2017/18 Knowledge Sharing Program with Paraguay
Total Page:16
File Type:pdf, Size:1020Kb
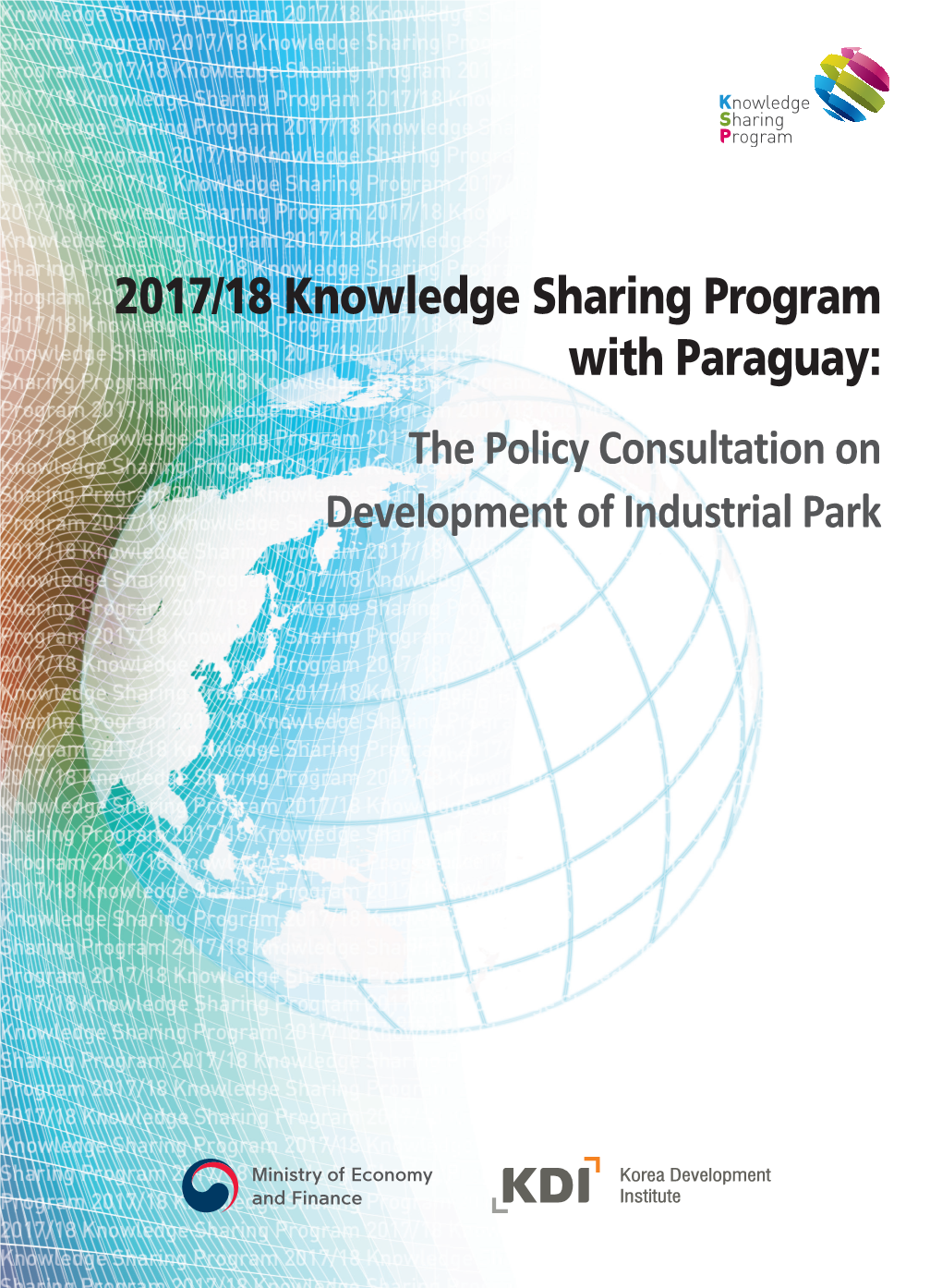
Load more
Recommended publications
-
Health Care Decentralization in Paraguay
HEALTH CARE DECENTRALIZATION IN PARAGUAY: EVALUATION OF IMPACT ON COST, EFFICIENCY, BASIC QUALITY, AND EQUITY Baseline Report MEASURE Evaluation Technical Report Series, No. 4 Gustavo Angeles John F. Stewart Rubén Gaete Dominic Mancini Antonio Trujillo Christina I. Fowler The technical report series is made possible by support from USAID under the terms of Cooperative Agreement HRN-A-00-97-00018-00. The opinions expressed are those of the authors and do not necessarily reflect the views of USAID. December 1999 Printed on recycled paper Other Titles in the Technical Report Series No. 1. Uganda Delivery of Improved Services for Health (DISH) Evaluation Surveys 1997. Path- finder International and MEASURE Evaluation. March 1999. No. 2. Zambia Sexual Behaviour Survey 1998 with Selected Findings from the Quality of STD Services Assessment. Central Statistics Office (Republic of Zambia) and MEASURE Evaluation. April 1999. No. 3. Does Contraceptive Discontinuation Matter? Quality of Care and Fertility Consequences. Ann K. Blanc, Siân Curtis, Trevor Croft. November 1999. Recommended Citation: Gustavo Angeles, John F. Stewart, Rubén Gaete, Dominic Mancini, Antonio Trujillo, Christina I. Fowler. Health Care Decentralization in Paraguay: Evaluation of Impact on Cost, Efficiency, Basic Quality, and Equity. Baseline Report. MEASURE Evaluation Technical Report Series No. 4. Carolina Population Center, University of North Carolina at Chapel Hill. December 1999. Acknowledgements We would like to acknowledge the cooperation and generous support of numerous individuals and organiza- tions that made the first phase of this study possible. We express our gratitude to the staff of 143 health facilities who cooperated with the research team to collect facility and staff data. -
The Study on the Export Corridor and Grain Port Improvement in Paraguay
Ministry of Public Works and Communications (MOPC) Republic of Paraguay The Study on the Export Corridor and Grain Port Improvement in Paraguay FINAL REPORT August 2006 JAPAN INTERNATIONAL COOPERATION AGENCY YACHIYO ENGINEERING CO., LTD. CENTRAL CONSULTANT INC. Exchange rates: May 2006 US$1.00 = Guarani Gs.5,500 US$1.00 = Yen ¥114.58 PREFACE In response to the request from the Government of the Republic of Paraguay, the Government of Japan decided to conduct the Study on the Export Corridor and Grain Port Improvement in the Republic of Paraguay and entrusted the study to the Japan International Cooperation Agency (JICA). JICA dispatched a Study Team headed by Mr. Toshihiro Hotta of Yachiyo Engineering Co., Ltd. to the Republic of Paraguay between September 2005 and July 2006. The Study Team held discussions with the concerned officials of the Republic of Paraguay and conducted the field surveys in the study area. Upon returning to Japan, the Study Team prepared this report. I hope that this report will contribute to the promotion of the project and to the enhancement of friendly relationship between our two countries. Finally, I wish to express my sincere appreciation to the concerned officials of the Republic of Paraguay for their close cooperation extended to the Study. August 2006 Kazuhisa MATSUOKA Vice President Japan International Cooperation Agency Letter of Transmittal August 2006 Mr. Kazuhisa MATSUOKA Vice President Japan International Cooperation Agency Dear Sir, It is a great honor for me to submit herewith the final reports for The Study on the Export Corridor and Grain Port Improvement in Paraguay. -
DOING BUSINESS in PARAGUAY October, 2020
THE POWER OF BEING UNDERSTOOD DOING BUSINESS IN PARAGUAY October, 2020 THE POWER OF BEING UNDERSTOOD AUDIT | TAX | CONSULTING PARAGUAY Population Geographical location The current population of Paraguay is 7.2 million inhabitants (with an average population density of 17.3 inhab./sq Paraguay is located at the heart of South America, between km), unevenly distributed across the territory. The largest parallels 19° 18’ and 27° 30` South latitude and meridians 54° population of Paraguay lives in Asunción in the Western 15` and 62° 38` longitude West of Greenwich. region, as well as in the big cities close to Argentina and Brazil. It is bounded by Argentina to the South East, South and The informal economic activity proportion in Paraguay is high, South West; by Bolivia, to the North and by Brazil to the and it is estimated at 39% of the GDP. The working population East. Given its navigable rivers, particularly the Paraná and aging more than 15 years is 70% and the unemployment rate Paraguay rivers, it has a fluvial outlet to the Río de la Plata reaches 6.9%. which in turn discharges into the Atlantic Ocean. The Paraguayan labor market is featured by a high Asunción is the capital city, located on the left margin of the underemployment rate and a predominance of activities Paraguay river, where 37% of the population is concentrated. requiring lower labor force qualifications. Other important cities are: Ciudad del Este, Encarnación, Pedro Juan Caballero, Salto del Guairá, some of which share Political system their boundaries with Brazil and Argentina, with which it has a Paraguay is a presidential republic where the President is the fluid commercial, social and cultural exchange. -
U-M·I University Microfilms International a Bell & Howell Information Company 300 North Zeeb Road
Castro's Cuba and Stroessner's Paraguay: A comparison of the totalitarian/authoritarian taxonomy. Item Type text; Dissertation-Reproduction (electronic) Authors Sondrol, Paul Charles. Publisher The University of Arizona. Rights Copyright © is held by the author. Digital access to this material is made possible by the University Libraries, University of Arizona. Further transmission, reproduction or presentation (such as public display or performance) of protected items is prohibited except with permission of the author. Download date 05/10/2021 11:08:31 Link to Item http://hdl.handle.net/10150/185284 INFORMATION TO USERS The most advanced technology has been used to photogr2,pb and reproduce this manuscript from the microfilm master. UMI films the text directly from the original or copy submitted.. Thus, some thesis and dissertation copies are in typewriter face, while others may be from any type of computer printer. The quality of this -reproduction is dependent upon the quality of the copy submitted. Broken or indistinct print, colored or poor quality illustrations and photographs, print bleedthrough, substandard margins, and improper alignment can adversely affect reproduction. In the unlikely event that the author did not send UMI a complete manuscript and there are missing pages, these will be noted. Also, if unauthorized copyright material had to be removed, a note will indicate the deletion. Oversize materials (e.g., maps, drawings, charts) are reproduced by sectioning the original, beginning at the upper left-hand corner and continuing from left to right in equal sections with small overlaps. Each original is also photographed in one exposure and is inciuded in reduced form at the back of the book. -
Doing Business in Paraguay: 2014 Country Commercial Guide for U.S
Doing Business in Paraguay: 2014 Country Commercial Guide for U.S. Companies INTERNATIONAL COPYRIGHT, U.S. & FOREIGN COMMERCIAL SERVICE AND U.S. DEPARTMENT OF STATE, 2014. ALL RIGHTS RESERVED OUTSIDE OF THE UNITED STATES. Chapter 1: Doing Business In Paraguay Chapter 2: Political and Economic Environment Chapter 3: Selling U.S. Products and Services Chapter 4: Leading Sectors for U.S. Export and Investment Chapter 5: Trade Regulations and Standards Chapter 6: Investment Climate Chapter 7: Trade and Project Financing Chapter 8: Business Travel Chapter 9: Contacts, Market Research, and Trade Events Chapter 10: Guide to Our Services Return to table of contents Chapter 1: Doing Business In Paraguay Market Overview Market Challenges Market Opportunities Market Entry Strategy Market Overview Return to top Paraguay has a small but rapidly growing open economy (13.6 percent GDP growth in 2013), with strong demand for U.S. manufactured products, and the potential for continued growth over the next decade. U.S.-Paraguay goods trade surpassed $2.2 billion in 2013, with the United States enjoying a $1.6 billion surplus. U.S. goods exports of $1.9 billion included machinery, video games, perfumes and cosmetics, vehicles, and agricultural products. Imports from Paraguay, totaling $277 million, were primarily soybeans, sugar, wood, gold, and corn. Paraguay generally has a strong macroeconomic position. Total foreign direct investment was $4.5 billion in 2012, with the majority directed to the services sector. The United States is the largest foreign investor in Paraguay, followed by Brazil, Argentina, and Spain. Foreign exchange reserves are USD 5.8 billion, about twice the amount of its external debt. -
Economic Asymmetry and Institutional Shortfall in Mercosur: Predictions For
Economic asymmetry and institutional shortfall in Mercosur: predictions for deepening Mercosur integration Master in Advanced European and International Studies – MAEIS Anglophone Branch Academic year 2012-2013 Master thesis Author: F.E. Bakker Supervisor: M. Waechter June 2013 Master Thesis Master in Advanced European and International Studies Author: Fleur Bakker Supervisor: M. Waechter June 2013 Table of content List of tables..............................................................................iii List of Abbreviations.................................................................iv 1. Introduction……………………………………………………1 1.1 Scope and structure……………………………………………………1 1.2 Research question……………………………………………………..3 2. The Southern Common Market (MERCOSUR)……………….4 2.1 A growing alliance between Brazil and Argentina: the origins and evolution of Mercosur…………………………………………………5 2.2 The neo-liberal years…………………………………………………..6 2.3 The start and transition period of Mercosur towards a crisis………….7 2.4 The crisis years of Mercosur…………………………………………..9 2.5 The turn to the left…………………………………………..………..11 3. The institutional framework of Mercosur and the European Union…………………………………………………...…….12 3.1 The decision making bodies within Mercosur…………………………....12 3.1.1 Parliamentary power in Mercosur……………………………..…...13 3.1.2 Popular representation in Mercosur…………………………...…..15 3.1.3 The Secretariat of Mercosur and its powers…………………....…16 3.1.4 Judiciary power within Mercosur………………………………….16 3.1.5 Mercosur’s legal system……………..………………………….....18 3.2.1 -
2021 LIMITED ACCESS STATE NUMBERED HIGHWAYS As of December 31, 2020
2021 LIMITED ACCESS STATE NUMBERED HIGHWAYS As of December 31, 2020 CONNECTICUT DEPARTMENT OF Transportation BUREAU OF POLICY AND PLANNING Office of Roadway Information Systems Roadway INVENTORY SECTION INTRODUCTION Each year, the Roadway Inventory Section within the Office of Roadway Information Systems produces this document entitled "Limited Access - State Numbered Highways," which lists all the limited access state highways in Connecticut. Limited access highways are defined as those that the Commissioner, with the advice and consent of the Governor and the Attorney General, designates as limited access highways to allow access only at highway intersections or designated points. This is provided by Section 13b-27 of the Connecticut General Statutes. This document is distributed within the Department of Transportation and the Division Office of the Federal Highway Administration for information and use. The primary purpose to produce this document is to provide a certified copy to the Office of the State Traffic Administration (OSTA). The OSTA utilizes this annual listing to comply with Section 14-298 of the Connecticut General Statutes. This statute, among other directives, requires the OSTA to publish annually a list of limited access highways. In compliance with this statute, each year the OSTA publishes the listing on the Department of Transportation’s website (http://www.ct.gov/dot/osta). The following is a complete listing of all state numbered limited access highways in Connecticut and includes copies of Connecticut General Statute Section 13b-27 (Limited Access Highways) and Section 14-298 (Office of the State Traffic Administration). It should be noted that only those highways having a State Route Number, State Road Number, Interstate Route Number or United States Route Number are listed. -
Routes & Schedules
657-8218 call call or or 5/30/18 4:44 PM www.mettransit.com or Information visit Information or F UPDATED AUGUST 2021 AUGUST UPDATED SCHEDULES & S ROUTE MET TRANSIT ONE-WAY FARES MET Bus Transfer Locations Adults (19 years & older) $1.75 Most MET routes, except 13, come together in downtown Billings at the transfer center at 220 N. 25th Street. Youth (6-18 years old) $1.50 Many routes come together at the Stewart Park Senior Citizens (62 years & older) Transfer Center just west of Rimrock Mall. For further #Disabled Citizens $0.85 information, please see the Transfer & Pulse System section inside this booklet. Pre-school (under 6 years) FREE Transfers FREE Billings METropolitan Transit MULTIPLE RIDE OPTIONS 1705 Monad Road P.O. Box 1178 Day Pass $4.00 Billings, Montana 59103 10 Ride Ticket $17.50 www.mettransit.com UNLIMITED RIDE MONTHLY PASSES Adult Pass (19 years & older) $28.00/mo. Drivers cannot #Disability I.D. Cards Student Pass (with Student I.D.) $21.00/mo. give change. All riders who qualify for a discounted disability pass Senior Citizen (62 years & older) must obtain a disability photo I.D. card from MET or #Disabled Citizen Pass $12.00/mo. Transit. The first photo I.D. card is free. Replacement All routes are photo I.D. cards are $5 each. For questions, contact #Proof of eligibility required at time of purchase. MET Disability wheelchair Photo I.D. Card, Medicare Card, or other proof accepted. accessible. us at 657-8218. METSchedCover0718.indd 1 METSchedCover0718.indd 2 Table of Contents Page Page Rt.# Rt. -
First Record of Liolaemus Azarai and Hemidactylus Mabouia for Ñeembucú Department, Paraguay
Novedad zoogeográfica Cuad. herpetol. 31 (1): 65-67 (2017) First record of Liolaemus azarai and Hemidactylus mabouia for Ñeembucú Department, Paraguay Víctor Hugo Zaracho1, María Esther Tedesco1, Martha Motte2, Alberto Yanosky3 1 Laboratorio de Herpetología. Facultad de Ciencias Exactas y Naturales y Agrimensura. Universidad Nacional del Nordeste. Av. Libertad 5470 (3400) Corrientes, Argentina. 2 Museo Nacional de Historia Natural del Paraguay. Km 10 ½ Ruta Mariscal Estigarribia. San Lorenzo, De- partamento Central, Paraguay. 3 Asociación Guyra Paraguay, Paraguay. Liolaemus azarai Ávila, 2003 Vulnerable (Motte et al., 2009). The new locality extends its distribution ca. 110 Km to the west of Locality- Paraguay, Ñeembucú Department, the two localities where it was previously recorded Laureles District, San Sebastián (27°11’33’’S; in Paraguay: Isla Yacyretá (Itapúa Department) and 57°48’11’’W. WGS84. 70 m above sea level.). Date: Yabebyry (Misiones Department). 23/01/2016. Col: M. E. Tedesco, V. H. Zaracho and Hemidactylus mabouia has been previously reported M. Motte. Voucher: MNHNP 12086 (juvenile, snout- in urban areas of Alto Paraná, Central, Concepción, vent length: 32.14 mm). San Pedro, and Itapúa Departments (Cacciali et al., 2016) (Fig. 1). It is an invasive species from Africa Hemidactylus mabouia (Moreau de Jonnès, 1818) that currently occurs in México, Cuba and other is- Locality-Paraguay, Ñeembucú Department, Cerrito lands, Venezuela, Guyana, Ecuador, Peru, Colombia, (27°20’38’’S; 57°38’24’’W. WGS84. 65 m above sea Brazil, Argentina, Uruguay and Paraguay (Cacciali level ). Date: 22/01/2016. Col: M. E. Tedesco, V. H. Zaracho and M. Motte. Voucher: MNHNP 12087 (adult, snout-vent length: 55.53 mm). -
Macroeconomic Policy
Alicia Bárcena Executive Secretary Antonio Prado Deputy Executive Secretary Osvaldo Kacef Chief, Economic Development Division Susana Malchik Officer-in-Charge Documents and Publications Division The Preliminary Overview of the Economies of Latin America and the Caribbean is an annual publication prepared by the Economic Development Division of the Economic Commission for Latin America and the Caribbean (ECLAC). This 2010 edition was prepared under the supervision of Osvaldo Kacef, Chief of the Division; Jürgen Weller and Sandra Manuelito were responsible for its overall coordination. In the preparation of this edition, the Economic Development Division was assisted by the Statistics and Economic Projections Division, the ECLAC subregional headquarters in Mexico City and Port of Spain, and the Commission’s country offices in Bogota, Brasilia, Buenos Aires, Montevideo and Washington, D.C. The regional analyses were prepared by the following experts (in the order in which the subjects are presented): Osvaldo Kacef and Luis Felipe Jiménez (introduction), Juan Pablo Jiménez (fiscal policy), Rodrigo Cárcamo (monetary and exchange-rate policy), Sandra Manuelito (economic activity and investment and domestic prices), Jürgen Weller (employment and wages), and Luis Felipe Jiménez, Fernando Cantú and Claudio Aravena (external sector). The text boxes were prepared by Andrea Podestá and staff from the ECLAC subregional headquarters for the Caribbean, as well as the Disaster Assessment Unit and the Sustainable Development and Human Settlements Division -
Chapter 6 Road Network of the Study Area
Feasibility Study for the Improvement of the National Route 2 and Route 7 Final Report CHAPTER 6 ROAD NETWORK OF THE STUDY AREA Feasibility Study for the Improvement of the National Route 2 and Route 7 Final Report 6 ROAD NETWORK OF THE STUDY AREA 6.1 Transportation System (1) Main Ports Inland water transport uses the Parana River and its tributary, the Paraguay River, connecting to the La Plata River on the downstream side. These rivers are the boundaries with Brazil and Argentina and most of the waterways are under joint management. This inland water transport is mainly used for international trade cargo. Principal export/import ports are described below: – Concepción Port: Located 1,940 km from Buenos Aires and in the independent management section of the Paraguay River running through Paraguay. This port is mainly used to load beans on vessels. – Asuncion Port: Located 1,630 km from Buenos Aires, this port is used for cotton export and principal everyday commodities, such as general cargoes and automobiles, are imported in containers via the Paraguay River. – Villeta Port: Located 37km to the south of Asuncion Port and used for export of beans and cotton. – Villa Hayes Port: Located near Asuncion and used for the import of steel making raw materials. – Villa Elisa Port: Located near Asuncion and used for the import of oils. – San Antonio Port: Located near Asuncion and used for the export of beans. – Vallemi Port: Port to import cement raw materials. – Encarnación: Located on the Parana River, 1,583km from Buenos Aires, and used for the export of beans. -
California-Baja California Border Master Plan
California-Baja California Border Master Plan Plan Maestro Fronterizo California-Baja California Final Report Informe Final SEPTEMBER 2008 SEPTIEMBRE 2008 SEPTEMBER 2008 SEPTIEMBRE 2008 California-Baja California Border Master Plan Plan Maestro Fronterizo California-Baja California Final Report Informe Final Submitted to Caltrans, District 11 4050 Taylor Street San Diego, CA 92110 Submitted by SANDAG Service Bureau 401 B Street, Suite 800 San Diego, CA 92101-4231 Phone 619.699.1900 Fax 619.699.1905 www.sandag.org/servicebureau The California-Baja California Border Master Plan was commissioned by the U.S./Mexico Joint Working Committee to the California Department of Transportation (Caltrans) and the Secretariat of Infrastructure and Urban Development of Baja California (Secretaría de Desarrollo Urbano del Estado de Baja California or SIDUE) for the California-Baja California border region. El Plan Maestro Fronterizo California-Baja California fue comisionado por el Comité Conjunto de Trabajo de los Estados Unidos y México a Caltrans y a SIDUE para la región fronteriza de California-Baja California. TABLE OF CONTENTS EXECUTIVE SUMMARY ..................................................................................................................... ES-1 Introduction ....................................................................................................................................... ES-1 Study Purpose and Objectives ........................................................................................................