Standardized Safety Training
Total Page:16
File Type:pdf, Size:1020Kb
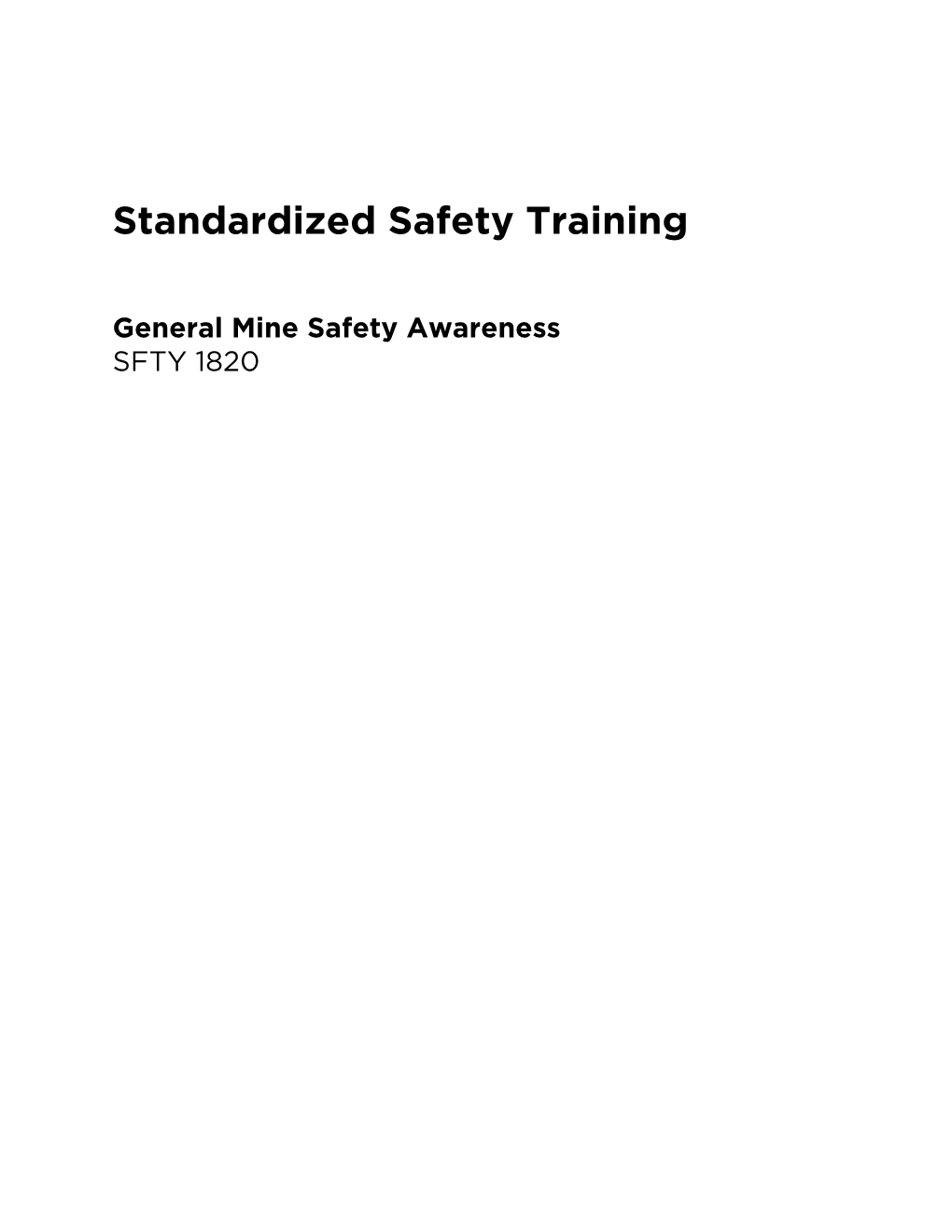
Load more
Recommended publications
-
Psychosocial Hazards and Occupational Stress
Psychosocial Hazards and Occupational Stress OHS Body of Knowledge Psychosocial Hazards and Occupational Stress April, 2012 Copyright notice and licence terms First published in 2012 by the Safety Institute of Australia Ltd, Tullamarine, Victoria, Australia. Bibliography. ISBN 978-0-9808743-1-0 This work is copyright and has been published by the Safety Institute of Australia Ltd ( SIA) under the auspices of HaSPA (Health and Safety Professionals Alliance). Except as may be expressly provided by law and subject to the conditions prescribed in the Copyright Act 1968 (Commonwealth of Australia), or as expressly permitted below, no part of the work may in any form or by any means (electronic, mechanical, microcopying, digital scanning, photocopying, recording or otherwise) be reproduced, stored in a retrieval system or transmitted without prior written permission of the SIA. You are free to reproduce the material for reasonable personal, or in-house, non-commercial use for the purposes of workplace health and safety as long as you attribute the work using the citation guidelines below and do not charge fees directly or indirectly for use of the material. You must not change any part of the work or remove any part of this copyright notice, licence terms and disclaimer below. A further licence will be required and may be granted by the SIA for use of the materials if you wish to: • reproduce multiple copies of the work or any part of it • charge others directly or indirectly for access to the materials • include all or part of the materials in advertising of a product or services, or in a product for sale • modify the materials in any form, or • publish the materials. -
Mediating Role of Psychosocial Hazard: an Integrated Modelling Approach
International Journal of Environmental Research and Public Health Article Impact of Safety Culture on Safety Performance; Mediating Role of Psychosocial Hazard: An Integrated Modelling Approach Gehad Mohammed Ahmed Naji 1,*, Ahmad Shahrul Nizam Isha 1, Mysara Eissa Mohyaldinn 2, Stavroula Leka 3 , Muhammad Shoaib Saleem 1, Syed Mohamed Nasir Bin Syed Abd Rahman 4 and Mohammed Alzoraiki 5 1 Department of Management & Humanities, Universiti Teknologi PETRONAS, Seri Iskandar 32610, Perak, Malaysia; [email protected] (A.S.N.I.); [email protected] (M.S.S.) 2 Department of Petroleum Engineering, Universiti Teknologi PETRONAS, Seri Iskandar 32610, Perak, Malaysia; [email protected] 3 Cork University Business School, University College Cork, T12 K8AF Cork, Ireland; [email protected] 4 Petronas Group Technology Solutions, Bandar Baru Bangi 43000, Selangor, Malaysia; [email protected] 5 Department of Technology Management and Business, Universiti Tun Hussein Onn Malaysia, Parit Raja 86400, Johor, Malaysia; [email protected] * Correspondence: [email protected] Abstract: We conceptualize that safety culture (SC) has a positive impact on employee’s safety performance by reducing their psychosocial hazards. A higher level of safety culture environment reduces psychosocial hazards by improving employee’s performance toward safety concerns. The Citation: Naji, G.M.A.; Isha, A.S.N.; purpose of this study was to evaluate how psychosocial hazard mediates the relationship between Mohyaldinn, M.E.; Leka, S.; Saleem, safety culture and safety performance. Data were collected from 380 production employees in M.S.; Rahman, S.M.N.B.S.A.; three states of Malaysia from the upstream oil and gas sector. -
IMPACT of PHYSICAL and PSYCHOSOCIAL WORKPLACE HAZARDS on EMPLOYEE HEALTH: an IRISH T ALE of CIVIL SERVANT WORKERS Kyle R
Clemson University TigerPrints All Dissertations Dissertations 5-2014 IMPACT OF PHYSICAL AND PSYCHOSOCIAL WORKPLACE HAZARDS ON EMPLOYEE HEALTH: AN IRISH T ALE OF CIVIL SERVANT WORKERS Kyle R. Stanyar Clemson University Follow this and additional works at: https://tigerprints.clemson.edu/all_dissertations Part of the Psychiatry and Psychology Commons Recommended Citation Stanyar, Kyle R., "IMPACT OF PHYSICAL AND PSYCHOSOCIAL WORKPLACE HAZARDS ON EMPLOYEE HEALTH: AN IRISH T ALE OF CIVIL SERVANT WORKERS" (2014). All Dissertations. 1401. https://tigerprints.clemson.edu/all_dissertations/1401 This Dissertation is brought to you for free and open access by the Dissertations at TigerPrints. It has been accepted for inclusion in All Dissertations by an authorized administrator of TigerPrints. For more information, please contact [email protected]. IMPACT OF PHYSICAL AND PSYCHOSOCIAL WORKPLACE HAZARDS ON EMPLOYEE HEALTH: AN IRISH TALE OF CIVIL SERVANT WORKERS ____________________________________ A Dissertation Presented to the Graduate School of Clemson University ____________________________________ In Partial Fulfillment of the Requirements for the Degree Doctor of Philosophy Industrial-Organizational Psychology ____________________________________ by Kyle R. Stanyar May 2014 ____________________________________ Accepted by: Dr. Robert R. Sinclair, Committee Chair Dr. Patrick Rosopa Dr. Paul Merritt Dr. James McCubbin ABSTRACT Obesity, mental health problems, and absenteeism are both economic and health burdens for employers and employees. Research suggests that physical and psychosocial hazards in the workplace contribute to health risks and health problems among employees. There is a need for researchers to examine how exercise, diet, and age interact with the negative effects of workplace hazards upon health. Hypotheses 1a through 3b predicted that physical and psychosocial workplace hazards would negatively impact body mass index (BMI), general mental health, and sickness absences. -
The Divers Logbook Free
FREE THE DIVERS LOGBOOK PDF Dean McConnachie,Christine Marks | 240 pages | 18 May 2006 | Boston Mills Press | 9781550464788 | English | Ontario, Canada Printable Driver Log Book Template - 5+ Best Documents Free Download A dive log is a record of the diving history of an underwater diver. The log may either be in a book, The Divers Logbook hosted softwareor web based. The log serves purposes both related to safety and personal records. Information in a log may contain the date, time and location, the profile of the diveequipment used, air usage, above and below water conditions, including temperature, current, wind and waves, general comments, and verification by the buddyinstructor or supervisor. In case of a diving accident, it The Divers Logbook provide valuable data regarding diver's previous experience, as well as the other factors that might have led to the accident itself. Recreational divers are generally advised to keep a logbook as a record, while professional divers may be legally obliged to maintain a logbook which is up to date and complete in its records. The professional diver's logbook is a legal document and may be important for getting employment. The required content and formatting of the professional diver's logbook is generally specified by the registration authority, but may also be specified by an industry association such as the International Marine Contractors Association IMCA. A more minimalistic log book for recreational divers The Divers Logbook are only interested in keeping a record of their accumulated experience total number of dives and total amount of time underwatercould just contain the first point of the above list and the maximum depth of the dive. -
Houdmont, Kerr and Randall
View metadata, citation and similar papers at core.ac.uk brought to you by CORE provided by Repository@Nottingham 1 Houdmont, J., Kerr, R., & Randall, R. (2012). Organizational psychosocial hazard exposures in UK policing: Management Standards Indicator Tool reference values. Policing: An International Journal of Police Strategies and Management, 35, 182-197. DOI 10.1108/13639511211215522 2 Abstract Purpose: There is a paucity of contemporary evidence on the organizational (as opposed to operational) psychosocial hazard (OPH) exposures of UK police officers. The purpose of this study is to report on OPH exposures measured via an instrument developed by the UK government - the Management Standards Indicator Tool - among police officers sampled from an entire UK force. The study provides reference values for UK police officers’ OPH exposures, considers these in relation to government exposure targets, and examines the association between officers’ OPH exposures and perceived work-related stress. Design/methodology/approach: Police officers (n = 1,729) completed the Management Standards Indicator Tool which measures perceived exposure to seven psychosocial work environment dimensions: demands, control, managerial support, peer support, relationships, role, and change. In addition, a single-item measure of perceived work-related stress was applied. Findings: Sector-specific reference values were generated by job role and rank on each of the seven dimensions assessed by the Indicator Tool. Scores on all seven dimensions were below government target levels (indicating that scores fell below the 80th percentile in relation to benchmark data). 46% of police officers reported their work to be very or extremely stressful. A significant positive correlation (p < .01) was found between scores on each of the seven psychosocial work characteristics and perceived work-related stress. -
Credit: 1 PDH
Credit: 1 PDH Course Title: Step-By-Step Procedure and Tools to Reduce Work-Related Stress Approved for Credit in All 50 States Visit epdhonline.com for state specific information including Ohio’s required timing feature. 3 Easy Steps to Complete the Course: 1. Read the Course PDF 2. Purchase the Course Online & Take the Final Exam 3. Print Your Certificate epdh.com is a division of Cer�fied Training Ins�tute ProvisionalChapter chapter 12 Step-By-Step Procedure andand ToolsTools toto ReduceReduce Work-Work- Related Stress Related Stress Azra Huršidić Radulović Azra Huršidić Radulović Additional information is available at the end of the chapter Additional information is available at the end of the chapter http://dx.doi.org/10.5772/66181 Abstract Based on available guidelines, protocol, etc., of the EU countries as well as evaluated results of the taken measures, step-by-step procedures are proposed as well as the tools of occupational medicine specialist for the identification of stressors and measures that should be taken to reduce stress at work. European Pact for Mental Health and Well- Being has focused its commitment on workplaces and a necessity to promote work settings, to create the atmosphere for mental health promotion emphasizing reconcili- ation between work and family life, to introduce a program for stress prevention at work and health promotion in the workplace and to support employment, rehabilitation and return to work of the workers with mental health issues and disorders. Any risk assessment at work, especially of psychosocial risks, requires support of employers and active participation of workers. -
Annexure No. Name
List of Annexures Annexure No. Name Annexure I ToR letter Annexure II MIDC Land transfer letter Annexure III MSDS Annexure IV Wild life sanctuary map Annexure V NBWL application copy Annexure VI QRA and HAZOP study report Correspondence with MOEFCC 1. Public hearing exemption clarification letter submission 2. Addition of product keeping same total production capacity+ project Title change intimation to EAC No.IA-J-11011/47/2018-IA-II(I) Goverment of India Minister of Enviroment,Forest and Climate Change Impact Assessment Division *** Indira Paryavaran Bhavan, Vayu Wing,3rd Floor,Aliganj, Jor Bagh Road,New Delhi-110003 22 Mar 2018 To, M/s FINE ORGANIC INDUSTRIES PVT LTD Fine Organic Industries,Plot no 124, MIDC ,Dombivali (East) Dist. Thane, Pin code 421201, Thane-421201 Maharashtra Tel.No.22-21025000; Email:[email protected] Sir/Madam, This has reference to the proposal submitted in the Ministry of Environment, Forest and Climate Change to prescribe the Terms of Reference (TOR) for undertaking detailed EIA study for the purpose of obtaining Environmental Clearance in accordance with the provisions of the EIA Notification, 2006. For this purpose, the proponent had submitted online information in the prescribed format (Form-1 ) along with a Pre-feasibility Report. The details of the proposal are given below: 1. Proposal No.: IA/MH/IND2/72688/2018 Proposed manufacturing unit for Salts of 2. Name of the Proposal: Propionic acid by M/s. Fine Organic Industries Ltd. 3. Category of the Proposal: Industrial Projects - 2 4. Project/Activity applied for: 5(f) Synthetic organic chemicals industry (dyes & dye intermediates; bulk 5. -
Workplace Action Plan
Action on Workplace Stress: Mental Injury Prevention Tools for Ontario Workers Part 5 — Workplace Action Plan Action on Workplace Stress A Worker’s Guide to Addressing Workplace Causes of Mental Distress This guide and resource kit will provide workers a basic understanding and a place to start to learn about workplace stress and what to do about it. The guide gives definitions, common causes of mental distress, legal frameworks (focusing on Ontario), possible actions to take, and resources available. It is an introduction and action guide created by workers for workers. These tools are not clinical diagnostic tools. They are not meant to diagnose medical or psychological conditions or to be used by a physician to these ends. These tools are designed to identify problems that may exist within the workplace and provide possible avenues to address them. This resource kit and tools are provided with a focus on the Ontario jurisdiction – workers in other provinces or in federally regulated workplaces should refer to their own legal framework. MIT First Edition 2012 Page 2 PART 5 — Workplace Action Plan Tip sheets for workers, JHSC members and union leaders can be found at the end of Part 5. The Case for Action Workers do all kinds of work and work within many different types of environments. Workers may work part time, full-time, contract, temporary, etc. And under the Occupational Health and Safety Act (1990), anyone collecting wages from an employer is defined as a worker. We as workers have good reasons to intervene and take action to improve the conditions of work that cause us mental distress. -
Health Impact of Psychosocial Hazards at Work: an Overview
Health Impact of Psychosocial Hazards at Work: An Overview Health Impact of Psychosocial Hazards at Work: An Overview Stavroula Leka BA MSc PhD CPsychol FRSPH Aditya Jain BA(H) MSc MA FRSPH Institute of Work, Health & Organisations, University of Nottingham Design & Layout: Philippos Yiannikouris WHO Library Cataloguing-in-Publication Data Health impact of psychosocial hazards at work: an overview / Stavroula Leka, Aditya Jain 1.Occupational health. 2.Risk management. 3.Workplace. 4.Psychology, Social. 5.Stress. 6.Risk assessment. I.Leka, Stavroula. II.Jain, A. III:World Health Organization. ISBN 978 92 4 150027 2 (NLM classification: WA 400) © World Health Organization 2010 All rights reserved. Publications of the World Health Organization can be obtained from WHO Press, World Health Organization, 20 Avenue Appia, 1211 Geneva 27, Switzerland (tel.: +41 22 791 3264; fax: +41 22 791 4857; e-mail: [email protected]). Requests for permission to reproduce or translate WHO publications – whether for sale or for noncommercial distribution – should be addressed to WHO Press, at the above address (fax: +41 22 791 4806; e-mail: [email protected]). The designations employed and the presentation of the material in this publication do not imply the expression of any opinion whatsoever on the part of the World Health Organization concerning the legal status of any country, territory, city or area or of its authorities, or concerning the delimitation of its frontiers or boundaries. Dotted lines on maps represent approximate border lines for which there may not yet be full agreement. The mention of specific companies or of certain manufacturers’ products does not imply that they are endorsed or recommended by the World Health Organization in preference to others of a similar nature that are not mentioned. -
Psychosocial Risks, Stress and Violence in the World of Work
INTERNATIONAL JOURNAL 2016 / Volume 8 / Issue 1–2 2016 / Volume OF LABOUR RESEARCH Psychosocial risks, stress and violence in the world of work 2016 / VOLUME 8 / ISSUE 1–2 Psychosocial risks, stress and violence in the world of work ILO International Journal of Labour Research 2016 Vol. 8 Issue 1–2 Psychosocial risks, stress and violence in the world of work INTERNATIONAL LABOUR OFFICE, GENEVA Copyright © International Labour Organization 2017 First published 2016 Publications of the International Labour Office enjoy copyright under Protocol 2 of the Uni- versal Copyright Convention. Nevertheless, short excerpts from them may be reproduced without authorization, on condition that the source is indicated. For rights of reproduction or translation, application should be made to ILO Publications (Rights and Licensing), International Labour Office, CH-1211 Geneva 22, Switzerland, or by email: [email protected]. The International Labour Office welcomes such applications. Libraries, institutions and other users registered with a reproduction rights organization may make copies in accordance with the licences issued to them for this purpose. Visit www.ifrro.org to find the reproduction rights organization in your country. International Journal of Labour Research Geneva, International Labour Office, 2017 ISSN 2076-9806 ILO Cataloguing in Publication Data The designations employed in ILO publications, which are in conformity with United Nations practice, and the presentation of material therein do not imply the expression of any opinion whatsoever on the part of the International Labour Office concerning the legal status of any country, area or territory or of its authorities, or concerning the delimitation of its frontiers. The responsibility for opinions expressed in signed articles, studies and other contributions rests solely with their authors, and publication does not constitute an endorsement by the International Labour Office of the opinions expressed in them. -
Environmental & Occupational Medicine
Environmental & Occupational Medicine Jānis Dundurs Environmental & Occupational Medicine Textbook for RSU foreign students Rīga RSU UDK 614.7 (075.8) + 613.6 (075.8) D 56 Dundurs, Jānis. Environmental and Occupational Medicine: Textbook for RSU foreign students. – Rīga: Rīga Stradiņš University, 2014. – 228 p. The book includes all of the most important issues of environmental and occupational medicine. As ecological parts of the environment, the air, water, settlements, as well as food toxicology, safety and quality assurance have been discussed. Some chapters are devoted to work environment and assessment of the effect of environmental risk factors on human body. The textbook has been written for international medical students. Environmental and occu pational medicine is closely related to other branches of environmental science and public health, therefore it may be used by many-branched environmental and public health specialists, envir onmental and work inspectors, ergonomists, ecologists and other interested groups. Head of the Publishing department: Tenis Nigulis Senior editor: Aija Lapsa Editor: Jānis Zeimanis Proof reader: Regīna Jozauska Layout design: Ilze Reitere Cover design: Mikus Čavarts RSU IPN No. 13-305 © Rīgas Stradiņa universitāte, 2014 Rīga, Dzirciema iela 16, LV 1007 ISBN 978-9984-793-62-7 Preface 5 PREFACE For many years, hygiene was a key discipline of preventive medicine with its roots in 2.5-thousand-year long history. In Latvia, Hygiene was one of the courses taught to future doctors since the establishment of the Faculty of Medicine in the early years of our country’s independence. During the years of Soviet occupation, teaching was carried out according to unified programmes that were limited only to some theoretical and practical aspects of hygiene recognized in the Soviet Union. -
Preventing and Managing Risks to Work-Related Psychological Health Contents
Workplace Health and Safety Queensland Preventing and managing risks to work-related psychological health Contents Psychosocial hazards and factors ................................................................3 Identifying and managing psychosocial hazards .........................................5 Critical success factors ................................................................................. 7 Job demands .................................................................................................9 Low job control ........................................................................................... 14 Poor support ............................................................................................... 16 Poor workplace relationships ..................................................................... 18 Low role clarity or role conflict ...................................................................20 Low recognition and reward ....................................................................... 21 Poor organisational justice ........................................................................23 Poor organisational change management .................................................25 Remote or isolated work ............................................................................. 27 Violent or traumatic events ........................................................................29 References .................................................................................................