Piezoelectric Motors & It's Applications
Total Page:16
File Type:pdf, Size:1020Kb
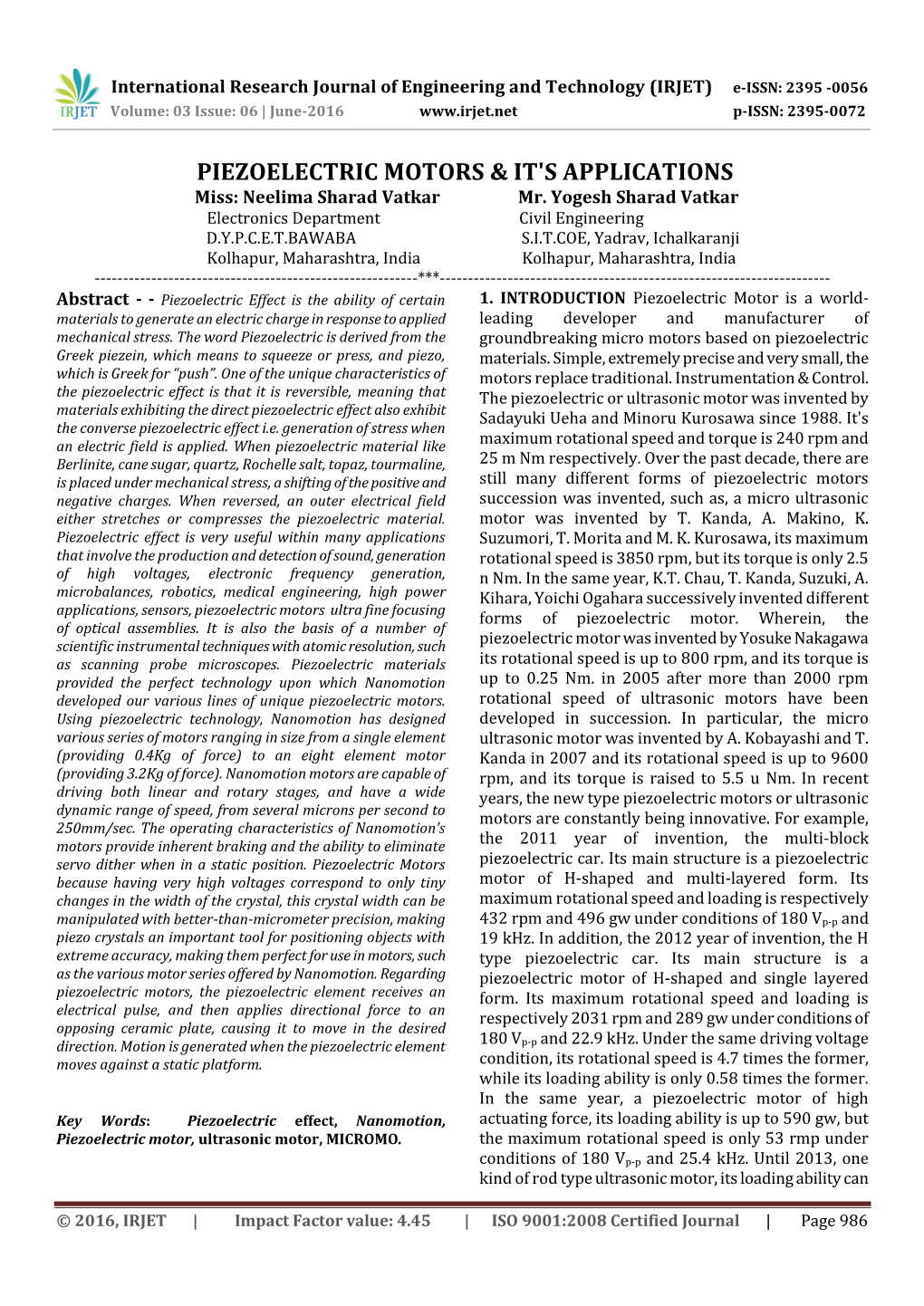
Load more
Recommended publications
-
Research and Development of a High-Resolution Piezoelectric Rotary Stage
KAUNAS UNIVERSITY OF TECHNOLOGY IGNAS GRYBAS RESEARCH AND DEVELOPMENT OF A HIGH-RESOLUTION PIEZOELECTRIC ROTARY STAGE Doctoral Dissertation Technological Sciences, Mechanical Engineering (09T) 2017, Kaunas This doctoral dissertation was prepared at Kaunas University of Technology, Institute of Mechatronics during the period of 2013–2017. The studies were supported by the Research Council of Lithuania. Scientific Supervisor: Habil. Dr. Algimantas Bubulis, (Kaunas University of Technology, Technological Sciences, Mechanical Engineering, 09T). Doctoral dissertation has been published in: http://ktu.edu Editor: Dovilė Dumbrauskaitė (Publishing Office “Technologija”) © I. Grybas, 2017 ISBN xxxx-xxxx The bibliographic information about the publication is available in the National Bibliographic Data Bank (NBDB) of the Martynas Mažvydas National Library of Lithuania KAUNO TECHNOLOGIJOS UNIVERSITETAS IGNAS GRYBAS AUKŠTOS SKYROS PJEZOELEKTRINIO SUKAMOJO STALIUKO KŪRIMAS IR TYRIMAS Daktaro disertacija Technologiniai mokslai, mechanikos inžinerija (09T) 2017, Kaunas Disertacija rengta 2013–2017 metais Kauno technologijos universiteto Mechatronikos institute. Mokslinius tyrimus rėmė Lietuvos mokslo taryba. Mokslinis vadovas: Habil. dr. Algimantas Bubulis (Kauno technologijos universitetas, technologiniai mokslai, mechanikos inžinerija, 09T). Interneto svetainės, kurioje skelbiama disertacija, adresas: http://ktu.edu Redagavo: Dovilė Dumbrauskaitė (leidykla “Technologija“) © I. Grybas, 2017 ISBN xxxx-xxxx Leidinio bibliografinė informacija pateikiama -
A Review of Application and Development Trends in Ultrasonic Motors
ES Mater. Manuf., 2021, 12, 3-16 ES Materials and Manufacturing DOI: https://dx.doi.org/10.30919/esmm5f933 A Review of Application and Development Trends in Ultrasonic Motors Xiaoniu Li, Zhiyi Wen, Botao Jia, Teng Cao, De Yu and Dawei Wu* Abstract The structure and performance of ultrasonic motors have gradually improved with the emergence of new materials, techniques, and structural forms. Therefore, the application scope of this technology is also expanding, especially in the field of high-end equipment. This paper conducts a review of research on the application status and progress at the frontier of research on ultrasonic motors. A summary and classification of both the status of application and cutting-edge research progress are presented, including the use of ultrasonic motors in aerospace, precision, biomedical and optical engineering and the influence on ultrasonic motor design resulting from the breakthrough in advanced processing and preparation technology, structural and functional integration technology, low voltage drives and open-loop control systems. Moreover, the performance of products developed with the aid of ultrasonic motors and representative devices are compared; and state of the art ultrasonic motor designs are discussed and summarized. Finally, potential future research efforts and prospects are highlighted. Keywords: Ultrasonic motors; applications; research progress; piezoelectric ceramics. Received date: 26 October 2020; Accepted date: 3 December 2020. Article type: Review article. 1. Introduction piezoelectric ceramics, micro-electro-mechanical systems Ultrasonic motors (USMs) involve the use of inverse (MEMS) micro-machining and 3D printing additive piezoelectric effects in piezoelectric ceramic materials to manufacturing technology.[10,11] generate rotation or linear motion by controlling the Until now, such advantages have enabled successful mechanical deformation. -
DESIGN, CONTROL, and APPLICATION of PIEZOELECTRIC ACTUATOR External-Sensing and Self-Sensing Actuator
DESIGN, CONTROL, AND APPLICATION OF PIEZOELECTRIC ACTUATOR External-Sensing and Self-Sensing Actuator ANDI SUDJANA PUTRA NATIONAL UNIVERSITY OF SINGAPORE 2008 DESIGN, CONTROL, AND APPLICATION OF PIEZOELECTRIC ACTUATOR External-Sensing and Self-Sensing Actuator ANDI SUDJANA PUTRA (B.Eng., Brawijaya University, M.T.D., National University of Singapore) A THESIS SUBMITTED FOR THE DEGREE OF DOCTOR OF PHILOSOPHY DEPARTMENT OF ELECTRICAL AND COMPUTER ENGINEERING NATIONAL UNIVERSITY OF SINGAPORE 2008 Acknowledgements I would like to express my sincere appreciation to all who have helped me during my candidature; without whom my study here would have been very much different. First and foremost, I thank my supervisors: Associate Professor Tan Kok Kiong and Associate Professor Sanjib Kumar Panda, who have provided invaluable guidance and suggestion, as well as inspiring discussions. With their enthusiasm and efforts in explaining things clearly, they have made research a fun and fruitful activity. I would have been lost without their direction. I would also like to thank the National University of Singapore for providing me with scholarship and research support; without which it would have been impossible to finish my study here. It is difficult to overstate my gratitude to the officers and students in Mechatronics and Automation Laboratory, who have also become my friends. Dr. Huang Sunan, Dr. Tang Kok Zuea, Dr. Zhao Shao, Dr. Teo Chek Sing, and Mr. Tan Chee Siong have always been very supportive and encouraging through the easy and difficult time during my research. I am indebted to many more colleagues in Faculty of Engineering and Faculty of Medicine, whose names, regrettably, I cannot mention all here. -
Course Description Bachelor of Technology (Electrical Engineering)
COURSE DESCRIPTION BACHELOR OF TECHNOLOGY (ELECTRICAL ENGINEERING) COLLEGE OF TECHNOLOGY AND ENGINEERING MAHARANA PRATAP UNIVERSITY OF AGRICULTURE AND TECHNOLOGY UDAIPUR (RAJASTHAN) SECOND YEAR (SEMESTER-I) BS 211 (All Branches) MATHEMATICS – III Cr. Hrs. 3 (3 + 0) L T P Credit 3 0 0 Hours 3 0 0 COURSE OUTCOME - CO1: Understand the need of numerical method for solving mathematical equations of various engineering problems., CO2: Provide interpolation techniques which are useful in analyzing the data that is in the form of unknown functionCO3: Discuss numerical integration and differentiation and solving problems which cannot be solved by conventional methods.CO4: Discuss the need of Laplace transform to convert systems from time to frequency domains and to understand application and working of Laplace transformations. UNIT-I Interpolation: Finite differences, various difference operators and theirrelationships, factorial notation. Interpolation with equal intervals;Newton’s forward and backward interpolation formulae, Lagrange’sinterpolation formula for unequal intervals. UNIT-II Gauss forward and backward interpolation formulae, Stirling’s andBessel’s central difference interpolation formulae. Numerical Differentiation: Numerical differentiation based on Newton’sforward and backward, Gauss forward and backward interpolation formulae. UNIT-III Numerical Integration: Numerical integration by Trapezoidal, Simpson’s rule. Numerical Solutions of Ordinary Differential Equations: Picard’s method,Taylor’s series method, Euler’s method, modified -
Meshing Drive Mechanism of Double Traveling Waves for Rotary Piezoelectric Motors
mathematics Article Meshing Drive Mechanism of Double Traveling Waves for Rotary Piezoelectric Motors Dawei An , Weiqing Huang *, Weiquan Liu, Jinrui Xiao, Xiaochu Liu and Zhongwei Liang School of Mechanical and Electrical Engineering, Guangzhou University, Guangzhou 510006, China; [email protected] (D.A.); [email protected] (W.L.); [email protected] (J.X.); [email protected] (X.L.); [email protected] (Z.L.) * Correspondence: [email protected] Abstract: Rotary piezoelectric motors based on converse piezoelectric effect are very competitive in the fields of precision driving and positioning. Miniaturization and larger output capability are the crucial design objectives, and the efforts on structural modification, new materials application and optimization of control systems are persistent but the effectiveness is limited. In this paper, the resonance rotor excited by stator is investigated and the meshing drive mechanism of double traveling waves is proposed. Based on the theoretical analysis of bending vibration, the finite element method (FEM) is used to compare the modal shape and modal response in the peripheric, axial, and radial directions for the stator and three rotors. By analyzing the phase offset and vibrational orientation of contact particles at the interface, the principle of meshing traveling waves is discussed graphically and the concise formula obtaining the output performance is summarized, which is analogous with the principles of gear connection. Verified by the prototype experimental results, the speed of the proposed motor is the sum of the velocity of the stator’s contact particle and the resonance rotor’s Citation: An, D.; Huang, W.; Liu, W.; contact particle, while the torque is less than twice the motor using the reference rotor. -
Actuator 2006: Ultrasonic Piezoelectric Motor
White Paper for ACTUATOR 2006 Survey of the Various Operating Principles of Ultrasonic Piezomotors K. Spanner Physik Instrumente GmbH & Co. KG, Karlsruhe, Germany Abstract: Piezoelectric ultrasonic motors have been known for more than 30 years. In recent years especially, a large number of different designs have been developed, both for rotation and linear drives. This talk will provide a definition of piezoelectric ultrasonic motors and classify their different operating principles. The operation of each type will then be explained, commercially available implementations described and the advantages and disadvantages of each discussed. The goal is to provide an international perspective on the current state of development of piezoelectric ultrasonic motors. Keywords: piezomotor, PZT, ultrasonic motor, travelling-wave, standing-wave, piezoelectric actuator Introduction There is today a large variety of drive designs arranged that their vibrational motion was exploiting motion obtainable from the inverse converted into rotary motion of a shaft and gear. piezoelectric effect. Ultrasonic piezomotors have a very special place among such devices. These motors achieve high speeds and drive forces, while still permitting the moving part to be positioned with very high accuracy. Such characteristics make these motors of great interest for many companies Fig. 1 Piezoelectric motor of L.W Williams and who make precision devices for which these drives Walter J. Brown [1]. are, in many cases, irreplaceable. Since then, there have been numerous Piezoelectric Motors developments in the field of piezoelectric motors. They can be classified by working principle, Piezoelectric actuators are electro-mechanical geometry, or the type of oscillation excited in the energy transducers; they transform electrical energy piezoceramic. -
Piezoelectric Inertia Motors—A Critical Review of History, Concepts, Design, Applications, and Perspectives
Review Piezoelectric Inertia Motors—A Critical Review of History, Concepts, Design, Applications, and Perspectives Matthias Hunstig Grube 14, 33098 Paderborn, Germany; [email protected] Academic Editor: Delbert Tesar Received: 26 November 2016; Accepted: 18 January 2017; Published: 6 February 2017 Abstract: Piezoelectric inertia motors—also known as stick-slip motors or (smooth) impact drives—use the inertia of a body to drive it in small steps by means of an uninterrupted friction contact. In addition to the typical advantages of piezoelectric motors, they are especially suited for miniaturisation due to their simple structure and inherent fine-positioning capability. Originally developed for positioning in microscopy in the 1980s, they have nowadays also found application in mass-produced consumer goods. Recent research results are likely to enable more applications of piezoelectric inertia motors in the future. This contribution gives a critical overview of their historical development, functional principles, and related terminology. The most relevant aspects regarding their design—i.e., friction contact, solid state actuator, and electrical excitation—are discussed, including aspects of control and simulation. The article closes with an outlook on possible future developments and research perspectives. Keywords: inertia motor; stick-slip motor; smooth impact drive; piezeoelectric motor; review 1. Introduction Piezoelectric actuators have long been used in diverse applications, especially because of their short response time and high resolution. The major drawback of these solid state actuators in positioning applications is their small stroke: actuators made of state-of-the-art lead zirconate titanate (PZT) ceramics only reach strains up to 2 . A typical piezoelectric actuator with 10 mm length thus reaches a maximum stroke of only 20 µm.h Bending actuator designs [1] and other mechanisms [2] can increase the stroke at the expense of stiffness and actuation force ([3]; [4] (pp. -
Brushless DC Electric Motor
Please read: A personal appeal from Wikipedia author Dr. Sengai Podhuvan We now accept ₹ (INR) Brushless DC electric motor From Wikipedia, the free encyclopedia Jump to: navigation, search A microprocessor-controlled BLDC motor powering a micro remote-controlled airplane. This external rotor motor weighs 5 grams, consumes approximately 11 watts (15 millihorsepower) and produces thrust of more than twice the weight of the plane. Contents [hide] 1 Brushless versus Brushed motor 2 Controller implementations 3 Variations in construction 4 AC and DC power supplies 5 KM rating 6 Kv rating 7 Applications o 7.1 Transport o 7.2 Heating and ventilation o 7.3 Industrial Engineering . 7.3.1 Motion Control Systems . 7.3.2 Positioning and Actuation Systems o 7.4 Stepper motor o 7.5 Model engineering 8 See also 9 References 10 External links Brushless DC motors (BLDC motors, BL motors) also known as electronically commutated motors (ECMs, EC motors) are electric motors powered by direct-current (DC) electricity and having electronic commutation systems, rather than mechanical commutators and brushes. The current-to-torque and frequency-to-speed relationships of BLDC motors are linear. BLDC motors may be described as stepper motors, with fixed permanent magnets and possibly more poles on the rotor than the stator, or reluctance motors. The latter may be without permanent magnets, just poles that are induced on the rotor then pulled into alignment by timed stator windings. However, the term stepper motor tends to be used for motors that are designed specifically to be operated in a mode where they are frequently stopped with the rotor in a defined angular position; this page describes more general BLDC motor principles, though there is overlap. -
Examination of High-Torque Sandwich-Type Spherical Ultrasonic Motor Using with High-Power Multimode Annular Vibrating Stator
actuators Article Examination of High-Torque Sandwich-Type Spherical Ultrasonic Motor Using with High-Power Multimode Annular Vibrating Stator Ai Mizuno 1,*, Koki Oikawa 1, Manabu Aoyagi 1,* ID , Hidekazu Kajiwara 1, Hideki Tamura 2 and Takehiro Takano 2 1 Graduate School of Engineering, Muroran Institute of Technology, 27-1, Mizumoto, Muroran, Hokkaido 050-8585, Japan; [email protected] (K.O.); [email protected] (H.K.) 2 Department of Information and Communication Engineering, Tohoku Institute of Technology, Sendai, Miyagi 982-8577, Japan; [email protected] (H.T.); [email protected] (T.T.) * Correspondence: [email protected] (A.M.); [email protected] (M.A.); Tel.: +81-143-46-5504 (M.A.) Received: 5 January 2018; Accepted: 20 February 2018; Published: 27 February 2018 Abstract: Spherical ultrasonic motors (SUSMs) that can operate with multiple degrees of freedom (MDOF) using only a single stator have high holding torque and high torque at low speed, which makes reduction gearing unnecessary. The simple structure of MDOF-SUSMs makes them useful as compact actuators, but their development is still insufficient for applications such as joints of humanoid robots and other systems that require MDOF and high torque. To increase the torque of a sandwich-type MDOF-SUSM, we have not only made the vibrating stator and spherical rotor larger but also improved the structure using three design concepts: (1) increasing the strength of all three vibration modes using multilayered piezoelectric actuators (MPAs) embedded in the stator, (2) enhancing the rigidity of the friction driving portion of the stator for transmitting more vibration force to the friction-driven rotor surface, and (3) making the support mechanism more stable. -
Development of a Linear Ultrasonic Motor with Segmented Electrodes
Development of a Linear Ultrasonic Motor with Segmented Electrodes by Jacky Ka Ki Lau A thesis submitted in conformity with the requirements for the degree of Master of Applied Science Graduate Department of Mechanical and Industrial Engineering University of Toronto © Copyright by Jacky Ka Ki Lau 2012 Development of a Linear Ultrasonic Motor with Segmented Electrodes Jacky Ka Ki Lau Master of Applied Science Graduate Department of Mechanical and Industrial Engineering University of Toronto 2012 ABSTRACT A novel segmented electrodes linear ultrasonic motor (USM) was developed. Using a planar vibration mode concept to achieve elliptical motion at the USM drive-tip, an attempt to decouple the components of the drive-tip trajectory was made. The proposed design allows greater control of the drive-tip trajectory without altering the excitation voltage. Finite element analyses were conducted on the proposed design to estimate the performance of the USM. The maximum thrust force and speed are estimated to be 46N and 0.5370m/s, respectively. During experimental investigation, the maximum thrust force and speed observed were 36N and 0.223m/s, respectively, at a preload of 70N. Furthermore, the smallest step achievable was 9nm with an 18µs impulse. Nevertheless, the proposed design allowed the speed of the USM to vary while keeping the thrust force relatively constant and allowed the USM to achieve high resolution without a major sacrifice of thrust force. ii Acknowledgements I would like to thank everyone who helped me in to the completion of my thesis and my Master’s program. Special mention goes to the following people and organizations: My supervisor, Professor Ridha Ben Mrad, for his guidance and support throughout my project. -
Gradniki in Tehnologije V Sistemih Vodenja
Univerza v Ljubljani Fakulteta za elektrotehniko Alesˇ Belicˇ Gradniki in tehnologije v sistemih vodenja Ljubljana 22. januar 2012 2 3 Predgovor Obravnava snovi pri predmetih Gradniki v sistemih vodenja na Univerzitetnem studijskemˇ programu in Gradniki v tehnologiji vodenja na visokosolskemˇ strokovnem studijskemˇ pro- gramu Fakultete za elektrotehniko Univerze v Ljubljani je nekoliko drugacnaˇ kot pri ostalih predmetih na smeri Avtomatika. Cepravˇ sta to dva od osnovnih predmetov na smereh, pa se vendarle ne navezujeta cistoˇ neposredno na ostale predmete na studijskihˇ programih Avto- matike. Ucbenikˇ obravnava prakticneˇ in izvedbene vidike sistemov vodenja, ki ostanejo pri poglobljeni obravnavi algoritmov vodenja mnogokrat v ozadju. Izbira ustreznih merilnih sistemov, krmilnikov ali regulatorjev ter izvrsnihˇ sistemov, ki pokrijejo potrebe po mociˇ in preciznosti vodenja, je kljucnaˇ za kvalitetno izvedbo vodenja. Ne glede na dobro nacrtanoˇ shemo vodenja, je na koncu vse odvisno od izvedbe. V praksi je delezˇ vlozenegaˇ dela v resnici mocnoˇ na strani izvedbenih problemov sistema vodenja, medtem ko se algoritmom vodenja posvetimo seleˇ proti koncu izvedbe, ko je obicajnoˇ premalo casa,ˇ da bi algoritem in njegove parametre optimalno nastavili. Pomen snovi tega predmeta za izvedbo sistemov vodenja je torej nesporen. Po drugi strani pa je to predmet, ki zahteva precej ucenjaˇ na pa- met, saj je potrebno sirokoˇ poznavanje moznihˇ podsistemov in principov delovanja. Snov, ki je zbrana v tej knjigi je plod lastnih izkusenjˇ avtorja na tem podrocjuˇ s pomembnimi pri- spevki prof. dr. Riharda Karbe, prof. dr. Jusaˇ Kocijana, prof. dr. Maje Atanasijevic-Kunc,´ doc. dr. Gregorja Klancarjaˇ in dr. Janka Petrovciˇ ca,ˇ ki zeˇ dolga leta sodelujejo na temah, ki jih predmet obravnava. -
Robust Position Control of Ultrasonic Motor Considering Dead-Zone
Robust Position Control of Ultrasonic Motor Considering Dead-Zone Shogo Odomari1, Araz Darba1, Kosuke Uchida1, Tomonobu Senjyu1, and Atsushi Yona1 1Department of Electrical and Electronics Engineering, University of the Ryukyus, Japan E-mail: [email protected] Abstract— Intrinsic properties of ultrasonic motor (high torque for low speed, high static torque, compact S1 D1 S3 D3 C L1 USM Load in size, etc.) offer great advantages for industrial ap- 1 Va plications. However, when load torque is applied, dead- E zone occurs in the control input. Therefore, a nonlinear Vb y controller, which considers dead-zone, is adopted for ul- C2 L 2 trasonic motor. The state quantities, such as acceleration, S2 D2 S4 D4 RE speed, and position are needed to apply the nonlinear controller for position control. However, rotary encoder causes quantization errors in the speed information. This − f MOS FET Micro ye paper presents a robust position control method for ultra- driver φ computer sonic motor considering dead-zone. The state variables y for nonlinear controller are estimated by a Variable r e Structure System(VSS) observer. Besides, a small, low Personal cost, and good response nonlinear controller is designed computer by using a micro computer that is essential in embedded system for the developments of industrial equipments. Fig. 1 Drive system of USM. Effectiveness of the proposed method is verified by the experimental results. 150 Va Vb 100 I. INTRODUCTION B V , [V] 50 A In recent years, ultrasonic motor(USM) is gaining V 0 attention as it has good characteristics and is small in size.