2Nd Qualification Test Series Results of the Upper Stage Engine LE-5B-3 for H3 Rocket
Total Page:16
File Type:pdf, Size:1020Kb
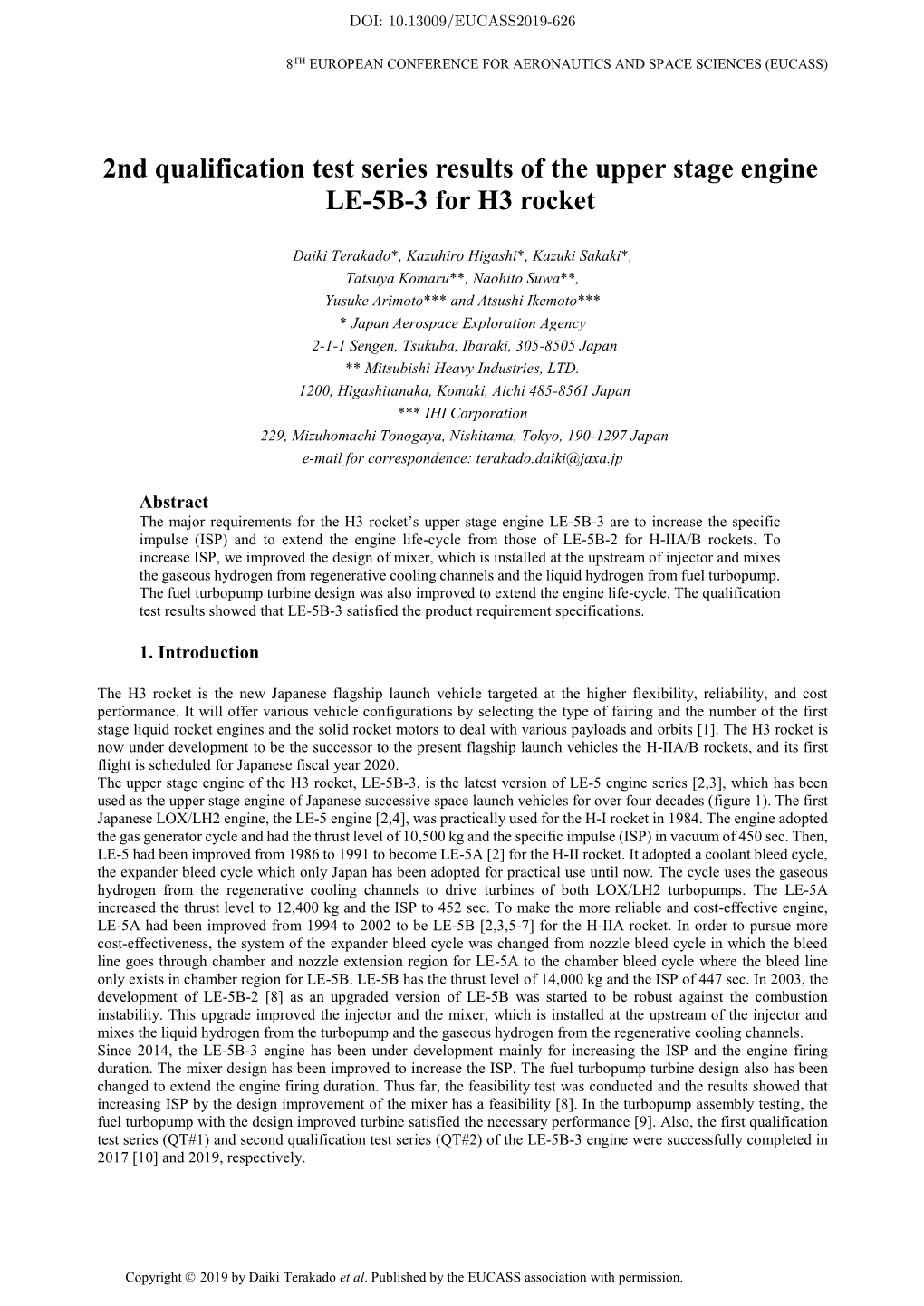
Load more
Recommended publications
-
Space) Barriers for 50 Years: the Past, Present, and Future of the Dod Space Test Program
SSC17-X-02 Breaking (Space) Barriers for 50 Years: The Past, Present, and Future of the DoD Space Test Program Barbara Manganis Braun, Sam Myers Sims, James McLeroy The Aerospace Corporation 2155 Louisiana Blvd NE, Suite 5000, Albuquerque, NM 87110-5425; 505-846-8413 [email protected] Colonel Ben Brining USAF SMC/ADS 3548 Aberdeen Ave SE, Kirtland AFB NM 87117-5776; 505-846-8812 [email protected] ABSTRACT 2017 marks the 50th anniversary of the Department of Defense Space Test Program’s (STP) first launch. STP’s predecessor, the Space Experiments Support Program (SESP), launched its first mission in June of 1967; it used a Thor Burner II to launch an Army and a Navy satellite carrying geodesy and aurora experiments. The SESP was renamed to the Space Test Program in July 1971, and has flown over 568 experiments on over 251 missions to date. Today the STP is managed under the Air Force’s Space and Missile Systems Center (SMC) Advanced Systems and Development Directorate (SMC/AD), and continues to provide access to space for DoD-sponsored research and development missions. It relies heavily on small satellites, small launch vehicles, and innovative approaches to space access to perform its mission. INTRODUCTION Today STP continues to provide access to space for DoD-sponsored research and development missions, Since space first became a viable theater of operations relying heavily on small satellites, small launch for the Department of Defense (DoD), space technologies have developed at a rapid rate. Yet while vehicles, and innovative approaches to space access. -
The Strutjet Rocket Based Combined Cycle Engine A. Siebenhaar And
J The Strutjet Rocket Based Combined Cycle Engine A. Siebenhaar and M.J. Bulman GenCorp Aerojet Sacramento, CA And D.K. Bonnar Boeing Company Huntington Beach, Ca TABLE OF CONTENTS 1C) In_.roduc_o;', 2 0 Struuet t n_ine 2.1 FIo_ Path Description 2.2 Engine Architecture 2.2.1 FIo_path Elements 2.2.2 Turbo Machine D . Propellant Supply & Thermal Management 2.2.3 Engine C)cle 2.2.4 Structural Concept 2.3 Strutjet Operating Modes 2.3.1 Ducted Rocket Mode 2.3.2 Ramjet Mode 2.3.3 Scramjet Mode 2.3.4 Scram Rocket and Ascent Rocket Modes 2.4 Optimal Propulsion System Selection 2.4.1 Boost Mode Selection 2.4.2 Engine Design Point Selection 2.4.3 Ascent Rocket Transition Point Selection 3.0 Strutjet Vehicle Inte_ation 3.1 Strutjet Reference Mission 3.2 Engine-Vehicle Considerations 33 Vehicle Pitching Moment 3.4 Engine Performance 3.5 Reduced Operating Cost Through Robustness 3.6 Vehicle Comparisons 4.0 Available Hydrocarbon'and Hydrogen Test Data and plan_d Future Test Activities 4.1 Storable Hydrocarbon System Tests 4.2 CD'ogenic H.xdrogen System Tests 4.3 Planned Flight Tests 5.0 Maturit2. Of Required Su'utjet Technologies 6.0 Summar) and Conclusions 7.0 References J List of Tables 1. Comparison of Rocket and Strut.let Turbopumps 2. Sensitixitx to Engine Robustness 3. Vehicle Design Features and System Robustness 4. All-Rocket Vehicle Mass Breakdown 5. Strutjet Vehicle Mass Breakdown 6. Design Parameters for the All-Rocket and the RBCC-SSTO Vehicle 7. -
Jaxa Today 10.Pdf
Japan Aerospace Exploration Agency April 2016 No. 10 Special Features Japan’s Technical Prowess Technical excellence and team spirit are manifested in such activities as the space station capture of the HTV5 spacecraft, development of the H3 Launch Vehicle, and reduction of sonic boom in supersonic transport International Cooperation JAXA plays a central role in international society and contributes through diverse joint programs, including planetary exploration, and the utilization of Earth observation satellites in the environmental and disaster management fields Contents No. 10 Japan Aerospace Exploration Agency Special Feature 1: Japan’s Technical Prowess 1−3 Welcome to JAXA TODAY Activities of “Team Japan” Connecting the Earth and Space The Japan Aerospace Exploration Agency (JAXA) is positioned as We review some of the activities of “Team the pivotal organization supporting the Japanese government’s Japan,” including the successful capture of H-II Transfer Vehicle 5 (HTV5), which brought overall space development and utilization program with world- together JAXA, NASA and the International Space Station (ISS). leading technology. JAXA undertakes a full spectrum of activities, from basic research through development and utilization. 4–7 In 2013, to coincide with the 10th anniversary of its estab- 2020: The H3 Launch Vehicle Vision JAXA is currently pursuing the development lishment, JAXA defined its management philosophy as “utilizing of the H3 Launch Vehicle, which is expected space and the sky to achieve a safe and affluent society” and to become the backbone of Japan’s space development program and build strong adopted the new corporate slogan “Explore to Realize.” Under- international competitiveness. We examine the H3’s unique features and the development program’s pinned by this philosophy, JAXA pursues a broad range of pro- objectives. -
The Insurance Institute of London
The Insurance Institute of London CII CPD accredited - demonstrates the quality of an event and that it meets CII/PFS member CPD scheme requirements. This webinar will count as 1 hour of CPD and can be included as part of your CPD requirement should you consider it relevant to your professional development needs. It is recommended that you keep any evidence of the CPD activity you have completed and upload copies to the recording tool as the CII may ask to see this if your record is selected for review. MHI Launch Services - key essence of MHI’s quality management - Ref. B01038001405 February 17, 2021 © MITSUBISHI HEAVY INDUSTRIES, LTD. All Rights Reserved. MHI PROPRIETARY INFORMATION MHI PROPRIETARY INFORMATION 1. Introduction of MHI & Insurance Activities for our products 2. Launch Services 2.1 current work force H-IIA/B 2.2 Next gen, flagship H3 - Under Development - 3. MHI Quality Management Overview 4. Overcoming anomalies 4.1 Launch Operation case, H-IIB F8 4.2 Development case, H3 main engine(LE-9) 5. Conclusion © MITSUBISHI HEAVY INDUSTRIES, LTD. All Rights Reserved. PROPRIETARY INFORMATION 3 1. Introduction of MHI & Insurance Activities for our products MHI PROPRIETARY Introduction of MHI INFORMATION Power Systems Foundation July 7, 1884 Capital (USD) 2,415 MUSD As of Mar. 2019 Employees Thermal Power Plant Compressor CO2 Recovery Plants Desalination Plant (consolidated) 80,744 As of Mar. 2019 Industry & Infrastructure Sales (consolidated) 38,055 MUSD As of Mar. 2020 EBITDA 115.1 Dubai Metro Intelligent Transport Systems Overseas offices 7 Aircraft, Defense & Space Currency rate: USD 1 = JPY 110 Boeing – 787 Space Jet Defense Aircraft Launch Vehicle (Composite main wings) (H-IIA/-IIB) © MITSUBISHI HEAVY INDUSTRIES, LTD. -
Corporate Profile
2013 : Epsilon Launch Vehicle 2009 : International Space Station 1997 : M-V Launch Vehicle 1955 : The First Launched Pencil Rocket Corporate Profile Looking Ahead to Future Progress IHI Aerospace (IA) is carrying out the development, manufacture, and sales of rocket projectiles, and has been contributing in a big way to the indigenous space development in Japan. We started research on rocket projectiles in 1953. Now we have become a leading comprehensive manufacturer carrying out development and manufacture of rocket projectiles in Japan, and are active in a large number of fields such as rockets for scientific observation, rockets for launching practical satellites, and defense-related systems, etc. In the space science field, we cooperate with the Japan Aerospace Exploration Agency (JAXA) to develop and manufacture various types of observational rockets named K (Kappa), L (Lambda), and S (Sounding), and the M (Mu) rockets. With the M rockets, we have contributed to the launch of many scientific satellites. In 2013, efforts resulted in the successful launch of an Epsilon Rocket prototype, a next-generation solid rocket which inherited the 2 technologies of all the aforementioned rockets. In the practical satellite booster rocket field, We cooperates with the JAXA and has responsibilities in the solid propellant field including rocket boosters, upper-stage motors in development of the N, H-I, H-II, and H-IIA H-IIB rockets. We have also achieved excellent results in development of rockets for material experiments and recovery systems, as well as the development of equipment for use in a space environment or experimentation. In the defense field, we have developed and manufactured a variety of rocket systems and rocket motors for guided missiles, playing an important role in Japanese defense. -
The Modified Fuel Turbopump of 2Nd Stage Engine for H3 Launch Vehicle
DOI: 10.13009/EUCASS2017-189 7TH EUROPEAN CONFERENCE FOR AERONAUTICS AND SPACE SCIENCES (EUCASS) The Modified Fuel Turbopump of 2nd stage engine for H3 launch vehicle Naoki Nagao*, Hideaki Nanri*, Koichi Okita*, Yohei Ishizu**, Shinnosuke Yabuki** and Shinichiro Kohno** *Japan Aerospace Exploration Agency 2-1-1 Sengen, Tsukuba-shi, Ibaraki 305-8505 **IHI Corporation 229 Tonogaya Mizuho-machi, Nishitama-gun, Tokyo 190-1297 Abstract The turbine of fuel turbopump of 2nd stage engine for H3 launch vehicle was changed from a partial admission type to a full admission type to meet the requirement of longer firing duration in a flight. The full admission type had an advantage of increasing the efficiency because of the uniform flow in circumference direction, on the other hand, had a disadvantage of decreasing the efficiency caused with the smaller height of turbine blade. The design of turbine was carefully modified and it was verified with experiments that the turbine had 10% higher performance than the previous design. 1. Introduction The next generation Japanese mainstay launch vehicle; H3 launch vehicle, has been developed since April 2014 to increase the launch capability of domestic launchers and to enhance the international competitiveness based on the “Basic Plan on Space Policy” [1]. As the result of system study on H3 launch vehicle, the second stage engine of H- IIA/B rocket, named LE-5B-2 is modified and adopted to H3 launch vehicle, because the performance of LE-5B-2 almost meets the requirement of the system and the high reliability of LE-5B series has been proved in the long-term operation. -
The Annual Compendium of Commercial Space Transportation: 2017
Federal Aviation Administration The Annual Compendium of Commercial Space Transportation: 2017 January 2017 Annual Compendium of Commercial Space Transportation: 2017 i Contents About the FAA Office of Commercial Space Transportation The Federal Aviation Administration’s Office of Commercial Space Transportation (FAA AST) licenses and regulates U.S. commercial space launch and reentry activity, as well as the operation of non-federal launch and reentry sites, as authorized by Executive Order 12465 and Title 51 United States Code, Subtitle V, Chapter 509 (formerly the Commercial Space Launch Act). FAA AST’s mission is to ensure public health and safety and the safety of property while protecting the national security and foreign policy interests of the United States during commercial launch and reentry operations. In addition, FAA AST is directed to encourage, facilitate, and promote commercial space launches and reentries. Additional information concerning commercial space transportation can be found on FAA AST’s website: http://www.faa.gov/go/ast Cover art: Phil Smith, The Tauri Group (2017) Publication produced for FAA AST by The Tauri Group under contract. NOTICE Use of trade names or names of manufacturers in this document does not constitute an official endorsement of such products or manufacturers, either expressed or implied, by the Federal Aviation Administration. ii Annual Compendium of Commercial Space Transportation: 2017 GENERAL CONTENTS Executive Summary 1 Introduction 5 Launch Vehicles 9 Launch and Reentry Sites 21 Payloads 35 2016 Launch Events 39 2017 Annual Commercial Space Transportation Forecast 45 Space Transportation Law and Policy 83 Appendices 89 Orbital Launch Vehicle Fact Sheets 100 iii Contents DETAILED CONTENTS EXECUTIVE SUMMARY . -
CRYOTE (Cryogenic Orbital Testbed) Concept
CRYOTE (Cryogenic Orbital Testbed) Concept Mari Gravlee* and Bernard Kutter† United Launch Alliance, Centennial, CO Mark Wollen ‡ Innovative Engineering Solutions, Murrieta, CA Noah Rhys § Yetispace, Inc., Huntsville, AL Laurie Walls ** NASA Kennedy Space Center, FL Demonstrating cryo-fluid management (CFM) technologies in space is critical for advances in long duration space missions. Current space-based cryogenic propulsion is viable for hours, not the weeks to years needed by space exploration and space science. CRYogenic Orbital TEstbed (CRYOTE) provides an affordable low-risk environment to demonstrate a broad array of critical CFM technologies that cannot be tested in Earth’s gravity. These technologies include system chilldown, transfer, handling, health management, mixing, pressure control, active cooling, and long-term storage. United Launch Alliance is partnering with Innovative Engineering Solutions, the National Aeronautics and Space Administration, and others to develop CRYOTE to fly as an auxiliary payload between the primary payload and the Centaur upper stage on an Atlas V rocket. Because satellites are expensive, the space industry is largely risk averse to incorporating unproven systems or conducting experiments using flight hardware that is supporting a primary mission. To minimize launch risk, the CRYOTE system will only activate after the primary payload is separated from the rocket. Flying the testbed as an auxiliary payload utilizes Evolved Expendable Launch Vehicle performance excess to cost-effectively demonstrate enhanced CFM. Nomenclature ACES Advanced Common Evolved Stage IES Innovative Engineering Solutions ACS Attitude Control System LAD Liquid Acquisition Device Centaur Upper stage of Atlas V EELV LH2 Liquid Hydrogen CFM Cryogenic Fluid Management MLI Multi-layer Insulation EDS Earth Departure Stage Rideshare Launching as an auxiliary payload EELV Evolved Expendable Launch Vehicle TRL Technology Readiness Level ESPA EELV Secondary Payload Adapter TVS Thermodynamic Vent System g Gravity ULA United Launch Alliance * Sr. -
22Nd IAA SYMPOSIUM on HUMAN EXPLORATION of the SOLAR SYSTEM (A5) Space Transportation Solutions for Deep Space Missions (4-D2.8)
70th International Astronautical Congress 2019 Paper ID: 49396 oral 22nd IAA SYMPOSIUM ON HUMAN EXPLORATION OF THE SOLAR SYSTEM (A5) Space Transportation Solutions for Deep Space Missions (4-D2.8) Author: Dr. Shoyo Hyodo Mitsubishi Heavy Industries, Ltd., Japan, shoyo [email protected] Mr. daisuke tsujita Mitsubishi Heavy Industries Ltd. - Nagoya Aerospace Systems, Japan, daisuke [email protected] Mr. Shinobu Matsuo Mitsubishi Heavy Industries, Ltd., Japan, shinobu [email protected] Mr. Osamu Kitayama Japan, osamu [email protected] A GATEWAY SUPPLY MISSION SCENARIO AND FLIGHT PLAN WITH UPGRADED H3 AND HTV-X Abstract The lunar orbital platform Gateway is led to be constructed by NASA in 2020s as the staging point for crewed and robotic lunar exploration. JAXA is studying to participate in the Gateway and MHI is considering how to realize the mission with their own techniques, such as supplying cargos with upgraded HTV-X launched by H3. Both H3 and HTV-X are currently being developed. H3 is based on the heritage of H-IIA/H-IIB. The maiden flight of H3 will be 2020. H3 intends to be more customer friendly launch vehicle by increasing reli- ability and launch capability while decreasing its price. On the other hand, HTV-X is an advanced version of H-II Transfer Vehicle (HTV) to increase supply cargo capability and provide an on-orbit demonstration opportunity for future exploration mission, like Gateway. HTV-X has two modules, service module(SM) and pressurized module (PM), and rendezvouses ISS by using SM functions, guidance, navigation and control system and propulsion system, and supplies cargos loaded in PM. -
Research Areas in Space
RESPOND & AI Capacity Building Programme Office ISRO HQ, Bengaluru RESPOND & AI Capacity Building Programme Office ISRO HQ, Bengaluru RESEARCH AREAS IN SPACE A Document for Preparing Research Project Proposals RESPOND & AI Capacity Building Programme Office ISRO HQ, Bengaluru January 2021 Technical Guidance Dr. M A Paul, Associate Director, RESPOND & AI, ISRO HQ Technical Support and Compilation Smt Nirupama Tiwari, Sci/Engr SE, CBPO, ISRO HQ Shri K Mahesh, Sr. Asst, CBPO, ISRO HQ Technical Guidance Dr. M A Paul, Associate Director, RESPOND & AI, ISRO HQ For any queries please contact Director, Capacity Building Programme Office (CBPO) Technical Support and Compilation Indian Space Research Organisation HQ Smt Nirupama Tiwari, Sci/Engr SE, CBPO, ISRO HQ Department of Space Shri K Mahesh, Sr. Asst, CBPO, ISRO HQ Government of India Antariksh Bhavan New BEL Road For any queries please contact Bangalore 560094 E-mail: [email protected] Director, Capacity Building Programme Office (CBPO) Indian Space Research Organisation HQ Department of Space Associate Director, RESPOND & Academic Interface Government of India Indian Space Research Organisation HQ Antariksh Bhavan Department of Space New BEL Road Government of India Bangalore 560094 Antariksh Bhavan E-mail: [email protected] New BEL Road Bangalore 560094 Associate Director, RESPOND & Academic Interface E-mail: [email protected] Indian Space Research Organisation HQ Department of Space Government of India Antariksh Bhavan New BEL Road Bangalore 560094 E-mail: [email protected] CONTENTS -
Development of Internationally Competitive Solid Rocket Booster for H3 Launch Vehicle
Development of Internationally Competitive Solid Rocket Booster for H3 Launch Vehicle YANAGISAWA Masahiro : Space Launch Vehicle Project Office, Rocket Systems Department, IHI AEROSPACE Co., Ltd. KISHI Koichi : Manager, Space Launch Vehicle Project Office, Rocket Systems Department, IHI AEROSPACE Co., Ltd. NAGAO Toru : Manager, Space Launch Vehicle Project Office, Rocket Systems Department, IHI AEROSPACE Co., Ltd. Recently, low cost launch vehicles intended for large commercial satellites are being developed actively all over the world, including Ariane 6 by Arianspace (Europe), Falcon 9 and Falcon Heavy by SpaceX (USA), a company led by Elon Musk, Vulcan by ULA (USA) and by Russian and Indian companies. Moreover, Japan is also developing the next flagship launch vehicle called H3. This paper introduces H3 and its strap-on booster “SRB-3.” 1. Introduction This paper introduces the outlines of the H3 launch vehicle and SRB-3, and elemental technologies introduced into the The development of the H3 launch vehicle was started in FY development of SRB-3 in order to achieve both low cost and 2014 as a Japan’s flagship launch vehicle replacing the H-IIA high reliability as the concepts of the SRB-3 development. and H-IIB launch vehicles. The development is currently in 2. H3 launch vehicle the detailed design phase, and we are aiming to launch the first H3 launch vehicle from the Tanegashima Space Center Figure 1 illustrates the H3 launch vehicle. (Kagoshima Pref.) of the National Research and Development The development of the H3 launch vehicle is expected to Agency, Japan Aerospace Exploration Agency (JAXA) in secure independence for Japan’s space transportation (space FY 2020. -
Systems-Theoretic Process Analysis of Space Launch Vehicles ⁎ John M
The Journal of Space Safety Engineering xxx (xxxx) xxx–xxx Contents lists available at ScienceDirect The Journal of Space Safety Engineering journal homepage: www.elsevier.com/locate/jsse Systems-Theoretic Process Analysis of space launch vehicles ⁎ John M. Risinga, , Nancy G. Levesonb a Massachusetts Institute of Technology, USA b Aeronautics and Astronautics, Massachusetts Institute of Technology, USA ABSTRACT This article demonstrates how Systems-Theoretic Process Analysis (STPA) can be used as a powerful tool to identify, mitigate, and eliminate hazards throughout the space launch system lifecycle. Hazard analysis tech- niques commonly used to evaluate launch vehicle safety use reliability theory as their foundation, but most modern space launch vehicle accidents have resulted from design errors or other factors independent of com- ponent reliability. This article reviews safety analysis methods as they are applied to space launch vehicles, and demonstrates that they are unable to treat many of the causal factors associated with modern launch accidents. Next, it describes how STPA can be applied to the design of space launch vehicles to treat these casual factors. Safety-guided design with STPA is then demonstrated with a hypothetical small-lift launch vehicle, launch safety system, and upper stage propulsion system. 1. Introduction reliability-based tools often used to evaluate safety are unable to predict or analyze software and component interactions. Furthermore, the 1.1. Motivation growing popularity of autonomous flight termination systems (AFTS) reinforces the need for software safety analysis tools. Designers of The causal factors of launch vehicle accidents are changing. Early launch systems need hazard analysis tools that are better equipped to accidents were often caused by electromechanical component failures, handle these new causes of launch vehicle accidents.