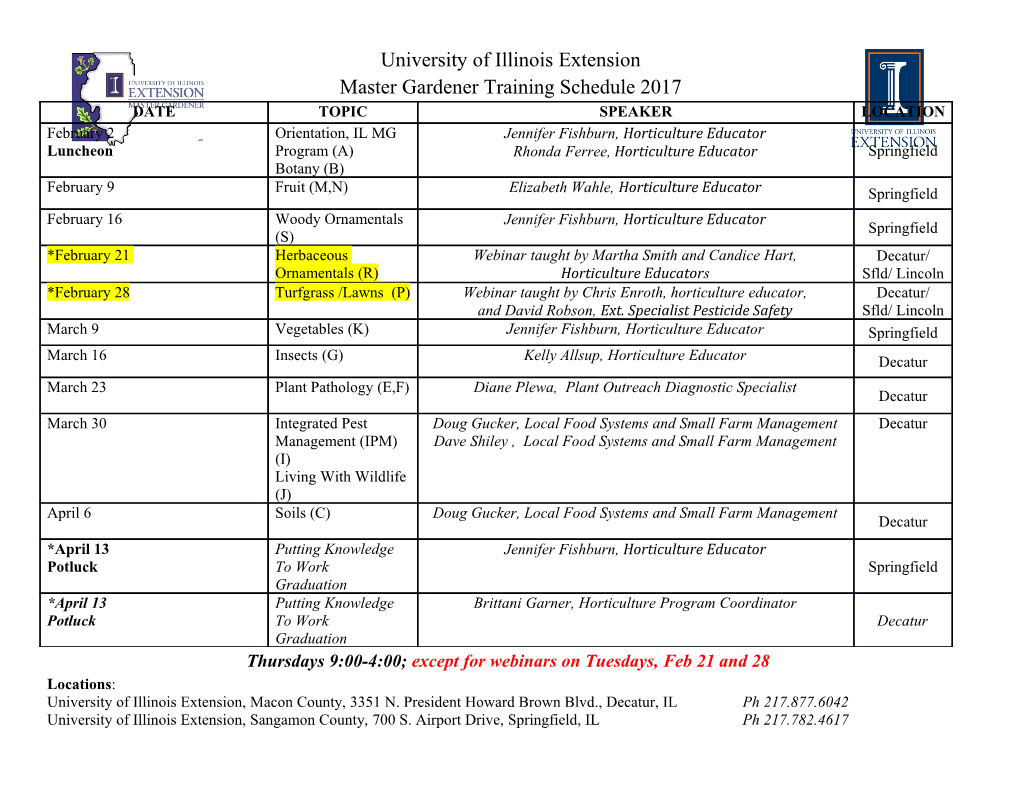
IAC–17–D2.8–A5.4 FLY ME TO THE MOON ON AN SLS BLOCK II Steven S. Pietrobon, Ph.D. Small World Communications, 6 First Avenue, Payneham South SA 5070, Australia, [email protected] Abstract We examine how a 140 t to low Earth orbit (LEO) Block II configuration of the Space Launch System (SLS) can be used to perform a crewed Lunar landing in a single launch. We show that existing RSRMV solid rocket motors can be used to achieve Block II performance by using a core with six RS–25E engines and a large upper stage (LUS) with two J–2X engines. A cryogenic propulsion stage (CPS) with four RL–10C–2 engines is used to perform trans Lunar injection (TLI), Lunar orbit insertion (LOI) and 75% of powered descent to the Lunar surface. A Lunar module (LM) initially carrying two crew and 509 kg of cargo is used to perform the remaining 25% of Lunar descent. The LM is in two parts consisting of a crew and propulsion module (CPM) and non–propulsive landing and cargo module (LCM). The CPM returns the crew and 100 kg of samples to the waiting Orion in Lunar orbit for return to Earth. Keywords: Exploration, Moon, SLS, Orion Acronyms TL Trans Lunar AB Advanced Boosters TLI Trans Lunar Injection CM Command Module UDMH Unsymmetrical Dimethyl Hydrazine CPM Crew and Propulsion Module VAB Vehicle Assembly Building CPS Cryogenic Propulsion Stage VSP Vehicle Support Posts ESM European Service Module Prologue EOI Earth Orbit Insertion The first Lunar mission will be the beginning. Later EUS Exploration Upper Stage missions will stay for longer periods on the Moon and GH2 Gaseous Hydrogen continue its exploration. But getting to the Moon is like GO2 Gaseous Oxygen getting to first base. From there we'll go on to open up HTPB Hydroxyl Terminated Polybutadiene the solar system and start in the direction of exploring the KSC Kennedy Space Center planets. This is the long range goal. Its a learning LAS Launch Abort System process. As more knowledge is gained, more confidence LCM Landing and Cargo Module is gained. More versatile hardware can be built. Simpler LEO Low Earth Orbit ways of doing things will be found. The flight crews will LH2 Liquid Hydrogen do more and more. “Fly Me to the Moon — And Back,” LLO Low Lunar Orbit National Aeronautics and Space Administration, LM Lunar Module Mission Planning and Analysis Division, 1966. LOI Lunar Orbit Insertion LOX Liquid Oxygen 1. Introduction LUS Large Upper Stage Recently, the United States decided to develop the maxQ Maximum Dynamic Pressure Space Launch System or SLS, initially in a 70 t to LEO MLAS Max Launch Abort System configuration (Block I) and later in a 130 t to LEO MMSEV Multi–Mission Space Exploration Vehicle configuration (Block II) [1]. Block I uses two five MPCV Multi Purpose Crew Vehicle segment RSRMV solid rocket motor (SRM) boosters NAFCOM NASA/Air Force Cost Model derived from the four segment RSRM boosters used on NASA National Aeronautics and Space the Space Shuttle. A new 8.4 m diameter core using four Administration liquid hydrogen/liquid oxygen (LH2/LOX) RS–25D N H Hydrazine engines (again from the Space Shuttle) and an upper 2 4 stage from the Delta–IV Heavy with one LH2/LOX N2O4 Nitrogen Tetroxide NBP Nominal Boiling Point RL–10B–2 engine is used to complete the Block I OMS Orbital Manoeuvring System configuration [2]. PC Plane Change Current planning for Block II assumes that advanced PD Powered Descent boosters (AB) are needed to obtain the required PDI Powered Descent Initiation performance [3]. One option is to use a new SRM with RP–1 Rocket Propellant Kerosene composite casings and hydroxyl terminated RPL Rated Power Level polybutadiene (HTPB) propellant and new five engine RSRM Reusable Solid Rocket Motor core [4]. The other option is to use new liquid boosters RSRMV Reusable Solid Rocket Motor Five Segment with LOX and rocket propellant kerosene (RP–1) SLA Spacecraft Launch Adaptor engines [5, 6]. All these configurations require the use of SLS Space Launch System a new LUS with two already developed LH2/LOX J–2X SMF Service Module Fairing engines for 130 t to LEO. A possibly cheaper alternative SRM Solid Rocket Motor is to use the existing RSRMV boosters with a new core TAD Transposition and Docking that has six RS–25E engines. This only requires two TCM Trajectory Correction Manoeuvre major developments (the core and LUS) compared to TEI Trans Earth Injection IAC–17–D2.8–A5.4 Page 1 of 14 Figure 1: Mission sequence of events. three major developments (SRM, core and LUS or engine is centrally located beneath the CPM and booster, engine and LUS) if using advanced boosters. protrudes through the middle of the LCM. Two descent To send the crew to the Moon in their Orion engines are at the sides of the ascent engine. The descent multipurpose crew vehicle (MPCV) and LM, a CPS with engines can throttle and rotate in two axis to enable four LH2/LOX RL–10C–2 engines is used. The design precise landing control. The ascent engine nominally of this stage is similar to the exploration upper stage performs Lunar ascent, carrying the crew and 100 kg of (EUS) proposed in [7], but using a common bulkhead in Lunar samples to Orion waiting in low Lunar orbit order to meet vehicle height restrictions. We examined (LLO). This engine is of fixed thrust and position for the case where the LUS performs partial TLI as in [8], but maximum reliability. we found best performance is achieved when the CPS During Lunar descent, if the descent engines fails to performs all of TLI due to the higher performance of the ignite or experiences an anomaly, the CPM separates RL–10 engines and lower dry mass of the CPS. from the LCM with the ascent engine being used for To simplify mission design we assume the LUS abort. If the LM fails to separate from the CPS, the CPM places the CPS and spacecraft into a 37x200 km separates from the LCM and performs an abort, using trajectory at apogee. This results in the LUS being safely either the descent or ascent engines. If the ascent engine targeted for reentry without requiring a deorbit burn. The fails or experiences an anomaly during Lunar ascent, the CPS performs a small burn at apogee to circularise the descent engines can be used as a backup. orbit. While in LEO Orion separates from its spacecraft Unlike other two stage LMs with a propulsive launch adaptor (SLA). At the same time the SLA is descent stage, the LCM can have a large cargo volume ejected. Orion then performs a transposition and docking as it is free from carrying propellant. Only the space manoeuvre and docks with the LM below. The CPS then where the ascent and descent engines passes through the performs TLI and LOI. This will require the CPS to have LCM is used. The surrounding volume can be used for a low boil–off rate, as the LH2 and LOX are stored at carrying a Lunar rover, tools, experiments, antenna, cryogenic temperatures. solar panels and supplies. For future more capable Due to the large mass of Orion at 26,520 kg [9], this versions of the SLS Block II configuration presented in puts significant limits on the LM. To overcome this this paper, the LM could be converted to a rover. This limitation we propose using the high performance of the would allow greater distances to be covered with CPS to also perform 75% of Lunar descent. The LM then missions of up to 14 Earth days. For a future Lunar base, performs the remaining 25% of Lunar descent to the LCM can carry pressurised and unpressurised touchdown. This requires a critical stage separation and supplies for the base, in addition to the crew. Thus, even ignition by the LM at the end of the CPS burn. To though using staged descent carries some risk (which we increase the reliability of this event, the LM has a CPM have tried to minimise) it has some great advantages, and an LCM. The LCM is a non–propulsive stage which including increased payload and future mission carries cargo, has landing legs and supports the CPM. flexibility. The CPM can carry up to four crew (two crew are Figure 1 shows the mission architecture. The mission carried in the initial flights), all the propellant and has sequence is 1. Launch, 2. RSRMV separation, 3. Core two sets of engines, descent and ascent. The ascent separation, 4. LAS ejection, 5. LUS separation, 6. IAC–17–D2.8–A5.4 Page 2 of 14 Transposition and docking in LEO, 7. TLI, 8. LOI, 9. LM The average exhaust speed is ve = (mp1 ve1 + mp2 ve2)/mp undocking, 10. Powered descent, 11. CPS separation, 12. = 2605.4 m/s (265.7 s). The burnout mass is 96,751 kg Lunar landing, 13. Lunar ascent, 14. Rendezvous and (95,844 kg dry and 907 kg slag) [7] and the action time docking, 15. LM undocking and TLI, 16. CM separation, is 128.4 s [8]. Using the graph of vacuum thrust verses 17. Reentry, 18. Parachute deployment. time in [11], we manually plotted the graph and A detailed analysis of the SLS Block II configuration calculated the total impulse. This was then used to adjust and LM we have selected is presented in the following the curve for the actual impulse of mpve = 1,647,887 kNs. sections. Figure 2 plots the vacuum thrust against time.
Details
-
File Typepdf
-
Upload Time-
-
Content LanguagesEnglish
-
Upload UserAnonymous/Not logged-in
-
File Pages14 Page
-
File Size-