Brazing Alloys
Total Page:16
File Type:pdf, Size:1020Kb
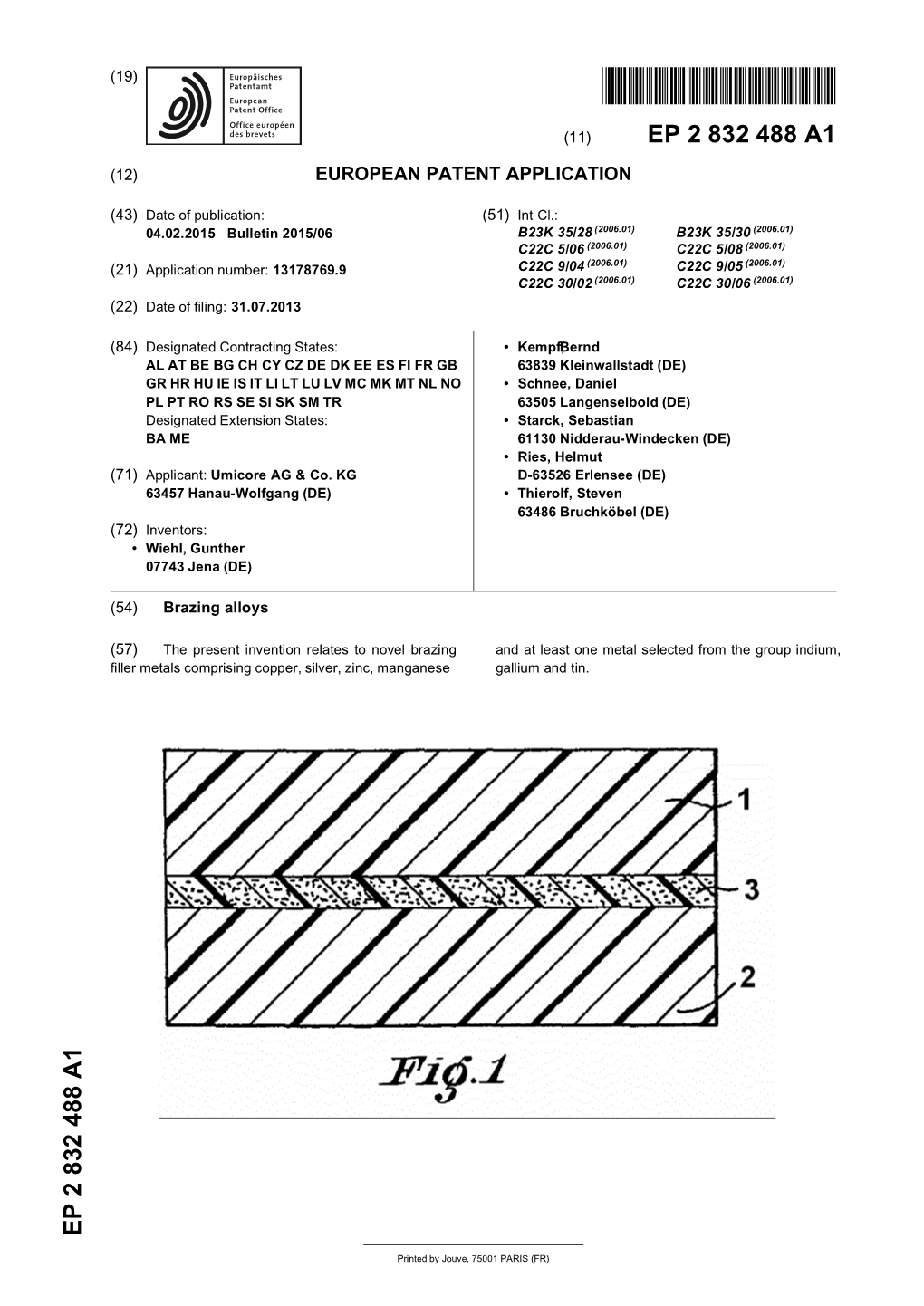
Load more
Recommended publications
-
Aluminum Brazing with Non-Corrosive
Aluminium Brazing with Non-corrosive Fluxes State of the Art and Trends in NOCOLOK® Flux Technology Dr. Hans – Walter Swidersky Solvay Fluor und Derivate GmbH Hans-Boeckler-Allee 20 – 30173 Hanover, Germany Presented at the 6th International Conference on Brazing, High Temperature Brazing and Diffusion Bonding (LÖT 2001), Aachen, Germany (May 2001) – Revised Text Abstract This paper summarises the general development and the current status of aluminium brazing with non-corrosive fluxes. Based on the most common manufacturing practices, present-day brazing operations are described. Numerous improvements to aluminium brazing technology have been made in recent years. The most significant devel- opments and trends are addressed, particularly process reengineering (e.g., cleaning, flux application), cost savings (e.g., water, flux, energy), and aluminium alloy improvements (e.g., high strength, good formability, and long-life). Table of contents Success or failure in CAB production relies on several • Introduction factors. The starting point is good product fit-up. Parts 1. Cleaning and Flux Application to be metallurgically joined must have intimate contact 2. Flux Application Methods at some point along the joint. An adequate (but not 3. Wet Flux Application excessive) quantity of filler metal must be available to 4. Dry/ Electrostatic Flux Application fill the joints. Capillary forces pull the filler into the 5. Post Braze Flux Residue joints. The gap tolerance is 0.1 to 0.15 mm for non-clad 6. Filler Metal Alloys components. When clad products are used, intimate 7. Brazing Alloys and Brazing Sheet contact is recommended; the clad layer(s) will act as a 8. -
Effect of Forming Temperature and Sheet Temper on the Brazing Characteristics of Aluminum Alloy Sheet
Effect of Forming Temperature and Sheet Temper on the Brazing Characteristics of Aluminum Alloy Sheet by Michael J. Benoit A thesis presented to the University of Waterloo in fulfillment of the thesis requirement for the degree of Doctor of Philosophy in Mechanical and Mechatronics Engineering Waterloo, Ontario, Canada, 2018 © Michael J. Benoit 2018 Examining Committee Membership The following served on the Examining Committee for this thesis. The decision of the Examining Committee is by majority vote. External Examiner DAVID WILKINSON Distinguished University Professor, McMaster University Supervisor MARY WELLS Professor, University of Waterloo Supervisor CAROLYN HANSSON Professor, University of Waterloo Internal Member NORMAN ZHOU Professor, University of Waterloo Internal Member MICHAEL WORSWICK Professor, University of Waterloo Internal-external Member ALEXANDER PENLIDIS Professor, University of Waterloo ii Author’s Declaration This thesis consists of material all of which I authored or co-authored: see Statement of Contributions included in the thesis. This is a true copy of the thesis, including any required final revisions, as accepted by my examiners. I understand that my thesis may be made electronically available to the public. iii Statement of Contributions The research contained within this thesis was conducted as part of a Natural Sciences and Engineering Research Council of Canada Collaborative Research and Development grant (NSERC CRD), in collaboration with Dana Canada Corporation and CanmetMATERIALS. Furthermore, the results presented in Chapters 3 to 6 have been adapted from manuscripts which are published, or are to be published. As a result, a number of co-authors have contributed to the current work. However, all measurements which were not performed by me were conducted either under my direct supervision, or were co-ordinated by me. -
Hand-Forging and Wrought-Iron Ornamental Work
This is a digital copy of a book that was preserved for generations on library shelves before it was carefully scanned by Google as part of a project to make the world’s books discoverable online. It has survived long enough for the copyright to expire and the book to enter the public domain. A public domain book is one that was never subject to copyright or whose legal copyright term has expired. Whether a book is in the public domain may vary country to country. Public domain books are our gateways to the past, representing a wealth of history, culture and knowledge that’s often difficult to discover. Marks, notations and other marginalia present in the original volume will appear in this file - a reminder of this book’s long journey from the publisher to a library and finally to you. Usage guidelines Google is proud to partner with libraries to digitize public domain materials and make them widely accessible. Public domain books belong to the public and we are merely their custodians. Nevertheless, this work is expensive, so in order to keep providing this resource, we have taken steps to prevent abuse by commercial parties, including placing technical restrictions on automated querying. We also ask that you: + Make non-commercial use of the files We designed Google Book Search for use by individuals, and we request that you use these files for personal, non-commercial purposes. + Refrain from automated querying Do not send automated queries of any sort to Google’s system: If you are conducting research on machine translation, optical character recognition or other areas where access to a large amount of text is helpful, please contact us. -
Brazing Compilation of Literature References from 1973 to 1978
OCTOBER 1979 BRAZING COMPILATION OF LITERATURE REFERENCES FROM 1973 TO 1978. BY J.C. RÖMER N et hf^rlfi rids E norqy R o soa re h \ oundation ECN does not assume any liability with respect to the use of, or for damages resulting from the use of any information, apparatus, method or process disclosed in this document. Netherlands Energy Research Foundation ECN P.O. Box 1 1755 ZG Petf.n(NH) The Netherlands Telephone (0)2246 - 62».. Telex 57211 ECN-7* OCTOBER 1979 BRAZING COMPILATION OF LITERATURE REFERENCES FROM 1973 T01978. BY J.C. ROMER -2- ABSTRACT This report is a compilation of published literature on high temperature brazing covering the period 1973-1978. The references are listed alphabetically with regard to the base material or combination of base materials to be brazed. Trade names are treated as base materials. The report contains approximately 1500 references, of which 300 are to patents. KEYWORDS BRAZING BRAZING ALLOYS FILLER METALS JOINING - 3 CONTENTS ABSTRACT 1. ALUMINIUM 2. ALUMINIUM (FLVXLESS) 3. ALUMINIUM - BERYLLIUM 4. ALUMINIUM/BORON COMPOSITES 5. ALUMINIUM - COPPER 5.1. Aluminium - graphite 5.2. Aluminium - nickel alloys 5.3. Aluminium - niobium 5.4. Aluminium ~ molyldenum 5.5. Aluminium - stainless steel 5.6. Aluminium - steels 5.7. Aluminium - tantalum 5.8. Aluminium - titanium 5.9. Aluminium - tungsten 6. BERYLLIUM 7. BORONNITRIDE• 8. BRASS 8.1. Brass - aluminium 8.2. Brass - steels 9. BRONZE 9.1. Bronze - stainless steels 10. CERAMICS 10.1. Ceramics - metal - 4 - CERMETS 61 11.1. Cermets - stainless steels 62 COBALT 63 COPPER ALLOYS 64 13.1. Copper alloys - brass 68 13.2. -
Punching Tools
TruServices Punching Tools Order easily – with the correct specifica- tions for the right tool. Have you thought of everything? Machine type Machine number Tool type Dimensions or drawings in a conventional CAD format (e.g. DXF) Sheet thickness Material Quantity Desired delivery date Important ordering specifications ! Please observe the "Important ordering specifications" on each product page as well. Order your punching tools securely and conveniently 24 hours a day, 7 days a week in our E-Shop at: www.trumpf.com/mytrumpf Alternatively, practical inquiry and order forms are available to you in the chapter "Order forms". TRUMPF Werkzeugmaschinen GmbH + Co. KG International Sales Punching Tools Hermann-Dreher-Strasse 20 70839 Gerlingen Germany E-mail: [email protected] Homepage: www.trumpf.com Content Order easily – with the correct specifica- General information tions for the right tool. TRUMPF System All-round Service Industry 4.0 MyTRUMPF 4 Have you thought of everything? Machine type Punching Machine number Classic System MultiTool Tool type Cluster tools MultiUse Dimensions or drawings in a conventional CAD format (e.g. DXF) 12 Sheet thickness Material Cutting Quantity Slitting tool Film slitting tool Desired delivery date MultiShear 44 Important ordering specifications ! Please observe the "Important ordering specifications" on each product page as well. Forming Countersink tool Thread forming tool Extrusion tool Cup tool 58 Marking Order your punching tools securely and conveniently 24 hours a day, 7 days a week in our E-Shop at: Center punch tool Marking tool Engraving tool Embossing tool www.trumpf.com/mytrumpf 100 Alternatively, practical inquiry and order forms are available to you in the chapter "Order forms". -
ALUXCOR 4047 Aluminum Flux Cored Braze Filler Metal
TECHNICAL INFORMATION SHEET ™ ALUXCOR 4047 ALUMINUM FLUX CORED BRAZE FILLER METAL DESCRIPTION Brazing Range 1080°F- 1120°F (582°C - 605°C) Electrical Conductivity: 40 (%IACS) Aluxcor 4047 flux cored brazing wire is designed for manual and Weight in ft./lb. (0.090 dia.) 184.5 semi-automatic aluminum flame brazing. A common application is brazing HVAC aluminum components including return bends, AVAILABLE FORMS headers, tube assemblies, and distributors. The flux core eliminates the need for a separate flux application and the core Standard diameters in coils, rods, spools, and formed rings. cross section is designed to release a measured amount of flux into the capillary. This ensures good oxidation protection and SPECIFICATION COMPLIANCE suitable capillary fill by the melted aluminum metal. Metal – AWS A5.8 Classification BAlSi-4 Aluxcor 4047 is available with different flux compositions. Each ISO 17672 Code Al 112 flux chemistry and ratio is designed to provide brazing Flux – Conforms to Harris Products Group engineering standard characteristics engineered for your specific application. for cored brazing material. Formula 15.1 is a potassium fluroaluminate salt with a SAFETY INFORMATION melting range of 1049 ° - 1061° F, (564° - 572°C). WARNING: PROTECT yourself and others. Read and understand this Formulas 15.2, 15.3 and 15.4 are cesium fluoroaluminate information. blends which lower flux activity temperature and corresponding FUMES AND GASES can be hazardous to your health. brazing temperature. Inclusion of this compound also allows HEAT RAYS, (infrared radiation) from flame or hot metal can injure eyes. brazing of magnesium containing base metals like 6063. Before use, read and understand the manufacturer’s instructions, Material Safety Data Sheets (MSDS), and your All flux core compositions are non-hygroscopic so post braze employer's safety practices. -
Soldering and Brazing of Copper and Copper Alloys Contents
Soldering and brazing of copper and copper alloys Contents 1. Introduction 4 5. Quality assurance 47 2. Material engineering fundamentals 9 6. Case studies 48 2.1. Fundamentals of copper and copper alloys 9 6.1 Hot-air solder levelling of printed circuit boards 48 2.2 Filler materials 10 6.2 Strip tinning 49 2.2.1 Soft solder 11 6.3 Fabricating heat exchangers from copper 49 2.2.2 Brazing filler metals 13 6.4 Manufacture of compact high-performance 2.3 Soldering or brazing pure copper 16 radiators from copper 49 2.4 Soldering / brazing copper alloys 18 2.4.1 Low-alloyed copper alloys 18 7. Terminology 50 2.4.2. High-alloyed copper alloys 22 8. Appendix 51 3. Design suitability for soldering/brazing 26 References 57 4. Soldering and brazing methods 29 Index of figures 58 4.1 The soldering/brazing principle 29 4.2 Surface preparation 30 Index of tables 59 4.3 Surface activation 32 4.3.1 Fluxes 33 4.3.2 Protective atmosphere / Shielding gases 35 4.4 Applying the solder or brazing filler metal 36 4.5. Soldering and brazing techniques 37 4.5.1 Soldering with soldering iron 38 4.5.2 Dip bath soldering or brazing 38 4.5.3 Flame soldering or brazing 40 4.5.4 Furnace soldering or brazing 40 4.5.5 Electric resistance soldering or brazing 43 4.5.6 Induction soldering or brazing 44 4.5.7 Electron beam brazing 45 4.5.8 Arc brazing 45 4.5.9 Laser beam soldering or brazing 46 2 | KUPFERINSTITUT.DE List of abbreviations Abbreviations Nd:YAG laser Neodymium-doped yttrium aluminium garnet laser SMD Surface-mounted device PVD Physical vapour deposition RoHS -
Effect of Homogenization on Recrystallization and Precipitation
Materials Transactions, Vol. 49, No. 2 (2008) pp. 250 to 259 #2008 The Japan Institute of Metals Effect of Homogenization on Recrystallization and Precipitation Behavior of 3003 Aluminum Alloy Hsin-Wen Huang, Bin-Lung Ou and Cheng-Ting Tsai Department of Mechanical Engineering, National Central University, Chung-Li, Taiwan 320, R.O. China This investigation studies 3003 aluminum alloys for automobile heat exchangers. The effects of precipitation in homogenization treatments, recrystallization in extrusion and brazing on extrusion forming ability and final material properties are examined. At first, fine second phase particles were precipitated during the 460C Â 9 h homogenization treatment and coarse particles were precipitated by homogenization treatments with 600C Â 9 h. Second, when the precipitation were not plentiful and fine enough during extrusion, the amount of solution dominated the extrusion breakout pressure, and recrystallization was easier; on the contrary, the domination state was replaced by plentiful and fine precipitated particles, and recrystallization became more difficult. Additionally, the hardness after extrusion was lower in the complete recrystallization position, and higher in the incomplete recrystallization position. Finally, in brazing, the sample under the 460C Â 9h condition (a) underwent full recrystallization from partial recrystallization with a reduction in strength; the local position of the edge of the sample under the 600C Â 9h ! 460C Â 3 h condition (c) exhibited a second recrystallization and a significant drop in hardness. [doi:10.2320/matertrans.MRA2007615] (Received June 19, 2007; Accepted November 26, 2007; Published January 25, 2008) Keywords: 3003 aluminum alloy, homogenization, precipitation, extrusion, brazing, recrystallization, second recrystallization 1. Introduction brazing were determined. -
The Brazing Guide GH Induction Atmospheres
The Brazing Guide GH Induction Atmospheres Turnkey Heating Solutions GH Induction Atmospheres • 35 Industrial Park Circle, Rochester New York 14624 USA • Tel: 585.368.2120 • Fax: 585.368.2123 • [email protected] • www.inductionatmospheres.com The Brazing Guide Brazing is a method of joining two pieces of metal together with a third, molten filler metal. Of all the methods available for metal joining, brazing may be the most versatile. The process is relatively fast and economical, requires relatively low temperatures and is highly adaptable to automation and lean manufacturing initiatives. Brazed joints have great tensile strength – they are often stronger than the two metals being bonded together. Brazed joints repel gas and liquid, withstand vibration and shock and are unaffected by normal changes in temperature. Because the metals to be joined are not themselves melted, they are not warped or otherwise distorted and retain their original metallurgical characteristics. Use this guide to learn about the different aspects of brazing and the many advantages offered by this unique process. Brazing Overview ..............................................................................................pg 2 Topics include brazing basics, when brazing works best, heat sources for brazing and types of braze joints. Basic Procedures .......................................................................................................pg 4 Describes the basic process and offers recommendations to improve your brazing techniques. Induction Brazing ...............................................................................................pg -
Boilermaking Manual. INSTITUTION British Columbia Dept
DOCUMENT RESUME ED 246 301 CE 039 364 TITLE Boilermaking Manual. INSTITUTION British Columbia Dept. of Education, Victoria. REPORT NO ISBN-0-7718-8254-8. PUB DATE [82] NOTE 381p.; Developed in cooperation with the 1pprenticeship Training Programs Branch, Ministry of Labour. Photographs may not reproduce well. AVAILABLE FROMPublication Services Branch, Ministry of Education, 878 Viewfield Road, Victoria, BC V9A 4V1 ($10.00). PUB TYPE Guides Classroom Use - Materials (For Learner) (OW EARS PRICE MFOI Plus Postage. PC Not Available from EARS. DESCRIPTORS Apprenticeships; Blue Collar Occupations; Blueprints; *Construction (Process); Construction Materials; Drafting; Foreign Countries; Hand Tools; Industrial Personnel; *Industrial Training; Inplant Programs; Machine Tools; Mathematical Applications; *Mechanical Skills; Metal Industry; Metals; Metal Working; *On the Job Training; Postsecondary Education; Power Technology; Quality Control; Safety; *Sheet Metal Work; Skilled Occupations; Skilled Workers; Trade and Industrial Education; Trainees; Welding IDENTIFIERS *Boilermakers; *Boilers; British Columbia ABSTRACT This manual is intended (I) to provide an information resource to supplement the formal training program for boilermaker apprentices; (2) to assist the journeyworker to build on present knowledge to increase expertise and qualify for formal accreditation in the boilermaking trade; and (3) to serve as an on-the-job reference with sound, up-to-date guidelines for all aspects of the trade. The manual is organized into 13 chapters that cover the following topics: safety; boilermaker tools; mathematics; material, blueprint reading and sketching; layout; boilershop fabrication; rigging and erection; welding; quality control and inspection; boilers; dust collection systems; tanks and stacks; and hydro-electric power development. Each chapter contains an introduction and information about the topic, illustrated with charts, line drawings, and photographs. -
Brazing Student Guide
STUDENT GUIDE DISCLAIMER This reference material is intended as collateral support for this course. This material has been assembled as part of a comprehensive training program in order to provide a common base of technical knowledge for the class participant. This material is not intended for use as a field operating manual nor is it intended as a substitute for any process instruction or standard operating or company safety procedures. The sample content of this notebook represents the information available from companies that provide brazing and cast iron repairs. ESW, Inc. assumes no liability for its accuracy, completeness or contents. 2 Tabs & Table of Contents 1 Safety 2 Tensile testing terms 3 Guidelines for welding cast iron 4 Types of cast iron 5 Welding of cast iron 6 Expansion & Contraction 7 Pre-heating & welding procedures 8 Torch tip size charts 9 Troubleshooting Victor torches 10 Guide to Oxy-Acetylene welding equipment 11 The Braze Book 12 Ref. 3 SAFETY The following is a list of some safety items that should be followed when using an Oxy- Acetylene outfit. 1. Never use Acetylene gas at a pressure over 15 psig. 2. Never use damaged equipment. 3. Never use oil or grease on or around Oxygen equipment. 4. Never use Oxygen or fuel gas to blow dirt or dust off clothing or equipment. 5. Never light a torch with matches or a lighter. Always use a striker. 6. When opening a Oxygen or fuel cylinder valve, always crack it open first. 7. Always make sure regulators have their adjusting screws released by turning them counter clockwise till free before opening cylinder valves. -
Improvement of Punch and Die Life and Part Quality in Blanking of Miniature Parts
Improvement of Punch and Die Life and Part Quality in Blanking of Miniature Parts DISSERTATION Presented in Partial Fulfillment of the Requirements for the Degree Doctor of Philosophy in the Graduate School of The Ohio State University By Soumya Subramonian Graduate Program in Mechanical Engineering The Ohio State University 2013 Dissertation Committee: Dr.Taylan Altan, Advisor Dr.Blaine Lilly, Advisor Dr.Gary L.Kinzel Dr.Jerald Brevick Abstract Blanking or piercing is one of the most commonly used sheet metal manufacturing processes in the industry. Having a good understanding of the fundamentals and science behind this high deformation shearing process can help to improve the tool life and blanked edge quality in various ways. Finite Element Modeling of the blanking process along with experimental testing is used in this study to study the influence of various process parameters on punch and die life and blanked edge quality. In high volume blanking and blanking of high strength materials, improving the tool life can save not only tool material but also change over time which can take up to a few hours for every change over. The interaction between punch, stripper plate and sheet material is first studied experimentally since a fundamental understanding of the behavior of these components at different blanking speeds is very essential to design robust tooling for high speeds. A methodology is developed using the experimentally obtained blanking load and FEM of blanking to obtain flow stress data of the sheet material at high strains and strain rates. This flow stress data is used to investigate the effects of various process parameters on tool stress and blanked edge quality.