27 February 2012 Legislative Council Panel on Economic Development Breakdown of Ngong Ping 360 Ropeway Occurring in December 2011 and January 2012 Purpose This paper reports to the Panel on the recent incidents involving service suspensions at Ngong Ping 360 (NP360) and the progress since the latest suspension on 25 January 2012. Review of Incidents on 8, 18, and 22 December 2011 2. NP360 suspended its cable car service on 8, 18 and 22 of December 2011 and on 25 January 2012. Subsequent investigations have confirmed that these were isolated incidents that did not affect the safety of the cable car operation. They also proved that both the daily monitoring system and the automatic monitoring system had functioned as designed in ensuring system safety. Nevertheless, NP360 understands the inconvenience the stoppages caused to the guests and would like to apologise to them. Incident on 8 December 2011 3. Cable car service was temporarily suspended at 4:35pm when the automatic monitoring system was triggered, stopping the cable car operation. The maintenance team carried out inspection immediately and conducted the necessary rectification. The team confirmed that there was partial wear on the haul rope sheave lining in the Ngong Ping Terminal which had affected the signal transmission system. Safety of the cable car operation was not affected and cable car service was resumed at 4:51pm to take guests back to the Tung Chung and Ngong Ping terminals. Cable car operation and guest boarding were then suspended and a detailed inspection of the cable car system was carried out after the operation hours. -
Dual Joys of Christmas at Ngong Ping 360 (Hong Kong, 27 November
Immediate Release CA27/2015 Dual Joys of Christmas at Ngong Ping 360 The world’s first Ip Man Experience Hall to debut at Ngong Ping 360 on 27 November with an aim to boost visitation The first local tourist attraction and movie project jointly present the use of AR technology to allow 3D interactions between actors and guests Ngong Ping 360 Managing Director Dr Stella Kwan shares the anticipated growth in number of daily guests during Christmas and visitation status in the peak travel season in Q4 (Hong Kong, 27 November, 2015) The grand opening of the world's first Ip Man Experience Hall has taken place on 27 November. The venue is open to the public from 28 November 2015 to 31 January 2016. The Ip Man Experience Hall is the key project of the cross-sectoral collaboration of Ngong Ping 360 x Ip Man 3, which opens up a new tourist experience, supports local cinema and art, and promotes the Hong Kong spirit. Despite of displaying the various movie sets, exhibiting the mains characters’ costumes and showcasing the rare authentic Wing Chun weapons in the hall, we provide a free Ip Man 3 smartphone app for guests to download. The app uses augmented reality (AR) technology to emulate Ip Man’s world on the smartphone screen which allows the guests to interact with 1:1 life-sized 3D images of the leading characters and they can also watch a “making of” version of the movie#. Ngong Ping 360 will donate 10% of proceeds from the designated package sales related to Ip Man Experience Hall, after deducting operating costs, to The Boys’ and Girls’ Clubs Association of Hong Kong, on behalf of both Ngong Ping 360 and Pegasus Motion Pictures Limited. -
Diversion of the Ngong Ping Stream Provisi
MTR Corporation Limited Tung Chung Cable Car Project & Tung Chung Cable Car Project – Diversion of the Ngong Ping Stream & Provision of Temporary Helipad at Tea Garden, Ngong Ping for Tung Chung Cable Car Project Environmental Monitoring & Audit Manual July 2005 Tung Chung Cable Car Project Environmental Monitoring & Audit Manual List of Contents Page Chapters and Appendices 1 INTRODUCTION 1 1.1 Background 1 1.2 Purpose of the Manual 2 1.3 Site Location 3 1.4 Sensitive Receivers 4 1.5 Environmental Monitoring and Audit Requirements 4 1.6 Environmental Management Organisation 5 1.7 Construction Programme 7 2 AIR QUALITY 8 2.1 Introduction 8 2.2 Air Quality Parameters 8 2.3 Monitoring Equipment 8 2.4 Monitoring Locations 8 2.5 Baseline Monitoring 10 2.6 Impact Monitoring 11 2.7 Event and Action Plan for Air Quality 11 3 NOISE 14 3.1 Introduction 14 3.2 Noise Parameters 14 3.3 Monitoring Equipment 14 3.4 Monitoring Locations 14 3.5 Baseline Monitoring 16 3.6 Impact Monitoring 16 3.7 Event and Action Plan for Noise 16 4 ECOLOGY 19 4.1 Introduction 19 4.2 Ecological Monitoring during Construction Phase 19 4.3 Ecological Monitoring during Operational Phase 20 5 VISUAL AND LANDSCAPE 22 5.1 General 22 5.2 Landscape and Visual Baseline 22 5.3 Construction and Operational Phase Audit 22 i Tung Chung Cable Car Project Environmental Monitoring & Audit Manual 6 WATER QUALITY 24 6.1 Introduction 24 6.2 Water Quality Monitoring during Construction Phase 24 7 WASTE 25 7.1 Introduction 25 7.2 Construction Phase Audit 25 8 SITE ENVIRONMENTAL AUDIT 26 8.1 -
CA04/2014 Ngong Ping 360 Actively Participates in and Promotes The
CA04/2014 Ngong Ping 360 actively participates in and promotes the development of Lantau Island Launches brand new programmes and services to enhance guests’ sensory experience (Hong Kong, 19 February 2014) Ngong Ping 360, one of Hong Kong's must-see attractions on Lantau, is a popular attraction for both tourists and local residents. Ngong Ping 360’s team is not only dedicated to maintaining the reliability of cable car services, but also to upholding the mission of providing visitors with unique travel experiences through new programmes and services, enabling them to embark on an extraordinary sensory journey. Ngong Ping 360 experienced satisfactory visitation in 2013 with over 1.65 million guests: 46% came from Western countries (19%) and Asia (27%), 35% came from China and Macau, and 19% were Hong Kong residents. According to 2013 figures, Italy, China and Macau, and France recorded the highest growth with 91%, 56% and 38% respectively. On the whole, in 2013 an average of 5,100 guests visited Ngong Ping 360 per day, breaking the previous record. Last month, the Hong Kong Government issued the “2014 Policy Address”, which stressed speeding up the development of Lantau Island and announced the establishment of the “Lantau Development Advisory Committee” to study the economic and community development strategies of Lantau Island. Accordingly, in 2014 Ngong Ping 360 will launch a wide range of new programmes and services to position itself as the gateway to Lantau Island West and a leading tourist destination, and to promote the economic and development of Lantau Island. Forming a strategic alliance with Lantau cultural attractions to provide one-stop travel fun Ngong Ping 360 is a founding member of the Hong Kong Association of Amusement Parks and Attractions (HKAAPA) and the Lantau Development Alliance (LaDA), and also chairs the LaDA’s Tourism Committee. -
OFFICIAL RECORD of PROCEEDINGS Wednesday, 10
LEGISLATIVE COUNCIL ─ 10 December 2008 2719 OFFICIAL RECORD OF PROCEEDINGS Wednesday, 10 December 2008 The Council met at Eleven o'clock MEMBERS PRESENT: THE PRESIDENT THE HONOURABLE JASPER TSANG YOK-SING, G.B.S., J.P. THE HONOURABLE ALBERT HO CHUN-YAN IR DR THE HONOURABLE RAYMOND HO CHUNG-TAI, S.B.S., S.B.ST.J., J.P. THE HONOURABLE LEE CHEUK-YAN DR THE HONOURABLE DAVID LI KWOK-PO, G.B.M., G.B.S., J.P. THE HONOURABLE FRED LI WAH-MING, J.P. DR THE HONOURABLE MARGARET NG THE HONOURABLE JAMES TO KUN-SUN THE HONOURABLE CHEUNG MAN-KWONG THE HONOURABLE CHAN KAM-LAM, S.B.S., J.P. THE HONOURABLE MRS SOPHIE LEUNG LAU YAU-FUN, G.B.S., J.P. THE HONOURABLE LEUNG YIU-CHUNG DR THE HONOURABLE PHILIP WONG YU-HONG, G.B.S. 2720 LEGISLATIVE COUNCIL ─ 10 December 2008 THE HONOURABLE WONG YUNG-KAN, S.B.S., J.P. THE HONOURABLE LAU KONG-WAH, J.P. THE HONOURABLE LAU WONG-FAT, G.B.M., G.B.S., J.P. THE HONOURABLE MIRIAM LAU KIN-YEE, G.B.S., J.P. THE HONOURABLE EMILY LAU WAI-HING, J.P. THE HONOURABLE ANDREW CHENG KAR-FOO THE HONOURABLE TIMOTHY FOK TSUN-TING, G.B.S., J.P. THE HONOURABLE TAM YIU-CHUNG, G.B.S., J.P. THE HONOURABLE ABRAHAM SHEK LAI-HIM, S.B.S., J.P. THE HONOURABLE LI FUNG-YING, B.B.S., J.P. THE HONOURABLE TOMMY CHEUNG YU-YAN, S.B.S., J.P. THE HONOURABLE ALBERT CHAN WAI-YIP THE HONOURABLE FREDERICK FUNG KIN-KEE, S.B.S., J.P. -
Railway Operations
Executive MTR CORPORATION LIMITED 09 management’s report Railway Operations SARS posed serious short-term challenges to the railway operations, Metros (CoMET) benchmarking report and won for the fifth time the but the small decline in revenue testifies to the subsequent recovery Customer Service Award in the transportation category organised by and MTR’s effective operations management. Total fare revenues fell “Next Magazine”. by 4% to HK$5,489 million. Service improvements Patronage The largest network enhancement was the completion of four- Patronage fell by up to 25% during the SARS peak but recovered later tracking of the Airport Railway between Lai King and Olympic stations, in the year, helped by traffic on the new Tseung Kwan O Line. as well as the new Nam Cheong Station on the Tung Chung Line (TCL). Four-tracking allows AEL and TCL trains to operate on separate tracks MTR Lines recorded total passenger volume of 770 million, against for 4.5 kilometres and its completion contributed to the successful 777 million in 2002, a 24.3% share of the total franchised public opening of the interchanges with KCRC’s West Rail at Nam Cheong transport market, and a good increase from 2002. This included an and Mei Foo stations. During the year,TCL trains were converted from increased share of cross-harbour traffic to 58.7%. Fare revenues fell 7-car to 8-car formation, resulting in a 14% increase in capacity. slightly to HK$5,064 million from HK$5,167 million. In 2003 we extended inter-modal fare discounts to travellers Airport Express Line (AEL) patronage declined 19% to 6.8 million.