Bloostar-PCT.Pdf
Total Page:16
File Type:pdf, Size:1020Kb
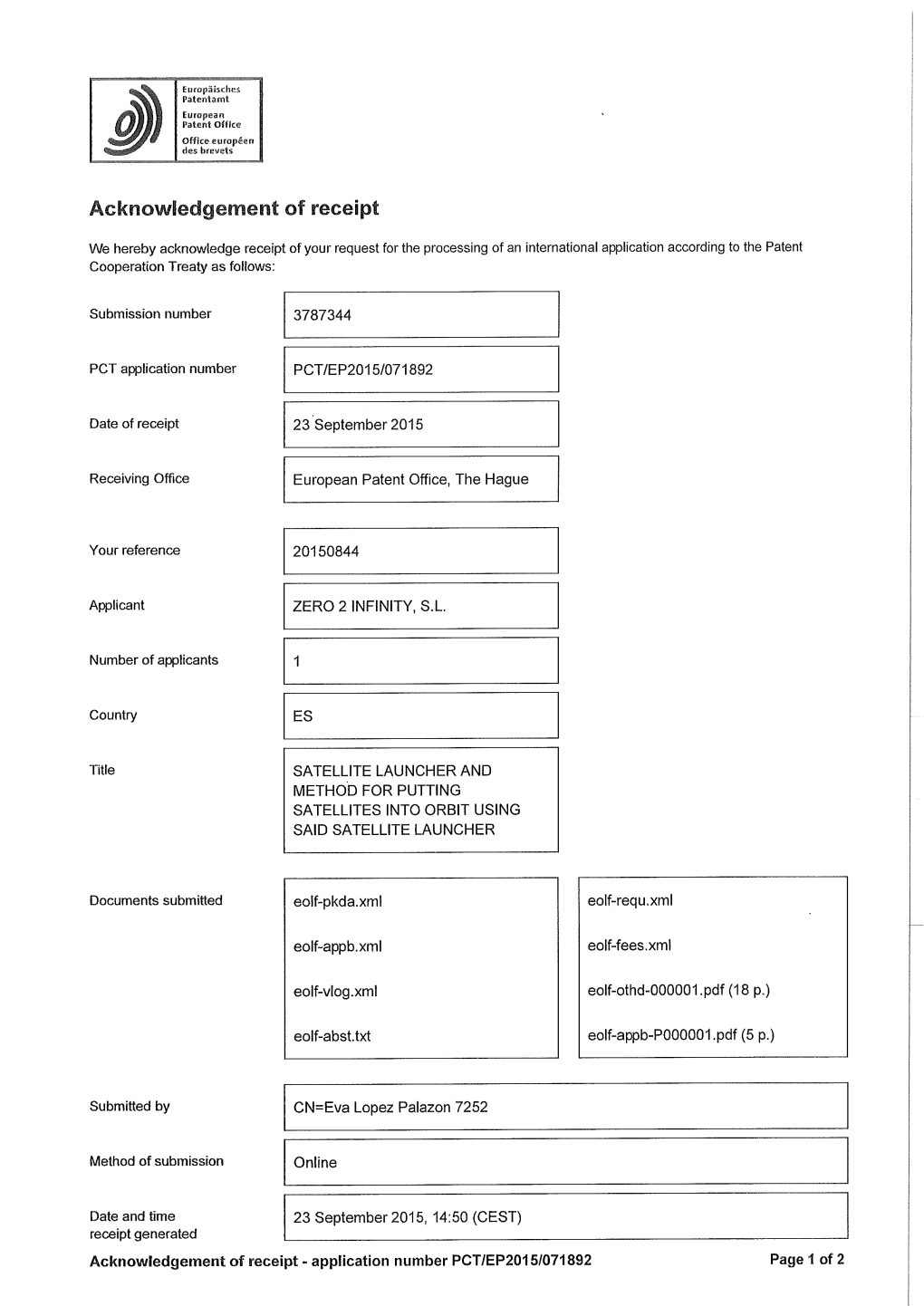
Load more
Recommended publications
-
GAS DIVISION NEWSLETTER Official Publication of the BFA Gas Division
GAS DIVISION NEWSLETTER Official Publication of the BFA Gas Division Volume 4, Issue 2 Copyright Peter Cuneo & Barbara Fricke, 2003 August 2003 On Saturday morning, we were greeted with a hotel RACE TO KITTY HAWK message saying the morning launch had been cancelled by Ray Bair but a briefing would take place at 7:00 a.m. The entire day was scrubbed due to substantial thunderstorms just west of Dayton in Indiana. As it turned out, the storms dissipated, and the day was pleasant for visiting the As part of the centennial celebration of powered various museums and city historic sites. That evening, flight, RE/MAX sponsored a Balloon Celebration we were treated to a reception at the Air Force Museum which included both hot air and gas flights for the and a briefing that made a Sunday morning launch seem weekend of the Fourth of July. At least that was the possible. Again the threat of severe weather prevented a plan. While about half the field of hot air balloons Saturday night launch. Later that night I found myself finally flew on Sunday morning, the gas flight was clustered in the main briefing room as the hotel staff totally scrubbed. gathered everyone for a tornado “drill”. The intended gas competition was an accuracy flight Sunday morning we were back on the field and once to the monument marking the first flight of the again prepared the equipment for launch. Another Wright brothers in Kitty Hawk, N.C. This is about couple of hours Sunday morning was only slightly better 500 miles from the launch site at Wright Patterson as the local weather allowed launch of some of the hot AFB in Dayton, Ohio. -
Paper Takes Flight Teacher Materials
Paper Takes Flight Teacher Materials Contents: LESSON PLAN .............................................................................................................................. 1 Summary: .................................................................................................................................... 1 Objectives:................................................................................................................................... 1 Materials:..................................................................................................................................... 1 Safety Instructions:...................................................................................................................... 1 Background: ................................................................................................................................ 1 Procedure:.................................................................................................................................... 2 Discussion ................................................................................................................................... 2 Assessment/Evaluation:............................................................................................................... 3 Extensions: .................................................................................................................................. 3 Math Integration......................................................................................................................... -
Atmospheric Planetary Probes And
SPECIAL ISSUE PAPER 1 Atmospheric planetary probes and balloons in the solar system A Coustenis1∗, D Atkinson2, T Balint3, P Beauchamp3, S Atreya4, J-P Lebreton5, J Lunine6, D Matson3,CErd5,KReh3, T R Spilker3, J Elliott3, J Hall3, and N Strange3 1LESIA, Observatoire de Paris-Meudon, Meudon Cedex, France 2Department Electrical & Computer Engineering, University of Idaho, Moscow, ID, USA 3Jet Propulsion Laboratory, California Institute of Technology, Pasadena, CA, USA 4University of Michigan, Ann Arbor, MI, USA 5ESA/ESTEC, AG Noordwijk, The Netherlands 6Dipartment di Fisica, University degli Studi di Roma, Rome, Italy The manuscript was received on 28 January 2010 and was accepted after revision for publication on 5 November 2010. DOI: 10.1177/09544100JAERO802 Abstract: A primary motivation for in situ probe and balloon missions in the solar system is to progressively constrain models of its origin and evolution. Specifically, understanding the origin and evolution of multiple planetary atmospheres within our solar system would provide a basis for comparative studies that lead to a better understanding of the origin and evolution of our Q1 own solar system as well as extra-solar planetary systems. Hereafter, the authors discuss in situ exploration science drivers, mission architectures, and technologies associated with probes at Venus, the giant planets and Titan. Q2 Keywords: 1 INTRODUCTION provide significant design challenge, thus translating to high mission complexity, risk, and cost. Since the beginning of the space age in 1957, the This article focuses on the exploration of planetary United States, European countries, and the Soviet bodies with sizable atmospheres, using entry probes Union have sent dozens of spacecraft, including and aerial mobility systems, namely balloons. -
Venus Balloon Technology Summary
Venus Balloon Technology Summary Jeffery L. Hall Supervisor Extreme Environment Robotics Group Jet Propulsion Laboratory California Institute of Technology December 7, 2015 Introduction • This Venus balloon briefing is being presented to the VEXAG Technology Working Group at their Dec. 7, 2015 telecon. • The purpose is to give a brief overview of Venus balloon technology and show examples for potential future missions. • The information reflects the author’s personal experience and is not meant to be a comprehensive synopsis of the field. 2 History of Venus Ballooning • The only non-terrestrial balloons that have ever flown were the Soviet VEGA-1 and VEGA-2 missions that flew at Venus in 1985. – There was one balloon each carried as a piggyback payload and deployed from the VEGA-1 and VEGA-2 landers during atmospheric descent. • These were short duration balloons that flew in the relatively cool clouds of the upper atmosphere. Key characteristic included: – Helium-filled superpressure balloon. – 2 day flight duration (transmitter battery died before balloon failed). – Flight was in the clouds at a 53-55 km altitude where the temperature ranged from 30 to 50 °C. – Balloon diameter was 3.5 m – Payload mass was 7 kg (everything carried under the balloon) – Balloon was constructed from a heavy, Teflon-like material that was resistant to the sulfuric acid aerosols in the clouds. • Both missions were successful and returned data on Venus winds, temperature and pressure. 3 VEGA Lander and Balloon VEGA lander (750 kg) VEGA balloon (15 kg balloon, 7 kg payload) 4 Future Venus Balloon Options • Many different kinds of balloons have been proposed for future Venus missions: – Different balloons can address different science at different locations. -
Lives in Engineering
LIVES IN ENGINEERING John Scales Avery January 19, 2020 2 Contents 1 ENGINEERING IN THE ANCIENT WORLD 9 1.1 Megalithic structures in prehistoric Europe . .9 1.2 Imhotep and the pyramid builders . 15 1.3 The great wall of China . 21 1.4 The Americas . 25 1.5 Angkor Wat . 31 1.6 Roman engineering . 38 2 LEONARDO AS AN ENGINEER 41 2.1 The life of Leonardo da Vinci . 41 2.2 Some of Leonardo's engineering drawings . 49 3 THE INVENTION OF PRINTING 67 3.1 China . 67 3.2 Islamic civilization and printing . 69 3.3 Gutenberg . 74 3.4 The Enlightenment . 77 3.5 Universal education . 89 4 THE INDUSTRIAL REVOLUTION 93 4.1 Development of the steam engine . 93 4.2 Working conditions . 99 4.3 The slow acceptance of birth control in England . 102 4.4 The Industrial Revolution . 106 4.5 Technical change . 107 4.6 The Lunar Society . 111 4.7 Adam Smith . 113 4.8 Colonialism . 119 4.9 Trade Unions and minimum wage laws . 120 4.10 Rising standards of living . 125 4.11 Robber barons and philanthropists . 128 3 4 CONTENTS 5 CANALS, RAILROADS, BRIDGES AND TUNNELS 139 5.1 Canals . 139 5.2 Isambard Kingdon Brunel . 146 5.3 Some famous bridges . 150 5.4 The US Transcontinental Railway . 156 5.5 The Trans-Siberian railway . 158 5.6 The Channel Tunnel . 162 6 TELEGRAPH, RADIO AND TELEPHONE 171 6.1 A revolution in communication . 171 6.2 Ørsted, Amp`ereand Faraday . 174 6.3 Electromagnetic waves: Maxwell and Hertz . -
Gas Division Newsletter
GAS DIVISIONH NEWSLETTER Official Publication of the BFA Gas Division Volume 1, Issue 2 Copyright Peter Cuneo & Barbara Fricke, 2000 Summer 2000 DANVILLE by Barbara Fricke The invitation went out for the National Gas Balloon Race to be held with the Oldsmobile Balloon Classic Illinois in Danville, Illinois. It would be a BFA sanctioned 3-part task race instead of a distance race. Ten balloons would compete. The pilots and co-pilots who registered, according to the rally's web site ( www.balloonclassic.org ), were: Troy Bradley and Bruce Hale Rusty Elwell and Don Weeks Barbara Fricke, Ray Bair and Danni Suskin Jim Hershend and Jack Holland David Levin and George Ibach Bert Padelt and Jack Edling Johnny Petrehn and Sam Parks The first briefing was on Thursday evening. Shane Robinson, Paul Morlock and Charles Page Not much said, since weather was the main concern Stan Wereschuk and Ron Martin and the weatherman was unavailable. The flags in Randy Woods and Ted Stanley front of the hotel were almost straight out. Friday morning resulted in the only pictures taken relating to gas ballooning. The organizers had arranged for many helpers with the big mound of sand. Friday's noon briefing was positive about an evening flight. The 7:00 pm briefing put the flight on hold. The later briefing called the Friday flight off – too windy. It would have been a "Denver" windy inflation and a flight towards, if not over, Lake Erie with sunrise while over the lake. Saturday's noon briefing tried to be positive, while the weather channel was forecasting evening thundershowers. -
Mark Sullivan
1 2 0 2 0 Mark Sullivan Mark Sullivan is a pilot, competitor and event organizer in both hot air and gas bal- looning. Mark served as the US delegate to the FAI Ballooning Commission for 18 years and for the past five years as its President. He earned his commercial hot air balloon license in 1983 and gas rating in 1985, currently has 3330 hours. He won the U.S. National Gas Balloon Championships in 1995 and that same year he founded the America’s Challenge Gas Balloon Race held annually at the Albuquer- que International Balloon Fiesta. Mark won the FAI North American Hot Air Cham- pionship in 1992. In 1998, the FAI awarded Mark his first Montgolfier Award for his service to ballooning. In 2005, in he was awarded a second Montgolfier Award for best performance in gas balloons with two podium finishes in the FAI World Gas Balloon Championships and FAI Coupe Aéronautique Gordon Bennett, taking 2nd in both events. He has competed in the Coupe Aéronautique Gordon Bennett 23 times and the World Gas Balloon Championship 4 times, best finish in both events 2nd. Flying with Cheri Edwards White they won the America’s Challenge Gas Balloon in 2008 & 2012. 2 It is amazing how living in Albuquerque and seeing balloons in the air for the first time can make such major changes to one’s life. Mark feels very fortunate to have found such a won- derful sport and been able to spend so much time flying all over the world. He has flown in thirty three countries and thirty nine states. -
Esa Standard Document
VENUS ENTRY PROBE TUDY OVERVIEW OF THE ENUS NTRY ROBE An ESA Technology Reference Study Planetary Exploration Studies Section (SCI-AP) Science Payload and Advanced Concepts Office (SCI-A) prepared by/préparé par Marcel van den Berg and Peter Falkner reference/réference SCI-AP/2006/173/VEP/MvdB issue/édition 2 revision/révision 3 Date of issue/date d’édition 27/02/2007 status/état Released Document type/type de document public report a ESTEC VEP_Study_Overview_2_3_2007.doc Keplerlaan 1 - 2201 AZ Noordwijk - The Netherlands Tel. (31) 71 5656565 - Fax (31) 71 5656040 Study overview of the Venus Entry Probe issue 2 revision 3 - 27/02/2007 SCI-A/2006/173/VEP/MvdB page 2 of 64 Venus Entry Probe Technology Reference Study – Study Team ESA Marcel van den Berg VEP TRS study manager Peter Falkner Technical officer VEP TRS activities Andre Schiele Technical officer microprobe project Arnaud Boutonnet Mission analysis validation EADS Astrium Ltd. Steve Kemble Mission analysis Surrey Satellite Andy Phipps Study manager Technology Ltd. Adrian Woodroffe OBDH Dave Gibbon Propulsion Peter Alcindor Power Craig Clark Power Nadeem Ghafoor Payloads/Science Alex Cropp ACS Carlos Lovett Lineares Communications John Buckley Projects Yoshi Hashida Trajectories Tanya Vladimirova Advanced Technologies Adam Baker Structure/Micro-power technologies Jackie Brooks Project Assistant Alex da Silva Curiel Research and Development Jim Clemmet Structure/Configuration Andrew Cawthorne Thermal Syed Husnain Thermal Phil Whittaker Navigation Vorticity Ltd. Steve Lingard Systems Engineering John Underwood Systems Engineering (entry vehicle and aerobot) Nick Bown Space inflatables Fluid Gravity Arthur Smith Thermal Protection System analysis validation Engineering Gavin Parnaby Thermal Protection System analysis validation Cosine Research B.V. -
Balloons Have the Right-Of-Way
6/4/2014 Balloons have the Right of Way Larry Konash RPS IMC Balloon Agency Minneapolis, MN Balloons have the Right of Way • Why did I pick that title? – First, they do ! – But, why do they ? – What we will cover in the next hour is not me trying to lecture you about the aviation insurance business. Balloons have the Right of Way • What we will cover is an introduction to ballooning. Then, we will look at ballooning as a business, their needs, and aspirations, and some fun facts that all of us as pilots know about airplanes, but have probably never thought about when it comes to these beautiful and colorful giants. 1 6/4/2014 History (short course) • 1783 was the year – Montgolfier was the family – November 21, 1783 First Flight • Champagne – Can’t balloon without it History • Hot Air vs Gas – Gas dominated – Both used 2 6/4/2014 • Don Piccard – First plastic tube balloon – 1957 History • Gas Today – Helium, Hydrogen, Ammonia, Natural Gas – Competition is 100% Hydrogen today – Near space is Helium 3 6/4/2014 Types & Construction • Hot Air • Gas • Airship – Gas – Thermal (hot air) • Fringes Types & Construction • Hot Air – Envelope – Basket – Burners – Accessories • Truck, Trailer, Radios, GPS, Fans, Ropes, Safety Hot Air Envelope 4 6/4/2014 Hot Air Envelope Hot Air Envelope Hot Air Envelope 5 6/4/2014 Hot Air Basket Hot Air Basket Hot Air Burners 6 6/4/2014 Hot Air Burners Hot Air Accessories • Gloves • Fans • Ropes • Restraint Harnesses • Radios • GPS • iPad Gas Balloon Envelope 7 6/4/2014 Gas Balloon Envelope Gas Balloon Envelope Gas -
UCI Rocket Project: Structures Final Report
Balloon-Based Rocket Launch System UCI Rocket Project: Structures Team Leader: Yuan Zhang Members: Nathan Cox, Ryan Williams, Isaiah Navarro, David Li, Robert Chung Advisors: Professor Kenneth Mease, Dave McCue University of California, Irvine 2nd Iteration October 5, 2015 Contents 1. Objective ......................................................................................................................................................................... 2 2. Introduction .................................................................................................................................................................... 2 3. Subsystem Final Report ............................................................................................................................................... 3 3.1 Solar Hot Air Balloon (Ryan Williams, David Li) ......................................................................................... 3 3.2 Helium balloon (Nathan Cox) ........................................................................................................................... 13 3.3 Prototype 2 Rocket (Isaiah Navarro) ............................................................................................................... 18 3.4 Rockoon Platform (Yuan Zhang) ..................................................................................................................... 24 3.5 Helium Balloon Filling System (Yuan Zhang) ............................................................................................. -
Rpt F First Flights
CIA NOTABLE FLIGHTS Part F. Firsts of all kinds Page 1 of 14 0200-0400 Earliest mythical manned flight Antarqui (small boy) Nazca Said to have been sent up in the air to spy on the enemy 1625 First description of hydrogen, first to use the word "gas". Founder of pneumatic chemistry. Johann Baptista van Helmont¹ Investigated and categorized hydrogen and several other gases. 1709-08-08 Earliest recorded model balloon flight Bartholomeu Lourenço de Gusmão Gusmão¹ 1731-11-17 First manned balloon flight according to Russian claims. Mr. Kriakoutny Balloon made of Ox-hides Flew from Ryazan town square. 1782-11-25/ First experiment by Montgolfier. Joseph-Michel Montgolfier¹ Montgolfière No 1. Silk cube. At 18, rue Saint-Etienne, Avignon 1782-12- First outdoor flight. Joseph & Étienne Montgolfier¹ Montgolfière No 2. Cylinder. Paper factory garden in Vidalon-les-Annonay 1782-12-14 First free flight with a model balloon Joseph & Étienne Montgolfier¹ Montgolfière No 3. Silk sphere. 1783-04-25 First free flight at night. Joseph & Étienne Montgolfier¹ Montgolfière No 4. Linen & paper sphere. Château du Colombier, Annonay. 1783-06-04 First public demonstration, free flight. Joseph & Étienne Montgolfier¹ Montgolfière No 4. Linen & paper sphere. Place des Cordeliers, Annonay. 1783-08-27 First Free flight by gas balloon. Jacques Alexandre César Charlière No 1. Rubberized silk sphere. Hydrogen. Charles & Robert brothers¹ Public demonstration. Champ de Mars, Paris - Gonesse 15 km NE Paris. 1783-08-30 First aviation Royal decision Louis XVI King of France¹ King Louis XVI agreed that first aeronauts be prisoners 1783-09-19 First free flight with animals. -
Bruce Comstock
FÉDÉRATION AÉRONAUTIQUE INTERNATIONALE Ballooning Commission Hall of Fame ROBERT BROTHERS, FRANCE Inducted 2000 Photo and plaque published with permission of the Anderson/Abruzzo International Balloon Museum in Albuquerque, New Mexico, USA 1 Anne-Jean Robert, (aîné, the elder). 1758-1820. Marie-Noël Robert, (cadet, the younger). 1760-1820. The Robert brothers were skilled mechanical constructors. They helped professor Jacques Alexandre César Charles build the first usable hydrogen balloons. Charles knew about the work of Cavendish, Black and Cavallo, and realised that hydrogen would make a suitable lifting agent. The problem was to find a airtight and light gas container. The brothers had found a method to dissolve rubber in turpentine. This mixture was used to varnish the silk used to construct the envelopes of the balloons (The silk was red and white but when rubberised, the white parts changed to light yellow). August 27, 1783 Professor Charles and the Robert brothers publicly demonstrated a 35 m3 hydrogen balloon - a rubberised silk sphere. This was the first free flight by a gas balloon. The balloon was launched from Champ de Mars, Paris. It quickly rose to high altitude and landed in Gonesse (15 km NE Paris) where scared villagers attacked the "monster from space". December 1st, 1783. The younger brother, Marie-Noël Robert, accompanied professor Charles on the first human flight in a gas balloon. The "charlière" contained 380 m3 hydrogen and was launched from "Le jardin des Tuileries" in Paris at 13.45. They landed in Nesle-La-Vallée after a 2 hour 5 minute flight covering 36 km. July 15th, 1784.