Reducing Electrical Noise in Instrument Circuits
Total Page:16
File Type:pdf, Size:1020Kb
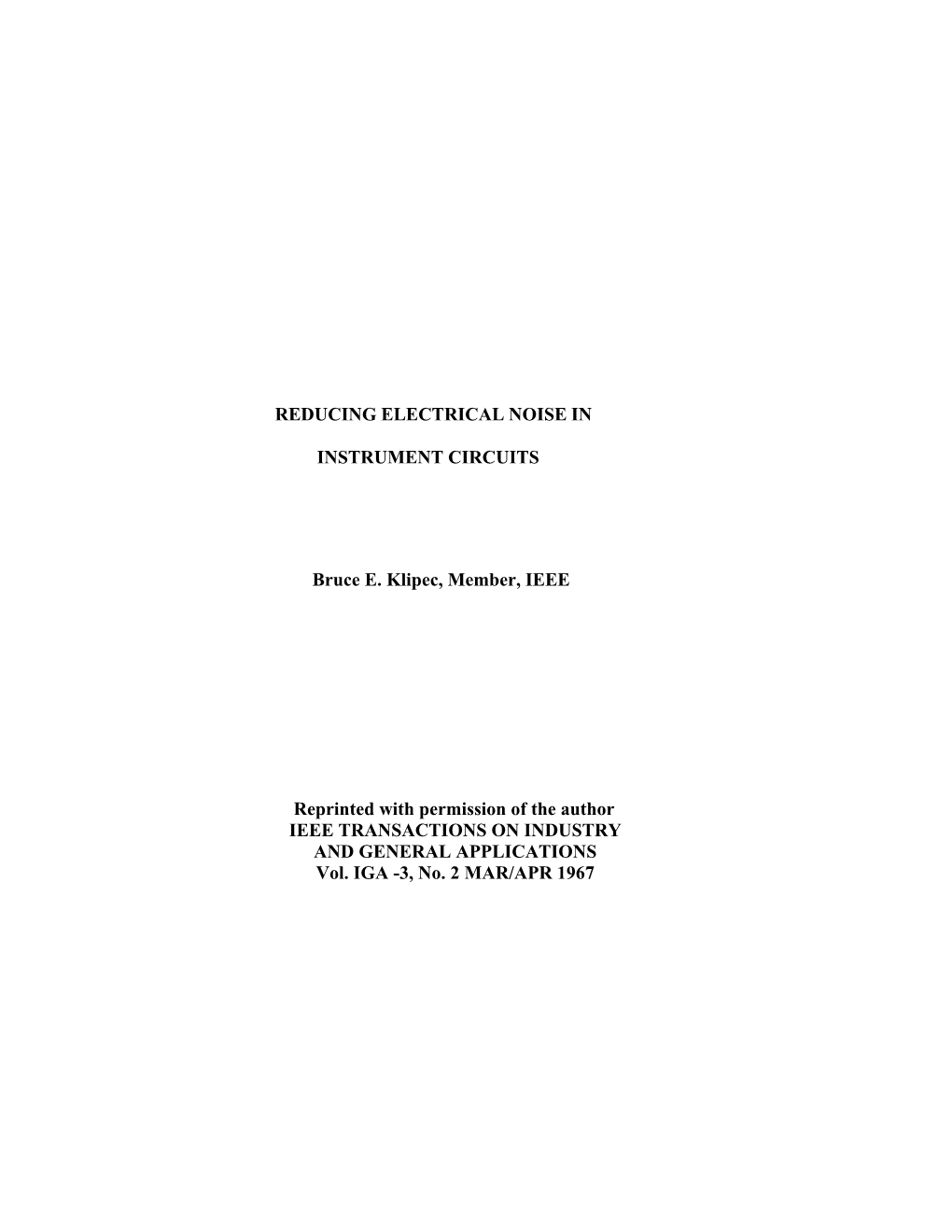
Load more
Recommended publications
-
How to Choose the Right Cable Category
How to Choose the Right Cable Category Why do I need a different category of cable? Not too long ago, when local area networks were being designed, each work area outlet typically consisted of one Category 3 circuit for voice and one Category 5e circuit for data. Category 3 cables consisted of four loosely twisted pairs of copper conductor under an overall jacket and were tested to 16 megahertz. Category 5e cables, on the other hand, had its four pairs more tightly twisted than the Category 3 and were tested up to 100 megahertz. The design allowed for voice on one circuit and data on the other. As network equipment data rates increased and more network devices were finding their way onto the network, this design quickly became obsolete. Companies wisely began installing all Category 5e circuits with often three or more circuits per work area outlet. Often, all circuits, including voice, were fed off of patch panels. This design allowed information technology managers to use any circuit as either a voice or a data circuit. Overbuilding the system upfront, though it added costs to the original project, ultimately saved money since future cable additions or cable upgrades would cost significantly more after construction than during the original construction phase. By installing all Category 5e cables, they knew their infrastructure would accommodate all their network needs for a number of years and that they would be ready for the next generation of network technology coming down the road. Though a Category 5e cable infrastructure will safely accommodate the widely used 10 and 100 megabit-per-second (Mbits/sec) Ethernet protocols, 10Base-T and 100Base-T respectively, it may not satisfy the needs of the higher performing Ethernet protocol, gigabit Ethernet (1000 Mbits/sec), also referred to as 1000Base-T. -
Modeling and Estimation of Crosstalk Across a Channel with Multiple, Non-Parallel Coupling and Crossings of Multiple Aggressors in Practical PCBS
Scholars' Mine Doctoral Dissertations Student Theses and Dissertations Fall 2014 Modeling and estimation of crosstalk across a channel with multiple, non-parallel coupling and crossings of multiple aggressors in practical PCBS Arun Reddy Chada Follow this and additional works at: https://scholarsmine.mst.edu/doctoral_dissertations Part of the Electrical and Computer Engineering Commons Department: Electrical and Computer Engineering Recommended Citation Chada, Arun Reddy, "Modeling and estimation of crosstalk across a channel with multiple, non-parallel coupling and crossings of multiple aggressors in practical PCBS" (2014). Doctoral Dissertations. 2338. https://scholarsmine.mst.edu/doctoral_dissertations/2338 This thesis is brought to you by Scholars' Mine, a service of the Missouri S&T Library and Learning Resources. This work is protected by U. S. Copyright Law. Unauthorized use including reproduction for redistribution requires the permission of the copyright holder. For more information, please contact [email protected]. MODELING AND ESTIMATION OF CROSSTALK ACROSS A CHANNEL WITH MULTIPLE, NON-PARALLEL COUPLING AND CROSSINGS OF MULTIPLE AGGRESSORS IN PRACTICAL PCBS by ARUN REDDY CHADA A DISSERTATION Presented to the Faculty of the Graduate School of the MISSOURI UNIVERSITY OF SCIENCE AND TECHNOLOGY In Partial Fulfillment of the Requirements for the Degree DOCTOR OF PHILOSOPHY in ELECTRICAL ENGINEERING 2014 Approved Jun Fan, Advisor James L. Drewniak Daryl Beetner Richard E. Dubroff Bhyrav Mutnury 2014 ARUN REDDY CHADA All Rights Reserved iii ABSTRACT In Section 1, the focus is on alleviating the modeling challenges by breaking the overall geometry into small, unique sections and using either a Full-Wave or fast equivalent per-unit-length (Eq. PUL) resistance, inductance, conductance, capacitance (RLGC) method or a partial element equivalent circuit (PEEC) for the broadside coupled traces that cross at an angle. -
Federal Communications Commission FCC 98-221 Federal
Federal Communications Commission FCC 98-221 Federal Communications Commission Washington, D.C. 20554 In the Matter of ) ) 1998 Biennial Regulatory Review -- ) Modifications to Signal Power ) Limitations Contained in Part 68 ) CC Docket No. 98-163 of the Commission's Rules ) ) ) ) ) NOTICE OF PROPOSED RULEMAKING Adopted: September 8, 1998 Released: September 16, 1998 Comment Date: 30 days from date of publication in the Federal Register Reply Comment Date: 45 days from date of publication in the Federal Register By the Commission: Commissioner Furchtgott-Roth issuing a separate statement. I. INTRODUCTION 1. In this proceeding, we seek to make it possible for customers to download data from the Internet more quickly. Our proposal, if adopted, could somewhat improve the transmission rates experienced by persons using high speed digital information products, such as 56 kilobits per second (kbps) modems, to download data from the Internet. Currently, our rules limiting the amount of signal power that can be transmitted over telephone lines prohibit such products from operating at their full potential. We believe these signal power limitations can be relaxed without causing interference or other technical problems. Therefore, we propose to relax the signal power limitations contained in Part 68 of our rules and explore the benefits and harms, if any, that may result from this change. This change would allow Pulse Code Modulation (PCM) modems, which are used by Internet Service Providers (ISPs) and other online information service providers to transmit data to consumers, to operate at higher signal powers. This modification will allow ISPs and other online information service providers to transmit data at moderately higher speeds to end-users. -
Zerox Algorithms with Free Crosstalk in Optical Multistage Interconnection Network
(IJACSA) International Journal of Advanced Computer Science and Applications, Vol. 4, No. 2, 2013 ZeroX Algorithms with Free crosstalk in Optical Multistage Interconnection Network M.A.Al-Shabi Department of Information Technology, College of Computer, Qassim University, KSA. Abstract— Multistage interconnection networks (MINs) have is on the time dilation approach to solve the optical crosstalk been proposed as interconnecting structures in various types of problem in the omega networks, a class of self-routable communication applications ranging from parallel systems, networks, which is topologically equivalent to the baseline, switching architectures, to multicore systems and advances. butterfly, cube networks et[10]. The time dilation approach Optical technologies have drawn the interest for optical solves the crosstalk problem by ensuring that only one signal is implementation in MINs to achieve high bandwidth capacity at allowed to pass through each switching element at a given time the rate of terabits per second. Crosstalk is the major problem in the network [11][12]. Typical MINs consist of N inputs, N with optical interconnections; it not only degrades the outputs and n stages with n=log N. Each stage is numbered performance of network but also disturbs the path of from 0 to (n-1), from left to right and has N/2 Switching communication signals. To avoid crosstalk in Optical MINs many Elements (SE). Each SE has two inputs and two outputs algorithms have been proposed by many researchers and some of the researchers suppose some solution to improve Zero connected in a certain pattern. Algorithm. This paper will be illustrated that is no any crosstalk The critical challenges with optical multistage appears in Zero based algorithms (ZeroX, ZeroY and ZeroXY) in interconnections are optical loss, path dependent loss and using refine and unique case functions. -
WP Demystifyingcble B 5/19/11 9:49 AM Page 2
WP_DeMystifyingCble_F (US)_WP_DeMystifyingCble_B 5/19/11 9:49 AM Page 2 FROM 5e TO 7A De-Mystifying Cabling Specifications – From 5e to 7A tructured cabling standards specify generic installation and design topologies that are characterized by a S“category” or “class” of transmission performance. These cabling standards are subsequently referenced in applications standards, developed by committees such as IEEE and ATM, as a minimum level of performance necessary to ensure application operation. There are many advantages to be realized by specifying standards-compliant structured cabling. These include the assurance of applications operation, the flexibility of cable and connectivity choices that are backward compatible and interoperable, and a structured cabling design and topology that is universally recognized by cabling professionals responsible for managing cabling additions, upgrades, and changes. CONNECTING THE WORLD TO A HIGHER STANDARD WWW. SIEMON. COM WP_DeMystifyingCble_F (US)_WP_DeMystifyingCble_B 5/19/11 9:49 AM Page 3 FROM 5e TO 7A The Telecommunications Industry Association (TIA) and International Standard for Organization (ISO) commit- tees are the leaders in the development of structured cabling standards. Committee members work hand-in-hand with applications development committees to ensure that new grades of cabling will support the latest innovations in signal transmission technology. TIA Standards are often specified by North American end-users, while ISO Standards are more commonly referred to in the global marketplace. In addition to TIA and ISO, there are often regional cabling standards groups such as JSA/JSI (Japanese Standards Association), CSA (Canadian Standards Association), and CENELEC (European Committee for Electrotechnical Standardization) developing local specifications. These regional cabling standards groups contribute actively to their country’s ISO technical advisory committees and the contents of their Standards are usually very much in harmony with TIA and ISO requirements. -
PLT); Study on Signal Processing Improving the Coexistence of VDSL2 and PLT
ETSI TR 102 930 V1.1.1 (2010-09) Technical Report PowerLine Telecommunications (PLT); Study on signal processing improving the coexistence of VDSL2 and PLT 2 ETSI TR 102 930 V1.1.1 (2010-09) Reference DTR/PLT-00030 Keywords emission, powerline ETSI 650 Route des Lucioles F-06921 Sophia Antipolis Cedex - FRANCE Tel.: +33 4 92 94 42 00 Fax: +33 4 93 65 47 16 Siret N° 348 623 562 00017 - NAF 742 C Association à but non lucratif enregistrée à la Sous-Préfecture de Grasse (06) N° 7803/88 Important notice Individual copies of the present document can be downloaded from: http://www.etsi.org The present document may be made available in more than one electronic version or in print. In any case of existing or perceived difference in contents between such versions, the reference version is the Portable Document Format (PDF). In case of dispute, the reference shall be the printing on ETSI printers of the PDF version kept on a specific network drive within ETSI Secretariat. Users of the present document should be aware that the document may be subject to revision or change of status. Information on the current status of this and other ETSI documents is available at http://portal.etsi.org/tb/status/status.asp If you find errors in the present document, please send your comment to one of the following services: http://portal.etsi.org/chaircor/ETSI_support.asp Copyright Notification No part may be reproduced except as authorized by written permission. The copyright and the foregoing restriction extend to reproduction in all media. -
Applicability of State-Of-The-Art Voice Bandwidth Compression
USBM Contract No. H0346045 TECHNICAL SERVICES FOR MINE COMMlTNI CATIONS RESEARCH APPLICABILITY OF STATE-OF-THE-ARli7 VOICE BANDWIDTH COMPRESSION TECHNIQUES FOR WIRELESS MINE COMMUNICATION Richard He Spencer -- Task Leader Warren G. Bender ARTHUR D. LITTLE, INC. Cambridge, Massachusetts 02140 C-77229 The views and conclusions contained in this document are those of the authors and should not be interpreted as necessarily representing the official policies or recommendations of the Interior ~epartment's Bureau of Mines or of the U.S. Government. USBM CONTRACT REPORT -- TASK A (Contract No. H0346045) TASK ORDER NO. 1 July 1975 UNITED STATES DEPARTMliSNT OF THE INTERIOR BUREAU OF MINES Arthur D Little, fnc. This report was prepared by Arthur D. Little, Inc., Cambridge, Massa- chusetts under USBM Contract No. H0346045. The contract was initiated under the Coal Mine Health and Safety Program, It was administered under the technical direction of the Pittsburgh Mining and Safety Research Center with Mr. Howard E. Parkinson acting as the technical project officer. Mr. Michael W. College was the contract administrator for the Bureau of Mines. This report is a summary of the work recently completed as part of this contract during the period May 1974 to July 1975. This report was sub- mitted by the authors in July 1975. No inventions or patents were developed and no applications for inven- tions or patents are pending. Arthur D Little, lnc TABLE OF CONTENTS Page LIST OF TABLES vi LIST OF FIGUWS vii I. EXECUTIVE SUMMARY A. INTRODUCTION B. FINDINGS 1. Real-Time Techniques 2. Non-Real-Time Techniques C. -
Ethernet Twisted Pair Cable Categories
Cabling Ethernet Twisted Pair Cable Categories. LPTPCATX_AN_ENB01W This Application Note explains the differences between twisted pair categories used for Structured Cabling. A Category 5 cable. Category 5 (CAT 5) cable is a multi-pair (usually 4 pair) high performance cable that consists of twisted pair conductors, used mainly for data transmission. Basic CAT 5 cable was designed for characteristics of up to 100 MHz. CAT 5 cable is typically used for LAN Ethernet networks running at 10 or 100 Mbps. Unshielded Twisted Pair (UTP) construction makes the cable highly cost-effective for data networks. B Category 5e Cable. Category 5e (CAT 5e) cable, also known as Enhanced Category 5, is designed to support full-duplex Fast Ethernet operation and Gigabit Ethernet. The main differences between CAT 5 and CAT 5e can be found in the specifications. The performance requirements have been raised slightly in the new standard. CAT 5e has stricter specifications for Power Sum Equal-Level Far-End Crosstalk (PS-ELFEXT), Near-End Crosstalk (NEXT), attenuation, and Return Loss (RL) than those for CAT 5. Like CAT 5, CAT 5e is a 100 MHz standard, but it has the capacity to handle bandwidth superior to that of CAT 5. C Category 6 Cable Category 6 (CAT 6) cable provides higher performance than CAT 5e and features more stringent specifications for crosstalk and system noise. The quality of the data transmission depends upon the performance of the components of the channel. To transmit according to CAT 6 specifications, jacks, patch cables, patch panels, cross-connects, and cabling must all meet CAT 6 standards. -
Crosstalk Characterization of the Unshielded Twisted-Pair Cable
Progress In Electromagnetics Research, PIER 58, 285–299, 2006 AN ELECTROMAGNETIC TOPOLOGY APPROACH: CROSSTALK CHARACTERIZATION OF THE UNSHIELDED TWISTED-PAIR CABLE P. Kirawanich and N. E. Islam Department of Electrical and Computer Engineering University of Missouri-Columbia Columbia, Missouri 65211, USA S. J. Yakura Air Force Research Laboratory Kirtland AFB, NM 87117, USA Abstract—The inductive effect of near-end crosstalk for a category five unshielded, twisted-pair cable has been verified using the electromagnetic topology simulation method. Crosstalk reduction and its dependency on such parameters as driving signals, circuit configuration and impedance, are studied. The simulation results are consistent with analytical analysis. Results show that the straight- through, differential-generator, twisted-pair receptor model is the most effective configuration to control the near-end crosstalk level. This is due to the influences from both the neutralizing mutual inductance and the single current generator. The simulation results also show that electromagnetic topology-based predictions are valid only for cables that are electrically short. Simulations are carried out using a compaction scheme with a single equivalent circuit. As a result, the unshielded, twisted-pair cable portion of the circuit can be combined with a larger network for analyzing the overall response of the entire network system. 1. INTRODUCTION Electromagnetic interference (EMI) analysis is a well known technique to determine the performance of network cables by considering emission, immunity, and crosstalk as the dominant components. Emission refers to energy that is radiated or conducted by cables, while 286 Kirawanich, Islam, and Yakura immunity refers to the ability of the cable to reject outside signals. -
N8833A and N8833B Crosstalk Analysis Application for Real-Time Oscilloscopes
N8833A and N8833B Crosstalk Analysis Application for Real-Time Oscilloscopes This document is discontinued and preserved for legacy customers. The N8833A and N8833B have been replaced by D9020ASIA. Information herein, may refer to products/services no longer supported. We regret any inconvenience caused by obsolete information. For the latest information go to: https://www.keysight.com/us/en/assets/7018-07031/data-sheets/5992- 3383.pdf Find us at www.keysight.com Page 1 Introduction Increased data communication speeds as well as the increased circuit density of mobile devices has led to very high serial data rates on multiple lanes, placed very close together. This combination of higher bit rates, spaced tightly together, leads to an increased amount of crosstalk distortion between serial data signals. As a result, crosstalk is becoming a more important problem to diagnose and quantify. Integrated circuit power supplies are also increasingly susceptible to crosstalk at these higher serial data rates. Simultaneous switching noise (SSN) and ground bounce from serial data signals and switching power supplies can create perturbations on the supplies that distort the data lanes they drive in the form of noise and jitter. The need to troubleshoot and characterize crosstalk is not new, but the legacy methods of measuring crosstalk in digital communications systems has relied on the process of selectively disabling some channels while enabling others. This necessarily requires measuring the crosstalk effects in the system while operating in special test modes, which means measuring them under abnormal conditions. Worse yet, some systems cannot even operate the necessary special modes. Keysight Technologies, Inc. -
Ansi/Tia-568-C.2-2009 Approved: August 11, 2009
ANSI/TIA-568-C.2-2009 APPROVED: AUGUST 11, 2009 Balanced Twisted-Pair Telecommunications Cabling and Components Standards TIA-568-C.2 August 2009 NOTICE TIA Engineering Standards and Publications are designed to serve the public interest through eliminating misunderstandings between manufacturers and purchasers, facilitating interchangeability and improvement of products, and assisting the purchaser in selecting and obtaining with minimum delay the proper product for their particular need. The existence of such Standards and Publications shall not in any respect preclude any member or non-member of TIA from manufacturing or selling products not conforming to such Standards and Publications. Neither shall the existence of such Standards and Publications preclude their voluntary use by Non-TIA members, either domestically or internationally. Standards and Publications are adopted by TIA in accordance with the American National Standards Institute (ANSI) patent policy. By such action, TIA does not assume any liability to any patent owner, nor does it assume any obligation whatever to parties adopting the Standard or Publication. This Standard does not purport to address all safety problems associated with its use or all applicable regulatory requirements. It is the responsibility of the user of this Standard to establish appropriate safety and health practices and to determine the applicability of regulatory limitations before its use. (From Standards Proposal No. 3-4426-RV3-B-2, formulated under the cognizance of the TIA TR-42 User Premises Telecommunications Cabling Requirements, TR-42.7 Subcommittee on Telecommunications Copper Cabling Systems.) Published by ©TELECOMMUNICATIONS INDUSTRY ASSOCIATION Standards and Technology Department 2500 Wilson Boulevard Arlington, VA 22201 U.S.A. -
Alien Crosstalk: the Limiting Noise Factor in Category 6A Channel Performance
WHITE PAPER February, 2014 Alien Crosstalk: The Limiting Noise Factor in Category 6A Channel Performance Introduction Today’s Category 6A (CAT 6A) systems are impacted by an increasing amount of noise. The typical environment for a data center is characterized by multiple Ethernet protocols running over a significant volume of different cable designs, performance levels, and manufacturers’ brands. All of these elements provide a very noisy environment for 10GBASE-T systems. It is generally understood by most in the Ethernet industry that active equipment is able to eliminate much of the internally generated noise within a 10GBASE-T channel. However, many in the industry are not aware that cancellation technology has improved, making alien crosstalk (AXT) the limiting factor in the overall noise level of 10GBASE-T systems. This white paper explains that the overall noise level for CAT 6A channels can only be improved by adding additional immunity to AXT in the system. The 10GBASE-T Channel The Ethernet protocol for 10Gb/s over twisted pair cabling, IEEE 802.3an 10GBASE-T, uses a standard CAT 6A cabling channel. CAT 6A cabling performance requirements are defined in TIA-568-C.2. CAT 6A component requirements are set for constructing reference implementation channels, up to 100m length with 4 connectors, thus providing a minimum performance necessary to support 10GBASE-T data link operating at maximum 10-¹² bit error rate (BER). The ideal cabling channel has no loss and no noise, because the two transceivers at the ends of a link are connected directly to each other. By introducing cabling component losses into the channel from intervening cable and connectors, the signal level is lowered and the noise level is raised, thus reducing the signal-to-noise ratio (SNR) as well as the system capacity.