Recumbent Vehicle Design and Entry for the 2020 ASME Human-Powered Vehicle Challenge a Technical Report Submitt
Total Page:16
File Type:pdf, Size:1020Kb
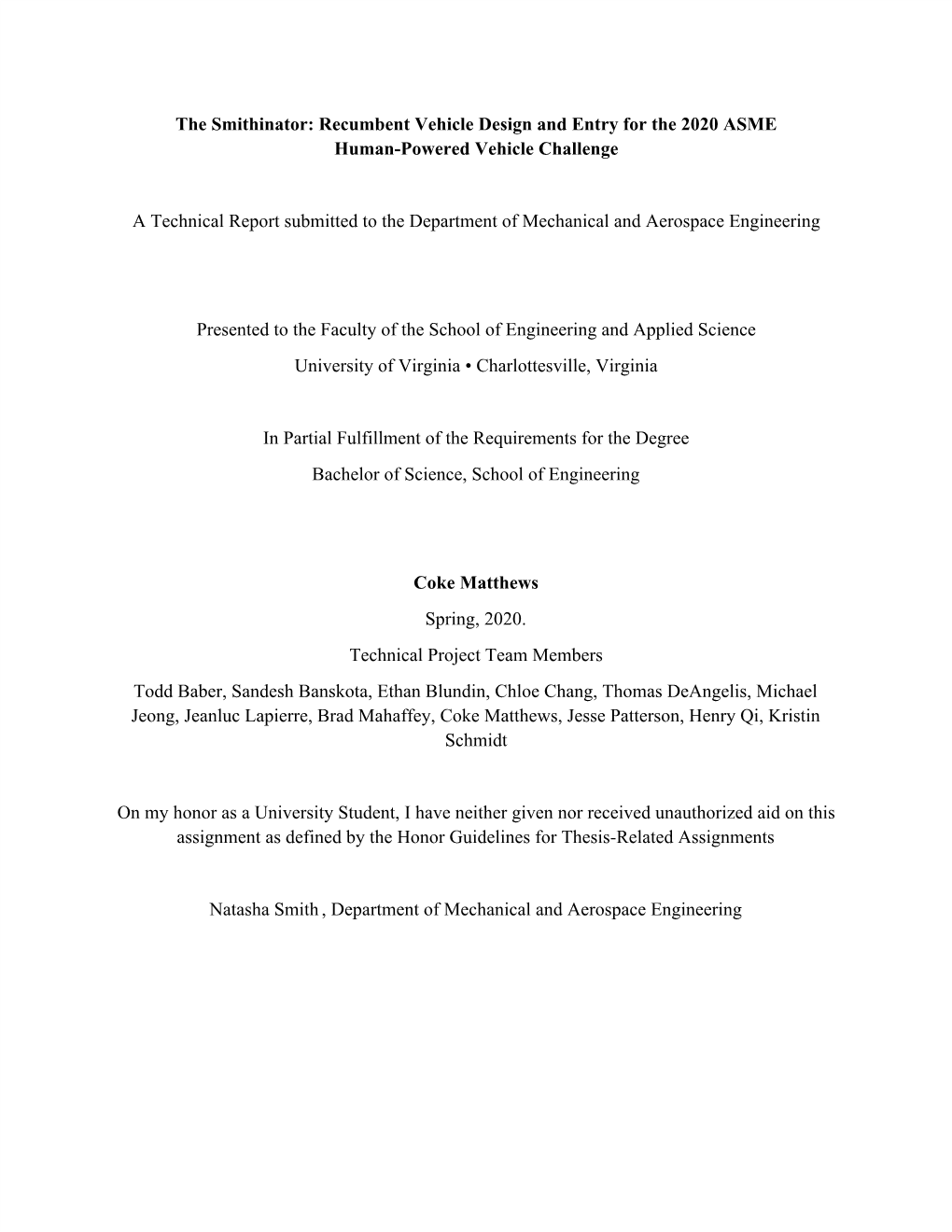
Load more
Recommended publications
-
Australian Adaptive Mountain Biking Guidelines
AUSTRALIAN ADAPTIVE MOUNTAIN BIKING GUIDELINES A detailed guide to help land managers, trail builders, event directors, mountain bike clubs, charities and associations develop inclusive mountain bike trails, events and programs for people with disabilities in Australia. Australian Adaptive Mountain Biking Guidelines AUSTRALIAN ADAPTIVE MOUNTAIN BIKING GUIDELINES Version 1.0.0 Proudly supported and published by: Mountain Bike Australia Queensland Government Acknowledgements: The authors of this document acknowledge the contribution of volunteers in the preparation and development of the document’s content. The authors would also like to extend their gratitude to the following contributors: Denise Cox (Mountain Bike Australia), Talya Wainstein, Clinton Beddall, Richard King, Cameron McGavin and Ivan Svenson (Kalamunda Mountain Bike Collective). Photography by Kerry Halford, Travis Deane, Emily Dimozantos, Matt Devlin and Leanne Rees. Editing and Graphics by Ripe Designs Graphics by Richard Morrell COPYRIGHT 2018: © BREAK THE BOUNDARY INC. This document is copyright protected apart from any use as permitted under the Australian Copyright Act 1968, no part may be reproduced by any process without prior written permission from the Author. Requests and inquiries concerning reproduction should be addressed to the Author at www.breaktheboundary.com Fair-use policy By using this document, the user agrees to this fair-use policy. This document is a paid publication and as such only for use by the said paying person, members and associates of mountain bike and adaptive sporting communities, clubs, groups or associations. Distribution or duplication is strictly prohibited without the written consent of the Author. The license includes online access to the latest revision of this document and resources at no additional cost and can be obtained from: www.breaktheboundary.com Hard copies can be obtained from: www.mtba.asn.au 3 Australian Adaptive Mountain Biking Guidelines Australian Adaptive Mountain Biking Guidelines CONTENTS 1. -
Road Test: Burley Canto
Issue No. 71 Recumbent Sept./ Oct. 2002 CyclistNews The New ZOX Tandem What’s Inside 2 Editorial License 19 Road Test: Burley Canto 4 Recumbent News 22 Rec-Tech: TerraCycle Fold- Forward Stem 6 Letters 24 On Getting ’Bent 9 Road Test: Penninger Trike 28 Rec-Equipment: Burley Nomad 15 Road Test: Burley Hepcat Trailer Editorial License if it was OK. I then told Jeff about my current test recumbent. Now, Jeff isn’t exactly the world’s biggest recumbent fan. He has a 50-year-old wooden sailboat that he owns (or perhaps owns him) and sails, but he does ride his mountain bike around town for transportation. He likes to tease me about my fleet of weird bikes. But when I we walked into the door of PT Cycles and he saw the Greenspeed GTT tandem tricycle, his eyes lit up. He decided to ride the tandem in the parade with his daughter Emma, who is six. We decided that Jeff needed a GTT piloting course. We rolled the GTT out the door. I told Jeff to hang on, and we were ripping down Water Street. Jeff reminded me that he needed to unlock his Stumpjumper so Amy could ride it home, so I pulled a quick U-turn in the middle of Water Street and headed back into town. Jeff and Emma Kelety ride the Greenspeed GTT in the Port Townsend Once that duty was taken care of, we took Rhody Parade (photo by Deborah Carroll) a left on Water as we started Jeff on a crash course of Tandem Trike Piloting 101. -
! Ch Ro=~ Check of $2,000
The Recumbent Cyclist 9 S.F. TO L.A. LIGHTNING-FAST On April 28, 1991 Pete Penseyres took the Lightning X-2 slightly furrowed brow. out for a Sunday spin, shattering the San Francisco to Los Angeles HPV record by more than three hours in the Pete was actually shooting for a 17 hour 45 minute time. He process and making a strong would have easily done opening bid for the $5,000 this had he not fallen at a JohnPaulMitchellSystems' stoplight before he could top prize. Pete started his get a foot down to the quad-centuryjaun tat about ground. Occuring early 3:30 a.m. at San Francisco in the ride, the fall dam City Hall and pulled into aged the Kevlar fairing's Los Angeles City Hall at "landing gear" flaps used 9:34 p.m., 18 hours and 4 to put his feet down. This minutes later. The Light forced him to ride most of ning X-2 was equipped for the distance with the the run with a powerful doors flapping wide open Night Sun headlight, and in a decidedly non-aero the heavy battery had to dynamic configuration, at light a tail light and tum least for the one-time 64 signals as well. Riding most m.p.h. X-2. When he fell, of the way on Interstate 5, Pete was penalized 30 Pete pedalled the over minutes for receiving as weight bicycle up Pacheco sistance from a concerned Pass and Tejon Pass to an onlookerfrumored to be a altitude of 4,144 feet, seemingly effortlessly except for a certain "T. -
Richard's 21St Century Bicycl E 'The Best Guide to Bikes and Cycling Ever Book Published' Bike Events
Richard's 21st Century Bicycl e 'The best guide to bikes and cycling ever Book published' Bike Events RICHARD BALLANTINE This book is dedicated to Samuel Joseph Melville, hero. First published 1975 by Pan Books This revised and updated edition first published 2000 by Pan Books an imprint of Macmillan Publishers Ltd 25 Eccleston Place, London SW1W 9NF Basingstoke and Oxford Associated companies throughout the world www.macmillan.com ISBN 0 330 37717 5 Copyright © Richard Ballantine 1975, 1989, 2000 The right of Richard Ballantine to be identified as the author of this work has been asserted by him in accordance with the Copyright, Designs and Patents Act 1988. • All rights reserved. No part of this publication may be reproduced, stored in or introduced into a retrieval system, or transmitted, in any form, or by any means (electronic, mechanical, photocopying, recording or otherwise) without the prior written permission of the publisher. Any person who does any unauthorized act in relation to this publication may be liable to criminal prosecution and civil claims for damages. 1 3 5 7 9 8 6 4 2 A CIP catalogue record for this book is available from the British Library. • Printed and bound in Great Britain by The Bath Press Ltd, Bath This book is sold subject to the condition that it shall nor, by way of trade or otherwise, be lent, re-sold, hired out, or otherwise circulated without the publisher's prior consent in any form of binding or cover other than that in which it is published and without a similar condition including this condition being imposed on the subsequent purchaser. -
The Lightning P-38 Recumbent 2 the Recumbent Cyclist the LIGHTNING P-38 RECUMBENT by Robert J
Cover Story: The Lightning P-38 Recumbent 2 The Recumbent Cyclist THE LIGHTNING P-38 RECUMBENT by Robert J. Bryant When the subject of high performance recumbents is waterbottle mounts, a pump peg and dropout eyelets. The presented, the Lightning P-38 is sure to come to mind. Lightning's paint is among the finest found on any recum- Considering all of the recumbents currently marketed in bent. It is electrostatic baked on urethane powder and the USA only a few are really built for performance and comes in red, or royal blue. This finish is extremely durable only two designs really have the speed records to back up and looks great. We have found powdercoat much more the claims. These qualities are not an after thought with durable than lmron, but not as glossy a finish. The the Lightning, but the purpose in which the bike is de- difference becomes apparent when the bike is a year or so signed. It is apparent through our interviews with RBCA old and the Powdercoat still looks new. The new aluminum member/ Lightning owners that they know what they want seat frame is anodized silver and much lighter than the in a recumbent bicycle. Lightning owners seem to be previous chro-molly seat frame. among the most loyal owners of any brand of recumbent that we've tested. When Tim shipped the test bike he also included some of Lightning's new custom cast lugs. The lugs were part of the AEROSPACE BEGINNINGS new seat design. The heat treated anodized aluminum Tim Brummer and Company build the Lightnings in seat bolts onto the lugs at the frame and to the seat stays Lompoc California. -
January 2021 - Diy Plans Catalog
JANUARY 2021 - DIY PLANS CATALOG Anyone Can Do This! Our DIY Plans detail every aspect of the building process using easy to follow instructions with high resolution pictures and diagrams. Even if this is your first attempt at building something yourself, you will be able to succeed with our plans, as no previous expertise is assumed. Detailed Plans – Instant Download! We use real build photos and detailed diagrams instead of complex drawings, so anyone with a desire to build can succeed. Our bike and trike plans are not engineering blueprints, and do not call for hard-to-find parts or expensive tools. DIY Means Building Yourself a Better Life. Unleash your creativity, and turn your drawing board ideas into reality. You don't need a fancy garage full of tools or an unlimited budget to build anything shown on our DIY site, you just need the desire to do it yourself. Take pride in your home built projects, and create something completely unique from nothing more than recycled parts. AURORA DIY SUSPENSION TRIKE PLAN The Aurora Delta Recumbent Trike merges speed, handling, and comfort into one great looking ride! With under seat steering, and rear suspension, you will be enjoying your laid-back country cruises in pure comfort and style. Of course, The Aurora DIY Trike is also a hot performer, and will get you around as fast as your leg powered engine feels like working. This DIY Plan Contains 198 Pages and 203 Photos. Click above for more information. WARRIOR LOW RACER TADPOLE TRIKE PLAN The Warrior is one fast and great looking DIY Tadpole Trike that you can make using only basic tools and parts. -
Design and Analysis of a Human Powered Vehicle's
Design and Analysis of a Human Powered Vehicle’s Frame and Seat Assistance Mechanism by Bradley S. Helm A Report Submitted to the Faculty of the Milwaukee School of Engineering in Partial Fulfillment of the Requirements for the Degree of Master of Science in Engineering Milwaukee, Wisconsin February 2017 2 ABSTRACT The objective of this project was to complete the redesign and analysis of a human powered vehicle (HPV) called the Heliocycle, which is an existing tricycle (also referred to as trike). The Heliocycle was a Senior Design Project that was completed at the Milwaukee School of Engineering (MSOE) by Bradley Helm, Kelly Bauserman, Michael Caelwaerts, and Nicholas Weis from September 2014 through May 2015. Since the Heliocycle’s debut in May 2015, it has been showcased and ridden, gaining exposure and feedback. In addition, a company (Omnium Cycles, LLC) was formed around the Heliocycle, and the Heliocycle received a provisional patent. This redesign was completed to improve the original design, based on knowledge gained through fabricating the initial prototype and feedback gathered during showcases. A brief market analysis determined a need for this trike and defined the target audience who would be most likely to buy and use this product. In order to complete this project, a five-stage design process was followed. Throughout these stages, this project involved engineering design and analysis, which included the selection of materials, mechanics of materials, and finite element analysis, as well as some minor business aspects. The analysis was completed to confirm the design would be safe and withstand the stated maximum load established during the design. -
Inclusion/Adaptive Recreation Office 1301 Valley Road Reno, NV 89512 (775) 333-7765 Reno.Gov/Adaptive
EQUIPMENT RENTAL PROGRAM Our adaptive recreation equipment is available for rent. Renting makes it affordable for participants to try before they buy, be a weekend warrior, gain skills, and be involved in more than one sport. Please note -- A minimum of 48 hours advance notice is preferred. Equipment inventory is limited and an appointment for proper fit is required. Inclusion/Adaptive Recreation Office 1301 Valley Road Reno, NV 89512 (775) 333-7765 Reno.Gov/Adaptive FEES & AGREEMENTS • The rental fee must be paid in advance. The daily fee is $15, weekend fee is $50 and full-week fee is $75. INCLUSION • A valid credit card is required. Its image will be CITY OF RENO held to make repairs on damaged, lost or stolen equipment, if necessary. The renter is responsible for replacement and repair costs. • The renter agrees to be the sole authorized user of ADAPTIVE the equipment. • A Release Agreement will be read and signed prior to leaving the premises. The Release Agreement EQUIPMENT requires the signature of either a parent or legal guardian if the renter is under the age of 18 or not their own guardian. RENTAL • The renter must be at least one-year post injury and must be their own legal guardian if over the age of 18. Equipment provided by a grant from the Craig H. Neilsen Foundation 1 7 1 CATRIKE RECUMBENT TRIKES 8 TOP END FORCE HANDCYCLE Sizes Available: Adult | Models: Villager, Road, 700 Sizes Available: Adult | Models: Force R, Gold, Force 3 The Catrike is a premium grade Recumbent trike suited for all Quad Elite, Quad Exelerator day touring and spirited rides. -
The Development of Modern Recumbent Bicycles
8 THE DEVELOPMENT OF MODERN RECUMBENT BICYCLES David Gordon Wilson A recumbent pedaling position is one having the tions such as front-wheel drive and front-steering pedaling axis substantially in front of the rider. Fur recumbents are introduced. ther recumbents of the type where the rider is in a Recumbent bicycles have had many revivals. A sitting position may be designated as semirecum recumbent called the Velocar disturbed the conven bent and those where the rider is lying down, as tional bicycling world in the 1933 to 1935 period full y recumbent. For this chapter, the boundary be because it was used to topple most existing bicycle tween semirecumbent and fully recumbent is set records, and it was ruled "not a bicycle." The latest as a seat-back angle of 45° with the horizontal. revival of interest in recumbents has come about Abbott defines four possible fully recumbent posi because of the formation of the IHPVA. Faired re tions: the supine position with face upward; the cumbent bicycles currently hold most of the world prone position with face down; and on the right or HPV records. Moreover, often the same recumbent left side, the right or left decubitus positions bicycles that have won the Speed Championships (Abbott, 1988). In general, full recumbents are used have also been awarded practical-vehicle prizes. only for speed-record attempts, because of the The recumbent bicycle, therefore, could have very position's inherent problems for both seeing and wide application. being seen. Technically speaking, the first pedaled bicycles were "recumbents," but this chapter briefly traces the development just of geared recumbent bicycles, from the first known examples that ap The Evolution of Safety Bicycles ~ peared in 1895 to the Cheetah of 1992. -
Utility and Style: a Cargo E-Bicycle for the Waste Reduction and Resource Awareness Program
Utility and Style: A Cargo E-Bicycle for the Waste Reduction and Resource Awareness Program Austen Thibault, [email protected] Student: Biology: Ecology & Biodiversity (Fall 2019) Compost Operator at WRRAP Jay Ryan, [email protected] Student: Environmental Science and Management: Ecological Restoration (Spring 2019) Bicycle Learning Center Director at WRRAP Morgan King, [email protected] Staff: Climate Action Analyst The Waste Reduction and Resource Awareness Program (WRRAP) is a student-led program at Humboldt State University which embodies the university’s culture of sustainability while providing numerous free services to students and employees. But we have a problem. WRRAP does not have a consistent way to transport its materials, causing a bottleneck effect on operations of every branch of WRRAP. For instance, Compost Squad has had to delay or even cancel compost pickups across campus due to the unavailability or failure of the current transportation borrowed from Facilities. The Zero Waste branch struggles to find suitable locations for clothing swap events due to the limitation of having to manually haul all clothing to and from our base of operations at the Warren House. Therefore, to gain sustainable transportation independence and increase the success of our mission, we submit the proposal to purchase a cargo electric bicycle for WRRAP. This e-bike would solve transportation issues, while also serving as a highly visible and attention-grabbing presence on campus, encouraging conversation and participation around sustainable practices. Further, this purchase synergizes with the recent absorption of the Bicycle Learning Center under WRRAP’s umbrella. The Bicycle Learning Center would use this e-bike as an educational tool for students and could assist in its maintenance. -
Handicap Accessible Bicycle
Handicap Accessible Bicycle BME 200/300 Preliminary Report | October 19, 2016 TEAM MEMBERS Team Leader: Morgan Kemp [email protected] Communicator:Tianna Garcia [email protected] BSAC:Shelby Mochal [email protected] BWIG: Will Fox [email protected] BPAG:Grant Karlson Ellifson [email protected] ADVISOR Dr. Edward Bersu [email protected] Department of Biomedical Engineering University of Wisconsin-Madison CLIENT Mr. Ted Elias [email protected] 1 ABSTRACT The life of a TBI (traumatic brain injury) patient is very limited in extracurricular activities such as a bike ride. Although there are adult sized attachments and recombinant bikes on the market, none of them fit the need for that of an adult that lacks mobility, but still able to participate in the event of riding a bike. These current designs although an option for just a passive ride, do not provide security required of a traumatic brain injury patient and are not cost effective either. Four potential designs were proposed to create a safe, interactive, and cost effective design for a disabled adult. The final design is composed of steel rods welded in a tricycle formation that attaches to the seat of a standard bicycle. This three wheeled attachment includes features of arm bars, shock absorbent tires, and a separate drivetrain allowing rehabilitation and participation in the event. 2 Table of Contents Abstract 2 Introduction 4 Motivation 4 Problem 4 Background 4-5 Traumatic Brain Injuries 4 Handicapped Accessible Bicycles 4 Design Specifications 4 Preliminary Designs 5-7 Design One – Trailer 5 Design Two – Sidecar 6 Design Three – Tandem 6 Design Four- Recumbent 7 Preliminary Evaluation 8-9 Final Design 9-10 Fabrication 10 Materials 10 Methods 11 Testing 11 Conclusions 11 References 12 Appendix 13-15 A. -
SUN EZ Series Owners Manual 2006
l a u n a M BICYCLESBIBICYCLES CYCLES s r e EST. 1971 n w O TABLE OF CONTENTS s General Rules...................1 Night Riding.....................1 e i Recumbent Riding Tips...2 r Fitting Your Recumbent..3 Assembly....................4-11 e EZ Rider .........................12 S EZ Speedster ...................13 - EZ-3 USX.....................14 Maintenance.............15-19 Z Limited Warranty........20-21 E Specifications.............22-27 Notice: This bicycle is partially assembled. It is intended to be sold in fully assembled and fully adjusted condition. Final assembly and adjustment are to be performed by your SUN BICYCLE dealer. Page 1 RECUMBENT SAFETY AND RIDING TIPS General Rules for Safe Recumbent Riding 1. Always wear a CPSC approved helmet and some form of eye protection. 2. Always ride with a rear view mirror attached to your helmet or mounted on the recumbent. 3. Obey all traffic rules and regulations, signs and signals. 4. Ride on the side of the road, going in the same direction as the traffic and in single file. 5. Use proper hand signals when turning or stopping. 6. Be alert at all times, especially watch for cars pulling out into traffic or for opening doors. 7. Inspect your Sun Recumbent before every ride. Make sure all nuts and bolts are securely tightened. Check your brakes by applying them and rock your Sun Recumbent forward and back to make sure they are engaging properly. Check your tires for proper air pressure as indicated on the sidewall of the tires. Make sure the quick release levers on wheels and seat are secure.