Manual on Quality Assurance for Khadi Jointly Prepared by KVIC and IIT, New Delhi, Is Being Circulated for Wider Consultation and Field-Implementation
Total Page:16
File Type:pdf, Size:1020Kb
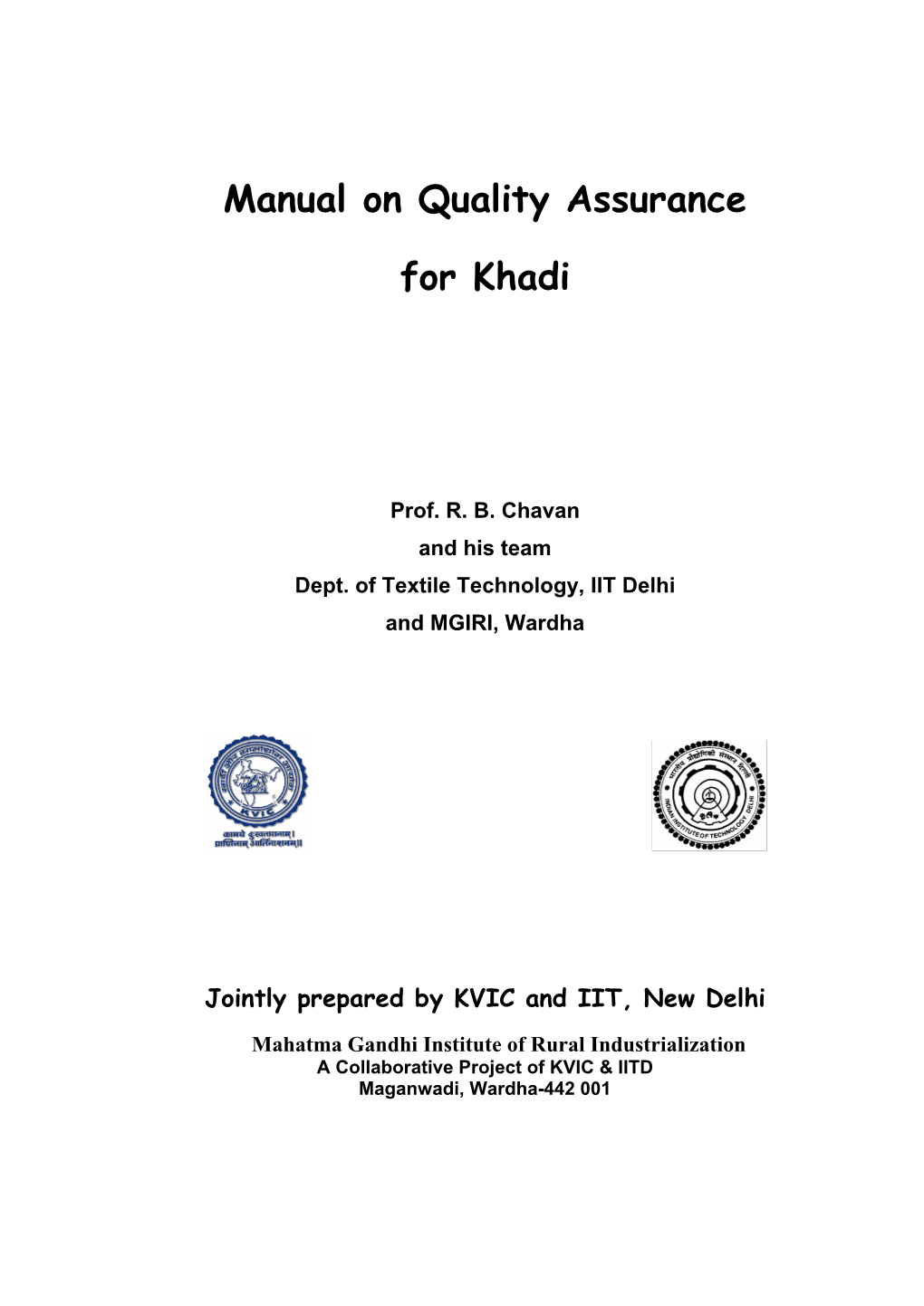
Load more
Recommended publications
-
Method of Operating an Electronic Dobby Loom
Patentamt JEuropaischesEuropean Patent Office Office europeen des brevets © Publication number : 0 466 636 A1 @ EUROPEAN PATENT APPLICATION @ Application number: 91810415.9 @ Int. CI.5: D03C 1/14, D03D 51/00 (22) Date of filing : 31.05.91 (30) Priority : 04.06.90 JP 144346/90 (72) Inventor : Honda, Hiroshi, c/o Kabushiki Kaisha Toyoda Jidoshokki Seisakusho, 1, Toyoda-cho @ Date of publication of application : 2-chome 15.01.92 Bulletin 92/03 Kariya-shi, Aichi-ken (JP) @ Designated Contracting States : @ Representative : Hammer, Bruno BE DE FR IT c/o Gebrueder Sulzer AG KSR/Patente/0007, Postfach CH-8401 Winterthur (CH) (R) Applicant : Kabushiki Kaisha Toyoda Jidoshokki Seisakusho 1, Toyoda-cho 2-chome, Kariya-shi Aichi-ken 448 (JP) (54) Method of operating an electronic dobby loom. (57) According to the method the heddle frames (5) of the loom are selected and assigned to a plurality of groups. In each of a plurality of picking cycles a group of heddle frames (5) is moved and leveled into the weaving position (up arrow, down arrow) according to the weaving pattern to be woven. During this operation the loom is preferably run at lower speed compared to the selected normal picking speed. This allows for avoiding excessive load of the drive motor and further remarkably reduces warp yarn breakes. The method thus provides for remarkably improved start up conditions of looms. < CO CO CO CO CO "<t o Q_ LU Jouve, 18, rue Saint-Denis, 75001 PARIS ' 1 g. 1 fig. I A) _ , , ncK Number H. F NO. , 2 3 | - 5 OFF — 6-10 OFF — — OFF *- — *- L I 2 3 4 5 6 7 b y IU II ic lOi'riJiD hi. -
Study on Improving the Production Rate by Rapier Looms in Textile Industry Aby Chummar, Soni Kuriakose, George Mathew
ISSN: 2277-3754 ISO 9001:2008 Certified International Journal of Engineering and Innovative Technology (IJEIT) Volume 2, Issue 7, January 2013 Study on Improving the Production Rate by Rapier Looms in Textile Industry Aby Chummar, Soni Kuriakose, George Mathew the company. It is mainly manufactured by the shuttle looms. Abstract— In India the textile industry is growing very fast. Conventional shuttle looms are mainly used during the Most of the earlier established textile industries are using weaving process in the industry. All these shuttle looms are conventional shuttle looms for the production of the cloth. But the too old. In these present conventional shuttle looms, it is advancement in the technology made the textile industry more competitive. The effective usage of the new methods of the necessary to pass a shuttle weighing around half a kilogram weaving technology, which is more energy efficient, makes the through the warp shed to insert a length of weft yarn which production more economical. It is found out that the usage of the weighs only few grams. The shuttle has to be accelerated conventional looms badly affects the cloth production. This study rapidly at the starting of picking cycle and also to be focuses on identifying the problems associated with the low decelerated, stopped abruptly at the opposite end. This production by the shuttle loom and suggesting suitable methods process creates heavy noise and shock and consumes by which these problems can be reduced. considerable energy. Beat-up is done by slay motion which again weighs a few hundred kilograms. The wear life of the Index Terms—Greige Fabric Picks, Rapier Loom, Shuttle Loom. -
History of Weaving
A Woven World Teaching Youth Diversity through Weaving Joanne Roueche, CFCS USU Extension, Davis County History of Weaving •Archaeologists believe that basket weaving and weaving were the earliest crafts •Weaving in Mesopotamia in Turkey dates back as far as 7000 to 8000 BC •Sealed tombs in Egypt have evidence of fabrics dating back as far as 5000 BC •Evidence of a weavers workshop found in an Egyptian tomb 19th Century BC •Ancient fabrics from the Hebrew world date back as early as 3000 BC History of Weaving (continued) •China – the discovery of silk in the 27th Century BCE •Swiss Lake Dwellers – woven linen scraps 5000 BCE •Early Peruvian textiles and weaving tools dating back to 5800 BCE •The Zapotecs were weaving in Oaxaca as early as 500 BC Weavers From Around the World Master weaver Jose Cotacachi in his studio in Peguche, Ecuador. Jose’s studio is about two and a half miles from Otavalo. Weavers making and selling their fabrics at the Saturday market in Otavalo, Ecuador. This tiny cottage on the small island of Mederia, Portugal is filled with spinning and weaving. Weavers selling their fabrics at an open market in Egypt. The painting depicts making linen cloth, spinning and warping a loom. (Painting in the Royal Ontario Museum.) Malaysian weavers making traditional Songket – fabric woven with gold or silver weft threads. A local Tarahumara Indian weaving on a small backstrap loom at the train station in Los Mochis. Weavers In Our Neighborhood George Aposhian learned Armenian pile carpets from his father and grandparents who immigrated to Salt Lake City in the early 1900’s. -
The Social Life of Khadi: Gandhi's Experiments with the Indian
The Social Life of Khadi: Gandhi’s Experiments with the Indian Economy, c. 1915-1965 by Leslie Hempson A dissertation submitted in partial fulfillment of the requirements for the degree of Doctor of Philosophy (History) in the University of Michigan 2018 Doctoral Committee: Associate Professor Farina Mir, Co-Chair Professor Mrinalini Sinha, Co-Chair Associate Professor William Glover Associate Professor Matthew Hull Leslie Hempson [email protected] ORCID iD: 0000-0001-5195-1605 © Leslie Hempson 2018 DEDICATION To my parents, whose love and support has accompanied me every step of the way ii TABLE OF CONTENTS DEDICATION ii LIST OF FIGURES iv LIST OF ACRONYMS v GLOSSARY OF KEY TERMS vi ABSTRACT vii INTRODUCTION 1 CHAPTER 1: THE AGRO-INDUSTRIAL DIVIDE 23 CHAPTER 2: ACCOUNTING FOR BUSINESS 53 CHAPTER 3: WRITING THE ECONOMY 89 CHAPTER 4: SPINNING EMPLOYMENT 130 CONCLUSION 179 APPENDIX: WEIGHTS AND MEASURES 183 BIBLIOGRAPHY 184 iii LIST OF FIGURES FIGURE 2.1 Advertisement for a list of businesses certified by AISA 59 3.1 A set of scales with coins used as weights 117 4.1 The ambar charkha in three-part form 146 4.2 Illustration from a KVIC album showing Mother India cradling the ambar 150 charkha 4.3 Illustration from a KVIC album showing giant hand cradling the ambar charkha 151 4.4 Illustration from a KVIC album showing the ambar charkha on a pedestal with 152 a modified version of the motto of the Indian republic on the front 4.5 Illustration from a KVIC album tracing the charkha to Mohenjo Daro 158 4.6 Illustration from a KVIC album tracing -
Weaving Technology: Advances and Challenges Ii
Volume3, Issue 1, Summer 2003 WEAVING TECHNOLOGY: ADVANCES AND CHALLENGES II Abdelfattah M. Seyam College of Textiles, N. C. State University Raleigh, NC, USA ABSTRACT This paper reviews the recent advances in weaving industry and addresses the challenges that face the weaving industry. The paper sheds the light on how the weaving machine manufacturers and woven fabric producers might strengthen the weaving industry by further advance the technology and taking advantages of the current and new advances in weaving technologies. KEYWORDS: Weaving, Automation, Jacquard, Pattern Change. INTRODUCTION and how the weaving machine manufacturers and woven fabric producers Recently weaving machine producers might strengthen the weaving industry by introduced to the woven fabric further advance the technology and taking manufacturers a sizeable number of advantages of the current and new advances technological advances. Examples of such in weaving technologies and supporting advances are higher speeds than seen before, systems. a higher level of automation, a new Jacquard shedding concept, waste reduction, and on- ADVANCES IN WEAVING line quality monitoring. These advances may enable the developed nations to drastically Weaving Speeds lower the labor cost and may be able to At recent machinery shows (ITMA’ 99, compete in the commodity fabric markets. ATME-I’ 2001), weaving machine Despite these significant development in manufacturers showed a broad range of weaving, weavers in the developed and machines with higher speed and rate of developing nations are faced with serious filling insertion (RFI) than seen before. The competition from other fabric forming fabric quality, which is significantly systems such as needlepunching and impacted by efficiency, is a must for the hydroentanglement nonwoven technologies. -
Textile Calendering Solutions for Every Application
Textile calendering Solutions for every application www.andritz.com/textile Tradition in innovation Textile calendering is part of our DNA Be it home textiles, technical textiles or traditional textiles, ANDRITZ Küsters CONTENTS offers exactly the right textile calender solution targeting your needs in an ever more demanding market. With more than 150 years of experience in textile calendering, Tradition and expertise 03 it is not just our daily business. It is our passion – and part of our DNA. Textile calenders 04 Experience and expertise The right partner for textile solutions Core competences With more than 3,500 textile calenders Our portfolio includes complete system ANDRITZ Küsters is currently the only Multicovering technology 13 delivered, ANDRITZ Küsters is a well- solutions, single units, rebuilds, automation supplier that can offer three different known brand that stands for top perfor- systems, and complete life-cycle services. deflection-controlled roll techno logies from teXmaster control system 13 mance, reliability, flexibility, and proven These are designed to meet your needs in one source. The technology set-up of the technology for every application. Gloss, an ever more demanding market. Together S-Roll, HyCon Roll, and Xpro Roll is our Defl ection-controlled rolls 14 density, smoothness, soft handle, silk we can design and innovate new technolo- core competence, and all rolls are manu- finish, metallic printing, embossing, lami- gies to create fi rst-class textiles for any end factured and tested at our facility in Krefeld, Heating systems 17 nating, or any other finish can be applied use. Our top-quality technical center offers Germany, before delivery. -
I Was Tempted by a Pretty Coloured Muslin
“I was tempted by a pretty y y coloured muslin”: Jane Austen and the Art of Being Fashionable MARY HAFNER-LANEY Mary Hafner-Laney is an historic costumer. Using her thirty-plus years of trial-and-error experience, she has given presentations and workshops on how women of the past dressed to historical societies, literary groups, and costuming and re-enactment organizations. She is retired from the State of Washington . E E plucked that first leaf o ff the fig tree in the Garden of Eden and decided green was her color, women of all times and all places have been interested in fashion and in being fashionable. Jane Austen herself wrote , “I beleive Finery must have it” (23 September 1813) , and in Northanger Abbey we read that Mrs. Allen cannot begin to enjoy the delights of Bath until she “was provided with a dress of the newest fashion” (20). Whether a woman was like Jane and “so tired & ashamed of half my present stock that I even blush at the sight of the wardrobe which contains them ” (25 December 1798) or like the two Miss Beauforts in Sanditon , who required “six new Dresses each for a three days visit” (Minor Works 421), dress was a problem to be solved. There were no big-name designers with models to show o ff their creations. There was no Project Runway . There were no department stores or clothing empori - ums where one could browse for and purchase garments of the latest fashion. How did a woman achieve a stylish appearance? Just as we have Vogue , Elle and In Style magazines to keep us up to date on the most current styles, women of the Regency era had The Ladies Magazine , La Belle Assemblée , Le Beau Monde , The Gallery of Fashion , and a host of other publications (Decker) . -
A Comparison of the Patterns Formed by Primary Textile Structures and Their Photographic Abstraction
Rochester Institute of Technology RIT Scholar Works Theses 9-22-1976 A comparison of the patterns formed by primary textile structures and their photographic abstraction Pamela Perlman Follow this and additional works at: https://scholarworks.rit.edu/theses Recommended Citation Perlman, Pamela, "A comparison of the patterns formed by primary textile structures and their photographic abstraction" (1976). Thesis. Rochester Institute of Technology. Accessed from This Thesis is brought to you for free and open access by RIT Scholar Works. It has been accepted for inclusion in Theses by an authorized administrator of RIT Scholar Works. For more information, please contact [email protected]. Thesis Proposal for the Master of Fine Arts De gree Collee;e of Fine and Applj_ed .Arts Rochester Institute of Technology Title: A Comparison of the Fatterns Formed by Primary Textile structures and their Phot ographic Abstraction Submitted by: Pamela Anne Perlman Date: September 22, 1976 Thesis Co mm it te~: Nr . Donald Du jnowski I-Ir. I,l az Lenderman hr. Ed 1iiller Depart~ental Approval : Date :-:--g---li6~-r-71-b-r-/ ----- ---------~~~~~'~~~r------------------------- Chairman of the School for American Craftsme:l: ___-r-----,,~---- ____ Da t e : ---.:...,'?7~JtJ--J7~i,-=-~ ___ _ Chairr.ian of the Gr3.duate Prog:rarn: ------------------------~/~~/~. --- Date: ___________________~ /~~,~~;j~~, (~/_' ~i~/~: 7 / Final Committee Decision: Date: ----------------------- Thesis Proposal for the Master of Fine Arts Degree College of Fine and Applied Arts Rochester Institute of Technology Title: A Comparison of the Patterns Frmed by Primary Textile Structures and their Photographic Abstraction My concern in textiles is with structure and materials. I v/ould like to do v/all hangings based on primary textile structures such as knotting, looping, pile, balanced weaves, and tapestry. -
Suicide Deaths and Quality of Indian Cotton: Perspectives from History of Technology and Khadi Movement Author(S): C
Suicide Deaths and Quality of Indian Cotton: Perspectives from History of Technology and Khadi Movement Author(s): C. Shambu Prasad Source: Economic and Political Weekly, Vol. 34, No. 5 (Jan. 30 - Feb. 5, 1999), pp. PE12-PE21 Published by: Economic and Political Weekly Stable URL: http://www.jstor.org/stable/4407604 . Accessed: 13/06/2014 06:16 Your use of the JSTOR archive indicates your acceptance of the Terms & Conditions of Use, available at . http://www.jstor.org/page/info/about/policies/terms.jsp . JSTOR is a not-for-profit service that helps scholars, researchers, and students discover, use, and build upon a wide range of content in a trusted digital archive. We use information technology and tools to increase productivity and facilitate new forms of scholarship. For more information about JSTOR, please contact [email protected]. Economic and Political Weekly is collaborating with JSTOR to digitize, preserve and extend access to Economic and Political Weekly. http://www.jstor.org This content downloaded from 130.92.9.57 on Fri, 13 Jun 2014 06:16:17 AM All use subject to JSTOR Terms and Conditions Suicide Deaths and Quality of Indian Cotton Perspectives from History of Technology and Khadi Movement C Shambu Prasad The suicide deaths of farmers is a failure of agricultural science and the historical nature of the crisis needs to be appreciated. This paper seeks to retrace the route by which the present connections between Indian cotton and the mechanised textile industry were first established, a direction that has led to the present crisis on the fields of the cotton jflrmers. -
Filage Et Tissage (2)
FILAGE ET TISSAGE (2) LINGUA È TECNICA LEXIQUE Français-Corse Réalisé par : ANTONDUMENICU MONTI Et MARIE-CHARLES ZUCCARELLI Traduzzione inglese d'Anghjula Maria Carbuccia Spinning and weaving ADECEC CERVIONI 1980 accrochage : azzingatura, azzinghera, azzinghime / warp and woof interlinking accrocher : azzingà / to interlink (warp and woof) aiguille : acu / needle aiguillée : curata, podana, acata, acughjata / needleful alépine : aleppina / bombazine alpaga : alpagà / alpaca alun : (teinture) : alume / alum alunage : alumatura / aluming aluner : alumà amidon : su(g)u / starch anacoste : arscottu / double-milled, woollen cloth apprêt (pour les étoffes) : approntu / finishing apprêter : appruntà / to finish armoisin : ermisinu / sarcenet armure (de tissage) : armatura.- fundamentale, semplice, cumposa, fattizia, dirivata, di fantasia, alluciata, guardrata, diritta (toile), à spichjoli (en losanges), à filetti (sergé), ) spighe (chevrons) / weave - foundation, simple, combined, sham, derived, fancy, open-work, square, plain, lozenge-shaped, serge-like; chevron pattern aspe ou asple : aspa / silk winder assouplir (les chemises et draps de lin) : derozà / to supple, to smooth attacher : attaccà, appiccià, alliacciulà / to tie baignage : bagnatura, bagnime / dye-bath, soaking baigner : bagnà / to soak bain : striscia, fascia, banda / dye-bath bande : striscia, fascia, banda / strip barège : baresgiu / light woollen cloth, barege bariolage : frisgiulime / medley of colours, motley pattern barioler : frisgiulà, frisgià, framisgià / to paint or -
Apparel-Online-India-January-1-15
2 Apparel Online India 4 Apparel Online India | JANUARY 1-15, 2016 | www.apparelresources.com Apparel Online India 5 Apparel Online India 6 7 Apparel Online India 8 Apparel Online India 9 Apparel Online India VOL. XVIII Issue 19 Editor-in-Chief DEEPAK MOHINDRA Editor ILA SAXENA Copy Editor January 1-15, 2016 VEERESHWAR SOBTI CONTENTS Asst. Copy Editor SAHIL SEHGAL Asst. Editor-News DHEERAJ TAGRA Asst. Editor NEHA CHHETRI Sr. Correspondent-Textiles SANJOGEETA OJHA Sr. Correspondent-Fashion KALITA LAMBA Sr. Executive-Advertising D K CHUGH Creative Team RAJ KUMAR CHAHAL PEEUSH JAUHARI SATYAPAL BISHT Photo Editor SUMIT THARAN Subscription Enquiry RANI MAHENDRU 011-47390000 25 30 50 52 69 Operation Director MAYANK MOHINDRA 09810611487 Publisher & Managing Director BusinessStrategies RENU MOHINDRA GLOBAL STRATEGIES FOR 09810058986, 9810438653 INTERNATIONAL BUSINESS 20 Head Office Apparel Resources Pvt. Ltd. B-32, South Extension-I, New Delhi-110 049 Phone: 91-11-47390000 SpecialFeatures E-mail: [email protected] UPFRONT INDUSTRY TAKING LEAD Web associate: www.apparelresources.com 24 Apparel Online contact: 91-11-47390000 [email protected] [email protected] BuyersSpeak Printing BUYERS BAT FOR CHANGE WITH TARA ART PRINTERS PVT. LTD. SUGGESTIONS 26 B-4, Hans Bhawan, B.S. Zafar Marg, New Delhi-110002 Tel: 23378626, 23379686 ---------------------------------------------------------- HubsUpdate SUBSCRIPTION FORM CENTRES UNDER THE SPOTLIGHT Yes, I wish to subscribe to Apparel Online for 29 BY REGULAR MAIL India Rs. -
DOUBLE WEAVE on the KNITTERS LOOM
DOUBLE WEAVEon the KNITTERS LOOM Create this beautiful double weave shuttle holder on a Knitters Loom with double heddle kit. Double Weave on the Rigid Heddle or Knitters Loom Double Weave and Brooks Bouquet on the black pair down and the white pair up Rigid Heddle or Knitters Loom using the 12. Take 1 white end from the pair of white Second Heddle Kit. ends (choose the one that is to the top or left of the pair) and thread through the eye to the You will need left Loom: Rigid Heddle Loom 40cm (16ins) or Knitters Loom 30cm (12ins) Reed: 2 x 40/10cm (10dpi) Warp & Weft Yarns: Ashford McKenzie 4 ply (100% Merino; 385m/421yds;100gms net) White 5. Place the reed in the up position 1 ball, Black 1 ball 6. Place the second reed in the front heddle Other: Two pick-up sticks (or shuttles) rest position Warping 1. Place one reed in the back heddle rest position 2.Excluding the first three and last three slots, warp across reed in the normal way but place 13. Continue across the reed two loops in each slot (one loop of black and 14. Check there are no crosses between the one of white) reeds. If the ends are crossed remove and repeat step 11 and 12. Your threading will look 7. Drape all ends from the back reed over the front reed (this will help to make the threading easier) 8. Take the first group of 4 ends (2 white ends and 1 black end from the slot and 1 end from the eye to the right and thread all 4 ends through the slot directly in front in the front reed 3.