Single-Event Transients in Indium Gallium Arsenide Mosfets for Sub-10
Total Page:16
File Type:pdf, Size:1020Kb
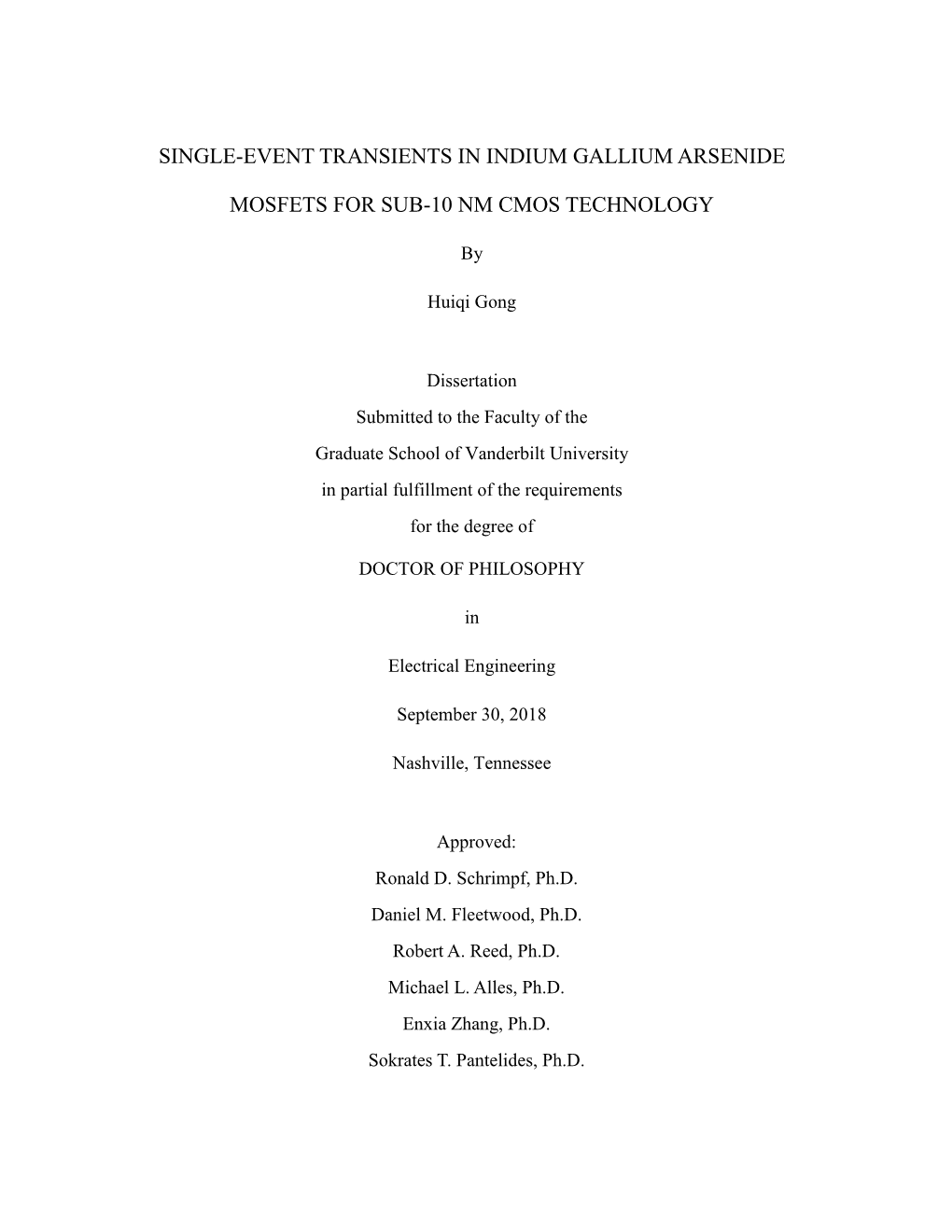
Load more
Recommended publications
-
IEEE Spectrum Gaas
Proof #4 COLOR 8/5/08 @ 5:15 pm BP BEYOND SILICON’S ELEMENTAL LOGICIN THE QUEST FOR SPEED, KEY PARTS OF MICRO- PROCESSORS MAY SOON BE MADE OF GALLIUM ARSENIDE OR OTHER “III-V” SEMICONDUCTORS BY PEIDE D. YE he first general-purpose lithography, billions of them are routinely microprocessor, the Intel 8080, constructed en masse on the surface of a sili- released in 1974, could execute con wafer. about half a million instructions As these transistors got smaller over the T per second. At the time, that years, more could fit on a chip without rais- seemed pretty zippy. ing its overall cost. They also gained the abil- Today the 8080’s most advanced descen- ity to turn on and off at increasingly rapid dant operates 100 000 times as fast. This phe- rates, allowing microprocessors to hum along nomenal progress is a direct result of the semi- at ever-higher speeds. ALL CHRISTIEARTWORK: BRYAN DESIGN conductor industry’s ability to reduce the size But shrinking MOSFETs much beyond their of a microprocessor’s fundamental building current size—a few tens of nanometers—will be blocks—its many metal-oxide-semiconductor a herculean challenge. Indeed, at some point in field-effect transistors (MOSFETs), which act the next several years, it may become impossi- as tiny switches. Through the magic of photo- ble to make them more minuscule, for reasons WWW.SPECTRUM.IEEE.ORG SEPTEMBER 2008 • IEEE SPECTRUM • INT 39 TOMIC-LAYER DEPOSITION provides one means for coating a semiconductor wafer with a high-k aluminum oxide insulator. The Abenefit of this technique is that it offers atomic-scale control of the coating thickness without requiring elaborate equipment. -
Indium Gallium Arsenide Detectors
TELEDYNE JUDSON TECHNOLOGIES A Teledyne Technologies Company Indium Gallium Arsenide Detectors Teledyne Judson Technologies LLC 221 Commerce Drive Montgomeryville, PA 18936 USA Tel: 215-368-6900 Fax: 215-362-6107 Visit us on the web. ISO 9001 Certified www.teledynejudson.com 1/9 J22 and J23 Detector Operating Notes (0.8 to 2.6 µm) TELEDYNE JUDSON TECHNOLOGIES A Teledyne Technologies Company General Accessories The J22 and J23 series are high For a complete system, Teledyne Judson performance InGaAs detectors offers low noise transimpedance amp- operating over the spectral range lifier modules, heat sink/preamp assem- from 0.8µm to 2.6µm. These blies and temperature controllers. For detectors provide fast rise time, further details, please visit our uniformity of response, excellent website. sensitivity, and long term reliability for a wide range of applications. For Call us enhanced performance or temperature stability of response Let our team of application engineers near the cutoff wavelength, Teledyne assist you in selecting the best Judson offers a variety of thermoele detector design for your application. ctrically cooled detector options. Or visit our website for additional Applications information on all of Teledyne Judson’s products. Device Options · Gas analysis · NIR-FTIR Teledyne Judson’s standard InGaAs · Raman spectroscopy detectors, the J22 series, offers high · IR fluorescence reliability and performance in the · Blood analysis spectral range from 0.8 μm to 1.7μm. · Optical sorting In addition, the J23 series extended · Radiometry InGaAs detectors are available in · Chemical detection four cutoff options at 1.9μm, 2.2μm, · Optical communication 2.4μm and 2.6μm. Figure 1 shows the · Optical power monitoring typical response for the J22 and J23 · Laser diode monitoring series at room temperature operation. -
Nanowires Grown on Graphene Have Surprising Structure
Close Nanowires grown on graphene have surprising structure When a team of University of Illinois engineers set out to grow nanowires of a compound semiconductor on top of a sheet of graphene, they did not expect to discover a new paradigm of epitaxy. The self-assembled wires have a core of one composition and an outer layer of another, a desired trait for many advanced electronics applications. Led by professor Xiuling Li, in collaboration with professors Eric Pop and Joseph Lyding, all professors of electrical and computer engineering, the team published its findings in the journal Nano Letters. Nanowires, tiny strings of semiconductor material, have great potential for applications in transistors, solar cells, lasers, sensors and more. “Nanowires are really the major building blocks of future nano-devices,” said postdoctoral researcher Parsian Mohseni, first author of the study. “Nanowires are components that can be used, based on what material you grow them out of, for any functional electronics application.” A false-color microscope image of a single nanowire, showing the InAs core and InGaAs shell. | Graphic by Parsian Mohseni Li’s group uses a method called van der Waals epitaxy to grow nanowires from the bottom up on a flat substrate of semiconductor materials, such as silicon. The nanowires are made of a class of materials called III-V (three-five), compound semiconductors that hold particular promise for applications involving light, such as solar cells or lasers. The group previously reported growing III-V nanowires on silicon. While silicon is the most widely used material in devices, it has a number of shortcomings. -
Selective Epitaxy of Indium Phosphide and Heteroepitaxy of Indium Phosphide on Silicon for Monolithic Integration
ROYAL INSTITUTE OF TECHNOLOGY Selective Epitaxy of Indium Phosphide and Heteroepitaxy of Indium Phosphide on Silicon for Monolithic Integration Doctoral Thesis by Fredrik Olsson Laboratory of Semiconductor Materials School of Information and Communication Technology Royal Institute of Technology (KTH) Stockholm 2008 Selective epitaxy of indium phosphide and heteroepitaxy of indium phosphide on silicon for monolithic integration A dissertation submitted to the Royal Institute of Technology, Stockholm, Sweden, in partial fulfillment of the requirements for the degree of Doctor of Philosophy. TRITA-ICT/MAP AVH Report 2008:11 ISSN 1653-7610 ISRN KTH/ICT-MAP/AVH-2008:11-SE ISBN 978-91-7178-991-4 © Fredrik Olsson, June 2008 Printed by Universitetsservice US-AB, Stockholm 2008 Cover Picture: Microscopy photograph of RIE etched and HVPE regrown waveguide structures showing near to perfect planarization. ii Fredrik Olsson: Selective epitaxy of indium phosphide and heteroepitaxy of indium phosphide on silicon for monolithic integration TRITA-ICT/MAP AVH Report 2008:11, ISSN 1653-7610, ISRN KTH/ICT-MAP/AVH- 2008:11-SE, ISBN 978-91-7178-991-4 Royal Institute of Technology (KTH), School of Information and Communication Technology, Laboratory Semiconductor Materials Abstract A densely and monolithically integrated photonic chip on indium phosphide is greatly in need for data transmission but the present day’s level of integration in InP is very low. Silicon enjoys a unique position among all the semiconductors in its level of integration. But it suffers from its slow signal transmission between the circuit boards and between the chips as it uses conventional electronic wire connections. This being the bottle-neck that hinders enhanced transmission speed, optical-interconnects in silicon have been the dream for several years. -
Gaas, Inp, Ingaas, Gainp, P+-I-N+ Multiplication Measurements for Modeling of Semiconductor As Photo Detectors
IJACSA Special Issue on Selected Papers from International Conference & Workshop On Advance Computing 2013 GaAs, InP, InGaAs, GaInP, p+-i-n+ Multiplication measurements for Modeling of Semiconductor as photo detectors Sanjay.C.Patil B.K.Mishra (Research Scholar at NMIMS MUMBAI) Thakur College of Engineering and Technology, Parshvanath College of Engineering, THANE (W), Kandivali (E) Mumbai, 400101 India Mumbai, 400601 India Abstract—Optoelectronic is one of the thrust areas for the Group III on the periodic chart (arsenic in the case of GaAs) recent research activity. One of the key components of the and one from Group V (gallium in the case of GaAs). Other optoelectronic family is photo detector to be widely used in three-five (or III-V in Roman numerals) semiconductors broadband communication, optical computing, optical include indium phosphide and gallium nitride. transformer, optical control etc. Present paper includes the investigation. carried on the basis of the. Multiplication The band gap energy of semiconductors tends to decrease measurements on GaAs, InP, InGaAs, GaInP, p+-i-n+s with – with increasing temperature. When temperature increases, the region thicknesses, with investigation of applicability of the local amplitude of atomic vibrations increase, leading too larger ionization theory. A local ionization coefficient to be increasingly inters atomic spacing. In a regular semiconductor crystal, the unrepresentative of the position dependent values in the device as band gap is fixed owing to continuous energy states. In a is reduced below 1 um. quantum dot crystal, the band gap is size dependent and can be altered to produce a range of energies between the valence Keywords— Photo detectors; Impact ionization. -
Open Document
june amp front_back_am&p master template 2010 QX6.qxt 5/22/2013 9:41 AM Page 10 industry EMERGING TECHNOLOGY news New metamaterial boosts invisibility briefs Engineers at Stanford University, Calif., took another step toward designing a meta- material that works across the entire visible spectrum. The new material exhibits a refrac- Staples Inc., Framingham, Mass., tive index well below anything found in nature, such as air, whose refractive index hovers is the first major U.S. retailer to just above 1. Interesting physical phenomena can occur if this index is near-zero or nega- sell 3-D printers. The Cube from 3D Systems Inc., Rock Hill, S.C., tive. Researchers designed a single metamaterial atom with characteristics that would allow is available on Staples.com for it to efficiently interact with both the electric and magnetic components of light. The team $1299.99 and will be sold in a few began with a 2-D planar structure then folded it into a 3-D nanoscale object, preserving the stores by late June. It includes Wi- original properties. The metamaterial consists of nanocrescent-shaped atoms arranged in Fi, Mac or Windows compatibility, a periodic array and it exhibits a negative refractive index over a wavelength range of and 25 3-D templates. It can print roughly 250 nm in multiple regions of the visible and near-infrared spectrum. A few tweaks items up to 5.5 × 5.5 × 5.5 in. could make it useful across the entire visible spectrum. For more information: Ashwin Atre, using material cartridges in 16 different colors. -
Indium Gallium Nitride Multijunction Solar Cell Simulation Using Silvaco Atlas
View metadata, citation and similar papers at core.ac.uk brought to you by CORE provided by Calhoun, Institutional Archive of the Naval Postgraduate School Calhoun: The NPS Institutional Archive Theses and Dissertations Thesis Collection 2007-06 Indium gallium nitride multijunction solar cell simulation using silvaco atlas Garcia, Baldomero Monterey California. Naval Postgraduate School http://hdl.handle.net/10945/3423 NAVAL POSTGRADUATE SCHOOL MONTEREY, CALIFORNIA THESIS INDIUM GALLIUM NITRIDE MULTIJUNCTION SOLAR CELL SIMULATION USING SILVACO ATLAS by Baldomero Garcia, Jr. June 2007 Thesis Advisor: Sherif Michael Second Reader: Todd Weatherford Approved for public release; distribution is unlimited THIS PAGE INTENTIONALLY LEFT BLANK REPORT DOCUMENTATION PAGE Form Approved OMB No. 0704-0188 Public reporting burden for this collection of information is estimated to average 1 hour per response, including the time for reviewing instruction, searching existing data sources, gathering and maintaining the data needed, and completing and reviewing the collection of information. Send comments regarding this burden estimate or any other aspect of this collection of information, including suggestions for reducing this burden, to Washington headquarters Services, Directorate for Information Operations and Reports, 1215 Jefferson Davis Highway, Suite 1204, Arlington, VA 22202-4302, and to the Office of Management and Budget, Paperwork Reduction Project (0704-0188) Washington DC 20503. 1. AGENCY USE ONLY (Leave blank) 2. REPORT DATE 3. REPORT TYPE AND DATES COVERED June 2007 Master’s Thesis 4. TITLE AND SUBTITLE Indium Gallium Nitride 5. FUNDING NUMBERS Multijunction Solar Cell Simulation Using Silvaco Atlas 6. AUTHOR(S) Baldomero Garcia, Jr. 7. PERFORMING ORGANIZATION NAME(S) AND ADDRESS(ES) 8. -
Tunnel Junctions for III-V Multijunction Solar Cells Review
crystals Review Tunnel Junctions for III-V Multijunction Solar Cells Review Peter Colter *, Brandon Hagar * and Salah Bedair * Department of Electrical and Computer Engineering, North Carolina State University, Raleigh, NC 27695, USA * Correspondence: [email protected] (P.C.); [email protected] (B.H.); [email protected] (S.B.) Received: 24 October 2018; Accepted: 20 November 2018; Published: 28 November 2018 Abstract: Tunnel Junctions, as addressed in this review, are conductive, optically transparent semiconductor layers used to join different semiconductor materials in order to increase overall device efficiency. The first monolithic multi-junction solar cell was grown in 1980 at NCSU and utilized an AlGaAs/AlGaAs tunnel junction. In the last 4 decades both the development and analysis of tunnel junction structures and their application to multi-junction solar cells has resulted in significant performance gains. In this review we will first make note of significant studies of III-V tunnel junction materials and performance, then discuss their incorporation into cells and modeling of their characteristics. A Recent study implicating thermally activated compensation of highly doped semiconductors by native defects rather than dopant diffusion in tunnel junction thermal degradation will be discussed. AlGaAs/InGaP tunnel junctions, showing both high current capability and high transparency (high bandgap), are the current standard for space applications. Of significant note is a variant of this structure containing a quantum well interface showing the best performance to date. This has been studied by several groups and will be discussed at length in order to show a path to future improvements. Keywords: tunnel junction; solar cell; efficiency 1. -
Getting Ready for Indium Gallium Arsenide High-Mobility Channels
88 Conference report: VLSI Symposium Getting ready for indium gallium arsenide high-mobility channels Mike Cooke reports on the VLSI Symposium, highlighting the development of compound semiconductor channels in field-effect transistors on silicon for CMOS. esearchers across the world are readying the layer overgrowth or aspect-ratio trapping (ART) — are implementation of indium gallium arsenide free in the vertical direction, and thickness and surface R(InGaAs) and other III-V compound semicon- smoothness are determined post-growth by lithography ductors as high-mobility channel materials in field- or chemical mechanical polishing (CMP). The CELO effect transistors (FETs) on silicon (Si) for mainstream process filters out defects by the abrupt change in complementary metal-oxide-semiconductor (CMOS) growth direction from vertical to lateral, as constrained electronics applications. The latest Symposia on VLSI by the cavity. The researchers believe their technique Technology and Circuits in Kyoto, Japan in June featured avoids the main problems of alternative methods of a number of presentations from leading companies and integrating InGaAs into CMOS in terms of limited wafer university research groups directed towards this end. size, high cost, roughness, or background doping. In addition, Intel is proposing gallium nitride (GaN) The cap of the cavity was removed to access the for mobile applications such as voltage regulators or InGaAs for device fabrication. Also the InGaAs material radio-frequency power amplifiers, which require low was removed from the seed region to electrically power consumption and low-voltage operation. Away isolate the resulting devices from the underlying from III-V semiconductors, much interest has been silicon substrate. -
Indium Gallium Arsenide Detectors
TELEDYNE JUDSON TECHNOLOGIES A Teledyne Technologies Company Indium Gallium Arsenide Detectors Teledyne Judson Technologies LLC 221 Commerce Drive Montgomeryville, PA 18936 USA Tel: 215-368-6900 Fax: 215-362-6107 Visit us on the web. ISO 9001 Certified www.teledynejudson.com 1/10 J22 and J23 Detector Operating Notes (0.8 to 2.6 µm) TELEDYNE JUDSON TECHNOLOGIES A Teledyne Technologies Company General Accessories The J22 and J23 series are high For a complete system, Teledyne Judson performance InGaAs detectors offers low noise transimpedance amp- operating over the spectral range lifier modules, heat sink/preamp assem- from 0.8µm to 2.6µm. These blies and temperature controllers. For detectors provide fast rise time, further details, please visit our uniformity of response, excellent website. sensitivity, and long term reliability for a wide range of applications. For Call us enhanced performance or temperature stability of response Let our team of application engineers near the cutoff wavelength, Teledyne assist you in selecting the best Judson offers a variety of thermoelec- detector design for your application. trically cooled detector options. Or visit our website for additional Applications information on all of Teledyne Judson’s products. Device Options · Gas analysis · NIR-FTIR Teledyne Judsons standard InGaAs · Raman spectroscopy detectors, the J22 series, offers high · IR fluorescence reliability and performance in the · Blood analysis spectral range from 0.8 µm to 1.7µm. · Optical sorting In addition, the J23 series extended · Radiometry InGaAs detectors are available in · Chemical detection four cutoff options at 1.9µm, 2.2µm, · Optical communication 2.4µm and 2.6µm. Figure 1 shows the · Optical power monitoring typical response for the J22 and J23 · Laser diode monitoring series at room temperature operation. -
Theoretical Performance of Multi-Junction Solar Cells Combining III-V and Si Materials
Theoretical performance of multi-junction solar cells combining III-V and Si materials Ian Mathews,1,2* Donagh O'Mahony,1 Brian Corbett1 and Alan P. Morrison1,2 1Tyndall National Institute, UCC, Lee Maltings, Prospect Row, Cork, Ireland 2Department of Electrical and Electronic Engineering, University College Cork, Cork, Ireland *[email protected] Abstract: A route to improving the overall efficiency of multi-junction solar cells employing conventional III-V and Si photovoltaic junctions is presented here. A simulation model was developed to consider the performance of several multi-junction solar cell structures in various multi- terminal configurations. For series connected, 2-terminal triple-junction solar cells, incorporating an AlGaAs top junction, a GaAs middle junction and either a Si or InGaAs bottom junction, it was found that the configuration with a Si bottom junction yielded a marginally higher one sun efficiency of 41.5% versus 41.3% for an InGaAs bottom junction. A significant efficiency gain of 1.8% over the two-terminal device can be achieved by providing an additional terminal to the Si bottom junction in a 3-junction mechanically stacked configuration. It is shown that the optimum performance can be achieved by employing a four-junction series-connected mechanically stacked device incorporating a Si subcell between top AlGaAs/GaAs and bottom In0.53Ga0.47As cells. © 2012 Optical Society of America OCIS Codes: (230.0230) Optical devices; (350.6050) Solar energy; (040.5350) Photovoltaic. References and links 1. M. A. Green, K. Emery, Y. Hishikawa, W. Warta, and E. D. Dunlop, “Solar cell efficiency tables (version 39),” Prog. -
Integrating Ingaas Transistor and III–V Laser on Silicon
72 Technology focus: III–Vs on silicon Integrating InGaAs transistor and III–V laser on silicon Researchers in Singapore and the USA says that they have taken a step towards low-cost, low-power, high-speed optoelectronic integrated circuits. esearchers based in Singapore and the USA have integrated indium gallium arsenide (InGaAs) Rtransistors with aluminium gallium arsenide (AlGaAs) laser diodes (LDs) using molecular beam epi- taxy (MBE) on silicon substrates [Annie Kumar et al, Optics Express, vol25, p31853, 2017]. The team from National University of Singapore, the Singapore–MIT Alliance for Research and Technology- Low Energy Electronic Systems, Nanyang Technological University in Singapore and Massachusetts Institute of Technology (MIT) in the USA are working towards low- cost, low-power, high-speed optoelectronic integrated circuits (OEICs). The same grouping of institutions reported in March 2017 transistor/LD integration on germanium substrate [www.semiconductor-today.com/ news_items/2017/mar/nus_290317.shtml]. In their latest work, the Si (100) substrate was offcut 6°C in the (110) direction. The germanium (Ge) part of the buffer was grown in a three-step process, reducing the intentional doping to zero, which achieved a threading dislocation density of less than 5x106/cm6. The III–V layers were grown after 650°C annealing under ultra-high vacuum aimed at creating Ge double atomic steps on the surface of the buffer layer, designed to avoid anti-phase boundaries (APB). The III–V growth was nucleated with 20 monolayers of GaAs grown at 300°C in low-temperature migration- enhanced epitaxy (MEE) to give good surface quality and to reduce APB-related defects.