FLY ME to the MOON on an SLS BLOCK II Steven S
Total Page:16
File Type:pdf, Size:1020Kb
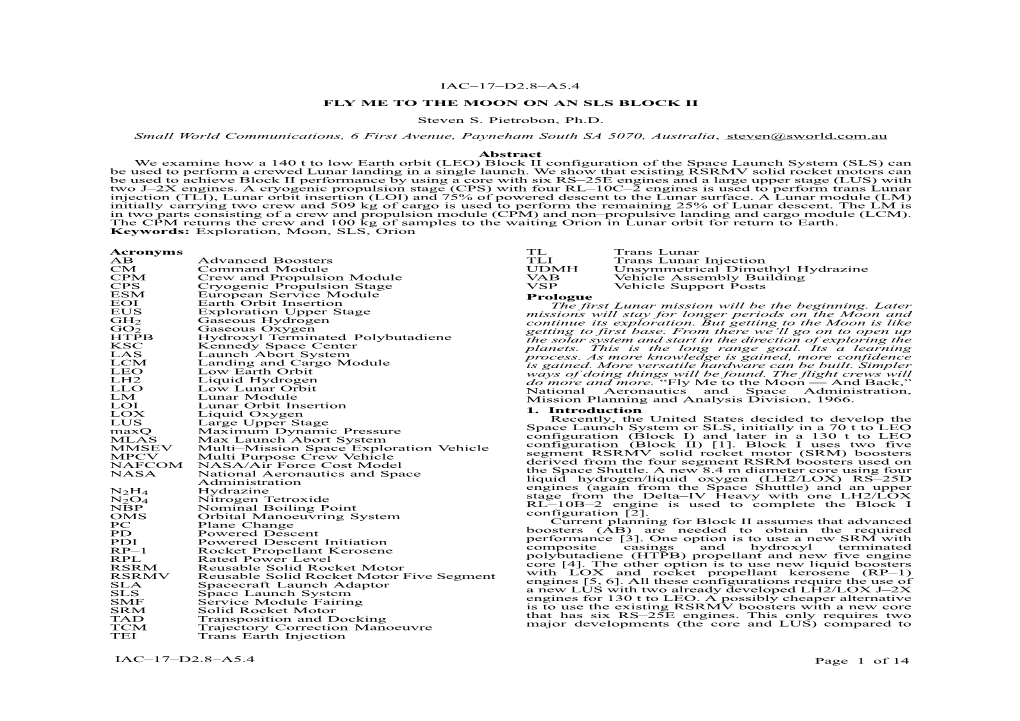
Load more
Recommended publications
-
Preparation of Papers for AIAA Journals
ASCEND 10.2514/6.2020-4000 November 16-18, 2020, Virtual Event ASCEND 2020 Cryogenic Fluid Management Technologies Enabling for the Artemis Program and Beyond Hans C. Hansen* and Wesley L. Johnson† NASA Glenn Research Center, Cleveland, Ohio, 44135, USA Michael L. Meyer‡ NASA Engineering Safety Center, Cleveland, Ohio, 44135, USA Arthur H. Werkheiser§ and Jonathan R. Stephens¶ NASA Marshall Space Flight Center, Huntsville, Alabama, 35808, USA NASA is endeavoring on an ambitious return to the Moon and eventually on to Mars through the Artemis Program leveraging innovative technologies to establish sustainable exploration architectures collaborating with US commercial and international partners [1]. Future NASA architectures have baselined cryogenic propulsion systems to support lunar missions and ultimately future missions to Mars. NASA has been investing in maturing CFM active and passive storage, transfer, and gauging technologies over the last decade plus primarily focused on ground development with a few small- scale microgravity fluid experiments. Recently, NASA created a Cryogenic Fluid Management (CFM) Technology Roadmap identifying the critical gaps requiring further development to reach a technology readiness level (TRL) of 6 prior to infusion to flight applications. To address the technology gaps the Space Technology Mission Directorate (STMD) strategically plans to invest in a diversified CFM portfolio approach through ground and flight demonstrations, collaborating with international partners, and leveraging Public Private Partnerships (PPPs) opportunities with US industry through Downloaded by Michele Dominiak on December 23, 2020 | http://arc.aiaa.org DOI: 10.2514/6.2020-4000 the Tipping Point and Announcement of Collaborative Opportunities (ACO) solicitations. Once proven, these system capabilities will enable the high performing cryogenic propellant systems needed for the Artemis Program and beyond. -
Delta II Icesat-2 Mission Booklet
A United Launch Alliance (ULA) Delta II 7420-10 photon-counting laser altimeter that advances MISSION rocket will deliver the Ice, Cloud and land Eleva- technology from the first ICESat mission tion Satellite-2 (ICESat-2) spacecraft to a 250 nmi launched on a Delta II in 2003 and operated until (463 km), near-circular polar orbit. Liftoff will 2009. Our planet’s frozen and icy areas, called occur from Space Launch Complex-2 at Vanden- the cryosphere, are a key focus of NASA’s Earth berg Air Force Base, California. science research. ICESat-2 will help scientists MISSION investigate why, and how much, our cryosphere ICESat-2, with its single instrument, the is changing in a warming climate, while also Advanced Topographic Laser Altimeter System measuring heights across Earth’s temperate OVERVIEW (ATLAS), will provide scientists with height and tropical regions and take stock of the vege- measurements to create a global portrait of tation in forests worldwide. The ICESat-2 mission Earth’s third dimension, gathering data that can is implemented by NASA’s Goddard Space Flight precisely track changes of terrain including Center (GSFC). Northrop Grumman built the glaciers, sea ice, forests and more. ATLAS is a spacecraft. NASA’s Launch Services Program at Kennedy Space Center is responsible for launch management. In addition to ICESat-2, this mission includes four CubeSats which will launch from dispens- ers mounted to the Delta II second stage. The CubeSats were designed and built by UCLA, University of Central Florida, and Cal Poly. The miniaturized satellites will conduct research DELTA II For nearly 30 years, the reliable in space weather, changing electric potential Delta II rocket has been an industry and resulting discharge events on spacecraft workhorse, launching critical and damping behavior of tungsten powder in a capabilities for NASA, the Air Force Image Credit NASA’s Goddard Space Flight Center zero-gravity environment. -
Nasa Engineering & Safety Center
National Aeronautics and Space Administration NASA ENGINEERING & SAFETY CENTER 2008 TECHNICAL UPDATE www.nasa.gov 1 It gives me a lot of pleasure to recognize the 5th anniversary of the establishment of the NASA Engineering and Safety Center. It also offers, for me, a valuable reminder that it is important always to be open to new ideas and new approaches to solving problems. When the NESC was established, I was more than a bit pessimistic that it could work, that it could provide value for the Agency over and above that offered by our various center engineering directorates. I was wrong. The synergy that has been achieved by the NESC and its cross-agency approach to solving difficult technical problems has been truly impressive. It is, in my mind, a useful model for future endeavors and a great example that it is actually possible for us to “be NASA”, to rise above some of the parochial geographic concerns which have plagued NASA for five decades. These days, when someone tells me that the NESC is looking at a particular issue, I am reassured, because I know that if a solution can be found, this group will find it. – Dr. Michael D. Griffin, NASA Administrator 2 Table of Contents Stakeholder Messages ........................................................................................ 2 NESC Leadership ................................................................................................ 3 Overview: How the NESC Works .......................................................................... 4 NESC Academy: Learning from the Past ............................................................... 8 Technical Highlights Collecting Flight Force Measurements to Improve Coupled Loads Analysis ... 11 Analysis of Constellation Program Mass Properties ....................................... 11 Prediction and Reduction of Ares SRB Thrust Oscillation ............................... 12 Review of the Launch Abort System Motor Qualification Plan ....................... -
Why NASA's Planet-Hunting Astrophysics Telescope Is an Easy Budget Target, and What Defeat Would Mean PAGE 24
Q & A 12 ASTRONAUT’S VIEW 20 SPACE LAUNCH 34 Neil deGrasse Tyson A realistic moon plan SLS versus commercial SPECIAL REPORT SPACE DARK ENERGY DILEMMA Why NASA’s planet-hunting astrophysics telescope is an easy budget target, and what defeat would mean PAGE 24 APRIL 2018 | A publication of the American Institute of Aeronautics andd Astronautics | aeroaerospaceamerica.aiaa.orgerospaceamerica.aiaa.org 9–11 JULY 2018 CINCINNATI, OH ANNOUNCING EXPANDED TECHNICAL CONTENT FOR 2018! You already know about our extensive technical paper presentations, but did you know that we are now offering an expanded educational program as part of the AIAA Propulsion and Energy Forum and Exposition? In addition to our pre-forum short courses and workshops, we’ve enhanced the technical panels and added focused technical tutorials, high level discussion groups, exciting keynotes and more. LEARN MORE AND REGISTER TODAY! For complete program details please visit: propulsionenergy.aiaa.org FEATURES | April 2018 MORE AT aerospaceamerica.aiaa.org 20 34 40 24 Returning to Launching the Laying down the What next the moon Europa Clipper rules for space Senior research scientist NASA, Congress and We asked experts in for WFIRST? and former astronaut the White House are space policy to comment Tom Jones writes about debating which rocket on proposed United NASA’s three upcoming space what it would take to should send the probe Nations guidelines deliver the funds and into orbit close to this for countries and telescopes are meant to piece together political support for the Jovian moon. companies sending some heady puzzles, but the White Lunar Orbital Outpost- satellites and other craft House’s 2019 budget proposal would Gateway. -
Materials for Liquid Propulsion Systems
https://ntrs.nasa.gov/search.jsp?R=20160008869 2019-08-29T17:47:59+00:00Z CHAPTER 12 Materials for Liquid Propulsion Systems John A. Halchak Consultant, Los Angeles, California James L. Cannon NASA Marshall Space Flight Center, Huntsville, Alabama Corey Brown Aerojet-Rocketdyne, West Palm Beach, Florida 12.1 Introduction Earth to orbit launch vehicles are propelled by rocket engines and motors, both liquid and solid. This chapter will discuss liquid engines. The heart of a launch vehicle is its engine. The remainder of the vehicle (with the notable exceptions of the payload and guidance system) is an aero structure to support the propellant tanks which provide the fuel and oxidizer to feed the engine or engines. The basic principle behind a rocket engine is straightforward. The engine is a means to convert potential thermochemical energy of one or more propellants into exhaust jet kinetic energy. Fuel and oxidizer are burned in a combustion chamber where they create hot gases under high pressure. These hot gases are allowed to expand through a nozzle. The molecules of hot gas are first constricted by the throat of the nozzle (de-Laval nozzle) which forces them to accelerate; then as the nozzle flares outwards, they expand and further accelerate. It is the mass of the combustion gases times their velocity, reacting against the walls of the combustion chamber and nozzle, which produce thrust according to Newton’s third law: for every action there is an equal and opposite reaction. [1] Solid rocket motors are cheaper to manufacture and offer good values for their cost. -
Orbital Fueling Architectures Leveraging Commercial Launch Vehicles for More Affordable Human Exploration
ORBITAL FUELING ARCHITECTURES LEVERAGING COMMERCIAL LAUNCH VEHICLES FOR MORE AFFORDABLE HUMAN EXPLORATION by DANIEL J TIFFIN Submitted in partial fulfillment of the requirements for the degree of: Master of Science Department of Mechanical and Aerospace Engineering CASE WESTERN RESERVE UNIVERSITY January, 2020 CASE WESTERN RESERVE UNIVERSITY SCHOOL OF GRADUATE STUDIES We hereby approve the thesis of DANIEL JOSEPH TIFFIN Candidate for the degree of Master of Science*. Committee Chair Paul Barnhart, PhD Committee Member Sunniva Collins, PhD Committee Member Yasuhiro Kamotani, PhD Date of Defense 21 November, 2019 *We also certify that written approval has been obtained for any proprietary material contained therein. 2 Table of Contents List of Tables................................................................................................................... 5 List of Figures ................................................................................................................. 6 List of Abbreviations ....................................................................................................... 8 1. Introduction and Background.................................................................................. 14 1.1 Human Exploration Campaigns ....................................................................... 21 1.1.1. Previous Mars Architectures ..................................................................... 21 1.1.2. Latest Mars Architecture ......................................................................... -
Interstellar Probe on Space Launch System (Sls)
INTERSTELLAR PROBE ON SPACE LAUNCH SYSTEM (SLS) David Alan Smith SLS Spacecraft/Payload Integration & Evolution (SPIE) NASA-MSFC December 13, 2019 0497 SLS EVOLVABILITY FOUNDATION FOR A GENERATION OF DEEP SPACE EXPLORATION 322 ft. Up to 313ft. 365 ft. 325 ft. 365 ft. 355 ft. Universal Universal Launch Abort System Stage Adapter 5m Class Stage Adapter Orion 8.4m Fairing 8.4m Fairing Fairing Long (Up to 90’) (up to 63’) Short (Up to 63’) Interim Cryogenic Exploration Exploration Exploration Propulsion Stage Upper Stage Upper Stage Upper Stage Launch Vehicle Interstage Interstage Interstage Stage Adapter Core Stage Core Stage Core Stage Solid Solid Evolved Rocket Rocket Boosters Boosters Boosters RS-25 RS-25 Engines Engines SLS Block 1 SLS Block 1 Cargo SLS Block 1B Crew SLS Block 1B Cargo SLS Block 2 Crew SLS Block 2 Cargo > 26 t (57k lbs) > 26 t (57k lbs) 38–41 t (84k-90k lbs) 41-44 t (90k–97k lbs) > 45 t (99k lbs) > 45 t (99k lbs) Payload to TLI/Moon Launch in the late 2020s and early 2030s 0497 IS THIS ROCKET REAL? 0497 SLS BLOCK 1 CONFIGURATION Launch Abort System (LAS) Utah, Alabama, Florida Orion Stage Adapter, California, Alabama Orion Multi-Purpose Crew Vehicle RL10 Engine Lockheed Martin, 5 Segment Solid Rocket Aerojet Rocketdyne, Louisiana, KSC Florida Booster (2) Interim Cryogenic Northrop Grumman, Propulsion Stage (ICPS) Utah, KSC Boeing/United Launch Alliance, California, Alabama Launch Vehicle Stage Adapter Teledyne Brown Engineering, California, Alabama Core Stage & Avionics Boeing Louisiana, Alabama RS-25 Engine (4) -
Physical & Thermodynamic Properties Of
PHYSICAL & THERMODYNAMIC PROPERTIES OF HYPERGOLIC PROPELLANTS: A REVIEW AND UPDATE S.L ARNOLD ENSCO, INC. VANDENBERG AFB, CA ABSTRACT Significant errors and omissions were found in some of the reported literature values for nitrogen tetroxide, monomethylhydrazine, and Aerozine-50. The methods used to try and resolve some of these errors included (1) a comparison of various literature values, including an assessment of data quality, to determine whether reported values were measured or estimated, (2) a derivation of temperature dependent correlation coefficients and validation with independent measurements (where sufficient measured data were available), and (3) an estimation of the missing parameters using modern techniques such as the method of corresponding states or group contribution methods. Utilizing these methods resulted in a validated set of properties (many as functions temperature) for hypergolic propellants, which are suitable for environmental modeling applications and more general engineering calculations. The complete parameter set is provided, along with references and examples illustrating the above methods. Also, mixing rules, pseudo-critical properties, and mixture properties are provided for a nominal composition Aerozine-50 mixture. INTRODUCTION The objective of this work was to find and validate existing hypergol parameters for use in environmental modeling applications. However, standard references and chemical engineering journals either do not have all of the required data, such as vapor viscosity as a function of temperature, or they contain crudely estimated values and outright errors. Although they contain some of the more hard to find parameters, the current propellant manuals no longer contain the ancillary information regarding data quality, sources, etc. Also, some of the reported data is mis- represented, i.e., if the original experiment was not specifically designed to measure critical properties, it’s most likely not an appropriate source for those parameters (especially when the original author has so stated). -
Instrument Host Overview - Spacecraft ======
Instrument Host Overview - Spacecraft ===================================== Launch Vehicle Description -------------------------- The launch vehicle used for Mars Pathfinder was the McDonnell Douglas Delta II 7925. An engine section in the Delta first stage housed the Rocketdyne RS-27 main engine and two Rocketdyne LR101-NA-11 vernier engines. The vernier engines provided roll control during main engine burn, and attitude control after main engine cutoff and before second stage separation. The RS-27 main engine was a single start, liquid bi-propellant rocket engine which provided approximately 894,094 N of thrust at lift off. The first stage propellant load (96,000 kg) consisted of RP-1 fuel (thermally stable kerosene) and liquid oxygen as an oxidizer. The RP-1 fuel tank and liquid oxygen tank were separated by a center body section that housed control electronics, ordnance sequencing equipment, a telemetry system, and a rate gyro. First stage thrust augmentation was provided by nine solid-propellant Graphite Epoxy Motors (GEMs), each fueled with 12,000 kg of hydroxyl-terminated polybutadiene solid propellant. Each GEM provided an average thrust of 439,796 N at lift off. The main engine, vernier engines, and six of the GEMs were ignited at lift off. The remaining three GEMs were ignited in flight. The GEMs were jettisoned from the first stage after motor burnout. The interstage assembly extended from the top of the first stage to the second stage mini-skirt. This assembly carried loads to the first stage, and contained an exhaust vent and six spring driven separation rods. The Delta II 7925 second stage propulsion system included a restartable, liquid bi-propellant Aerojet AJ10-118K engine that consumed Aerozine 50 fuel (a 50/50 mix of hydrazine and asymmetric dimethyl hydrazine) and nitrogen tetroxide (N2O4). -
THE MAX LAUNCH ABORT SYSTEM – CONCEPT, FLIGHT TEST, and EVOLUTION Michael G
THE MAX LAUNCH ABORT SYSTEM – CONCEPT, FLIGHT TEST, AND EVOLUTION Michael G. Gilbert(1), PhD (1) Principal Engineer, NASA Engineering and Safety Center 11 Langley Blvd., MS 116,Hampton VA 23681 USA Email:[email protected] Abstract escape system Maxime Faget [1]. The effort was intended to provide The NASA Engineering and Safety Center programmatic risk-reduction for the (NESC) is an independent engineering Constellation Program (CxP) Orion Crew analysis and test organization providing Exploration Vehicle (CEV) project. support across the range of NASA programs. In 2007 NASA was developing The CEV project baseline Launch Abort the launch escape system for the Orion System (LAS) development is an evolution spacecraft that was evolved from the of the Apollo towered-rocket design, Fig. traditional tower-configuration escape 2. Unlike the Apollo LAS, the CEV LAS systems used for the historic Mercury and incorporated an attitude control motor to Apollo spacecraft. The NESC was tasked, ensure stable flight following the escape as a programmatic risk-reduction effort to motor burn. At the time the MLAS project develop and flight test an alternative to the was initiated, the CEV LAS was Orion baseline escape system concept. experiencing development delays related This project became known as the Max to the LAS attitude control motor. Launch Abort System (MLAS), named in Therefore, the MLAS project was to honor of Maxime Faget, the developer of consider escape system concepts that the original Mercury escape system. Over would not require active attitude control or the course of approximately two years the stabilization following escape motor NESC performed conceptual and tradeoff burnout. -
Testing Strategies and Methodologies for the Max Launch Abort System Dawn M
Testing Strategies and Methodologies for the Max Launch Abort System Dawn M. Schaible Daniel E. Yuchnovicz NASA Engineering and Safety Center Hampton, Virginia ABSTRACT The National Aeronautics and Space Administration (NASA) Engineering and Safety Center (NESC) was tasked to develop an alternate, tower-less launch abort system (LAS) as risk mitigation for the Orion Project. The successful pad abort flight demonstration test in July 2009 of the “Max” launch abort system (MLAS) provided data critical to the design of future LASs, while demonstrating the Agency’s ability to rapidly design, build and fly full-scale hardware at minimal cost in a “virtual” work environment. Limited funding and an aggressive schedule presented a challenge for testing of the complex MLAS system. The successful pad abort flight demonstration test was attributed to the project’s systems engineering and integration process, which included: a concise definition of, and an adherence to, flight test objectives; a solid operational concept; well defined performance requirements, and a test program tailored to reducing the highest flight test risks. The testing ranged from wind tunnel validation of computational fluid dynamic simulations to component ground tests of the highest risk subsystems. This paper provides an overview of the testing/risk management approach and methodologies used to understand and reduce the areas of highest risk — resulting in a successful flight demonstration test. KEY WORDS: Testing, risk management, flight test, launch abort systems MLAS PROJECT OVERVIEW NASA’s next generation crewed spacecraft, named Orion, is a part of the overall Constellation Program. The baseline Orion design includes a launch abort system (LAS) with tower, derived from the Apollo design. -
The Annual Compendium of Commercial Space Transportation: 2017
Federal Aviation Administration The Annual Compendium of Commercial Space Transportation: 2017 January 2017 Annual Compendium of Commercial Space Transportation: 2017 i Contents About the FAA Office of Commercial Space Transportation The Federal Aviation Administration’s Office of Commercial Space Transportation (FAA AST) licenses and regulates U.S. commercial space launch and reentry activity, as well as the operation of non-federal launch and reentry sites, as authorized by Executive Order 12465 and Title 51 United States Code, Subtitle V, Chapter 509 (formerly the Commercial Space Launch Act). FAA AST’s mission is to ensure public health and safety and the safety of property while protecting the national security and foreign policy interests of the United States during commercial launch and reentry operations. In addition, FAA AST is directed to encourage, facilitate, and promote commercial space launches and reentries. Additional information concerning commercial space transportation can be found on FAA AST’s website: http://www.faa.gov/go/ast Cover art: Phil Smith, The Tauri Group (2017) Publication produced for FAA AST by The Tauri Group under contract. NOTICE Use of trade names or names of manufacturers in this document does not constitute an official endorsement of such products or manufacturers, either expressed or implied, by the Federal Aviation Administration. ii Annual Compendium of Commercial Space Transportation: 2017 GENERAL CONTENTS Executive Summary 1 Introduction 5 Launch Vehicles 9 Launch and Reentry Sites 21 Payloads 35 2016 Launch Events 39 2017 Annual Commercial Space Transportation Forecast 45 Space Transportation Law and Policy 83 Appendices 89 Orbital Launch Vehicle Fact Sheets 100 iii Contents DETAILED CONTENTS EXECUTIVE SUMMARY .