By a 965% ATT'ys
Total Page:16
File Type:pdf, Size:1020Kb
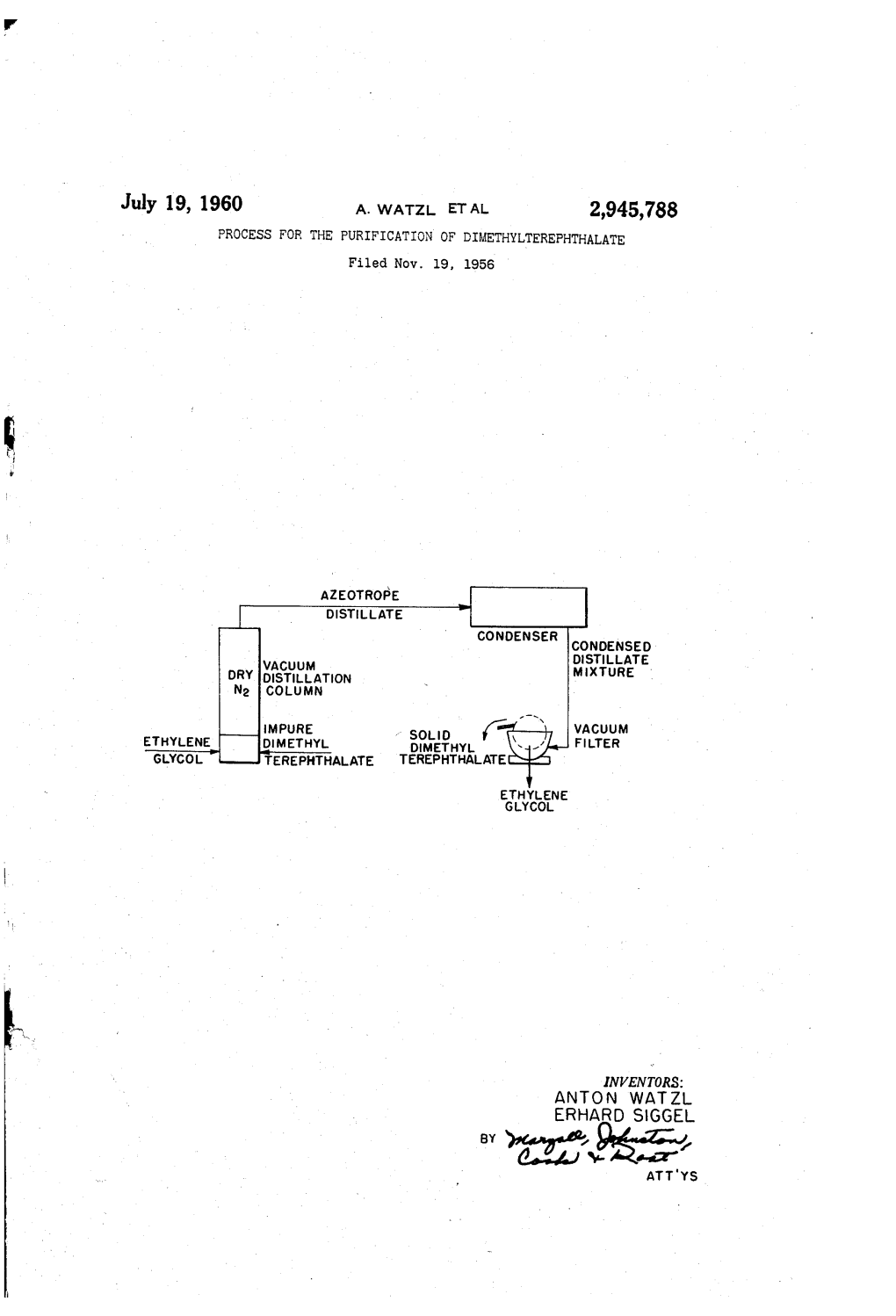
Load more
Recommended publications
-
The Separation of Three Azeotropes by Extractive Distillation by An-I Yeh A
The separation of three azeotropes by extractive distillation by An-I Yeh A thesis submitted in partial fulfillment of the requirement for the degree of Master of Science in Chemical Engineering Montana State University © Copyright by An-I Yeh (1983) Abstract: Several different kinds of extractive distillation agents were investigated to affect the separation of three binary liquid mixtures, isopropyl ether - acetone, methyl acetate - methanol, and isopropyl ether - methyl ethyl ketone. Because of the small size of the extractive distillation column, relative volatilities were assumed constant and the Fenske equation was used to calculate the relative volatilities and the number of minimum theoretical plates. Dimethyl sulfoxide was found to be a good extractive distillation agent. Extractive distillation when employing a proper agent not only negated the azeotropes of the above mixtures, but also improved the efficiency of separation. This process could reverse the relative volatility of isopropyl ether and acetone. This reversion was also found in the system of methyl acetate and methanol when nitrobenzene was the agent. However, normal distillation curves were obtained for the system of isopropyl ether and methyl ethyl ketone undergoing extractive distillation. In the system of methyl acetate and methanol, the relative volatility decreased as the agents' carbon number increased when glycols were used as the agents. In addition, the oxygen number and the locations of hydroxyl groups in the glycols used were believed to affect the values of relative volatility. An appreciable amount of agent must be maintained in the column to affect separation. When dimethyl sulfoxide was an agent for the three systems studied, the relative volatility increased as the addition rate increased. -
Development of a Process for N-Butanol Recovery from Abe
937 A publication of CHEMICAL ENGINEERING TRANSACTIONS VOL. 74, 2019 The Italian Association of Chemical Engineering Online at www.cetjournal.it Guest Editors: Sauro Pierucci, Jiří Jaromír Klemeš, Laura Piazza Copyright © 2019, AIDIC Servizi S.r.l. ISBN 978-88-95608-71-6; ISSN 2283-9216 DOI: 10.3303/CET1974157 Development of a Process for N-Butanol Recovery from Abe Wastewater Streams by Membrane Technology * Marco Stoller , Marco Bravi, Paola Russo, Roberto Bubbico, Barbara Mazzarotta Sapienza University of Rome, Dept. of Chemical Materials Environmental Engineering, Via Eudossiana 18, 00184 Rome, Italy [email protected] The aceton-butyl-ethanolic fermentation process (ABE) is a biotechnological process that leads to the production of acetone, n-butanol and ethanol (ABE compounds) from glucose sources and amides by use of certain biomasses. The process was developed initially during the middle of the last century and suffers from decline due to the greater petrochemical production of products and the lowering of the costs of the sector. Nowadays, the ABE process is regaining great interest because the fraction with the highest concentration, i.e. n-butanol, is an excellent constituent for biofuels. The ABE process has been optimized over time to obtain maximum yields of n-butanol, but the problem of separating and concentrating the butanol in the outlet stream of the ABE process persists. To allow an adequate use, often distillation by use of more columns is required. Moreover, the contained biomasses and suspended solids, in high quantity, must be eliminated, leading to overall high treatment costs. This work will report the main idea and some preliminary experimental results for the development and application of a process based on membrane technologies, to separate and concentrate the butanol from ABE process streams to sensibly reduce the difficulty to perform a final distillation. -
Evaluation of Azeotropic Dehydration for the Preservation of Shrimp. James Edward Rutledge Louisiana State University and Agricultural & Mechanical College
Louisiana State University LSU Digital Commons LSU Historical Dissertations and Theses Graduate School 1969 Evaluation of Azeotropic Dehydration for the Preservation of Shrimp. James Edward Rutledge Louisiana State University and Agricultural & Mechanical College Follow this and additional works at: https://digitalcommons.lsu.edu/gradschool_disstheses Recommended Citation Rutledge, James Edward, "Evaluation of Azeotropic Dehydration for the Preservation of Shrimp." (1969). LSU Historical Dissertations and Theses. 1689. https://digitalcommons.lsu.edu/gradschool_disstheses/1689 This Dissertation is brought to you for free and open access by the Graduate School at LSU Digital Commons. It has been accepted for inclusion in LSU Historical Dissertations and Theses by an authorized administrator of LSU Digital Commons. For more information, please contact [email protected]. This dissertation has been 70-9089 microfilmed exactly as received RUTLEDGE, James Edward, 1941- EVALUATION OF AZEOTROPIC DEHYDRATION FOR THE PRESERVATION OF SHRIMP. The Louisiana State University and Agricultural and Mechanical College, PhJD., 1969 Food Technology University Microfilms, Inc., Ann Arbor, Michigan Evaluation of Azeotropic Dehydration for the Preservation of Shrimp A Dissertation Submitted to the Graduate Faculty of the Louisiana State University and Agricultural and Mechanical College in partial fulfillment of the requirements for the degree of Doctor of Philosophy in The Department of Food Science and Technology by James Edward Rutledge B.S., Texas A&M University, 1963 M.S., Texas A&M University, 1966 August, 1969 ACKNOWLEDGMENT The author wishes to express his sincere appreciation to his major professor, Dr, Fred H. Hoskins, for the guidance which he supplied not only in respect to this dissertation but also in regard to the author’s graduate career at Louisiana State University, Gratitude is also extended to Dr. -
FUGACITY It Is Simply a Measure of Molar Gibbs Energy of a Real Gas
FUGACITY It is simply a measure of molar Gibbs energy of a real gas . Modifying the simple equation for the chemical potential of an ideal gas by introducing the concept of a fugacity (f). The fugacity is an “ effective pressure” which forces the equation below to be true for real gases: θθθ f µµµ ,p( T) === µµµ (T) +++ RT ln where pθ = 1 atm pθθθ A plot of the chemical potential for an ideal and real gas is shown as a function of the pressure at constant temperature. The fugacity has the units of pressure. As the pressure approaches zero, the real gas approach the ideal gas behavior and f approaches the pressure. 1 If fugacity is an “effective pressure” i.e, the pressure that gives the right value for the chemical potential of a real gas. So, the only way we can get a value for it and hence for µµµ is from the gas pressure. Thus we must find the relation between the effective pressure f and the measured pressure p. let f = φ p φ is defined as the fugacity coefficient. φφφ is the “fudge factor” that modifies the actual measured pressure to give the true chemical potential of the real gas. By introducing φ we have just put off finding f directly. Thus, now we have to find φ. Substituting for φφφ in the above equation gives: p µ=µ+(p,T)θ (T) RT ln + RT ln φ=µ (ideal gas) + RT ln φ pθ µµµ(p,T) −−− µµµ(ideal gas ) === RT ln φφφ This equation shows that the difference in chemical potential between the real and ideal gas lies in the term RT ln φφφ.φ This is the term due to molecular interaction effects. -
Heterogeneous Azeotropic Distillation
PROSIMPLUS APPLICATION EXAMPLE HETEROGENEOUS AZEOTROPIC DISTILLATION EXAMPLE PURPOSE This example illustrates a high purity separation process of an azeotropic mixture (ethanol-water) through heterogeneous azeotropic distillation. This process includes distillation columns. Additionally these rigorous multi- stage separation modules are part of a recycling stream, demonstrating the efficiency of ProSimPlus convergence methods. Specifications are set on output streams in order to insure the required purity. This example illustrates the way to set "non-standard" specifications in the multi-stage separation modules. Three phase calculations (vapor-liquid- liquid) are done with the taken into account of possible liquid phase splitting. ACCESS Free-Internet Restricted to ProSim clients Restricted Confidential CORRESPONDING PROSIMPLUS FILE PSPS_EX_EN-Heterogeneous-Azeotropic-Distillation.pmp3 . Reader is reminded that this use case is only an example and should not be used for other purposes. Although this example is based on actual case it may not be considered as typical nor are the data used always the most accurate available. ProSim shall have no responsibility or liability for damages arising out of or related to the use of the results of calculations based on this example. Copyright © 2009 ProSim, Labège, France - All rights reserved www.prosim.net Heterogeneous azeotropic distillation Version: March, 2009 Page: 2 / 12 TABLE OF CONTENTS 1. PROCESS MODELING 3 1.1. Process description 3 1.2. Process flowsheet 5 1.3. Specifications 6 1.4. Components 6 1.5. Thermodynamic model 7 1.6. Operating conditions 7 1.7. "Hints and Tips" 9 2. RESULTS 9 2.1. Comments on results 9 2.2. Mass and energy balances 10 2.3. -
Enhanced Distillation • Use of Triangular Graphs
Lecture 15. Enhanced Distillation and Supercritical Extraction (1) [Ch. 11] • Enhanced Distillation • Use of Triangular Graphs - Zeotropic mixture -Mixture forming one minimum-boiling azeotrope - Mixture forming two minimum-boiling azeotropes • Residue-Curve Maps • Distillation-Curve Maps • Product-Composition Regions at Total Reflux Enhanced Distillation • Cases when ordinary distillation is not economical - Boiling point difference between components is less than 50℃ - Relative volatility is less than 1.10 - Mixture forms an azeotrope • Enhanced distillation - Extractive distillation : adding a large amount of solvent - Salt distillation : adding a soluble , ionic salt - Pressure-swing distillation : operating at two different pressures - Homogeneous azeotropic distillation : adding an entrainer - Heterogeneous azeotropic distillation : adding an entrainer - Reactive distillation : adding a separating agent to react selectively and reversibly with feed component(s) Zeotropic vs. Azeotropic Systems Binary zeotropic system Binary azeotropic system P = constant AtAzeotrope C T-y T-x Pure B xA, yA Pure A Use of Triangular Graphs • Triangular vapor-liquid diagram for ternary mixture - Too complex to understand • Plot with only equilibr ium liquid composition fofoatenayr a ternary mixture - Easy to understand -Convenient to use - Provide useful information in distillation of ternary components . Residue curve . Distill ati on curve Distillation Curves for Ternary Systems Each curve in each diagram is the locus of possible equilibrium liquid-phase -
Separation of Dimethyl Carbonate and Methanol Mixture by Pervaporation Using Hybsi Ceramic Membrane
Separation of dimethyl carbonate and methanol mixture by pervaporation using HybSi ceramic membrane Dissertation presented by Antoine GOFFINET for obtaining the master's degree in Chemical and Materials Engineering Supervisors Patricia LUIS ALCONERO Readers Iwona CYBULSKA, Denis DOCHAIN, Wenqi LI Academic year 2017-2018 Abstract In the current context of high biodiesel production, some by-products are created partic- ularly glycerol. Glycerol has a wide range of applications however its market is supersatu- rated as its production is very high. A solution found is the production of a value added com- ponent from glycerol. This value added component is the glycerol carbonate (GC) produced by transesterification reaction of glycerol with dimethyl carbonate (DMC). The reaction in- cludes four components: glycerol, DMC, GC and methanol. As methanol and DMC make up an azeotropic mixture, it is not possible to separate them by distillation. Pervaporation is a solution for this separation as it can break the azeotrope mixture and have other advantages especially energy saving. The pervaporation using polymeric membrane presents disadvan- tages as the low thermally and chemically resistance. Therefore another kind of membrane is needed. As ceramic membrane resistance is higher, the commercial HybSi ceramic is se- lected for this thesis experiments. This study aim to analyse the separation of DMC and methanol by pervaporation. The separation performance of HybSi membrane is evaluated at 40-50-60◦C with binary mixture of different concentrations. The permeation through the membrane is analysed by the solution-diffusion model. h kg i The results showed low permeate flux between 0 and 0.86 hm2 . -
Partial Separation of an Azeotropic Mixture of Hydrogen Chloride and Water and Copper (II) Chloride Recovery for Optimization of the Copper-Chlorine Cycle
Partial Separation of an Azeotropic Mixture of Hydrogen Chloride and Water and Copper (II) Chloride Recovery for Optimization of the Copper-Chlorine Cycle by Matthew P. Lescisin A Thesis Submitted in Partial Fulfillment of the Requirements for the Degree of Master of Applied Science in The Faculty of Engineering and Applied Science Mechanical Engineering University of Ontario Institute of Technology September 2017 © Matthew P. Lescisin, 2017 Contents Contents ii Abstract v Acknowledgments vi List of Figures vii List of Tables viii Nomenclature ix Quantities...................................... ix Greek Letters.................................... x Subscripts...................................... xi Acronyms...................................... xi 1 Introduction1 2 Background4 2.1 Boiling in the Subcooled Liquid Region .................. 4 2.2 Vapor-Liquid Equilibrium (VLE)...................... 5 2.3 Phase Diagrams................................ 5 2.3.1 Tie-Lines ............................... 6 2.4 Distillation .................................. 6 2.5 Azeotropes .................................. 8 3 Literature Review9 3.1 Azeotropic Distillation............................ 9 3.2 Extractive Distillation............................ 10 3.3 Pressure-Swing Distillation .......................... 11 3.4 Batch Mode.................................. 13 3.5 Heat-Integrated Distillation Columns.................... 13 3.5.1 Heat-Integrated PSD......................... 14 ii CONTENTS iii 3.6 Reflux Ratio ................................. 15 -
Purification of Lactic Acid
PURIFICATION OF LACTIC ACID by SIDNEY HSIN-HUAI CHOW B. S., Taiwan Provincial Cheng Kung University, 1957 A MASTER'S THESIS submitted in partial fulfillment of the requirements for the degree MASTER OF SCIENCE Department of Chemical Engineering KANSAS STATE UNIVERSITY Manhattan, Kansas 1962 11 TABLE OF CONTENTS INTRODUCTION 1 Properties of Lactic Acid 1 Preparation of Lactic Acid 3 Utilization of Lactic Acid 13 Purification of Lactic Acid 14 Purpose of this Research 23 DESCRIPTION OF THE PROCESS 24 Materials 24 Equipment 25 Experimental Procedure 26 Analytical Methods . 27 EXPERIMENTAL RESULTS 29 Material Losses 29 Yields 29 Effect of Feed Composition 32 Effect of Time of Run 32 Effect of Concentration of Catalyst 33 Effect of Temperature 33 Purity of the Products 33 DISCUSSION OF RESULTS 34 RECOMMENDATIONS 35 ACKNOWLEDGMENTS 38 LITERATURE CITED 39 APPENDIX 41 INTRODUCTION Properties of Lactic Acid OH Lactic acid is alphahydroxy propionic acid, CH3---C---COOH. Because of the asymmetry of the alpha carbon atom, this acid exists in two modifi- cations, a dextro acid and a levo acid. COOH COOH HO OH CH3 CH3 Dextro -Lactic Acid Levo-Lactic Acid The commercial acid is a mixture of the two forms, usually in equal proportions; and it is, therefore, inactive with respect to the rotation of the plane of polarized light. Lactic acid is both an alcohol and an acid; and, therefore, its molecules can form esters with one another. In water solutions containing less than 20 percent of lactic acid, the acid is in the simple monomeric form; but solutions of greater concentration contain some esters involving two or more of the simple molecules. -
Lecture 36. the Phase Rule
Lecture 36. The Phase Rule P = number of phases C = number of components (chemically independent constituents) F = number of degrees of freedom xC,P = the mole fraction of component C in phase P The variables used to describe a system in equilibrium: x11, x21, x31,...,xC −1,1 phase 1 x12 , x22 , x32 ,..., xC−1,2 phase 2 x1P , x2P , x3P ,...,xC−1,P phase P T,P Total number of variables = P(C-1) + 2 Constraints on the system: m11 = m12 = m13 =…= m1,P P - 1 relations m21 = m22 = m23 =…= m2,P P - 1 relations mC,1 = mC,2 = mC,3 =…= mC,P P - 1 relations 1 Total number of constraints = C(P - 1) Degrees of freedom = variables - constraints F=P(C- 1) + 2 - C(P - 1) F=C- P+2 Single Component Systems: F = 3 - P In single phase regions, F = 2. Both T and P may vary. At the equilibrium between two phases, F = 1. Changing T requires a change in P, and vice versa. At the triple point, F = 0. Tt and Pt are unique. 2 Four phases cannot be in equilibrium (for a single component.) Two Component Systems: F = 4 - P The possible phases are the vapor, two immiscible (or partially miscible) liquid phases, and two solid phases. (Of course, they don’t have to all exist. The liquids might turn out to be miscible for all compositions.) 3 Liquid-Vapor Equilibrium Possible degrees of freedom: T, P, mole fraction of A xA = mole fraction of A in the liquid yA = mole fraction of A in the vapor zA = overall mole fraction of A (for the entire system) We can plot either T vs zA holding P constant, or P vs zA holding T constant. -
Optimization Study on the Azeotropic Distillation Process for Isopropyl Alcohol Dehydration
Korean J. Chem. Eng., 23(1), 1-7 (2006) Optimization study on the azeotropic distillation process for isopropyl alcohol dehydration Jungho Cho and Jong-Ki Jeon*,† Department of Chemical Engineering, Dong Yang University, 1, Kyochon-dong, Poongki-eup, Youngju, Gyeongbuk 750-711, Korea *Department of Chemical Engineering, Kongju National University, 182, Shinkwan-dong, Gongju, Chungnam 314-701, Korea (Received 9 August 2005 • accepted 26 November 2005) Abstract−Modeling and optimization work was performed using benzene as an entrainer to obtain a nearly pure an- hydrous isopropyl alcohol product from dilute aqueous IPA mixture through an azeotropic distillation process. NRTL liquid activity coefficient model and PRO/II with PROVISION 6.01, a commercial process simulator, were used to simulate the overall azeotropic distillation process. We determined the total reboiler heat duties as an objective function and the concentration of IPA at concentrator top as a manipulated variable. As a result, 38.7 mole percent of IPA at concentrator top gave the optimum value that minimized the total reboiler heat duties of the three distillation columns. Key words: Azeotropic Distillation, Entrainer, NRTL Liquid Activity Coefficient Model, Simulation, Optimization INTRODUCTION using special distillation. One is to utilize an azeotropic distillation process using benzene or cyclohexane as an entrainer [Font et al., An anhydrous isopropyl alcohol (IPA) product with purity over 2003; Tao et al., 2003; Al-Amer, 2000; Fele et al., 2000] and the 99.9% by weight has been widely used as a raw material of paint other is an extractive distillation process using ethylene glycol as a or ink products and as a solvent in electronic and medicine indus- solvent [Ligero and Ravagnani, 2003; Pinto et al., 2000]. -
Azeotropes As Powerful Tool for Waste Minimization in Industry and Chemical Processes
molecules Review Azeotropes as Powerful Tool for Waste Minimization in Industry and Chemical Processes Federica Valentini and Luigi Vaccaro * Laboratory of Green S.O.C., Dipartimento di Chimica, Biologia e Biotecnologie, Università degli Studi di Perugia, Via Elce di Sotto 8, 06123 Perugia, Italy; [email protected] * Correspondence: [email protected]; Tel./Fax: +39-07-5585-5541 Academic Editor: Derek J. McPhee Received: 17 October 2020; Accepted: 10 November 2020; Published: 12 November 2020 Abstract: Aiming for more sustainable chemical production requires an urgent shift towards synthetic approaches designed for waste minimization. In this context the use of azeotropes can be an effective tool for “recycling” and minimizing the large volumes of solvents, especially in aqueous mixtures, used. This review discusses the implementation of different kinds of azeotropic mixtures in relation to the environmental and economic benefits linked to their recovery and re-use. Examples of the use of azeotropes playing a role in the process performance and in the purification steps maximizing yields while minimizing waste. Where possible, the advantages reported have been highlighted by using E-factor calculations. Lastly azeotrope potentiality in waste valorization to afford value-added materials is given. Keywords: azeotrope; waste minimization; solvent recovery; azeotropic distillation; process design; waste valorization 1. Introduction The materials not incorporated into the final desired product and the energy required for conducting a process can be considered most trivially as the major direct origin of “waste” associated to chemical production. In addition, the possible formation of undesired isomers or byproducts also results in the generation of costly waste, that being in some cases hazardous, can limit the final application of the main product.