19. Recovering the Tinsmith's
Total Page:16
File Type:pdf, Size:1020Kb
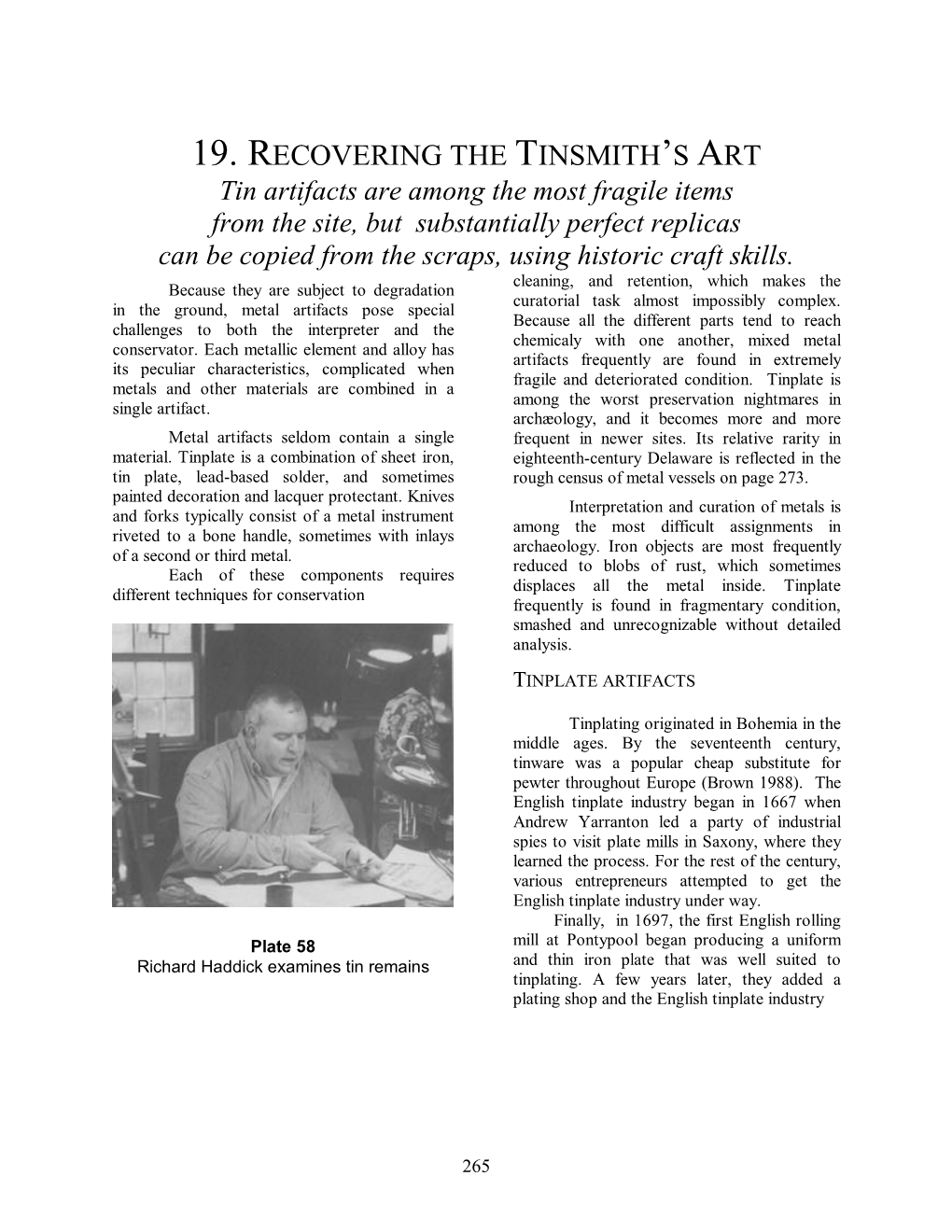
Load more
Recommended publications
-
UAW Ford Agreements Cvr 1Up.Indd 2 11/15/16 7:07 AM SKILLED TRADES AGREEMENTS and LETTERS of UNDERSTANDING
SKILLED TRADES AGREEMENTS AND LETTERS OF UNDERSTANDING between UAW® and the FORD MOTOR COMPANY Agreements Dated November 5, 2015 133 MICHIGAN (Effective November 23, 2015) ♲ printed on recycled paper PRINTED IN U.S.A. 64353-UAW Ford Skilled Trades Cvr 1up.indd 1 10/26/16 8:24 AM National Ford Department Staff 2015 Negotiations Jimmy Settles Vice President and Director UAW Ford, Aerospace, Chaplaincy and Insurance Greg Drudi Roy Escandon Angelique Peterson- Don Godfrey Jeffrey Faber Mayberry Brett Fox Ford Motor Company and the UAW recognize Darryl Nolen Gregory Poet Kenneth Gafa their respective responsibilities under federal Bob Tiseo Reggie Ransom and state laws relating to fair employment Phil Argento Michael Gammella Lorenzo Robinson practices. Tracy Ausen Raenell Glenn Michael Robison Carol Bagdady R. Brian Goff Nick Rutovic The Company and the Union recognize the Matthew Barnett Ruth Golden Angelo Sacino Monica Bass moral principles involved in the area of civil Jane Granger Les Shaw David Berry rights and have reaffirmed in their Collective Andre Green Michael Shoemaker Carlo Bishop Bargaining Agreement their commitment not Joe Gucciardo Casandra Shortridge Shawn Campbell to discriminate because of race, religion, color, Dan Huddleston Larry Shrader Jerry Carson age, sex, sexual orientation, union activity, Michael Joseph Garry Sommerville Alfonzo Cash Thomas Kanitz national origin, or against any employee with Jeffrey Terry Tiffany Coger Brandon Keatts disabilities. Kevin Tolbert Gerard Coiffard Michael Kerr Vaughan Tolliver Sean -
Welsh Acheivements Brochure
WELSH ACHIEVEMENTS [ IN SCIENCE, TECHNOLOGY AND ENGINEERING ] ‘Our vision in Wales is of a learning country, where highly- skilled and highly-qualified people are employed in high- technology, high added-value companies.’ Professor John Harries, first chief scientific adviser for Wales, speaking in 2011 at the Welsh universities collaboration, research knowledge and expertise programme – Welsh Crucible. This publication is also available electronically from business.wales.gov.uk/innovation To discuss your innovation needs please call Business Wales on 03000 6 03000 or visit business.wales.gov.uk. Print ISBN 978 1 4734 0171 6 Printed on recycled paper Digital ISBN 978 1 4734 0169 3 WG16613 / G/MH/4578 / 0813 © Crown copyright 2013 2 On a global scale Wales is a small, but smart country, in which every opportunity has been taken to optimise resources, designs and processes. Shaped by landscape and culture it made its mark on the world through the maximisation of the great natural mineral wealth found here. Wales continues to make its mark through in-depth scientific and technical understanding and commercial innovation. From the past to the present an impressive list of achievements, many of which are the first of their kind in the world, have given Wales a great momentum for the future. CONTENTS 02 Foreword 05 Bioscience and Health 13 The Built Environment 20 Telecommunications and ICT 26 Creative Industries 35 Energy 41 Engineering 45 Environmental Sciences 50 Materials 56 Transport 64 People 74 Milestones 86 Conclusion 1 The modern world is increasingly made up of the products of the application of science, technology and engineering. -
Journal of Milk Technology
'-/· .> Ί ' JOURNAL OF MILK TECHNOLOGY Volu 14 Number 2 MARCH-APRIL, 1941 Official Publication of International Association of Milk Sanitarians (Association Organized 1911) Alto designated publication of California Association of Dairy and Milk Inspectors Central States Milk Sanitarians Chicago Dairy Technology Society Connecticut Association of Dairy and Milk Inspectors Indianapolis Dairy Technology Club Massachusetts Milk Inspectors’ Association Metropolitan Dairy Technology Society Michigan Association of Dairy and Milk Inspectors Missouri Association of Milk Sanitarians New York State Association of Dairy and Milk Inspectors Pacific Northwest Association of Dairy and Milk Inspectors Pennsylvania Association of Dairy Sanitarians Philadelphia Dairy Technology Society Texas Association of Milk Sanitarians West Virginia Association of Milk Sanitarians II A dvertisements PERHAPS as a boy you took many a drink from it without a thought about how insanitary it might be. N ot so today. The patient work of sanitation and pub YOUR DAIRY CUSTOMERS can actually lic health officers has taught you to say see the safe protection of the Welded “nix” to the public drinking cup. And Wire Hood —and seeing is believing. their science, too, has solved many They recognize that you are safeguard problems of dairy sanitation—including ing their health when they see how you how to protect the pouring lip of your protect that pouring lip from contami sterilized milk and cream bottles. nation. Vet, even though the Hood is locked on with welded wire, it comes off HEALTH OFFICERS themselves say that quickly, without effort. they prefer the complete protection of the Welded Wire Hood Seal. It covers FREE INFORMATION-W rite for details the entire pouring lip and top against on Hood Capping and our interesting insanitary dust and filth. -
Commodity Master List
Commodity Master List 005 ABRASIVES 010 ACOUSTICAL TILE, INSULATING MATERIALS, AND SUPPLIES 015 ADDRESSING, COPYING, MIMEOGRAPH, AND SPIRIT DUPLICATING MACHINE SUPPLIES: CHEMICALS, INKS, PAPER, ETC. 019 AGRICULTURAL CROPS AND GRAINS INCLUDING FRUITS, MELONS, NUTS, AND VEGETABLES 020 AGRICULTURAL EQUIPMENT, IMPLEMENTS, AND ACCESSORIES (SEE CLASS 022 FOR PARTS) 022 AGRICULTURAL IMPLEMENT AND ACCESSORY PARTS 025 AIR COMPRESSORS AND ACCESSORIES 031 AIR CONDITIONING, HEATING, AND VENTILATING: EQUIPMENT, PARTS AND ACCESSORIES (SEE RELATED ITEMS IN CLASS 740) 035 AIRCRAFT AND AIRPORT, EQUIPMENT, PARTS, AND SUPPLIES 037 AMUSEMENT, DECORATIONS, ENTERTAINMENT, TOYS, ETC. 040 ANIMALS, BIRDS, MARINE LIFE, AND POULTRY, INCLUDING ACCESSORY ITEMS (LIVE) 045 APPLIANCES AND EQUIPMENT, HOUSEHOLD TYPE 050 ART EQUIPMENT AND SUPPLIES 052 ART OBJECTS 055 AUTOMOTIVE ACCESSORIES FOR AUTOMOBILES, BUSES, TRUCKS, ETC. 060 AUTOMOTIVE MAINTENANCE ITEMS AND REPAIR/REPLACEMENT PARTS 065 AUTOMOTIVE BODIES, ACCESSORIES, AND PARTS 070 AUTOMOTIVE VEHICLES AND RELATED TRANSPORTATION EQUIPMENT 075 AUTOMOTIVE SHOP EQUIPMENT AND SUPPLIES 080 BADGES, EMBLEMS, NAME TAGS AND PLATES, JEWELRY, ETC. 085 BAGS, BAGGING, TIES, AND EROSION CONTROL EQUIPMENT 090 BAKERY EQUIPMENT, COMMERCIAL 095 BARBER AND BEAUTY SHOP EQUIPMENT AND SUPPLIES 100 BARRELS, DRUMS, KEGS, AND CONTAINERS 105 BEARINGS (EXCEPT WHEEL BEARINGS AND SEALS -SEE CLASS 060) 110 BELTS AND BELTING: AUTOMOTIVE AND INDUSTRIAL 115 BIOCHEMICALS, RESEARCH 120 BOATS, MOTORS, AND MARINE AND WILDLIFE SUPPLIES 125 BOOKBINDING SUPPLIES -
Collecting Punched Tin Lanterns
Collecting Punched Tin Lanterns By Grant Hamilton Many of us who make an attempt to limit our lantern collections to models that were specifically used on railroads still find ourselves picking up interesting examples of other types of lighting. Many collections end up including non-railroad models from a favorite manufacturer, or unusual early lanterns. One such lantern is the punched or pierced tin lantern. Although use of these lanterns by railroads was probably very limited (oil lanterns with glass globes were widely available by the time railroads began regular night operations), it is not unlikely that some saw railroad service. In locations where a broken oil lamp or lantern created a greater fire hazard, a well enclosed candle lantern was needed. The punched tin lantern was also easier to produce in regions that were far removed from the major glass-making centers. They were also no doubt used on stage coaches, ships, and the other early modes of transportation. Regardless of where it was used, a pierced tin lantern makes a nice addition to any collection, and provides a connection to an early period in our country’s history. The following article is reprinted from the monthly New York - Pennsylvania Collector magazine, and provides an excellent overview of the history of this well-known form of early lighting. The punched (or pierced) tin lantern has been a symbol of Early America in many illustrations and serves as a colonial craft project for school groups and adults at interpretive historical sites. They are often misnamed “Paul Revere” lanterns in reference to the “one if by land, two if by sea” account of the famous signaling of the movement of British troops in Boston. -
Blacksmith Metalsmith Knifemaker Farrier •
Pieh Tool Company Pieh Tool Product Catalog Blacksmith Metalsmith Knifemaker Farrier • www.piehtoolco.com www.piehtoolco.com 888.743.4866 928.554.0700 $7 Pieh Tool Company is located in Arizona’s pristine Yavapai County, just minutes from captivating Sedona. We are in a country that is rich with metalsmiths, sculptors, artists and horse enthusiasts! We stock a variety of machinery, vises, power tools, saws, anvils, forges, fluxes, finishes, hammers, tongs, horseshoes, feed, nails, rivets, lag bolts, videos & hundreds of book titles. We serve blacksmiths, fabricators, knifemakers, jewelers, farriers, horseowners and hobbyists. The Pieh Legacy Collection™ demonstrates our commitment to quality blacksmith tools. Be sure to check out the Billy™ tongs, our new Ergonomic Hammer line, and other Pieh Tool products. We’re sure you will be Pieh Tool Company Distribution Center in Camp Verde, Arizona extremely satisfied! EDUCATION The "Bill Pieh Resource for Metalwork" offers educational opportunities to the metal working trades in the United States. Classes are held monthly. Reservations are required. SEMINARS Semi-annual demonstrations offer you an opportunity to learn from the masters in your craft. Be sure to visit the Calendar on our website for our schedule of events. CONVENIENCE Secure online shopping is available to you at www.piehtoolco.com. We ship worldwide. The following trademarks are owned by their respective companies; Pieh Tool Company: Pieh Legacy Collection, the Billy, the Bonnie; Radians: Radians AV; Rad Band, Thoro’Bred: Thoro’Bred, Queens Plate, Easy Care: Easy Boot Glove, Hoof Suspension; Equine Innovations: Hoofjack; Gene Ovnicek: Natural Balance; JET, WILTON, Powermatic: Milwaukee, Sawzall, Hackzall, Thunderbolt, M12, M18, Shockwave. -
Haywood's Historic Farmers Market 2016 Heritage Craft
HAYWOOD’S HISTORIC FARMERS MARKET 2016 HERITAGE CRAFT GUIDELINES Haywood’s Historic Farmers Market is dedicated to assisting local artisans in advancing their craft endeavors. One facet of this obligation is through the Jury process that provides critique and distinction for artisan work judged to be of the highest level of quality indicative of the Western North Carolina region and Appalachia’s fine heritage of creativity and workmanship. HERITAGE CRAFTS DEFINED: (as to inclusion in Haywood’s Historic Farmers Market) Crafts representative of the Appalachian heritage handmade and created within our local communities in a traditional manner, made predominately from materials that originate in the Western North Carolina region. PURPOSE: The purpose of Haywood’s Historic Farmers Market crafts initiative is to preserve and promote the history of Appalachian crafts, emphasizing the techniques and tools that mountain people used in everyday life. The market provides a venue where rural artists can sell culturally significant and quality heritage crafts that define the artistry and heritage of the region. CATEGORIES: BASKETRY: basket weaving, chair caning, brooms FIBER / TEXTILES: quilting, weaving, rug making (rag rugs), wall hangings (all from natural fibers), wearable fiber; dyes, spinning & looms GLASS: hand blown glassware and bowls LEATHER: cobblers, saddlers, and harness makers METALWORKING: blacksmith, bladesmith, tinsmith (copper), silversmith, goldsmith, rifle making MUSICAL INSTRUMENTS: dulcimers, drums, flutes, banjoes, fiddles ORGANIC MEDIA: gourds, dried floral, herbal wreaths, cornhusk crafts (toys, hats, purses, baskets, wreaths) POTTERY, CERAMICS and STONE: plates, containers, sculptural objects, sharpening stones WOOD and BAMBOO: turning, whittling, bending, carving, constructed wood, cabinetry, walking sticks ELIGIBILITY: In keeping with the above Purpose, all jury submissions must be produced by artisans residing in Haywood County, or counties contiguous to Haywood County within the State of North Carolina. -
Direct Match Title File, 2018
U.S. Bureau of Labor Statistics On behalf of the Office of Management and Budget (OMB) and the Standard Occupational Classification Policy Committee (SOCPC) November 2017 (Updated April 15, 2020) ***Questions should be emailed to soc@bls. -
Wales Heritage Interpretation Plan
TOUCH STONE GREAT EXPLANATIONS FOR PEOPLE AT PLACES Cadw Pan-Wales heritage interpretation plan Wales – the first industrial nation Ysgogiad DDrriivviinngg FFoorrcceess © Cadw, Welsh Government Interpretation plan October 2011 Cadw Pan-Wales heritage interpretation plan Wales – the first industrial nation Ysgogiad Driving Forces Interpretation plan Prepared by Touchstone Heritage Management Consultants, Red Kite Environment and Letha Consultancy October 2011 Touchstone Heritage Management Consultants 18 Rose Crescent, Perth PH1 1NS, Scotland +44/0 1738 440111 +44/0 7831 381317 [email protected] www.touchstone-heritage.co.uk Michael Hamish Glen HFAHI FSAScot FTS, Principal Associated practice: QuiteWrite Cadw – Wales – the first industrial nation / Interpretation plan i ____________________________________________________________________________________________________________________________________________________________________________ Contents 1 Foreword 1 2 Introduction 3 3 The story of industry in Wales 4 4 Our approach – a summary 13 5 Stakeholders and initiatives 14 6 Interpretive aim and objectives 16 7 Interpretive themes 18 8 Market and audiences 23 9 Our proposals 27 10 Interpretive mechanisms 30 11 Potential partnerships 34 12 Monitoring and evaluation 35 13 Appendices: Appendix A: Those consulted 38 Appendix B: The brief in full 39 Appendix C: National Trust market segments 41 Appendix D: Selected people and sites 42 The illustration on the cover is part of a reconstruction drawing of Blaenavon Ironworks by Michael -
Understanding Alloy Design Principles and Cast Metal Technology in Hot Molds for Medieval Bengal
Indian Journal of History of Science, 45.1 (2010) 101-140 UNDERSTANDING ALLOY DESIGN PRINCIPLES AND CAST METAL TECHNOLOGY IN HOT MOLDS FOR MEDIEVAL BENGAL BARNALI MANDAL*, PRANAB K. CHATTOPADHYAY**, DIPTEN MISRA+ AND PRASANTA K. DATTA++ (Received 9 September 2009; revised 17 November 2009) Two beautiful bronze images of medieval period unearthed in South Bengal have been investigated. After laser cleaning, material characterization was undertaken to reconstruct the technology as well as the knowledge base of metal workers. The bronze items were found to be cast product whose chemistry belongs to copper – zinc – lead system with small addition of tin. The use of copper-zinc alloy in place of copper-tin with addition of lead becomes quite significant in this respect and points towards developing a working knowledge for copper-alloy design. The analysis of microstructures signifies towards a casting technology, where, hot molds were used. For confirmation of the molds, some tribal metal casting operations were also investigated. The technology was then reconstructed in the laboratory and some casting as the facts were produced. Microstructures of all three types look almost similar leading to the conclusion that coppersmiths used hot clay molds for bronze production. Key words: Alloy-design, Bronze casting, Hot molds, Laser cleaning INTRODUCTION East Indian subcontinent has got a long history of using different metals from ancient time and a number of archaeological sites have been * Research Scholar: Department of Metallurgical & Material Engineering, Jadavpur University, Kolkata- 700 032. India, [email protected]. ** Centre for Archaeological Studies & Training, Eastern India, 4 Camac Street, Kolkata- 700 016. -
History of American Decorative Arts
History of American Decorative Arts Hudson #4 3/14/16 Minor Decorative Arts Metals Silver/gold Pewter Iron brass copper tin Glass Ceramics Textiles Metals: PRECIOUS—silver and gold, silversmith, goldsmith Formed by being cast in a mold or hand-wrought Decorated by being chased, engraved, turned, repoussed _________________________________________________ Cast handles Tankard 1690-1700 Boston MA John Coney Tankard 1670-80 Boston MA Sanderson Detail of cast handle return Detail of lid engraving C 1700 Boston 1680-90 Boston MA Winslow MA John Coney SUGAR BOXES C1700 Boston MA John Coney One of a pair of spoons c 1680 Boston MA John Coney Teaspoon c1785 Boston MA Paul Revere Serving Spoon c1750 Philadelphia PA Philip Syng Sauceboat c1790 Boston MA Benjamin Burt Pair of salts c 1760 Philadelphia PA George Dowig Wedding service 1773 Boston MA Teapot 1760-70 Baltimore MD G.Lewyn Paul Revere II Tea Kettle c1720 NYC Salver 1754-69 NY Daniel C Feuter Salver 1761 Boston MA Paul Revere II Cake Basket 1754-69 NY Daniel Feuter Ale Jug 1755-75 NY Myer Myers Coffee Pot c1753 Philadelphia Philip Syng Pair of Candlesticks c 1710 Boston MA John Coney (cast) Pair of Candlesticks c1790 Philadelphia PA Joseph + Nathaniel Richardson Tea Set 1793 Boston MA Paul Revere II Pair of sauceboats 1808-19 Philadelphia PA Anthony Rasch Tureen 1809-45 NY William Thomson Tea Set c1888 NYC Tiffany + Co , enamel and silver Ewer, tray, chalice 1850s NY gold Francis Cooper + Fisher Arts & Crafts jar BASE METALS (any metals not precious) blacksmith, tinsmith Formed by casting, -
Construction Labor Market Analyzer (CLMA) Construction Disciplines, Definitions & Titles
Construction Labor Market Analyzer (CLMA) Construction Disciplines, Definitions & Titles CLMA Craft / Engineering / Project Discipline Definition Discipline Example Titles Code* Controls Discipline Boilermaker, Boiler Fitter, Boiler Installer, Construction Boilermakers fabricate, assemble, erect, test, maintain and repair boilers, vessels, 472011 Boilermaker Boilermaker, Industrial Boilermaker, Marine Boilermaker, Pressure tanks, towers, heat exchangers and other heavy-metal structures. Vessel Fabricator Boilermaker Welders weld piping and other heavy-metal structures in support of 472011.1 Boilermaker Welder Boildermaker Welder, Boildermaker Welder Fitter boilermaker work operations. MIG welding uses a feed wire which constantly moves through the gun to create 472011.2 Boilermaker Welder (Mig) Boildermaker Welder, Boildermaker Welder Fitter, Mig Welder spark and melts to form the weld. 472011.3 Boilermaker Welder (Tig) TIG welding uses long rods to fuse two metals directly together. Boildermaker Welder, Boildermaker Welder Fitter, Tig Welder Bricklayers lay bricks, concrete blocks, stone and other similar materials to construct or repair walls, arches, chimneys, fireplaces and other structuresin accordance with Bricklayer, Brickmason, Refractory Bricklayer, Stonecutter, 472021 Bricklayer / Blockmason blueprints and specifications. Segmental pavers cut, place, and arrange a variety of Blockmason, Stonemason, Segmental Pavers finished masonry such as brick and concrete in order to create paths, patios, driveways, and steps. Carpenter,