Con-Cor's HO Scale CNS&M Electroliner
Total Page:16
File Type:pdf, Size:1020Kb
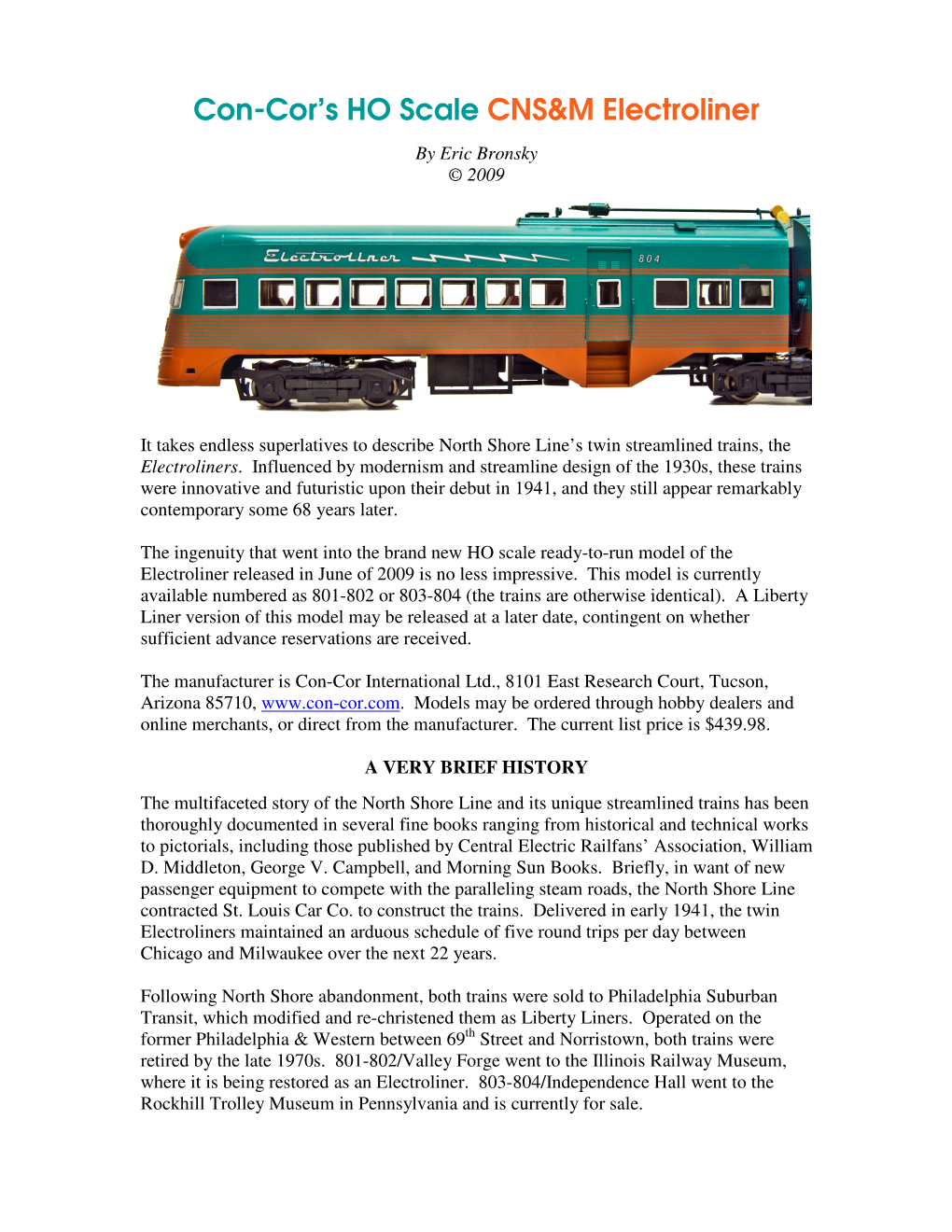
Load more
Recommended publications
-
Published by the Friends of Philadelphia Trolleys, Inc. Volume 11, Number 2 Spring 2017
Published by the Friends of Philadelphia Trolleys, Inc. Volume 11, Number 2 Spring 2017 By Harry Donahue Photos by Harry Donahue and Bill Monaghan ver the past winter, the Friends of Philadelphia Trolleys awarded grants to O trolleys in four different museums. Continuing our current effort to raise funding, a grant of $1,000.00 was given for ex-PTC Brill car Square Rail Museum on West Chester Pike in #8042 at the Pennsylvania Trolley Museum. The grant is being delayed by FPT until the late Newtown Square. Although Car #23 will be a summer. At this time, the annual Washington static display and not actually operate, FPT County Matching Grant program will made an exception in the case in giving this commences, thus allowing the grant amount to grant because another $500.00 grant was given be matched. If you would like to help increase the amount of the grant, please use the attached donation form for 8042. Help to get this wonderful old Brill Peter Witt car back in service at PTM. A grant of $500.00 was awarded on behalf of Red Arrow “St. Louie” #23 now at the Newtown to Brilliner #8 now at Shore Line Trolley Museum (Branford, Connecticut). There are several Red Arrow cars at Branford, but #8 is probably closest to operating condition. And finally, another $500.00 was awarded to the seat renewal project for Philadelphia Transportation Company’s PCC #2743 at the Rockhill Trolley Museum. All the refurbished seats have been returned to the car and are awaiting installation. This last grant will help pay the final bills on the project. -
Dear Electroliner/Liberty Liner Enthusiast
Dear Electroliner/Liberty Liner Enthusiast: Please help us continue to improve the operating and physical condition of the Liberty Liner Independence Hall! A MAJOR MILESTONE HAS BEEN ACCOMPLISHED—WE HAVE RETURNED THIS HISTORIC TRAIN TO OPERABLE CONDITION AND ARE USING IT FOR SPECIAL EVENTS – BUT MORE HELP IS NEEDED ! Thanks to tremendous volunteer commitment as well as a substantial material donation, this historic train has been returned to operable condition 50 years after it was rebuilt into its Liberty Liner configuration. Now, the challenge is to further improve its reliability and make it look beautiful again. Will you help us ensure that an example of each of these trains is beautifully preserved, in operable condition, in both Electroliner and Liberty Liner configurations? The train is always popular with visitors and looks right at home in the rolling Pennsylvania landscape. The train Much like the work of this mechanic in 1964, recent returned to operation in February at an annual gathering efforts have focused on replacement of the train’s of volunteers from a number of electric railway resistor grids, enabling a return to operation. museums. HERE IS WHAT WE CAN ACCOMPLISH WITH YOUR HELP , IN ORDER OF PRIORITY : Purchase supplies to rewire the control switchgear at the 803A end as has been done at the 804A1 end Rebuild two additional motor-generator sets to provide spare low voltage capacity Steam clean interior seating, repair damaged areas of interior flooring, and repaint the interior walls and ceilings Purchase supplies and repaint the exterior either as a volunteer led project, or as a contracted project if sufficient funds are raised In the longer term, make the train’s air conditioning system operable again. -
Published by the Friends of Philadelphia Trolleys,Inc
PUBLISHED BY THE FRIENDS OF PHILADELPHIA TROLLEYS, INC. Volume 14|Number 1 Winter 2020 anuary 20, 2020 was a cold and windy that did not deter a group of Friends of Philadelphia Trolleys members to meet at Philadelphia’s Thirtieth Street Station. The occasion was to take farewell rides on one or more of the Southeastern Pennsylvania Transit Authority’s historic PCC II cars on its #15 Girard Avenue line. The “farewell” was because the line would be temporarily suspended to bus service, effective After boarding Bill’s car #9043, the group rode out to Sunday, January 26, 2020. The reason for this was due the end of the line at the Angora Loop, located at Baltimore Avenue and 61st Street. Of course, there was to bridge work on portions of Girard Avenue that no resisting not taking a “group picture” of everyone … included track replacement and the necessity of much well mostly everyone. Some stayed inside the trolley. needed maintenance on the trolleys themselves. The After all, it was cold and windy outside. All too soon, suspension itself is expected to take 12 to 18 months. the group had to re-board so that Bill could keep to his schedule on the return trip. After gathering at the one of the Pennsylvania Railroad’s grand masterpieces, the group moved to the After saying our farewells and thanks to Bill, we westbound Thirtieth Street Station on SEPTA’s departed the Thirteenth and Market Station stop to Subway-Surface Trolley Line to meet a #34 trolley. It transfer over to the Frankford-Market Elevated line for was not just any trolley, but one that was operated by Girard Avenue. -
Published by the Friends of Philadelphia Trolleys, Inc. Scott R. Becker
Published by the Friends of Philadelphia Trolleys, Inc. Volume 12, Number 4 Fall 2018 By Harry Donahue Pictures from the Andy Maginnis Collection e are pleased to announce that the challenge grant for Philadelphia Transportation Company car #8042 has been met through the efforts of the Pennsylvania Trolley Museum. A facsimile of the letter from PTM’s Executive Director Scott Becker wrote to Friends of Philadelphia Trolleys tells the story. Hello Matt, Harry and Bill, I am very happy to report that we have raised over $33,074.00 to meet the 20th Century Electric Railway Foundation's Challenge Grant! We are particularly pleased with the response from our supporters to this fund from the Washington County Community Foundation’s Gives Campaign Event on Sept 12 which brought in over $23,874.00! This includes the WCCF’s match and bonus money they added to donations received. I have requested that the 20th Century Electric Railway Foundation release their $25,000.00 grant for this project! Scott R. Becker Executive Director I want to thank you all for your efforts to raise funds for PTC 8042. Pennsylvania Trolley Museum Our volunteers have been hard at work on this car and once Keith Bray returns, it should move along at a faster pace. The pictures above show #8042’s last day on Route #55. The bottom one shows the car on Thanks again for your continued Old York Road, south of Highland Avenue, in the support! Abington Township. SEPTA #2168 GETS is published by the SOME NEEDED ATTENTION The Streamliner By Harry Donahue Friends of Philadelphia Trolleys, a Pennsylvania non-profit corporation. -
Classic Trains' 2014-2015 Index
INDEX TO VOLUMES 15 and 16 All contents of publications indexed © 2013, 2014, and 2015 by Kalmbach Publishing Co., Waukesha, Wis. CLASSIC TRAINS Spring 2014 through Winter 2015 (8 issues) ALL ABOARD! (1 issue) 876 pages HOW TO USE THIS INDEX: Feature material has been indexed three or more times—once by the title under which it was published, again under the author’s last name, and finally under one or more of the subject categories or railroads. Photographs standing alone are indexed (usually by railroad), but photographs within a feature article are not separately indexed. Brief items are indexed under the appropriate railroad and/or category. Most references to people are indexed under the company with which they are commonly identified; if there is no common identification, they may be indexed under the person’s last name. Items from countries from other than the U.S. and Canada are indexed under the appropriate country name. ABBREVIATIONS: Sp = Spring Classic Trains, Su = Summer Classic Trains, Fa = Fall Classic Trains, Wi = Winter Classic Trains; AA! = All Aboard!; 14 = 2014, 15 = 2015. Albany & Northern: Strange Bedfellows, Wi14 32 A Bridgeboro Boogie, Fa15 60 21st Century Pullman, Classics Today, Su15 76 Abbey, Wallace W., obituary, Su14 9 Alco: Variety in the Valley, Sp14 68 About the BL2, Fa15 35 Catching the Sales Pitchers, Wi15 38 Amtrak’s GG1 That Might Have Been, Su15 28 Adams, Stuart: Finding FAs, Sp14 20 Anderson, Barry: Article by: Alexandria Steam Show, Fa14 36 Article by: Once Upon a Railway, Sp14 32 Algoma Central: Herding the Goats, Wi15 72 Biographical sketch, Sp14 6 Through the Wilderness on an RDC, AA! 50 Biographical sketch, Wi15 6 Adventures With SP Train 51, AA! 98 Tracks of the Black Bear, Fallen Flags Remembered, Wi14 16 Anderson, Richard J. -
Car & Locomotive Shop
ScaleScale OOTraiTraiTrainsnsns O ◆◆ ◆◆ Jan/FebJan/Feb 2004 2004 IIssuessue #12 #12 $5.95$5.95 US $5.95.95 • Can $7.95.95 Display until Feb. 29th Modeling for the O Scale Craftsman 31280 Groesbeck, Fraser, MI 48026 586-296-6116 Open Mon-Fri 10-8, P&DHobbyHobby ShopShop Sat 10-6, Sun 12-5 P&D Fax: 586-296-5642 PowerPower oror RepowerRepower KitsKits forfor RedRed CabooseCaboose GPsGPs PDP2201K-Repower kit, Red Caboose GP9, P&D brass EMD Blomberg trucks PDP2200K-Repower Kit, Red Caboose GP9 PDP2201K-Repower Kit, Red Caboose GP9 with with plastic Blomberg trucks...$160.00 P&D brass Blomberg trucks...$200.00 The P&D TWIN TOWER DRIVE for the Red Caboose GP screws that are furnished in the Red Caboose body kit. body kit is functionally equivalent to the P&D power units These P&D Twin Tower Drive kits can also be used to repower already available for the P&D F units, GPs, RSDs, and the existing Red Caboose GPs. Two kits are offered: #PDP2200K has Weaver FAs, FBs, RS-3s and GP-38s. plastic Blomberg trucks, while #PDP2201K features the P&D brass The Red Caboose power kits provide only the necessary Blomberg trucks, which are truly some of the finest trucks on the power related parts to supplement the Red Caboose GP market. Each kit also includes a powerful Pittman motor and all body kit. These power kits fully utilize the underframe the necessary parts to complete the installation. Detailed instruc- (platform), deck, air tanks, fuel tanks, motor mounts and tions are included. -
2013 APTA Public Transportation Fact Book
2013 Public Transportation Fact Book 2013 PUBLIC TRANSPORTATION FACT BOOK 64th Edition October 2013 PUBLISHED BY American Public Transportation Association Fact book historical tables and additional data are available at: http://www.apta.com/resources/statistics/Pages/transitstats.aspx American Public Transportation Association 1666 K Street, N.W., Suite 1100 Washington, DC 20006 TELEPHONE: (202) 496-4800 E-MAIL: [email protected] www.apta.com APTA’s Vision Statement Be the leading force in advancing public transportation. APTA’s Mission Statement APTA serves and leads its diverse membership through advocacy, innovation, and information sharing to strengthen and expand public transportation. prepared by John Neff, Senior Policy Researcher (202) 496-4812 [email protected] Matthew Dickens, Policy Analyst (202) 496-4817 [email protected] PUBLIC TRANSPORTATION FACT BOOK American Public Transportation Association Washington, DC October 2013 Material from the 2013 Public Transportation Fact Book may be quoted or reproduced without obtaining the permission of the American Public Transportation Association. Suggested Identification: American Public Transportation Association: 2013 Public Transportation Fact Book, Washington, DC, October, 2013. TABLE OF CONTENTS Table of Contents APTA AND THE FACT BOOK ......................................... 5 Figure 11: Percent of Systems with Arrival Time Formats .................................................................. 15 NATIONAL DATA SUMMARY ......................................... 6 VEHICLES ..................................................................... -
November 14, 2014 in Honor of Veterans Day This Week, My Thanks
Dear All: November 14, 2014 In honor of Veterans Day this week, my thanks go out to the men and women of yesterday, today and tomorrow who have and who will sacrifice so much for the U.S.A. It seems to me, the train world really comes alive during the holidays to help us remember years gone by. So many of you volunteer your time to set up and run a layout at various locations, how amazing it is because you are touching the lives of so many in a positive and healthy way. Bravo! I would love to include YOUR story with the next e‐ blast that connects your family memories with the holiday season and the world of trains. I think it would be great to share these stories over the next several weeks leading up to the end of 2014! What did you say? You have pictures to go along with the story, well send them along to me and as long as they are family friendly I’ll share them with those that read the eblast. As a reminder, the eblasts and attachments will be placed on the WB&A website under the “About” tab for your viewing/sharing pleasure http://www.wbachapter.org/2014%20E‐ Blast%20Page.htm The attachments are contained in the one PDF attached to this email in an effort to streamline the sending of this email and to ensure the attachments are able to be received. If you need a PDF viewer to read the document which can be downloaded free at http://www.adobe.com/products/acrviewer/acrvd nld.html. -
March 2004 Bulletin.Pub
TheNEW YORK DIVISION BULLETIN - MARCH, 2004 Bulletin New York Division, Electric Railroaders’ Association Vol. 47, No. 3 March, 2004 The Bulletin BROOKLYN BRIDGE “L” SERVICE QUIT 60 YEARS Published by the New York Division, Electric AGO Railroaders’ Association, Incorporated, PO Box On March 5, 1944, BMT elevated trains furnished through service to midtown Man- 3001, New York, New ceased operating across the Brooklyn Bridge hattan. Because riding declined and service York 10008-3001. to Park Row. The Sands Street and Adams was curtailed in the 1920s and 1930s, the Street stations were abandoned, and trains elaborate Park Row terminal’s tail switch For general inquiries, were turned at a new terminal, Bridge-Jay tracks and exit platforms were no longer contact us at Street. A double crossover was installed east needed. Starting November 27, 1935, trains [email protected] or by of this station, formerly called Bridge Street. terminated at the easterly platforms and phone at (212) 986-4482 The west end of the platform was extended switched back on a new double crossover (voice mail available). ERA’s website is and a new entrance was built at Jay Street east of the station. The structure supporting www.electricrailroaders. and Myrtle Avenue, where passengers could the tail switch tracks and the exit platforms org. transfer to the trolley cars or the IND subway. was demolished. Editorial Staff: Editor-in-Chief: Bernard Linder News Editor: Randy Glucksman Contributing Editor: Jeffrey Erlitz Production Manager: David Ross Park Row looking south, after exit platforms were removed in the mid-1930s. ©2004 New York Bernard Linder collection Division, Electric Park Row looking south, before exit platforms were Railroaders’ removed. -
Just Visiting—Second New Jersey Pcc Car Finds Temporary Home at Museum
WINTER (November-January) 2012 Volume 48 Number 4 JUST VISITING—SECOND NEW JERSEY PCC CAR FINDS TEMPORARY HOME AT MUSEUM NEW PARTNERSHIP BENEFITS OPEN CAR #1875 AS WELL AS HISTORIC PCC CAR By Matt Nawn Less than one year after former New Jersey Transit PCC Car #6 arrived at Rockhill Furnace to become part of the museum’s collection, a second former New Jersey Transit PCC Car arrived on January 27. This car, #10, is projected to be just a temporary visitor, however, unlike #6. The arrival of former NJT #10 at Rockhill Trolley Museum is part of a new partnership with UTCRAS approved this January by the Board of Directors. UTCRAS, located in Morton, PA, has provided support to the rail transit industry since 1982. UTCRAS is an AAR-Certified wheel, bearing, and axle shop and has performed high quality work for railroads, transit systems, and museums throughout North America. UTCRAS purchased NJT #10 for transfer to a future historic trolley operator at the same time our museum purchased #6, and has requested Rockhill Trolley Museum make the car #10 operational again in the same manner as was done with #6. We will also remove the trucks for overhaul by UTCRAS and subsequently retruck the car after the overhaul is completed. In exchange for our efforts, UTCRAS will perform an overhaul of the trucks from open car #1875 to include new bearings, axles, and replacement of wheels (supplied by Rockhill Trolley Museum). As UTCRAS is not a motor shop, we will still need to fund the overhaul of the four traction motors, but getting the mechanical work accomplished on these trucks will be a huge leap forward toward our efforts to maintain the car as a reliable operating exhibit for the long term. -
July Final.Indd
RAIL REPORT July 2015 NO. 660 Rocky Mountain Railroad Club • Rocky Mountain Railroad Historical Foundation Please Remember: There Is No Meeting In Barnes Hall In July Car 25 Open House August 8th • 10 AM to 2 PM See You At The Federal Center RMRRC 2015 Calendar July 18th Como Rail Project Work Day. July 26th Como Rail Project Work Day. August 8th Car 25 Open House at the Federal Center. August 11th Meeting and Program, “Photo and Video Potpourri.” September 8th Meeting and Program, “Photo Production Seminar” presented by Greg Walz. October Annual Luncheon Banquet. November 10th Meeting and Program. December 8th Annual Business Meeting and Program. Due to circumstances beyond our control, programs and dates are subject to change without notice. Please contact Dave Schaaf with program ideas at [email protected] or 303 988-3456. August 8, 2015 The Annual Tradition Continues! The City of Lakewood’s Interurban Car 25 Open House Free Rides, Weather Permitting Enter the Denver Federal Center at All adults need a government photo Gate 1 on Kipling Street South of 6th ID (i.e. drivers license) to enter the Avenue. Once inside the gate follow the Federal Center. Sorry, pets are not yellow signs to building No. 78. permitted. Como Rail Project Work Days Saturday July 18th and Sunday July 26th Some details are still being worked out, Those interested in assisting with the but the plan to lay rail in Como has pro- project should contact Pat Mauro at gressed. The track that will be laid will 303-838-7740 (phone preferred) or by connect the Como Roundhouse turn- email at [email protected]. -
Streetcar Currents
MINNESOTA STREETCAR MUSEUM September—2012 Minneapolis & Excelsior, Minnesota Streetcar Camp Bill Arends—General Supt. hen you were a kid did you ever go to camp dur- W ing the summer? Do you remember the anticipa- tion the night before? Maybe tossed and turned, didn’t sleep well? Spent the night thinking about the adventure that awaited you? Maybe a little apprehensive or worried about the unknown, about the kid who you may be part- nered with? Because you are reading this, you undoubtedly are in- terested in large machines that run on rails. Now imagine Bill The Motorman being a kid and knowing that tomorrow you are going to Says: Streetcar Camp and you will have the opportunity to op- • Our Halloween and San- erate a 46,000 pound streetcar. That’s what five young ta trolleys will be oper- campers got to experience last week. ating in the fall, so spread the word about n a beautiful August morning, under the direction of head camp counselor them to your friends & O Rod Eaton, assistant counselors Ben Franske, Sam VanTassel, Jim Berry neighbors. and yours truly, gathered at the carbarn to ready TCRT standard streetcar No. 1300, • Give a big THANK YOU to go over the curriculum and be ready for the campers by 9 AM. all our volunteers when At 9:00 AM the streetcar pulled into the Linden Hills Station. Excited campers, you see them. They with their parents, waited on the platform. Youthful exuberance, excitement, shy ap- make our Museum go! prehension and maybe “Oh my gosh! That thing is soooo big.