Motor / Actuator
Total Page:16
File Type:pdf, Size:1020Kb
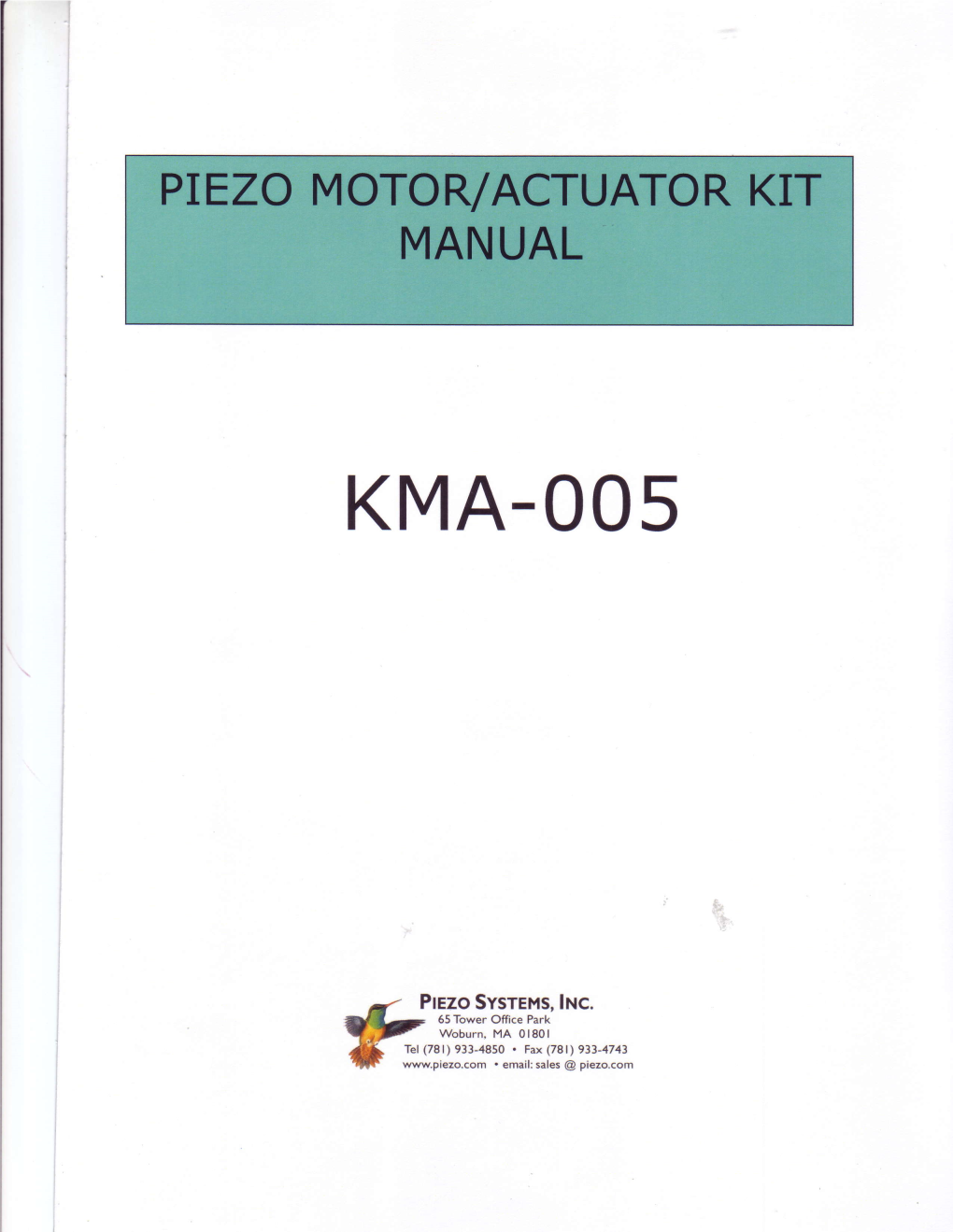
Load more
Recommended publications
-
DESIGN, CONTROL, and APPLICATION of PIEZOELECTRIC ACTUATOR External-Sensing and Self-Sensing Actuator
DESIGN, CONTROL, AND APPLICATION OF PIEZOELECTRIC ACTUATOR External-Sensing and Self-Sensing Actuator ANDI SUDJANA PUTRA NATIONAL UNIVERSITY OF SINGAPORE 2008 DESIGN, CONTROL, AND APPLICATION OF PIEZOELECTRIC ACTUATOR External-Sensing and Self-Sensing Actuator ANDI SUDJANA PUTRA (B.Eng., Brawijaya University, M.T.D., National University of Singapore) A THESIS SUBMITTED FOR THE DEGREE OF DOCTOR OF PHILOSOPHY DEPARTMENT OF ELECTRICAL AND COMPUTER ENGINEERING NATIONAL UNIVERSITY OF SINGAPORE 2008 Acknowledgements I would like to express my sincere appreciation to all who have helped me during my candidature; without whom my study here would have been very much different. First and foremost, I thank my supervisors: Associate Professor Tan Kok Kiong and Associate Professor Sanjib Kumar Panda, who have provided invaluable guidance and suggestion, as well as inspiring discussions. With their enthusiasm and efforts in explaining things clearly, they have made research a fun and fruitful activity. I would have been lost without their direction. I would also like to thank the National University of Singapore for providing me with scholarship and research support; without which it would have been impossible to finish my study here. It is difficult to overstate my gratitude to the officers and students in Mechatronics and Automation Laboratory, who have also become my friends. Dr. Huang Sunan, Dr. Tang Kok Zuea, Dr. Zhao Shao, Dr. Teo Chek Sing, and Mr. Tan Chee Siong have always been very supportive and encouraging through the easy and difficult time during my research. I am indebted to many more colleagues in Faculty of Engineering and Faculty of Medicine, whose names, regrettably, I cannot mention all here. -
Course Description Bachelor of Technology (Electrical Engineering)
COURSE DESCRIPTION BACHELOR OF TECHNOLOGY (ELECTRICAL ENGINEERING) COLLEGE OF TECHNOLOGY AND ENGINEERING MAHARANA PRATAP UNIVERSITY OF AGRICULTURE AND TECHNOLOGY UDAIPUR (RAJASTHAN) SECOND YEAR (SEMESTER-I) BS 211 (All Branches) MATHEMATICS – III Cr. Hrs. 3 (3 + 0) L T P Credit 3 0 0 Hours 3 0 0 COURSE OUTCOME - CO1: Understand the need of numerical method for solving mathematical equations of various engineering problems., CO2: Provide interpolation techniques which are useful in analyzing the data that is in the form of unknown functionCO3: Discuss numerical integration and differentiation and solving problems which cannot be solved by conventional methods.CO4: Discuss the need of Laplace transform to convert systems from time to frequency domains and to understand application and working of Laplace transformations. UNIT-I Interpolation: Finite differences, various difference operators and theirrelationships, factorial notation. Interpolation with equal intervals;Newton’s forward and backward interpolation formulae, Lagrange’sinterpolation formula for unequal intervals. UNIT-II Gauss forward and backward interpolation formulae, Stirling’s andBessel’s central difference interpolation formulae. Numerical Differentiation: Numerical differentiation based on Newton’sforward and backward, Gauss forward and backward interpolation formulae. UNIT-III Numerical Integration: Numerical integration by Trapezoidal, Simpson’s rule. Numerical Solutions of Ordinary Differential Equations: Picard’s method,Taylor’s series method, Euler’s method, modified -
Piezoelectric Inertia Motors—A Critical Review of History, Concepts, Design, Applications, and Perspectives
Review Piezoelectric Inertia Motors—A Critical Review of History, Concepts, Design, Applications, and Perspectives Matthias Hunstig Grube 14, 33098 Paderborn, Germany; [email protected] Academic Editor: Delbert Tesar Received: 26 November 2016; Accepted: 18 January 2017; Published: 6 February 2017 Abstract: Piezoelectric inertia motors—also known as stick-slip motors or (smooth) impact drives—use the inertia of a body to drive it in small steps by means of an uninterrupted friction contact. In addition to the typical advantages of piezoelectric motors, they are especially suited for miniaturisation due to their simple structure and inherent fine-positioning capability. Originally developed for positioning in microscopy in the 1980s, they have nowadays also found application in mass-produced consumer goods. Recent research results are likely to enable more applications of piezoelectric inertia motors in the future. This contribution gives a critical overview of their historical development, functional principles, and related terminology. The most relevant aspects regarding their design—i.e., friction contact, solid state actuator, and electrical excitation—are discussed, including aspects of control and simulation. The article closes with an outlook on possible future developments and research perspectives. Keywords: inertia motor; stick-slip motor; smooth impact drive; piezeoelectric motor; review 1. Introduction Piezoelectric actuators have long been used in diverse applications, especially because of their short response time and high resolution. The major drawback of these solid state actuators in positioning applications is their small stroke: actuators made of state-of-the-art lead zirconate titanate (PZT) ceramics only reach strains up to 2 . A typical piezoelectric actuator with 10 mm length thus reaches a maximum stroke of only 20 µm.h Bending actuator designs [1] and other mechanisms [2] can increase the stroke at the expense of stiffness and actuation force ([3]; [4] (pp. -
Brushless DC Electric Motor
Please read: A personal appeal from Wikipedia author Dr. Sengai Podhuvan We now accept ₹ (INR) Brushless DC electric motor From Wikipedia, the free encyclopedia Jump to: navigation, search A microprocessor-controlled BLDC motor powering a micro remote-controlled airplane. This external rotor motor weighs 5 grams, consumes approximately 11 watts (15 millihorsepower) and produces thrust of more than twice the weight of the plane. Contents [hide] 1 Brushless versus Brushed motor 2 Controller implementations 3 Variations in construction 4 AC and DC power supplies 5 KM rating 6 Kv rating 7 Applications o 7.1 Transport o 7.2 Heating and ventilation o 7.3 Industrial Engineering . 7.3.1 Motion Control Systems . 7.3.2 Positioning and Actuation Systems o 7.4 Stepper motor o 7.5 Model engineering 8 See also 9 References 10 External links Brushless DC motors (BLDC motors, BL motors) also known as electronically commutated motors (ECMs, EC motors) are electric motors powered by direct-current (DC) electricity and having electronic commutation systems, rather than mechanical commutators and brushes. The current-to-torque and frequency-to-speed relationships of BLDC motors are linear. BLDC motors may be described as stepper motors, with fixed permanent magnets and possibly more poles on the rotor than the stator, or reluctance motors. The latter may be without permanent magnets, just poles that are induced on the rotor then pulled into alignment by timed stator windings. However, the term stepper motor tends to be used for motors that are designed specifically to be operated in a mode where they are frequently stopped with the rotor in a defined angular position; this page describes more general BLDC motor principles, though there is overlap. -
Gradniki in Tehnologije V Sistemih Vodenja
Univerza v Ljubljani Fakulteta za elektrotehniko Alesˇ Belicˇ Gradniki in tehnologije v sistemih vodenja Ljubljana 22. januar 2012 2 3 Predgovor Obravnava snovi pri predmetih Gradniki v sistemih vodenja na Univerzitetnem studijskemˇ programu in Gradniki v tehnologiji vodenja na visokosolskemˇ strokovnem studijskemˇ pro- gramu Fakultete za elektrotehniko Univerze v Ljubljani je nekoliko drugacnaˇ kot pri ostalih predmetih na smeri Avtomatika. Cepravˇ sta to dva od osnovnih predmetov na smereh, pa se vendarle ne navezujeta cistoˇ neposredno na ostale predmete na studijskihˇ programih Avto- matike. Ucbenikˇ obravnava prakticneˇ in izvedbene vidike sistemov vodenja, ki ostanejo pri poglobljeni obravnavi algoritmov vodenja mnogokrat v ozadju. Izbira ustreznih merilnih sistemov, krmilnikov ali regulatorjev ter izvrsnihˇ sistemov, ki pokrijejo potrebe po mociˇ in preciznosti vodenja, je kljucnaˇ za kvalitetno izvedbo vodenja. Ne glede na dobro nacrtanoˇ shemo vodenja, je na koncu vse odvisno od izvedbe. V praksi je delezˇ vlozenegaˇ dela v resnici mocnoˇ na strani izvedbenih problemov sistema vodenja, medtem ko se algoritmom vodenja posvetimo seleˇ proti koncu izvedbe, ko je obicajnoˇ premalo casa,ˇ da bi algoritem in njegove parametre optimalno nastavili. Pomen snovi tega predmeta za izvedbo sistemov vodenja je torej nesporen. Po drugi strani pa je to predmet, ki zahteva precej ucenjaˇ na pa- met, saj je potrebno sirokoˇ poznavanje moznihˇ podsistemov in principov delovanja. Snov, ki je zbrana v tej knjigi je plod lastnih izkusenjˇ avtorja na tem podrocjuˇ s pomembnimi pri- spevki prof. dr. Riharda Karbe, prof. dr. Jusaˇ Kocijana, prof. dr. Maje Atanasijevic-Kunc,´ doc. dr. Gregorja Klancarjaˇ in dr. Janka Petrovciˇ ca,ˇ ki zeˇ dolga leta sodelujejo na temah, ki jih predmet obravnava. -
Hoofdblad IE Nummer 49/19 4 December
Nummer 49/19 04 december 2019 Nummer 49/19 2 04 december 2019 Inleiding Introduction Hoofdblad Patent Bulletin Het Blad de Industriële Eigendom verschijnt The Patent Bulletin appears on the 3rd working op de derde werkdag van een week. Indien day of each week. If the Netherlands Patent Office Octrooicentrum Nederland op deze dag is is closed to the public on the above mentioned gesloten, wordt de verschijningsdag van het blad day, the date of issue of the Bulletin is the first verschoven naar de eerstvolgende werkdag, working day thereafter, on which the Office is waarop Octrooicentrum Nederland is geopend. Het open. Each issue of the Bulletin consists of 14 blad verschijnt alleen in elektronische vorm. Elk headings. nummer van het blad bestaat uit 14 rubrieken. Bijblad Official Journal Verschijnt vier keer per jaar (januari, april, juli, Appears four times a year (January, April, July, oktober) in elektronische vorm via www.rvo.nl/ October) in electronic form on the www.rvo.nl/ octrooien. Het Bijblad bevat officiële mededelingen octrooien. The Official Journal contains en andere wetenswaardigheden waarmee announcements and other things worth knowing Octrooicentrum Nederland en zijn klanten te for the benefit of the Netherlands Patent Office and maken hebben. its customers. Abonnementsprijzen per (kalender)jaar: Subscription rates per calendar year: Hoofdblad en Bijblad: verschijnt gratis Patent Bulletin and Official Journal: free of in elektronische vorm op de website van charge in electronic form on the website of the Octrooicentrum -
(19) United States (12) Patent Application Publication (10) Pub
111111 1111111111111111111111111111111111111111111111111111111111111111111111111111 us 20200002828Al (19) United States (12) Patent Application Publication (10) Pub. No.: US 2020/0002828 At MILLS (43) Pub. Date: Jan. 2, 2020 (54) ELECTRICAL POWER GENERATION Publication Classification SYSTEMS AND METHODS REGARDING (51) Int. Cl. SAME e25B 13104 (2006.01) H05H 1124 (2006.01) (71) Applicant: BRILLIANT LIGHT POWER, INC., HOlL 3110725 (2006.01) Cranbury, NJ (US) HOlL 3110735 (2006.01) H02S 40132 (2006.01) (72) Inventor: RANDELL L. MILLS, CRANBURY, H02S 40138 (2006.01) NJ (US) H02S 40122 (2006.01) H02S 40142 (2006.01) (73) Assignee: BRILLIANT LIGHT POWER, INC., e25B 1104 (2006.01) CRANBURY, NJ (US) (52) U.S. Cl. CPC ............... e25B 13104 (2013.01); H05H 1124 (21) Appl. No.: 16/567,689 (2013.01); HOlL 3110725 (2013.01); HOlL 3110735 (2013.01); H05H 2277/13 (2013.01); (22) Filed: Sep. 11, 2019 H02S 40138 (2014.12); H02S 40122 (2014.12); H02S 40142 (2014.12); e25B 1104 (2013.01); Related U.S. Application Data H02S 40132 (2014.12) (63) Continuation of application No. 15/314,196, filed on (57) ABSTRACT Nov. 28, 2016, now Pat. No. 10,443,139, filed as A solid or liquid fuel to plasma to electricity power source application No. PCTlUS2015/033165 on May 29, that provides at least one of electrical and thermal power 2015. comprising (i) at least one reaction cell for the catalysis of (60) Provisional application No. 62/004,883, filed on May atomic hydrogen to form hydrinos, (ii) a chemical fuel 29, 2014, provisional application No. 62/012,193, mixture comprising at least two components chosen from: a source of H 0 catalyst or H 0 catalyst; a source of atomic filed on Jun. -
Performance and Applications of L1B2 Ultrasonic Motors
actuators Review Performance and Applications of L1B2 Ultrasonic Motors Gal Peled, Roman Yasinov * and Nir Karasikov Nanomotion Ltd., 3 Hayetsira St., Yokneam 20692, Israel; [email protected] (G.P.); [email protected] (N.K.) * Correspondence: [email protected]; Tel.: +972-073-249-8023 Academic Editor: Kenji Uchino Received: 13 April 2016; Accepted: 25 May 2016; Published: 1 June 2016 Abstract: Piezoelectric ultrasonic motors offer important advantages for motion applications where high speed is coupled with high precision. The advances made in the recent decades in the field of ultrasonic motor based motion solutions allow the construction of complete motion platforms in the fields of semiconductors, aerospace and electro-optics. Among the various motor designs, the L1B2 motor type has been successful in industrial applications, offering high precision, effective control and operational robustness. This paper reviews the design of high precision motion solutions based on L1B2 ultrasonic motors—from the basic motor structure to the complete motion solution architecture, including motor drive and control, material considerations and performance envelope. The performance is demonstrated, via constructed motion stages, to exhibit fast move and settle, a repeatability window of tens of nanometers, lifetime into the tens of millions of operational cycles, and compatibility with clean room and aerospace environments. Example stages and modules for semiconductor, aerospace, electro-optical and biomedical applications are presented. The described semiconductor and aerospace solutions are powered by Nanomotion HR type motors, driven by a sine wave up to 80 V/mm rms, having a driving frequency of 39.6 kHz, providing a maximum force up to 4 N per driving element (at 5 W power consumption per element) and a maximum linear velocity above 300 mm/s. -
LINEAR MOVEMENTS Linear Motors, Precision Lead Screws & Miniature Ball Screws Introduction: Dynetics – Dynamic in Mechatronics
LINEAR MOVEMENTS Linear Motors, Precision Lead Screws & Miniature Ball Screws Introduction: Dynetics – dynamic in mechatronics Dynetics specialises in high-quality, high-precision mechatronic components and helps customers economise their designs by offering solutions with an optimum price- performance ratio. Most of its products can be customised to the client’s specific needs. Dynetics, founded in 1994 and with offices in Germany and`the Netherlands, assists engineers in selecting the most suitable motor for their mechatronic assignment. Dyneticsrepresents leading manufacturers such as Nidec (Copal, Servo Etc.), KSS, Nippon Pulse Motor (NPM) and Elmo, and offers a wide range of small rotating motors (up to 200 W) and highprecision linear motors (up to 100,000 N) with various technologies (piezo, brush, brushless, coreless), together with peripherals like ultra-high-precision lead screws, miniature ball screws, gearboxes, electronics and so on. Many of the motors supplied by Dynetics can be customised. Examples of such include a double shaft or modified shafts, encoders and different windings. All fans and motors can be fitted with connectors as per customer request. Many of our fans and blowers can also be customized, e.g. with wire, plug, pulse generator, PWM connection for speed control, IP class protection, etc. Portfolio The products in the Dynetics portfolio can be roughly divided into five groups: 1. Rotating solutions in different technologies: • stepping motors (PM or hybrid); • brush and brushless AC, and PMDC-motors (with or without gear head); • coreless motors; • piezo motors; • options like gearheads and encoders. 2. Linear solutions in different technologies: • linear servo motors (actuators, cylinders and stages); • precision lead screws and miniature ball screws. -
New Start Stop Ultrasonic Piezoelectric Nanomotor
NANOTECHNOLOGY • APPLICATION RESEARCH IN THE FIELD OF NANOTECHNOLOGY NEW STARTSTOP ULTRASONIC PIEZOELECTRIC NANOMOTOR UPM22 WITH ULTRAHIGH RESOLUTION AND ULTRAHIGH TORQUE FOR NANOPOSITIONING SYSTEM AND OTHER APPLICATIONS Description technologies, hospital equipment, prostheses; food industry – weight batch equipment, piezoelectric driven ball valves; LILEYA’s nanopositioning inexpensive unidirectional rotation banking equipment and security systems – safe, locks, auto piezoelectric motor UPM22 (fig.1) on the bases standing matic opening and closing of doors. wave combine high torque, variable speed, and high angular resolution using new piezoelectric generator. The piezoelectric motor UPM22 can be used in either continuous or stepper mode to provide accurate angular positioning. When the piezoelectric motor is deenergized, it operates as a position ing holder (brake) with practically undetectable backlash and drift. The inbuilt angle positioning system (using the magnet "marks" established by the customer himself) enables to real ize the shaft fixation in chosen positions. The motor control is carried out by means of the driver on two lines of the XP1 joint (see driver to UPM20 www.piezomotor.com.ua ) Fig.1 Ultrasonic Piezoelectric NanoMotor UPM22 Innovative Aspect and Main Advantages Devices on the bases UPM22 The motor operation employs the radial oscillation of a propri etary ringbased piezoelectric resonator operating at approxi mately 80 kHz. Each cycle of radial nanooscillation by means of the rotor produces a single step of angular movement. A continuous sequence of single angular step results in a smooth angular/rotary movement of the shaft on which the rotor is mounted. The magnitude of the resulting nanomove ment depends on the number of single angular steps made, which depends on the duration of excitation. -
PRZEGLĄD ELEKTROTECHNICZNY Vol 2017, No 2
PRZEGLĄD ELEKTROTECHNICZNY Vol 2017, No 2 Contents 01 Rafał PIOTUCH, Ryszard PAŁKA - Comparison of Two Synchronous Motors with Interior Magnets 1 02 Adam BIERNAT - Coil-turn short-circuit of PMSM influence on the transformed phase voltage frequency pattern 5 03 Grzegorz BARTOSIK 1, Henryk BANACH - Optimal operation of the separately excited dc motor 10 04 Krzysztof BIEŃKOWSKI, Krzysztof JACKIEWICZ - Control parameters impact on mechanical characteristics 13 of double-phase switched reluctance motor 05 Maciej BOGUMIŁ, Konrad DĄBAŁA, Zdzisław KRZEMIEŃ - Thermal calculations and tests of brushless motor 17 with liquid-cooled frame 06 Andrzej BYTNAR, Sławomir WRÓBLEWSKI - Automatic Diagnostics of Vibration and Technical Condition of 21 Turbogenerator Stator Core's Teeth 07 Konrad DĄBAŁA, Renata SULIMA - Evaluation of the influence of applying high efficiency electrical motors for 26 the energy saving 08 Michał DROGOSZ, Krzysztof BIEŃKOWSKI, Jerzy GRYGORCZUK, Bartosz KĘDZIORA - Impact of tubular 30 reluctance motor design parameters on the performance of ground penetrator for space missions 09 Paweł EWERT, Marcin MUSIAŁ - Detecting of misalignment of the drive systems with induction motor supplied 34 by a frequency converter 10 Rafał GABOR, Piotr MYNAREK, Marcin KOWOL - The concept and calculation of switched reluctance motor 39 with external-rotor designed for the electric bike 11 Pavlo GAKAL, Olena OVSIANNYKOVA, Jerzy PRZYBYSZ, Oleksii TRETIAK - Analysis of the temperature 43 field of the rotor of 550-MW turbogenerator with direct hydrogen -
Design and Implementation of a Power Inverter for a High Power Piezoelectric Brake Actuator in Aircrafts
DESIGN AND IMPLEMENTATION OF A POWER INVERTER FOR A HIGH POWER PIEZOELECTRIC BRAKE ACTUATOR IN AIRCRAFTS Rongyuan Li, Norbert Fröhleke, Joachim Böcker Institute of Power Electronics and Electrical Drives Paderborn University, Paderborn, Germany [email protected], [email protected], [email protected] Abstract — Piezoelectric brake actuators for airplanes required brake downforce, EMAs based on electromagnetic are currently under development to dispense with motors require a reduction gear resulting in high weight and hydraulic systems. Subject of this contribution is a novel also inertia. Thus, during antiskid operation, high power PWM controlled inverter of the kW power range, feeding peaks will occur as a result of the dynamic change of kinetic a multi-mass ultrasonic motor (MM-USM) via a LLCC- energy of the drive train. Though Boeing and Airbus decided type filter. It is designed in a way to reduce the total to employ electromagnetic actuators in aircrafts that are harmonic distortion of the motor voltage and to locally currently under development, it is regarded only as first step compensate for the reactive power of the motor. By in the conversion of technologies. combining latter inverter and filter, the driving voltage of Emerging high power piezoelectric vibration motors, the motor can be varied in a suitable frequency range, thanks to their characteristics of high force at low speed as though the output filter shows an optimal performance at well as low inertia, will hopefully overcome latter mentioned minimized volume and weight. drawbacks of electromagnetic actuators. They are expected 1 as novel technology for airborne brakes. Therefore, the EC Keywords—Power supply, DC/AC converter, multi- funded project PIBRAC [1] was started to study, design and level converter, pulse width modulation (PWM), inverter- test a piezoelectric brake actuator and its involved control fed piezo actuator.